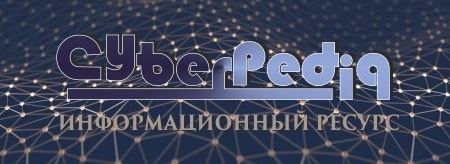
Своеобразие русской архитектуры: Основной материал – дерево – быстрота постройки, но недолговечность и необходимость деления...
Индивидуальные очистные сооружения: К классу индивидуальных очистных сооружений относят сооружения, пропускная способность которых...
Топ:
Когда производится ограждение поезда, остановившегося на перегоне: Во всех случаях немедленно должно быть ограждено место препятствия для движения поездов на смежном пути двухпутного...
Марксистская теория происхождения государства: По мнению Маркса и Энгельса, в основе развития общества, происходящих в нем изменений лежит...
Интересное:
Отражение на счетах бухгалтерского учета процесса приобретения: Процесс заготовления представляет систему экономических событий, включающих приобретение организацией у поставщиков сырья...
Подходы к решению темы фильма: Существует три основных типа исторического фильма, имеющих между собой много общего...
Лечение прогрессирующих форм рака: Одним из наиболее важных достижений экспериментальной химиотерапии опухолей, начатой в 60-х и реализованной в 70-х годах, является...
Дисциплины:
![]() |
![]() |
5.00
из
|
Заказать работу |
|
|
Оно включает следующие переходы:
· разрыхлительный,
· трёпальный,
· чесальный,
· ленточный,
· ровничный.
В хлопкопрядении на разрыхлительном переходе хлопковое волокно извлекается из спрессованных кип. Схема разрыхлительного агрегата приведена на рис.1
Рисунок 1 – Схема разрыхлительного агрегата
Кипы хлопка 2 устанавливаются в контейнер 1, перемещаемый возвратно-поступательно транспортерами 5. Решетки 3 предотвращают провисание хлопка, а вращающиеся колковые барабанчики 4 извлекают волокна хлопка и сбрасывают их на транспортер 6. Последний подает разрыхленный хлопок к приемнику пневмотранспорта 7, направляющего хлопок в бункера трепальных машин.
Задачей автоматизации этого агрегата является обеспечение возвратно-поступательного движения контейнера 1. Для этого используется схема управления электроприводом транспортеров 5, приведенная на рис. 2.
Рисунок 2 – Схема управления реверсивным электроприводом
Выключатель S0 подает питание на трехфазный асинхронный электродвигатель М. Две фазы обеспечивают питание двух схем пуска двигателя. Реле К1 своими контактами К1.1, К1.2, К1.3 включает двигатель «вперед», а реле К2 своими контактами К2.1, К2.2, К2.3 включает двигатель «назад». Кнопки «Пуск» S1, S3, кнопки «Стоп» S2,S4. Первоначально двигатель может быть запущен в любую сторону, но срабатывание соответствующего реле (например К1) сразу исключает возможность запуска двигателя в другую сторону размыканием блокировочного контакта (К1.5), предотвращая короткое замыкание в цепях питания двигателя. Когда контейнер 1, двигаясь «вперед», доходит до крайнего положения, он нажимает технологические контакты (в нашем примере К5.1 размыкается, а К5.2 замыкается). При этом реле К1 отпускает, замыкается его контакт К1.5, а контакт К5.2 включает реле К2, запуская двигатель в другую сторону. Контейнер движется «назад». При достижении другого крайнего положения контейнера 1 происходит нажатие технологических контактов К6.1 и К6.2. Реле К2 отпускает, а К1 срабатывает. Контейнер вновь движется «вперед». Кнопки «Стоп» позволяют остановить контейнер в любой момент.
