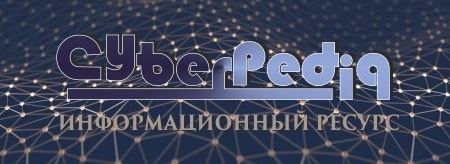
Историки об Елизавете Петровне: Елизавета попала между двумя встречными культурными течениями, воспитывалась среди новых европейских веяний и преданий...
Типы сооружений для обработки осадков: Септиками называются сооружения, в которых одновременно происходят осветление сточной жидкости...
Топ:
Выпускная квалификационная работа: Основная часть ВКР, как правило, состоит из двух-трех глав, каждая из которых, в свою очередь...
Особенности труда и отдыха в условиях низких температур: К работам при низких температурах на открытом воздухе и в не отапливаемых помещениях допускаются лица не моложе 18 лет, прошедшие...
Оценка эффективности инструментов коммуникационной политики: Внешние коммуникации - обмен информацией между организацией и её внешней средой...
Интересное:
Инженерная защита территорий, зданий и сооружений от опасных геологических процессов: Изучение оползневых явлений, оценка устойчивости склонов и проектирование противооползневых сооружений — актуальнейшие задачи, стоящие перед отечественными...
Принципы управления денежными потоками: одним из методов контроля за состоянием денежной наличности является...
Лечение прогрессирующих форм рака: Одним из наиболее важных достижений экспериментальной химиотерапии опухолей, начатой в 60-х и реализованной в 70-х годах, является...
Дисциплины:
![]() |
![]() |
5.00
из
|
Заказать работу |
|
|
Станочные приспособления классифицируются по ряду признаков (табл.1.3). В табл.1.4 приведена система станочных приспособлений как составная часть системы технологической оснастки.
Таблицa 1.3
Классификация станочных приспособлений
Признаки | Характеристики | |
1.По степени специализации | Универсальные безналадочные, | |
(системы станочных приспособлений) | универсально-сборные, | |
универсальноналадочные, специализированные наладочные, сборноразборные, неразборные, специальные | ||
2.По виду оснащаемых работ | Токарные, сверлильные, фрезерные, | |
шлифовальные и др. | ||
3.По числу устанавливаемых заготовок | Одноместные, многоместные | |
4.По числу используемых при | Одноинструментные, | |
обработке инструментов | многоинструментные | |
5.По порядку применения | Для последовательной обработки; | |
инструментов и расположенных | для параллельной обработки; | |
заготовок | для последовательно-параллельной обработки | |
6.По числу позиций, занимаемых | Однопозиционные, | |
заготовкой по отношению к | многопозиционные | |
инструменту | ||
7.По степени непрерывности обработки заготовок | Для дискретной обработки; | |
для непрерывной обработки | ||
8.По участию человека в обслуживании приспособлений | Ручные, механизированные, | |
автоматические |
Таблица 1.2
Система станочных приспособлений
Система приспособлений | Краткая характеристика систем | Время оперативного оснащения операции приспособлением,ч |
1. УБП-универ-сальные безнала-дочные | Законченный механизм с несъемными элементами для базирования, обеспечивающий установку заготовок с эле-ментарными схемами базирования | - |
2. УСП - универ- | Собираются из стандартных деталей и узлов многократного применения | 3-4 |
сально-сбор- | ||
ные | ||
3. УНП –универсально- | Состоят из универсального базового агрегата и сменных наладочных элементов для установки различных по конфигурации и схемам базирования заготовок | |
наладочные | ||
4. СНП-специа- лизированные наладочные | Состоят из специализированного базового агрегата и сменных нала- док для установки родственных по конфигурации заготовок с идентичными схемами базирования | |
5. СРП-сборно- | Собираются из стандартных деталей и сборочных единиц как специальные приспособления для долгосрочного крепления | 20-25 |
разборные | ||
6.НСП-не разборные | Необратимые конструкции, не предназначенные для разборки с целью повторного использования их деталей в других конструкциях | |
специальные | ||
|
Тема 2.2 Конструкция и особенности эксплуатации различных типов станочных приспособлений
Приспособления для станков токарной группы
Приспособления к токарным станкам служат для установки и закрепления заготовок, у которых обрабатывают наружные и внутренние поверхности вращения.
