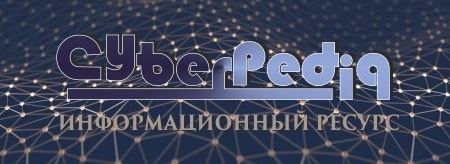
Поперечные профили набережных и береговой полосы: На городских территориях берегоукрепление проектируют с учетом технических и экономических требований, но особое значение придают эстетическим...
Папиллярные узоры пальцев рук - маркер спортивных способностей: дерматоглифические признаки формируются на 3-5 месяце беременности, не изменяются в течение жизни...
Топ:
Марксистская теория происхождения государства: По мнению Маркса и Энгельса, в основе развития общества, происходящих в нем изменений лежит...
Основы обеспечения единства измерений: Обеспечение единства измерений - деятельность метрологических служб, направленная на достижение...
Когда производится ограждение поезда, остановившегося на перегоне: Во всех случаях немедленно должно быть ограждено место препятствия для движения поездов на смежном пути двухпутного...
Интересное:
Мероприятия для защиты от морозного пучения грунтов: Инженерная защита от морозного (криогенного) пучения грунтов необходима для легких малоэтажных зданий и других сооружений...
Что нужно делать при лейкемии: Прежде всего, необходимо выяснить, не страдаете ли вы каким-либо душевным недугом...
Уполаживание и террасирование склонов: Если глубина оврага более 5 м необходимо устройство берм. Варианты использования оврагов для градостроительных целей...
Дисциплины:
![]() |
![]() |
5.00
из
|
Заказать работу |
|
|
Сборка сухих отсеков.
Сборка сухих отсеков происходит в вертикальном положении в стапеле. Стапель – специальное приспособление внутри которого располагаются детали и узлы (сборки) стапеля для базирования, фиксации и сборки деталей отсека. Внутри стапеля части отсека устанавливаются на свои места (базируются), фиксируются, затем соединяются между собой (заклепок, винтов, шайб, гаек). Стапель состоит из нижней и верхней плит, на которые устанавливаются стыковочные шпангоуты. Сами плиты крепятся к колоннам. Между плитами располагаются детали и узлы (сборки) стапеля для базирования, фиксации и сборки деталей отсека.
Сборку ГО в стапеле производят в горизонтальном положении, собирая по отдельности каждую створку ГО.
Сборку сухих отсеков производит бригада рабочих, располагающихся на специальных рабочих площадках снаружи и внутри стапеля. Детали сухого отсека в основном соединяют с помощью заклепок, т.к. они значительно более легкие чем винты, шайбы, гайки. Винты применяют в тех местах сухого отсека, где значительные нагрузки. Клепку производят вручную специальным пневмоинструментом.
Сборку сухих отсеков в стапеле производят двумя методами:
1) с базой от каркаса – когда сначала в стапеле устанавливаются детали каркаса (стрингеры, шпангоуты, соединительные детали), они соединяются между собой, а затем устанавливают обшивку и соединяют ее с каркасом.
2) с базой от обшивки – когда сначала в стапеле устанавливают обшивку, а затем детали силового набора (каркаса), которые соединяются между собой и с обшивкой.
При любом методе сборки в стрингерах, шпангоутах, соединительных деталях уже имеются ведущие отверстия под крепеж. Эти отверстия при сборке рассверливаются до большего диаметра совместно с обшивкой и в них затем устанавливают заклепки и винты.
|
Стыковочные отверстия в стыковочных шпангоутах отсека сверлят в стапеле по отверстиям в нижней и верхней плитам стапеля, где эти отверстия уже имеются. Плазово-шаблонный метод обеспечивает взаимозаменяемость и точность как при изготовлении деталей отсека, так и при изготовлении и сборки стапеля. Это, в том числе, обеспечивает точное совпадение стыковочных отверстий в смежных отсеках при сборке ступени РН или при сборке целиком РН или КА.
Возможны два варианта сборки сухих отсеков в стапеле:
а) панелированная сборка – когда часть обшивки клепается со стрингерами (панель) вне стапеля, а затем устанавливается в стапель и собирается с остальными деталями сухого отсека,
б) непанелированная сборка – когда сборка сухого отсека от начала до конца идет только в стапеле.
