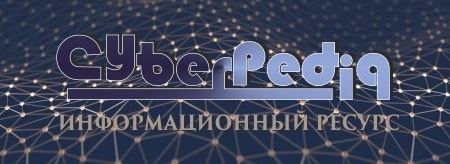
Наброски и зарисовки растений, плодов, цветов: Освоить конструктивное построение структуры дерева через зарисовки отдельных деревьев, группы деревьев...
Двойное оплодотворение у цветковых растений: Оплодотворение - это процесс слияния мужской и женской половых клеток с образованием зиготы...
Топ:
Теоретическая значимость работы: Описание теоретической значимости (ценности) результатов исследования должно присутствовать во введении...
Интересное:
Наиболее распространенные виды рака: Раковая опухоль — это самостоятельное новообразование, которое может возникнуть и от повышенного давления...
Уполаживание и террасирование склонов: Если глубина оврага более 5 м необходимо устройство берм. Варианты использования оврагов для градостроительных целей...
Средства для ингаляционного наркоза: Наркоз наступает в результате вдыхания (ингаляции) средств, которое осуществляют или с помощью маски...
Дисциплины:
![]() |
![]() |
5.00
из
|
Заказать работу |
|
|
В. П. Круглов, Г. М. Гончаров
РЕМОНТ И МОНТАЖ ТЕХНОЛОГИЧЕСКОГО ОБОРУДОВАНИЯ ПРЕДПРИЯТИЙ НЕФТЕХИМИЧЕСКОЙ ПРОМЫШЛЕННОСТИ
Рекомендовано
научно-методическим советом университета
в качестве учебно-методического пособия
ЯРОСЛАВЛЬ 2015
УДК 678.05.002.72.004/67
ББК 32.97
К84
Круглов, В.П.
К84 Ремонт и монтаж оборудования: учебно-методическое пособие / В.П. Круглов, Г. М. Гончаров. – Ярославль: Издат. дом ЯГТУ, 2015. – 118 с.
ISBN
Изложены основы организации и проведения ремонта основных узлов и монтажа технологического оборудования предприятий нефтехимической промышленности. Приведены краткие сведения об организации ремонтных и монтажных работ; рассмотрены вопросы износа основных деталей машин и повышения их износоустойчивости. Рассмотрены вопросы разборки, очистки и промывки деталей, методы и способы их восстановления, а также основные аспекты ремонта, сборки, настройки и регулировки основных узлов оборудования. Представлены основные сведения о проведении такелажных работ в процессе демонтажа и монтажа оборудования.
Предназначено для подготовки бакалавров техники и технологии по профилю подготовки 151000.62 «Технологическое оборудование химических и нефтехимических производств» при изучении дисциплины «Ремонт и монтаж оборудования».
Ил. 54. Табл. 14. Библиогр. 6.
УДК 678.05.002/72/004/67
ББК 32.97
Рецензенты: В.Е. Шленский, технический директор ОАО “Ярославский завод опытных машин”
С.Н. Быстров, главный механик ПАО “Ярославский шинный завод”
ISBN
© Ярославский государственный технический университет, 2015
ОГЛАВЛЕНИЕ
ВВЕДЕНИЕ 5
1. ОРГАНИЗАЦИЯ РЕМОНТНЫХ РАБОТ 6
|
1.1. Система планово-предупредительного ремонта (ППР) 6
1.2. Техническое (межремонтное) обслуживание.
