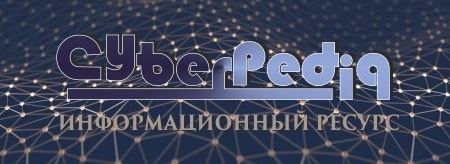
Поперечные профили набережных и береговой полосы: На городских территориях берегоукрепление проектируют с учетом технических и экономических требований, но особое значение придают эстетическим...
Типы оградительных сооружений в морском порту: По расположению оградительных сооружений в плане различают волноломы, обе оконечности...
Топ:
Комплексной системы оценки состояния охраны труда на производственном объекте (КСОТ-П): Цели и задачи Комплексной системы оценки состояния охраны труда и определению факторов рисков по охране труда...
Выпускная квалификационная работа: Основная часть ВКР, как правило, состоит из двух-трех глав, каждая из которых, в свою очередь...
Основы обеспечения единства измерений: Обеспечение единства измерений - деятельность метрологических служб, направленная на достижение...
Интересное:
Берегоукрепление оползневых склонов: На прибрежных склонах основной причиной развития оползневых процессов является подмыв водами рек естественных склонов...
Искусственное повышение поверхности территории: Варианты искусственного повышения поверхности территории необходимо выбирать на основе анализа следующих характеристик защищаемой территории...
Аура как энергетическое поле: многослойную ауру человека можно представить себе подобным...
Дисциплины:
![]() |
![]() |
5.00
из
|
Заказать работу |
|
|
Сварка представляет собой технологический процесс, при помощи которого получают неразъемные соединения деталей в узлах и конструкциях. Сварочный процесс используют также для производства наплавочных работ.
Для осуществления сварки необходимо сблизить металлические поверхности, подлежащие соединению, настолько, чтобы между ними начали действовать силы межатомного сцепления.
Основными параметрами сварочных процессов являются температура и давление. Соответственно этому все способы сварки можно разбить на три группы.
Сварка плавлением основана на местном разогреве деталей до плавления и образования сварного соединения путем перемешивания жидких фаз. В этом процессе главную роль играет один параметр — температура; поэтому сварка возможна при применении мощных тепловых источников.
Пластическая сварка основана на местном разогреве деталей до пластического состояния и приложении давления к свариваемым местам. Здесь оперируют двумя параметрами — температурой и давлением.
Холодная сварка основана на приложении к свариваемым участкам холодных деталей значительного усилия. Здесь оперируют одним параметром — давлением.
Значительное распространение сварных конструкций в машиностроении следует объяснить рядом преимуществ: экономией металла, малой трудоемкостью и сокращенными сроками изготовления, простотой оборудования, легкостью исправления дефектов и др. При помощи сварки можно изготовить сварные конструкции сложной формы, получая при этом прочность сварного соединения, равную прочности металла конструкции.
Сварка позволяет создавать принципиально новые конструкции машин и сооружений, основанные на использовании катаных, литых, кованых и штампованных заготовок. Это оказывает влияние не только на отдельные детали объектов, но и на форму всей конструкции в целом.
|
В настоящее время известно свыше шестидесяти способов сварки, из них в промышленности используется несколько десятков видов и разновидностей, которые классифицируются, как правило, по способу нагрева металла. Значительное место в производстве занимают электрические способы сварки, при которых происходит превращение электромагнитной формы энергии в тепловую.
Дуговая сварка состоит в том, что кромки деталей и конец электрода разогреваются мощным источником тепла — электрической дугой, возникающей между электродом и свариваемым металлом.Жидкий металл, перемешиваясь, заполняет стык между деталями, а после остывания образует шов.
Для защиты жидкого металла шва от вредного воздействия кислорода и азота воздуха электроды покрывают специальными обмазками или процесс проводят в защитных средах (аргон, гелий, азот, углекислый газ или их комбинации). В последнем случае говорят о газоэлектрической сварке. Когда защитная среда образуется при нагреве сыпучей смеси компонентов, процесс называют сваркой под слоем флюса.
Почти все способы дуговой сварки обладают определенной универсальностью. С их помощью можно сваривать детали толщиной от 2 до 200мм и больше.
Электрическая контактная сварка состоит в том, что при прохождении тока большой силы через заранее сжатые детали в контакте между ними выделяется теплота. Под ее воздействием металл нагревается до пластического состояния или плавления, и после охлаждения образуется соединительный элемент.
