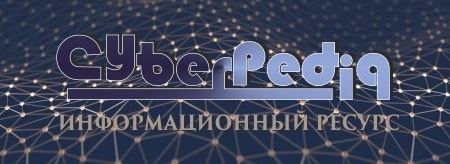
Особенности сооружения опор в сложных условиях: Сооружение ВЛ в районах с суровыми климатическими и тяжелыми геологическими условиями...
История развития пистолетов-пулеметов: Предпосылкой для возникновения пистолетов-пулеметов послужила давняя тенденция тяготения винтовок...
Топ:
История развития методов оптимизации: теорема Куна-Таккера, метод Лагранжа, роль выпуклости в оптимизации...
Теоретическая значимость работы: Описание теоретической значимости (ценности) результатов исследования должно присутствовать во введении...
Комплексной системы оценки состояния охраны труда на производственном объекте (КСОТ-П): Цели и задачи Комплексной системы оценки состояния охраны труда и определению факторов рисков по охране труда...
Интересное:
Уполаживание и террасирование склонов: Если глубина оврага более 5 м необходимо устройство берм. Варианты использования оврагов для градостроительных целей...
Искусственное повышение поверхности территории: Варианты искусственного повышения поверхности территории необходимо выбирать на основе анализа следующих характеристик защищаемой территории...
Наиболее распространенные виды рака: Раковая опухоль — это самостоятельное новообразование, которое может возникнуть и от повышенного давления...
Дисциплины:
![]() |
![]() |
5.00
из
|
Заказать работу |
|
|
Материал режущего инструмента | Углеродистая сталь | Легированная сталь | Серый чугун | Чугун, НВ 375-400 |
Т60К6 | 0,7-4 | 0,7-4 | ___ | _ |
Т30К4 | 3-4 | 4-6 | — | — |
Т15К6 | 5-7 | 9-10 | — | — |
Т5К10 | 12-13 | — | — | |
ВК9 | — | — | — | |
ВК8 | — | 17-25 | 13-14 | — |
ВК6 | — | — | — | |
ВК4 | —. | 25-30 | — | — |
ВКЗ | — | 9-10 | ||
ВК2 | - | - | 4-26 | |
Примечание.Данные получены при следующих условиях: сталь углеродистая, ов = 500-^600 МПа при скоростях резания 100 — 400 м/мин; сталь легированная, ств = 920-Н100 МПа при скоростях резания 100 — 200 м/мин; серый чугун, НВ 187 — 207 при скоростях резания 50— 150 м/мин; данные для закаленного чугуна с НВ 375 — 400 относятся к тонкому растачиванию. |
На размерный износ влияют материал режущего инструмента, конструкция, геометрия и состояние лезвия, режимы обработки, жесткость системы и другие факторы. Например, зависимость радиального (размерного) износа от времени работы Т (мин), скорости резания v (м/мин) для обработки деталей из стали 45 резцом с пластиной из твердого сплава Т15К6 может быть выражена формулой
Однако в достаточной степени обобщенных зависимостей размерного износа инструмента от указанных факторов пока нет. Поэтому часто, определяя размерный износ для обрабатываемой партии деталей, исходят из ориентировочных значений относительного износа или задаются допустимым для данного вида обработки размерным износом инструмента (табл. 29).
Влияние температурных деформаций на точность обработки. Теплота, образующаяся при резании, трении сопряженных деталей станков, а также внешнее тепловое воздействие приводят к упругой деформации технологической системы, появлению погрешностей обработки
|
1АТ.
Теплота в процессе резания образуется в результате внутреннего трения между части
29. Допустимый размерный износ (мкм) инструмента при обработке партии заготовок
|
цами обрабатываемого материала в процессе деформации (бдеф), внешнего трения стружки о переднюю поверхность резца (бп.тр) и поверхности резания, обработанной поверхности о задние поверхности резца (Q3 хр), отрыва стружки, диспергирования (бдисп)'
Q ~ Qдеф "I" Qn. тр Q.3. тр бдисп-
Так как механическая работа почти полностью переходит в теплоту,
Е Е
где Q — количество теплоты; R — работа резания (R = Pzv); v — скорость резания; Е — механический эквивалент теплоты.
