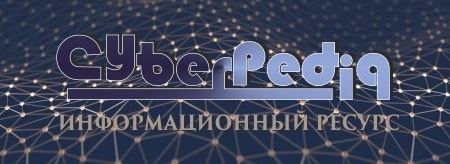
Наброски и зарисовки растений, плодов, цветов: Освоить конструктивное построение структуры дерева через зарисовки отдельных деревьев, группы деревьев...
Типы сооружений для обработки осадков: Септиками называются сооружения, в которых одновременно происходят осветление сточной жидкости...
Топ:
Генеалогическое древо Султанов Османской империи: Османские правители, вначале, будучи еще бейлербеями Анатолии, женились на дочерях византийских императоров...
Установка замедленного коксования: Чем выше температура и ниже давление, тем место разрыва углеродной цепи всё больше смещается к её концу и значительно возрастает...
Характеристика АТП и сварочно-жестяницкого участка: Транспорт в настоящее время является одной из важнейших отраслей народного...
Интересное:
Берегоукрепление оползневых склонов: На прибрежных склонах основной причиной развития оползневых процессов является подмыв водами рек естественных склонов...
Инженерная защита территорий, зданий и сооружений от опасных геологических процессов: Изучение оползневых явлений, оценка устойчивости склонов и проектирование противооползневых сооружений — актуальнейшие задачи, стоящие перед отечественными...
Подходы к решению темы фильма: Существует три основных типа исторического фильма, имеющих между собой много общего...
Дисциплины:
![]() |
![]() |
5.00
из
|
Заказать работу |
|
|
Процесс коррозии определяется целым рядом внутренних и внешних факторов.
Внутренние факторы характеризуют влияние природы металла на вид и скорость коррозии. К ним относятся:
1. Активность металла. Чем более химически или электрохимически активен металл, тем быстрее он разрушается.
2. Состав и структура металла;
3. Состояние поверхности металла:
а) степень ее шероховатости – в целом, чем более гладкой является поверхность металла, тем ниже скорость его коррозии, поскольку различные щели, зазоры, углубления являются потенциальными центрами образования коррозии;
б) наличие на поверхности пленок влаги;
в) наличие на поверхности металла продуктов коррозии, свойства и структура этих пленок. Оксидные, гидроксидные и солевые пленки, образующиеся на поверхности металла, в целом обладают защитным действием, которое зависит от следующих свойств:
Химический характер защитных оксидных и гидроксидных пленок на поверхности металла: если они кислотные, то металл будет разрушаться в щелочных средах; если они основные, то металл неустойчив в кислых средах. Амфотерные пленки защищают металл только в нейтральной среде.
Растворимость пленок. Пленки могут быть химически инертными по отношению к окружающей среде, но при этом растворяются в воде. В этом случае их защитное действие не проявляется.
Толщина, эластичность и рыхлость пленок. Чем толще и чем эластичнее пленка, тем меньше возможность образования в ней трещин, открывающих для металла контакт с окружающей средой.
4. Температура металла.
Внешние факторы определяют влияние состава коррозионной среды и условий протекания коррозии. К ним относятся:
1. Концентрация коррозионно-агрессивных веществ (КАВ) в окружающей среде;
|
2. Состав и свойства КАВ;
3. Скорость движения коррозионной среды, которая определяет интенсивность подвода КАВ к поверхности металла и отвода от нее продуктов коррозии;
4. Температура окружающей среды. Как правило, с повышением температуры скорость коррозии возрастает. Это связано с термическим разрушением защитных пленок.
5. Давление (в случае газовой коррозии);
6. Неодинаковая аэрация, обусловленная неодинаковой концентра-цией кислорода в разных областях окружающей среды, контактируюшей с металлом.
Для определения скорости коррозии обычно ведут наблюдения за изменением во времени какой-либо характеристики, объективно отражающей изменение того или иного свойства металла. Чаще всего используют следующие показатели скорости коррозии:
1. Показатель изменения массы. Это изменение массы образца Dm в результате коррозии, отнесенный к единице поверхности металла S и единице времени t:
К = Dm/S . t, г/м2.ч.
В зависимости от условий коррозии различают:
а) отрицательный показатель изменения массы, в котором учитывают убыль массы металла за время коррозии после удаления продуктов коррозии;
б) положительный показатель изменения массы, в котором учитывают увеличение массы металла за время коррозии вследствие роста пленки продуктов коррозии.
