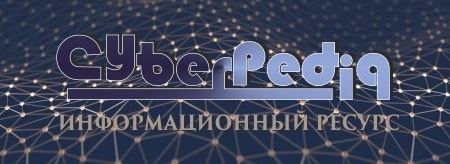
Таксономические единицы (категории) растений: Каждая система классификации состоит из определённых соподчиненных друг другу...
Опора деревянной одностоечной и способы укрепление угловых опор: Опоры ВЛ - конструкции, предназначенные для поддерживания проводов на необходимой высоте над землей, водой...
Топ:
История развития методов оптимизации: теорема Куна-Таккера, метод Лагранжа, роль выпуклости в оптимизации...
Когда производится ограждение поезда, остановившегося на перегоне: Во всех случаях немедленно должно быть ограждено место препятствия для движения поездов на смежном пути двухпутного...
Процедура выполнения команд. Рабочий цикл процессора: Функционирование процессора в основном состоит из повторяющихся рабочих циклов, каждый из которых соответствует...
Интересное:
Отражение на счетах бухгалтерского учета процесса приобретения: Процесс заготовления представляет систему экономических событий, включающих приобретение организацией у поставщиков сырья...
Искусственное повышение поверхности территории: Варианты искусственного повышения поверхности территории необходимо выбирать на основе анализа следующих характеристик защищаемой территории...
Наиболее распространенные виды рака: Раковая опухоль — это самостоятельное новообразование, которое может возникнуть и от повышенного давления...
Дисциплины:
![]() |
![]() |
5.00
из
|
Заказать работу |
|
|
Для получения идеального вяжущего материала для покрытий из HMA необходима его модификация с целью улучшения характеристик по следующим направлениям (см. рис. 7–8) (30):
1. Снижение густоты (или вязкости) при высоких конструкционных температурах для облегчения подачи жидкого битумного вяжущего, а также смешивания и уплотнения HMA.
2. Повышение густоты при высоких рабочих температурах (лето) для менее интенсивного образования колей и сдвигов.
3. Понижение густоты и повышение скорости релаксации при низких рабочих температурах (зима) для борьбы с образованием низкотемпературных трещин.
4. Усиление адгезии между битумным вяжущим и заполнителем в присутствии влаги для предотвращения отслаивания вяжущего от заполнителя.
В прошлом некоторого улучшения характеристик покрытий из HMA удавалось добиться за счет правильного подбора смеси и марки битума. В настоящее время открываются новые перспективы для применения модификаторов и добавок (29). Однако необходимо проанализировать ряд ключевых вопросов, касающихся модификации битумов, а именно:
a) Какое именно улучшение требуется внести? Следует назвать конкретные характеристики, которые нуждаются в усилении.
b) Какой модификатор будет наиболее эффективным? Не существует универсальных модификаторов; нередко модификатор улучшает какое-то одно свойство HMA за счет другого. Так, например, некоторые жидкие модификаторы, препятствующие отслаиванию вяжущего от заполнителя, ослабляют вредное воздействие влаги, но при этом способствуют размягчению битумного вяжущего, что создает риск образования колеи.
c) Каким образом следует вводить модификатор в вяжущее и/или в смеси? Этот вопрос, скорее всего, приобретет ключевое значение в условиях роста числа доступных модифицированных систем.
|
d) Нужно ли анализировать вопрос о совместимости? Ответ на этот вопрос однозначно положительный, но, к сожалению, на настоящий момент еще не до конца отработана универсальная технология проверки совместимости.
e) Каким образом следует хранить вяжущее для того, чтобы оно сохраняло свои свойства в течение длительного времени?
f) Какие нормативы следует ввести для вяжущего материала?
g) Влияет ли модификатор на результаты рутинных тестов? Например, введение определенных модификаторов препятствует точному определению содержания битума в HMA.
h) Можно ли провести рециклинг HMA? Этот вопрос был поднят, например, в случае HMA, содержащих резиновую крошку в качестве модификатора.
i) Каким образом модификатор влияет на стоимость жизненного цикла? Обоснованно ли повышение первоначальной стоимости c точки зрения затрат на жизненный цикл?
j) Каково возможное влияние модификатора на здоровье и безопасность персонала?