Панелированная сборка считается более прогрессивной, т.к. вне стапеля можно клепать не вручную, а на прессе, что быстрее и качественнее. Кроме того, вне стапеля больше свободного места и одновременно клепать можно несколько панелей, а в стапеле в это время выполняются другие сборочные роботы. Таким образом, время сборки отсека сокращается.
После завершения сборки в стапеле отсек вынимается из него. Стыковочные шпангоуты фрезеруются по стыковочной плоскости, с них снимается небольшой припуск, в результате плоскости стыковочных шпангоутов параллельны с высокой точностью.
Снаружи сухого отсека по местам стыков деталей, по головкам крепежных деталей (заклепки, винты) наносят герметик, что обеспечивает пылевлагозащиту отсека. Герметик наносят полосами, перед нанесением на отсек эмали.
18.Изготовление и сборка ферменных отсеков РН и КА. Монтажные работы при сборке сухих и ферменных отсеков РН и КА.
Ферменные отсеки (фермы), так же как и сухие отсеки, негерметичны и соединяют другие отсеки между собой или крепят двигательную установку к корпусу ступени РН или к КА, но не имеют обшивки.
|
Ферма, чаще всего, состоит из двух стыковочных шпангоутов, между которыми располагаются прямолинейные стойки (тяги), соединяющие эти шпангоуты. Стыковочные шпангоуты служат для стыковки фермы со смежными отсеками РН или КА. На стыковочных шпангоутах находятся стыковочные отверстия под болты и штыри.
Для крепления стоек между собой и со шпангоутами служат соединительные детали – кронштейны, фитинги и другие. Две соседние стойки фермы и часть шпангоута между ними должны образовывать треугольник (треугольная форма является наиболее жесткой и устойчивой).
Ферма может быть без стыковочных шпангоутов, т.е. состоять из стоек и фитингов, соединяющих стойки. Основания фитингов образуют стыковочные площадки для соединения со смежными отсеками, на которых расположены стыковочные отверстия для болтов.
Детали силового набора фермы бывают трех типов:
1) стыковочные шпангоуты,
2) прямолинейные стойки (играют роли стрингеров и шпангоутов),
3) соединительные детали – кронштейны и фитинги.
По массе конструкции ферма легче аналогичного по размерам и назначению сухого отсека из того же материала. Ферма применяется тогда, когда не требуется наличие обшивки или обшивка специально не устанавливается.
Ферменный отсек используется при горячем разделении ступеней РН. В свободное пространство между стойками фермы выходит наружу дым и пламя в первые секунды горячего разделения ступеней. Если не обеспечить такой свободный выход для дыма и пламени, то можно повредить хвостовой отсек «новой» ступени РН или вызвать взрыв остатков ракетного топлива в отделяемой ступени РН.
Так же ферма используется при креплении ракетного двигателя к ступени (ферма и двигатель находятся внутри сухого отсека).
Еще одно применение ферменного отсека – промежуточный отсек между КА и последней ступенью РН, или между КА и РБ. Такой промежуточный отсек часто называют адаптер. С его помощью КА устанавливается на РН, а затем после выведения КА на околоземную орбиту КА отделяется от него (полное отделение от РН). Обшивка для такого отсека не нужна, т.к. отсек и КА находятся под ГО и не соприкасаются с атмосферой. Такой же промежуточный ферменный отсек используется и в том случае, если одна РН сразу выводит в космос несколько КА, расположенных на ферме параллельно.
|
Ферменная конструкция также применяется в качестве основы (корпуса) для посадочных блоков межпланетных КА. Часть такой фермы используется в качестве посадочных опор, а к оставшейся части фермы крепятся двигательная установка, топливные баки, приборы, оборудование и коммуникации различных систем межпланетного КА. Такой ферменный корпус применялся на посадочной части американского корабля «Аполлон» при пилотируемых полетах на Луну.
Особенностями ферменных отсеков являются:
1) высокая прочность и жесткость,
2) способность воспринимать ударные нагрузки (например, посадка на планету),
3) относительная простота конструкции,
4) высокая надежность,
5) относительно невысокая стоимость,
6) возможность точного изготовления несложными методами.
Основные требования к ферменным отсекам:
1) необходимые прочность и жесткость,
2) точность посадочных поверхностей – на стыковочных шпангоутах,
3) устойчивость стержневых элементов – не деформируются и не ломаются,
4) надежность соединения всех элементов (шпангоуты, стойки, соединительные детали) с помощью сварки или крепежных деталей,
5) точная центровка (положение центра масс) относительно продольной оси РН или КА,
6) требования, связанные с конкретным назначением фермы.
