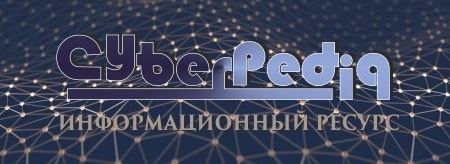
Опора деревянной одностоечной и способы укрепление угловых опор: Опоры ВЛ - конструкции, предназначенные для поддерживания проводов на необходимой высоте над землей, водой...
Особенности сооружения опор в сложных условиях: Сооружение ВЛ в районах с суровыми климатическими и тяжелыми геологическими условиями...
Топ:
Проблема типологии научных революций: Глобальные научные революции и типы научной рациональности...
Методика измерений сопротивления растеканию тока анодного заземления: Анодный заземлитель (анод) – проводник, погруженный в электролитическую среду (грунт, раствор электролита) и подключенный к положительному...
Устройство и оснащение процедурного кабинета: Решающая роль в обеспечении правильного лечения пациентов отводится процедурной медсестре...
Интересное:
Подходы к решению темы фильма: Существует три основных типа исторического фильма, имеющих между собой много общего...
Уполаживание и террасирование склонов: Если глубина оврага более 5 м необходимо устройство берм. Варианты использования оврагов для градостроительных целей...
Распространение рака на другие отдаленные от желудка органы: Характерных симптомов рака желудка не существует. Выраженные симптомы появляются, когда опухоль...
Дисциплины:
![]() |
![]() |
5.00
из
|
Заказать работу |
|
|
Лекция 2
Производственно-оперативное планирование. Его место в системе внутризаводского планирования. Задачи. Этапы.
Планирование производственной деятельности состоит из следующих, последовательно осуществляемых элементов:
1) разработка плана;
2) разработка и внедрение в производство организационно-технических мероприятий, обеспечивающих выполнение плана;
3) подготовка выполнения плана средствами производства, рабочей силой, технической документацией и пр.;
4) оперативное регулирование, перераспределение ресурсов в ходе выполнения планов;
5) учет, контроль и анализ результатов выполнения планов.
Планирование производственной деятельности предприятия по каждому объекту состоит из двух увязанных между собой частей:
- технико-экономического;
- оперативно-производственного.
Различие между этими двумя частями внутризаводского планирования заключается прежде всего в объектах планирования и учета.
Такие объекты планирования и учета:
- общий объем продукции, задаваемый заводу (цеху),
- себестоимость продукции,
- производительность труда,
- затраты и экономия средств производства на единицу продукции (на 1000 руб. выпуска),
- экономическая эффективность оргтехмероприятий,
- рентабельность производства и др., являются важнейшими в системе технико-экономического планирования.
I. Различие между ними — разные сроки планируемых мероприятий.
Технико-экономическое планирование осуществляется путем разработок перспективных плановых заданий и расчетов, охватывающих производственно-хозяйственную деятельность за большие отрезки времени (5 и более лет, год, квартал и месяц), без дифференциации их в форме календарного плана на короткие отрезки времени.
|
Назначением оперативно-производственного планирования является расчленение перспективных заданий, их распределение по исполнителям (цехам, участкам и рабочим местам) на более короткие отрезки времени: по кварталам, месяцам, декадам, пятидневкам, суткам, сменам и нередко по часовому графику.
II. Следующее различие определяется применяемыми планово-учетными единицами.
Технико-экономическое планирование характеризуется объемным характером расчетов. Наиболее важными объектами планирования и учета здесь являются:
- объем продукции, подлежащей изготовлению предприятием, цехом, участком, бригадой;
- необходимый для этого общий объем трудовых и денежных затрат;
- объем работ и затрат по обеспечению основного производства инструментом, ремонтом, материалом;
- объем выпуска на одного рабочего и т. д.
Оперативно-производственное планирование, исходя из установленных общих объемных показателей, расчленяет плановое задание на составные части, определяет подлежащие выполнению конкретные работы и по каждой работе — сроки и место выполнения.