Рис. 7–8. Характеристики густоты обычного и идеального модифицированного вяжущего (30)
Классификация
Добавки и модификаторы можно классифицировать по-разному. В таблице 7–6 приведена модифицированная версия оригинальной универсальной системы классификации, предложенной в (32). Следует отметить, что перечень добавок, включенных в каждую категорию этой системы, быстро меняется. Ниже обсуждается каждый тип добавок или модификаторов.
Минеральные наполнители
Понятие «минеральный наполнитель» охватывает минеральную пыль от измельчения и просеивания заполнители (включая мелкие фракции из пылеуловителя с рукавными фильтрами), известняк, портланд-цемент и зола. Такие материалы, как сажа и сера, используются, главным образом, для модификации свойств битумного вяжущего и при этом не выполняют функции наполнителя. Наполнители могут использоваться для (1) заполнения пустот и, соответственно, снижения оптимального содержания битума, (2) приведения гранулометрического состава заполнителя в соответствие с нормативными требованиями, (3) повышения устойчивости смесей и (4) укрепления связи между битумом и заполнителем. Как правило, с повышением содержания наполнителя снижается оптимальное содержание битума, увеличивается плотность и повышается устойчивость смесей (33).
|
Минеральные наполнители используются, в основном, в двух первых случаях. Однако в литературе имеются многочисленные данные о том, что такие минеральные наполнители, как мелкие фракции из пылеуловителя с рукавными фильтрами, в действительности влияют на поведение битумных вяжущих асфальтовяжущих и HMA (34, 35). Минеральные наполнители вызывают общее загущение или оказывают армирующее воздействие на HMA. Однако сила эффекта загущения, как правило, определяется пустотностью по Ригдену (Rigden void content – содержание пустот между мелкими частицами в сухом уплотненном состоянии). Этот показатель, в свою очередь, зависит от минералогического типа, характера распределения частиц по размерам, формы частиц и текстуры поверхности минеральных наполнителей (34). Некоторые виды мелких фракций из пылеуловителя с рукавными фильтрами (в основном, содержащие глину) могут способствовать отслаиванию вяжущего в HMA.
Таблица 7-6. Универсальная классификация добавок и модификаторов для асфальтных смесей
ТИП | УНИВЕРСАЛЬНЫЕ ПРИМЕРЫ |
1. Наполнитель | · Минеральный наполнитель: мелкие фракции от дробления известняка портланд-цемент зола · Сажа |
2. Разбавитель | · Сера · Лигнин |
ПОЛИМЕРЫ
|
Все наполнители следует вводить в асфальтобетонные смеси в определенной последовательности и в правильном соотношении; в противном случае свойства смеси серьезно ухудшатся. При избытке наполнителя обычно сокращается показатель VMA – до уровня, при котором в смесь невозможно ввести то количество битума, которое необходимо для обеспечения ее долговечности. При высоком содержании наполнителя также увеличивается площадь поверхности заполнителя, что приводит к значительному истончению битумной пленки. Некоторые нормативы устанавливают предельные величины для соотношения пыль/битум; как правило, это соотношение должно составлять 0,6–1,2 по весу. В идеальном случае норматив должен регулировать объемное соотношение пыль/битум с учетом содержания пустот по Ригдену (которые обычно отвечают за эффект загущения).
Несмотря на то, что известь является минеральным наполнителем, она добавляется к HMA, в основном, для минимизации отслаивания вяжущего. Этот вопрос обсуждается ниже.
Сажу можно считать «микронаполнителем», так как она состоит из очень мелких частиц. Имеются сажи различных марок и типов, так как сажа находит широкое применение в других отраслях промышленности, например, для армирования резиновых шин. Сажа, которая используются в HMA, включает частицы субмикронного размера (порядка 1014 частиц на грамм). Этот материал состоит из очень мелких частиц, которые могут легко переноситься по воздуху, что вызывает загрязнение атмосферного воздуха. Поэтому сажу обычно комбинируют с высококипящим мальтеновыми фракциями, и из этой смеси изготавливают таблетки, более удобные для обработки на установках по производству HMA. Рекомендуемые концентрации таких таблеток находятся в диапазоне от 10 до 15% по весу битума. В целях обеспечения необходимых низкотемпературных свойств в условиях холодного климата при одновременном сохранении заданных высокотемпературных свойств, некоторые автодорожные агентства используют более мягкие сорта битума по сравнению с традиционно используемым сортом. Сажа поставляется в полиэтиленовых пакетах или в контейнерах для сыпучих материалов. Еe можно предварительно смешать с битумом либо на нефтеперерабатывающем заводе, либо на установке по производству HMA. Для компенсации эффекта загущения при применении сажи можно поднять температуру смешения с 10оF до 20оF (с 6оС до 11оС). Получена информация о том, что битумное вяжущее, армированное сажей, повышает сопротивление покрытий из HMA колееобразованию, увеличивает их износостойкость и стойкость к истиранию, а также уменьшает окислительное твердение и охрупчивание вяжущего в атмосферных условиях. Вопрос об использовании сажи в HMA изучался различными исследователями (36, 37).
