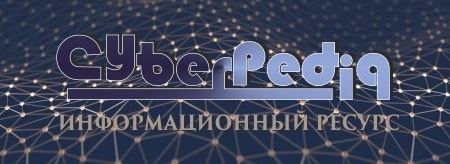
Папиллярные узоры пальцев рук - маркер спортивных способностей: дерматоглифические признаки формируются на 3-5 месяце беременности, не изменяются в течение жизни...
История создания датчика движения: Первый прибор для обнаружения движения был изобретен немецким физиком Генрихом Герцем...
Топ:
Определение места расположения распределительного центра: Фирма реализует продукцию на рынках сбыта и имеет постоянных поставщиков в разных регионах. Увеличение объема продаж...
Организация стока поверхностных вод: Наибольшее количество влаги на земном шаре испаряется с поверхности морей и океанов...
Эволюция кровеносной системы позвоночных животных: Биологическая эволюция – необратимый процесс исторического развития живой природы...
Интересное:
Уполаживание и террасирование склонов: Если глубина оврага более 5 м необходимо устройство берм. Варианты использования оврагов для градостроительных целей...
Искусственное повышение поверхности территории: Варианты искусственного повышения поверхности территории необходимо выбирать на основе анализа следующих характеристик защищаемой территории...
Финансовый рынок и его значение в управлении денежными потоками на современном этапе: любому предприятию для расширения производства и увеличения прибыли нужны...
Дисциплины:
![]() |
![]() |
5.00
из
|
Заказать работу |
|
|
Факторы, которые влияют на максимальную плотность, которой можно достичь конкретным набором катков на рабочем объекте, это характеристики горячей асфальтовой смеси, ее температура при укладке, толщина слоя, температура и твердость основания для укладки смеси, температура воздуха, скорость и влажность воздуха и уровень солнечной радиации. Большинство из этих факторов непосредственно влияют на скорость охлаждения слоя горячей асфальтобетонной смеси и на продолжительность времени, когда смесь остается достаточно горячей для уплотнения. Информация о скорости охлаждения и времени, доступном для уплотнения, обычно представлена или в форме таблицы, или в форме графиков. Таблица 6-4 содержит один набор рекомендованных минимальных укладочных температур для диапазона температуры основания и толщины слоя. Эти температуры уплотнения – лишь предположения, и будут отличаться при различных битумных вяжущих и заполнителях. Эта таблица была составлена для типичных асфальтобетонных смесей, используемых в Соединенных Штатах (14). Заметьте, что для тонкого слоя время доступное для уплотнения меньше. Например, для слоя ¾ дюйма (19мм) который укладывается при минимальной рекомендуемой температуре, есть только 6 минут для уплотнения для достижения желаемой плотности. Скорость катка нельзя увеличить значительно, так как это может негативно отразится на плотности. Поэтому, могут понадобиться дополнительные катки при укладке при низких температурах.
Таблица 6-4. Рекомендуемые минимальные укладочные температуры, ° F (14)
Основание |
Толщина слоя, дюймы
1 Увеличивается на 15°F (8°С) когда укладка производится на основу или подстилающий грунт содержащий замороженную влагу.
|
2 Время доступное для укладки между рекомендуемой укладочной температуро и температурой остановки 175°F (80°С), кода попытки уплотнения смеси должны быть остановлены.
Схемы прокатки
На слоях с постоянным поперечным уклоном используются схемы проходов отличные, от схем для проходов изменяющегося поперечного профиля или виража. При прокатке слоя, неимеющего жеского бокового ограничителя (бордюр, слой старого асфальтобетонного покрытия, с постоянным поперечным уклоном, первый проход катка должен быть по наружной (низкой) кромке слоя, с каждым последующим проходом, продвигающимся выше к верхней кромке слоя, как показано на Рис 6-28. Следующий проход должен перекрывать предыдущий хотя бы на 6 дюймов (150 мм). Проходы катка должны заканчиваться в различных местах, чтобы предотвратить образование бугров. Последний проход прокатка, по верхней кромке, должен перекрывать верхнюю кромку хотя бы на 6 дюймов (150 мм)
Рис. 6-28. Рекомендуемый метод укатки тонки слоев без опоры (<2 дюмов), с постоянным поперечным уклоном (15)
Также важна проходы по поперечным швам, чтобы убедиться что соединения плотные и гладкие. Если возможно, поперечные швы должны прокатываться в поперечном направлении. Для этого требуется, чтобы использовались доски ограничивающих горячую АБС, чтобы не допустить разрушение кромки. Доски должны быть такой же ширины как и уложенная асфальтобетонная смесь. Очень часто, из соображений дорожного движения и рабочего пространства, поперечные швы должны прокатываться в продольном направлении, в таком случае нет необходимости в использовании досок. При прокатке в продольном направлении, слой горячего асфальта имеет тенденцию отталкиваться от холодной асфальтовой смеси, что приводит к появлению впадин.