Материалом для изготовления деталей ферменного отсека служат, в первую очередь, различные алюминиевые сплавы. Реже в качестве материалов применяют титановые сплавы, высокопрочные стали, композиционные неметаллические материалы.
Схема изготовления ферм:
а) изготовление стоек из стандартных профилей или труб,
б) изготовление стыковочных шпангоутов из стандартных профилей,
в) изготовление соединительных деталей (фитингов и кронштейнов) из заготовок на металлорежущих станках,
г) сборка ферменного отсека в стапеле,
д) покрытие, контроль, маркировка, клеймение.
Схема изготовления стоек из стандартных профилей и труб:
1) резка профилей или труб по нужной длине,
2) слесарная зачистка заусенцев и притупление острых кромок,
3) обработка местных усложнений формы стойки для обеспечения сборки с соединительными деталями,
|
4) покрытие, контроль, маркировка, клеймение.
Схема изготовления стыковочных шпангоутов из стандартных профилей:
1) резка профилей по нужной длине, стыковочный шпангоут фермы делается из нескольких частей,
2) слесарная зачистка заусенцев и притупление острых кромок,
3) обработка местных усложнений формы шпангоута для обеспечения сборки с соединительными деталями,
4) гибка шпангоута в соответствии с формой ферменного отсека,
5) нанесение покрытия, контроль, маркировка, клеймение.
Заготовками для фитингов и кронштейнов являются поковки или отливки. Форма фитингов и кронштейнов довольно сложная, поэтому обработка производится на фрезерных станках, позволяющих обрабатывать эти плоскости. Часто применяют фрезерные станки с ЧПУ. Станки с ЧПУ обеспечивают более высокое качество обработки. После завершения обработки на станке проводится контроль, маркировка, клеймение, нанесение покрытия.
Более мелкие соединительные детали возможно изготавливать из листовых заготовок штамповкой.
Крепежные детали (винты, шайбы, гайки) изготавливаются в соответствии со стандартами для этих деталей или закупаются уже готовые на других предприятиях, входящих в кооперацию по изготовлению РН или КА.
После изготовления деталей приступают к сборке фермы. Сборку производят в вертикальном положении в стапеле, аналогично сухим отсекам.
После разделки стыковочных отверстий по шпангоутам фермы, ее вынимают из стапеля и фрезеруют стыковочные поверхности шпангоутов, снимая заранее предусмотренный небольшой припуск. Этим достигается параллельность стыковочных плоскостей шпангоутов фермы.
Для собранной фермы проводят контроль, маркировку, клеймение, нанесение покрытия и отправляют ее в цех окончательной сборки.
Соединение деталей фермы между собой возможно не только с помощью крепежных деталей, а и с помощью сварки. Возможно соединение деталей комбинированным способом. В случае применения сварки необходимо учитывать, что сварка нагревает соединяемые детали, в них возникают внутренние напряжения, которые могут вызвать деформацию сваренных деталей и всего ферменного отсека в целом. В таких случаях говорят, что детали и отсек «коробит» или «повело». Эти деформации будут тем больше, чем тоньше сваренные детали.
Чтобы снизить до приемлемых эти вредные последствия сварки, сварку деталей фермы ведут в определенном порядке, обеспечивающем минимальные напряжения и деформации в сваренной ферме. После сварки предусматривают отжиг (ТО) для снятия внутренних напряжений. В случае сборки фермы с помощью сварки проводят контроль качества сварных швов.
|
«+»: сварных соединений в облегчении конструкции.
«-»: сварной фермы – внутренние напряжения и деформации после сварки.
Классификация испытаний.
Все многообразие испытаний объединяется в систему испытаний, в которой есть определенные требования (правила), рассмотренные выше, а также существуют классификация и конкретные виды испытаний.
Испытания классифицируют по следующим признакам:
а) По месту проведения испытания могут быть наземными и летными (натурными). Промежуточное положение занимают так называемые огневые испытания. Они типичны для испытаний двигательных установок или отдельных ступеней РН. Наземные испытания могут быть заводскими, полигонными (в монтажно-испытательном корпусе космодрома) и предстартовыми, которые проводятся на изделии, установленном на стартовом столе.