Текущий, средний и капитальный ремонты. 7
1.3. Структура ремонтной службы предприятия 9
1.4. Нормативы на ремонт оборудования 10
1.5. Структура и продолжительность ремонтных циклов 11
1.6. Категории сложности ремонта 11
1.7. Планирование ремонтных работ 12
2. НАДЕЖНОСТЬ И РЕМОНТНОПРИГОДНОСТЬ
ОБОРУДОВАНИЯ 13
2.1. Основные проблемы обеспечения надежности 13
2.2. Экономическая оценка надежности 14
2.3. Основные определения надежности 15
2.4. Ремонтопригодность оборудования 16
2.5. Повышение ремонтопригодности 17
3. ТРЕНИЕ В МАШИНАХ 18
3.1. Основные виды трения 19
3.2. Смазка оборудования и смазочные материалы 21
3.3. Выбор смазочных материалов 23
3.4. Организация смазочного хозяйства на предприятии 23
4. ИЗНОС ОБОРУДОВАНИЯ. ВИДЫ ИЗНОСА 24
4.1. Механический износ 25
4.2. Усталостный износ 27
4.3. Молекулярно-механический износ 28
4.4. Коррозионный износ 28
5. ИЗНОС ДЕТАЛЕЙ ОСНОВНЫХ УЗЛОВ
ОБОРУДОВАНИЯ 29
5.1. Износ деталей механических передач 29
5.2. Факторы, влияющие на износ деталей 31
5.3. Методы обнаружения дефектов деталей и неисправностей
оборудования 31
5.4. Нормы допускаемого износа деталей 32
5.5. Способы повышения износоустойчивости 34
6. ОСНОВНЫЕ РЕМОНТНЫЕ ОПЕРАЦИИ 35
6.1. Разборка машин на узлы и детали. Правила разборки
оборудования 35
6.2. Разборка основных видов разъемных соединений 37
6.3. Очистка и промывка деталей 38
6.4. Дефектация деталей при ремонте 39
7. ВОССТАНОВЛЕНИЕ ИЗНОШЕННЫХ ДЕТАЛЕЙ 39
7.1. Методы восстановления деталей 39
7.2. Ремонт и восстановление деталей слесарной и
механической обработкой 41
7.3. Восстановление сваркой и наплавкой 42
7.4. Восстановление металлизацией 44
7.5. Восстановление электролитическими способами 45
7.6. Восстановление деталей пластической деформацией 47
8. РЕМОНТ ТИПОВЫХ ДЕТАЛЕЙ И УЗЛОВ 48
8.1. Ремонт валов 48
8.2. Ремонт подшипников скольжения 49
8.3. Замена подшипников качения 50
8.4. Ремонт муфт 51
|
8.5. Ремонт зубчатых колес 53
8.6. Ремонт червячных передач 54
8.7. Ремонт гидравлических систем (цилиндров, поршней и пр.) 55
8.8. Ремонт уплотнительных устройств 56
9. СБОРКА ОБОРУДОВАНИЯ 58
9.1. Общие правила и методы сборки 58
9.2. Сборка резьбовых соединений 60
9.3. Сборка прессовых соединений 62
9.4. Сборка узлов с подшипниками качения 64
9.5. Сборка зубчатых и червячных передач 65
10. МОНТАЖ ОБОРУДОВАНИЯ 65
10.1. Планирование и организация монтажных работ 65
10.2. Строительные материалы, основания и фундаменты 67
10.3. Геодезические знаки, закладываемые в фундамент 69
10.4. Способы соединения машины с фундаментом 70
11. УСТАНОВКА И ВЫВЕРКА МАШИНЫ НА
ФУНДАМЕНТЕ 71
12. ВИБРОИЗОЛЯЦИЯ ОБОРУДОВАНИЯ 73
13. ТАКЕЛАЖНЫЕ РАБОТЫ 75
13.1. Блоки, полиспасты, тали и тельферы 76
13.2. Домкраты и лебедки 78
13.3. Канаты, цепи и стропы 81
14. ТЕХНИКА БЕЗОПАСНОСТИ ПРИ РЕМОНТНЫХ
И МОНТАЖНЫХ РАБОТАХ 81
15. МЕТОДИЧЕСКИЕ УКАЗАНИЯ ПО ВЫПОЛНЕНИЮ ЛАБОРАТОРНЫХ РАБОТ 83
Лабораторная работа № 1 84 Лабораторная работа № 2 90
Лабораторная работа № 3 96
Лабораторная работа № 4 103
Лабораторная работа № 5 110
БИБЛИОГРАФИЧЕСКИЙ СПИСОК 118
ВВЕДЕНИЕ
На любом промышленном предприятии, будь то предприятие машиностроительное, химическое, пищевое или любое другое, все здания, сооружения, все виды основного технологического и вспомогательного оборудования, транспортных систем и систем управления, являются объектами ремонта.
Основными задачами ремонтных служб предприятия являются:
– содержание оборудования в технически исправном, работоспособном состоянии;
– проведение регулярного технического обслуживания всех механизмов, узлов и агрегатов производственных линий для решения вопросов наиболее полной эффективности использования технологического оборудования и обеспечения высокого качества выпускаемой продукции;
– сокращение простоев оборудования в периоды ремонтных циклов и повышение коэффициента использования оборудования;
– повышение производительности труда ремонтного персонала, снижение трудоемкости и повышение экономичности ремонтных работ.