|
Продольные швы важны, из-за их распространенности в большинстве укладочных проектов. Важно чтобы продольные швы были правильно уплотнены, чтобы убедиться, что соединения были гладкие и практически незаметные при пересечении. Если продольные швы уплотнены неправильно, соединения могут вызывать тряску и шум при их пересечении, это может стать потенциальным местом будущего размыва или расслоения, что в свою очередь может стать опасностью при вождении. Продольные швы уплотняются, используя катки доступные для уплотнения других частей горячей асфальтовой смеси.
Существуют несколько подходов для уплотнения соприкасающихся продольных швов. При укладки двухлинейного полотна, продольные швы можно эффективно исключить с помощью укладки эшелоном (второй укладчик работает сразу за первым). Длина некоторых проектов достаточно короткая, чтобы укладчик поместил вторую линию асфальта пред тем как остынет первая линия. Когда обе стороны продольного шва горячие, с уплотнением шва не возникает проблем.
Обычный метод уплотнения продольных швов состоит из укладки второго горячего полотно прилегающим (2 –3 дюйма (51 – 76 мм) с перекрытием к первой полосе, после того как последняя остыла. Однако, используя этот метод, трудно получить высокую плотность в соединении. Другой метод заключается в нагреве холодного слоя прилегающего к соединению с помощью разогревателя швов, пред укладкой слоя горячего асфальтобетона. Опыт показывает смешанные результаты от использования этого метода, как плохие, так и хорошие. И окончательный метод, который иногда используется на летном поле и на других широких дорожных покрытиях, заключается в отрезке 2 –3 дюймов (51 – 76 мм) холодного полотна, примыкающего к кромке, с помощью нарезчика швов, чтобы оголить чистый, плотный, вертикальный край. Примыкающая линия укладывается, перекрывая обрезанный край на 2 –3 дюйма (51 – 76 мм). Эта техника показывает хорошую плотность, но может быть непрактичной на многих магистралях, где дорожное движение продолжается по примыкающей линии.
Уплотнение продольных швов выполняется, используя много различных техник. Однако почти все методы включают в себя сначала уплотнение шва, затем продвижение в противоположную сторону уплотняемого полотна и возврат обратно в сторону шва. При уплотнении продольных швов с помощью вибрационного катка, следует быть очень осторожным, чтобы вибрация не разрушила материал с холодной стороны шва. Разрушение материала с холодной стороны шва зависит от типа заполнителя в асфальтобетонной смеси и температуры холодной стороны во время уплотнения. Важно чтобы вибрационный каток не привел к появлению трещин в заполнителе или асфальтобетонной смеси.
|
Когда каток меняет направление движения, он должен остановиться, прежде чем поменять направление. Важно каким образом происходит эта остановка,. Остановка должна выполняться постепенно и каток должен поворачивать медленно, чтобы во время остановки колеса не были под прямым углом к направлению движения. Это может быть трудно выполнить для пневмоколёсного дорожного катка, но будет возможным, если проникновение шин в материал минимальное. Оператор катка должен особенно позаботиться, чтобы уменьшить образование царапин и ухабов на горячей асфальтобетонной смеси, когда каток меняет направление движения. Если каток остановится, с колесами под прямым углом к направлению движения, и появятся следы от катка, потом очень трудно от них избавиться. Однако, следы, которые косые к направлению укатки можно удалить более просто и их более трудно ощутит при проезде в автомобиле. Вибрационные катки современной конструкции оборудованы регулируемыми настройками включения – выключения скорости движения, которые автоматически отключают вибрацию и снова ее включают, когда каток меняет направление движения. Следует избегать ставить каток на стоянку на свежем полотне, так как это может вызвать появление впадин. Лучше, чтобы каток продолжал работать, но если он вынужден стоять в течении продолжительного времени, его следует оставить на холодном покрытии или настолько далеко от свежего покрытия, насколько это возможно.