б) В зависимости от уровня сборки испытуемого объекта испытания могут быть узловыми (сборочных единиц - узлов), агрегатными (отсеков, агрегатов, блоков) и общими (собранных РН или КА):
· Автономные испытания имеют целью проверку отдельных приборов или групп приборов, входящих в сборочную единицу, агрегат или изделие, на специальных стендах с заменой (имитацией) остальной части сборочной единицы эталонными приборами.
· Комплексные испытания собранных агрегатов и изделий имеют целью проверку входящих в них приборов на взаимодействие.
в) Исследовательские испытания проводятся с целью определения возможности реализации конструкторских идей в новом изделии.
г) Контрольно-технологические испытания имеют главной целью проверку на отсутствие производственных дефектов у серийных, устанавливаемых на летные образцы, узлов, агрегатов, а также полностью собранных летных образцов изделий.
д) Имитационными принято считать такие испытания, в которых создаются специальные уникальные условия космического пространства (вакуум, тепловое воздействие, излучения, невесомость и т.д.) в отдельности или в совокупности.
Виды испытаний.
При проведении испытаний отсеков РН и КА, их отдельных агрегатов, приборов и систем, а также при испытании целиком РН и КА, проводят следующие конкретные виды испытаний:
1) Испытания на функционирование отдельных систем, узлов, устройств и т.д. составляют основу большинства программ и методик. В чистом виде они представляют собой проверку работоспособности различных систем и устройств при отсутствии специально созданных внешних воздействий, т.е. при нормальных условиях цеха (при нулевом воздействии).
2) Испытания на статическую прочность состоят в определении фактических деформаций и напряжений в элементах и узлах аппарата при воздействии постоянных сил.
3) Испытания на герметичность - создание избыточных давлений или глубокого вакуума внутри или снаружи испытываемых емкостей (герметичные баки или жилые отсеки).
4) Динамические испытания - проверка функционирования конструкции, систем, механизмов и устройств изделия при воздействии на него разного рода динамических воздействий и снятие динамических характеристик изделия. В зависимости от характера и вида динамического воздействия различают отдельные виды динамических испытаний:
а) Вибрационные испытания - определяется способность элементов конструкции противостоять вибрационным нагрузкам, не разрушаясь и не получая механических повреждений, особенно опасно появление резонанса при колебаниях. Источником вибрации может служить ракетный двигатель и устройства двигательной установки.
б) Акустические испытания - разновидность вибрационных испытаний на звуковых частотах. Источниками акустических нагрузок в изделии являются шумы от истекающей огненной струи в ракетных двигателях, работы различных внутренних устройств, вибраций элементов КА на звуковой частоте и т.д. Акустические нагрузки воздействуют на элементы конструкции пока изделие еще двигается в атмосфере Земли, т.е. акустическая (звуковая) вибрация передается на конструкцию через воздух.
в) Ударные испытания имитируют ударные нагрузки, возникающие при разделении ступеней и отсеков, при раскрытии и сбросе створок головного обтекателя (ГО) РН, при раскрытии парашютной системы, при посадке аппарата, а также при транспортировке. При ударной нагрузке к конструкции изделии кратковременно прикладывается значительная сила, а затем в конструкции возникают колебания.
5) Температурные испытания бывают на теплоустойчивость или холодоустойчивость. Возможны испытания на циклический (повторный) нагрев (охлаждение) и на температурный удар (резкое изменение температуры).
6) Вакуумные испытания проводятся с целью определения функционирования различных систем, узлов и деталей в условиях вакуума, проверки герметичности, отсутствия холодного схватывания в подвижных соединениях изделия, скорости испарения материала.
7) Имитационные испытания на воздействие различного вида излучений (солнечное излучение, отраженное и собственное излучение Земли, космическая радиация) - испытывается радиационная стойкость материалов и воздействия излучений на различные элементы, приборы и оборудование.
8) Летные испытания проводятся с целью проверки аэродинамической формы изделия, эффективности теплозащитного покрытия, отражательной способности поверхности изделия, срабатывание парашютной и двигательной систем мягкой посадки.
Изготовление деталей баков.
Общая схема изготовления баков состоит из этапа изготовления отдельных деталей обеих групп и этапа сборки.
В подвесных баках обечайки имеют меньшую толщину, чем в несущих баках.