|
Разбавители
Концепция разбавления битумного вяжущего получила заметное развитие после введения эмбарго на нефть в 1973 г. в связи с ожиданием дальнейшего роста цен на битум и его возможного дефицита. Федеральная дорожная администрация (FHWA) инициировала исследования по разбавлению битумного вяжущего за счет частичного замещения его серой и лигнином. Кроме того, изучался вопрос о создании заменителя битума на основе серы (Sulphlex) (38). Основная масса и серы, и лигнина является побочным продуктом других производств: сера – процесса десульфурации природного газа, а лигнин – целлюлозно-бумажного производства. Из-за сильного колебания объемов поставок серы и цен на нее после введения эмбарго на нефть в 1973 г. случаи использования серы носили единичный характер. В настоящее время (1996 г.) в связи со снижением цен на битум и ростом цен на серу последняя не может конкурировать с битумом. Что касается лигнина, то опыт его промышленного использования в HMA также незначителен. Лигнин – в основном в виде топлива – идет на внутрипроизводственные нужды.
Сера – широко распространенный неметаллический химический элемент. При комнатной температуре это твердое кристаллическое вещество желтого цвета. При температуре порядка 240оF (116оС) сера плавится и превращается в свободнотекущую жидкость цвета соломы. При температурах выше 310оF (154оС) жидкая сера приобретает высокую вязкость. В диапазоне от 250оF до 290оF (от 121оС до 143оС), который практикуется при производстве HMA и строительстве покрытий из них, вязкость серобитумного вяжущего ниже вязкости самого битума. Сера используется для модифицирования базового, связующего и поверхностного слоев HMA
|
Ввиду того, что удельный вес серы (около 2,07 при 68оF, или 20оС) приблизительно вдвое превышает удельный вес битума, удельный вес серобитумного вяжущего возрастает с ростом содержания серы. Последнее варьирует от 10 до 50% от веса вяжущего материала; однако чаще всего степень замещения оказывается в диапазоне 20–35% по весу (приблизительно 10–17,5 % по объему) вяжущего. Серу поставляют либо в твердом, либо в жидком виде, как правило, в железнодорожных цистернах или грузовом автотранспорте и вводят в битум непосредственно перед смешением компонентов HMA. В случае системы с жидкой серой необходимо предусмотреть отдельный бак-накопитель для жидкой серы, а также соответствующий насос, измерительную систему, а в некоторых случаях и устройство для предварительного смешения. При использовании системы с твердой серой необходимо оборудовать площадку для хранения и предусмотреть конвейерную систему, небольшую дробилку, шнековый питатель и воздуходувную систему. Разработаны различные методы и оборудование для комбинирования серы и битума перед их добавлением к заполнителю на установке по производству HMA (29). Во избежание накопления газообразного диоксида серы (SO2) или сероводорода (H2S) очень важно обеспечить эффективный температурный контроль в сочетании с надлежащей системой вентиляции. Инструкции по проектированию, контролю качества и строительству покрытий из асфальтобетонных смесей с серобитумным вяжущим можно найти в (39). Различные исследователи сообщали о проведенном ими анализе серобитумных вяжущих и смесей (40, 41, 42). В итоге было показано, что по своим эксплуатационным характеристикам дорожные покрытия на основе серобитумного вяжущего эквивалентны обычным покрытиям из HMA. Полагают, что только какая-то часть серы модифицирует вяжущий материал, а остальная часть выкристаллизовывается и выступает в роли наполнителя.
Горячая расплавленная сера представляет такую же опасность, что и горячее битумное вяжущее или любая иная горячая жидкость. Сера горит, если ее поджечь. Недопустимо нахождение любых источников огня (курение, открытое пламя, искры) вблизи от жидкой серы. Очень важно всегда поддерживать температуру серобитумных смесей на уровне ниже 300оF (149оС). Выше этой точки возможно быстрое нарастание эмиссии паров сероводорода, диоксида серы и серы, что может нанести вред здоровью персонала.
