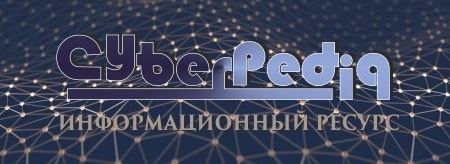
Адаптации растений и животных к жизни в горах: Большое значение для жизни организмов в горах имеют степень расчленения, крутизна и экспозиционные различия склонов...
Индивидуальные и групповые автопоилки: для животных. Схемы и конструкции...
Топ:
Установка замедленного коксования: Чем выше температура и ниже давление, тем место разрыва углеродной цепи всё больше смещается к её концу и значительно возрастает...
Оснащения врачебно-сестринской бригады.
Марксистская теория происхождения государства: По мнению Маркса и Энгельса, в основе развития общества, происходящих в нем изменений лежит...
Интересное:
Средства для ингаляционного наркоза: Наркоз наступает в результате вдыхания (ингаляции) средств, которое осуществляют или с помощью маски...
Аура как энергетическое поле: многослойную ауру человека можно представить себе подобным...
Финансовый рынок и его значение в управлении денежными потоками на современном этапе: любому предприятию для расширения производства и увеличения прибыли нужны...
Дисциплины:
![]() |
![]() |
5.00
из
|
Заказать работу |
|
|
Существенное ускорение процесса спекания может быть достигнуто, если одновременно с собственно спеканием будет происходить диффузионное легирование каждой из частиц прессовки. Процесс диффузионной гомогенизации сопровождается повышением концентрации вакансий, возникновением напряжений, которые обусловлены градиентом концентрации диффундирующего компонента.
Все эти процессы способствуют повышению «активности» частиц и, как следствие этого, ускорению процесса спекания.
Реально описанную возможность ускорения процесса усадки можно осуществить с помощью нескольких различных приемов, которые объединены общностью цели: создать на поверхности каждой из частиц слой вещества, диффундирующего в процессе спекания в тело частицы. Этот слой может быть
Рис. 7.2. Концентрационная зависимость усадки смесей Сu – Ni [1]:
1 – Экспериментальная кривая, Т = 1000 ºС, t = 15 мин;
2 – Зависимость D l / l0 = (1/ l0)[ L AA c* + L BB(1 – c *)];
3 – Зависимость D l / l0 = (1/ l0)×2 L0c* (1 – c*), полученная вычитанием прямой 2 из кривой 1
нанесен химически или же может образовываться в процессе спекания. В последнем случае вещество покрытия вводится в прессовку в форме малойпримеси весьма мелкодисперсных частиц, вещество которых либо, испаряясь, конденсируется на поверхности зерен основного компонента, либо покрывает эту поверхность вследствие поверхностной диффузии.
Необходимо подчеркнуть отличия процессов, протекающих в прессовках из порошков, легируемых в процессе спекания, от процессов, наблюдающихся в прессовках из смесей порошков. Одно из них заключается в том, что при наличии локальных градиентов концентрации компонентов контакты между разноименными порошинками отсутствуют и в этом смысле прессовка из легируемых порошков является «однородной». Второе состоит в том, что масса модифицирующей добавки значительно меньше массы частиц основы. В связи с этим принципиально не исключенное влияние эффекта Френкеля на усадку практически не имеет места и процесс диффузионной гомогенизации лишь способствует усадке.
|
В зависимости от диффузионных констант системы «основное вещество – вещество покрытия» и от линейных размеров частиц обсуждаемый механизм активирования может определить «активность» либо в объеме всей частицы, либо в ее приповерхностных слоях. Во втором случае активирование процесса спекания скажется на ускоренном росте контактных площадей между отдельными припекшимися частицами в большей степени, чем на убыстрении усадки, регистрируемой дилатометрически.
Выбор вещества – модификатора необходимо делать с учетом цели, которая при этом преследуется. Если активирование должно коснуться в основном лишь приповерхностных слоев, то коэффициент диффузии вещества покрытия в вещество основы должен быть большим, чем для потока в обратном направлении. Для «объемного» активирования соотношение между потоками должно быть обратным. Эффект модифицирования зависит от соотношения масс вещества покрытия и вещества порошинки. Для того чтобы активирование способствовало объемной усадке, линейный размер порошинки L, коэффициент взаимной диффузии вещества порошинки и покрытия D и время спекания t должны удовлетворять неравенству L <<(Dt)1/2.