Если детали собраны внахлестку, они после сварки соединены ядром. Такой процесс именуется точечной сваркой. При выполнении конструкций, работающих на герметичность, используется роликовая сварка, при которой точки перекрывают друг друга. Точечная и роликовая сварка легко поддаются автоматизации и применяются в массовом производстве однотипных деталей из тонкого листового материала.
|
При сборке деталей встык (стержни, трубы, полосы) детали свариваются по всему контактному сечению — сварка называется стыковой.
При электрошлаковой сварке нагревательным элементом является расплавленный токопроводящий флюс, заключенный между свариваемыми пластинами, охладителями и сварным швом снизу. Процесс ведется вертикально.
Целесообразно сваривать детали большой толщины, применяемых при производстве станин прессов, прокатных станов и др.
Самостоятельными видами электрической сварки являются сварка пучком электронов в вакууме, индукционная сварка и др.
Сварочные процессы, в которых используется теплота, выделяющаяся при сжигании различных горючих продуктов, относятся к химической сварке. Из процессов этой группы широко используется газовая сварка. Кромки металла нагреваются
выходящим из горелки пламенем,получаемым при сгорании горючего газа в смеси с кислородом. Для формирования шва добавляют присадочную проволоку. Тепловая мощность пламени невелика, поэтому этот вид сварки используют для производства деталей из тонкого листа и деталей из цветных металлов и сплавов.
За последние годы получили распространение способы сварки, в которых местный разогрев деталей осуществляется теплотой при превращении механической энергии в тепловую (сварка трением, сварка ультразвуком).
Каждый способ сварки дает наилучшие качественные показатели и экономическую целесообразность в рамках определенных толщин свариваемых материалов, их физических свойств и требований, предъявляемых к сварной конструкции. Вместе с тем следует считаться с технологическими особенностями каждого способа сварки. Это особенно учитывается тогда, когда конструкция может быть сварена несколькими способами.
Вопросы для повторения и закрепления:
1. Какие виды сварки применяются при производстве деталей?
Виды сварных соединений.
В сварных конструкциях различают стыковые, нахлесточные, угловые, тавровые и заклепочные соединения (рис. 28.1).
Стыковые соединения (рис. 28.1, а - ж) различают по виду предварительной подготовки кромок. В зависимости от толщины свариваемого металла производят различную подготовку кромок, которая для ручной электродуговой сварки и автоматической сварки под слоем флюса регламентируется соответственно ГОСТ 5264—58 и ГОСТ 8713—58.
|
При толщине металла до 3ммприменяют отбортовку без зазора (рис. 28.1, а), высота бортика h = 2s; при толщине металла до 4мм (иногда до 8мм ) сварку производят без разделки кромок при зазоре до 2мм (рис. 28.1, б, в).
Металл при толщине 13—15ммсваривают с односторонней V -образной разделкой кромок (рис. 28.1, г). При толщине металла больше 15ммрекомендуется двусторонняя Х-образная разделка кромок (рис. 28.1, д). Металл толщиной более 20ммсваривают с чашеобразной разделкой кромок, которая может быть односторонней и двусторонней (рис. 28.1, е, ж).
Соединения внахлестку (рис. 28.1, з) производят угловыми швами; величина нахлестки равна трех- пятикратной толщине свариваемых элементов.
Рис. 28.1. Виды сварных соединений и швов
Угловые соединения (рис. 28.1, и) выполняют без скоса и со скосом кромок.
Тавровые соединения выполняют приваркой одного элемента изделия к другому (рис. 28.1, к). Без скоса кромок сваривают конструкции малой нагрузкой. При изготовлении ответственных конструкций с элементами толщиной 10…20мм применяют односторонний скос, а при толщине элементов более 20мм – двусторонний.
По положению в пространстве (рис. 28.2.) швы могут быть нижние и горизонтальные (а), вертикальные (б) и потолочные (в)
![]() |
Рис. 28.2 Типы швов при различном положении в пространстве
Вертикальные швы могут быть расположены на вертикальной плоскости в любом направлении. Наиболее трудными для выполнения являются потолочные швы.
Они располагаются в любом направлении на верхней горизонтальной плоскости.