– проведение непрерывного автоматизированного контроля оборудования на технологическую точность, т. е. определение связи параметров состояния оборудования с выходными характеристиками готовой продукции, или “техническое обслуживание по фактическому состоянию”.
|
В общем случае к основным видам работ ремонтных служб предприятия в периоды межремонтных циклов относятся:
1. Монтаж нового оборудования (такелажные работы).
2. Пуско-наладочные работы, приемочные испытания, сдача оборудования в эксплуатацию.
3. Техническое обслуживание и ремонт оборудования.
4. Демонтаж машины и выборочная разборка узлов на детали.
5. Восстановление или замена деталей.
6. Сборка и монтаж оборудования.
7. Проверка и регулировка, наладка, обкатка на холостом ходу и под нагрузкой.
В пособии кратко описаны общие вопросы ремонта химического оборудования и в качестве примеров рассмотрены некоторые особенности отдельных видов ремонтных работ.
Представлены методические указания по выполнению лабораторных работ, предусмотренных программой курса «Ремонт и монтаж оборудования», в соответствии с направлением подготовки бакалавров 151000 «Технологические оборудование химических и нефтехимических производств».
ОРГАНИЗАЦИЯ РЕМОНТНЫХ РАБОТ
1.1. Система планово-предупредительного ремонта (ППР)
Срок службы оборудования определяется его изготовителем. Однако его продолжительность во многом зависит от своевременного проведения технического обслуживания и ремонта оборудования для поддержания оборудования в работоспособном состоянии. Периодичность технического обслуживания (ТО) в период межу плановыми ремонтами производится в соответствии с требованиями инструкций производителя оборудования.
Система ППР – это комплекс организационных и технических мероприятий по обслуживанию и ремонту оборудования для обеспечения его безотказной работы.
Система ППР выполняет следующие задачи:
1) предупреждение преждевременного износа деталей и узлов оборудования для поддержания его в работоспособном состоянии;
2) предупреждение аварийных ситуаций;
3) проведение ремонтных работ по плану, согласованному с производственным планом, при минимальных затратах времени и средств;
4) своевременная подготовка запчастей, материалов и рабочей силы для выполнения работ при минимальном простое оборудования [1].
|
Планово-предупредительные ремонты осуществляются периодически через определенное планом (графиком) время непрерывной работы оборудования. При составлении плана ремонта учитывается межремонтный цикл для данного типа оборудования.
Межремонтным циклом называется время между двумя капитальными ремонтами.
Длительность межремонтного цикла изменяется в зависимости от отработанного оборудованием времени с начала его ввода в эксплуатацию, числа проведенных ремонтов, состояния оборудования и условий его эксплуатации.
Межремонтным периодом называется время между двумя ремонтами любой категории сложности.
Правильно организованная структура ППР имеет важное технико-экономическое значение, так как она определяет основные затраты на проведение ремонтных работ и потери от простоев оборудования, жестко связанных с основным производственным планом любого предприятия.
В данном курсе не рассматривается понятие аварийных ремонтов, потому что как раз система ППР и должна предусматривать их предотвращение.
Рис. 1.1. Структура ремонтной службы предприятия
По такой схеме организации ремонтного обслуживания на крупных предприятиях все проектные, строительные и энергомеханические службы подчинены главному инженеру (техническому директору). При этом, службы главного механика осуществляют эксплуатацию и ремонт всего технологического и механического оборудования, а также строительных сооружений, коммуникаций и металлоконструкций.
В последние годы на отечественных предприятиях наблюдается сокращение состава энергомеханических и метрологических служб, их вывод из состава предприятий и передача функций ремонта и монтажа оборудования на так называемый аутсорсинг, т. е. привлечение для проведения этих работ сторонних организаций, что не всегда технически оправдано и экономически целесообразно.
Таблица 1.1 – Примерные нормативы времени на различные виды ремонта
Р, (часов) | П, (часов) | З, (чел.- часов) | ||||||
КР | СР | ТР | КР | СР | ТР | КР | СР | ТР |
Допускаемые отклонения от установленных норм времени работы оборудования между ремонтами:
между КР + 10%,
между СР + 20 %,
между ТР – не допускается.
Для текущего ремонта отклонения от норм времени работы оборудования между ремонтами недопустимы.
Категории сложности ремонта
Чем сложнее аппарат или машина, тем выше категория сложности их ремонта:
(1)
где: tк – трудоемкость капитального ремонта (чел.- час);
r – трудоемкость капитального ремонта (усл. ед.) = 35 чел.- час.