Методы активирования спекания целесообразно подразделять на две основные группы:
физические, к которым могут быть отнесены циклические изменения температуры спекания, совмещение прессования со спеканием (горячее прессование), влияние магнитного поля, ультразвука, различных типов излучения и других воздействий, приводящих к созданию дефектов;
химические, основанные на использовании окислительно-восстановительных реакций, процессов диссоциации химических соединений, химического транспорта спекаемого вещества и др.
|
Избыток поверхностной энергии, т.е. высокая активность, является следствием подведения к системе извне избыточной энергии, в частности, в процессе синтеза (предыстория порошка), за счет пластической или хрупкой деформации при прессовании, образования напряженного состояния, метастабильных химических соединений в результате приложения давления. Избыточная энергия может возникать непосредственно в процессе обжига, например, за счет протекания окислительно-восстановительных процессов, действия полей различной природы и интенсивности. Таким образом, активность всегда связана с повышением неравновесности системы (и чем она выше, тем выше и активность), и может быть врожденной, связанной с химической предысторией системы; и приобретенной, привнесенной в систему на различных этапах технологического процесса.
Помимо этого, процесс уплотнения может интенсифицироваться не только рассмотренной выше структурной активностью, но и геометрической активностью, которая обусловлена тем, что геометрия межчастичных контактов определяет градиент химического потенциала, поскольку в точке контакта частиц система обладает наибольшей избыточной энергией.
Рассмотрим некоторые физические аспекты активирования процесса спекания.
Усадка и относительная плотность при спекании в ультразвуковом поле увеличивается вследствие влияния ультразвука на кинетику молекулярных процессов как в жидких, так и в твердых телах. Ультразвук значительно изменяет ход кристаллизации из жидкой фазы, давая возможность повысить дисперсность кристаллов. Под действием ультразвука может изменяться кинетика рекристаллизации и скорость пластической деформации.
Выяснению влияния ультразвука на активирование переноса массы посвящены исследования Пинеса и сотрудниками. По данным этих работ, ускоренный массоперенос в процессе спекания может быть следствием структурных изменений, вызванных ультразвуком. Показано, что линии на рентгенограммах образцов, подвергавшихся действию ультразвука, значительно шире; можно полагать, что в этом случае при высоких температурах возникает тонкоблочная структура.
Исследования воздействия ультразвука на карбид титана показали, что при температурах выше 1400 °С происходит ускорение спекания за счет ударной нагрузки ультразвуковых колебаний из-за активирования взаимного проскальзывания частиц. Диффузионные процессы ускоряются в результате облучения материала потоками частиц высоких энергий.
|
Химические методы активирования спекания могут быть классифицированы следующим образом:
по поведению активаторов: спекание, при котором активаторы спекания остаются в спекшихся изделиях (спекание с одновременным образованием химических соединений, с участием жидкой фазы); спекание, при котором активаторы не остаются в составе спекшихся изделий (галогены и др.);
по источникам активирования: из газовой фазы, из засыпки, из примесей в спекаемых брикетах;
по этапу действия активаторов или активации: до спекания, в процессе спекания;
по составу активаторов.
Одной из наиболее широко изученной разновидностью активирования спекания с помощью активаторов, остающихся в составе спекшегося изделия, является т.н. реакционное спекание. В данном случае твердая фаза, взаимодействующая с соответствующей газовой или жидкой, поступающей преимущественно извне заготовки, с положительным объемным эффектом, и является таким активатором. К этому же типу относятся случаи, когда добавка образует с основной фазой либо твердые растворы, либо одновременно твердые растворы и химические соединения.
Следует отметить, что спекание оксидов и других тугоплавких соединений с добавками, образующими жидкую фазу, как показано выше (см. раздел 2.4), протекает тем интенсивнее, чем меньше краевой угол смачивания твердой фазы жидкой и выше поверхностное натяжение последней. При этом процесс может осуществляться с участием жидкой фазы, как исчезающей в процессе спекания, так и остающейся до конца спекания.
