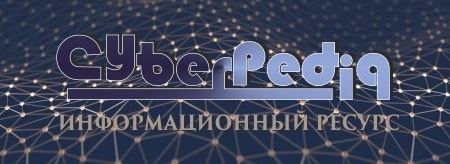
Двойное оплодотворение у цветковых растений: Оплодотворение - это процесс слияния мужской и женской половых клеток с образованием зиготы...
Поперечные профили набережных и береговой полосы: На городских территориях берегоукрепление проектируют с учетом технических и экономических требований, но особое значение придают эстетическим...
Топ:
Теоретическая значимость работы: Описание теоретической значимости (ценности) результатов исследования должно присутствовать во введении...
Марксистская теория происхождения государства: По мнению Маркса и Энгельса, в основе развития общества, происходящих в нем изменений лежит...
Интересное:
Распространение рака на другие отдаленные от желудка органы: Характерных симптомов рака желудка не существует. Выраженные симптомы появляются, когда опухоль...
Уполаживание и террасирование склонов: Если глубина оврага более 5 м необходимо устройство берм. Варианты использования оврагов для градостроительных целей...
Финансовый рынок и его значение в управлении денежными потоками на современном этапе: любому предприятию для расширения производства и увеличения прибыли нужны...
Дисциплины:
![]() |
![]() |
5.00
из
|
Заказать работу |
|
|
Скорость процесса уплотнения порошковых прессовок зависит от структурного состояния порошков, от степени их т.н. «активности». Понятие «активность» с точки зрения физики процесса спекания формально не определено; более активным считается порошок, прессовка из которого при прочих равных условиях уплотняется с большей скоростью.
Степень активности порошка может быть значительно изменена путем изменения условий его получения. Методы синтеза исходных порошков оксидов весьма разнообразны. Они могут быть получен по золь-гель технологии, термическим разложением солей, лазерным испарением, распылительным термолизом, осаждением, криохимическим методом, окислением и др.
В золь-гель методе сначала получают золь, затем гель. Гель можно использовать непосредственно для синтеза пленок или монолитных изделий. Проблемой является изготовление заготовок больших размеров, поскольку при их сушке и обжиге усадка достигает 70 %, что приводит к возникновению механических напряжений вплоть до образования трещин. Для получения золя проводят гидролиз солей слабых оснований или алкоголятов. Для перевода золя в гель из него удаляют часть воды нагреванием, экстракцией соответствующим растворителем. К основным достоинствам золь-гель метода можно отнести лучшие гомогенность композиций (на молекулярном уровне), распределение добавок, контроль стехиометрии; меньшее загрязнение, более высокую дисперсность и реакционную способность порошков, что позволяет снизить температуры процессов термообработки и даже синтезировать неравновесные фазы. Материалы и изделия, полученные с использованием золь-гель технологии, как правило, обладают более высоким качеством. С технологической точки зрения преимуществами золь-гель метода являются возможность повторного использования материалов геля, отсутствие пыления. В качестве недостатков можно назвать достаточно высокую стоимость сырьевых материалов, большие усадки монолитов, более высокую остаточную пористость, содержание остаточного углерода (в случае использования органических реагентов) и др.
|
Вариантом золь-гель метода считают распределение водорастворимых солей в матрице из геля поливинилового спирта (ПВС). Гель получают при смешивании и нагревании водных растворов ПВС и соответствующих солей. Последующее прокаливание приводит к их разложению и образованию ксерогелей оксидов. Реализуется процесс образования защитного слоя вокруг наночастицы, что способствует сохранению ее размеров и свойств. В то же время защитный слой может препятствовать взаимодействию наночастиц, когда задачей является синтез химического соединения, например, сложного оксида. Получение сложного оксида затрудняется тем, что температуры разложения солей при их переводе в оксиды могут значительно различаться. Появляющийся первым оксид может образовывать крупные частицы до начала взаимодействия с другими оксидами, входящими в сложный оксид. Более перспективно использование в качестве прекурсоров двойных солей или комплексных соединений, в которых входящие в сложный оксид катионы находятся в таком же соотношении, как в синтезируемом сложном оксиде.
Довольно широкое распространение в золь-гель методе приобрело использование гидролиза алкоксидов металлов. В некоторых случаях можно применять не очень чистые и поэтому недорогие металлы и в дальнейшем очистить алкоксиды дистилляцией. При гидролизе спирт препятствует агрегации и экстрагирует воду, обеспечивая переход золя в гель. Гидролизуя смесь алкоксидов, возможно синтезировать сложные соединения. Примеси органических веществ удаляются во время термообработки порошков в процессе перевода гидроксидов в оксиды. При синтезе сложных оксидов значительную часть компонентов можно вводить вместе с водой, используемой для гидролиза алкоксида. Высокая неравновесность процесса требует применения специальных мер для предупреждения старения частиц порошка. Брак при сушке заготовок, изготовленных непосредственно из геля, удается снизить при использовании специальных ПАВ, называемых химическими агентами, контролирующими сушку: глицерин, формамид и т.д.
|
После термической обработки ксерогеля размер частиц порошка составляет 0,5 – 5,0 мкм.