III. Наконец, различны и единицы измерения, используемые для плановых расчетов. Конечные результаты технико-экономических расчетов, как правило, имеют ценностное выражение, а для оперативно-производственного планирования характерными являются расчеты в натуральном или трудовом выражении.
Несмотря на существенные различия технико-экономическое и оперативно-производственное планирования тесно связанны и взаимообусловленны части единого процесса внутризаводского планирования.
Задачи оперативно-производственного планирования
В машиностроении оперативно-производственное планирование является одним из основных факторов, обусловливающих решение следующих задач:
1. Равномерное и комплектное выполнение производственной программы и соблюдение директивных и договорных сроков выпуска товарной продукции.
|
2. Полное и наиболее целесообразное использование средств производства и трудовых ресурсов предприятия.
3. Минимальное связывание оборотных средств в стадии производства.
4. Создание условий, способствующих развитию передовых форм организации труда.
5. Обеспечение условий для механизации и автоматизации основных объемных и календарных расчетов путем точного (математического) формулирования решаемых задач оперативно-производственного планирования, подготовки исходной и нормативной информации, а также соответствующих форм документации.
Решение первой основной задачи говорит о непосредственном воздействии оперативно-производственного планирования на выполнение задания по наиболее важному показателю техпромфинплана - показателю выпуска и реализации продукции.
Решение второй задачи — полного и наиболее целесообразного использования средств производства и трудовых ресурсов предприятия обеспечивается оперативно-производственным планированием с помощью:
1) тщательных расчетов полноты и равномерной занятости трудовых ресурсов и площадей;
2) такого распределения задания между цехами, участками и рабочими местами, при котором равномерная загрузка оборудования и рабочей силы сочетается с минимальными размерами простоев во время настройки и подготовки к работе;
3) широкого внедрения поточных форм организации работ;
4) максимальной специализации рабочих мест на производстве ограниченного числа различных технологических операций.
Минимальное связывание оборотных средств в стадии производства обеспечивается оперативно-производственным планированием путем такого распределения заказа во времени по рабочим местам при котором обеспечивается максимальное сокращение длительности производственного цикла заготовок, деталей, узлов и изделия в целом, и в результате — максимальное уменьшение незавершенного производства и ускорение оборачиваемости оборотных средств в производстве.
Этапы оперативно-производственного планирования
Вес расчеты, связанные с оперативно-производственным планированием, должны вестись постепенной детализацией производственных заданий и путем постепенного их уточнения по мере выяснения результатов работы за истекший период, выявления дополнительных ресурсов и внесения необходимых коррективов в планы последующих периодов времени (квартал, месяц, декада и т. д.).
|
Оперативно-производственное планирование на предприятии осуществляется тремя последовательными этапами.
На I этапе органы оперативно-производственного и технико-экономического планирования распределяют производственную программу по месяцам планового года и на каждый месяц (квартал) определяют программу работы каждого цеха. Для этой цели по каждому цеху рассчитывают, с одной стороны, минимально необходимые ему для выполнения заданий ресурсы (рабочую силу, оборудование и площади), с другой — ресурсы, которыми располагает цех.
Сопоставляя потребные ресурсы с имеющимися в цехе, определяют при необходимости такие оргтехмероприятия, которые устранят недостаток ресурсов или при наличии их излишков обеспечат досрочное выполнение цехами заданий и о необходимости дополнительных заданий цеху на плановый год.
В результате объемных расчетов составляются для каждого цеха плановые задания на год и кварталы в натуральном и трудовом (в некоторых случаях и в ценностном) измерениях.
I этап условно называется этапом объемного планирования, поскольку основное его содержание заключается в объемных расчетах.
На II этапе оперативно-производственного планирования производится дальнейшая детализация и дифференциация по срокам, а также уточнение разработанных на I этапе плановых заданий по каждому цеху.