Таким образом, снижение температуры спекания может быть достигнуто в результате увеличения дисперсности порошка исходного материала, повышения дефектности его кристаллической решетки и за счет введения добавок. Температура спекания также зависит от наличия примесей, газовой среды обжига и др.
|
Дисперсность тугоплавкой фазы оказывает решающее влияние на активность к спеканию. С повышением дисперсности увеличиваются суммарная поверхностная энергия и контактная площадь соприкосновения частиц, возрастает дефектность строения, что создает более благоприятные условия для уплотнения. Например, считается, что максимальный размер зерен оксида алюминия, способных к активному твердофазовому спеканию, не превышает 2–5 мкм.
Значительного прогресса с точки зрения снижения температуры спекания можно достичь за счет применения новых методов подготовки высокодисперсных порошков, активных к спеканию. Эти методы основаны на способности наследования последующей фазой структуры предыдущей фазы. При этом наследуется не только форма, размер частиц и агрегатов порошка, но и элементы строения кристаллической решетки, особенно в тех случаях, когда фазы совпадают по типу сингонии (см. раздел 5.2).
Степень агрегации и свойства агрегатов порошков промежуточных соединений, строение которых наследуется оксидами, зависят от метода получения. Прочные агрегаты спекаются в первую очередь, образуя крупные кристаллы с внутренними порами. Поэтому, современные методы подготовки порошков должны обеспечить как можно меньший размер агрегатов, чтобы получить равноплотную беспористую структуру. С другой стороны, чтобы предотвратить агрегацию и неравноплотность при спекании, порошок не должен состоять из крайне высокодисперсных частиц. Оптимальный размер высокодисперсных порошков лежит в пределах 0,2 – 0,4 мкм.
Установлено, что не содержащие модифицирующих добавок оксидные керамические материалы характеризуются невысоким уровнем свойств, трудно регулируемой микроструктурой, низкой плотностью.
Исследования по влиянию добавок на спекание керамики на основе чистых оксидов проведены Н.М. Павлушкиным, а впоследствии интенсивно продолжались Д.Н. Полубояриновым, В.Л. Балкевичем, И.С. Кайнарским, Г.В. Куколевым,
Н.Н. Силиной, В.Н. Батыгиным, E.C. Лукиным, В.И. Верещагиным, Г.А. Выдриком, Э.В. Дегтяревой, Г.П. Каллигой, А.М. Черепановым, Д.С. Рутманом, Р. Гарви, У.Д. Кингери, Р.Л. Коблом, В.К. Сингом и др.
Обобщение работ по спеканию керамики на основе чистых оксидов с добавками показывает, что, согласно Е.С. Лукину, по характеру взаимодействия с оксидами их можно классифицировать на 4 группы:
· Полностью растворимые в кристаллической решетке основного оксида (Li2O в MgO; HfO2 в Y2O3, Y2O3 в ZrO2 и др.);
· Добавки, нерастворимые в кристаллической решетке основного оксида, а образующие жидкую фазу за счет плавления или взаимодействия с основным оксидом с образованием эвтектического расплава (CaO – Al2O3 – SiO2,
Y2O3 – SiO2, MnO – Cr2O3 – SiO2 и др.);
|
· Нерастворимые в кристаллической решетке основного оксида и не взаимодействующие с ним (эвтектические составы в системах Al2O3 – ZrO2, BeO – ZrO2 и др.);
· Вступающие в химическое взаимодействие с основным оксидом с образованием химического соединения (Al2O3 в Y2O3, Ga2O3 в MgO и др.).
Наиболее широко применяются в технологии современной керамики добавки первой и второй групп. Действие добавок первой группы сводится к изменению концентрации вакансий в катионной и/или анионной подрешетке материала. При этом добавка должна повышать концентрацию тех дефектов, которые лимитируют скорость спекания.