Распределение теплоты резания между стружкой, деталью, инструментом зависит от метода, условий обработки, материала обрабатываемой детали и инструмента. Так, при обработке точением материалов с высокой теплопроводностью (углеродистые стали) распределение теплоты таково: в стружку 60 — 90%; в инструмент 3 — 5%. При такой же обработке материалов с низкой теплопроводностью (жаропрочные, титановые сплавы) 35 — 45% всей теплоты резания переносится в деталь, 20 — 40 % — в резец.
Наибольшее количество теплоты переходит в деталь при шлифовании (до 60 — 85 %) и сверлении (до 60%).
Для обработки деталей на станках характерен одновременный перенос теплоты теплопроводностью, конвекцией и излучением (сложный теплообмен). Изучение сложного теплообмена встречает известные трудности, которые на практике до сих пор удовлетворительно не решены. При исследовании устанавливают температурное поле (совокупность значений температуры 0 в данный момент времени т для всех точек изучаемого про
странства) 0 =/(х, у, z, т), где х, у, z — координаты точки. Температурное поле является случайным для данного станка. Если температура тела есть функция координат и времени, то температурное поле, будет нестационарным,
|
/ае \
т. е. зависящим, от времени — Ф 0. Такое
V дт)
поле соответствует неустановившемуся тепловому режиму теплопроводности, характерному для детали и станка в начальный период работы. Однако через некоторый промежуток времени происходит стабилизация теплообмена — температура точек станка есть функция только координат точек и не изменяется с те- /50 \
чением времени —- = 0; температурное по-
\дт J
ле станка будет стационарным.
Средние значения деформаций, связанных со стационарными процессами, могут быть учтены при построении процесса и тем самым будет повышена точность обработки.
Расчет температурных полей сложных объектов обычно упрощают. Разработана приближенная методика определения температурных деформаций деталей станков. Однако надежные данные по температурным полям, деформациям станков можно получить при экспериментальном исследовании. Только в простейших случаях, например при равномерном нагреве простой детали, можно вычислить изменение размера детали: AL=aLA0fl, где L— размер детали; a — коэффициент линейного расширения материала детали; А0Д - изменение температуры детали. Так, при шлифовании деталей с охлаждением 0Д = = (0Ж + 1,5) + 1, где 0Ж — температура охлаждающей жидкости.
Обычно при обработке вследствие неравномерного нагрева происходит изменение размеров, формы и расположения поверхностей. Так, температура в различных точках станка различается на 10 — 60 °С, и это вызывает смещение и перекос оси шпинделя относительно оси детали.
Температура и температурные деформации станка в значительной степени определяются конструкцией узлов, фактическими зазорами и натягами в подшипниках, методом подачи и объемом смазочного материала.
При испытании станков на точность проверяют стабильность взаимного расположения рабочих органов под тепловой нагрузкой. Для круглошлифовальных станков линейное смещение оси шпинделя шлифовального круга относительно оси передней и задней бабок в результате нагрева на холостом ходу в течение 60 мин допускается 32 — 63 мкм соответственно для станков с наибольшим устанавливаемым диаметром 100 — 800 мм, а угловое смещение 4 мкм на длине 100 мм. Указанные отклонения относятся к станкам класса П. Для станков классов В и А отклонения меньше в 1,6 и 2,5 раза соответственно.
|
Температурные деформации вызывают не только смещение узлов станка, но и изменение жесткости станков. Так, после нагрева бесцен- трово-шлифовальных станков жесткость узлов увеличилась в 1,5 раза, отклонение формы — в 1,5 раза.