Один из традиционных способов подготовки шихты для оксидных материалов – одновременное смешение и помол оксидов исходных компонентов с их последующим прокаливанием для синтеза твердых растворов. Эти стадии часто не могут обеспечить высокую однородность и приводят к загрязнению шихты материалом мельницы и мелющих тел, которые трудно оценить количественно.
Порошки оксидов как в промышленности, так и лабораторной практике получают путем термического разложения малорастворимых соединений, например оксалатов, гидроксидов, карбонатов, которые переходят в оксиды при сравнительно низких температурах; разложение происходит примерно в интервале 200 – 600 °С . Из-за масштабности производств, по сравнению с получением в лаборатории, могут наблюдаться некоторые недостатки порошков, например недостаточная однородность распределения компонентов.
Такая же закономерность наблюдается в отношении не только оксидов, но и любых порошков, применимых к получению прозрачной керамики. Так, например, керамика на основе промышленного карбоната иттрия обладает худшими свойствами по сравнению с материалом, изготовленным на основе карбоната иттрия, синтезированного в лабораторных условиях. Порошки, полученные путем гидролиза изопропилата иттрия, характеризуются меньшим размером частиц. На их основе изготовлены керамические материалы со светопропусканием 64 % в видимой области спектра. Образцы, синтезированные из промышленного карбоната иттрия непрозрачны; с видимыми неоднородностями.
При исследовании свойств промышленных порошков оксидов из разных партий установлено существенное различие в их дисперсности и строении. Так, по удельной поверхности они могут отличаться более чем в 5 – 10 раз, состоять из агрегатов разного размера. Как правило, промышленные порошки состоят из пористых достаточно крупных агрегатов.
|
Одним из способов повышения «активности» порошков к спеканию является увеличение дисперсности. Он широко применяется на практике в технологии оксидной керамики, при этом дисперсность увеличивают путем длительного мокрого измельчения, часто в течение десятков часов, получая порошки с размером частиц 1 – 3 мкм. Следует отметить, что в отличие от порошков, полученных химическими методами, промышленные оксиды обладают меньшей активностью.
Например, наиболее простой и широко применяемый в технологии прозрачной керамики из промышленного оксида иттрия метод получения многокомпонентных по составу изделий основан на смешении и одновременном измельчении порошков оксида иттрия совместно с оксидом добавки, синтезе в твердой фазе и обжиге. Однако при использовании оксидного метода достичь однородности распределения небольших количеств добавки очень трудно даже при длительном совместном измельчении, так как ее частицы намного меньше частиц основного оксида. Использование соизмеримых по размеру зерен вызывает локальные неоднородности состава, приводящие к неравномерности микроструктуры и значительному разбросу свойств изделий. Несмотря на это, в ряде случаев он дает достаточно стабильные результаты, в частности, примером может служить создание прозрачной керамики на основе Y2O3 с добавкой ZrO2.
Таким образом, в массовом производстве уместен синтез прозрачной керамики на основе оксида иттрия из промышленных оксидов, так как химическое получение сырья сложно и дорого. Изготовление прозрачной керамики из промышленных порошков возможно при условии повышения его активности к спеканию путем длительного мокрого измельчения и введения модифицирующих добавок.
Метод лазерного испарения позволяет получить тонкодисперсные порошки оксидов. Его сущность заключается в испарении оксида металла импульсным СО2-лазером и последующей конденсацией оксида на платиновой пластинке. В результате лазерного испарения, по данным микроскопического анализа, синтезированы порошки оксидов с размерами сферических частиц в диапазоне 2 – 28 нм. Ограниченность применения данного метода обусловлена высокими капитальными затратами, большой энергоемкостью процесса, а также низкой производительностью.
|
Метод распылительного термолиза органических или водноорганических растворов элементосодержащих соединений способствует синтезу тонкодисперсных порошков с размером частиц до 0,1 мкм. Растворы солей, как правило нитратов или сульфатов, подаются в реактор под углом 30 – 60° вместе с потоком молекулярного кислорода в вертикальный поток кислородной плазмы при температуре плазменной струи 2700 – 3800 ºС. Способ обладает высокой производительностью, но очень большой энергоемкостью, что существенно ограничивает его применение. Размер частиц синтезированного порошка 0,1 – 1,0 мкм.
Широкое распространение получил метод сжигания смеси солей с органическими восстановителями – мочевиной, лимонной кислотой, глицерином и др. Он позволяет получать индивидуальный оксиды, однородные смеси двух и более оксидов, твердые растворы оксидов, соли, а также композиты типа металл-оксид. При этом размер частиц составляет 50 – 65 нм.