Объектом планирования на этом этапе являются отдельные узлы и детали и их движение в производстве как в пределах данного цеха, так и между отдельными цехами.
В этом смысле планы на II этапе являются более дифференцированными и уточненными. Уточняются сроки производства:
- общие сроки, устанавливаемые на I этапе на всю совокупность работ по плановому заданию (на квартал и месяц) и
- корректируются путем детализации их для каждого участка или бригады по каждому узлу, каждой детали и даже операции.
Составляется календарный план производства изделий не только по заготовительной, обработочной и сборочной стадиям отдельно, но и по точно увязанным срокам между ними с распределением работ по участкам и даже по рабочим местам в пределах каждого цеха.
|
Важным содержанием работ на этом этапе планирования являются нормативные расчеты:
- расчеты размеров партий и длительности производственных циклов,
- расчеты внутрицеховых и межцеховых запасов заготовок, деталей и узлов, необходимых для обеспечения бесперебойной работы цехов и участков.
II этап условно называется этапом составления календарного плана производства.
Основным содержанием календарного плана является построение сложной системы сроков производства по изделию в целом, по отдельным узлам, деталям и в некоторых случаях по отдельным операциям.
III этап (заключительный) планирования характеризуется окончательным уточнением производственных заданий и организацией их выполнения: точно определяются по каждому рабочему месту наименования работ и задания конкретным исполнителям на каждую смену. На этом этапе основным содержанием оперативно-производственного планирования являются:
1) точное формулирование задания каждому рабочему месту на смену;
2) ежедневный учет фактических результатов производства и на их основании корректирование сроков и планов, разработанных на I и II этапах;
3) регулирование работ между рабочими местами, между участками и цехами в целях предупреждения и устранения потерь, могущих возникнуть или возникших вследствие всякого рода отклонений от предусмотренных в плане наименований и сроков окончания работ.
III этап оперативно-производственного планирования условно называется оперативным планированием, поскольку характерным содержанием на этом этапе является разработка и осуществление оперативных мероприятий, т. е. таких, выполнение которых должно быть по возможности немедленным, а не в перспективе:
- оперативное регулирование работ между рабочими местами,
- обеспечение их материальными элементами подготовки производства,
- своевременная регистрация отклонений от плана и
- внесение коррективов в графики работ на каждый день, смену.
Перечисленные три этапа по своему содержанию не являются самостоятельными звеньями в системе оперативно-производственного планирования, а составляют единый процесс планирования, каждый этап которого представляет собой развитие, уточнение и исправление содержания предыдущего этапа.
Оперативно-производственное планирование на машиностроительном предприятии может быть как межцеховое, так и внутрицеховое.
На I этапе в системе межцехового планирования органы оперативно-производственного планирования, базируясь на производственной программе предприятия, устанавливают плановое задание - программу выпуска продукции в плановом периоде для каждого цеха, обосновывая ее соответствующими объемными расчетами.
|
В системе внутрицехового планирования па I этапе определяют программу (наименование и объем продукции) на плановый период для каждого участка, обосновывая ее также объемными расчетами. Детализация производственной программы в первом и во втором случаях может иметь различную степень.
Календарный план (II этап) в системе межцехового планирования регламентирует сроки движения продукции по цехам завода, не раскрывая частных, внутрицеховых пооперационных сроков производства по каждому предмету.
В системе же внутрицехового планирования календарный план увязывает между собой работу участков цеха или отдельных групп оборудования в пределах каждого участка и в результате устанавливает по каждой детали (заготовке) или по комплекту деталей сроки запуска в первую операцию, сроки прохождения по операциям технологического процесса или по участкам цеха и сроки выпуска в готовом виде.
На III этапе межцехового планирования осуществляется учет, контроль и оперативное регулирование работ между цехами (обеспечение своевременного движения продукции из цеха в цех), а в системе внутрицехового планирования эти же функции осуществляются по каждому цеху в целях обеспечения установленных в календарном плане сроков движения продукции по участкам и отдельным рабочим местам.
