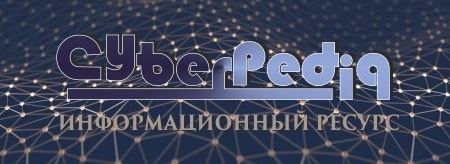
Адаптации растений и животных к жизни в горах: Большое значение для жизни организмов в горах имеют степень расчленения, крутизна и экспозиционные различия склонов...
Автоматическое растормаживание колес: Тормозные устройства колес предназначены для уменьшения длины пробега и улучшения маневрирования ВС при...
Топ:
Отражение на счетах бухгалтерского учета процесса приобретения: Процесс заготовления представляет систему экономических событий, включающих приобретение организацией у поставщиков сырья...
Оценка эффективности инструментов коммуникационной политики: Внешние коммуникации - обмен информацией между организацией и её внешней средой...
Характеристика АТП и сварочно-жестяницкого участка: Транспорт в настоящее время является одной из важнейших отраслей народного...
Интересное:
Уполаживание и террасирование склонов: Если глубина оврага более 5 м необходимо устройство берм. Варианты использования оврагов для градостроительных целей...
Наиболее распространенные виды рака: Раковая опухоль — это самостоятельное новообразование, которое может возникнуть и от повышенного давления...
Отражение на счетах бухгалтерского учета процесса приобретения: Процесс заготовления представляет систему экономических событий, включающих приобретение организацией у поставщиков сырья...
Дисциплины:
![]() |
![]() |
5.00
из
|
Заказать работу |
|
|
Наряду с металлическими находят применение и неметаллические корпуса РДТТ из композиционных материалов: стеклопластиков, углепластиков, боропластиков и другие. Изготовление таких корпусов производится методом намотки соответствующих волокон (из стекла, углерода, бора), выполняющих роль несущего (силового) наполнителя, пропитанных различными смолами на специальные легкоудаляемые после намотки оправки (болванки). Преимуществами таких корпусов являются выигрыш в массе, отсутствие коррозии, меньшая теплопроводность, что позволяет уменьшить толщину теплозащитного слоя.
Используют два метода нанесения смолы на волокна: мокрый, когда связующая смола наносится непосредственно на уложенную ровницу (волокна) в процессе намотки, и сухой, когда волокна пропитываются смолой до намотки и хранятся при определенных температуре и влажности воздуха.
Методом намотки можно изготовить цилиндрические обечайки, корпуса двигателей заодно с передним днищем, сферические корпуса и отдельно днища.
Могут применяться и другие методы изготовления корпусов РДТТ, например, метод изготовления монолитного корпуса РДТТ электролитическим осаждением высокопрочного металла на подготовленные основы. Схема изготовления корпусов этим методом состоит из следующих этапов: в специальной форме отливается топливный заряд; после застывания и отверждения заряда на него накладывается теплозащитная каучуко-асбестовая прокладка; к топливному заряду присоединяется внутренняя теплозащита переднего днища и теплозащита заднего днища, выполненная заодно с теплозащитой сопла; на топливный заряд наносится защитное покрытие для предохранения его от влаги в электролите; далее на полученную таким образом заготовку наносится специальное металлическое покрытие, создающее катодную полярность полученной сборки, выполняющей роль подложки для электролитического осаждения. Далее выполняется обычная операция электролитического осаждения, например, никеля или другого высокопрочного материала, со скоростью осаждения 0,08-0,1 мм/ч. В результате получается монолитный корпус РДТТ, выполненный заодно с сопловым блоком и передним днищем. Этот метод позволяет снизить массу на 12-15%, повысить надежность и прочность корпуса двигателя, снизить стоимость изготовления за счет сокращения количества технологической оснастки, снижения или даже исключения механической обработки.
|
Все изготовленные корпуса РДТТ проходят гидростатические испытания на специальных стендах под давлением, на 10-15% превышающим ожидаемое максимальное давление в камере сгорания, при этом в технологии испытаний нужно учитывать, что для некоторых теплозащиты и стеклопластиков контакт с водой не допускается. Тогда вместо воды для испытаний используют воздух.