2. Объемный показатель коррозии. Это объем газа V, поглощенного или выделившегося в процессе коррозии, отнесенный к единице поверхности металла S и единице времени t:
К= V/ S . t, см3/см2. ч.
В случае ЭХК учитываются кислородный и водородный показатели (см. лекцию по ЭХК).
3. Показатель сопротивления. Это изменение электрического сопротивления образца металла за определенное время коррозионных испытаний:
КR = (R/Ro) . 100 %,
где Ro и R – электрическое сопротивление образца соответственно до и после коррозии.
Этим методом чаще всего определяют удельное сопротивление, т.е. изменение электрического сопротивления на единицу площади образца при его длине, равной 1. Наиболее точные данные получают для проволочных образцов, для сварных соединений метод не пригоден.
|
4. Механический показатель коррозии. Это изменение какого-либо механического свойства металла, например предела прочности, за время коррозии. Сравнительно часто пользуются изменением предела прочности.
5. Глубинный показатель коррозии. Это глубина разрушения металла в единицу времени, например, мм/год. Глубинный показатель используется для характеристики как равномерной, так и неравномерной коррозии.
Все эти показатели учитываются еще на стадии проектирования.
В целях снижения возможного коррозионного ущерба на стадиях проектирования и производства аппаратуры, оборудования, трубопроводов и т.п.:
1) проводят детальный анализ характера и свойств окружающей среды, условий технологического процесса, в которых будет эксплуатироваться данное изделие;
2) повышают степень обработки поверхности металла;
3) уменьшают площадь контакта деталей, изготовленных из разных металлов;
4) при конструировании сварных узлов и деталей не допускают создания возможных центров коррозии: избегают скопления швов и образования прерывистых швов, исключают точечную сварку и т.п.
Химическая коррозия
ХК – это взаимодействие металлической поверхности с окружающей средой, не сопровождающееся возникновением электрохимических (электродных) процессов на границе фаз. Это обычная гетерогенная ОВР с участием металла и окислителя из окружающей среды. Она может протекать в любых средах и возникновением электрического тока не сопровождается. Этот вид коррозии протекает в основном равномерно по всей поверхности металла. В связи с этим ХК менее опасна, чем ЭХК. Примерами ХК служат ржавление железа и покрытие бронзы патиной. В промышленных условиях металлы нередко нагреваются до высоких температур, что способствует ускорению ХК.
Механизм химической коррозии включает реактивную диффузию атомов или ионов металла сквозь постепенно утолщающуюся пленку продуктов коррозии в окружающую среду и встречную диффузию атомов или ионов окислителя. Этот процесс имеет ионно-электронный механизм, аналогичный процессам электропроводности в ионных кристаллах.
По типу агрессивной среды ХК делится на газовую коррозию (ГК) и коррозию в жидких неэлектролитах (КЖН).
|
1.5.1 Газовая коррозия.(ГК)
ГК проходит в среде сухих газов и паров, т.е. без конденсации влаги на поверхности металла, обычно при высоких температурах. Она наблюдается при плавлении и термической обработке металлов, при эксплуатации газовых турбин, химических аппаратов, двигателей внутреннего сгорания и других металлических изделий, на внутренних стенках оборудования для хранения и транспортировки природных газов и в процессах их химической переработки. В связи с этим газовая коррозия наносит большой ущерб в различных отраслях, в первую очередь металлургической, нефтегазовой и химической промышленности.
ГК может протекать в воздухе, в атмосфере водорода, водяных паров, метана и других углеводородов, оксидов углерода и серы, сероводорода, галогенов и их соединений. Наиболее часто на практике встречается газовая коррозия при окислении металлов О2, SO2, H2S, Cl2, НСl, NO3, CO2, CO и H2. При этом образуются соответствующие оксиды, хлориды, нитриды, сульфиды, карбонаты металлов.
Примеры таких реакций:
2Fe + O2 = 2FeO;
Zn + CO2 = ZnO + CO;
Al + H2O = Al2O3 + H2;
3Ni + SO2 = 2NiO + NiS;
Fe + Cl2 → FeCl2 или FeCl3
Самым распространенным окислителем является кислород. Типичным продуктом кислородной ГК является окалина, которая в виде пленки возникает на раскаленных кусках металла при их прокатке.
Скорость газовой коррозии с участием кислорода обычно выражают через скорость роста оксидной пленки:
Vгк = dх/dτ,
где х – толщина оксидной пленки; τ – время окисления металла.
