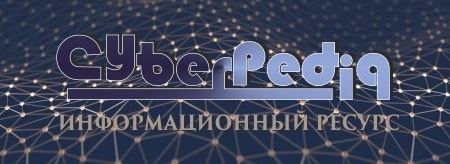
История развития хранилищ для нефти: Первые склады нефти появились в XVII веке. Они представляли собой землянные ямы-амбара глубиной 4…5 м...
Поперечные профили набережных и береговой полосы: На городских территориях берегоукрепление проектируют с учетом технических и экономических требований, но особое значение придают эстетическим...
Топ:
Основы обеспечения единства измерений: Обеспечение единства измерений - деятельность метрологических служб, направленная на достижение...
Характеристика АТП и сварочно-жестяницкого участка: Транспорт в настоящее время является одной из важнейших отраслей народного...
Проблема типологии научных революций: Глобальные научные революции и типы научной рациональности...
Интересное:
Уполаживание и террасирование склонов: Если глубина оврага более 5 м необходимо устройство берм. Варианты использования оврагов для градостроительных целей...
Подходы к решению темы фильма: Существует три основных типа исторического фильма, имеющих между собой много общего...
Что нужно делать при лейкемии: Прежде всего, необходимо выяснить, не страдаете ли вы каким-либо душевным недугом...
Дисциплины:
![]() |
![]() |
5.00
из
|
Заказать работу |
|
|
После разборки, мойки и очистки остовов производят их дефектировку, включающую в себя замеры базовых и сопрягаемых размеров, а также проверку неразрушающими средствами контроля
Замеры включают в себя следующие параметры:
- диаметры якорных горловин;
- диаметры моторно-осевых горловин;
- диаметры посадочные поверхности щитов;
- диаметры под установку обойм подшипников;
- высоту опорных поверхностей полюсов;
- базовые расстояния между противоположными опорными поверхностями полюсов;
- межосевое расстояние между якорной и моторно-осевой горловиной (централь);
- расстояния между посадочными поверхностями шапки моторно-осевых подшипников;
- расстояние между опорными поверхностями носиков трамвайной подвески,
а также ряд других замеров в соответствии с требованиями нормативно-технической документации и конструктивных особенностей электрических машин.
Замеры осуществляются стандартными и специальными измерительными инструментами. Некоторые измерения возможны либо с применением специальных измерительных систем, либо с использованием технологических возможностей горизонтально-расточных станков (соосность горловин, межосевые расстояние горловин, нахождение осей в одной плоскости и их параллельность, а также другие параметры.)
Калибрами проверяется износ резьбовых отверстий, визуально осматриваются состояние резьбовых поверхностей.
Замеры позволяют определить дефекты и отклонения от требований ремонтной документации вызванные износами, деформациями и аварийными повреждениями.
Результаты замеров и дефектировки отражаются в ремонтном листе остова и в карте замеров. При этом указываются способы восстановления (наплавить, расточить и т.д.).
|
Моторно-осевые горловины
При ослаблении натяга по замковым плоскостям шапок в остов. Производится наплавка поверхностей порошковой проволокой. Наплавка осуществляется специальным сварочным автоматом.
Если износ, выраженный отклонением цилиндрических поверхностей горловин от допусков, составляет небольшую величину, то дефекты устраняются одновременно расточкой горловин обеих шапок на горизонтально-расточном станке в пределах ремонтных допусков.
При более значительной величине отклонений, производится наплавка цилиндрических поверхностей на автоматической наплавочной установке. Автоматика установки осуществляет заданную скорость основного движения рабочего органа, заданную величину подачи. При этом при прохождении стыков соединения шапки и остова сварочная дуга отключается. После осуществления наплавки производится механическая обработка до чертежных размеров.
На торцевых поверхностях горловин на остове и шапке наносятся клейма с указанием номера остова и расположения шапки (левая или правая).
Рис.5.Автомат для наплавки цилиндрических поверхностей остовов
1. Колона. 2. Пульт управления. 3. Управление подачей проволоки. 4. Механизм подачи сварочной проволоки. 5.Рабочий орган (мундштук). 6 Источник сварочного тока.
После наплавки производится механическая обработка фрезерованием до чертежных размеров.
Горловина установки подшипниковых щитов (якорная горловина).
Замеры производятся одновременно с проверкой резьбовых отверстий крепления подшипникового щита. Проверяется, как состояние резьбы (износ, повреждения ниток) так и соосность окружности, которая проходит через оси отверстий с посадочной поверхностью установки щита.
В случае отклонений превышающих ремонтные допуски, одновременно производится наплавка посадочной поверхности горловины и полная заварка резьбовых отверстий с полным заполнением металла на всю глубину.
|
Остов устанавливается на стол горизонтально-расточного станка. Базирование осуществляется по оси моторно-осевой горловины и линии соединяющей оси моторно-осевой и якорной горловины, так называемая централь. При этом централь должна быть параллельной поверхности стола станка, то есть размещаться строго горизонтально.
