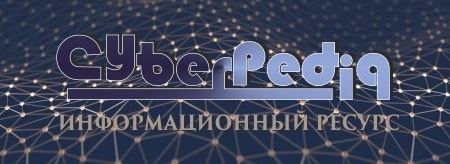
Состав сооружений: решетки и песколовки: Решетки – это первое устройство в схеме очистных сооружений. Они представляют...
Адаптации растений и животных к жизни в горах: Большое значение для жизни организмов в горах имеют степень расчленения, крутизна и экспозиционные различия склонов...
Топ:
Методика измерений сопротивления растеканию тока анодного заземления: Анодный заземлитель (анод) – проводник, погруженный в электролитическую среду (грунт, раствор электролита) и подключенный к положительному...
Установка замедленного коксования: Чем выше температура и ниже давление, тем место разрыва углеродной цепи всё больше смещается к её концу и значительно возрастает...
Выпускная квалификационная работа: Основная часть ВКР, как правило, состоит из двух-трех глав, каждая из которых, в свою очередь...
Интересное:
Инженерная защита территорий, зданий и сооружений от опасных геологических процессов: Изучение оползневых явлений, оценка устойчивости склонов и проектирование противооползневых сооружений — актуальнейшие задачи, стоящие перед отечественными...
Уполаживание и террасирование склонов: Если глубина оврага более 5 м необходимо устройство берм. Варианты использования оврагов для градостроительных целей...
Мероприятия для защиты от морозного пучения грунтов: Инженерная защита от морозного (криогенного) пучения грунтов необходима для легких малоэтажных зданий и других сооружений...
Дисциплины:
![]() |
![]() |
5.00
из
|
Заказать работу |
|
|
При деформации металла с нагревом одновременно протекают как упрочняющие (за счет повышения плотности дислокаций, вытянутости зерен и др.), так и разупрочняющие процессы (за счет повышения температуры).
Разупрочняющие процессы подразделяются на статические, происходящие при нагреве холоднодеформированного металла, и динамические, происходящие в процессе деформации нагретого металла.
Динамические разупрочняющие процессы значительно отличаются от статических. Так как пластическая деформация облегчает протекание диффузионных процессов, то энергия активации динамических разупрочняющих процессов ниже, чем у статических. Благодаря этому значительно возрастает подвижность дислокаций и в результате динамические разупрочняюшие процессы протекают с более высокой скоростью, чем статические.
Различают следующие стадии разупрочнения металла при деформации с нагревом: возврат, полигонизация и рекристаллизация.
Возврат протекает при температурах деформации Т В=(0,2–0,3) Т ПЛ, приводит к частичному уменьшению упругих искажений кристаллической решетки за счет перераспределения дислокаций, главным образом путем поперечного скольжения винтовых дислокаций.
Возврат несколько повышает пластичность и вязкость металла без снижения его прочности. Однако деформирование стали при температурах возврата сопровождается упрочнением, хотя интенсивность его несколько меньше.
При температурах возврата деформация стали может сопровождаться старением, которое приводит к некоторому увеличению прочности и снижению пластичности. При возврате сохраняется вытянутая структура и текстура деформации зерен.
Полигонизация протекает при температурах деформации Т П=(0,3–0,4) Т ПЛ, сопровождается образованием новых малоугловых границ в виде вытянутых дислокационных скоплений в пределах каждого деформированного зерна металла, в результате чего формируются субзерна, то есть полигонизация вызывает структурные изменения за счет образования субструктуры (рис. 19).
|
Рис. 19. Субграницы дислокационные. ´15000
Скорость полигонизации увеличивается с увеличением степени и температуры деформации. Первый фактор ускоряет поперечное скольжение винтовых дислокаций, второй – диффузию атомов. Полигонизация сопровождается частичной аннигиляцией дислокаций, которая происходит таким образом, что часть беспорядочно рассеянных противоположных по знаку дислокации самоуничтожается (аннигилирует), а другая часть перераспределяется с образованием субграниц. Полигонизация приводит (за счет снижения плотности дислокаций) к заметному понижению прочности и повышению пластичности сплава. Однако появление субграниц вызывает некоторое упрочнение сплава, что используется при механико-термической обработке.