Таблица 1.2 – Нормы трудности ремонтов (в усл. ед.)
РАБОТЫ | Трудоемкость ремонтов (чел.- час) | ||
ТР | СР | КР | |
Слесарные | |||
Станочные | 0,9 | 3,6 | 8,5 |
Прочие | 0,5 | 1,8 | 3,5 |
Всего: | 4,4 | 17,4 |
|
Зная категорию сложности оборудования, можно определить трудоемкость ремонтов:
tкр = R· r; tср = 0,5 tкр; tтр = 0,126 tкр
Планирование ремонтных работ
Составление годового графика ППР для планирования ремонтных работ представлено в [1]. Примеры проведения расчетов количества необходимых ремонтов, их продолжительности и времени межремонтных циклов и периодов прдставлено в [2].
Пример составления графика ППР оборудования сборочного цеха шинного завода представлен в табл. 1.3.
Таблица 1.3 – График ППР
Наименование оборудования | Месяцы | |||||||||||
HF-сборочный станок | Т | Т | Т | Т | - | Т | Т | Т | Т | Т | Т | Т |
HF-сборочный станок | Т | Т | С | Т | Т | - | Т | Т | Т | Т | Т | Т |
HF-сборочный станок | Т | Т | Т | С | Т | Т | - | Т | Т | Т | Т | Т |
HF-сборочный станок | Т | Т | Т | Т | К | Т | Т | - | Т | Т | Т | - |
HF-сборочный станок | Т | Т | Т | Т | Т | С | Т | Т | - | Т | Т | Т |
HF-сборочный станок | Т | Т | Т | Т | Т | Т | С | Т | Т | - | Т | Т |
HF-сборочный станок | Т | Т | Т | Т | Т | Т | Т | К | Т | Т | - | Т |
HF-сборочный станок | Т | Т | Т | Т | Т | Т | Т | Т | Т | Т | Т | - |
HF-сборочный станок | Т | Т | - | Т | Т | Т | Т | Т | Т | Т | Т | Т |
“Имбергер” | - | Т | Т | Т | Т | Т | Т | Т | Т | С | Т | Т |
VMI-изготовление крыльев | Т | - | Т | Т | Т | Т | Т | Т | Т | Т | К | Т |
VIPO – изготовление бортовых колец | Т | Т | - | Т | Т | Т | Т | Т | Т | Т | Т | С |
Триплекс «Konstrukta» | С | Т | Т | Т | - | Т | Т | Т | Т | Т | Т | Т |
Дуплекс «Konstrukta» | Т | К | Т | Т | Т | - | Т | Т | Т | Т | Т | Т |
Гермослой «Konstrukta» | Т | Т | Т | Т | Т | Т | - | Т | С | Т | Т | Т |
Рис. 2.1. Экономическая оценка надежности
При расчетах экономической эффективности от повышения надежности действующего оборудования принимается, что дополнительные капитальные вложения окупятся в течение нормативного срока окупаемости, принятого в химической промышленности (5 лет).
2.3. Основные определения надежности
Работоспособность – состояние объекта, при котором он способен выполнять заданные функции, сохраняя значения заданных параметров в пределах, установленных нормативно-технической документацией.
Неработоспособность – состояние объекта, при котором значение хотя бы одного из заданных параметров, характеризующего способность
выполнять определенные функции, не соответствует требованиям, установленным нормативно-технической документацией.
Безотказность – свойство объекта непрерывно сохранять работоспособность в течение некоторого промежутка времени или некоторой наработки.
Отказ – событие, заключающееся в нарушении работоспособности объекта.
Предельное состояние – состояние объекта, при котором его дальнейшая эксплуатация должна быть прекращена из-за неустранимого нарушения требований безопасности, выхода заданных параметров за установленные пределы, снижения эффективности эксплуатации ниже допустимой или, наконец, необходимости проведения текущего либо капитального ремонта.
Наработка – продолжительность или объем работы объекта.
Технический ресурс – наработка объекта от начала эксплуатации или ее возобновления после капитального ремонта до наступления предельного состояния.
Гамма-процентный ресурс – наработка, в течение которой оборудование не достигнет предельного состояния с заданной вероятностью γ процентов.
Долговечность – свойство объекта сохранять работоспособность до наступления предельного состояния при установленной системе технического обслуживания и ремонтов.
