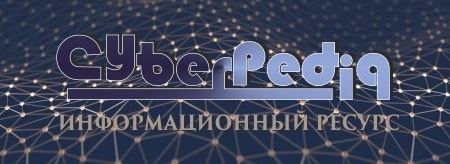
Семя – орган полового размножения и расселения растений: наружи у семян имеется плотный покров – кожура...
Индивидуальные очистные сооружения: К классу индивидуальных очистных сооружений относят сооружения, пропускная способность которых...
Топ:
Оценка эффективности инструментов коммуникационной политики: Внешние коммуникации - обмен информацией между организацией и её внешней средой...
Генеалогическое древо Султанов Османской империи: Османские правители, вначале, будучи еще бейлербеями Анатолии, женились на дочерях византийских императоров...
Организация стока поверхностных вод: Наибольшее количество влаги на земном шаре испаряется с поверхности морей и океанов...
Интересное:
Подходы к решению темы фильма: Существует три основных типа исторического фильма, имеющих между собой много общего...
Что нужно делать при лейкемии: Прежде всего, необходимо выяснить, не страдаете ли вы каким-либо душевным недугом...
Финансовый рынок и его значение в управлении денежными потоками на современном этапе: любому предприятию для расширения производства и увеличения прибыли нужны...
Дисциплины:
![]() |
![]() |
5.00
из
|
Заказать работу |
|
|
Прокатка позволяет с наименьшими удельными затратами производить изделия, которые либо полностью воспроизводят предусмотренное конструктором поперечное сечение детали, либо максимально приближаются к нему. Прокатка обладает более высокими технико-экономическими показателями по сравнению с другими способами обработки металлов: высокой производительностью, низкой себестоимостью и высоким коэффициентом использования металла. Заготовки из проката используют при непосредственном изготовлении из них деталей на металлорежущих станках и для получения поковок.
При продольной прокатке (рис.6.1, а) заготовка 1деформируется между двумя валками 2, вращающимися в разные стороны, и перемещается в направлении, перпендикулярном осям валков.
При поперечной прокатке (рис.6.1, б) валки 2 вращаются в одном направлении, а заготовка 7, имеющая форму тела вращения, перемещается параллельно осям валков и обжимается по образующей с увеличением длины и уменьшением площади поперечного сечения.
При поперечно-винтовой прокатке (рис.6.1, в) валки 2 расположены под углом друг к другу, вращаются в одну сторону и при обжатии заготовки 1 сообщают ей вращательное и поступательное движения. В процессе прокатки во всех случаях перемещение заготовки между валками обеспечивается наличием контактного трения между обрабатываемой заготовкой и рабочей поверхностью валков.
Рисуеок 6.1 - Схема основных видов прокатки: а - продольная; б - поперечная; в - поперечно-винтовая
Круглый сортовой прокат (постоянное поперечное сечение) используют для изготовления гладких и ступенчатых валов с небольшим перепадом ступеней, стаканов диаметром до 50 мм и втулок с наружным диаметром до 25 мм. Предусматривается ГОСТом 2590-71 следующие диаметры круглого проката 5, 5.5, 6, 6.3, 6.5, 7-48 через 1 мм, 50, 52, 53, 55, 56, 57, 58, 60, 62, 63, 65, 68, 70, 72, 75, 78, 80, 82, 85, далее до 135 через 5 мм, 140-250 через 10 мм.
|
Сортовой квадратный ГОСТ 2591-71 5-48 мм через 1 мм, 50, 52, 55, 58, 60, 63, 65, 70, 75, 80, 85, 90, 93, 95, далее до 150 мм через 5 мм, от 160 до 200 через 10 мм.
Сортовой шестигранный ГОСТ2879-69 диаметр вписанного круга 8-22 через 1 мм, 24,25,26, 28, 30, 32, 34, 36, 40, 42, 45, 48, 50, 52, 55, 60, 63, 65, далее до 100 мм через 5 мм.
Прямоугольный прокат ГОСТ 103-76 шириной от 11 до 200 мм и толщиной 4 - 60мм.
Применяют для изготовления крепежных деталей, небольших деталей типа тяг, рычагов и планок.
Листовой прокат идет на изготовление цилиндрических полых заготовок, фланцев и плоских деталей различной формы.
Трубы горячекатаные бесшовные ГОСТ 8732-78 и холоднодеформированные бесшовные ГОСТ 8734-75 используют для изготовления цилиндров, втулок, гильз, стаканов, барабанов, роликов, фланцев и т. п.
Периодический профильный прокат (поперечное сечение непостоянно) может быть продольным и поперечно-винтовым. Из продольного проката получают заготовки гаечных ключей, барашков, лопаток турбин, шатунов, вилок, рычагов и тонких деталей. Применение его позволяет по сравнению с обычным прокатом снизить расход металла на 15 %, повысить производительность труда на 25...30 % и уменьшить себестоимость заготовок на 10...20 %.
Из поперечно-винтового проката изготавливают шары для подшипников качения, углеразмольных и цементных мельниц, заготовки валов винтового профиля, полые профилированные трубчатые заготовки и пр.
Прессованные профили
Прессование - процесс выдавливания металла из контейнера через одно или несколько отверстий в матрице с площадью меньшей, чем поперечное сечение исходной заготовки. При прессовании реализуется одна из самых благоприятных схем нагружения, обеспечивающая максимальную пластичность - всестороннее неравномерное сжатие. Это позволяет обрабатывать даже малопластичные материалы. Обычно коэффициент вытяжки при прессовании составляет 10-50, а в отдельных случаях может быть значительно выше.
|
Прессование может выполняться двумя методами - прямым и обратным (рис. 6.2, а и б). При прямом методе (рис. 6.2, а) заготовку 1 помещают в полость контейнера 2 и с помощью мощного пресса через пуансон 3 и пресс-шайбу 4 выдавливают нагретый или холодный металл через отверстие в матрице 5, укрепленной в матрице-держателе 6.
