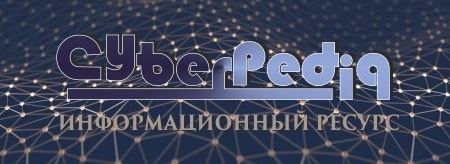
Особенности сооружения опор в сложных условиях: Сооружение ВЛ в районах с суровыми климатическими и тяжелыми геологическими условиями...
Состав сооружений: решетки и песколовки: Решетки – это первое устройство в схеме очистных сооружений. Они представляют...
Топ:
Процедура выполнения команд. Рабочий цикл процессора: Функционирование процессора в основном состоит из повторяющихся рабочих циклов, каждый из которых соответствует...
Выпускная квалификационная работа: Основная часть ВКР, как правило, состоит из двух-трех глав, каждая из которых, в свою очередь...
Установка замедленного коксования: Чем выше температура и ниже давление, тем место разрыва углеродной цепи всё больше смещается к её концу и значительно возрастает...
Интересное:
Аура как энергетическое поле: многослойную ауру человека можно представить себе подобным...
Берегоукрепление оползневых склонов: На прибрежных склонах основной причиной развития оползневых процессов является подмыв водами рек естественных склонов...
Уполаживание и террасирование склонов: Если глубина оврага более 5 м необходимо устройство берм. Варианты использования оврагов для градостроительных целей...
Дисциплины:
![]() |
![]() |
5.00
из
|
Заказать работу |
|
|
Форма организации производственного процесса на участке определяется, как правило, типом производства. Тип производства — это степень постоянства загрузки рабочих мест, линии, участка, цеха, завода одной и той же работой. Различают три типа производства: массовый, серийный, единичный.
Правильное определение типа производства на участке позволяет выбрать эффективную форму его организации. Основой для определения типа производства являются программа выпуска, вид изделия и трудоемкость его изготовления. В качестве показателя для определения типа производства можно использовать коэффициент специализации и коэффициент массовости.
![]() |
где m — количество операций по технологическому процессу;
Спр — количество рабочих мест (единиц оборудования), необходимых для выполнения данного технологического процесса. Таким образом, коэффициент специализации равен
Полученное значение КСП ≤ 1 и равно 0,64 — это означает, что производство платы АРУ относится к массовому типу производства.
Коэффициент массовости определяется по формуле:
где tштi — норма штучного времени на i - ой операции с учётом коэффициента выполнения норм времени, мин
m — количество операций по технологическому процессу
rНЛ — такт (ритм) выпуска изделий (rНЛ = 0,6 мин/шт)
Определим программу выпуска по формуле:
Nз = Fэ*60 /rНЛ =329,28*60/0,60 = 32 928 шт.
где Nз - годовая (месячная) норма запускаемого изделия
Fэ - годовой (месячный) эффективный фонд времени работы оборудования, определяется по формуле:
Fэ = Fн * Кп.о = 336 * 0,98 = 329,28 ч.
где Fн - номинальный фонд времени работы оборудования (Fн = 2*8*21 =
336).
|
Кп.о - коэффициент учитывающий время простоя оборудования (для верстаков и монтажных столов Кп.о = 0,98).
Км=8,40/(9*0.60)=1,56, что подтверждает выбор массового типа производства, каждая операция технологического процесса полностью загружает минимум одно рабочее место на протяжении всего планируемого периода.
Основанием для выбора поточной линии является обоснование типа производства. Так как массовый тип производства, то целесообразна организация поточного типа производства.
2 Расчет календарно-плановых нормативов ОНПЛ
ОНПЛ применяются в массовом и крупносерийном типах производства, когда норма времени выполнения операций производственного процесса равна или кратна такту, предметы труда перемещаются с одного рабочего места на другое без пролёживания каждая операция постоянно закреплена за определённым рабочим местом, рабочие места расположены в порядке следования технологического процесса.
Основной состав календарно-плановых нормативов ОНПЛ следующий:
укрупненный такт или ритм потока; количество рабочих мест по операциям и по всей поточной линии; скорость движения конвейера; период конвейера и система адресования; величина заделов; длительность производственного цикла; стандарт-план ОНПЛ.
Произведем расчет КПН:
Такт поточной линии
Его величина зависит от программы выпуска изделий и эффективного фонда времени работы поточной линии.
где Nз – программа выпуска изделий
Fэ-месячный эффективный фонд времени работы оборудования
Fэ =Fн Kно = 21дней*8ч*2см*0,98=329,28ч.
Fн- номинальный фонд времени работы оборудования, ч
Кно- коэффициент, учитывающий время простоя оборудования в плановом ремонте(0,98)
Количество рабочих мест.
Перед расчетом количества необходимых рабочих мест необходимо произвести синхронизацию технологического процесса
Число рабочих мест на каждой i-ой операции определяется по формуле:
, шт.
Ср – это расчетное количество рабочих мест, а для определения принятого количества рабочих мест необходимо расчетное количество округлить до целого числа. Затем рассчитывается коэффициент загрузки, он определяется путем деления расчетного количества оборудования на принятое. Расчеты произведем в таблице 4.
|
Таблица 4 ─ Синхронизация технологического процесса, расчет потребного количества оборудования (рабочих мест) и коэффициента загрузки.
№ | Содержание | tшт | Коэф | Tшт с уч. коэф | гнл | Ср | Спр | К-т загрузки |
вручную | 1,24 | 1,24 | 0,60 | 2,07 | 1,03 | |||
вручную | 0,60 | 0,60 | 0,60 | 1,00 | 1,00 | |||
Вручную пинцет | 0,60 | 0,60 | 0,60 | 1,00 | 1,00 | |||
Вручную пинцет | 0,61 | 0,61 | 0,60 | 1,02 | 1,02 | |||
Установка «Волна», вручную | 0,58 | 0,58 | 0,60 | 0,97 | 0,97 | |||
Вручную, паяльник 50 Вт, 36В, совок-скребок | 1,20 | 1,20 | 0,60 | 2,00 | 1,00 | |||
Вручную, паяльник 50 Вт, 36В, пинцет с изоляцией | 0,59 | 0,59 | 0,60 | 0,98 | 0,98 | |||
вручную | 1,78 | 1,78 | 0,60 | 2,97 | 0,99 | |||
Испытательный стенд | 1,20 | 1,20 | 0,60 | 2,00 | 1,00 | |||
ИТОГО | 8,40 |
|
|
Таксономические единицы (категории) растений: Каждая система классификации состоит из определённых соподчиненных друг другу...
Наброски и зарисовки растений, плодов, цветов: Освоить конструктивное построение структуры дерева через зарисовки отдельных деревьев, группы деревьев...
Археология об основании Рима: Новые раскопки проясняют и такой острый дискуссионный вопрос, как дата самого возникновения Рима...
Эмиссия газов от очистных сооружений канализации: В последние годы внимание мирового сообщества сосредоточено на экологических проблемах...
© cyberpedia.su 2017-2024 - Не является автором материалов. Исключительное право сохранено за автором текста.
Если вы не хотите, чтобы данный материал был у нас на сайте, перейдите по ссылке: Нарушение авторских прав. Мы поможем в написании вашей работы!