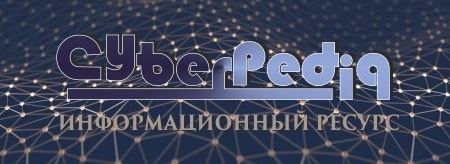
Индивидуальные и групповые автопоилки: для животных. Схемы и конструкции...
Автоматическое растормаживание колес: Тормозные устройства колес предназначены для уменьшения длины пробега и улучшения маневрирования ВС при...
Топ:
Установка замедленного коксования: Чем выше температура и ниже давление, тем место разрыва углеродной цепи всё больше смещается к её концу и значительно возрастает...
Характеристика АТП и сварочно-жестяницкого участка: Транспорт в настоящее время является одной из важнейших отраслей народного...
Процедура выполнения команд. Рабочий цикл процессора: Функционирование процессора в основном состоит из повторяющихся рабочих циклов, каждый из которых соответствует...
Интересное:
Средства для ингаляционного наркоза: Наркоз наступает в результате вдыхания (ингаляции) средств, которое осуществляют или с помощью маски...
Искусственное повышение поверхности территории: Варианты искусственного повышения поверхности территории необходимо выбирать на основе анализа следующих характеристик защищаемой территории...
Берегоукрепление оползневых склонов: На прибрежных склонах основной причиной развития оползневых процессов является подмыв водами рек естественных склонов...
Дисциплины:
![]() |
![]() |
5.00
из
|
Заказать работу |
|
|
Обработка результатов эксперимента проводилась по следующему алгоритму: на основании данных измерений производилась интегральная оценка скорости коррозии, проводился регрессионный анализ с целью выявления типа и определения количественных параметров регрессии, проводилась статистическая обработка результатов эксперимента с целью определения достоверности полученной модели.
Интегральная оценка скорости коррозии определялась как среднее арифметическое значение, полученное на трех образцах. Скорость коррозии K на каждом из образцов определялась по формуле:
(3. 1)
где m0 – масса образца до испытаний, кг;
m1 – масса образца после испытаний и удаления продуктов коррозии, кг;
S – площадь поверхности образца, м2;
t – продолжительность испытаний, сут.
Результаты испытаний сведены в таблицу 3.7.
Таблица 3.7 – Значения скорости коррозии участков сварного соединения магистральных трубопроводов
Продолжительность испытаний, сутки | |||||||||
№ образца | Участок соединения | Состояние образца | Скорость коррозии, кг/м2 год | ||||||
Сварной шов | Не обработан | 355,2236 | 352,4633 | 352,1107 | 350,0008 | ||||
После обработки | 346,4507 | 345,0628 | 342,9964 | 341,3131 | |||||
З.т.в. | Не обработан | 360,9462 | 360,1847 | 360,439 | 358,1937 | ||||
После обработки | 350,2849 | 348,7619 | 348,2532 | 347,3653 | |||||
Основной металл | Не обработан | 340,7967 | 339,7809 | 340,2896 | 338,1406 | ||||
После обработки | 337,7447 | 337,7462 | 337,236 | 333,8029 | |||||
Сварной шов | Не обработан | 354,0787 | 353,5856 | 353,5808 | 350,7477 | ||||
После обработки | 346,7099 | 345,2362 | 344,8802 | 342,0727 | |||||
З.т.в. | Не обработан | 361,1121 | 360,1223 | 360,1223 | 356,0789 | ||||
После обработки | 349,7225 | 350,4537 | 347,9735 | 346,0719 | |||||
Основной металл | Не обработан | 340,628 | 339,3629 | 339,8699 | 337,8968 | ||||
После обработки | 339,1118 | 337,0839 | 335,6885 | 335,0141 | |||||
Сварной шов | Не обработан | 353,9495 | 353,2514 | 351,3315 | 350,5039 | ||||
После обработки | 346,2701 | 345,2229 | 345,0484 | 344,1758 | |||||
З.т.в. | Не обработан | 362,8428 | 362,372 | 361,2079 | 360,0843 | ||||
После обработки | 350,7051 | 350,2474 | 349,3195 | 348,7914 | |||||
Основной металл | Не обработан | 342,9498 | 342,2489 | 342,364 | 340,7434 | ||||
После обработки | 341,548 | 340,8471 | 341,3126 | 339,2072 | |||||
|
Анализ представленных в таблице данных позволяет сделать следующие выводы:
· Скорость коррозии в рассмотренном интервале уменьшается на всех участках сварного соединения с течением времени как для образцов в исходном состоянии, так и для образцов, термически обработанных на оптимальном режиме. Эта тенденция может быть объяснена образованием на поверхности образцов окисной пленки, которая ограничивала доступ коррозионной среды к испытуемому материалу.