Толщина пленки может быть самой различной. Она зависит от сплошности первично образующейся пленки, которая определяет способность этой пленки тормозить дальнейшее окисление металла. Если объем получаемого оксида Voкс меньше объема металла Vмет (Voкс/Vмет <1), то образуется несплошная пористая пленка, обладающая низкими защитными свойствами. Если же Voкс/Vмет <1, то образуются сплошные пленки, защищающие металл от коррозии.
Наиболее высокими защитными свойствами обладает сплошная, достаточно тонкая прочная эластичная пленка, возникающая на гладкой поверхности металла, имеющая с ним хорошее сцепление и одинаковый с ним коэффициент линейного расширения. При этом пленка должна иметь некоторую оптимальную толщину, чтобы в достаточной степени тормозить встречную диффузию молекул агрессивного агента и катионов металла.
|
Однако на большинстве металлов защитная пленка после достижения известной толщины растрескивается, что позволяет ГК развиваться дальше. Разрушение пленки возможно по ряду причин. Если объем пленки больше объема металла, на месте которого она образовалась, то это приводит к появлению внутренних напряжений, сжимающих пленку параллельно поверхности и стремящихся оторвать ее от металла. При высоких внутренних напряжениях пленка разрушается. Таким образом, важны не только защитные свойства пленки, но и ее механические свойства – прочность, упругость и др.
Скорость газовой коррозии зависит не только от свойств образующихся пленок, но и от других внутренних и внешних факторов (см. 1.4). К внутренним факторам относятся природа металла, состав и структура сплава, степень обработки поверхности, наличие внутренних напряжений.
Скорость ГК сплавов на основе железа значительно снижается при содержании в них титана, меди, кобальта, бериллия, хрома, алюминия, кремния. Углерод заметного влияния не оказывает. В то же время скорость ГК значительно возрастает при содержании в сплавах ванадия, вольфрама и молибдена. В целом наименее устойчивы к действию ГК наиболее активные металлы – K, Ca, Na, Mg. Наиболее устойчивыми являются Pd, Ir, Pt, Au.
Особенно большое ускоряющее влияние на коррозию сталей оказывают соединения ванадия, в первую очередь V2O5, если они содержатся в продуктах сгорания углеводородного топлива. Оксид ванадия (V) содержится в золе, образующейся при сжигании мазута и других нефтепродуктов. При так называемой ванадиевой коррозии зола налипает на металл и увеличивает скорость его коррозии в десятки раз. Это обусловлено легкоплавкостью V2O5 и его способностью офлюсовывать вещества золы и окалины, т.е. переводить их в жидкое состояние, что снижает защитные свойства пленок окалины. Кроме того, оксид ванадия (V) активно участвует в процессе окисления железа по схеме:
4Fe + 3V2O5 = 2Fe2O3 + 3 V2O3
V2O3 + O2 = V2O5
V2O5 + Fe2O3 = 2FeVO4
Атомарное железо вначале окисляется оксидом ванадия (V) до трехвалентного. Образовавшийся при этом оксид ванадия (III) легко окисляется снова до пятивалентного состояния. При высокой температуре взаимодействие оксидов ванадия (V) и железа (III) приводит к образованию ванадата железа.
Гладкие металлические поверхности подвергаются ГК несколько медленнее, при этом степень обработки поверхности влияет на скорость ГК лишь на начальной стадии окисления.
|
Температурным влиянием на коррозию определяются такие важные свойства металлов, как жаростойкость и жаропрочность. Жаростойкость характеризует способность металла сопротивляться коррозионному воздействию газов при высокой температуре. Жаропрочность определяет способность материала в условиях высокотемпературного воздействия сохранять необходимые механические свойства, длительную прочность и сопротивление ползучести.
Так, например, жаропрочные стали можно эксплуатировать до 700 0С, алюминиевые и медные сплавы – до 400-500 0С, свинец – до 150 0С. Никель-хромовые сплавы работают до 1000 0С.
Резкие температурные изменения часто вызывают быстрое разрушение защитной пленки. Это связано прежде всего с различными коэффициентами линейного расширения металла и пленки, что способствует возникновению добавочных внутренних напряжений и механическому разрушению пленки.