Ремонтопригодность – свойство объекта, заключающееся в приспособленности к предупреждению и обнаружению причин возникновения его отказов, повреждений и устранению их последствий путем проведения ремонтов и технического обслуживания.
Ремонтируемый объект – объект, исправность и работоспособность которого в случае возникновения отказа или повреждения подлежит восстановлению.
Неремонтируемый объект – объект, исправность и работоспособность которого в случае возникновения отказа или повреждения не подлежит восстановлению.
Надежность – качественное и количественное свойство изделия, однако в дальнейшем будут иметься в виду лишь количественные ее показатели, такие как коэффициент технического использования или вероятность безотказной работы.
ТРЕНИЕ В МАШИНАХ
В каждой машине движущиеся и соприкасающиеся детали изнашиваются из-за трения, возникающего при воздействии нормального и сдвигающего усилий на детали.
В процессе производства и переработки полимерных материалов, в том числе и резиновых смесей, имеет место фрикционное взаимодействие перерабатываемого материала с поверхностью рабочих органов машин. Знание закономерностей этого взаимодействия позволяет представить картину физических явлений в зоне взаимодействия, обеспечивать теоретические предпосылки процессов, предвидеть и обосновать причины износа рабочих органов машин.
Основной закономерностью фрикционного взаимодействия между двумя телами при их относительном смещении является так называемый первый закон трения (закон Амонтона):
(4)
где F – сила трения, кГс;
N – нормальная нагрузка, кГс;
µ – коэффициент трения.
Рис. 3.1. К закону трения
Этот же закон в другой записи:
(5)
где – удельная сила трения, кГс / см²;
– нормальное давление, кГс / см²;
где S – площадь поверхности контакта тел, см².
Такая линейная связь справедлива для металлов в определенном значении давлений и скоростей скольжения.
При взаимодействии полимеров с металлической поверхностью связь между τ и Р носит, как правило, нелинейный характер и описывается формулой Тириона:
, (6)
где А и В – некоторые эмпирические константы.
Практические вопросы изучения процесса трения рассмотрены в лабораторной работе № 1.
Основные виды трения
Трение различают по двум признакам: по характеру движения трущихся поверхностей и по характеру смазки этих поверхностей.
По характеру движения трущихся поверхностей различают два вида трения: скольжения и качения.
Трение скольжения по поверхности – движение ползуна в направляющих.
Трение скольжения по линии – вращение вала по поверхности подшипника.
Трение качения – движение сферы (шарика) или цилиндра (ролика) по поверхности обоймы подшипника.
Часто эти виды трения совмещаются, например, в зубчатых зацеплениях.
Трение является основной причиной износа оборудования. Наибольший износ происходит при сухом трении, т.е. в отсутствие смазки. Поэтому для уменьшения сил трения и предотвращения преждевременного износа применяется смазка.
Во время работы трущиеся поверхности, разделенные слоем смазки, не соприкасаются между собой, а мельчайшие неровности, размер которых превышает толщину смазочного слоя, срезаются и уносятся смазкой, предотвращая абразивный износ деталей. Кроме того, смазка предохраняет поверхность деталей от коррозии и эффективно отводит тепло из зоны соприкосновения трущихся деталей.
В зависимости от характера и режима смазки различают следующие виды трения: жидкостное, полужидкостное, граничное, полусухое и сухое [1].
Жидкостное трение – поверхности сопрягаемых деталей полностью разделены слоем смазки и нагрузка воспринимается смазочной пленкой.
Рис. 3.2 Жидкостное трение [1]
Условия жидкостного трения: высокая скорость вала, чистота обработки, оптимальный зазор, оптимальная вязкость смазки.
При вращении вала масло из зазора увлекается под цапфу вала и в месте сужения образуется “масляный клин”.
Коэффициент жидкостного трения в литературе указывается в пределах от 0,001…0,008 мм.
Полужидкостное трение происходит в том случае, когда большая часть сопряжения поверхностей разделена слоем смазки, но отдельные элементы (микронеровности) поверхностей соприкасаются. Коэффициент трения при этом находится в пределах 0,01…0,08 мм.
Граничное трение происходит, если скользящие поверхности разделены слоем смазки толщиной в несколько молекул.
При недостатке или отсутствии смазки возникает полусухое или сухое трение.
Рис. 3.3. Изменение коэффициента трения при различных видах трения
Выбор смазочных материалов
Основным критерием при выборе смазочных материалов является вязкость, величины которой зависят от условий работы пары трения.