Когда уплотнение завершено, следует провести визуальную проверку, чтобы определить состояние только уплотненной поверхности. На ней не должно быть следов от катка, которые не были убраны при чистовом прокатывании. Там не должно быть нероаностей на поверхности либо в продольном, либо в поперечном направлениях. Текстура поверхности должна быть равномерной и без трещин.
|
Большинство региональных отделений Министерства Транспорта требуют, чтобы профиль поверхности проверялся с помощью разравнивающей рейки определенной длины, обычно 10 футов (3.0 м). Замечается степень отклонения профиля полотна дороги от рейки и сравнивается со спецификациями. Обычно максимальное разрешаемое отклонение составляет 1/8 дюйма (3.2мм) для длины в 10 футов (3.0 м). Разравнивающая рейка также используется для проверки всех поперечных швов и других видимых нарушений поверхности. Ее помещают на поверхность параллельно центральной линии, измеряется максимальное отклонение между поверхностью дороги и нижней части рейки.
Большинство штатов проверяет окончательное качество поверхности, проверяя гладкость дороги во время движения по ней с заданной скоростью. В некоторых штатах степень гладкости, это субъективная величина, определяемая инспектором или инженером. В других штатах гладкость определяется с использованием некоего типа устройства для измерения гладкости дороги, например профилометр или роадметр (roadmeter) (Глава 8). Если дорога слишком неровная, гладкость улучшается посредством фрезерованияя высоких участков.
Типы ТУ по плотности, используемые для изготовления горячих асфальтобетонных смесей.
Количество пустот в горячей асфальтобетонной смеси, это возможно единственный наиболее важный фактор, отражающийся на работе смеси за весь ее эксплуатационный период. Для заданного гранулометрического состава заполнителя, пустоты прежде всего зависят от содержания битума, уплотняющего усилия во время уплотнения и дополнительного уплотнения во время дорожного движения. Требования по плотности и методы ее измерения значительно отличаются от одной компании к другой. Некоторые компании выстраивают контрольную полосу для испытания, измеряют ее плотность и используют измеренную плотность как эталон для всего проекта. Другие компании уплотняют образцы в передвижных лабораториях, во время подбора конструкции дорожного полотна, и используют эту плотность или некоторый процент от нее, как целевую плотность. Иные компании измеряют теоретически максимальную плотность (ASTM D2041) и используют некоторый процент от нее как целевую плотность. Все эти техники успешно использовались при строительстве дорожных покрытий, которые работали удовлетворительно; однако, все ими также злоупотребляли, производя дорожное покрытие, которое не показало удовлетворительные эксплуатационные характеристики.
|
Одна трудность в подготовке плотностных спецификаций, это описание методов их измерения. Существуют два главных метода измерений плотности: (1) забирается керн из рабочего покрытия и затем измеряется его плотность в лабораторных условиях; (2) используется радиоизотопный плотномер для измерения плотности на месте. Большинство инженеров согласно, что радиоизотопный плотномер не измеряет плотность настолько аккуратно, как это делает испытание керна в лаборатории. Многие компании используют плотномеры для разработки схемы уплотнения, но уточняют что необходимо забирать образцы из реального покрытия для испытаний на плотность с последующим принятием или утвержением. Однако некоторые компании верят, что правильно откалиброванний и правильно используемый радиоизотопный плотномер может предоставить достаточно точные результаты, чтобы их можно было принять в качестве проверочных. Некоторые керны следует регулярно изымать из покрытия, чтобы убедиться, что плотномер правильно откалиброван.