Состав газовой среды во многом определяет скорость газовой коррозии. Наиболее активными газообразными окислителями являются фтор, кислород, диоксид серы, хлор, сероводород. Их активность по отношению к различным металлам не одинакова. Коррозия низколегированных и углеродистых сталей в выхлопных газах двигателей внутреннего сгорания, в топочных и печных газах сильно зависит от соотношения СО и О2. Повышение содержания О2 увеличивает скорость газовой коррозии и, наоборот, повышение содержания СО ослабляет коррозию.
Скорость движения газа заметно влияет на скорость ГК в начальной стадии окисления.
Несмотря на обилие факторов, скорость ГК определяется прежде всего свойствами возникающей на поверхности металла защитной пленки. В свою очередь, физико-химические свойства пленок определяются природой металла и окислителя, а также температурой.
1.5.2 Химическая коррозия в жидких неэлектролитах
Неэлектролитами называются вещества, неспособные подвергаться электролитической диссоциации, поэтому их растворы и расплавы не проводят электрический ток.
Коррозия металлов в жидких неэлектролитах (КЖН) протекает в среде агрессивных органических жидкостей, являющихся неэлектролитами, под действием содержащихся в них окислителей. К промышленным неэлектролитам относятся органические растворители (бензол, хлороформ и др.), расплавы солей серы и других веществ, жидкое топливо (обезвоженная нефть, керосин, бензин, другие нефтепродукты), сероуглерод, жидкий бром и другне.
В нефтяной промышленности КЖН происходит на внутренних поверхностях нефтехранилищ, нефтепроводов, нефтехимического оборудования, бензобаков.
В некоторых случаях на металлической поверхности образуется защитная пленка, которая затрудняет диффузию окислителя к поверхности металла и тем самым тормозит коррозионный процесс.
Температура в значительной степени влияет на скорость КЖН. В ряде случаев изменение температуры приводит к изменению растворимости окислителя и пленки продуктов коррозии в неэлектролите, что неоднозначно влияет на скорость процесса.
Углеводороды и органические растворители, входящие в состав жидких топлив, сами не являются коррозионно-активными по отношению к металлам. Так, бензин прямой гонки при отсутствии воды практически не действует на технически важные металлы.
В то же время в сырой нефти и неочищенных нефтепродуктах присутствуют различные примеси, обладающие коррозионной активностью. Например, крекинг-бензин при взаимодействии с железом и другими металлами (Pb, Mg, Cu, Zn) осмоляется, при этом повышается его кислотность, что ускоряет коррозию.
Наличие воды в нефти и других неэлектролитах значительно активирует коррозионное действие примесей и вызывает интенсивную электрохимическую коррозию, т.е. в присутствии воды меняется механизм коррозионного процесса.
В присутствии кислорода или диоксида углерода, растворенных в нефти или воде, возникает соответственно кислородная или углекислотная коррозия нефтегазового оборудования и трубопроводов. Кислородная коррозия нефтепромыслового оборудования, как правило, протекает более интенсивно, чем углекислотная. В продуктивных пластах кислород не содержится, его присутствие в коррозионной среде всегда имеет техногенное происхождение.
Наиболее существенный источник кислорода – вода из природных водоёмов, которая используется при заводнении пластов и обессоливании нефти. Она содержит до 7 мг/л растворённого О2, тогда как для коррозии достаточно менее 1 мг/л. В связи с этим водоводы, транспортирующие пресную воду, особенно подвержены кислородной коррозии. Кроме того, растворённый кислород значительно снижает эффективность работы ингибиторов коррозии широко применяемых на нефтяных месторож-дениях.
Однако наиболее высокая коррозионная активность нефти и газа обусловлена растворенными в ней сернистыми соединениями, в первую очередь сероводорода H2S, которые вызывают один из наиболее опасных видов химической коррозии – так называемую сероводородную коррозию (СК).
Негативная роль сероводорода H2S в процессах коррозии нефтегазового оборудования и трубопроводов разнообразна:
1. При растворении в воде он образует слабую сероводородную кислоту, которая хорошо реагирует с железом, его сплавами и многими другими металлами (Cu, Ag, Pb и др.) с образованием соответствующих сульфидов:
Fe + H2S = FeS + H2.
Это приводит к возникновению точечной коррозии, особенно в присутствии кислорода или диоксида углерода.
2. Образовавшиеся сульфиды образуют микрогальваническую пару с железом в составе стали, что вызывает ЭХК и приводит к быстрому разрушению технологического оборудования и трубопроводов.