Рекристаллизация - зарождение и рост новых зерен по границам деформированных зерен, приводящее к образованию равноосной структуры металла, протекает при температурах деформации Т Р > 0,5 Т ПЛ. Зарождение новых зерен происходит в местах с наибольшей плотностью дислокаций, обычно на границах деформированных зерен. Образовавшиеся зародыши растут до взаимного соприкосновения, что соответствует стадии первичной рекристаллизации. При дальнейшем повышении температуры или длительности выдержки протекает собирательная рекристаллизация, которая заключается в укрупнении одних зерен за счет других путем миграции границ зерен.
Движущей силой собирательной рекристаллизации служит уменьшение свободной энергии зерен за счет уменьшения их поверхностной энергии. Сильно деформированные зерна имеют большую свободную энергию и будут поглощаться менее деформированными и более стабильными зернами.
|
Знание теории разупрочняющих процессов позволяет путем выбора соответствующих температуры, скорости и степени деформации в широких пределах управлять структурой сплава, а следовательно, и его механическими свойствами.
На рост зерна, кроме температуры и состава сплава, большое влияние оказывает степень предварительной деформации.
При небольших степенях деформации КР=1,5–10%, называемых критическими, в процессе рекристаллизации зерно приобретает очень большие размеры, что обусловливается неоднородностью деформации зерен при этих степенях деформации (рис. 20).
Рис.20.Влияние степени деформации на размер рекристаллизационного зерна
Законы рекристаллизации:
- рекристаллизация протекает только у деформированного металла;
-чем выше степень деформации, тем ниже температура начала
рекристаллизации и размер рекристаллизованного зерна;
- новые зерна не могут поглощать деформированные зерна идентичной
или слегка отличающейся ориентации;
- наличие примесей и легирующих приводит к повышению температуры начала рекристаллизации сплава.
Виды деформации в зависимости от температуры нагрева
Горячая при Т ДЕФ=0,6–0,8 Т ПЛ (выше А 3 или Аcm), в течении которой металл полностью разупрочняется за счет полного протекания процессов рекристаллизации.
Полугорячая протекаетпри Т ДЕФ=0,4–0,6 Т ПЛ (ниже А 1 или А 3), при которой процессы рекристаллизации протекают частично, не полностью, и структура металла состоит из равноосных рекристаллизованных зерен и вытянутых деформированных нерекристаллизованных зерен.
Теплая протекает при Т ДЕФ=0,2–0,4 Т ПЛ, при которой деформируемость несколько улучшается за счет процессов возврата (поперечного скольжения винтовых дислокаций), структура металла не изменяется, остается деформированной или полигонизованной.
Холодная протекает при комнатной температуре, или Т ДЕФ< 0,2 Т ПЛ. Структура деформированная, с вытянутыми зернами, наклепанная, т.е. упрочненная за счет деформации в результате повышения плотности дислокаций и других дефектов кристаллической решетки.
Влияние температуры нагрева
на механические свойства сплавов
Температурный интервал обработки давлением выбирают с учетом диаграммы состояния сплава так, чтобы металл находился в однофазном состоянии. В двух- или многофазном состоянии при низкой пластичности одной из фаз возможно разрушение металла. Исключение представляют доэвтектоидные стали, которые при температурах двухфазного состояния между линиями GS и PS (диаграммы состояния Fe–C)обладают достаточно высокой пластичностью.
|
Температурные зависимости механических свойств показывают их аномалии (незакономерные изменения) при температурах деформационного старения 250–350 ОС (синеломкости) и эвтектоидного превращения.
Нагрев должен обеспечить равномерное распределение температуры по сечению и длине заготовки, минимальное обезуглероживание поверхностного слоя и минимальное образование окалины.
Температура окончания процесса горячей обработки давлением не должна быть слишком низкой, так как происходящий при этом процесс упрочнения и снижения пластичности может вызвать образование трещин. Эта температура не должна быть и чрезмерно высокой вследствие опасности получения крупнозернистой структуры.
