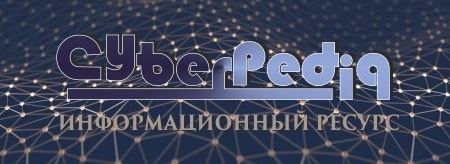
Своеобразие русской архитектуры: Основной материал – дерево – быстрота постройки, но недолговечность и необходимость деления...
Механическое удерживание земляных масс: Механическое удерживание земляных масс на склоне обеспечивают контрфорсными сооружениями различных конструкций...
Топ:
Процедура выполнения команд. Рабочий цикл процессора: Функционирование процессора в основном состоит из повторяющихся рабочих циклов, каждый из которых соответствует...
Оценка эффективности инструментов коммуникационной политики: Внешние коммуникации - обмен информацией между организацией и её внешней средой...
Марксистская теория происхождения государства: По мнению Маркса и Энгельса, в основе развития общества, происходящих в нем изменений лежит...
Интересное:
Подходы к решению темы фильма: Существует три основных типа исторического фильма, имеющих между собой много общего...
Берегоукрепление оползневых склонов: На прибрежных склонах основной причиной развития оползневых процессов является подмыв водами рек естественных склонов...
Лечение прогрессирующих форм рака: Одним из наиболее важных достижений экспериментальной химиотерапии опухолей, начатой в 60-х и реализованной в 70-х годах, является...
Дисциплины:
![]() |
![]() |
5.00
из
|
Заказать работу |
|
|
Мировые прогнозные запасы природного газа по разным оценкам достигают 200-300 трлн. м3, в том числе разведанные – более 100 трлн. м3. В России сосредоточено более 30% мировых запасов природного газа.
Перевод автомобильного транспорта на газовые топлива осуществляется во всех развитых странах мира. Существуют проекты и образцы автомобильных газонаполнительных компрессорных станций (АГНКС) различной производительности, разработано и производится облегченное в 2-3 раза газобаллонное оборудование из композитных материалов. Используемый СНГ (пропан-бутан) в настоящее время для заправки автомобилей нельзя считать перспективным топливом для двигателей внутреннего сгорания из-за его дефицитности. Это ценное нефтехимическое сырье, получаемое в ограниченном количестве при добыче и переработке нефти.
Наиболее перспективны как моторные топлива это КПГ и особенно СПГ. Более далекой перспективой является применение в качестве моторного топлива жидкого водорода. Газовые топлива являются полноценными заменителями автомобильного бензина и частично – дизельного. Природный газ уступает нефтяным топливам по самовоспламеняемости, его применение в дизелях возможно только в сочетании с запальным количеством до 20% дизельного топлива. Ограничения применения сжиженного природного газа – СПГ возникают из-за трудностей хранения, заправки, усложнения конструкции топливных систем и криогенных топливных баков (в т.ч. увеличения объемов).
Использование природного газа в качестве моторного топлива резко сокращает токсичность отработавших газов и загрязнение окружающей среды продуктами сгорания топлив. Кроме того, увеличиваются в 1,4-1,8 раза ресурс работы двигателей, на 40-50% – свечей зажигания и в 2-2,5 раза – срок службы моторного масла. Себестоимость производства топлив из природного газа в 2-3 раза ниже, чем топлив из нефти. В то же время газовые топлива практически не превосходят нефтяные по энергетическим показателям, т.к. теплота сгорания стехиометрической смеси топливо/воздух для всех видов топлив близки и находятся в пределах 2,8-3,4 МДж/кг (3,0-3,6 МДж/л).
|
1.7. Что называют кислыми газами, зачем природный газ очищают от кислых компонентов
Кислыми газами называют сернистые компоненты газа и диоксид углерода. Среди сернистых компонентов чаще всего встречаются сероводород, меркаптаны, серооксид углерода, сероуглерод и сульфиды. Содержание сероводорода в добываемых газах колеблется в широких пределах - от нескольких долей до нескольких десятков процентов. Сернистые соединения отравляют катализаторы в процессах переработки газа, при сгорании образуют оксиды серы, содержание которых в воздушном бассейне опасно для человека и окружающей среды, вызывает коррозию газопроводов и аппаратуры, весьма ядовиты для человека и животных. Поэтому в газе, подаваемом потребителям, должно содержаться сероводорода не более 5,7 мг/м3 газа и общей серы - не более 50 мг/м3 газа.Диоксид углерода снижает теплотворную способность газа, уменьшает пропускную способность газопроводов (так как является балластом для топливного газа) и так же, как и сернистые соединения, вызывает коррозию трубопроводов и оборудования. Объемное содержание диоксида углерода в газе, поставляемом потребителям, должно составлять не более 2-5%.
В то же время сернистый компоненты природного- газа, и в первую очередь сероводород, являются прекрасным сырьем для производства элементной серы.Диоксид углерода используется для производства твердой углекислоты, в качестве консерванта при хранении сельскохозяйственной продукции, при сварке металлов и для других целей.