При выборе масел можно руководствоваться следующими рекомендациями [1]:
1. Быстроходные механизмы смазываются маслами пониженной вязкости.
2. Чем больше удельной давление между деталями узла трения, тем больше должна быть вязкость масла.
3. Чем больше величина зазора в паре вал – подшипник, тем более вязкое масло следует применить.
4. Чем выше температура узла сопряжения деталей, тем выше должна быть начальная вязкость масла, т. к. при повышении температуры вязкость масел уменьшается.
Масла для смазки подшипников скольжения выбирают в зависимости от удельной нагрузки на подшипник и окружной скорости шейки вала:
- индустриальные (ИС-20, ИС-45) – для нагрузок до 65 кгс/см² и скоростей до 30 м/с;
- велосит – для скоростей свыше 30 м/с.
- компрессорное (АК-10) – для нагрузок до 150 кг/см².
Консистентные смазки для подшипников качения:
- солидол (УС-2, УС-3) – для скоростей до 1500 оборотов/мин и температур до 60º С.
- консталин жировой – для температур до 110º С.
- ЦИАТИМ-201 – для температур от – 50 до + 100º С и любых скоростей.
Механический износ
Механический износ вызывается силами трения при скольжении одной детали по другой. Трущиеся поверхности деталей имеют неровности, размер которых составляет 0,05 – 0.1 мкм [1]. Такие микронеровности вызывают соприкосновение деталей не по всей площади, а по так называемой площади фактического контакта, которая значительно меньше номинальной. Следовательно, и нагрузка от одной поверхности к другой передается только в местах контакта. Это приводит к значительному повышению удельного давления на контактирующие поверхности. Происходит пластическая деформация неровностей (выступов), их срезание и отламывание.
Износ существенно возрастает, если между поверхностями деталей оказываются твердые частицы, которые попадают на контактирующие поверхности из окружающей среды или являются продуктами собственного износа. Такой износ называется абразивным.
Механический износ происходит при работе оборудования в местах сопряжения деталей таких, как поршень–цилиндр, вал–подшипник, в зубчатых передачах и множестве других.
В результате износа происходит изменение размеров деталей, их формы, появление задиров, царапин, трещин, увеличение вибраций или заклинивание.
Износ зависит от следующих факторов [2]:
– свойства материалов трущихся деталей (коэффициент трения, температура, изменение размеров);
– чистота обработки трущихся поверхностей;
– наличие и качество смазки в местах сопряжения.
Чистота обработки поверхностей определяет фактическую площадь контакта трущихся деталей. В начале работы деталей микронеровности, образованные на поверхности деталей в результате предшествующей механической обработки, разрушаются, и возникает новый микрорельеф поверхности.
Чистота обработки определяет в основном износ деталей в период обкатки (начальный период работы оборудования).
Изменение шероховатости поверхности во времени при различной начальной чистоте обработки деталей имеет явно выраженный экспоненциальный характер, показанный на рисунке 4.1 [2].
Рис. 4.1. Изменение шероховатости поверхности во времени
при различной начальной чистоте обработки деталей [2]
Величина шероховатости стремится к установившемуся значению. Время τ1характеризует период приработки. При τ > τ1начинается период установившегося износа (притирка). В этот период шероховатость поверхности остается ~ постоянной. Коэффициент трения и износ минимальны. Такая картина характерна для нормальных условий работы трущихся деталей.
При повышенных нагрузках или отсутствии смазки может произойти “схватывание” поверхностей, появляются задиры и шероховатость резко увеличивается. Возрастает износ деталей.
При изготовлении сопрягаемых деталей необходимо обеспечить оптимальную чистоту обработки их поверхностей.
Качество обработки поверхности деталей, изготовленных из твердых материалов, особенно сильно влияет на интенсивность износа деталей из мягких материалов. Износ баббитовых вкладышей и бронзовых втулок тем больше, чем ниже качество обработки стального вала.
На рисунке 4.2 [2] представлена характерная кривая износа трущихся деталей во времени.
Рис. 4.2. Кривая износа трущихся деталей во времени
I – период приработки (обкатки машины, оборудования). Характеризуется повышенным износом. Не рекомендуется давать полную нагрузку (по аналогии с ограничением скоростного режима автомобиля), необходима частая замена смазки для отвода продуктов износа.
II – период устойчивой работы. Характеризуется постоянной скоростью износа. Необходима грамотная эксплуатацией оборудования в соответствии с инструкциями по эксплуатации и техническому обслуживанию.