Опыт применения лигнина в качестве разбавителя битума для HMA в промышленных масштабах отсутствует. Однако была проведена оценка его потенциала для использования в качестве заменителя или разбавителя битума лабораторных условиях (43).
Полимеры
Как видно из таблицы 7–6, и резина, и пластмассы отнесены к полимерам. В упрощенном виде определение «полимер» можно сформулировать следующим образом: это химические соединения, состоящие из больших молекул, образованных большим (отсюда «поли») количеством повторяющихся малых молекул (мономеров), химически присоединенных друг к другу в виде цепей или кластеров. Последовательность расположения мономеров и их химическая структура определяют физические свойства образующегося полимера. Полимеры, макромолекулы которых содержат несколько типов мономерных звеньев, называются сополимерами. Они могут располагаться случайным образом (хаотично) или образовывать блоки. Так, например, если смешать случайным образом полистирол (твердую, хрупкую пластмассу) и полибутадиен (мягкий резиноподобный) материал и дать им прореагировать друг с другом, то из этих двух сильно отличающихся друг от друга мономеров получится новый полимер, называемый сополимером, свойства которого сильно отличаются от свойств исходных мономеров. Можно целенаправленно синтезировать полимеры, обладающие широким спектром физических свойств. Все полимеры можно разделить на две большие группы: эластомеры (резины) и пластомеры (пластмассы).
Эластомеры, или резины, используемые в качестве модификаторов битума, включают натуральную резину, латексный сополимер бутадиен-стирол, или SBR, блок-сополимеры стирол-бутадиен-стирол (SBS), блок-сополимеры стирол-изопрен-стирол (SIS), полихлоропреновые латексы и резиновую крошку (из переработанных покрышек). При приложении нагрузки эластомеры сопротивляются деформации за счет растяжения и быстро восстанавливают свою форму после снятия нагрузки. Эти полимеры лишь в незначительной степени придают прочность битуму, если они не растянуты. Однако прочность эластомеров на разрыв возрастает с удлинением (44).
Пластомеры, или пластмассы, используемые в качестве модификаторов битума, включают полиэтилен, полипропилен, этилвинилацетат (EVA), поливинилхлорид (PVC), этилен-пропилен (EPDM) и полиолефины. Пластомеры характеризуются наличием плотной, жесткой трехмерной сетки, которая сопротивляется деформации. Эти полимеры быстро проявляют раннее упрочнение при приложении нагрузки, но могут дать трещины при деформации (44).
В результате модифицирования битумов эластомерами из HMA получаются более гибкие и эластичные дорожные покрытия. С другой стороны, пластомеры, как правило, повышают модуль жесткости покрытий из HMA. Однако результат модификации в обоих случаях в значительной степени зависит от концентрации, молекулярного веса, химического состава и молекулярной структуры конкретного полимера. Не менее важны характеристики сырья, особенности процесса очистки и марка чистого битумного вяжущего.
Из эластомеров (резин) и пластомеров (пластмасс) можно составить самые разнообразные комбинации, чтобы получить модифицированное битумное вяжущее с заданными свойствами.
Резина. Как видно из таблицы 7–6, существует множество резиновых материалов (или эластомеров), которые можно применять для модификации битумного вяжущего. Многие из них выпускаются в промышленности под другими, возможно, более знакомыми, торговыми названиями. Конкретную информацию по этим продуктам можно найти в (29). Резиновые материалы имеют очень сложную природу, и при смешении в чистом виде с битумом они не всегда передают материалам свои свойства. Более того, при введении такого модификатора в HMA, особенно в случае тонких пленок, возможно ослабление или даже изменение этих свойств. Каждый модификатор может по-своему реагировать с разными битумами, и поэтому очень трудно предсказать, даст ли конкретная комбинация желаемый эффект. Для этого нужно протестировать битумное вяжущее после модификации.
Основная цель, которая преследуется при введении резины в качестве модификатора битума в HMA, – повысить жесткость при высоких температурах эксплуатации, придать большую эластичность для сопротивления усталостному растрескиванию при промежуточных температурах и обеспечить снижение или неизменность жесткости при низких температурах эксплуатации для сопротивления образованию низкотемпературных трещин. Как ожидается, в будущем вопрос о достижимости поставленных целей за счет использования резиновых модификаторов можно будет решать с помощью процедур проектирования и анализа смеси по системе Superpave.