Принципиальная технологическая схема однопоточной абсорбционной очистки газа растворами этаноламинов приведена на рис.4 1. Поступающий на очистку газ I проходит восходящим потоком через абсорбер 1 навстречу потоку регенерированного абсорбента V. Насыщенный кислыми газами раствор абсорбента VI, выходящий с низа абсорбера, подогревается в теплообменнике 5 регенерированным раствором из десорбера 6 и подается на верх его. После частичного охлаждения в теплообменнике 5 регенерированный раствор дополнительно охлаждается в холодильнике 3 и подается на верх абсорбера 1.
|
Тепло, необходимое для регенерации насыщенного раствора, сообщается последнему в рибойлерах, обогреваемых водяным паром. Кислый газ из десорбера охлаждается для конденсации содержащихся в нем водяных паров. Конденсат этих паров из сепаратора 8 возвращают в десорбер 6 несколько выше входа насыщенного раствора амина.
В схеме предусмотрен экспанзер (выветриватель) 4, в котором за счет снижения давления насыщенного раствора выделяются физически растворенные в абсорбенте углеводороды и частично сероводород и диоксид углерода Экспан-зерный газ III после очистки используется в качестве топливного газа или ком-примируется и подается в исходный газ I.
В представленной на рис. 4.1 схеме регенерированный абсорбент подается одним потоком (поэтому схема названа однопоточной) на верхнюю тарелку абсорбера. Однако, помимо описанной, в промышленности широкое распространение получила схема с раздельными потоками подачи в абсорбер регенерированного абсорбента одинаковой степени регенерации: 70-80% раствора абсорбента подается в середину абсорбера, а остальное количество - на верхнюю тарелку. Это позволяет снизить затраты энергии на перекачку раствора абсорбента, уменьшить металлоемкость абсорбера (абсорбер имеет меньший диаметр выше тарелки ввода абсорбента в его середине из-за меньших жидкостных нагрузок на тарелках), а также повысить степень извлечения COS за счет подачи среднего потока раствора абсорбента с более высокой температурой и осуществления реакции гидролиза COS
1.8. Получение и утилизация сероводорода. Источники и методы получения. Производство серы методом Клауса и его модификации.
Извлекаемая из природного газа смесь кислых газов наполовину и более по объему состоит из сероводорода. Остальная часть включает углекислый газ и небольшие количества серооксида углерода и УВ (метан, этан). Эта смесь кислых газов утилизируется обычно на месте очистки природного газа с целью получения из него элементной серы.
|
Основным процессом получения серы из сероводорода уже более 100 лет (с 1882г.) является процесс Клауса, основанный на следующих реакциях окисления. При двухстадийном окислении: 2Н2S+3O2→2SO2+2H2O; 2H2S+SO2→3S+2H2O Одновременно с таким двухстадийным образованием серы протекает реакция прямого окисления: 2H2S+O2→2S+2H2O
Поскольку в составе кислых газов кроме сероводорода присутствуют другие компоненты, в процессе горения протекают также следующие побочные реакции: CO2+H2S→COS+H2O; CH4+S2→CS2+2H2
Технология получения серы методом Клауса реализует указанные выше реакции обычно в три ступени.
Технологическое оформление процесса зависит при этом от состава кислого газа- содержания в нем сероводорода и углеводородов. Принципиальная схема производства серы методом Клауса показана на рис. По этой схеме почти весь кислый газ (95-98%) подается на первую термическую ступень конверсии, представляющую собой паровой котел газотрубного типа. В зоне горения 1 (топке) этого котла поддерживается температура около1100С, которая снижается до 350С после прохождения трубного пучка, где генерируется водяной пар высокого давления (2,0-2,5 МПа). Затем газ охлаждается в конденсаторе 3 до 185С и поступает на вторую ступень. Из низкотемпературных зон термического реактора и охладителя 3 через серозатворы выводится из системы жидкая сера. Максимальный выход серы на первой ступени составляет 60-70% от общего ее выхода. Вторая ступень состоит из печи 4 для сжигания оставшейся части кислого газа и превращения оксида серы, содержащегося в газе после первой ступени. Реакции на этой ступени протекают при температуре 240-250С в каталитическом реакторе 5, заполненным специальным катализатором (активированный оксид алюминия). В последнее время стали широко применяться катализаторы на основе диоксида титана (содержание TiO2>85%). На выходе из реактора 5 температура достигает около 330С, и газ затем охлаждается в охладителе до 170С с выделением из него сконденсированной серы. Газ из охладителя 6 поступает на третью ступень, вначале в печь 7, где его температура повышается до 220С (за счет горения топливного газа lll), затем газ проходит каталитический реактор 8, в котором температура газа повышается на 20-30С (до 250С). После этого газ снова охлаждается в охладителе 9, из которого сконденсированная сера отводится через серозатвор, а уходящий газ через сепаратор 10 направляется на дожиг в печь 11. В этой печи при 500-550С дожигаются остатки непрореагировавшего сероводорода, после чего хвостовой газ 7 выбрасывается через дымовую трубу. С целью снижения загрязнения атмосферы на многих установках Клауса используют блок очистки хвостового газа на блоке СКОТ12- абсорбционным поглощением SO2 раствором сульфанола и диизопропаноламина.
|
1.9 Принципиальные схемы блоков АТ установок. Режим работы отбензинивающей и основной колонн, продукты АТ и их использование. Какими критериями руководствуются при выборе варианта тех-ой схемы при ППН.