Обработка на станках этой группы производится при различной установке обрабатываемых деталей: в центрах, в патроне, на суппорте и на станине станка. Поэтому и приспособления для этих станков можно разделить на группы.
К первой группе относятся приспособления для обработки в центрах. Основными элементами приспособлений этой группы являются центры (передний и задний), на которые устанавливаются обрабатываемые детали, поводковые устройства, которыми деталь приводится во вращение в процессе обработки, люнеты, предохраняющие легко деформирующиеся детали от деформации и вибрации под действием сил резания, центровые и разжимные оправки, пальцы и др.
Ко второй группе относятся универсальные и специальные патроны и планшайбы, обеспечивающие надежную установку и закрепление обрабатываемых деталей на шпинделе передней (иногда и задней) бабки станка.
|
К третьей группе относятся специальные конструкции приспособлений, с помощью которых выполняются операции, требующие, например, одновременного продольного и поперечного движения инструмента (приспособления для обработки конических, сферических и других сложных поверхностей).
Кроме этих приспособлений для станков, необходимо изготовлять различные устройства, составляющие группу вспомогательного инструмента, включающую специальные инструментальные наладки, резцедержавки, головки и т. п. Иногда необходимо изготовлять приспособления к станку для выполнения такой работы, для которой данный станок не предназначен.
Станочные центры
Характерными элементами таких приспособлений являются отдельно выполненные детали (центра), предназначенные для установки на станке обрабатываемых деталей типа валов при обточке, шлифовании и других подобных операциях. Передняя (рабочая) часть центра выполняется в виде конуса с углом при вершине 60°, задняя — в виде конуса Морзе, соответствующего конусному отверстию в шпинделе станка. На переднюю часть центра устанавливается обрабатываемая деталь своим центровым отверстием («гнездом»). Задним конусным хвостовиком центр помещается в отверстие шпинделя станка непосредственно или с промежуточной втулкой.
Так как шпиндель передней бабки токарного и центрового шлифовального станков вращается, а шпиндель задней бабки этих станков не вращается, то в процессе обработки детали со шпинделем вместе вращается и передний центр, в то время как задний центр остается неподвижным. Следовательно, условия работы переднего и заднего центров различны. Передний воспринимает нагрузки, вызывающие в его поперечных сечениях нормальные напряжения изгиба и сжатия и касательные напряжения среза (от силы веса обрабатываемой детали, от сил резания и от центробежных сил инерции). Напряжения изгиба и среза изменяются по симметричному знакопеременному циклу, а напряжения сжатия — по постоянному циклу. В сечениях заднего центра, вследствие его неподвижности, кроме указанных напряжений, возникают касательные напряжения кручения от момента трения между центром и обрабатываемой деталью, но изменяются все эти напряжения не по симметричному, а по пульсирующему знакопостоянному циклу. Кроме этого, задний центр (его рабочий конус) подвергается значительному изнашиванию под действием вращающейся на нем детали. При этом изнашивается и центровое отверстие детали, что вызывает определенные погрешности обрабатываемых поверхностей детали. При больших скоростях вращения разогревается задний центр и конец детали, помещенный на нем, а это может привести к усиленному износу центра и к еще большим погрешностям обработки.
|
Для уменьшения этих погрешностей задние центры изготовляют из прочных высокоуглеродистых сталей и подвергают закалке до высокой твердости. Иногда применяют среднеуглеродистую сталь с наплавлением твердого сплава или хромированием рабочего конуса. Кроме того, для уменьшения погрешностей применяют вращающиеся центры, выполненные в виде съемных стандартных конструкций, которые могут устанавливаться на любом станке, или в виде специальных постоянных конструкций, встроенных в пиноль задней бабки. Последние применяются главным образом на многорезцовых станках и на станках для обработки тяжелых деталей, постоянно выполняющих одну и ту же операцию.
Вращающиеся центры должны надежно воспринимать осевые и радиальные силы и иметь минимальный вылет (для универсальных центров), возможность регулировки подшипников и шлифования конуса после сборки, хорошую смазку, достаточную устойчивость против радиальных колебаний, возможность компенсации удлинения обрабатываемой детали от нагрева и, кроме того, должны быть удобны при сборке. Особое значение эти требования приобретают при проектировании центров для скоростного и силового точения.