Пустоты в асфальтобетонных смесях непосредственно соотносятся с плотностью, поэтому плотность должна строго контролироваться, чтобы убедиться что начальное содержание воздушных пустот в смеси в пределах допустимого диапазона. Существует большое количество доказательных данных, показывающих, что начальное содержание воздушных пустот в уложенном твердом асфальтобетонном покрытии, должно быть не больше 8 процентов и никогда не падать ниже 3 процентов за все время эксплуатации покрытия (16, 17, 18, 19, 20, 21). Высокое содержание пустот позволяет воде и воздуху проникать в структуру покрытия, что приводит к размыву, окислению, расслоению и растрескиванию. Низкое содержание пустот приводит к колееобразованию и появлению ухабов. Этот рекомендованный диапазон пустот в дорожном покрытии применим только к плотным асфальтобетонным смесям. Другие смеси, которые специально разработаны с высоким или низким содержанием воздушных пустот, могут работать правильно, когда конструкция использует правильные технологии.
В исследованиях для штата Арканзас Форд (Ford) показал, что горячие асфальтобетонные смеси должны разрабатываться и изготавливаться таким образом, чтобы содержание пустот в покрытии оставалось выше 2.5 процентов. Основываясь на воздушных пустотах, определенных из испытания кернов и глубины колеи измеренной в покрытиях находящихся в эксплуатации, данные Форда показывают, что с уровнем содержания пустот выше 2.5 процентов ожидаемая глубина колеи должна быть менее 10/32 дюйма (7.9 мм) (Рис 6-29).
Браун (Brown) и Кросс (Cross) показали, что значительное колееобразование произойдет в смеси, если при лабораторном уплотнении в ней 3 или менее процента воздушных пустот. Когда использовался подходящий заполнитель, и содержание воздушных пустот оставалось выше 3 процентов, наблюдалось очень небольшое колееобразование. Хубер (Huber) (18) в изучении асфальтобетонных дорожных покрытий в Канаде, рассмотрел определенное количество причин колееобразования и пришел к выводу, что одна из главных причин, это содержание воздушных пустот ниже 3 процентов.
Зьюб (Zube) показал, что плотным асфальтобетонные покрытия стали более доступны проникновению воды при воздушных пустотах в них более 8 процентов. Рис 6-30 показывает, что пока содержание воздушных пустот ниже 8 процентов, водопроницаемость не должна быть проблемой. Но проницаемость быстро увеличивается, когда уровень содержания воздушных пустот превышает 8 процентов. Браун, Коллинс (Collins) и Браунфилд (Brownfield), в изучении отделенных в штате Джоржия, также показали, что асальтобетонные смеси остаются недоступны проникновению воды, пока содержание воздушных пустот в них оставалось ниже примерно 8 процентов. Рис 6-31 показывает что проникаемость быстро увеличивается, когда содержание воздушных пустот выше 8 процентов.
Рис 6-29. Отношение между воздушными пустотами и глубиной колеи в Арканзасе (16)
Рис 6-30. Зависимость Проницаемости от объема воздушных пустот для 10 проектов в Калифорнии (19)
Рис 6-31. Зависимость Проницаемости от объема воздушных пустот для дорожного покрытия в Джорджии (19)
Сантуччи (Santucci) (21) показал, что остаточное проникновение битумного вяжущего зависит от содержания воздушных пустот в асфальтобетонной покрытии. Рис 6-32 показывает, что потеря проникающей способности асфальтового вяжущего сильно увеличивается когда содержание воздушных пустот выше 8 процентов. Поэтому, если плотные асфальтобетонные смеси изготавливаются с содержанием воздушных пустот ниже 8 процентов, избегается быстрое окисление, которое приводить к растрескиванию и расслоению и приводит к несоответствующим эксплуатационным характеристикам.
Из результатов описанных исследований можно заключить: что плотные асфальтобетонные смеси должны изготавливаться с начальным содержание воздушных пустот ниже примерно 8 процентов; и что окончательное содержание воздушных пустот, после воздействия дорожного движения, должно быть выше примерно 3 процентов. Покрытие должно показать хорошие эксплуатационные характеристики, если находиться в этом диапазоне и используется подходящий заполнитель и битумное вяжущее.