Обычно температурные интервалы горячей деформации составляют:
-углеродистых сталей 1250–800 ОС;
-легированных 1150–900 ОС.
Режим нагрева крупных стальных слитков и заготовок обычно состоит из двух ступеней: первой – нагрев 700 – 800 ОС и второй – нагрев до температур горячей деформации.
Во избежание образования трещин, металл необходимо нагревать с определенной скоростью.
Скорость нагрева представляет собой величину повышения температуры металла за единицу времени. Скорость нагрева до заданной температуры зависит от теплопроводности и теплоемкости металла, размеров и формы заготовок, характера расположения заготовок в печи.
Теплопроводность стали зависит от температуры, химического состава и состояния. Легированные стали имеют меньшую теплопроводность, чем углеродистые. Поэтому легированные стали и стали в литом состоянии (слитки) нагревают обычно медленно.
В зависимости от сечения и химического состава заготовки ее охлаждение после горячей обработки давлением может производиться либо на воздухе, либо медленно в теплоизолирующих средах (песке, шлаке и др.) или в печи. Заготовки крупного сечения и заготовки из легированных сталей, предрасположенные к образованию макро- и микротрещин, охлаждают медленно.
|
Как правило, с повышением температуры деформации сопротивление деформации металла понижается, а пластичность повышается (рис. 21).
Рис. 21. Влияние температуры деформации
на механические свойства стали
Для сравнения температурных зависимостей деформационных характеристик различных сплавов используют гомологическую температуру θ:
где Т ДЕФ – температура деформации; Т ПЛ – температура плавления.
Влияние скорости деформации
на механические свойства сплавов
Скорость деформации - это отношение степени деформации ко времени, в течение которого происходит деформация. Например, при осадке скорость деформации будет равна:
(с-1); (3.2)
, (3.3)
где = Н О – Н = ΔН/Н О - относительная степень деформации;
Н O и Н – исходная и текущая высота образца соответственно;
t – время деформации (с);
V = ∆Н ∕ t – скорость деформирования или скорость перемещения инструмента (м/с).
Увеличение скорости деформации приводит к повышению прочности и уменьшению пластичности сплавов (рис. 22).
10-3 10-2 10-1 , с-1 10-3 10-2 10-1
,с-1
а б
Рис. 22. Влияние скорости деформациина сопротивление деформации
в полулогарифмических (а) и логарифмических (б) координатах
Скоростная зависимость истинного сопротивления деформации i удовлетворительно описывается уравнением (рис. 22, а):
i =
О
,
где О – const;
– скорость деформации; m – скоростной коэффициент.
Последнее выражение в логарифмических координатах представляет уравнение прямой (рис. 22, б):
lg i = lg
О + m lg
,
откуда
Скоростной коэффициент m представляет собой интенсивность изменения сопротивления деформации от скорости деформации
.
С повышением температуры деформации сопротивление деформации уменьшаются, а скоростной коэффициент m –увеличивается.
С увеличением скорости деформации уменьшается релаксация напряжений, что приводит к повышению сопротивления деформации. Однако с увеличением температуры деформации релаксация напряжений возрастает, что приводит к повышению деформируемости (пластичности) сплава и увеличению скоростного коэффициента m.
Таким образом, скоростной коэффициент m служит мерой пластичности сплавов. При m ≥ 0,3 сплав становится сверхпластичным.
При холодной деформации влияние скорости незначительно и скоростным коэффициентом в инженерных расчетах пренебрегают.
Увеличение скорости деформации также приводит к повышению температуры начала рекристаллизации.
|
Сверхпластичность
Сверхпластичность представляет собой высокую пластичность металла при растяжении на сотни и даже тысячи процентов.
Сверхпластичность подразделяется на:
а) структурную – у сплавов с ультрамелкой зернистой структурой, имеющей размер зерна 1 – 10 мкм;
б) фазовую – протекающую при температурах, близких к температурам фазовых превращений (например, в сталях при температурах ниже на 10–30 OС температуры А 1 эвтектоидного превращения аустенита в перлит – П®А).