В современных станках подвод заднего центра к обрабатываемой детали механизируют и автоматизируют. При этом привод к пиноли должен обеспечивать надежное ее зажатие после создания необходимой осевой силы на обрабатываемую деталь.
В конструкции, показанной на рис. 2.1, в результате давления сжатого воздуха на поршень 2 в полости 3 цилиндра 4 пиноль 1 останавливается. После этого сжатый воздух отводит цилиндр вправо, тяга 6, связанная с цилиндром, поворачивает колесо 7, которое выдвигает клиновой фиксатор 8, стопорящий пиноль. По окончании обработки детали сжатый воздух поступает в полость 5 цилиндра, который перемещается влево до тех пор, пока фиксатор не освободит пиноль, после этого приходит в движение поршень и оттягивает пиноль вправо. Одностороннее отжатие пиноли клином является недостатком этой конструкции.
|
Рис. 2.1. Типовая конструкция центра с пневмоподачей
При обработке на станках торцовых поверхностей канавок и других элементов, находящихся на точном расстоянии от торца вала, этот торец следует использовать в качестве установочной поверхности, т. е. при установке вала данный торец должен дойти до постоянного упора (рис. 2.2, а), относительно которого определяется положение инструмента. Чтобы при этом вследствие возможного различия глубины центрового отверстия, не случилось так, что вал не дойдет до упора (рис. 2.2, б) или дойдя до него, окажется неправильно установленным (рис. 2.2, в), применяют так называемые плавающие центра.
Рис. 2.2. Плавающие центры (а, б, в), конструкция плавающего центра (г) и поводковые центры ( д, е)
На рис. 2.2, г показана одна из конструкций плавающего центра, обеспечивающего не только правильную установку вала на центр и фиксацию в осевом направлении, но и выполняющего одновременно функции поводкового устройства, вращающего вал в процессе обработки.
Пружина 4 выдвигает центр 7 вправо до упора 1. Обрабатываемая деталь при установке на центр перемещает его влево. Когда деталь дойдет до поводковой шайбы 6, последняя сожмет резиновые пробки 8 и переместит плунжеры 5, действующие на кольцо 2, за которым помещены шарики 3. Если установочный торец обрабатываемой детали недостаточно строго перпендикулярен оси детали, поводковая шайба 6 поворачивается почти без трения на центре и без сдвига в поперечном направлении. Плунжеры 5 при этом с помощью шариков 3 самоустанавливаются, удерживая поводковую шайбу в нужном положении, не нарушая установку обрабатываемой детали на центре 7.
При обработке полых деталей типа втулок или труб нередко применяют постоянные рифленые центры (рис. 2.2, ди е), устанавливаемые в передней бабке станка, и рифленые центровые пальцы вращающихся центров — в задней бабке. Гайка 11 (рис. 2.2, д)и гайка 10с двумя штифтами 9(рис. 2.2, ё) служат для выталкивания центров из отверстия шпинделя и одновременно предохраняет переднюю часть шпинделя от повреждений.
Центровые оправки
Для обработки полых тонкостенных деталей типа втулок и деталей с короткими центральными отверстиями типа зубчатых и червячных колес применяются оправки, на которые обрабатываемые детали с гладким отверстием надеваются с прессовой или переходной посадкой. Иногда детали дополнительно укрепляют на оправке с помощью гайки с быстросъемной шайбой. Для деталей со шлицевыми или шпоночными отверстиями оправки также выполняются со шлицами или шпонками. Оправку вместе с помещенными на ней деталями устанавливают на центрах станка подобно обычному валу. Оправки делятся на жесткие и разжимные.
|
Жесткие оправки выполняют гладкими цилиндрическими, иногда слегка коническими, цилиндрическими со шпонками и со шлицами. Для обеспечения определенного положения обрабатываемой детали при обточке и подрезке одного торца на оправке выполняют с одной стороны опорный буртик, а с другой — проточку для выхода резца на расстоянии от буртика, меньшем длины детали на 5 мм. При необходимости подрезать оба торца детали оправку выполняют с двумя проточками на расстоянии, меньшем длины детали на 10мм.