III – период аварийного износа.
Механический износ возрастает при нарушении правил эксплуатации и технического обслуживания оборудования, в результате некачественного ремонта узлов сопряжения деталей, а также при нарушении режимов смазки.
Усталостный износ
Усталостный износвозникает под действием ударных и переменных по величине и направлению нагрузок [1]. Он имеет место при напряжениях, значительно меньших допустимым по пределу прочности материалов, из которых изготовлены детали.
Под действием переменных нагрузок на поверхности деталей возникают микротрещины. В местах царапин, раковин, надрезов, резких переходов от одного сечения детали к другому происходит концентрация напряжений в результате чего микротрещины увеличиваются и могут привести к разрушению деталей.
Характерный усталостный износ наблюдается в зубьях шестерен, на поверхности вкладышей подшипников скольжения на беговых дорожках подшипников качения. Это явление может возникать при перегрузке машин, нарушении смазочного режима, а также в результате некачественного изготовления и ремонта деталей машин/
Коррозионный износ
Коррозионный износпроисходит в результате химического или электрохимического воздействия на материал деталей агрессивных веществ, перерабатываемых на оборудовании или находящихся в окружающей среде [1]. Под влиянием коррозии поверхность деталей разрушается «разъедается», меняется ее микрорельеф, и опять-таки начинает действовать механизм механического износа.
Одним из главных узлов машины является привод, обеспечивающий действие ее рабочих органов [1]. Приводы могут быть электромеханические (электродвигатель с редуктором), гидравлические (насосы и гидроцилиндры), пневматические (компрессоры и пневмоцилиндры) и др.
Приводные механизмы имеют характерные типовые детали и узлы, обеспечивающие передачу движения и преобразование его из одного вида в другой.
К характерным деталям и узлам механических приводов относятся валы, подшипники, муфты, шкивы, зубчатые и червячные колес и др.
Гидравлические приводы состоят из цилиндров, поршней, плунжеров, штоков, уплотнительных устройств.
Трущиеся поверхности деталей приводов подвергаются износу.
Работоспособность и долговечность перерабатывающего оборудования в значительной степени зависят от прочности, износоустойчивости и качества ремонта узлов и деталей приводных механизмов.
Из простейших деталей перерабатывающего оборудования, к наиболее изнашиваемым, можно отнести детали резьбовых и шпоночных соединений, соединительных муфт и уплотнительных узлов.
В оборудовании по переработке пластмасс и резиновых смесей значительному износу подвергаются поверхности, находящиеся в контакте с перерабатываемым материалом.
При этом характерно сочетание механического, теплового и химического воздействия перерабатываемого материала на рабочие органы технологического оборудования.
ОСНОВНЫЕ РЕМОНТНЫЕ ОПЕРАЦИИ
Технологический процесс ремонта оборудования включает следующие работы:
– Разборка машины или аппарата на узлы и детали,
– Очистка и промывка сборочных единиц и деталей.
– Определение характера и степени износа деталей, контроль, дефектация и сортировка деталей.
– Восстановление изношенных деталей.
– Подбор и изготовление новых деталей для замены непригодных к дальнейшей эксплуатации.
– Сборка узлов и механизмов с пригонкой деталей и регулировкой узлов (механизмов).
– Общая сборка машины или аппарата.
– Проверка и регулировка машины, обкатка на холостом ходу, пробные включения на выпуск продукции.
– Приемочные испытания и сдача в эксплуатацию.
Очистка и промывка деталей
Очистку и мойку деталей поводят механическим или физико-химическим способами.
К механическим относится чистка специальными скребками и щетками, вращающимися от эл/дрели насадками.
К физико-химическим – мойка деталей в ваннах и струйная мойка. Способы мойки состав моющих средств зависят от вида загрязнений, материала и габаритов деталей.
Промывка деталей производится щелочными растворами и синтетическими моющими средствами, например, представленными в табл. 6.1.
Таблица 6.1 – Растворы и моющие средства для промывки деталей
Состав | Сталь, чугун | Медные, алюминиевые сплавы |
Едкий натр NaOH | 0,75 – 2,0 | – |
Углекислый натр Na2CO3 | 5,0 | 0,5 – 1,0 |
Тринатрий фосфат Na3PO4 | 1,0 – 5,0 | – |
Хромпик K2Cr2O7 | – | 0,1 |
Мыло хозяйственное | 0,25 | 0,5 |
Жидкое стекло | 3,0 | 0,2 |
Вода | Остальное |
Подшипники качения, а также все масляные загрязнения, чаще всего промывают в керосине или солярке с последующей обдувкой сжатым воздухом.