3. В нефти также содержатся органические производные сероводорода – меркаптаны и тиофенолы общей формулы RSH. При взаимодействии с металлами переменной валентности они образуют соответствующие меркаптиды, тиофеноляты и элементарную серу, которые тоже коррозионно агрессивны.
4. Наиболее опасный сероводород не только изначально входит в состав нефти и газа, но и образуется в результате термического расщепления серосодержащих органических соединений, серооксида углерода и сероуглерода. С увеличением глубины добычи происходит повышение рабочих температур, при этом выделение сероводорода растет как за счет уменьшения его растворимости, так и за счет усиления распада сернистых веществ.
5. Сероводородная коррозия резко ускоряется в присутствии кислорода или воды, а еще более значительно – при их одновременном присутствии, что характерно для состава сырой нефти. Коррозия при одновременном действии H2S и О2 называется сульфитно-оксидной. В присутствии оксидов ванадия СК также резко ускоряется.
6. Газообразный сероводород, особенно в составе нефтяного попутного газа, вызывает интенсивную газовую коррозию нефтегазового оборудования и трубопроводов. Этому способствуют повышенное давление в трубопроводах и даже небольшая влажность транспортируемого газа.
Сухой сероводород при комнатной температуре для углеродистых сталей не представляет опасности. Однако с повышением температуры опасность сероводородной коррозии углеродистых сталей значительно увеличивается. При температуре выше 300 °С железо подвергается сильной коррозии в серосодержащих газовых средах.
В результате сероводородной коррозии значительно сокращается срок службы силового генерационного оборудования и аппаратуры при добыче, транспорте, переработке и использовании газа. В промысловых условиях особенно большому коррозионному воздействию подвергаются трубы, задвижки, камеры сгорания и поршни силовых установок электростанций, счетчики газа, компрессоры, холодильники.
Значительная часть сероводорода реагирует с металлом и может отложиться в виде продуктов коррозии на клапанах силовых установок, компрессоров, на внутренних стенках аппаратуры, коммуникаций и магистрального газопровода.
Проблема сероводородной коррозии становится все более острой в связи с постоянным увеличением доли сернистых нефтей в общем объеме добычи как в РФ, так и во всем мире.
Электрохимическая коррозия
Наиболее распространенным и опасным видом коррозии является электрохимическая коррозия (ЭХК). Она всегда сопровождается образованием электрического тока, поэтому может протекать только в токопроводящих средах, содержащих электролиты. В нефтегазовой отрасли такими средами могут быть:
1) водные растворы солей, кислот, щелочей;
2) морская и речная вода;
3) пластовые воды нефтяных месторождений;
4) буровые растворы;
5) атмосфера влажных газов;
6) влажная почва.
Возникновение тока при ЭХК связано с образованием на поверхности металла микрогальванических элементов (МГЭ), в которых корродирующий металл является анодом. Катодом могут быть участки металлического материала, имеющие по сравнению с анодом более положительный или менее отрицательный электродный потенциал. Роль катода могут выполнять:
1) примеси других металлов или их соединения. Например, в стали и чугуне роль катода могут выполнять примеси Co, Ni, Cu, а также карбиды железа FenCm;
2) продукты химической коррозии металла, например оксидные пленки;
3) деталь изделия, выполненная из другого, менее активного, металла.
Отметим, что если структура поверхности металла неоднородна, то МГЭ может образоваться и в отсутствие примесей или контакта с другим металлом.
МГЭ образуются на поверхности металла в большом количестве. Их называют накоротко замкнутыми и микрогальваническими по следующим причинам:
а) участки металла с разными значениями электродных потенциалов при замыкании цепи образуют гальванопару, в которой возникает электродвижущая сила (ЭДС);
б) размеры анода и катода, а также расстояния между ними очень малы;
в) анод и катод непосредственным образом контактируют друг с другом, поэтому в МГЭ, в отличие от искусственных ГЭ, для переноса электронов от анода к катоду внешняя цепь, т.е. проводник 1-го рода не требуется.
1.6.1 Общие принципы работы МГЭ
В основе ЭХК, как и любого коррозионного процесса, лежит гетерогенная ОВР, которая проходит на поверхности металла. Реагентами в данной ОВР являются сам металл, который выполняет роль восстановителя, и окислитель, называемый в данном процессе деполяризатором. При этом окислению, а следовательно, коррозионному разрушению всегда подвергается анод, т.е. наиболее электрохимически активный металл в составе металлического материала. Сущность процесса разрушения анода заключается в том, что его атомы необратимо окисляются до катионов, например: Zn0 – 2e ® Zn2+. Образующиеся катионы переходят в водную фазу.