Латексный сополимер бутадиен-стирол (SBR) – это серовато-белая жидкость, которая поставляется в бочках объемом 55 галлонов (210 л) или в розлив. Доза вводимого SBR латекса составляет 2–3% сухой твердой резины от веса битума. Латекс можно добавлять к горячему битуму в смесителе на нефтеперерабатывающем заводе, после чего модифицированный вяжущий материал поступит на установку по производству HMA. Пар, образующийся в результате испарения воды по ходу этого процесса, удаляется с помощью циклона. Также латекс можно добавлять на самой установке по производству HMA. Критичной для получения желаемого результата является последовательность добавления компонентов. Заполнитель должен быть полностью покрыт чистым битумом до введения латекса. В установках периодического действия латекс обычно вводят через 8–10 сек. после загрузки чистого битума. В данном случае общее время смешения «мокрым способом» примерно на 10 сек больше, чем обычно для такого процесса. В случае барабанных смесителей латекс следует вводить в барабан в промежутке между моментом введения чистого битума и временем выгрузки смеси из барабана. В случае SBR латекса в обычные процедуры укладывания и уплотнения HMA, как правило, не вносится существенных изменений.
Блок-сополимеры стирол-бутадиен-стирол (SBS) поставляются в твердом виде в форме таблеток, в виде крошки или в измельченном виде в пакетах или навалом. Обычная доза этих блок-сополимеров составляет ~5% от веса битума. С помощью оборудования для смешения с высокими усилиями сдвига данный модификатор смешивают с горячим битумом, температура которого поддерживается на уровне 350оF –380оF (177оС –193оС). Модифицированное битумное вяжущее можно приготовить на нефтеперерабатывающем заводе и доставить на установку для HMA, как в случае обычного битума; оно не требует перемешивания в период хранения. В рамках большинства процедур проектирования устанавливаются определенные пределы по вязкости битумного вяжущего при смешении и уплотнении. Поэтому, возможно, потребуется повысить температуры смешения и уплотнения при проведении лабораторных исследований. Однако, как показали полевые испытания, никаких непредвиденных сложностей не возникает и в случае обычных температур смешения при обработке и уплотнении HMA, полученной с применением такого модифицированного вяжущего материала с высокой вязкостью. Скорее всего, причиной этого являются относительно более высокие усилия сдвига, возникающие при производстве в полевых условиях по сравнению с лабораторными условиями. Соответственно, как в лабораторных, так и в полевых условиях, при выборе температур смешения и уплотнения необходимо следовать рекомендациям поставщика.
Регенерированная резина является, в основном, продуктом переработки шин, которые в США ежегодно выбрасываются в отходы в количестве около 285 млн. Из этого количества шин 55 млн. получают новый слой протектора и используются повторно (перепродаются), а около 42 млн. отводится на различные альтернативные нужды (например, сжигается при производстве электроэнергии и служит в качестве добавок к HMA). Оставшиеся 188 млн. шин поступают на существующие полигоны, мусорные свалки или несанкционированные свалки. По оценкам Агентства по охране окружающей среды США, в 1992 г. насчитывалось от 2 до 3 млрд. выброшенных шин (45). В некоторых штатах было разработано соответствующее законодательство для регулирования проблемы таких отходов.
Резиновую крошку, полученную в результате переработки шин, можно измельчить либо в условиях окружающей среды (при комнатной или более высокой температуре), либо с помощью криогенной техники (измельчение при температуре ниже температуры хрупкости; часто с использованием жидкого азота). Резиновая крошка, измельченная в условиях окружающей среды, имеет губчатую поверхность, и благодаря очень большой площади поверхности такая резина достаточно быстро реагирует с битумом. Что касается резины, измельченной в криогенных условиях, то в некоторых случаях она приобретает нежелательную морфологию (структуру) частиц. Измельчение в криогенных условиях дает резину с чистыми плоскими поверхностями, что, в свою очередь, может замедлить реакцию с горячим битумом. Как показало одно из исследований (46), в случае криогенно измельченной резины выигрыш в эластичности был меньше, чем в случае резины, измельченной в условиях окружающей среды.