Межцеховое оперативно-производственное планирование осуществляется в центральном планово-производственном отделе (ППО) предприятия, называемым также планово-диспетчерским отделом (ПДО) предприятия.
Внутрицеховое оперативно-производственное планирование осуществляется в планово-диспетчерском бюро (ПДБ) цеха.
Границы межцехового и внутрицехового планирования могут заметно измениться по мере развития и практического внедрения автоматизированных систем управления процессом производства.
Лекция 3
Основные факторы, обусловливающие содержание объемного планирования. Задачи.Фонды времени.
Объемное планирование как первый этап оперативно-производственное планирование (ОПП) решает две взаимосвязанные задачи.
1. Определение номенклатуры продукции, включаемой в программу цехов и участков по отрезкам планового года.
2. Проверка путем объемных расчетов соответствия планируемой номенклатуры ресурсам цехов и участков (трудовым, по оборудованию и площадям).
Программа цеха (участка), проверенная на соответствие имеющимся ресурсам, должна содержать:
- номенклатуру готовой (в данном цехе) продукции;
- количество и дифференцированные сроки выпуска по каждой позиции;
- необходимый объем работ, который должен выполнить цех (участок).
В номенклатурное задание включается готовая продукция цеха как реализуемая на стороне товарная продукция предприятия (готовые заготовки, детали, узлы), так и та, которая подлежит дальнейшей обработке (или сборке) в других цехах.
Степень детализации объемного планирования и расчетов, а также их характер обусловлены в первую очередь трудоемкостью производства, масштабом и степенью регулярности выпуска по отдельным позициям программы.
В цехах с регулярно повторяющимся выпуском одной и той же продукции (серийное производство) загрузка рабочих мест также повторяется регулярно из месяца в месяц по объему и в основном по ассортименту работ. Объем загрузки изменяется (увеличивается или уменьшается) в соответствии с количественным ростом или сокращением выпуска по отдельным изделиям.
Для цехов с мелкосерийным производством характерны нерегулярное повторение выпуска одной и той же продукции и большее число различных изделий в программе.
В связи с этим на каждый плановый период (квартал, месяц) в задании цеху необходимо предусмотреть особый комплекс изделий различных наименований с таким расчетом, чтобы суммарный объем работ обеспечивал полное использование имеющихся ресурсов.
В условиях неповторяющегося единичного производства указанное усложнение расчетов увеличивается. Наиболее сложным следует считать широко распространенный в машиностроении случай, когда в цехе и на его участках сочетается продукция серийного, мелкосерийного и единичного типов производства.
Другим серьезным фактором, обусловливающим характер и сложность объемного планирования, является длительность производственного цикла изделия. Чем больше длительность производственного цикла изделия выходит за пределы планового периода тем сложнее объемное планирование.
Необходимость заблаговременного развертывания производства вынуждает включить в программу планового периода не весь комплект частей изделий (заготовок деталей, узлов), а только некоторую часть их, а остальную часть планировать на более ранние периоды.
Наконец, фактором, влияющим на степень детализации номенклатурных заданий основным цехам и на сложность объемных расчетов является уровень предметной специализации подразделений предприятия.
Структура фондов времени оборудования и затрат времени на производство
В производстве, как правило, имеют место потери, возникающие по техническим и организационным причинам. Выявление причин и правильная классификация этих потерь являются важными условиями как для соблюдения необходимой точности объемных расчетов, так и для успешной борьбы за их всемерное сокращение и устранение.
В системе оперативно-производственного планирования одни потери учитываются в минимально неизбежных размерах (на ремонт оборудования), а другие - полностью устранимые — учитываются только в той мере, в какой их устранение не обеспечено в плановом периоде соответствующими организационно-техническими мероприятиями (связанные с отсутствием технической документацией и др.).
