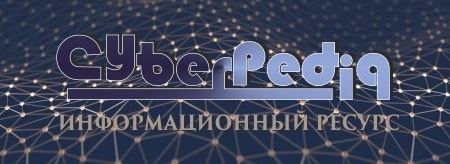
Типы оградительных сооружений в морском порту: По расположению оградительных сооружений в плане различают волноломы, обе оконечности...
Общие условия выбора системы дренажа: Система дренажа выбирается в зависимости от характера защищаемого...
Топ:
Марксистская теория происхождения государства: По мнению Маркса и Энгельса, в основе развития общества, происходящих в нем изменений лежит...
Характеристика АТП и сварочно-жестяницкого участка: Транспорт в настоящее время является одной из важнейших отраслей народного хозяйства...
Интересное:
Аура как энергетическое поле: многослойную ауру человека можно представить себе подобным...
Национальное богатство страны и его составляющие: для оценки элементов национального богатства используются...
Распространение рака на другие отдаленные от желудка органы: Характерных симптомов рака желудка не существует. Выраженные симптомы появляются, когда опухоль...
Дисциплины:
![]() |
![]() |
5.00
из
|
Заказать работу |
|
|
Первая холодная прокатка
5.1.1 Первую холодную прокатку производят на четырехклетьевом стане 1300 с толщины 2,2-2,8 мм на толщину 0,50-0,85 мм по заданию ПДО на основании рекомендаций ЦЗЛ.
Режимы обжатий в зависимости от назначения на толщину приведены в таблице 1 Режимы обжатий в зависимости от назначения на толщину.
5.1.2 Предельное отклонение по толщине от номинала ±0,03 мм.
Отклонение по толщине более предельного допускается:
- на концах полосы длиной до 25 м;
- на участках полосы с дефектами подката.
5.1.3 Профилировку валков, периодичность перевалок и подготовку валков производят согласно ИЭ 48576703-013-004.
Таблица 1 - Режимы обжатий в зависимости от назначения на толщину
№ клети |
Толщина полосы, мм
Обжатие
На толщину 0,85 мм
На толщину 0,80 мм
На толщину 0,75 мм
Таблица 1 - продолжение
№ клети |
Толщина полосы, мм
Обжатие
На толщину 0,70 мм
На толщину 0,65 мм
На толщину 0,60 мм
На толщину 0,55 мм
|
На толщину 0,50 мм
Примечание: допускается перераспределение обжатий по клетям ±5%.
5.1.4 При прокатке на стане 1300 в качестве технологической смазки используют водную эмульсию на основе эмульсола «Универсал ТС» согласно ТУ 0258-001-45846757-01.
Диапазон изменения температуры эмульсии от 40°С до 60°С.
Эмульсия должна отвечать следующим требованиям:
- рН 7-9;
- содержание эмульсола от 2% до 6%;
- механические примеси в эмульсии до 100 мг/л;
- содержание неэмульгированных масел до 1%.
Проверку эмульсии производят в ЦЗЛ 5 раз в неделю в утреннюю смену руководствуясь требованиями МВИ Х-29/04-09-2013 и МВИ Х-29/04-10-2013.
5.1.5 Скорость прокатки полосы не должна превышать 8 м/с.
5.1.6 Измерение толщины прокатываемой полосы производится автоматически бесконтактным толщиномером с записью на диаграммную ленту. Проверку правильности показаний толщиномеров производят в соответствии с требованиями ИЭ 48576703-013-006,не менее трёх раз в смену и не менее одного раза из них – в присутствии дежурного радиоизотопной лаборатории, который вносит результаты проверки в производственный журнал.
5.1.7 Прокатку производят с использованием системы автоматического регулирования толщины (САРТиН).
Допускается отключение отдельных узлов САРТиН в период настройки системы, а также при прокатке первого рулона после изменения сортамента или простоя стана, при условии обеспечения толщины полосы в пределах допусков.
5.1.8 Прокатанный рулон должен отвечать следующим требованиям:
- ровно и плотно смотан;
- выступающие витки в местах подмоток - не более 100 мм, в остальных местах - не более 20 мм;
- телескопичность не более 40 мм;
- обвязан и замаркирован на внешнем витке;
|
Следы эмульсии и прижогов на поверхности рулона не допускаются.
Подготовка металла после первой холодной прокатки
5.2.1 При подготовке рулонов в промежуточной толщине на АПР-1, 2 перед обезуглероживающе-рекристаллизационным отжигом производят подрезку кромок, вырезку участков полосы с дефектами и с толщиной, выходящей за пределы допусков, сварку всего рулона в единую полосу в соответствии с ТИ 13.18.
Допустимые отклонения по толщине полосы: ±0,03 мм.