· Термическая обработка приводит к снижению скорости коррозии на всех участках сварного соединения. Данная тенденция может быть объяснена относительной гомогенизацией микроструктуры и снятием остаточных напряжений.
Проведенный регрессионный анализ показал, что функция изменения скорости коррозии на наблюдаемом этапе исследований может быть с достаточно высокой точностью описана линейным уравнением (графическое представление изменения скорости коррозии участков сварных соединений магистральных трубопроводов, претерпевших длительную эксплуатацию, до и после термической обработки на рис. 3.22-3.27). Для построения линии тренда использовался известный метод наименьших квадратов. Коэффициенты смещения линии регрессии и угловой коэффициент определялись согласно формулам [19 с. 198]:
(3.2)
(3.3)
где, хi – i-е значение выборки продолжительности испытаний;
yi – i-е значение выборки скорости коррозии.
![]() |
![]() |
![]() |
![]() |
![]() |
![]() |
|
Как видно из представленных графиков изменение скорости коррозии в результате термической обработки для разных участков сварного соединения отличается. Наиболее существенное снижение наблюдается для зоны термического влияния, менее значительное – для сварного шва и наименее заметное – для основного металла трубопровода. Данная тенденция коррелирует с изменениями в микроструктуре сварного соединения, где также наиболее заметные изменения в результате термической обработки наблюдаются зоне термического влияния (видманштеттова структура) и зоне столбчатых кристаллов в облицовочном шве. Релаксация внутренних напряжений в сварном соединении в таком случае и будет являться основной причиной снижения скорости коррозии в сварных соединениях магистральных трубопроводов после длительной эксплуатации.
Замедление скорости коррозии практически не изменяется для всех участков и мало зависит от факта проведения термической обработки образцов (линии тренда почти параллельны друг другу). Данное обстоятельство может быть объяснено методикой проведения эксперимента, когда образовывающийся слой оксидов, ограничивающий доступ коррозионной среды к исследуемому материалу, не удаляется полностью. В тоже время частичное удаление происходит благодаря низкой адгезии окисной пленки. Происходит падение продуктов коррозии под собственным весом на дно лабораторной установки, что обеспечивает относительное постоянство толщины слоя оксидов на поверхности металла и нивелирует более высокую скорость их роста для сварного шва и зоны термического влияния. Выявлено, что скорость коррозии основного металла возрастает с увеличением содержания углерода в стали (рис. 3.28). Сходные результаты получены и другими исследователями [154 с. 32]. В тоже время влияние углерода на коррозионную стойкость не значительно. При почти двукратном увеличении количества углерода в Стали 17ГС по сравнению со Сталью 09ГС скорость коррозии возрастает приблизительно на 1%.
|
В результате количественного анализа выявлено, что термическая обработка сварных соединений магистральных трубопроводов, проработавших длительное время, позволяет повысить коррозионную стойкость до 3,28% в зависимости от участка сварного соединения, что подробнее отражено в таблице 3.8.
Таблица 3.8 – Прирост коррозионной стойкости различных участков сварных соединений магистральных трубопроводов.