В соответствии с этим потери в использовании оборудования (производственных площадей) и трудовых ресурсов, являющиеся возможными резервами загрузки цехов и участков, по их характеру и источникам возникновения могут быть разделены натри категории:
1. Потери, сокращающие полезный фонд времени оборудования.
2. Потери, связанные с непроизводительной или недостаточно производительной работой оборудования, увеличивающие затраты времени на производство.
3. Потери от некомплектности оборудования.
Потери, сокращающие полезный фонд времени оборудования (производственных площадей) могут быть в свою очередь разделены на три группы:
Первая группа — потери, связанные с режимом работы, установленным для (машиностроительной) промышленности (Ппром):
- выходные и праздничные дни;
- сокращенная длительность рабочей недели. Если из полного календарного фонда времени (24.365) вычесть эти потери, то оставшееся количество часов составит просто календарный фонд времени Fk.
Вторая группа — потери, связанные с режимом, установленным для данного предприятия (Пцред):
- нерабочие смены.
Остаток после вычета этих потерь из Fk является календарным фондом времени, возможным для использования F воз-
Третья группа — потери от простоев оборудования по организационно-техническим причинам (Порг):
- ремонт оборудования;
- неудовлетворительная организация обслуживания рабочих мест;
- неудовлетворительное оперативно-производственное планирование.
При объемных же расчетах на годовой отрезок времени норма потерь на ремонт по разным группам оборудования может заметно колебаться, так как вывод в капитальный и текущий ремонты отдельных единиц оборудования подчинен их индивидуальному графику.
Потери, возникающие от неудовлетворительной организации обслуживания рабочих мест и недостатков оперативно-производственного планирования, относятся к категории полностью устранимых. Тем не менее их действительная величина на предприятиях велика и нередко выходит за пределы 10 % фонда времени оборудования. В то же время практически эти потери возникают в скрытой форме и при объемных расчетах не учитываются.
К потерям, связанным с непроизводительной или недостаточно производительной работой оборудования, относятся резервы и потери, связанные с превышением затрат времени на производство продукции (см. табл. 2.1).
В табл. 2.1 представлена структура фонда времени оборудования и его использования. В правой части таблицы показана известная в техническом нормировании структура затрат времени на производство.
По данным табл. 2.1 видно, что превышение может иметь место в отношении любого элемента калькуляционного времени. Задача заключается в выявлении размеров этих потерь или возможных резервов, в разработке и проведении необходимых конструктивно-технологических и организационно-плановых мероприятий по их снижению или использованию резервов.
Калькуляционное время tк не может служить нормой затрат времени (труда) на единицу продукции, поскольку оно, как правило, не отражает достигнутого уровня производительности труда. В основу значительной части расчетов на всех трех этапах оперативно-производственного планирования должны быть положены действительные затраты времени на единицу продукции, а именно, калькуляционное время, деленное на средний коэффициент выполнения норм kв
В kв получают отражение как средние величины снижения перечисленных в табл. 2.1 потерь, включаемых в калькуляционное время, так и допущенные в процессе производства потери на непроизводительную работу tбp (брак и дополнительные работы).
С учетом сказанного затрачиваемое на единицу продукции время в дальнейшем изложении будет называться необходимым временем tн.
Группы оборудования загружаются неравномерно: одни перегружаются работой, образуя «узкие места», другие, наоборот, имеют неиспользованные излишки фонда времени. Этот вид потерь достигает значительных размеров.
Понятия необходимого времени tн на производство и используемого фонда времени оборудования имеют наиболее широкое применение в расчетах оперативно-производственного планирования.
Лекция 4
Лекция 5
Планирование производственных мощностей цехов и участков. Особенности.
Объемные расчеты загрузки цехов и участков имеют своим назначением:
1) проверить соответствие производственной программы, рассчитанной по месяцам (кварталам) планового года, используемому фонду времени (Рд) цехов и участков;
2) устранить или ослабить несоответствие программы ресурсам цехов (участков) путем перераспределения ее по месяцам (кварталам) планового года.