Материал катода в процессе ЭХК никаким превращениям не подвергается. На его поверхности происходит восстановление наиболее активного окислителя из окружающей среды, который называется деполяризатором. Сущность катодного восстановления деполяризатора заключается в принятии им на поверхности катода электронов, перешедших с анода.
Роль деполяризатора могут выполнять:
1) в кислой среде (рН<7) ионы водорода H+, которые восстанавливаются по следующей реакции:
2H+ + 2е → Н2.
Этот процесс называется водородной деполяризацией.
Иногда водородная поляризация может протекать и в щелочной среде с участием воды в качестве окислителя:
2H2O + 2е → Н2 + 2ОН-;
2) в нейтральной и щелочной средах (pH≥7) деполяризатором обычно является атмосферный кислород O2, который всегда присутствует в водной среде и восстанавливается по следующей реакции:
О2 + 2H2O + 4е → 4ОН-.
Этот процесс называется кислородной деполяризацией. Этот тип деполяризации является основным при контакте металла с речной, морской, пластовой водой, влажной почвой и воздушной атмосферой.
Иногда кислородная деполяризация может протекать и в кислой среде:
О2 + 4H+ + 4е → 2H2O.
Перенос электронов от анода к катоду происходит в металлическом материале напрямую, так как они накоротко замкнуты. Для замыкания цепи в окружающей среде должен присутствовать электролит, анионы которого обеспечивают проводимость водной фазы.
Роль анионов-проводников тока в водной среде могут выполнять:
– в кислой среде – кислотные остатки кислот-деполяризаторов (SO42-, Cl- и т.п.), которые остаются в избытке после восстановления на катоде ионов водорода H+;
– в нейтральной или щелочной среде – анионы ОН-, образующиеся при восстановлении О2 на катоде.
При взаимодействии образующихся на аноде катионов металла с анионами, остающимися в избытке или образующимися на катоде, образуются вторичные продукты коррозии:
– в кислой среде образуются соли, например: Fe2+. + 2 Cl- ® FeCl2.
– в нейтральной и щелочной средах образуются гидроксиды и оксиды, например Met+2 + 2OH- = Met(OH)2 → MetO + H2O. В случае железа при рН≥7 образуется бурая ржавчина.
Таким образом, для образования МГЭ и протекания в нем ЭХК обязательны следующие условия:
– наличие в металле или металлическом материале участков с различными значениями электродных потенциалов;
– наличие контактирующей с металлом токопроводящей среды, содержащей воду с растворенными в ней электролитами;
– присутствие деполяризатора в токопроводящей среде.
На скорость ЭХК влияют те же факторы, что и при коррозии любого вида – это состав, степень неоднородности и состояние поверхности металлического материала, наличие в нем механических напряжений; температура; давление; состав, уровень рН и скорость движения коррозионной среды; наличие защитных пленок на поверхности металла; присутствие в почве и горных породах анаэробных бактерий, усиливающих коррозию.
В то же время для ЭХК характерно влияние и других факторов:
1. Природа металла и находящихся в нем примесей. Так, чем больше разность электродных потенциалов анода и катода, тем больше ЭДС возникающего МГЭ, и тем больше скорость ЭХК.
2. Наличие в почве блуждающих токов, ускоряющих анодное окисление металлического оборудования и трубопроводов. Они появляются в подземных металлических сооружениях в связи с работой электрифицированного транспорта и электрических устройств, использующих землю в качестве токопровода. Источниками блуждающих токов являются линии электрифицированных железных дорог, линии электропередачи, установки катодной защиты и др. Блуждающие токи стекают, как правило, с небольшой площади поверхности, что приводит к очень быстрому образованию глубоких язв в металле.
3. Явление поляризации. При работе МГЭ уменьшается разность начальных электродных потенциалов, что сопровождается уменьшением коррозийного тока. Этот процесс называется поляризацией. Различают анодную и катодную поляризацию. При анодной поляризации в случае усиленного растворения металла катионы металла медленнее переходят в раствор, чем электроны отводятся в катодную область. Вследствие этого катионы металла накапливаются у поверхности анода, и его потенциал смещается в сторону положительных значений.
Катодная поляризация сопровождается смещением потенциала катода в сторону отрицательных значений вследствие низкой скорости восстановления деполяризатора.