Сверхпластичность проявляется в условиях:
а) низкой скорости деформации, порядка = 10-4 – 10-1 с-1;
б) высокой чувствительности сопротивления деформации к скорости деформации, когда скоростной коэффициент m ≥ 0,3. Величина m ≥ 0,3 наблюдается при температурах деформации Т ДЕФ ≥ 0,5 Т ПЛ;
в) когда зерна в структуре металла имеют равноосную форму. Если они имеют пластинчатую форму, то сверхпластичность не наблюдается.
Сверхпластичность происходит благодаря следующим механизмам деформации:
а) дислокационному скольжению или двойникованию;
б) диффузионному массопереносу;
в) зернограничному проскальзованию.
При сверхпластической деформации, несмотря на большие степени деформации, не происходит вытягивание зерен в направлении деформации и сохраняется их равноосная форма. При этом не повышается плотность дислокаций, не образуется их скоплений, в результате чего металл не упрочняется.
При растяжении сверхпластичность протекает методом бегущей шейки: сначала в какой-то момент появляется первое утонение – шейка, в котором металл упрочняется сильнее, чем в соседних областях, в результате рядом с этой шейкой появляются новые шейки и происходит деформация образца по методу бегущей шейки.
Сверхпластичность наиболее легко протекает в двухфазных сплавах, при условии, что зерна каждой фазы имеют равноосную форму и равномерно распределены по объему заготовки.
В настоящее время сверхпластичность получена у алюминиевых, титановых и др. сплавов, а также у углеродистых, конструкционных, инструментальных, быстрорежущих и легированных сталей.
Преимущества сверхпластической деформации
1. Большие степени деформации, достигаемые при сверхпластичности, позволяют получать заготовки методом пластического деформирования за одну операцию, вместо нескольких переходов при обычной ОМД.
2. Низкие усилия деформирования при сверхпластичности позволяют использовать маломощное оборудование при получении больших заготовок, в том числе методом вакуумной или пневматической формовки.
3. Сверхпластическая деформация улучшает механические свойства сплава, снижает их анизотропию, способствует повышению антикоррозионной стойкости металла.
Недостатки сверхпластичности:
1. Низкая производительность, обусловленная низкой скоростью деформирования;
2. Для достижения сверхпластичности необходима такая изотермическая деформация, при которой температура нагрева инструмента была бы близка к температуре деформации металла.
Тепловой эффект деформации
Энергия, затрачиваемая на деформирование тела, расходуется на упругую и пластическую деформацию и на преодоление дополнительных напряжений. Энергия, затраченная на упругую деформацию, освобождается при разгрузке тела; энергия, затраченная на преодоление дополнительных напряжений, остается в теле, а энергия, израсходованная на пластическую деформацию, превращается в теплоту.
Тепловой эффект тем больше, чем больше скорость деформации, так как при малой скорости большое количество теплоты успевает рассеиваться в окружающую среду. Например, при скоростном деформировании дуралюмина, титановых сплавов температура металла может повыситься на ~200°С.
Тепловой эффект обычно вызывает повышение пластичности и снижение сопротивления деформированию металла. Однако в тех случаях, когда в результате теплового эффекта сплав попадает в зону фазовых превращений или пережога, происходит охрупчивание сплава и повышение сопротивления деформированию.
Закон наименьшего сопротивления
Всякая точка деформированного тела в случае ее возможного перемещения в различных направлениях движется по направлению наименьшего сопротивления.
Направлением наименьшего сопротивления является направление кратчайшей нормали, которое перпендикулярно периметру поперечного сечения. При деформации поперечное сечение заготовки в условиях значительной величины коэффициента трения стремится принять конфигурацию с наименьшим периметром, т.е. стремится к кругу. Например, при осадке прямоугольного образца прямоугольное сечение сначала будет принимать форму эллипса, а при больших степенях деформации приблизится к форме круга (рис. 23).