Для определения объема работ по цеху (или отделению цеха — стадии): необходимо получить по каждому изделию следующие данные:
2. Упрощенные графики производственного цикла изделий мелкосерийного и единичного производства. (см. рис. 3.1).
3. Распределение объема работ (выраженного в единицах необходимого времени) по месяцам опережения выпуска готового изделия (или партии изделий) и по каждой стадии отдельно (см. нижнюю часть рис. 3.1).
В табл. 3.1 показано распределение остатка используемого фонда времени Фд по изделиям и месяцам первого полугодия планового года. Такое распределение, разумеется, выполняется на основании запланированного варианта распределения производственной программы и графиков длительности производственного цикла по данной стадии.
В верхней части табл. 3.1 показано в первом варианте распределение объема механической обработки по месяцам.
В средней части таблицы записаны суммарные объемы необходимого времени по всем указанным изделиям, полученные в каждом k -м. месяце:
В нижней части табл. 3.1 показаны остатки используемого фонда времени в каждом месяце планового периода (первые шесть месяцев) Фf, и получаемые излишки или недостаток этих остатков после вычитания суммарного объема необходимого времени (по каждому из двух вариантов распределения).
В табл. 3.1 показаны два варианта распределения производственной программы. По первому варианту срок выпуска готового изделия В установлен в V мес и соответственно установлены сроки опережения по механической обработке всего множества деталей (I, II и III мес). Далее срок выпуска готового изделия С установлен в IV мес, а сроки опережения механической обработки II и III мес
По I-му варианту недостаток используемого фонда времени имеет место в первых месяцах планового периода, а излишки фонда — в последующие месяцы (не рационально).
При втором варианте распределения производственной программы излишки и недостатки используемого фонда времени размещаются более рационально. Следует отметить, что излишек в 1 мес в объеме 5450 ч компенсирует значительную часть недостатков во II—IV мес; это в оперативных условиях значительно облегчает преодоление остающейся перегрузки в 2100ч.
Уточненные объемные расчеты по каждой стадии производства имеют своим назначением:
1) определить по каждой группе оборудования или сборочных рабочих мест соответствие объема работ, подлежащего выполнению участками цеха за плановый период, имеющимся трудовым ресурсам;
2) наметить мероприятия по устранению диспропорции в использовании трудовых ресурсов по профессиям и квалификации основных рабочих;
3) уточнить уровень загрузки и сменности групп оборудования в процессе производства для определения резервов их использования и расстановки основных рабочих участка по рабочим местам.
Уточненные объемные расчеты выполняются непосредственно перед началом планового периода (квартала, месяца), т. е. когда результаты производства за отчетный период выявлены, потребность и программа в номенклатуре по каждой стадии производства на новый плановый период (заготовки, детали, узлы конкретных наименований) уточнены.
Объем необходимого времени по уточненной номенклатуре, определенный в сумме по всем группам оборудования и сборочных мест, может заметно отличаться от соответствующих данных, полученных после предварительных объемных расчетов. Точно также и фактически имеющиеся трудовые ресурсы к началу планового периода могут не совпадать с потребными расчетами, выраженными в суммарном фонде используемого времени Fк при предварительных объемных расчетах. Поэтому важно определить, имеет ли место в наступающем k-м плановом периоде по каждой данной j-й группе оборудования (рабочих мест) излишек или недостаток трудовых ресурсов:
Излишек или недостаток ресурсов по отдельным группам оборудования используется или устраняется (недостаток) различными методами, в частности путем организации соответствующей межучастковой, межцеховой и при необходимости межзаводской коопераций.
Уровень использования групп оборудования в уточненных объемных расчетах определяется путем сопоставления располагаемого для работы фонда времени с необходимым временем на программу. Это сопоставление может быть выполнено в двух формах:
- определением излишка или недостатка ресурсов и
- оценкой среднего коэффициента загрузки оборудования.