Рис 6-32. Зависимость остаточного проникновения от воздушных пустот (21)
Требуемая плотность, как процент от лабораторной плотности. Один метод для определения плотности покрытия требует, чтобы материал до уплотнения на месте проведения работ, уплотнялся до определенного процента в лабораторных условиях. Метод Маршалла определяет, чтобы лабораторные образцы уплотнялись использованием или 50, или 75 ударов молота Маршалла. За последние годы, большинству штатов требуется 75 ударов для дорог с интенсивным дорожным движением. Обычно плотностные спецификации требуют, чтобы плотность покрытия была по крайней мере 95 процентов от лабораторной плотности и в некоторых случаях, по крайней мере 98 процентов. Некоторые спецификации запрещают плотность дорожного покрытия больше 100 процентов от лабораторной плотности, из-за возможного преждевременного колееобразования, как результат низкого содержания воздушных пустот.
Чтобы эти спецификации работали эффективно, необходимы несколько вещей. Первое, это материал, изготовленный на асфальтобетонном заводе, должен быть уплотнен в лабораторных условиях, чтобы установить оптимальную плотность и оценить количество воздушных пустот в смеси при данной плотности. Если содержание воздушных пустот в материале, уплотненном в лабораторных условиях, неудовлетворительное, смесь должна быть скорректирована таким образом, чтобы получить необходимое содержание воздушных пустот. Часто единственное изменение, которое необходимо сделать, это небольшое изменение содержания битума. Плотность получаемая при разработке конструкции смеси, нельзя брать за образец, так как обычно материалы изготовленные в лаборатории, так или иначе, отличаются от материалов производимых на заводе. Заполнитель имеет склонность к разрушению во время изготовления смеси, увеличивая содержание пыли и таким образом изменяя параметры уплотненной асфальтобетонной смеси. Из-за обычного выборочного контроля и ошибок тестирования перед началом и во время проектирования смеси, материал изготовленный на заводе, может отличаться от снабжаемого для разработки конструкции смеси.
В развитии метода Маршалла, при использовании ручного молота Маршалла полученная плотность коррелировала с плотностью дорожного покрытия после воздействия дорожного движения (22). Поэтому любой другой метод уплотнения (механический или другой) должен быть откалиброван, чтобы производить уплотнение равное полученному с помощью ручного молота Маршалла или что еще лучше, должен быть откалиброван чтобы производить плотность, которую покрытие получает после нескольких лет дорожного движения. Процедуры описанные в ASTM D1559 и AASHTO T245 для теста Маршалла, требуют чтобы использовался ручной молот Маршалла или чтобы был окалиброван выбранный метод уплотнения. Это позволит достичь той же плотности, как при помощи ручного молота.
Предположим, смесь рассчитана иметь 4 процента пустот и необходимое уплотнение должно составлять, по крайней мере, 95 процентов лабораторной плотности. Это требование выльется в содержание пустот до 9 процентов (4 процента при 100% лабораторной плотности плюс еще 5 процентов при 95% лабораторной плотности) сразу после уплотнения, и должно уменьшиться до примерно 4процентов после нескольких лет дорожного движения. Начальный объем воздушных пустот (9процентов) может быть немного высок, но конечное содержание пустот (4 процента) должно быть приемлемым. Начальное, высокое содержание воздушных пустот может привести к быстрому окислению и как результат, увеличению растрескивания и расслоения. Если эта смесь является объектом воздействия большого объема дорожного движения, тогда это приведет к возникновению небольшой колеи (5 процентов от толщины слоя, 0.10 дюйма (2.5 мм) для 2-х дюймового (51 мм) слоя) на месте прохода шин. Эта 0.10 дюйма (2.5 мм) колея, сама по себе незначительна и вызывается уплотнением от дорожного движения.
Если смесь должна иметь 4 процента воздушных пустот и уплотнена до плотности большей чем 100 процентов, колееобразование может проявиться раньше, так как во время эксплуатации дорожного покрытия, начальное содержание воздушных пустот в смеси после уплотнения меньше 4 процентов. Если для получения соответствующей плотности после нескольких лет дорожного движения достаточно применения лабораторного уплотнительного усилия, тогда как показал опыт, подрядчик не сможет уплотнить смесь до плотности выше, чем достигнутая во время лабораторных испытаний. Так, если плотность в любом проекте постоянно приближается или превосходит 100 процентов лабораторной плотности, тогда возможно, что эталонная лабораторная плотность низкая или на месте применяется слишком сильное уплотняющее усилие.