Длинные обечайки собираются обычно из отдельных цилиндрических секций (монолитных панелей), число которых может быть значительно, при их сборке одновременно устанавливаются и поперечные силовые элементы, кронштейны, перегородки и т.д., сборка производится в стапелях. Соединение с помощью сварки, которая обеспечивает герметичность. После контроля швов и приварки всех арматурных и установочных деталей обечайка поступает на сборку бака.
Стыковочные шпангоуты баков предназначены для стыковки обечаек с днищами баков и со смежными отсеками. К ним могут предъявляться более высокие требования по точности, герметичности, коррозионной стойкости.
Шпангоуты изготавливаются из стандартных профилей нужного поперечного сечения по обычной схеме изготовления.
По форме обводов днища, применяемые на РН и КА, могут быть сферическими, эллиптическими, параболическими, куполообразными и полуторовыми (половина тора) с бортами различной формы и без бортов.
По диаметру различают малогабаритные (до 300 мм), среднегабаритные (300-1000 мм) и крупногабаритные (более 1000 мм) днища. По составу исходных заготовок различают:
1) простые цельноформованные (штампованные),
2) сложные штампосварные конструкции днищ, сваренные из отдельных сегментов.
На технологию изготовления оказывают существенное влияние относительная толщина стенок (отношение толщины стенки к диаметру днища) и требуемая точность.
Для днищ в большинстве случаев используются листовые заготовки различной толщины (от 0,5 мм до 30 мм и выше). Основой изготовления днищ являются, как правило, методы холодного формообразования. Общие требования к днищам такие же, как и к бакам.
Обобщенная схема изготовления днищ:
1) Листы освобождают от упаковки, протирают смазку и осматривают поверхность: не допускаются царапины, вмятины, трещины и другие поверхностные дефекты; при необходимости производят контроль толщины.
2) Разметка очищенного листа производится с помощью разметочного инструмента, проверяется с помощью шаблона заготовки. Здесь же отрезаются образцы для механических испытаний и химического анализа; производится клеймение листов и образцов.
3) Раскрой заготовок днищ производится на гильотинных или роликовых ножницах, на фрезерных или карусельных станках, иногда газовой или плазменной резкой. Для сложных штампосварных днищ вырезаются треугольные или сегментные заготовки элементов днищ. Для крупных малонагруженных днищ могут применяться сварные (с последующей зачисткой и отжигом швов) листовые заготовки.
4) Если раскрой заготовки производится на ножницах или резкой, то контур ее обрабатывается механически. Кроме того, на этом этапе иногда производится механическая обработка (фрезерование на копировально-фрезерных станках) поверхности заготовок для получения вафельных или другой формы карманов с целью облегчения днища; иногда применяется для этого химическое фрезерование.
5) Заготовки после слесарной доработки тщательно протираются, обезжириваются и подвергаются отжигу (термообработка для снятия внутренних напряжений).
6) После отжига поверхности тщательно очищают, производят травление, промывку, сушку. Если операция формообразования производится со смазкой, то наносится соответствующая смазка.
7) В настоящее время известно много методов формообразования днищ: холодная листовая штамповка, обтяжка, ротационное выдавливание и обкатка, штамповка взрывом, вибрационная штамповка и другие.
Наибольшее распространение среди методов формообразования днищ находят методы листовой штамповки, наиболее освоенные производством: формовка, которая преимущественно выполняется за один переход и рекомендуется для днищ большой относительной толщины и малой относительной глубины; вытяжка различными способами. При изготовлении днищ из малопластичных материалов (магниевые и титановые сплавы) или из высокопрочных сталей с большой относительной толщиной применяют метод вытяжки с подогревом. Температура нагрева заготовки зависит от свойств материала. В некоторых случаях подогревается сам штамп. Применение штамповки с подогревом позволяет увеличить коэффициент и уменьшить число переходов при изготовлении днищ с большой относительной глубиной.
8) При многопереходном формообразовании днища подвергаются промежуточному отжигу. После операции формообразования днища или элементы сложных днищ проходят окончательную термообработку (отжиг, закалка, отпуск).
9) Формообразованные элементы сложных днищ после термообработки подвергаются механической обработке по кромкам под сварку на специальных кромкофрезерных станках.
10) После механической обработки производится слесарная доработка кромок, зачистка их, обезжиривание и подготовка под сварку.