На оправках для правильного и быстрого надевания детали создается специальная приемная часть, равная приблизительно половине длины отверстия обрабатываемой детали.
В целях лучшего центрирования деталей на гладких оправках рабочую часть таких оправок иногда выполняют длиной больше диаметра отверстия детали и, как указывалось, слегка конусной.
Рис. 2.3 Гладкая жёсткая конусная центровая оправка
Изготовляются оправки из малоуглеродистых обычных и легированных сталей с последующей цементацией рабочих поверхностей и закалкой до твердости HRC 58 - 62. Рекомендуется применять хромистую сталь марки 20Х.
Разжимные центровые оправки выполняют в виде цанговых, плунжерных, мембранных конструкций и конструкций с гидропластмассой. Необходимость в таких оправках обусловлена наличием в механизмах и машинах большого количества тонкостенных деталей типа втулок, которые во многих случаях нельзя без деформации запрессовать на жесткую оправку. Разжимные оправки удобны для обработки деталей с установочным отверстием значительного диаметра.
Наиболее точная обработка достигается при использовании оправок с гидропластмассой, вследствие того, что с помощью таких оправок разжимная сила распределяется равномерно по всей поверхности установочного отверстия, в то время как при использовании других оправок эта сила действует не на всю поверхность отверстия, а только на поверхность соприкосновения с деталью лепестков цанги, секторов мембран или плунжеров. Вследствие этого только оправки с гидропластмассой практически не могут вызвать радиальную деформацию детали, которая возможна при других разжимных оправках, особенно при плунжерных.
Высокая точность центрирования деталей с помощью оправок с гидропластмассой обусловлена и тем, что в таких оправках нет звеньев, точность которых влияла бы на точность центрирования, как это имеет место в других конструкциях, точность которых по мере износа трущихся частей и возможного засорения сильно понижается.
На рис. 2.4 показана оправка с гидропластмассой для обработки тонкостенной стальной гильзы 3 цилиндра двигателя.
Корпус 5 оправки представляет полую деталь с углублениями для гидропластмассы. Углубления перекрыты тонкостенными оболочками 4 и 5, являющимися установочными для обрабатываемой детали 5. Разжимаются гильзы с помощью этих оболочек путем давления плунжеров 2 и 7 на гидропластмассу при подвинчивании гаек 1 и 8. Для этого оправка помещается вертикально в специальную подставку, в которой при завинчивании, например, гайки 8 гайка 1 удерживается от проворачивания. Когда движение гайки 8 прекращается, она начинает проворачиваться вместе с корпусом 5, который при этом ввинчивается в гайку 1 и заставляет ее перемещать ряд плунжеров 2. Недостатком такой конструкции является то, что на плунжеры действуют вращающиеся детали (гайки 1 и 5), что может вызвать перекос плунжеров. Для предотвращения этого перекоса между плунжерами и гайками следует поместить на шпонках шайбы, которые при завинчивании гаек перемещаются только поступательно.
Рис. 2.4. Центровая оправка с гидропластмассой
Настройка оправки на предельный размер диаметра, обусловленный допустимой деформацией тонкостенных оболочек 4 и 6, производится при помощи предусмотренных в конструкции ограничительных винтов 10 и съемных толстостенных втулок-калибров 9.
Конструкции с гидропластмассой сложны при изготовлении вследствие необходимости создания надежной герметичности полостей для гидропластмассы. В настоящее время имеются конструкции упругих центрирующих устройств без полужидкой массы, а, следовательно, и без необходимости герметичных полостей для нее.
Поводковые устройства
Поводковыми называются устройства, служащие для связи обрабатываемой детали, установленной на центрах, со шпинделем станка. К простейшим из этих устройств относятся хомутики и скобы.
Хомутики (Рис 2.5) являются наиболее простыми поводковыми устройствами. Обрабатываемая деталь закрепляется в проёме хомутика 1 стопорным винтом 2.
К недостаткам хомутиков следует отнести неравномерный отжим обрабатываемой детали в разные стороны.
Рис. 2.5 Хомутики
Работа с хомутиками непроизводительна и утомительна, поэтому их постоянно совершенствуют.