Вопрос об использовании резиновой крошки для модифицирования битума прорабатывался в течение последних 25 лет. При модифицировании HMA резиновая крошка используется, главным образом, в рамках двух процессов, которые обычно называют «мокрым процессом» и «сухим процессом».
1. «Мокрый процесс» (Резинобитум).
В ходе мокрого процесса резиновая крошка смешивается с битумом перед введением вяжущего в смесь. Модифицированный вяжущий материал обычно называют «резинобитумом». Как правило, 18–26% резиновой крошки (≤16 меш) от веса битума реагирует с ним при температуре 375оF–425оF (191оС –218oC) в течение 1–2 часов. Смесь формируется при повышенных температурах, что стимулирует химическое и физическое связывание двух компонентов. Первая технология, в рамках которой применялся «мокрый процесс», получила название «процесса Мак-Дональда». Она также используется для создания стрессовоспринимающих мембран (stress absorbing membrane – SAM) и промежуточных стрессовоспринимающих мембран (stress absorbing membrane interlayer – SAMI), а также для производства материалов для герметизации трещин. SAM– это изолирующее покрытие, в котором резинобитум выступает в качестве вяжущего. Стрессовоспринимающую мембрану, помещенную в качестве промежуточного слоя между слоями HMA, называют промежуточной стрессовоспринимающей мембраной.
2. «Сухой процесс» (Резиномодифицированная смесь).
В этом процессе резиновая крошка смешивается с заполнителем перед введением битума. Как правило, используется крупные фрагменты резины (максимальный размер 1/16"–1/4", или 1,6–6,4 мм) в количестве 3–5% от веса заполнителя. Природный заполнитель обычно имеет гранулометрический состав с промежутками, что позволяет использовать фрагменты резины в качестве заполнителя. Количество резиновой крошки, используемой в сухом процессе, может в 2–4 раза превышать таковое в случае мокрого процесса. Первый «сухой процесс», примененный в США, получил название «PlusRide». Отметим в этой связи имеющиеся данные о том, что из-за повышенной эластичности смеси, модифицированной резиной, с поверхности покрытия, устроенного из такой смеси, легко удаляется лед.
Для получения резинобитумного вяжущего приемлемого качества с применением «мокрого процесса» необходимо определить температуру и время девулканизации для конкретной комбинации битума и резиновой крошки. Вязкость смеси проверяется для различных временн'ых интервалов в ходе процессов смешения и девулканизации. Тот факт, что вязкость установилась на достаточно постоянном уровне, говорит о том, что первичная реакция близка к завершению и что вяжущее готово к использованию. Первичная реакция изучена недостаточно подробно, но, по всей видимости, она связана с химическим и физическим обменом между частицами битума и резины, в ходе которого происходит набухание резины, что приводит к повышению вязкости. При продолжительном смешении битума и резины по завершении исходной реакции может начаться снижение вязкости смеси в связи с разрушением фрагментов резины при перемешивании. Однако этот процесс идет с невысокой скоростью и при высоких температурах может занять несколько часов.
Если резинобитумная смесь оказывается слишком вязкой, то обычно вводится добавка масла-разбавителя. Однако если содержание резиновой крошки составляет менее 10% от веса битума, то такой необходимости не возникает.
Резинобитумную смесь следует использовать по назначению сразу же после завершения первичной реакции, а до этого необходимо обеспечить ее непрерывную рециркуляцию. Смеси дают охладиться в баках-накопителях, после чего повторно нагревают ее перед использованием без каких-либо осложнений.
При использовании резинобитума в качестве вяжущего в HMA применяются следующие диапазоны температур смешения:
§ HMA с непрерывным гранулометрическим составом:
325оF –375oF (163оС –191оС)
§ HMA с прерывистым гранулометрическим составом:
275оF –325оF (135оС –163оС)
При повышении температуры смешения могут усилиться выбросы из дымовых труб. HMA, содержащие резинобитумное вяжущее, нельзя долго хранить в бункере; возможн выпуск смеси через небольшой промежуточный бункер. Не допускается применение дизельного масла в качестве опалубочной смазки для дна и стенок грузовика, так как помимо загрязнения самой HMA это приводит к налипанию смеси ко дну и стенкам. Вместо этого рекомендуется применять известковую воду, мыльный раствор или силиконовую эмульсию.