Температурные деформации могут быть существенно уменьшены:
1) обеспечением постоянства температурного поля в зоне установки станка: поддержанием в цехе определенного температурного режима (табл. 30), установкой прецизионных станков в специальных термоконстантных помещениях;
2) уменьшением неравномерного нагрева станков в результате: а) вынесения внутренних источников теплоты (электродвигателей, гидроприводов) за пределы станка; б) применения систем для поддержания определенной температуры смазочного масла; СОЖ; в) искусственного нагрева отдельных частей станка;
3) уменьшением влияния температурных деформаций путем выбора материалов деталей и оптимальных Направлений (не совпадающих с направлением выдерживаемого размера) температурных деформаций, применения устройств для компенсации температурных смещений;
4) эксплуатационными мероприятиями: правильной установкой станков, своевременным регулированием подшипниковых узлов, обработкой точных деталей после достижения станком стационарного теплового состояния (после длительного останова, на холостом ходу в течение 20 — 30 мин).
При простейших расчетах учитывают удлинение резца при установившемся тепловом состоянии:
/vK7
где С — постоянная (при t ^ 1,5 мм; s ^ 0,2 мм/об; v = 100 200 м/мин С = 4,5); Lp - вылет резца; F — площадь поперечного сечения рез-
ца, мм' |
tQ
Кт=-------- коэффициент, учитывающие
щий охлаждение резца из-за перерывов в работе.
Температура резания при токарной обработке может быть вычислена по следующим приближенным соотношениям:
для деталей из стали (ств = 770 МПа; 5 = = 22%)
0 = 166,5t>°'4r0'105s0'2;
для деталей из чугуна
0 = 13Sv0,36t°'09s0,133.
При шлифовании различают температуру: мгновенную 0М, развивающуюся непосредственно в зоне микрорезания шлифующим зерном и являющуюся высокой (от 1000 °С до температуры плавления обрабатываемого материала) и кратковременной; контактную 0К (среднюю в зоне шлифования) в зоне контакта круга с деталью (~ 200 — 1100 °С); среднюю 0С на поверхности шлифуемой детали (~20 — 350 °С).
|
30. Температурный режим в механических цехах
|
* Работа выполняется на полуавтоматических делительных машинах, установленных в специальных кабинах. Оператор в процессе деления в кабине не присутствует. |
Местная температура при трении может достигать 250—1000 °С. Средняя температура в коробках скоростей и других подобных узлах 65 —80°С.
Полную погрешность обработки, связанную с температурными деформациями, обычно определить не удается. Для операций с жесткими допусками на обработку приблизительно принимают
LAr = 0,l + 0,4As,
причем для обработки лезвийным инструментом
£АТ = 0,1 -г- 0,15АЬ
при шлифовании £АТ составляет до 30 — 40% суммарной погрешности Aj\
Методы оценки надежности технологических систем по параметрам качества изготовляемой продукции (ГОСТ 27.202 — 83) включают и методы оценки показателей надежности технологических операций и процессов, а также средств технологического оснащения по точности. Контроль точности технологических систем проводят по альтернативному (при разработке технологических процессов на этапе технологической подготовки производства и при управлении технологическими процессами) или количественному (при определении периодичности подналадок технологического оборудования, выбора методов и планов статистического регулирования технологических процессов и операций и т. д.) признаку.
При контроле по количественному признаку определяют значения показателей точности, основными из которых являются:
коэффициент точности (по контролируемому параметру X)
|
Кт = со/Г,
где со — поле рассеяния (или размах R) значений контролируемого параметра за установленную наработку технологической системы, определяемое с доверительной вероятностью у по выражению со = / (у) S, здесь / (у) — коэффициент, зависящий от закона распределения параметра X и значения у; S — среднее квадра- тическое отклонение параметра X; Т— допуск параметра X.
Размах R определяют как разность максимального и минимального значений параметра в объединенной выборке, состоящей из серии мгновенных выборок со «R = Хтах — Хтт.