При обратном прессовании (рис. 6.2, б) давление пресса передается через полый пуансон 3 с смонтированной внутри его матрицей 5. Таким образом, металл заготовки 1 течет навстречу движению пуансона.
При прямом прессовании требуется прикладывать значительно большее усилие, так как часть его затрачивается на преодоление трения при перемещении металла заготовки внутри матрицы. Отчасти поэтому значительная часть металла заготовки не может быть выдавлена из контейнера. Остающаяся его часть - пресс-остаток - составляет в отдельных случаях 30-40% от массы исходной заготовки.
Усилие при обратном прессовании примерно на 25% меньше, пресс-остаток также почти вдвое меньше, чем при прямом.
Однако сложность конструкции пресса, ограниченность размеров получаемых изделий по длине препятствуют широкому применению способа обратного прессования.
Рисунок 6.2 - Схемы прессования прямого (а), обратного (б) и пустотелого (в) профилей на примере трубы: 1 - заготовка; 2 - контейнер; 3 - пуансон; 4 - пресс-шайба; 5 - матрица; 6 - матрица-держатель; 7 - заглушка; 8 - игла
К достоинствам процесса прессования следует отнести возможность получения изделий сложных профилей, в том числе и пустотелых, не только из высокопластичных, но и малопластичных металлов и сплавов; универсальность применяемого оборудования, позволяющего легко переходить на производство профилей различных конфигураций; достаточно высокую точность размеров и малую шероховатость поверхности получаемых изделий. На рис. 19.13, в представлена схема получения пустотелого профиля типа тонкостенной трубы. Инструмент для прессования - контейнер, матрица, пресс-шайбы, иглы - работают в очень сложных условиях: больших удельных давлений до 150 кгс/мм2 и часто при высоких температурах. Температурный интервал прессования цветных металлов 500-900 °С, а сталей, никелевых и титановых сплавов 1000-1250 °С. Поэтому для изготовления инструмента применяют дорогие материалы с повышенными жаростойкостью и прочностными характеристиками. Стоимость комплекта инструмента для получения пустотелых профилей иногда достигает 15% от стоимости всего агрегата.
|
В качестве силового агрегата для прессования наибольшее распространение получили гидравлические прессы с усилием прессования 1000-5000 т. Они не боятся перегрузки, позволяют регулировать в широких пределах скорость перемещения силового плунжера, легко автоматизируются, в том числе с помощью систем программного управления.
Скорость прессования влияет на качество заготовки. Более пластичные, металлы обычно прессуют с большей скоростью, чем малопластичные. Например, скорость истечения стали составляет 6,..8 м/с, алюминия - до 25, а у магниевых сплавов - всего лишь 0,01...0,05 м/с.
Прессование широко применяют для получения изделий из меди, латуни, бронзы, алюминия, магния, цинка, титана, сталей, сплавов никеля.
Прессованием изготавливают прутки, трубы разнообразных сечений, используемые в качестве заготовок в машиностроении (заготовки для производства шестерен в часовой промышленности).
Прессование труб диаметром менее 20 мм экономически более выгодно, чем прокатка.
Качество получаемого продукта в существенной степени зависит от правильности выбранного режима и качества исходной заготовки. Например, минимальная вытяжка должна быть не менее 10-кратной; допускаются вытяжки весьма значительные: для меди- 280, латуни - 700, алюминия - 1000.
Считается оптимальным отношение длины к диаметру заготовки, равное 2-3 при производстве сплошных профилей и 1,5-2 для пустотелых.
Подготовка исходной заготовки заключается в зачистке поверхности и удалении обнаруженных дефектов, прошивке отверстий при производстве полых профилей, нанесении технологической смазки на поверхность. Роль смазки чрезвычайно высока: она снижает усилие деформирования, уменьшает неравномерность течения металла при прессовании, удлиняет срок службы инструмента, повышает качество поверхности. Выбор состава смазки зависит от рода обрабатываемого материала. Это может быть графит, добавляемый в минеральные масла, добавки канифоли. Для стали, сплавов никеля и титана, прессование которых ведут при высоких температурах, в качестве смазки применяют стекло.
На рис. 6.3 представлены примеры поперечного сечения профилей, полученных прессованием.
Рисунок 6.3 - Примеры прессованных профилей
|
|
Опора деревянной одностоечной и способы укрепление угловых опор: Опоры ВЛ - конструкции, предназначенные для поддерживания проводов на необходимой высоте над землей, водой...
Автоматическое растормаживание колес: Тормозные устройства колес предназначены для уменьшения длины пробега и улучшения маневрирования ВС при...
Поперечные профили набережных и береговой полосы: На городских территориях берегоукрепление проектируют с учетом технических и экономических требований, но особое значение придают эстетическим...
Особенности сооружения опор в сложных условиях: Сооружение ВЛ в районах с суровыми климатическими и тяжелыми геологическими условиями...
© cyberpedia.su 2017-2024 - Не является автором материалов. Исключительное право сохранено за автором текста.
Если вы не хотите, чтобы данный материал был у нас на сайте, перейдите по ссылке: Нарушение авторских прав. Мы поможем в написании вашей работы!