Перемещением стола или передней бабки станка от оси моторно-осевой горловины на расстояние равное чертежному размеру централи. Например, для большинства тепловозных ТЭД централь равна – 468,8 мм. Расточка осуществляется с помощью борштанги установленной в люнетах, или суппорта планшайбы передней бабки, сосной шпинделю.
Такая схема базирования гарантирует, что оси якорной и моторно-осевой горловин сосны и находятся в одной плоскости, а расстояние между осями соответствует чертежному размеру централи. Соответственно будет обеспечено отсутствие перекоса в тяговой зубчатой передаче и совпадение делительных окружностей ведущей шестерни и ведомого зубчатого колеса.
Существует мнение, согласно которому расточку остовов на горизонтально-расточном станке можно производить только борштангой с использование стойки. Иначе достичь чертежных требований параллельности и размещения в одной плоскости горловин остовов двигателя невозможно
Но как показывает практика при грамотном технологическом подходе можно достигать требуемой точности и без применения борштанги и задней стойки. Для этого необходимо соблюдение следующих условий:
- горизонтально-расточной станок должен быть оснащен поворотным столом;
- стол должен иметь систему оптического контроля угла поворота;
- состояние подшипников шпиндельного узла должно обеспечивать величину биения шпинделя не более 0,05мм (при полном вылете)
Рис. 6 Расточка остовов ТЭД на горизонтально расточном станке
Отличительной особенностью конструкции остовов тяговых электродвигателей отсутствие плоских поверхностей, которые можно было бы использовать в качестве технологической базы. В процессе механической обработки при изготовлении новых ТЭД на электромашиностроительных предприятиях расточка горловин осуществляется одновременно двумя борштангами специальными двухшпиндельными станками. И поэтому единственной базой является централь. Этим также объясняется отсутствие ремонтного допуска на изменение межосевого расстояния, как и тем, что централь является и межосевым размером зубчатого зацепления. Таким образом, процесс технологического базирования является многоступенчатым и носит косвенный характер. Это вызывает увеличение вспомогательного технологического времени затраченного на установку и базирование остова на станке.
|
В начале 80-х годов на остовах тяговых электродвигателях ЭД118Б по требованию МПС предприняты попытки создания дополнительных технологических баз для ремонтных нужд. Эти базы представляют собой приливы на верхней части остова в виде паралепипеда с фрезерованной верхней плоскостью. Но это не упростило задач технологического базирования и обеспечения точности ремонтного процесса.
В середине 80-х годов НПО станкостроения г. Иваново разработаны и изготовлены для электромашинного производства специальные расточные станки ИР-375. В его конструкции базирования остовов осуществляется не на столе станка, а на специальных приспособлениях – спутниках, входящих в комплект поставки станка. Спутник представляет собой точно изготовленную плиту. Плита оборудована всем необходимым для базирования, фиксации и крепления остова. На спутнике линия централи устанавливается горизонтально, то есть параллельно поверхности спутника. Спутник вместе с закрепленным остовом устанавливается на стол станка и фиксируется в одном из крайних положений. Крайние положения остова точно соответствуют положению, при которых ось шпинделей станка совпадает с осью той или иной горловины. Шпиндели станка, расположенные с двух противоположных сторон остова, оборудованы суппортами установки резцов для расточки моторно-осевой и якорной горловин, а также обработки их торцевых поверхностей. Фиксированный размер перемещения из одного крайнего положения спутника в другое строго соответствует размеру централи.
В случае износа отверстий или повреждения резьбы они заплавляются электродуговой сваркой с использованием порошковой проволоки или в среде углекислого газа. После расточки остов устанавливается с вертикальным направлением осей горловин. Производится сверление отверстий и нарезание резьбы. Сверление осуществляется при помощи кондуктора, который базируется на внутренней цилиндрической поверхности якорной горловины. Обычно используется радиально сверлильный станок 2М55 или 2К555.
|
|
История развития пистолетов-пулеметов: Предпосылкой для возникновения пистолетов-пулеметов послужила давняя тенденция тяготения винтовок...
Индивидуальные очистные сооружения: К классу индивидуальных очистных сооружений относят сооружения, пропускная способность которых...
Организация стока поверхностных вод: Наибольшее количество влаги на земном шаре испаряется с поверхности морей и океанов (88‰)...
Поперечные профили набережных и береговой полосы: На городских территориях берегоукрепление проектируют с учетом технических и экономических требований, но особое значение придают эстетическим...
© cyberpedia.su 2017-2024 - Не является автором материалов. Исключительное право сохранено за автором текста.
Если вы не хотите, чтобы данный материал был у нас на сайте, перейдите по ссылке: Нарушение авторских прав. Мы поможем в написании вашей работы!