Эта техника оценки результата уплотнения дорожного покрытия будет находиться в хорошей взаимосвязи с правильно сконструированными смесями если: 1) лабораторные образцы уплотнены во время изготовления для установления образцовой плотности; 2) для уплотнения лабораторных образцов использовалась правильная техника уплотнения; 3) установлены минимальные требования по уплотнению, чтобы убедиться что содержание воздушных пустот в дорожном полотне будет не более 8 процентов.
Требования к плотности как проценту от теоретической максимальной плотности. Второй метод контроля плотности при уплотнении требует, чтобы подрядчик достиг некоего минимального процента от теоретической максимальной плотности (ТМП). Эти требования по уплотнению предоставляют непосредственный метод для спецификации воздушных пустот на месте проведения работ и косвенный метод контроля уплотнения. Этот метод включает в себя забор образца асфальтовой смеси во время изготовления и проведение испытаний для измерения ТМП (ASTM D2041). Объемная плотность асфальтовой смеси измеряется после уплотнения уложенной смеси и сравнивается с ТМП.
Этот тип спецификации уплотнения требует, чтобы ТМП, которая является образцовой плотностью, измерялась регулярно во время конструкции дорожного покрытия. ТМП измеренная во время проектирования смеси должна стать отправной точкой для конструкции, но не должна использоваться как образцовая плотность для реально изготовленного материала.
Некоторые страны, во время конструкции покрытия, не уплотняют образцы дорожной одежды в лаборатории. Некоторые специалисты верят, что в лабораторном уплотнении образцов нет необходимости, так как образцовая плотность основывается на ТМП, которая определяется без уплотняемых образцов. Образцы горячей асфальтобетонной смеси должны забираться во время конструкции и должны уплотняться в лаборатории для контроля над процессом укладки и для проверки удовлетворительного содержания воздушных пустот в смеси. Пустоты в образцах, уплотненных в лабораторных условиях, должны измеряться и оцениваться для определения содержания пустот в дорожном покрытии после дорожного движения. Нежелательно строить покрытие с изначальным содержанием воздушных пустот 7 – 8 процентов, если после летнего сезона дорожного движения, их содержание уменьшиться на 1–2 процента. Единственный способ оценить окончательное содержание пустот в полотне (что является наиболее важным параметром асфальтобетонной смеси), это уплотнять образцы в лаборатории, используя специфицированную технику лабораторного уплотнения (руководство или эквивалент) и затем измерять пустоты. Если содержание пустот на неприемлемом уровне (обычно около 4 процентов), тогда смесь должна быть модифицирована, чтобы достичь желаемого содержания пустот.
Этот тип спецификаций плотности часто неправильно использовался из-за перестраховки в достижении необходимого процента ТМП. Увеличенное содержание битума заполняет пустоты, что создает впечатление, что необходимое уплотнение достигнуто. При этом низкое содержание пустот в полотне достигается, но не за счет уплотнения. Содержание пустот будет продолжать уменьшаться под воздействием дорожного движения, пока не упадет ниже 3 процентов. После чего, вполне возможно, разовьется колееобразование из-за пластической деформации асфальтобетонной смеси. Содержание битума часто увеличивается при укладке в холодную погоду или при других условиях, когда трудно достичь необходимой плотности. Если, во время конструкции в холодную погоду или в другое время, содержание пустот высокое, прежде чем пытаться модифицировать конструкцию смеси, требуется приложение дополнительного уплотняющего усилия или улучшенный план прокатки.
Поэтому, этот метод спецификации плотности не приветствует добавление дополнительного количества битумного вяжущего и наполнителя, чтобы сделать плотность покрытия легко достижимой, если плотность является главным критерием для принятия дорожного покрытия(23). Лабораторные испытания на уплотнение должны выполняться во время конструкции, чтобы убедиться, что пустоты в образцах, сжатых в лабораторных условиях поддерживаются на приемлемом уровне. ТМП должна регулярно измеряться на укладываемом материале, чтобы получить правильную ТМП для сравнения с плотностью в укладываемом полотне. Не следует добавлять дополнительное битумное вяжущее только ради уменьшения содержания воздушных пустот в дорожном покрытии, чтобы это соответствовало требованиям по плотности. Содержание битума в смеси должно меняться только для улучшения параметров (прежде всего пустот) смесей, испытываемых в лаборатории.