Рис.23. Схема наименьшего сопротивления
течения металла при деформации
Если коэффициент трения очень низкий, то этот закон наименьшего сопротивления не выполняется и течение металла при деформации происходит по направлению радиусов. В этом случае форма поперечного сечения образца (например, прямоугольная) после деформации сохраняется.
Напряженное и деформированное состояния металлов
Пластичность металлов и сплавов в основном зависит от механической схемы деформации, которая состоит из схемы напряженного состояния и схемы деформированного состояния.
Напряженное состояние, возникающее в каждой точке металла при действии внешних сил, может быть выражено девятью компонентами напряжений: тремя нормальными и шестью касательными (рис. 24).
Рис. 24. Схема напряженного состояния
Координатные оси x, y, z можно выбрать таким образом, что в площадках элементарного объема будут действовать только нормальные напряжения, а касательные равны нулю. В этом случае напряженное состояние будет описываться тензером главных напряжений
,
где 1,
2,
3 – главные нормальные напряжения.
Если главные нормальные напряжения равны между собой, то получим шаровой тензор напряжений.
Составляющие напряжений шарового тензора в общем случае равны среднему напряжению:
и шаровой тензор напряжений будет иметь вид
Шаровой тензор характеризует только упругое изменение объема.
Если из общего тензора напряжений вычесть шаровой тензор, то получится новый тензор напряжений D σ, называемый девиатором напряжения:
D σ = Т σ - Т σо .
Девиатор напряжения D σ не вызывает изменение объема, а вызывает пластическое изменение формы заготовки, т.е. под его действием происходит пластическая деформация.
Таким образом, общий тензор напряжений равен сумме шарового тензора Т σо и девиатора D σ напряжений:
Т σ = Т σо + D σ.
Обобщенной характеристикой напряженного состояния служит интенсивность нормальных напряжений
а интенсивность касательных напряжений равна
Деформированное состояние металлов может быть описано, как и напряженное состояние, тензором главных деформаций:
,
где 1,
2,
3 – главные деформации по координатным осям.
Этот тензор, как и тензор главных напряжений, может быть разложен на шаровой тензор деформации и девиатор деформации D , которые равны:
а) шаровой тензор деформации
где СР, - средняя деформация, равная:
СР = (
1 +
2 +
3)/3.
Из закона о постоянстве объема следует то, что сумма главных истинных деформаций равна нулю:
1 +
2 +
3 = 0
Тогда
СР = 0
и шаровой тензор деформации
б) девиатор деформации
Так как
СР = 0,
то
,
т.е. общий тензор деформации Т равен девиатору деформации D
:
Т = D
.
Девиатор деформации характеризует изменение формы тела.
Обобщенной характеристикой деформированного состояния также служит эквивалентная деформация или интенсивность деформации ε i, которая соответствует степени изменения формы тела и определяется по формуле
а интенсивность сдвиговых деформаций равна
Схемы напряженного состояния
Возможны девять схем напряженного состояния, подразделяющиеся на линейные, плоские и объемные (рис. 25).
а – линейные
б – плоские
в – объемные
Рис. 25. Схемы напряженного состояния
Схемы линейного напряженного состояния наблюдаются при растяжении и сжатии при небольших степенях деформации. Плоская схема напряженного состояния наблюдается при двухосном растяжении тонкой пластины.
К объемным схемам напряженного состояния относится большинство процессов обработки металлов давлением (прокатка, ковка, волочение и др.).
Схемы деформированного состояния
Так как сумма главных истинных деформаций равна нулю, а одна из них равна сумме двух других, то возможны только три схемы деформаций (рис. 26).
а б в
Рис. 26. Схемы деформированного состояния:
а – при растяжении; б – сдвиге; в – сжатии
Механическая схема деформаций
Механическая схема деформаций представляет собой совокупность схем главных напряжений и главных деформаций. Всего возможны 23 схемы механических деформаций.
Механическая схема деформаций является основным фактором, обусловливающим деформируемость заготовки.
Примеры механической схемы деформаций приведены на рис. 27.