11) Порядок сборки и сварки элементов днищ определяется их количеством и возможностью установки в одном приспособлении, которое должно обеспечить точное базирование элементов и возможность автоматической сварки по стыкам. После сварки производится отжиг сварных швов и контроль их методами неразрушающего контроля.
12) Сваренное днище поступает на операцию окончательной калибровки и правки. Элементы днищ до сварки проходят индивидуальную калибровку.
13) Для пробивки отверстий в днищах, число которых может быть значительно, применяют пробивные штампы.
14) При изготовлении крупных днищ их часто делают методом химического фрезерования. Эта операция может выполняться до формообразования или сразу после формообразования до сварки и вырубки отверстий.
15) Днища поступают на операцию нанесения покрытий (анодирование, кадмирование и т.д.), иногда наружная поверхность днищ шлифуется или полируется для получения высоких отражательных характеристик, например, чтобы отражать тепловые потоки, тогда покрытие не наносится (чистый металл).
После этого днища поступают на общую сборку бака в стапеле с помощью сварки.
22.Изготовление обечаек из монолитных панелей. Сборка герметичных отсеков. Система испытаний герметичных отсеков.
Монолитная панель – это одна единая деталь. Обечайка (боковая поверхность) герметичного отсека собирается сваркой из таких монолитных панелей. Монолитные панели включают в себя обшивку с продольным и поперечным набором (ребра жесткости). Эти ребра жесткости играют роль стрингеров и промежуточных шпангоутов, как у сухих отсеков, но только они входят в состав монолитной панели для обеспечения герметичности панели.
В монолитных панелях ребра жесткости могут быть или только в продольном или в продольном и поперечном направлениях ("вафельного" типа), или расходящимися лучами из одной точки. Применение монолитных панелей вызвано, с одной стороны, постоянным увеличением нагрузок на конструкцию и стремлением в то же время сохранить их массовые характеристики, с другой стороны, развитием технологических методов изготовления монолитных панелей с достаточно тонкими ребрами и обшивкой, позволяющими реализовать этот массовый выигрыш.
Конструктивными преимуществами являются:
1) Меньшая масса при равной прочности
2) Уменьшение трудоемкости проектирования, конструкции за счет уменьшения количества элементов;
3) Увеличение прочности, жесткости, устойчивости за счет уменьшения числа стыков и швов, некоторое увеличение внутреннего объема агрегата,
4) Высокая герметичность конструкции,
5) Высокое качество наружных поверхностей обшивок.
Технологическими преимуществами монолитных панелей являются: уменьшение объема сборочных работ и во многих случаях суммарной механической обработки, уменьшение работ по герметизации, высвобождение производственных площадей и сборочного оборудования, упрощение сборочной оснастки, уменьшение стоимости изготовления панелей.
Недостатками монолитных панелей являются значительная стоимость заготовительной оснастки, низкий коэффициент использования металла, удлинение цикла подготовки и переналадки производства из-за длительности проектирования и изготовления оснастки. В опытном и единичном производстве применение монолитных панелей иногда может привести к удорожанию опытных изделий, технологические преимущества их полностью выявляются при серийном производстве.
Существует много способов изготовления монолитных панелей: механическое фрезерование из плит, прессование, прокатка, горячая штамповка, литье, химическое фрезерование, размерная электрохимическая обработка и другие. Применяют следующие методы изготовления монолитных панелей:
1) Механическое фрезерование монолитных панелей является одним из распространенных методов их изготовления, особенно в опытном и серийном производстве. Прямолинейные плоские панели фрезеруют из плит на копировально-фрезерных станках, позволяющих получать ребра жесткости любого расположения, и станках с программным управлением.
Панели криволинейной формы одинарной кривизны изготовляют из плит по двум схемам:
а) фрезерование плоской плиты, затем гибка ее по форме отсека,
б) гибка плоской плиты, а затем фрезерование криволинейной плиты.
Преимуществами механического фрезерования монолитных плит являются относительная простота оборудования, простота и дешевизна оснастки, возможность получения панелей различных конфигураций с любым расположением ребер жесткости и с любой толщиной, высокая точность и хорошее качество поверхности. Но такие недостатки, как низкий коэффициент использования металла (много стружки), большая трудоемкость и худшие механические характеристики металла панели, обусловили рекомендацию этого метода только для опытного и единичного производства. В серийном производстве этот метод допустим только в период подготовки более производительного метода.