работы фонд времени, то должны быть намечены мероприятия, обеспечивающие повышение ее пропускной способности или разгружающие эту группу оборудования от части работ.
На этапе объемных расчетов, помимо коэффициента загрузки, полезно знать средний коэффициент сменности действующего оборудования.
Средним коэффициентом сменности Ксм j работы данной группы оборудования называется величина отношения необходимого для выполнения программы фонда времени к располагаемому фонду, взятому в одну смену.
При правильном его применении и соответствующей расстановке рабочих по сменам. Ксм j позволяет календарно сократить продолжительность выполнения данной операции.
Предварительные объемные расчеты выполняются в центральном планово-производственном органе предприятия. Уточненные — в цеховом плановом органе.
Лекция 6 (1)
Понятие календарного плана и основные принципы его разработки. План-график движения детали в производственном цикле. Длительность цикла. состав работ при разработке календарного плана.
Содержание и методы построения календарного плана видоизменяются значительно в зависимости от степени неизменности производственных условий на рабочих местах участков и цехов, участвующих в производстве планируемых изделий.
Поэтому методы разработки календарного плана должны быть рассмотрены раздельно по каждому основному типу производства (единичное, серийное, массовое). В то же время сущность и целевое назначение разработки календарного плана для любых производственных условий являются неизменными.
Если представить себе план производства отдельной детали машины как часть календарного плана изготовления всего изделия, то в условиях любого типа производства при любой сложности и трудоемкости технологического процесса его построение всегда подчинено простому графику, изображенному на рис. 4.1.
При любой системе планирования производства решение этой задачи состоит из совокупности расчетов и построений:
1. Расчет и построение плана или графика производственного цикла главной сборки изделия на основе расчленения сборочного процесса на ko этапов (укрупненных операций) и определение срока f подачи.
2. Расчет длительности производственного цикла сборки узла ef и определение срока (в точке е) подачи готовой детали
3. Построение плана движения детали по операциям и определение длительности нахождения ее на этих стадиях cd и аЬ.
4. Определение длительности межцеховых перерывов в производстве tмц - отрезки be, dе и f о.
Отрезки ab и ор показывают опережение первой заготовительной операции, которое необходимо предусмотреть в процессе производства предмета чтобы обеспечить своевременное начало механической обработки.
Разработка календарного плана производства машины в целом, состоящей обычно из сотен, тысячи и более частей, естественно, значительно сложнее. Возникает ряд трудных задач, которые должны быть решены еще до составления календарного плана.
Должен быть решен вопрос о периоде планирования: составлять ли календарный план однажды на целый год или четыре раза в год — на каждый квартал или двенадцать раз — на каждый месяц. Целесообразность каждого из этих вариантов определяется производственными условиями. Календарный план в целом по всем деталям (узлам) должен содержать определенный объем работ, равномерно распределенный по частям планового периода и рассчитанный на равномерную и полную загрузку основных рабочих, оборудования и площадей.
Следует отметить (см. рис. 4.1), что длительность периода ар, полученная в результате построения календарного плана по отдельным стадиям технологического процесса, имеет важное экономическое значение. В течение этого периода затраты на изготовление данной детали, постепенно нарастая по мере выполнения каждой следующей операции, остаются связанными в производстве и освобождаются только после выпуска готового изделия и его реализации. Чем короче отрезок времени ар, тем, следовательно, быстрее происходит нарастание затрат, тем скорее они возвращаются предприятию, содействуя общему ускорению оборота оборотных средств.
Выбор варианта календарного плана усложняется необходимостью целесообразного сочетания ускорения оборота оборотных средств с высоким уровнем производительности труда, использования основных фондов и рабочих основных профессий, т.е. такого важного показателя, как снижение себестоимости продукции. В связи с этим индивидуальная форма движения предмета в производстве не всегда является экономически наиболее целесообразной. Так основной формой движения в серийном производстве является работа партиями, сокращающая удельную величину затрат на настройку оборудования и на подготовку к работе, а также способствующая уменьшению штучного времени.