Участок сварного соединения | Состояние образца | Средняя скорость коррозии, кг/м2 год | Повышение коррозионной стойкости, % |
Сварной шов | Не обработан | 352,4496 | 2,41 |
После обработки | 343,9557 | ||
З.т.в. | Не обработан | 359,9409 | 3,13 |
После обработки | 348,6663 | ||
Основной металл | Не обработан | 339,7519 | 0,92 |
После обработки | 336,6325 | ||
Сварной шов | Не обработан | 352,9982 | 2,34 |
После обработки | 344,7247 | ||
З.т.в. | Не обработан | 359,3589 | 3,01 |
После обработки | 348,5554 | ||
Основной металл | Не обработан | 339,4394 | 0,8 |
После обработки | 336,7246 | ||
Сварной шов | Не обработан | 352,2591 | 2,01 |
После обработки | 345,1793 | ||
З.т.в. | Не обработан | 361,6267 | 3,28 |
После обработки | 349,7658 | ||
Основной металл | Не обработан | 342,0765 | 0,39 |
После обработки | 340,7287 |
Рис. 3.28 – Средняя скорость коррозии основного металла труб магистральных трубопроводов
Для оценки достоверности рассматриваемой гипотезы проводилась статистическая обработка полученных результатов. Определялись математическое ожидание (средние значения) экспериментальных данных:
– математические формулы [19 с. 193]:
(3.4)
(3.5)
где, n – количество проведенных испытаний;
дисперсия:
– математическая формула [26 с. 341]:
(3.6)
стандартное отклонение:
– математическая формула [26 с. 345]:
(3.7)
коэффициенты корреляции и вариации:
– математические формулы [26]:
(3.8)
(3.9)
Результаты проведенных расчетов для образцов в исходном состоянии (после длительной эксплуатации) и образцов, подвергшихся термической обработке по оптимальному режиму представлены в таблице 3.9.
|
Таблица 3.9 – Результаты статистической обработки эксперимента
№ образца | Участок соединения | Состояние образца | а | b | ![]() | ![]() | ![]() | ![]() | ![]() |
Сварной шов | Не обработан | -0,158 | 354,816 | 352,4496 | 3,4517 | 1,8579 | -0,9107 | 0,53 | |
После обработки | -0,176 | 346,6 | 343,9557 | 3,8386 | 1,9592 | -0,9647 | 0,57 | ||
З.т.в. | Не обработан | -0,091 | 361,309 | 359,9409 | 1,0927 | 1,0453 | -0,936 | 0,29 | |
После обработки | -0,089 | 350,003 | 348,6663 | 1,1231 | 1,0598 | -0,902 | 0,3 | ||
Основной металл | Не обработан | -0,084 | 341,009 | 339,7519 | 0,9944 | 0,9972 | -0,9012 | 0,29 | |
После обработки | -0,147 | 338,835 | 336,6325 | 2,712 | 1,6468 | -0,956 | 0,49 | ||
Сварной шов | Не обработан | -0,117 | 354,749 | 352,9982 | 1,7292 | 1,315 | -0,9516 | 0,37 | |
После обработки | -0,153 | 347,019 | 344,7247 | 2,815 | 1,6778 | -0,9775 | 0,49 | ||
З.т.в. | Не обработан | -0,173 | 361,955 | 359,3589 | 3,7495 | 1,9364 | -0,9587 | 0,54 | |
После обработки | -0,15 | 350,803 | 348,5554 | 2,8681 | 1,6935 | -0,9488 | 0,49 | ||
Основной металл | Не обработан | -0,083 | 340,689 | 339,4394 | 0,9959 | 0,9979 | -0,8955 | 0,29 | |
После обработки | -0,128 | 338,654 | 336,7246 | 2,4567 | 1,5674 | -0,8759 | 0,47 | ||
Сварной шов | Не обработан | -0,122 | 354,095 | 352,2591 | 1,9458 | 1,3949 | -0,941 | 0,4 | |
После обработки | -0,064 | 346,141 | 345,1793 | 0,554 | 0,7443 | -0,9238 | 0,22 | ||
З.т.в. | Не обработан | -0,098 | 363,102 | 361,6267 | 1,1472 | 1,0711 | -0,9846 | 0,3 | |
После обработки | -0,067 | 350,767 | 349,7658 | 0,5657 | 0,7521 | -0,952 | 0,22 | ||
Основной металл | Не обработан | -0,072 | 343,159 | 342,0765 | 0,663 | 0,8143 | -0,9502 | 0,24 | |
После обработки | -0,076 | 341,874 | 340,7287 | 0,8353 | 0,9139 | -0,8959 | 0,27 |
Из представленных данных видно, что модуль коэффициента корреляции находиться в диапазоне от 0,8759 до 0,9846. Следовательно, характер взаимного стохастического влияния изменения полученных в результате эксперимента случайных величин может быть оценен как сильный. Абсолютные (стандартное и среднеквадратическое отклонение) и относительные показатели (коэффициент вариации) вариации скорости коррозии малы. Экспериментальные значения исследуемой величины находятся в среднем в интервале . Это свидетельствует о незначительном рассеивании значений скорости коррозии. Изменение коэффициентов регрессии, корреляции и показателей вариации после термической обработки не имеет закономерности.