2) Прессование монолитных панелей является одним из самых производительных способов их изготовления. При этом обеспечивается высокий коэффициент использования металла, более высокие механические свойства заготовок и высокое качество поверхности. Недостатком этого метода можно считать ограничения по форме и размерам панелей: можно получать панели только с продольными ребрами жесткости шириной до 850 мм и с толщиной обшивки не менее 2-3 мм. Для получения панелей с переменным по длине сечением применяется дополнительное фрезерование.
3) Прокатка монолитных панелей: преимуществами этого метода являются возможность получения панелей с толщиной обшивки менее одного миллиметра и панелей вафельного типа. Заготовками для панелей с продольными ребрами служат прессованные панели, которые в результате прокатки удлиняются за счет утонения обшивки и ребер. При прокатке панелей вафельного типа листовая заготовка - плита, сложенная с матрицей, имеющей обратную конфигурацию, прокатывается через гладкие валки, где металл заготовки перетекает в углубление матрицы. Посредством многократной прокатки с постепенным сближением валков получают вафельную панель требуемой формы. Процесс идет при температуре горячей штамповки. Технология обработки таких панелей и подготовки их к сборке в оболочки аналогична технологии изготовления прессованных панелей.
4) Горячая штамповка монолитных панелей на мощных прессах является методом, позволяющим получать панели с любой конфигурацией и переменной толщиной по длине ребер и со стыковыми узлами, что обеспечивает значительный выигрыш в массе и лучшую конструктивную прочность.
«-»: необходимость прессов большой мощности, длительный срок изготовления штампов, невозможность получения стенок малой толщины (менее 5-8 мм), низкая точность и достаточно сложная технология. Горячештампованные панели подвергаются длительной и сложной механической обработке или химическому фрезерованию. Объем такой обработки может быть уменьшен применением операции горячей калибровки. Горячештампованные панели рекомендуется применять в сильнонагруженных конструкциях при серийном, крупносерийном и массовом производстве.
5) Литье монолитных панелей
«+»: возможность получения панелей с различным расположением ребер, с более тонкой обшивкой, большая производительность, уменьшение объема механической обработки, уменьшение периода технологической подготовки производства, отсутствие больших усилий в процессе формообразования, возможность более быстрой переналадки оборудования.
«-»: худшие механические характеристики, они находят применение в малонагруженных агрегатах, когда их преимущества оказываются эффективными.
Метод литья панелей должен удовлетворять следующим условиям: до застывания металла в любом сечении через него должен пройти весь металл, питающий последующие сечения, и излишек металла из последующих сечений; при застывании не должно образовываться усадочных раковин, т.е. застывающие участки должны подпитываться жидким металлом; процесс литья должен обеспечивать удаление шлаков из отливки; желательно обеспечивать более плотную структуру металла в процессе литья. Методами, отвечающими этим условиям, является литье выжиманием, бесшовная заливка под низким давлением, центробежное литье.
6) Химическое фрезерование (размерное контурное травление) монолитных панелей
При химическом фрезеровании на металлический лист наносятся линии специальной мастики (краски). Там где наносят эту защитную краску будут ребра ячеек вафельной панели. Металлический лист опускают в ванну с раствором электролита. Под действием электрического тока в растворе электролита с непокрытых краской мест частицы металла уносятся и образуются углубления (ячейки) вафельной панели.
Преимуществом химического фрезерования по сравнению с механическим фрезерованием является при обеспечении высокой точности (до 0,05 мм) возможность получения панелей самых разнообразных форм и размеров с широкими и узкими пазами. При химическом фрезеровании исключаются деформации панелей. Метод позволяет создавать более равнопрочные конструкции. Химически фрезерованные панели практически не требуют дальнейшей ручной слесарной доработки и после отработки местных усложнений формы (отверстия, пазы и т.д.) передаются на сборку. При этом процессе прочностные показатели поверхностного слоя исходного материала не улучшаются из-за отсутствия поверхностного пластического деформирования (наклепа).
Сборка герметичных отсеков (аналогично сухим отсекам).
Испытания на герметичность.
Испытания на герметичность относятся к основным видам испытаний баков, обеспечивающих надежность и качество их в эксплуатации, проводятся для всех без исключения баков, после всех испытаний баков на прочность и динамических испытаний.