Швы можно выполнять непрерывными и прерывистыми в зависимости от действующей нагрузки.
|
Рис. 28.3. Типы швов по отношению к направлению действующих на них усилий
Задание:
Составить план ответа по разделу «Сварка металла»
|
ОБРАБОТКА МЕТАЛЛОВ РЕЗАНИЕМ
Виды обработки металла
Виды обработки металлов резанием различаются между собой конструкцией используемого режущего инструмента и характером относительных движений, совершаемых инструментом и обрабатываемой заготовкой на металлорежущем станке.
Геометрическая форма любой поверхности может быть образована копированием или огибанием сопряженной поверхностью. Требуемый контур детали получается в результате сочетания определенных движений инструмента и заготовки.
Классификация методов обработки поверхностей деталей резанием учитывает кинематические признаки (по принципу сочетания движений заготовки и инструмента) и признаки, определяющие сущность данного метода обработки — условия процесса стружкообразования (физические особенности процесса резания). В соответствии с этим принципом все методы обработки резанием разделяют на четыре группы: точение, строгание, фрезерование и шлифование.
Методы обработки различных групп могут осуществляться при одних и тех же сочетаниях прямолинейных и вращательных движений. Отличительным признаком каждой группы являются вид и направление главного движения или движения резания, в процессе которого происходит срезание припуска.
Главное движение, определяющее скорость резания, является либо вращательным, либо прямолинейным. Оно сообщается заготовке или режущему инструменту, а в ряде случаев одновременно заготовке и режущему инструменту
Рис. 28.1. Методы обработки поверхностей леталей резанием:
А – точение; б – фрезерование; в – строгание; г – шлифование
Рис. 29.1. Методы обработки поверхностей деталей резанием:
а – точение; б – фрезерование; в – строгание; г – шлифование
При точении (рис. 29.1, а) главное движение — это движение по направляющей обрабатываемой поверхности. При точении наружных и внутренних поверхностей вращения главным движением является вращение вокруг оси детали.
При фрезеровании (рис. 29.1, б) траектория главного движения не совпадает с обрабатываемой поверхностью. Здесь главным движением является вращение вокруг оси инструмента — фрезы.
При строгании (рис. 29.1, в) главное движение представляют собой прямолинейное движение вдоль образующей или по касательной к направляющей обрабатываемой поверхности.
Все остальные движения, присущие кинематике различных схем резания, обеспечивают постепенное удаление припуска. Эти движения, определяющие толщину среза (срезаемого слоя), являются движениями подачи.
Эти движения либо прямолинейные, либо вращательные и сообщаются режущему инструменту или заготовке. Скорости главного рабочего движения и движения подачи обозначаются соответственно V и S. Направление главного движения определяет характер протекания процесса обработки. Методы точения характеризуются непрерывностью процесса резания при обработке непрерывных поверхностей. Методы фрезерования характеризуются прерывистостью процесса резания с образованием стружки, толщина которой меняется от нуля до некоторой максимальной величины и наоборот.
|
Строгание — промежуточный процесс между точением и фрезерованием. Строгание можно рассматривать как частный случай точения с постоянной толщиной среза, но с перерывами в работе при обработке поверхностей вращения и плоскостей, когда главное движение направлено вдоль образующей. Строгание является частным случаем фрезерования при обработке поверхностей вращения и винтовых поверхностей, когда главное движение направлено по касательной к направляющей.
При шлифовании (рис. 29.1, г) главным движением является вращение шлифовального круга вокруг оси. Методы шлифования характеризуются специфическими особенностями работы абразивного инструмента.
Для разных видов обработки применимы общие понятия и определения. Для удобства рассмотрим их на примере точения.
Вопросы для повторения и закрепления:
1. Что называется главным, а что вспомогательным движениями?
2. Какие существуют основные методы обработки металла резанием?
|
|
История создания датчика движения: Первый прибор для обнаружения движения был изобретен немецким физиком Генрихом Герцем...
Папиллярные узоры пальцев рук - маркер спортивных способностей: дерматоглифические признаки формируются на 3-5 месяце беременности, не изменяются в течение жизни...
Двойное оплодотворение у цветковых растений: Оплодотворение - это процесс слияния мужской и женской половых клеток с образованием зиготы...
Организация стока поверхностных вод: Наибольшее количество влаги на земном шаре испаряется с поверхности морей и океанов (88‰)...
© cyberpedia.su 2017-2024 - Не является автором материалов. Исключительное право сохранено за автором текста.
Если вы не хотите, чтобы данный материал был у нас на сайте, перейдите по ссылке: Нарушение авторских прав. Мы поможем в написании вашей работы!