Требования к плотности как проценту как к проценту от контрольной полосы. Третий метод, который используется для спецификации плотности, это сравнение объёмной плотности контрольной полосы, укладываемой асфальтобетонной смеси, с объёмной плотностью контрольной полосы, которая создана, используя выбранные процедуры уплотнения. Большинство спецификаций, которые используют метод контрольной полосы, требуют, чтобы контрольная полоса была уплотнена до некоего минимального процента плотности от плотности лабораторной конструкции или от минимального процента ТМП. Если спецификации не требуют некой минимальной плотности для контрольной полосы, тогда инспектор должен тщательно оценить уплотнительное оборудование процедуры прокатки, чтобы убедиться что к асфальтобетонной смеси применяется разумное уплотнительное усилие. Любые значительные изменения в смеси во время конструкции требуют, чтобы новая контрольная полоса была изготовлена и оценена.
Этот метод контроля плотности позволяет оценить уплотняемость смеси и включается как часть обязательных спецификаций. Отслеживание плотности с помощью радиоизотопного плотномера предоставляет информацию, необходимую для того, чтобы знать когда была достигнута максимальная плотность для используемых катков. Если эта максимальная плотность ниже, чем желаемая, возможно необходимо увеличить размер катков или улучшить технику прокатки. На плотность влияют большое количество факторов, и изменение любого из них может сделать испытание полосы неэффективным. Обычные факторы, влияющие на плотность, это гранулометрический состав заполнителя (особенно процент прохода через сито номер 200), содержание битума, содержание влаги, температура смеси, температура воздуха, толщина слоя, твердость нижележащего слоя, вес катка, способ прокатки, скорость катка и т.д.
Типичная спецификация полосы контроля требует некоторой минимальной плотности для полосы контроля. Оставшаяся часть конструкции должна достигнуть некоторого минимального процента плотности полосы контроля. Эта спецификация может быть сделана более простой, если уплотненная смесь будет соответствовать некоторому проценту от лабораторной плотности или ТМП. Контрольная полоса может быть изготовлена, чтобы гарантировать, что указанная плотность достижима, и разработаны соответствующие типы прокатки. Например: предположим, что спецификация требует, чтобы контрольная полоса имела плотность, по крайней мере 94 процента от ТМП, и чтобы все горячие асфальтобетонной смеси, помещенные после изготовления контрольной полосы, имели плотность по крайней мере 98 процентов контрольной полосы. Эта спецификация могла быть сделана более простой, если укладываемая смесь, была уплотнена до минимальной плотности 92 процента от ТМП, так как оба этих примера пришли к одинаковым требованиям по уплотнению (0.94 x 0.98 = 0.92).
Метод контрольной полосы для спецификации плотности может использоваться для получения удовлетворительных результатов. Однако спецификации должны быть написаны так, чтобы начальное содержание пустот в горячей асфальтобетонной смеси укладываемого полотна не превысили приблизительно 8 процентов, и объем пустот в полотне после дорожного движения не упадет ниже приблизительно 3 процентов. Чтобы гарантировать, что содержание пустот никогда не упадет ниже 3 процентов, лабораторные образцы должны уплотняться в течение строительства, для оценки содержания воздушных пустот после воздействия дорожного движения.
Измерение плотности
Метод испытания керна. Метод измерения плотности керна, это контрольная процедура, которая является стандартом и с которым сравнивается показания радиоизотопного плотномера. Требования, чтобы плотность измерялась испытанием керна, вызывает задержку между завершением уплотнения и определения результатов измерения плотности, так как дорожное покрытие должно охладиться прежде, чем образцы смеси могут быть взяты и затем высушены, чтобы получить сухой вес. В большинстве случаев при использовании метод испытания керна, результаты по плотности получаются на следующий день после завершения конструкции дорожного полотна.