При введении растворимых добавок возможно образование твердых растворов внедрения или замещения с основным оксидом. Установлено, что для образования непрерывного ряда твердых растворов замещения должны выполняться следующие условия: близость параметров решеток основного оксида и добавки, различие ионных радиусов катионов не более 15 %, совпадение зарядов катионов оксидов в твердом растворе. Образование растворов внедрения возможно при различном размере катиона добавки и основного оксида, причем размер катиона добавки должен быть существенно меньшим. Возможен и третий случай, когда заряд катиона добавки отличается от заряда основного оксида, а их радиусы практически равны (отличие < 15 %).
Влияние добавок на спекание Al2O3, рассмотренное Н.М. Павлушкиным, позволило разделить изученные соединения на 3 подгруппы, по-разному влияющие на спекание и размер кристаллов:
· Облегчающие спекание и ускоряющие рост кристаллов (Ti4+, Ti2+, Mn2+, Ca2+, Sr2+, Ni2+);
· Замедляющие спекание и рост кристаллов (К+, Rb+, Sn2+, Pb2+);
· Добавки промежуточного типа (В3+, Ba2+, Cd2+, Au+).
W. Smothers и H. Reynolds отнесли:
к первой подгруппе – Ti2+, Ti4+, Nb5+, Mn2+, Cu+, Cu2+, Ge4+;
ко второй подгруппе – Ga3+, Y3+, P5+, Fe3+, Th4+, Ce4+, Zr4+, Co3+;
к третьей подгруппе – Na+, Sb3+, Ca2+, K+, Ba2+, Sr2+, Sn2+, Cr3+, La3+, V5+, Si4+.
С.Г. Тресвятский при рассмотрении добавок, не образующих жидкую фазу в процессе обжига, дает следующую классификацию:
· Ускоряющие процесс спекания с одновременным ускорением процесса вторичной рекристаллизации (TiO2 в Al2O3, Li2O в MgO, CaO в ThO2,
GeO2 в MgO);
· Активирующие спекание и одновременно замедляющие процесс вторичной рекристаллизации (MgO или BeO в Al2O3);
· Добавки, замедляющие как процесс спекания, так и процесс роста кристаллов.
Содержание активаторов, образующих растворы внедрения, обычно составляет менее 5 мол. %, в то время как добавок, формирующих изовалентный твердый раствор – 15–30 мас. %. Последнее обусловлено тем, что количество такой добавки должно оказаться достаточным для искажения решетки и увеличения подвижности ионов. Эффект влияния активаторов значительно усиливается при введении в матрицу соединений, образующих твердые растворы изовалентного и иновалентного замещения. Единственным ограничением в данном случае является то, что добавки не должны реагировать друг с другом с образованием соединения.
В ряде случаев с целью активирования спекания могут использоваться добавки, не остающиеся в составе спекшегося материала. К такому типу активаторов могут быть отнесены галогены и галогениды, доставляющиеся к обжигаемому материалу из газовой фазы либо входящие в состав спекаемого ансамбля частиц. Аналогичными активаторами спекания являются водород и другие газы, участвующие в процессах окисления – восстановления.
Процесс активирования в этих случаях сводится к своеобразному травлению поверхности обжигаемого материала и, соответственно, повышению его химического потенциала. Значительное влияние в этом случае может оказывать перенос через газовую фазу, что особенно интенсифицирует процесс спекания.
Особый вид дефектных структур представляют собой нестехиометрические соединения. Активность в этом случае проявляется как результат стремления к восстановлению стехиометричности либо вследствие высокой диффузионной подвижности компонентов. Спекание фаз внедрения также интенсифицируется с ростом дефектности решетки по неметаллу (углероду, азоту и др.).
Для сравнительной оценки влияния добавок, принадлежащих к одной группе системы Д.И. Менделеева, В.И. Верещагиным предложен структурно-энергетический коэффициент эффективности:
, (7.17)
где D Fd’ и DF0’ – приведенные свободные энергии образования оксида добавки и основного оксида;
D r/r0 – относительная разность радиусов катиона добавки и основного оксида.
При этом:
, (7.18)
где D F – свободная энергия образования оксида;
m – число атомов металла в формуле оксида;
Z – заряд катиона.