При укладке смеси необходимо поддерживать ее температуру в заданном диапазоне. Для уплотнения обычно используются статические катки на стальных колесах. Катки с резиновыми шинами захватывают дорожный ковер, а виброкатки отдирают его или вызывают образование сдвигов. Если необходимо открыть дорогу для движения сразу после операции уплотнения, а транспорт имеет тенденцию к захвату дорожного ковра, то по его поверхности рекомендуется рассыпать песок для бетонной смеси из расчета 1–2 фунта на квадратный ярд.
Огромное значение имеет вопрос о пригодности для рециклинга HMA, содержащих резиновую крошку. Его следует решить до начала широкомасштабного использования резиновой крошки, полученной в результате переработки выброшенных шин. В настоящее время (1996 г.) имеется лишь ограниченный опыт рециклинга таких смесей. Однако весьма вероятно, что в будущем при таком рециклинге производственный процесс будет приводить к загрязнению атмосферного воздуха. Что произойдет с резинобитумным вяжущим во время рециклинга? Каким образом следует проектировать смесь для рециклинга? Если эти вопросы не будут решены, рециклинг HMA, содержащих резиновую крошку, может оказаться невозможным. В таком случае проблема удаления РАП (рециклируемого асфальтового покрытия) может оказаться значительно более серьезной, чем проблема утилизации шин.
Следует отметить, что «процесс МакДональда» («мокрый процесс») и «процесс PlusRide» («сухой процесс»), которые обсуждались выше, запатентованы. Однако срок действия оригинального патента на «процесс МакДональда» истек в 1992 г. В последнее время внедряется ряд новейших концепций, таких как универсальный «сухой процесс» (generic dry process), асфальтобетон с фрагментами резины (chunk rubber asphalt concrete) и непрерывно смешиваемый резинобитум (continuously blended asphalt rubber) (45).
При применении универсального «сухого процесса» резиновую крошку можно ввести в заполнитель с «универсальным» гранулометрическим составом (а не с пропуском некоторых фракций, как в случае «PlusRide» системы). Имеются данные об опытном применении универсального «сухого» процесса в полевых условиях в штатах Нью-Йорк, Флорида, Айова, Канзас, Орегон и Иллинойс (45).
Концепция непрерывного смешения резинобитума используется Департаментом транспорта штата Флорида. Это «мокрый» процесс, в котором задействовано 5–15% мелкой резиновой крошки (180 μ, или № 80 меш), что позволяет избежать использования растворных баков и облегчить непрерывное смешение. Для смешения резиновой крошки и битума применяется автономное портативное смесительно-измерительное устройство.
Пластмассы. Как видно из таблицы 7–6, для модификации битумного вяжущего можно применять множество пластических материалов (пластомеров). Конкретную информацию по торговым названиям этих продуктов можно найти в 29. По особенностям своего поведения при различных манипуляциях, хранении и использовании пластические полимеры очень сходны с резиновыми.
Одним из примеров модификаторов битума является полиэтилен высокого давления (ПЭВД) – как новый, так и регенерированный. В этом случае модифицированный вяжущий материал представляет собой двухфазную систему, состоящую из полиэтилена и чистого битума. Содержание полиэтилена, как правило, составляет 4-6% от веса модифицируемого вяжущего. Модифицированный вяжущий материал получают на установке по производству HMA по патентованному способу смешения с высоким усилием сдвига на специальном производственном оборудовании (смонтированном на передвижной смесительной установке). При хранении этот материал следует перемешивать во избежание расслоения и восходящей миграции полиэтилена сквозь жидкий битум. Ввиду того, что модифицированное вяжущее имеет высокую вязкость, смешение и укладку полученной смеси следует производить при температуре на ~35оF выше, чем обычно для немодифицированных HMA. Уплотнение модифицированных HMA при температуре ниже 270оF (132оС), как правило, неэффективно из-за того, что добавленный полиэтилен кристаллизуется ниже этой температуры.
Этилвинилацетат (EVA) поставляется в качестве модификатора битума в виде легкосыпучих таблеток, от полупрозрачных до белых по цвету, в пакетах или навалом. Доза модификатора составляет 2–5% от веса битума. Этилвинилацетат вводят в асфальтоцемент при температурах в диапазоне 300оF –340оF (149оС –171оС). Для эффективного смешения достаточно лишь умеренное перемешивание (например, в аппарате смешения с низким усилием сдвига) или циркуляция. Смеси хранятся без разделения в течение нескольких недель. Для достижения заданных свойств покрытий необходимо, чтобы этилвинилацетат был совместим с чистым битумом.