5.2.2 Подготовку концов рулонов осуществляют с минимальным количеством поперечной обрези до толщины 1,0 ± 0,2 мм. При наличии на концах рулонов, рванин, трещин замятых или забитых кромок полос (по визуальной оценке), подготовку концов рулонов производят до устранения дефектов с минимальным попаданием металла в поперечную обрезь.
На обложке стендовой партии - «разведчика», назначенной на лабораторное моделирование, ЦЗЛ или ПДО ставит отметку «ЛМ». Начало рулонов 1, 3 и 5 этого «разведчика» обрабатывают с допуском отклонения по толщине полосы ±0,03 мм от номинальной.
5.2.3 Подрезку боковых кромок производят на ширину, указанную заданием ПДО с допуском +5,0 мм. Отклонение по ширине полосы не должно превышать ±1,0 мм.
При наличии единичных кромочных дефектов по длине полосы:
- глубиной ≤ 20мм – производят их вырубку штампом;
- глубиной > 20мм – производят вырезку дефектного участка со сваркой полосы на сварочной машине.
При наличии множественных кромочных дефектов стендовую партию задерживают и проводят мероприятия в соответствии с требованиями СТП СМК 48576703-8.5-003.
5.2.4 Рулоны после подготовки должны отвечать следующим требованиям:
- состоять из единой сваренной полосы без подмоток;
- обвязаны обручкой и замаркированы на внешнем витке;
- ровно и плотно смотаны (допускаются отдельные выступающие витки до 10 мм у сварных швов);
- телескопичность не более 40 мм;
- места сварных швов должны быть отмечены закладками;
- величина заусениц по кромкам - не более 0,10 мм;
- рванины, дыры, замятая кромка, ржавчина и другие явные дефекты не допускаются;
- осевое смещение сваренных полос не допускается.
Обезжиривание полосы
5.3.1 Перед обработкой в проходных агрегатах АРО-1,2,АОО 1А, АОО-3, 4 металл проходит операцию обезжиривания. Обезжиривание производят в щёточно-моечных машинах агрегатов, с применением обезжиривающих растворов.
|
5.3.2 Обезжиривающие растворы готовят централизованно в ООО «Завод технологической химии» в соответствии с требованиями ТИ 48576703-ЦЗЛ-03.
5.3.3 Уровень щелочности раствора в пересчете на NaOH должен находиться в пределах 6,0-15,0 г/л. Температура обезжиривающего раствора на АРО-1,2 не менее 80°C, на АОО-1А 60-80°C. На АОО-3А,Б и АОО-4А,Б - 60-80°C.
5.3.4 Анализ обезжиривающих рабочих растворов на уровень щелочности на каждом агрегате производят один раз в смену. Технологический персонал ТУОРО с помощью пробоотборника из рабочего бака, расположенного в химическом подвале линий АОО 1А, 3А, 4А, АОО 3Б, 4Б, АРО-1,2 отбирает пробы раствора и доставляет в ГХИ ЦЗЛ и результаты анализа из лабораторного журнала записывает в паспорт стендовой партии.
5.3.5 Переход на свежие растворы на линиях АОО 1А, АРО-1 иАОО-3 осуществляют по нечетным дням, на линиях АРО-2 иАОО-4 – по четным дням. Заполнение каждого из двух рабочих баков обезжиривающим раствором производится автономно, только после слива остатков отработанного раствора в дренаж. Технологический персонал ТУОРО делает запись о смене обезжиривающего раствора в паспорт стендовой партии и книгу производства.
5.3.6 Поверхность полосы после обезжиривания должна быть чистой, без пятен и подтеков.
Контроль загрязненности полосы на АОО производят методом протирки поверхности после обезжиривания фильтровальной бумагой. На бумаге не должно быть следов загрязнения.
При наличии загрязнения технологический персонал проверяет состав и температуру обезжиривающего раствора (см. п.5.3.3 данной инструкции), и при необходимости:
- меняет обезжиривающий раствор, либо промывную воду;
- проверяет качество отжима растворов и воды на отжимных роликах;
- меняет щётки щёточно-моечной машины.
|
|
Автоматическое растормаживание колес: Тормозные устройства колес предназначены для уменьшения длины пробега и улучшения маневрирования ВС при...
Архитектура электронного правительства: Единая архитектура – это методологический подход при создании системы управления государства, который строится...
Папиллярные узоры пальцев рук - маркер спортивных способностей: дерматоглифические признаки формируются на 3-5 месяце беременности, не изменяются в течение жизни...
Состав сооружений: решетки и песколовки: Решетки – это первое устройство в схеме очистных сооружений. Они представляют...
© cyberpedia.su 2017-2024 - Не является автором материалов. Исключительное право сохранено за автором текста.
Если вы не хотите, чтобы данный материал был у нас на сайте, перейдите по ссылке: Нарушение авторских прав. Мы поможем в написании вашей работы!