Таким образом, высокий отпуск по предложенному оптимальному режиму приводит не только к восстановлению ударной вязкости трубного материала, претерпевшего длительную эксплуатацию, но и к снижению скорости коррозии до 3,28%. Повышение коррозионной стойкости наблюдается на всех участках сварного соединения, что может быть объяснено относительной гомогенизацией микроструктуры и снятием остаточных напряжений. Наиболее существенное снижение наблюдается для зоны термического влияния, менее значительное – для сварного шва и минимальное – для основного металла трубопровода. Данная тенденция коррелирует с изменениями в микроструктуре сварного соединения, где также наиболее заметные изменения в результате термической обработки наблюдаются зоне термического влияния (видманштеттова структура) и зоне столбчатых кристаллов в облицовочном шве. Релаксация внутренних напряжений в сварном соединении в таком случае и будет являться основной причиной снижения скорости коррозии в сварных соединениях магистральных трубопроводов после длительной эксплуатации. Вышеизложенное позволяет рекомендовать проведение высокого отпуска с целью повышения эксплуатационных свойств материала сварных соединений магистральных трубопроводов, претерпевших длительную эксплуатацию.
|
Выводы по главе 3
1. Определен оптимальный режим термической обработки кольцевых сварных соединений магистральных трубопроводов, после длительной эксплуатации, заключающийся в нагреве до 680˚С, выдержки в течении 30 минут и дальнейшем охлаждении на спокойном воздухе.
2. Установлено, что предложенная обработка приводит к существенному росту значений ударной вязкости , характеризующей уровень надежности сварного соединения магистрального трубопровода, и незначительному снижению предела текучести
и предела прочности
, которое может не учитываться при проведении прочностных расчетов. Изменения механических характеристик подтверждаются соответствующими изменения в микроструктуре.
3. Установлено, что предложенная термическая обработка – высокий отпуск на оптимальных режимах также несколько повышает коррозионную стойкость (до 3,28%) основного металла и сварных соединений магистральных трубопроводов. При этом наиболее существенное снижение скорости коррозии наблюдается для зоны термического влияния, менее значительное – для сварного шва и минимальное – для основного металла трубопровода. [3-А, 5-А, 6-А, 10-А, 11-А]
ГЛАВА 4. ЭКСПРЕСС-МЕТОД ОПРЕДЕЛЕНИЯ МЕХАНИЧЕСКИХ ХАРАКТЕРИСТИК СВАРНОГО СОЕДИНЕНИЯ МАГИСТРАЛЬНОГО ТРУБОПРОВОДА
4.1 Необходимость определения механических свойств материалов магистральных трубопроводов
Обеспечение надежной и безопасной работы магистральных трубопроводов возможно при использовании эффективных методов контроля его напряженно-деформированного состояния. В настоящее время расчет трубопроводов производиться в соответствии со СНиП 2.05.06 [69]. В соответствии с этим техническим нормативным правовым актом подземные трубопроводы проверяют на прочность, способность деформироваться и устойчивость в продольном направлении. В тоже время данная методика не учитывает возможный опасный переход металла от механизма вязкого разрушения к хрупкому разрушению при снижении вязкопластических свойств. Значения характеристик относительного удлинения и ударной вязкости, которые имеют пониженные значения в сварном шве и зоне термического влияния не принимаются во внимание, также как и возникающая концентрация напряжений у стыковых сварных соединений труб и продольного шва. Не учитываются остаточные напряжения, возникающие после сварки листов на заводе изготовителе и сварки стыков труб при соединении труб во время сооружения трубопровода.
Большая часть необходимых для расчета данных представляет собой случайные величины, которые рассеиваются в определенных пределах. Изменяется рабочее давление перекачиваемой среды, которое в некоторые промежутки времени может даже превосходить расчетное. Значительное рассеивание имеют механические характеристики металла трубы, которые могут существенно отличаться от характеристик исходного листа. В результате анализа выбранных случайным образом 600 сертификатов, имеющихся в ЧУП «Запад-Транснефтепродукт» на поставленные трубы нами было выявлено, что отношение между минимальным и максимальным значением для предела текучести составляет 1,4 раза, для предела прочности – 1,46 раза, относительного удлинения – 1,83 раза, ударной вязкости более чем в 5 раз. Результаты исследований, приведенные во второй главе, также подтверждают значительный разброс механических характеристик у основного металла магистральных трубопроводов претерпевших длительную эксплуатацию и еще более существенный разброс у сварных соединений.