Герметичностью называют свойство бака не пропускать рабочий компонент (жидкость или газ) через соединения или через поры основного материала. Хотя герметичность связана с отсутствием утечек реального рабочего компонента, называемого рабочей средой, испытания обычно проводятся с помощью контрольных веществ (жидкостей или газов), называемых контрольными (пробными или индикаторными) средами. Контрольная среда обладает, как правило, большей проникающей способностью и меньшей стоимостью. Кроме экономических преимуществ это обеспечивает более высокую надежность испытаний, безопасность при испытаниях и меньшее влияние (например, коррозионное) на испытуемое изделие, что особенно важно для штатных (применяемых в летных изделиях) баков.
Герметичность характеризуется количественным параметром, называемым степенью герметичности, под которой понимается объемное или массовое количество вытекающего через места утечки компонента в единицу времени при определенных условиях. Допускаемая степень герметичности задается конструктором исходя из условий правильного функционирования и эксплуатации бака. Т.е. абсолютной (идеальной) герметичности не существует, всегда есть некоторые утечки компонента из конструкции, а с помощью степени герметичности устанавливаются приемлемые для конструкции бака утечки компонента.
При контроле герметичности важнейшей характеристикой метода и аппаратуры (схемы испытаний) является чувствительность. Чувствительность схемы испытаний должна быть выше, чем заданная (контролируемая) степень герметичности емкости. Чувствительность определяется с помощью контрольной течи - установки, с помощью которой создается поток контрольной среды заданной величины. Степень герметичности, определяемая в результате испытаний, должна быть меньше, чем заданная - в этом случае бак удовлетворяет требованиям конструкторской документации (чертежи, технические условия (ТУ) и другие) и считается годным.
Все методы испытаний герметичности можно разделить на две группы:
1) определение суммарной негерметичности, которая определяет степень герметичности бака в целом, не определяя места возможных утечек,
2) определение локальной негерметичности, связанное с определением конкретных мест утечек контрольной (или индикаторной) среды.
В ТУ могут задаваться степень как суммарной, так и локальной негерметичности по отдельным местам бака (сварные швы, места разъемных соединений и другие).
Значительно более высокой чувствительностью обладают методы определения негерметичности с помощью специальных течеискателей и индикаторных газов, которые основаны на определении наличия и концентрации определенного индикаторного газа в заданном объеме. Наиболее распространенными типами течеискателей являются масс-спектрометрические с использованием в качестве индикаторного газа гелия (гелиево-воздушная или азотно-гелиевая смеси). Преимуществами гелия как индикаторного газа являются малое содержание его в атмосфере (5.10-4%), высокая проникающая способность, химическая инертность, безвредность и взрывобезопасность, невоспламеняемость. Гелиевые течеискатели состоят из трех основных узлов:
1) ионного источника, в котором молекулы газа, сталкиваясь с электронами, ионизируются в ионы с положительным зарядом е;
2) анализаторной камеры, в которой ионы ускоряются под действием электрического поля и приобретают скорость, зависящую от их массы m, и разделяются под действием магнитного поля на компоненты в зависимости от отношения m/е и скорости;
3) коллектора с регистрирующим устройством, определяющим интенсивность выделенного ионного пучка данного газа.
Кроме этих основных узлов течеискатели имеют выносные пульты управления (ВПУ) с приборами-указателями и рабочий щуп для забора смеси газов в контролируемой точке, откачные системы с вакуумными насосами и устройствами для создания контрольной течи для калибровки течеискателей (эталоны).
Существует много различных конструкций течеискателей масспектрометрического типа с выс
|
|
Археология об основании Рима: Новые раскопки проясняют и такой острый дискуссионный вопрос, как дата самого возникновения Рима...
Адаптации растений и животных к жизни в горах: Большое значение для жизни организмов в горах имеют степень расчленения, крутизна и экспозиционные различия склонов...
Двойное оплодотворение у цветковых растений: Оплодотворение - это процесс слияния мужской и женской половых клеток с образованием зиготы...
Автоматическое растормаживание колес: Тормозные устройства колес предназначены для уменьшения длины пробега и улучшения маневрирования ВС при...
© cyberpedia.su 2017-2024 - Не является автором материалов. Исключительное право сохранено за автором текста.
Если вы не хотите, чтобы данный материал был у нас на сайте, перейдите по ссылке: Нарушение авторских прав. Мы поможем в написании вашей работы!