1.6.2 Схемы процесса ЭХК в различных условиях
1.6.2.1 ЭХК в условиях контакта двух металлов или при контакте металла и содержащейся в нем примеси.
![]() |
Железо в промышленности используется в виде сталей и сплавов. Поэтому оно всегда содержит примеси с более положительным значением электродного потенциала, например, вкрапления меди или углерода, которые накоротко замкнуты с железным материалом. При контакте такого сплава или стали с раствором электролита (в данном примере это раствор H2SO4) возникает МГЭ, в котором железо является анодом, а медь или углерод – катодом. В результате начинает уже протекать не химическая, а ЭХК, скорость процесса резко возрастает.
В нейтральной или щелочной среде ЭХК протекает аналогичным образом с той разницей, что роль деполяризатора выполняет растворенный в воде кислород, а продуктом вторичного процесса является не соль железа, а ржавчина.
Дальнейшее превращение гидроксида в ржавчину возможно только для железа и некоторых других черных металлов. В случае остальных металлов конечным вторичным продуктом является гидроксид общей формулы Met(OH)n, где n = 2 или 3 в зависимости от характерной степени окисления металла.
1.6.2.2 ЭХК в условиях неодинаковой аэрации
Влияние концентрации деполяризатора на скорость ЭХК проявляется в условиях неодинаковой аэрации. Неодинаковая аэрация – это различная концентрация кислорода в объеме раствора электролита.
Процесс протекает следующим образом. Поверхность железа под действием O2 подвергается химической коррозии по уравнению: Fe + O2 → FeO:
![]() |
Наибольшая концентрация кислорода наблюдается в поверхностном слое капли. Поэтому максимальная скорость образования оксида железа FeO и его наибольшее накопление на поверхности металла происходит по периметру капли. Под центром капли у поверхности железа концентрация кислорода низка, в этой области образование оксида железа незначительно. Оксид железа не только выполняет роль защитной пленки, но имеет более положительный потенциал, чем железо. В результате возникает МГЭ, в котором железо под центром капли является анодом, а FeO по краю капли – катодом. В результате проходящей ЭХК под центром капли возникают углубления и даже сквозные отверстия.
ЭХК в условиях неодинаковой аэрации широко распространена в нефтяной отрасли. Ее возникновению сильно способствует образование застойных зон сырой нефти в аппаратах и трубопроводах, а при образовании в застойных зонах осадков процесс еще больше ускоряется.
1.6.2.3 ЭХК в условиях повреждения защитного металлического покрытия
Одним из способов защиты металлического материала от коррозии является нанесение на него покрытия из другого металла.
Металлические покрытия делятся на анодные и катодные. Для получения анодного покрытия на защищаемый металл наносят слой электрохимически более активного металла. Пример – оцинкованное железо. Если цинковое покрытие не повреждено, то железо корродировать не может, так как к нему нет доступа окислителя. В этом случае может происходить только ХК самого покрытия.
Однако при повреждении или разрушении покрытия в среде электролита возникает ЭХК вследствие того, что:
1) образуется МГЭ, в котором цинк является анодом, а железо – катодом;
2) электрическая цепь замыкается, так как оба электрода теперь имеют доступ к токопроводящей среде.
При повреждении анодного покрытия будет разрушаться анод, т.е. само покрытие, но не защищаемый металл. Поэтому анодные покрытия применяются в тех случаях, когда велика опасность их повреждения (например, оцинкованные корпуса автомобилей).
Катодные покрытия делают из металла электрохимически менее активного, чем защищаемый металл. Пример – луженое железо, в котором для катодного покрытия железа используют олово. При повреждении катодного покрытия в токопроводящей среде возникает МГЭ, в котором олово будет катодом, а железо – анодом, которое и будет подвергаться коррозии. Поэтому катодные покрытия применяются при небольшой вероятности их повреждения (например, для внутреннего покрытия консервных банок или для покрытия церковных куполов).
![]() |
В нейтральной и щелочной средах ЭХК при повреждении анодного или катодного покрытия протекает аналогично с участием О2 в роли деполяризатора. Вторичным продуктом является гидроксид разрушаемого металла, а в случае железа – ржавчина.
ЭХК представляет большую опасность для нефтегазового оборудования и трубопроводов. Она может происходить:
а) внутри труб и оборудования при хранении или транспортировке углеводородного сырья под действием примесей воды и влаги, содержащих электролиты (соли, органические кислоты, ПАВ и др.);
б) снаружи под воздействием почвенного электролита – влаги, пластовых и других подземных вод, содержащих соли, щелочи, органические и неорганические кислоты.