Изготовление сопел РДТТ.
Сопло РДТТ часто называют сопловым блоком. Сопловые блоки РДТТ бывают составной конструкции и простые монолитные.
Простые монолитные сопловые блоки встречаются реже. Они обычно изготавливаются из жаропрочного и тугоплавкого материала (вольфрам, молибден) методами механической обработки, осаждения из газовой фазы, электролитического осаждения, плазменным напылением с последующей механической доработкой. Такие блоки предназначаются обычно для РДТТ небольшой тяги с малым сроком работы.
Сопловые блоки составной конструкции состоят из следующих элементов: несущий внешний корпус, иногда изготовляемый из отдельных обечаек; внутренняя теплозащита, которая может состоять из нескольких частей; стыковочные шпангоуты для стыковки с элементами днища; различные герметизирующие резиновые кольца.
|
Несущий внешний корпус (силовая часть сопла) может быть изготовлен из металлических, композиционных или сотовых материалов. Металлический корпус сопел обладает следующими преимуществами: высокая прочность, жесткость, надежность конструкции и относительная простота изготовления. Его недостатки: возможность коррозии и окисления, большая масса. Изготовление металлических корпусов в зависимости от размеров и формы может производиться механической обработкой; раскаткой из трубчатых заготовок, получаемых вытяжкой; вальцовкой из листовых заготовок и продольной сваркой; осаждением из газовой фазы.
Композиционные (стеклопластиковые, углепластиковые, боропластиковые) корпуса сопел получаются намоткой. Преимуществами их являются высокая прочность и малая масса. В такие корпуса часто в процессе намотки заделываются металлические детали, служащие для соединения с другими элементами соплового блока.
Сотовые корпуса сопел находят применение для малонагруженных корпусов, например, для корпусов конических или профилированных раструбов (частей) крупных сопел. В местах сосредоточенных нагрузок необходимо устанавливать в процессе изготовления внутри сотовой обечайки металлические усиливающие кольца. Недостатками являются относительная сложность изготовления, более высокая стоимость и трудность контроля качества склеивания сот с обшивкой (рентгеновский и ультразвуковой контроль).
Внутренняя теплозащитная облицовка сопел РДТТ работает в условиях высоким температур, значительных давлений, эрозионного воздействия истекающей струи раскаленных газов. Конструктивно внутренняя теплозащитная облицовка состоит из отдельных кольцевых элементов (вкладышей), полученных различными способами. Наиболее тяжелонагруженными из них являются вкладыши критического сечения двигателя. Кольцевые вкладыши изготавливают механической обработкой из вольфрама, молибдена, графита, огнеупорного карбида и других материалов. Вкладыши могут также изготавливаться намоткой графитовой или других лент, пропитанных фенольной смолой. Сборка кольцевых вкладышей теплозащиты с корпусом сопла производится склеиванием в скрепленном состоянии.
Собранное сопло подвергается контролю ультразвуком и рентгеноконтролю для определения сплошности материала и целостности конструкции сопла. Точное соблюдение технологических требований и режимов на всех стадиях изготовления сопел является необходимым условием обеспечения высокого качества и надежности. На поверхность теплозащитной облицовки иногда наносят керамические жаростойкие покрытия, что позволяет уменьшить толщину теплозащиты сопла РДТТ.
|
Сборка и испытания РДТТ.
После изготовления всех деталей и узлов и комплектации они поступают на операцию заливки топливной массы и общую сборку РДТТ. Процесс заливки готовой топливной массы часто занимает значительное время (исчисляемое иногда десятками часов), поэтому полимеризация топлива начинается уже в процессе заливки. С целью обеспечения сплошности топлива и требований к снаряженному двигателю заливка проводится в специализированных установках с несколькими заливочными трубопроводами и специальными стержнями по особой технологии. Процесс полимеризации топлива протекает в течение 50-200 ч в зависимости от размеров двигателя. Так как при полимеризации топливный заряд может уменьшаться в размерах, в конструкции камеры предусматривается установка каучуковых прокладок в переднем днище для компенсации усадки заряда.