Удаление накипи проводят горячим раствором каустической соды (едкий натр) 8 – 10 в. ч. при Т = 60 – 70 ºС.
Ржавчину и окалину целесообразно удалять гидропескоструйным способом.
Рис. 7.3. Правка изгиба валов
Для этого применяются винтовые скобы, домкраты и другие приспособления.
Правка выпуклостей и вмятин в корпусах аппаратов обычно осуществляется с нагревом выпрямляемого участка поверхности. Выпуклости правятся ударами медной кувалды по окружностям от периферии к центру. Нагрев стенок из легированных сталей не целесообразен, т. к., при этом может произойти изменение структуры металла.
Обжатие и раздача применяются для изменения размеров тонкостенных деталей их пластичных материалов (латунь, низкоуглеродистая сталь) с нагревом до 800-900 ºС (рис. 7.4 и 7.5).
Рис. 7.4. Обжатие мундштука Рис. 7.5. Раздача бронзовой
Сварочной горелки втулки
Увеличение наружного диаметра втулки производится за счет увеличения ее внутреннего диаметра, который можно наплавить или восстановить гильзовкой. Возможен вариант одновременного восстановления и внутреннего, и наружного диаметров, за счет некоторого уменьшения длины втулки.
Накатка производится на токарном станке. К поверхности детали прижимается ролик из твердосплавного металла с насечкой (вместо резца). Применяется для посадок неответственных неподвижных соединений.
Ремонт валов
В процессе эксплуатации валы передают крутящий момент и воспринимают изгибающие усилия. Основные дефекты валов: прогиб, износ шеек, шпоночных канавок и шлицев, трещины и выбоины на поверхности.
Величина прогиба вала определяется при его вращении в центрах с помощью индикатора часового типа и считается допустимой в пределах от 0,02 до 0,05 мм.
Валы с превышением пределов допустимого прогиба выправляют холодным (винтовым прессом) или горячим (горелкой) способом. Холодный способ применяют для валов диаметром до 60 мм (рис. 8.1).
Рис. 8.1. Холодный способ Рис. 8. 2. Горячий способ
Горячим способом валы большого диаметра и пустотелые валы выправляют при нагреве до температуры ковки (рис. 8.2). Выпуклость вверху обкладывают мокрым листовым асбестом, оставляя открытым участок длиной 40-70 мм. Открытое место открытое место нагревают горелкой до 500-550 ºС (до темно-вишневого цвета) и быстро охлаждают сжатым воздухом. Операцию повторяют несколько раз.
Шейки вала при износе приобретают овальность, конусность или бочкообразность. При износе до 0,1 мм шейки ремонтируют шлифованием. При больших износах шейку вала можно восстановить также вибродуговой наплавкой, металлизацией, отсталиванием.
Незначительные повреждения шпоночных канавок (до 5 % первоначальной ширины) устраняют опиливанием и шабрением, значительные – строганием с увеличением ширины канавки до 15 % номинальной ширины. Естественно – изготавливается новая шпонка.
При больших износах шпоночную канавку можно заварить с последующей зачисткой. Шпоночный паз фрезеруют на новом месте с отступом от старого на 120 º по окружности вала.
Трещины на поверхности вала небольшой глубины заваривают, предварительно разделав их до неповрежденного металла.
Замена подшипников качения
Замену подшипников качения производят при обнаружен<
|
|
Семя – орган полового размножения и расселения растений: наружи у семян имеется плотный покров – кожура...
Поперечные профили набережных и береговой полосы: На городских территориях берегоукрепление проектируют с учетом технических и экономических требований, но особое значение придают эстетическим...
Археология об основании Рима: Новые раскопки проясняют и такой острый дискуссионный вопрос, как дата самого возникновения Рима...
История развития хранилищ для нефти: Первые склады нефти появились в XVII веке. Они представляли собой землянные ямы-амбара глубиной 4…5 м...
© cyberpedia.su 2017-2024 - Не является автором материалов. Исключительное право сохранено за автором текста.
Если вы не хотите, чтобы данный материал был у нас на сайте, перейдите по ссылке: Нарушение авторских прав. Мы поможем в написании вашей работы!