В некоторых случаях ЭХК, особенно в отсутствие достаточной защиты от нее, может вызвать очень быстрое появление сквозных свищей в металле трубы и этим вывести трубопровод из строя.
1.7 Методы защиты металлов от коррозии
Защитные мероприятия начинают на стадиях проектирования и производства изделий и продолжают в процессе их эксплуатации.
Способы защиты металлов от коррозии делятся на следующие группы:
I. Способы, основанные на изменении химических, физико-химических или электрохимических свойств металлов. К ним относятся:
1. Легирование металлов.
2. Изоляция металлов путем нанесения защитных покрытий.
3. Электрохимическая защита.
II. Способы, основанные на изменении свойств агрессивной среды.
1.7.1 Легирование металлов
Это введение в металл добавок других металлов, которые повышают его коррозионную устойчивость и увеличивают прочность защитных пленок. При добавлении к железу Cr, Mo, Ni, Mn, W, Al в качестве легирующих добавок получают нержавеющие стали. Такие стали не покрываются ржавчиной, а их поверхностная коррозия протекает с малой скоростью.
При изменении концентрации легирующих добавок коррозионная стойкость металлов меняется скачкообразно. Так, резкое повышение коррозионной устойчивости железа наблюдается при введении легирующей добавки в количестве 1/8 атомной доли.
Особенности легирования железа различными металлами:
Хром. Обладает высокой склонностью к пассивации в средах с различными значениями рН. Устойчив к питтинговой коррозии. Пассивность хрома обусловлена образованием на его поверхности слоя оксида Cr2O3.
Никель. Основным недостатком хромистых сталей является их высокая склонность к хрупкому разрушению. Для преодоления этого недостатка хромистые стали легируют никелем, который придает им прочность и пластичность. Основным недостатком хромоникелевых сталей является их низкая устойчивость к коррозионному растрескиванию.
Молибден. Его вводят в хромоникелевые нержавеющие стали для повышения их коррозионной стойкости. Молибден улучшает пассивируемость сталей в неокислительных средах и снижает их склонность к питтинговой и щелевой коррозии.
Вольфрам. Основным недостатком хромникельмолибденовых сталей является их низкая стойкость в окислительных средах. Для преодоления этого недостатка их дополнительно легируют вольфрамом.
Медь. Легирование сталей медью повышает их коррозионную устойчивость в растворах минеральных кислот.
Для защиты от сероводородной коррозии эффективно легирование металлов хромом, алюминием, молибденом и кремнием.
Существует способ повышения устойчивости металла, основанный не на введении легирующих добавок, а наоборот, на удалении из него примесей, усиливающих коррозию.
1.7.2 Защитные покрытия
Они изолируют металлическую поверхность изделий, в том числе нефте-, газотрубопроводов, от агрессивной среды и делятся на металлические, неметаллические и химические.
Металлические покрытия, применяемые для защиты от ЭХК, делятся на анодные и катодные (см. 1.6).
Для защиты металлов от ХК металлические покрытия часто изготавливают из достаточно активного металла, который в условиях эксплуатации имеет повышенную коррозионную стойкость. Примеры: горячее алюминирование, оцинкование, хромирование.
Неметаллические покрытия бывают органические и неорганические. К органическим относятся лаки, краски, битумы, полимеры, резины. К неорганическим относятся покрытия из эмалей и бетонов. Лаки и краски наиболее эффективны в условиях атмосферной коррозии. Для защиты под
|
|
Индивидуальные очистные сооружения: К классу индивидуальных очистных сооружений относят сооружения, пропускная способность которых...
Историки об Елизавете Петровне: Елизавета попала между двумя встречными культурными течениями, воспитывалась среди новых европейских веяний и преданий...
Поперечные профили набережных и береговой полосы: На городских территориях берегоукрепление проектируют с учетом технических и экономических требований, но особое значение придают эстетическим...
Типы оградительных сооружений в морском порту: По расположению оградительных сооружений в плане различают волноломы, обе оконечности...
© cyberpedia.su 2017-2024 - Не является автором материалов. Исключительное право сохранено за автором текста.
Если вы не хотите, чтобы данный материал был у нас на сайте, перейдите по ссылке: Нарушение авторских прав. Мы поможем в написании вашей работы!