АТ- атмосферная трубчатая установка, предназначенная для получения светлых нефтепродуктов, выкипающих до 350С (бензин, керосин, ДТ), а также для получения мазута-сырья для вторичных процессов переработки нефти.
Сырьём установки является нефть, газоконденсат.
В зависимости от качества сырья и от производительности установки существует несколько вариантов схем.
1. схема с однократным испарением и однократной ректификацией
-содержание серы меньше 0,5%
- содержание бензиновой фракции меньше 10%
- производительность установки меньше 1 млн. т/год
Установка состоит из одной сложной ректификационной колонны
2.Схема с двукратным испарением и однократной ректификацией
Данная схема используется если
-содержание серы меньше 0,5%
- содержание бензиновой фракции больше 10%
- производительность установки меньше 1,5 млн. т/год
В данной схеме перед сложной ректификационной колонной устанавливается испаритель
(эвапоратор)-пустотелый аппарат, сверху которого отбирается смесь паров бензина и газа.
3.Схема с двукратным испарением и двукратной ректификацией.
-содержание серы больше 0,5%
- содержание бензиновой фракции меньше 10%
- производительность установки больше 1,5 млн. т/год
Данная установка состоит из отбензинивающей и сложной ректификационной колонны.
На современных НПЗ в большинстве случаев используется третий вариант переработки.
Недостаток двухколонной схемы – большой расход дополнительного тепла, подводимого «горячей струёй»,след-но большие капитальные и эксплуатационные затраты. Недостатак одноколонной схемы- нефть поступает в колонну вместе с растворенными в ней газами и легкими фракциями,сл-но требуется увеличить диаметр и поверхность конденсатора для конденсации газобензиновых паров, выходящих сверху колонны.
|
Назначение отбензинивающей колонны – извлечение из нефти растворенного в ней газа и легкой бензиновой фракции с tк.к =85С (или 120С). Число тарелок = 20-25, D=3,6-4 м, t верха колонны 110-115С, t низа 240-260С. В низ отбензинивающей колонны подводится поток тепла в виде «горячей струи» для повышения четкости выделения при кратности орошения 1,5-2. Давление в колонне составляет 0,35-0,5МПа. Отбензиненная нефть снизу колонны прокачивается насосом и поступает в трубчатую печь, где нагревается до 350С. 15-20% отбензиненой нефти возвращается в нижнюю часть отбензинивающей колонны (ГС) для создания потока паров в отгонной части, а остальная часть отбензиненой нефти поступает в атмосферную колонну (число тарелок=40-45,D=6,5-7 м), которая предназначена для разделения предварительно отбензиненой нефти на несколько светлых (топливных фракций (бензин 120-180, керосин 140-230, дт 200-350) и мазут. Давление в колонне поддерживается порядка 0,14-0,16МПа. В стипингах обычно по 4 тарелки. Вниз атмосферной колонны вводят ВП, для уменьшения парциального давления УВ сырья. t верха колонны 120С, t низа 300С.
Продукты:
В атмосферной части схема перегонки может быть одноколонной - А-1 и двухколонной - А-2 (с предварительным отбензиниванием нефти). Выбор той или иной из них зависит в первую очередь от типа нефти и ее класса (особенно по содержанию меркаптановой серы) и от содержания в нефти растворенных газов. Каждая из этих схем имеет достоинства и недостатки, о которых будет сказано далее (см. раздел 10.1).
К схеме 2:
Варианты энергосберегающих схем глубокой атмосферной перегонки нефти:
1-4 - ректификационные колонны: отбензинивающая, бензиновая, основная атмосферная и испарительная; 5 - испарители-сепараторы; 6 - печи; 7 - теплообменники; 8 - эжекторы; /- нефть; Я- отбензиненная нефть: ///- углеводородный газ; IV- бензин; V - керосин; VI - дизельное топливо; VII - тяжелый компонент дизельного топлива; VIII - тяжелая флегма; IX - мазут, X - утяжеленный мазут; XI - водяной пар.
|
|
Своеобразие русской архитектуры: Основной материал – дерево – быстрота постройки, но недолговечность и необходимость деления...
Папиллярные узоры пальцев рук - маркер спортивных способностей: дерматоглифические признаки формируются на 3-5 месяце беременности, не изменяются в течение жизни...
История развития пистолетов-пулеметов: Предпосылкой для возникновения пистолетов-пулеметов послужила давняя тенденция тяготения винтовок...
Индивидуальные и групповые автопоилки: для животных. Схемы и конструкции...
© cyberpedia.su 2017-2024 - Не является автором материалов. Исключительное право сохранено за автором текста.
Если вы не хотите, чтобы данный материал был у нас на сайте, перейдите по ссылке: Нарушение авторских прав. Мы поможем в написании вашей работы!