На реальных металлических порошковых прессовках активирование легированием изучено в значительном количестве работ. Исследовано влияние малых добавок Ni и Со на кинетику спекания прессовок из порошков железа (рис. 7.3). Добавки никеля и кобальта вводили путем смешивания порошка железа с растворами нитратов никеля и кобальта при непрерывном выпаривании влаги. В этих условиях на поверхности железных частиц осаждались слои нитратов, из которых при высокотемпературном разложении образовывались слои металлов. Слои Ni и Со способствуют ускорению усадки, т.е. активируют спекание. Введение малых добавок Ni в прессовку из железного порошка путем механического перемешивания способствует увеличению усадки в значительно меньшей степени, чем в случае химического смешивания, при котором обеспечивается равномерное распределение активирующей добавки на всей поверхности частиц.
Изучено спекание прессовок из порошков вольфрама, активированных малыми добавками никеля. Показано, что модифицирование вольфрама никелем приводит к
Рис. 7.3. Объемная усадка порошковых прессовок: а – вихревое железо с добавками Ni (1) и Co (2), Т = 1200 ºС, t = 1 ч; б – железо (3), железо с добавкой 1,8 % Co (4) и 1,9 % Ni (5) при различных температурах, t = 1 ч; в – железо (6), железо с добавкой 5,2 % Co (7) и 5,5 % Ni (8) при Т = 1200 ºС
существенному снижению температуры, при которой наблюдается заметная усадка.
Производственная практика свидетельствует о том, что существенное активирование спекания может быть достигнуто при окислении и последующем восстановлении оксидов на поверхности порошков, при обжиге в агрессивных газовых средах и др.
На первый взгляд описанные факты противоречат тому, что процессы, происходящие на поверхности, не могут определить кинетику объемной усадки и способны лишь повлиять на сфероидизацию пор, скорость роста контакта между частицами, т.е. процессы, которые не приводят к объемной усадке, но способны изменить механические и электрические свойства прессовок. Это противоречие является, однако, кажущимся.
Перечисленные выше процессы активирования поверхности, как правило, сопровождаются возникновением в приповерхностном слое большого количества дефектов: вакансий, дислокации и др. Перемещаясь из этого слоя вглубь прессовки и, в частности, в приконтактную область, они способствуют увеличению «активности» объема прессовки.
Возникновение избыточных вакансии в приповерхностном слое приводит к направленному самодиффузионному потоку вакансий вглубь частицы. Этот процесс сопровождается «активированием» структуры, т. е. ее разрыхлением вследствие образования пористости, дислокационных петель и др. Подобное отчетливо наблюдали в опытах, в которых сравнивались структуры медных проволок (диаметр 10-4 м),отжигавшихся в вакууме и в условиях периодического чередования процессов окисления и восстановления поверхности. Вo втором случае после 10 циклов окисления – восстановления наблюдалось значительное разрыхление структуры проволоки вдали от поверхности.
Явление ухода дислокаций из приповерхностного слоя вглубь кристалла наблюдали в экспериментах с ионными монокристаллами (NaCI, LiF), поверхность которых деформировали шлифованием. После кратковременного низкотемпературного отжига наблюдали резкое понижение плотности дислокаций в приповерхностном слое и увеличение таковой в глубинных слоях – 100 – 150 мкм от поверхности. Такое расширение дислокационной приповерхностной зоны является естественным следствием стремления к понижению упругой энергии, наличие которой обусловлено скоплением дислокации в приповерхностном слое.
|
|
Кормораздатчик мобильный электрифицированный: схема и процесс работы устройства...
Состав сооружений: решетки и песколовки: Решетки – это первое устройство в схеме очистных сооружений. Они представляют...
Поперечные профили набережных и береговой полосы: На городских территориях берегоукрепление проектируют с учетом технических и экономических требований, но особое значение придают эстетическим...
История развития пистолетов-пулеметов: Предпосылкой для возникновения пистолетов-пулеметов послужила давняя тенденция тяготения винтовок...
© cyberpedia.su 2017-2024 - Не является автором материалов. Исключительное право сохранено за автором текста.
Если вы не хотите, чтобы данный материал был у нас на сайте, перейдите по ссылке: Нарушение авторских прав. Мы поможем в написании вашей работы!