Материал исходного прокатанного листа контролировался в основном по 2-5 образцам, вырезаемых из одной плавки, и испытываемых на растяжение. Контроль ударной вязкости проводился факультативно. При последующем «изгибе» листа в длинное полукольцо и сварке этих полуколец основной металл трубы подвергается значительному наклепу, в результате которого повышаются пределы прочности и текучести, снижаются относительное удлинение и ударная вязкость. В сварных соединениях образуются остаточные напряжения и зоны с отличными от основного металла свойствами. В процессе эксплуатации протекают процессы старения, которые также отражаются на показателях механических свойств материала магистральных трубопроводов. Существенное влияние также оказывает и коррозионные процессы, в результате действия которых, появляются повреждения самого различного вида (коррозионные пятна, щели, серии микро или макротрещин).
Таким образом, у эксплуатирующих магистральные трубопроводы организаций фактически отсутствуют адекватные данные о механических свойствах материала трубопровода. Поэтому оценка напряженно-деформированного состояния в локальных областях проводиться только на основании геометрических параметров трубопровода и усредненных данных механических свойств материала, что в некоторых случаях может привести к возникновению аварийной ситуации. В связи с этим для принятия обоснованного решения, обеспечивающего достаточный уровень надежности и безопасности магистрального трубопровода, необходима точная информация о механических свойствах металла в локальных участках.
Традиционно механические свойства определяются с помощью машин для испытаний на растяжение, усталость и маятникового копра на вырезаемых из конструкции образцах. В тоже время вырезка темплетов материала для получения образцов не целесообразна, так как длина вырезки может совпадать, или превышать длину обследуемого участка, что приведет к его замене, и вопрос изучения механических свойств материала не будет иметь практической выгоды. Кроме того, вырезка образцов сопряжена с последующим дорогостоящим ремонтом магистрального трубопровода. Поэтому актуальной задачей является совершенствование методов определения механических характеристик, и в первую очередь ударной вязкости, магистральных трубопроводов неразрушающими методами.
4.2 Неразрушающие методы определения механических свойств трубопроводных материалов
В течение эксплуатации вследствие воздействия совокупности факторов различной природы и интенсивности происходит изменение ряда параметров оборудования и конструкций. Это обуславливает необходимость адекватной оценки их технического состояния с целью обеспечения надежности и безопасности функционирования. При оценке изменения механических свойств материала в основном используют стандартные методы испытания макропроб отобранных образцов в соответствии с требованиями действующих технических нормативных правовых актов. В тоже время при проведении диагностических работ не всегда имеется возможность вырезки темплета материала для исследования в лабораторных условиях. Кроме того, практика показывает, что часто возникают разрушения именно в тех местах, где до этого проводились работы по изъятию образцов. Эти обстоятельства привели к развитию неразрушающих методов контроля механических свойств. Наибольшее распространение среди них получили методы, основанные на измерении твердости. Это объясняется простотой применения и высокой производительностью данного неразрушающего метода механических испытаний [30 С.]. Создано множество видов и модификаций стационарных и переносных приборов для измерения твердости, отличающихся принципом действия, областью применения, а также массой и габаритными размерами. Особая роль в расширении возможностей принадлежит переносным твердомерам, позволяющим определять твердость на эксплуатируемых конструкциях любой формы, размеров в любом пространственном положении и при этом используют меньшие нагрузки по сравнению со стационарными приборами [74].
Из множества статических способов определения твердости наиболее удобными и широко применяемыми в заводских и исследовательских лабораториях являются методы Бринелля, Роквелла и Виккерса, которые предусматривают вдавливание соответственно закаленного стального шарика, алмазного конуса с углом при вершине 120˚ и алмазной пирамиды с квадратным основанием и углом между противоположными гранями 136˚ [76, 77, 78], а наиболее распространенным динамическим является метод Шора [75], в котором о твердости судят по высоте отскока бойка с коническим или сферическим алмазным индентором. Каждый из указанных способов имеет свою область применения в зависимости от толщины образцов, их пластичности, твердости.