а - растяжение б - сжатие
в - прессование г - волочение
Рис. 27. Некоторые механические схемы деформаций
Наиболее благоприятной схемой напряженного состояния, обеспечивающая наиболее высокую пластичность, является схема всестороннего неравномерного сжатия (например, при прессовании), характеризующаяся наибольшей долей сдвигающих напряжений, вызывающих деформацию. Наименее благоприятная схема для деформируемости – схема всестороннего растяжения.
Таким образом, деформируемость образца и его пластичность в основном зависят не от схемы деформированного состояния, а от схемы напряженного состояния.
Интенсивности напряжений i и деформаций
i позволяют сложное напряженно-деформированное состояние привести к эквивалентному по своему результату линейному напряженно-деформированному состоянию.
Установлено, что зависимость между i и
i характерна для данного металла и на нее не оказывает влияние вид напряженно-деформированного состояния. В этой связи графические и аналитические зависимости между напряжением и деформацией (кривые упрочнения), полученные по результатам испытаний при линейном напряженном состоянии (растяжении, сжатии), можно рассматривать как зависимость между интенсивностью напряжений и деформаций при сложном напряженно-деформированном состоянии.
Показатель напряженного состояния
Показатель напряженного состояния является характеристикой схемы главных напряжений и в зависимости от вида нагружения определяется различными методами.
Наиболее широко применяется показатель напряженного состояния П в виде отношения
П = ( 1 +
2 +
3) /
i,
где 1,
2,
3 – главные нормальные напряжения;
i – интенсивность нормальных напряжений.
Показатель П равен: при растяжении П = 1; при сжатии П = –1; при кручении П = 0.
Кроме способов нагружения (растяжения, сжатия, кручения, изгиба), величину показателя напряженного состояния П можно варьировать радиусом выточки на образце для растяжения (рис. 28).
Рис. 28. Эскиз образца с выточкой
В этом случае показатель напряженного состояния определяется по формуле
Практические значения данного показателя Псоставляют:
а) в условиях объемного растяжения П = +1…+6;
б) в условиях объемного сжатия П = -1… -6.
Чем больше величина П, тем выше жесткость cхемы напряженного состояния (меньше составляющая напряжения сдвига), тем материал более склонен к хрупкому разрушению.
Варьируя значения показателя П, например, величиной R н можно определить чувствительность материала к наряженному состоянию по графику предельная деформация – показатель напряженного состояния ( Y – П):
n Y = d /dП= tgα,
где n Y – коэффициент чувствительности пластичности к напряженному состоянию.
Коэффициент n Y является структурной чувствительной характеристикой, то есть обусловливается структурным состоянием металла, которое формируется технологией выплавки, деформации, термообработки и т.п.
Исходные данные для построения диаграмм пластичности обычно получают из испытаний (например, цилиндрических образцов) на растяжение,
кручение и сжатие, проведение которых позволяет определить показатель напряженного состояния в интервале значений П≈ + 2,0 …- 1,0. При этом в рассматриваемых процессах величина показатель напряженного состояния равна:
-при линейном растяжении П = + 1;
-при кручении П = 0;
-при линейном сжатии П = – 1.
При растяжении гладких образцов в области равномерной деформации (до P max) по всему объему П = + 1,а в области сосредоточенной деформации на поверхности шейки П = + 1 и его величина возрастает по направлению к оси образца до П = + 2 и более. Для получения более жестких схем нагружения производят испытание надрезанных образцов с различными радиусами выточек (~ R H = 0,2–8,0 мм), при котором величина П может быть +6.
Значительный градиент напряжений и увеличение П по направлению к оси образца приводит к тому, что процесс разрушения, начиная с его ранних стадий, в центральной части опережает процесс разрушения в приповерхностных слоях. Поэтому разрушение (макротрещина или система макротрещин) может начаться в центральной части, и тогда деформирование без визуально заметного на поверхности разрушения продолжается некоторое время при наличии внутренней трещины.
Моделирование процессов ОМД
Моделированиепроводят с целью определения прочностных и пластических параметров технологического процесса обработки металлов давлением в лабораторных условиях на образцах (моделях) меньших размеров по сравнению с натурой. Для того чтобы экспериментальные данные, полученные в лаборатории, можно было распространить на производственные условия, необходимо соблюдать геометрическое и физическое подобие модели и натуры.