Метод осаждения позволяет синтезировать однородные порошки с распределением частиц по размерам, близким к монофракционному. Последнее возможно за счет высокой степени неравновесности процесса зародышеобразования, что реализуется при введении малого количества осаждаемого вещества в избыток осадителя. Перспективно использование вязких жидкостей, в которых замедляются скорость диффузионного массопереноса и рост частиц, а также уменьшается вероятность образования прочных агрегатов.
В криохимическом методе водный раствор солей, золь или суспензию замораживают настолько быстро, чтобы в максимальной степени сохранить взаимное распределение компонентов, соответствующее раствору или суспензии. Для ускорения замораживания распыление проводят в криоагент, например, в жидкий азот, который особенно удобен в связи с его невысокой стоимостью и инертностью по отношению ко многим веществам. Лед из гранул удаляют сублимацией, не допуская образования жидкой фазы. Низкое поверхностное натяжение на границе лед-воздух резко замедляет агрегацию по сравнению с водой. Размер частиц синтезируемого порошка 0,2 – 2,0 мкм. Однако многостадийность процесса повышает его стоимость, а неравновесность затрудняет воспроизводимость результатов.
Существует возможность получения оксидов непосредственным окислением тонкодисперсного порошка металлов в потоке кислорода. Размер частиц получаемого порошка может составлять 10 – 400 мкм. Метод обладает рядом недостатков: малая производительность, невозможность контроля протекания реакции, повышенные требования по охране труда.
|
Электрохимический метод способствует осуществлению процессов, которые в обычных условиях не происходят или протекают очень медленно. Изменяя электрические параметры, влияют на размеры получаемых частиц.
В газовой фазе проводят процессы испарения-поликонденсации, осаждения, в том числе на твердую фазу, топохимические реакции (восстановления, окисления, разложения частиц твердой фазы).
Для синтеза порошков используют также процессы, в которых энергия передается исходным веществам через плазму или лазерный луч (плазмохимический, электроэрозионный, ударно-волновой). Недостатками последних являются их дороговизна, широкое распределение частиц по размерам, проблемой – отделение частиц от газовой фазы.
Механохимический синтез основан на возможности образования новых химических связей при разрыве предыдущих, происходящем при измельчении материалов. В условиях такого воздействия можно осуществлять полиморфные превращения; реакции разложения или синтеза. Синтез прост, но энергоемок и длителен. Недостатком является то, что в процессе помола в измельчаемый порошок попадает материал мелющих тел и футеровки мельницы.
Рассмотрим идеализированную модель «активного» материала, в которой зерно представлено совокупностью чередующихся слоев неискаженной решетки (коэффициент диффузии D0)и тонких прослоек с повышенной диффузионной проницаемостью (коэффициент диффузии Ds). В этой модели, являющейся подобием «слоеного пирога», λ0 — ширина «равновесного» слоя, λs — ширина слоя, в котором диффузия осуществляется в меру коэффициента Ds. Приближенно эффективный коэффициент диффузии D* в направлении, совпадающем с направлением прослоек, с величинами D0 и Ds связан соотношением*)
, (5.1)
Или, так как ,
. (5.2)
Таким образом, повышенная активность порошка по сравнению с «инертным» материалом может быть определена следующим критерием, называемым
c - фактором:
. (5.3)
При разумных значениях констант (Ds/D0 – 104 – 105, λ0 ≈ 10-5 м,
λs = 10-8 м)оказывается χ = 10 – 102.
Влияние макроскопических дефектов на степень диффузионной «активности» может быть определяющим на далекой стадии процесса спекания, когда дислокационная «активность» существенно ослаблена.
Экспериментально роль развитой сетки границ в увеличении диффузионной «активности» была отчетливо показана в опытах, в которых изучали диффузию серы S36 в медь гальванического происхождения. Роль развития субструктуры материала с увеличением его диффузионной «активности» исследована как применительно к фазовым переходам, так и применительно к пластической деформации.
|
|
История создания датчика движения: Первый прибор для обнаружения движения был изобретен немецким физиком Генрихом Герцем...
Таксономические единицы (категории) растений: Каждая система классификации состоит из определённых соподчиненных друг другу...
Наброски и зарисовки растений, плодов, цветов: Освоить конструктивное построение структуры дерева через зарисовки отдельных деревьев, группы деревьев...
Своеобразие русской архитектуры: Основной материал – дерево – быстрота постройки, но недолговечность и необходимость деления...
© cyberpedia.su 2017-2024 - Не является автором материалов. Исключительное право сохранено за автором текста.
Если вы не хотите, чтобы данный материал был у нас на сайте, перейдите по ссылке: Нарушение авторских прав. Мы поможем в написании вашей работы!