Проводят контроль прочности скрепления заряда с теплозащитой стенок корпуса двигателя радиографическим методом, позволяющим обнаружить зазор между теплозащитой стенок корпуса и топливным зарядом, а также контроль сплошности заряда твердого топлива (наличие трещин и раковин).
При общей сборке производится установка всех деталей и узлов двигателя. После этого устанавливается заднее днище с сопловым блоком. Установленное количество твердотопливных двигателей из партии проходит огневые испытания с контролем тяги (мощности двигателя) и с последующим определением степени эрозии (разрушение и унос поверхностного слоя) теплозащитных облицовок двигателя. Все штатные РДТТ проходят химико-термическую стерилизацию, что должно быть предусмотрено при выборе материалов и способов соединения отдельных элементов двигателя. Полностью собранные и испытанные двигатели консервируются и поступают на общую сборку РН или КА.
|
26.Изготовление и испытания трубопроводов и солнечных батарей КА.
Изготовление и испытания трубопроводов.
В конструкциях РН и КА широко применяются трубопроводы, требования к которым следующие: прочность, жесткость, герметичность, коррозионная стойкость, стойкость при криогенных температурах, надежность. Материалами для трубопроводов являются алюминиевые и титановые сплавы, нержавеющие и жаропрочные стали, сплавы на основе никеля, иногда цветные сплавы (латунь, бронза).
По конфигурации трубопроводы делятся на прямые, криволинейные в одной плоскости и криволинейные в двух или трех плоскостях. Они могут быть простыми, состоящими из одного трубопровода, и составными, собираемыми из нескольких трубопроводов, с разъемными и неразъемными соединениями. Разъемные соединения могут быть резьбовыми или замковыми. Неразъемные соединения - сварные.
Общая схема изготовления трубопровода зависит от вида исходной заготовки. Наиболее распространенными видами заготовок для трубопроводов являются металлические бесшовные стандартные трубы и листовые заготовки.
Cхема изготовления трубопроводов из труб состоит из следующих этапов: отрезка труб по заданной длине, зачистка заусенцев, гибка, испытания, промывка, сушка, консервация.
Отрезка труб заданной длины осуществляется дисковыми пилами, которые позволяют получать как прямые, так и косые торцы. Методом отрезки труб также является отрезка их абразивными кругами, что обеспечивает более высокую точность и меньшие заусенцы. Отрезку труб также производят на токарных станках резцами, что дает хорошую точность и качество торцов, но низкую производительность. В серийном производстве применяют специальные трубоотрезные станки, которые позволяют отрезать трубы диаметром до 280 мм с высокой точностью, отсутствием заусенцев и деформаций даже у тонкостенных труб.
Если в стенках трубопроводов имеются различные окна, прорези, пазы, то их изготовление производится до гибки, когда они остаются на прямолинейной части трубы, а в случае крупных окон, попадающих в криволинейную часть трубы – после гибки. В мелкосерийном производстве изготовление их осуществляется на фрезерных станках пальцевыми или дисковыми фрезами. При больших объемах выпуска прорези могут выполняться в штампах.
Сложность гибки заключается в том, что ее режимы и условия подбираются экспериментально в зависимости от свойств материала, размеров трубопровода, радиуса гибки. При гибке возможно появление следующих отрицательных явлений: наружная стенка утоняется, а внутренняя утолщается; на внутренней стенке возможно появление складок; круглое сечение трубы приобретает овальную форму.
|
Для избежания дефектов, гибку производят с различными наполнителями: кварцевый песок; замороженная вода; для алюминиевых труб применяют парафин. Иногда трубы гнут с внутренним гидронагружением, когда один конец трубы заглушается, а другой заполняется жидкостью или маслом под давлением.
Другим путем, позволяющим избежать дефектов гибки или уменьшить их, является местный нагрев изгибаемого участка трубы, например, пламенем газовой горелки.