Комбинированные модификаторы. Путем комбинирования полимеров двух или более разных типов (таких, как резина и пластмассы) можно добиться улучшения эксплуатационных свойств дорожных покрытий из HMA, недостижимого с помощью модификатора только одного типа. Так, например, пластический полимер может повысить сопротивление колееобразованию в летний период, но будет недостаточно эффективно предотвращать температурное растрескивание в холодных погодных условиях. Этот недостаток можно устранить, добавив резиновый полимер к пластическому. Однако если полимеры двух различных типов химически несовместимы, то их комбинация может даже оказаться вредной для покрытия. Поэтому комбинированные модификаторы необходимо тщательно исследовать на предмет возможных негативных побочных эффектов. Кроме того, если затраты, связанные с применением двух и более полимеров окажутся слишком высокими, то от такой комбинации придется отказаться (29).
Волокнистые материалы
Как известно, натуральные волокна, например, такие как асбест, имеют многолетнюю историю применения. Однако после того как выяснилось, что асбест вреден для здоровья человека, в США отказались от его использования. Это послужило стимулом для производства искусственных или синтетических заменителей асбеста. Волокнистые материалы, чаще всего, используются в производстве кровельных или промышленных гидроизоляционных мембранных системах для армирования или придания жесткости конструкциям. Эти материалы могут применяться и для армирования HMA, а также для повышения их прочности на разрыв и усилении когезионных свойств. Введение волокнистых материалов позволяет повысить содержание битума в HMA без его стекания. Это особенно важно в случае укладки смесей для слоев износа с прерывистым гранулометрическим составом заполнителя и щебеночно-мастичных смесей. Из-за высокого содержания битума образуются толстые пленки вяжущего, что способствует повышению долговечности дорожных покрытий. Волокнистые материалы обычно вводят в смеси на установках по производству HMA. Большинство производителей поставляет волокнистые материалы в пакетах из легкоплавких пластиков, так как из-за малых размеров частиц и их тонкого измельчения с ними трудно работать навалом. В случае барабанных смесителей волокна вводятся в барабан с помощью пневматических систем. Производители волокнистых материалов обычно предоставляют подрядчикам, чья деятельность связана с HMA, специальное оборудование (или оказывают иную помощь с оборудованием) для работы конкретно с производимыми ими волокнами. В случае HMA, содержащих волокнистые материалы, могут возникнуть сложности при выглаживании и укладке вручную.
Полипропиленовые волокна длиной около 10 мм используются для армирования асфальтобетона. Как правило, волокна добавляются в количестве 0.3% от общего веса HMA. Удельный вес полипропиленовых волокон приблизительно равен 0,91. Температура HMA не должна превышать 300оF (149оС), а температура заполнителя – 290оF (143оС) –во избежание размягчения или расплавления полипропиленовых волокон. В установке периодического действия хорошая дисперсия волокон обычно достигается после проведения цикла сухого смешения (10 сек) с последующим циклом мокрого смешения (35 сек). Готовую HMA следует проверить на отсутствие скоплений волокон. Если они будут обнаружены, то следует удлинить цикл мокрого смешения, а именно провести несколько дополнительных этапов смешения длительностью 5 сек. каждый до тех пор, пока не будет получена однородная смесь. В случае барабанных смесителей волокнистые материалы доставляются с заданной скоростью транспортерами.
Полиэфирные волокна
|
|
Адаптации растений и животных к жизни в горах: Большое значение для жизни организмов в горах имеют степень расчленения, крутизна и экспозиционные различия склонов...
Своеобразие русской архитектуры: Основной материал – дерево – быстрота постройки, но недолговечность и необходимость деления...
Индивидуальные и групповые автопоилки: для животных. Схемы и конструкции...
Поперечные профили набережных и береговой полосы: На городских территориях берегоукрепление проектируют с учетом технических и экономических требований, но особое значение придают эстетическим...
© cyberpedia.su 2017-2024 - Не является автором материалов. Исключительное право сохранено за автором текста.
Если вы не хотите, чтобы данный материал был у нас на сайте, перейдите по ссылке: Нарушение авторских прав. Мы поможем в написании вашей работы!