На рис. 2.6 показано устройство более совершенного хомутика. На обрабатываемую деталь при использовании этого хомутика действуют только составляющие силы резания Рz и Ру, так как момент силы R, действующей со стороны поводкового пальца, заменен моментом пары сил R', приложенных к двум, симметрично расположенным относительно оси обрабатываемого вала 11 поводковым пальцам 3 и 10, поэтому не вызывающим дополнительных нагрузок на центры станка. Сила, отжимающая вал при этом направлена постоянно в одну сторону.
Рис. 2.6. Усовершенствованный хомутик
Активная и одновременная работа двух поводковых пальцев 3 и 10 достигается с помощью рычажков 2 и 9 плунжеров 5 и 8 и шариков 7, так как сила R' на пальце 3 через рычажок 2, плунжер 5, шарики 7, плунжер 8 и рычажок 9 вызывает ответную силу R' на пальце 10 (и наоборот).
Обрабатываемый вал самозажимается с помощью криволинейного кулачка 4, угловое положение которого относительно его оси регулируется в зависимости от диаметра вала поворотом эксцентриковой оси 1, которая в нужном положении фиксируется гайкой 6.
Такие устройства позволяют быстро без применения ключа сменять оправку с обработанной деталью второй оправкой с установленной заранее заготовкой очередной детали, в результате этого они получили широкое применение на заводах.
Люнеты
Люнеты применяют главным образом при обработке длинных деталей во избежание прогиба их под действием сил резания и собственного веса и одновременно для частичной разгрузки центров станка. Люнеты устанавливают на каретке станка и перемещают вместе с ней вдоль станины, непрерывно поддерживая обрабатываемую деталь на постоянном расстоянии от инструмента (подвижный люнет показан на рис.2.7) или неподвижно закрепляют непосредственно на станине станка - неподвижный люнет (рис. 2.8).
![]() | ![]() |
Рис. 2.7 Подвижный сдвоенный люнет | Рис. 2.8 Неподвижный роликовый люнет |
Люнеты подразделяют на универсальные и специальные. Универсальными называются люнеты с раздвижными опорными кулачками, допускающими использование люнета при обработке деталей разных диаметров. Специальные люнеты применяют при обработке одной определенной детали или для поддержки приспособления, установленного на шпинделе станка и имеющего значительный вылет.
Рис. 2.9. Типы кулачков к люнету
При проектировании люнетов любого назначения следует обеспечить соприкосновение их с обрабатываемой деталью не по сплошной и цилиндрической поверхности, а с помощью отдельных кулачков 3 и 6 (рис. 2.9). Этим облегчается настройка люнета при первоначальной его установке на станке, а также при износе его трущихся деталей. Кулачки должны соприкасаться с обрабатываемой деталью 1 или 4 сменными сухарями 2 (рис. 2.9, а) или, что предпочтительнее, роликами 5 (рис. 2.9, б).
При скоростной обработке валов на токарных станках возникает вибрация, ухудшающая условия работы инструмента и отрицательно влияющая на качество обрабатываемой поверхности. Чтобы избежать вибрацию, иногда применяют движущиеся вместе с резцом люнеты-виброгасители, конструктивно схожие с подвижным люнетом рис. 2.7, но имеющими встроенные элементы для гашения вибраций.
При точении длинных валов (l / d = 50÷100) такие люнеты целесообразно применять совместно с неподвижным люнетом. Виброгасители повышают производительность, улучшают чистоту и точность обработки.
|
|
Типы оградительных сооружений в морском порту: По расположению оградительных сооружений в плане различают волноломы, обе оконечности...
Состав сооружений: решетки и песколовки: Решетки – это первое устройство в схеме очистных сооружений. Они представляют...
Биохимия спиртового брожения: Основу технологии получения пива составляет спиртовое брожение, - при котором сахар превращается...
Автоматическое растормаживание колес: Тормозные устройства колес предназначены для уменьшения длины пробега и улучшения маневрирования ВС при...
© cyberpedia.su 2017-2024 - Не является автором материалов. Исключительное право сохранено за автором текста.
Если вы не хотите, чтобы данный материал был у нас на сайте, перейдите по ссылке: Нарушение авторских прав. Мы поможем в написании вашей работы!