В машиностроении для различных частей одного и того же изделия могут быть применены различные методы построения календарного плана. При этом выбор метода в каждом случае должен быть подчинен требованиям наибольшей экономической целесообразности. Построению календарного плана должна предшествует большая расчетно-подготовительная работа, состоящая из двух основных частей.
Первая часть этой работы заключается в разработке и внедрении мероприятий по совершенствованию производственной структуры завода и цехов.
Углубление предметной специализации надо понимать как стремление к полному замыканию технологического процесса изготовляемой продукции в рамках данного цеха, т. е. без отвлечения продукции в другие цехи для выполнения промежуточных или конечных операций (например, для выполнения шлифовальных, зуборезных и других операций).
Совершенствование производственной структуры завода и цехов заметно повышает экономические показатели работы предприятия. Переход на предметную организацию участков позволяет четко формулировать ответственность руководства ими за своевременный выпуск готовых частей изделия и избежать необходимости пооперационного планирования сроков производства и выпуска.
Совершенствование производственной структуры осуществляется путем закрепления за данным цехом и каждым его участком целых групп однородной продукции и соответствующим расчетом потребного оборудования, а также численности производственных рабочих.
Вторая часть расчетно-подготовительной работы заключается в выполнении нормативных расчетов, обусловливающих характер движения предметов производства по операциям и стадиям технологического процесса.
По каждому наименованию предмета и по каждой стадии должны быть выполнены следующие нормативные расчеты:
1) расчеты нормальных размеров партии;
2) расчеты длительности производственного цикла;
3) определение периодичности повторения производства;
4) расчеты незавершенного производства.
Нормативные расчеты служат исходными данными для построения календарного плана производства.
Разработка календарного плана и связанные с ним нормативные расчеты должны быть подчинены независимо от типа производства следующим основным принципам.
1. Своевременность производства — система очередности (сроков) производства частей изделия должна быть выдержана в календарном плане одновременно в двух направлениях:
- точного соблюдения (в количествах и сроках) директивного задания по выпуску готовой продукции;
- планомерного, полного и наиболее целесообразного использования трудовых ресурсов, рабочих механизмов и производственных площадей.
2. Периодичность производства — нормативные расчеты и система сроков в календарном плане должны обеспечить ритмичное повторение производства отдельных частей изделия в соответствии с характером и масштабам ритмичного выпуска готовой продукции.
3. Комплектность производства — система очередности (приоритета) производства по отдельным изделиям в календарном плане должна обеспечить комплектное производство по всей совокупности изделий, предусмотренной в производственной программе завода и соответственно комплектный выпуск готовой продукции.
4. Максимальная простота построения, допускаемая сферой применения календарного плана, — степень дифференциации сроков в плане должна соответствовать необходимой точности их исполнения.
Все это значит:
- если календарный план составлен пооперационно, т. е. сроки регламентированы по каждой операции предмета данного наименования, то его выполнение учитыв<
|
|
Особенности сооружения опор в сложных условиях: Сооружение ВЛ в районах с суровыми климатическими и тяжелыми геологическими условиями...
Общие условия выбора системы дренажа: Система дренажа выбирается в зависимости от характера защищаемого...
Организация стока поверхностных вод: Наибольшее количество влаги на земном шаре испаряется с поверхности морей и океанов (88‰)...
Биохимия спиртового брожения: Основу технологии получения пива составляет спиртовое брожение, - при котором сахар превращается...
© cyberpedia.su 2017-2024 - Не является автором материалов. Исключительное право сохранено за автором текста.
Если вы не хотите, чтобы данный материал был у нас на сайте, перейдите по ссылке: Нарушение авторских прав. Мы поможем в написании вашей работы!