К трубопроводам присоединяют более мелкие детали, которые называют деталями арматуры – это штуцера, патрубки, фланцы. Сами детали арматуры изготавливают обработкой на станках. Их соединение с трубопроводами производят сваркой, используют приспособления для фиксации и базирования свариваемых деталей. Аналогично производится сварка трубопроводов друг с другом. После сварки швы зачищаются, отжигаются и подвергаются контролю неразрушающими методами (рентген, ультразвук).
Схема изготовления трубопроводов из листа следующая: разметка листа, вырезка заготовок; изгиб заготовок; сварка трубопровода; зачистка швов; промывка и сушка; контроль и испытания.
Особую группу трубопроводов составляют тоннельные трубопроводы, служащие для подачи одного компонента топлива через бак с другим компонентом. Главной особенностью тоннельной трубы является наличие ряда кольцевых рифтов (волнообразных складок) по длине тоннельной трубы для компенсации возможных деформаций. Материалы для тоннельных труб те же, что и для обычных труб.
Заготовками для тоннельных труб чаще всего являются листы. Схема изготовления состоит из следующих этапов: раскрой заготовки из листа по шаблону; деформация заготовки в трубу с образованием рифтов; механическая обработка кромок под сварку; сварка продольного шва; зачистка и отжиг сварных швов; контроль и испытания.
К трубопроводам также относят сильфоны (гибкие трубопроводы), представляющие собой тонкостенные цилиндрические или конические металлические оболочки с поперечными волнообразными складками на поверхности - гофрами, благодаря которым сильфоны имеют возможность в определенных пределах изменять длину и изгибаться.
Сильфоны применяют для:
1) соединения жестких трубопроводов, имеющих угловое и осевое смещение,
2) температурной компенсации (расширение или сжатие трубопроводов),
3) устранения монтажных напряжений (внутренних сил) при сборке,
4) демпфирования (гашения) вибраций и колебаний,
5) в качестве упругих элементов, реагирующих на изменение давлений или сил,
6) для подвижных соединений трубопроводов.
Материалы для сильфонов должны обладать высокой пластичностью, позволяющей получать гофры; достаточной прочностью и упругостью при низких и высоких температурах; устойчивостью против агрессивных компонентов топлива; усталостной прочностью для работы в условиях изгибов и вибрации; хорошей свариваемостью.
Наиболее распространенным материалом для сильфонов РН и КА является закаленная нержавеющая сталь, обладающая всеми вышеперечисленными свойствами. Сильфоны из этой стали могут работать в интервале температур от -194 до 400 град.С. Распространенным материалом для сильфонов является также латунь, которая может работать в интервале температур от -60 до 100 град.С. Для изготовления сильфонов применяются также титановые и алюминиевые сплавы.
Заготовками для сильфонов служат тонкостенные бесшовные трубы. Формообразование гофров производится раскаткой трубы роликами, при которой металл течет как внутрь, так и наружу трубы. После формообразования гофров сильфоны проходят отжиг, механическую обработку торцов и кромок, промывку, сушку.
Методы соединения сильфонов с арматурой: механическое (винтовое) соединение, скрепление бандажами (кольцами), соединение сваркой.
|
|
Эмиссия газов от очистных сооружений канализации: В последние годы внимание мирового сообщества сосредоточено на экологических проблемах...
Семя – орган полового размножения и расселения растений: наружи у семян имеется плотный покров – кожура...
Особенности сооружения опор в сложных условиях: Сооружение ВЛ в районах с суровыми климатическими и тяжелыми геологическими условиями...
История развития пистолетов-пулеметов: Предпосылкой для возникновения пистолетов-пулеметов послужила давняя тенденция тяготения винтовок...
© cyberpedia.su 2017-2024 - Не является автором материалов. Исключительное право сохранено за автором текста.
Если вы не хотите, чтобы данный материал был у нас на сайте, перейдите по ссылке: Нарушение авторских прав. Мы поможем в написании вашей работы!