В результате сравнительного анализа указанных методов выявлено, что определение твердости по Виккерсу позволяет получить большее количество информации об исследуемом материале, чем при определении другими методами. Это связано с тем, что отпечатки и волна вокруг них, полученные при взаимодействии конического или сферического индентора (методы Бринелля, Шора, Роквелла) с исследуемым материалом, имеют вертикальную ось симметрии, а их проекция на горизонтальную плоскость представляет круг. Поэтому по проекциям этих отпечатков нельзя сделать дополнительных заключений о механических свойствах металла [22 С.]. Существующие корреляционные уравнения связывают в основном твердость, определенную по одному из данных методов, с величинами предела прочности и предела текучести [5, 73, 122, 142]. Наибольшее распространение получили линейные зависимости вида:
, МПа (4.1)
, МПа (4.2)
где, – коэффициенты пропорциональности, зависящие от материала.
Таким образом, методы Роквелла, Шора и Бринеля не позволяют получить информацию о пластических свойствах материалов, что ограничивает их возможности для оценки технического состояния конструкций.
В отличие от указанных методов, проекции на горизонтальную плоскость пирамидальных отпечатков полученные при определении твердости по Виккерсу имеют форму близкую к квадрату с выпуклыми или вогнутыми сторонами.
а) б)
а — отпечаток с вогнутыми гранями; б — отпечаток с выпуклыми гранями
Рисунок 4.1 – Форма отпечатков, полученных при внедрении в материал алмазной пирамиды с углом между противоположными гранями 136°: D — диагональ отпечатка; S — ширина отпечатка. []
Отпечаток с выпуклыми гранями характерен для пластичных материалов (например, отожженной стали). Отпечаток с вогнутыми гранями характерен для материалов с высокой твердостью (сталь, упрочненная пластическим деформированием, закаленная сталь). Металл кольцевых сварных соединений магистрального трубопровода, после длительной эксплуатации имеет преимущественно среднюю твердость и для него характерны отпечатки без значительных искажений.
Рисунок 4.2 – Типичная форма отпечатка пирамидального индентора на трубной стали (200х)
Сила, действующая при вдавливании на центр, больше сил в угловых точках проекции пирамиды, соответственно и величина деформации в этой центре больше. Следовательно, деформация металла около стороны отпечатка распределяется так, что в центре стороны она достигает максимальных значений, постепенно уменьшаясь к краям. Таким образом, форма отпечатка свидетельствует о способности материала воспринимать пластическую деформацию и ее изменение коррелирует с изменениями пластических свойств металла. [21, 45] В работах [43, 44] приведены корреляционные взаимосвязи твердости НV и параметрами пирамидального отпечатка (диагональ и ширина) механическими характеристиками (σВ, δ5, ψ). Уравнения взаимосвязи имеют вид:
, МПа (4.3)
, отн. ед. (4.4)
, отн. ед. (4.5)
Где, k — коэффициент кратности (для нагрузки, равной 1000 Н (100 кг); 500 Н (50 кг); 300 Н (30 кг); 200 Н (20 кг); 100 Н (10 кг) и 50 Н (5 кг). Величина коэффициента k составляет 1; 1,414; 1,825; 2,235; 3,161 и 4,472 соответственно.
Таким образом, измерение твердости по Виккерсу по зависимостям 4.3-4.5 позволяет оценивать как прочностные, так и пластические свойства исследуемого материала неразрушающим способом. В тоже время в отличие от ударной вязкости, данные характеристики в процессе эксплуатации магистральных трубопроводов изменяются не значительно. Следовательно, необходимо разработать способ определения ударной вязкости сварных кольцевых соединений магистральных трубопроводов, претерпевших длительную эксплуатацию.
|
|
Кормораздатчик мобильный электрифицированный: схема и процесс работы устройства...
История развития пистолетов-пулеметов: Предпосылкой для возникновения пистолетов-пулеметов послужила давняя тенденция тяготения винтовок...
Биохимия спиртового брожения: Основу технологии получения пива составляет спиртовое брожение, - при котором сахар превращается...
Механическое удерживание земляных масс: Механическое удерживание земляных масс на склоне обеспечивают контрфорсными сооружениями различных конструкций...
© cyberpedia.su 2017-2024 - Не является автором материалов. Исключительное право сохранено за автором текста.
Если вы не хотите, чтобы данный материал был у нас на сайте, перейдите по ссылке: Нарушение авторских прав. Мы поможем в написании вашей работы!