Коэффициент мгновенного рассеяния (по контролируемому параметру)
Kp(t)=w(t)/T,
где со (Г) — поле рассеяния параметра в момент времени t.
Коэффициент смещения (контролируемого параметра)
Kc = A(t)/T,
где A (t) — среднее значение отклонения параметра относительно середины поля допуска в момент времени t:
A(t) = |*(t)-*o|.
здесь J? (f) —среднее значение параметра; Х0 — значение параметра, соответствующее середине поля допуска (при симметричном поле допуска значение Х0 совпадает с номинальным значением Хном)-
Коэффициент запаса точности (по контролируемому параметру)
K3 = O,5-Kc(t)-0,5Kp(t). Для обеспечения надежности технологической системы по параметрам точности необходимо в любой момент времени (в пределах установленной наработки) выполнить условие КТ^КТ о < 1; К3 (t) > 0, где Кт 0 — нормативное (предельное, технически обоснованное) значение Кт.
В условиях единичного и мелкосерийного производства, когда число одноименных деталей не позволяет применить указанные выше коэффициенты, контроль точности технологической системы можно выполнить по альтернативному признаку, используя метод приведенных отклонений (по справочному приложению к ГОСТ 27.202-83). В одну выборку включают детали, характеризующиеся конструктивным подобием и общностью технологического процесса обработки.
Точность технологической операции считается удовлетворительной при выполнении одного из следующих условий:
0^ Д„р/ =------ jr— < U
i
_ t <Г a _ 2 (Ад j — A0 J
I ^ Anp i -
i
— при расчете приведенных отклонений размера соответственно относительно нижнего Днг-, верхнего Дш предельных отклонений и координаты середины поля допуска Д0/; 0 ^ Дпр/ =
= —-— ^ 1 — при расчете приведенных от-
клонений для параметров формы и расположения для всех деталей i = 1 ч- и, объединенных В Выборку. ЗдеСЬ Дц; и Дф д / — действительные отклонения размера и формы (расположения) г-й детали; Tt и Тф i — допуск размера и формы (расположения) г-й детали.
В одну выборку включают по нескольку экземпляров разных деталей. Проверку условий проводят по каждому значению Дпрг.
Показатели надежности технологических систем кроме рассмотренных показателей точности включают показатели выполнения заданий по качеству (параметрам качества продукции), по технологической дисциплине и комплексные показатели.
Оценку выполнения заданий по параметрам качества изготовляемой продукции проводят для технологических процессов (операций), влияющих на качество продукции, и по которым получены неудовлетворительные результаты оценок по точности и технологической дисциплине. При оценке используют показатели вероятности выполнения задания по одному или нескольким (п) параметрам качества изготовленной в момент времени t продукции Рь..., „ (0 = Р ^ Xi(t) < XBi} при i = 1,..., п.
Комплексные показатели оценки надежности технологических систем по параметрам качества изготовляемой продукции включают показатели надежности технологических систем по критериям дефектности, возвратов продукции, брака. Вероятность соблюдения норматива проверяют (обычно регистрационным методом) по указанным показателям.
|
|
Адаптации растений и животных к жизни в горах: Большое значение для жизни организмов в горах имеют степень расчленения, крутизна и экспозиционные различия склонов...
Семя – орган полового размножения и расселения растений: наружи у семян имеется плотный покров – кожура...
Типы оградительных сооружений в морском порту: По расположению оградительных сооружений в плане различают волноломы, обе оконечности...
Опора деревянной одностоечной и способы укрепление угловых опор: Опоры ВЛ - конструкции, предназначенные для поддерживания проводов на необходимой высоте над землей, водой...
© cyberpedia.su 2017-2024 - Не является автором материалов. Исключительное право сохранено за автором текста.
Если вы не хотите, чтобы данный материал был у нас на сайте, перейдите по ссылке: Нарушение авторских прав. Мы поможем в написании вашей работы!