Геометрическое подобие – отношения сходственных линейных размеров (длины L, ширины B, высоты H) модели и натуры должны быть одинаковыми:
,
где L Н, B Н, H Н– длина, ширина, высота натуры;
L М, B М, H М – длина, ширина, высота модели;
n – коэффициент моделирования.
Для соблюдения геометрического подобия необходимо также, чтобы формы рабочей части инструментов для деформирования натуры и модели были геометрически подобными.
Степени деформации в рассматриваемый момент натуры и модели должны быть равны:
Н =
М.
Это условие предопределяет одинаковую степень упрочнения при деформации натуры и модели.
Скорости деформации натуры и модели должны быть равны:
Н=
М.
Это условие необходимо для обеспечения одинакового протекания процессов упрочнения и разупрочнения при деформации модели и натуры. При этом одним из условий является равенство скоростей деформирования
V М = V Н,
которые обусловливают скорость деформации:
= V / H.
В этом случае получаем, что
Откуда
V М = V Н /n.
Таким образом, для выполнения этого условия необходимо, чтобы скорость деформирования модели должна быть в n раз меньше скорости деформирования натуры, где n – коэффициент моделирования.
Коэффициенты трения должны быть одинаковы при деформации натуры и модели:
μ М = μ Н.
Это условие может быть выполнено только в случае равенства скоростей деформирования V Н и V М, но на основании предыдущего выражения V Н ≠ V М и, следовательно, условие равенства коэффициентов трения не выполнимо.
Физическое подобие заключается в том, чтобы у натуры и модели был одинаковый химический состав, структура, режимы обработки, величина коэффициентов теплопроводности и теплоотвода, энергии при пластической деформации.
Так как с увеличением размеров тела отношение его полной поверхности S П к объему W уменьшается, что видно на примере цилиндра:
то при горячей деформации теплоотвод у натуры будет меньше, чем у модели, что приведет к меньшему сопротивлению деформации:
Н <
М.
Таким образом, при моделировании не все условия подобия выполнимы, что вынуждает применять приближенные методы моделирования.
При холодной деформации влияние скорости деформации незначительно и здесь процессы моделирования более выполнимы.
При горячей деформации влияние скорости значительно и также играет большую роль сила трения. Для такой деформации вводят поправочные коэффициенты, например, масштабный фактор j =0,6–0,8, который учитывают при определении сопротивления деформации:
Н = φ
М.
Если геометрические и физические условия деформирования модели и натуры соблюдены, то удельные усилия их деформирования будут равны.
Обычно при моделировании используют такие материалы, как свинец, алюминий и др. Свинец часто применяется для моделирования процессов горячей деформации, так как деформация свинца при комнатной температуре соответствует горячей (θ ≥ 0,5) деформации:
ТЕХНОЛОГИЧЕСКИЕ ПРОЦЕССЫ ОМД
Прокатка
Прокатка – деформирование материала на прокатных станах между вращающимися валками.
Прокатка – основной вид ОМД, которому подвергают до 70% выплавляемого металла.
Прокатка подразделяется на:
а) продольную, поперечно - винтовую и др.;
б) объемную, листовую и др.;
в) горячую, теплую, холодную и др.
|
|
Общие условия выбора системы дренажа: Система дренажа выбирается в зависимости от характера защищаемого...
Автоматическое растормаживание колес: Тормозные устройства колес предназначены для уменьшения длины пробега и улучшения маневрирования ВС при...
Семя – орган полового размножения и расселения растений: наружи у семян имеется плотный покров – кожура...
Адаптации растений и животных к жизни в горах: Большое значение для жизни организмов в горах имеют степень расчленения, крутизна и экспозиционные различия склонов...
© cyberpedia.su 2017-2024 - Не является автором материалов. Исключительное право сохранено за автором текста.
Если вы не хотите, чтобы данный материал был у нас на сайте, перейдите по ссылке: Нарушение авторских прав. Мы поможем в написании вашей работы!