После вырезания керна из слоя дорожного покрытия, недавно уложенный материал должен быть отделен от нижележащего, прикрепленного материала. В некоторых случаях бумага или другой материал укладывается на существующую поверхность перед укладыванием горячей асфальтобетонной смеси, чтобы предотвратить ее скрепление с нижележащим слоем. Когда это сделано, керн может быть легко отделен. Однако был изъят в правильном месте. Есть некоторые проблемы в использовании бумаги или другого материала как разрушающего сцепление, поскольку есть некоторое сомнение, что над этим материалом, измеряемая плотность асфальтовой смеси может быть более низкой.
Метод чаще всего используемый для получения образцов, это произвольно определить места изъятия образцов, вырезать керн на полную глубину дорожного асфальтового покрытия, и отпилить или как либо иначе отделить испытываемый слой от нижележащего материала. Этот метод, как полагают, является самым подходящим для оценки общей плотности дорожного покрытия.
Бурати (Burati) и Элзогби (Elzoghbi) (24) показали, что изменчивость результатов испытания на плотность была ниже в измерениях с кернами, чем с помощью радиоизотопного плотномера
. Их исследование включало использование радиоизотопных плотномеров, изготовленных тремя различными производителями, которые использовались на двух строительных проектах. Они обнаружили, что было статистически существенное различие в средней плотности, измеренной через керны и с помощью радиоизотопного плотномера.
Метод радиоизотопного плотномера. Радиоизотопные плотномеры использовались в течение множества лет для измерения объёмной плотности горячих асфальтобетонных смесей. Эта техника имеет то преимущество, что результаты могут быть определены быстро и без разрушения дорожного покрытия.
Большинство радиоизотопных плотномеров измеряет плотность горячих асфальтобетонных смесей в режиме обратнорассеянного излучения. Плотномер помещается на выбранном месте на поверхности дорожного покрытия, и производяться измерения. Плотность, определенная по показаниям плотномера, представляет среднюю плотность нескольких верхних дюймов дорожного покрытия. Например, средняя плотность может быть представительной для верхних 6 дюймов (150 мм) дорожного покрытия, однако, толщина слоя представляющего интерес, может быть только 2 дюйма (51 мм). Один способ устранять эффект нижележащих слоев, это откалибровать радиоизотопный плотномер, чтобы получить ту же самую плотность, как и полученную из испытаний изъятых в этом месте сердечников. Эта калибровка корректируется для учета плотности нижележащего материала. Даже с этой калибровкой, ошибки все же существуют из-за изменений в толщине слоя и изменениях в плотности нижележащих слоев вдоль проекта.
В последние годы, был разработан радиоизотопный плотномер, который измеряет плотность тонких слоев. Этот новый плотномер должен обеспечить большую точность в измерении плотности в сравнении с предыдущими. Однако, общая точность этих плотномеров не известна.
Лучшее использование радиоизотопных плотномеров, это в разработке методов прокатки через быстрый контроль изменений в уплотнении горячих асфальтобетонных материалов. Некоторые радиоизотопные плотномеры были присоединены к каткам, для непрерывно измерения плотность во времяосуществления прокатки. Используемый регулярно, радиоизотопный плотномер может быть ценным инструментом проверки качества. Из-за возможности ошибок при использовании радиоизотопных плотномеров, не рекомендуется, чтобы в приёмочных испытаних использовались только эти приборы, даже при ежедневной калибровки прибора. Некоторые сердечники должны регулярно изыматься, чтобы проверять точность радиоизотопного плотномера и гарантировать, что получена приемлемая плотность.
|
|
Автоматическое растормаживание колес: Тормозные устройства колес предназначены для уменьшения длины пробега и улучшения маневрирования ВС при...
Опора деревянной одностоечной и способы укрепление угловых опор: Опоры ВЛ - конструкции, предназначенные для поддерживания проводов на необходимой высоте над землей, водой...
Особенности сооружения опор в сложных условиях: Сооружение ВЛ в районах с суровыми климатическими и тяжелыми геологическими условиями...
Эмиссия газов от очистных сооружений канализации: В последние годы внимание мирового сообщества сосредоточено на экологических проблемах...
© cyberpedia.su 2017-2024 - Не является автором материалов. Исключительное право сохранено за автором текста.
Если вы не хотите, чтобы данный материал был у нас на сайте, перейдите по ссылке: Нарушение авторских прав. Мы поможем в написании вашей работы!