|
В шерстопрядении шерсть поступает на предприятие в мешках, повергается ручной сортировке, затем моется па проходных барках и подается в сушильный агрегат (рис. 3). Промытая шерсть из барки 1 поступает на сетчатый транспортер 2, приводимый двигателем М. Сушка производится горячим воздухом, нагнетаемым вентиляторами 5. Контроль влажности шерсти вблизи выхода агрегата осуществляется радиоактивными датчиками, включающими излучатели 3 и приемники излучения 4. Принцип действия датчиков основан на зависимости поглощения радиоактивного излучения слоем шерсти от ее влажности. Приемники 4 подключены к блоку преобразования и индикации (БПИ). Последний подает сигнал о текущей влажности шерсти в блок управления (БУ). Последний формирует управляющее воздействие: при переувлажненной шерсти БУ останавливает двигатель М транспортера на время от 3 до 10 минут (в зависимости от типа шерсти и ее текущей влажности). При пересушенной шерсти БУ выключает часть вентиляторов, пока влажность шерсти не нормализуется. Высушенная шерсть поступает в приемник пневмотранспорта 6.
Рисунок 3 – Агрегат сушки шерсти
На трепальном переходе происходит отчистка волокна от сорных примесей и дальнейшее разрыхление. Здесь актуально решение задачи регулирования уровня волокна в бункерах с использованием фотоэлектрических датчиков.
Чесальный переход предназначен для ориентации волокон вдоль формируемого холста и разделения его на ленты. Важной задачей является стабилизация толщины холста, которая может измеряться педальным датчиком (рис. 4). Холст по ширине «прощупывается» несколькими педалями. Система шарниров осредняет перемещение отдельных педалей и формирует воздействие на регулятор, подающий волокно на прочес.
|
Рисунок 4 – Педальный датчик толщины холста
Ленточный переход призван обеспечить необходимую степень ровноты волокнистого материала (ленты) до поступления его на прядильный переход. Это осуществляется сложением нескольких лент (обычно 6-8), полученных с чесального перехода, и вытягиванием их до толщины одной ленты. Таких операций (переходов) может быть несколько. При этом обеспечивается параллелизация волокон вдоль ленты. Один из вариантов автоматизации ленточной машины показан на рис. 5.
Рисунок 5 – Схема автоматизации ленточной машины
Вытягивание ленты происходит между подающими цилиндрами (ПЦ) и вытяжными цилиндрами (ВЦ). Последние вращаются быстрее первых, приводимых двигателем М. Разность их скоростей определят степень вытягивания, которая должна зависеть от толщины сложенной ленты на входе в зону вытягивания. Эта толщина измеряется датчиком ровноты (ДР), подвижный диск которого воздействует на узел запоминания 2, представляющий собой вращающийся согласованно с (ПЦ) цилиндр, по образующим которого расположены стальные пальцы 3. Датчик ровноты смещает их сдвигающей планкой 1 вдоль цилиндра в зависимости от текущей толщины ленты. Считывающая планка 4 в зависимости от положения пальцев сдвигает рычажной системой 6 ремень 7 на коноидной передаче 8. Стирающая планка 5 возвращает пальцы в исходное положение. При смещении ремня 7 вверх скорость ВЦ увеличивается. Узел запоминания обеспечивает необходимую задержку от момента измерения толщины элемента ленты до попадания его в зону вытягивания.
Ровничный переход используется для получения в дальнейшем пряжи высоких номеров (тонкой пряжи). На этом переходе лента дополнительно вытягивается и слегка скручивается для придания ей большей прочности. На этом переходе особое внимание уделяется плавности пуска двигателей и контролю обрывов ровницы.
ПРЯДИЛЬНОЕ ПРОИЗВОДСТВО
Оно имеет целью получение пряжи из ленты или ровницы. Существует два основных видов прядения: веретенное и безверетенное.
При веретенном прядении лента или ровница вытягивается, энергично скручивается и наматывается на веретено, образуя початок (рис. 6). Початок имеет гнездо, тело и вершину. Наматывание пряжи на веретено происходит с большой скоростью (до 30 м/с). Диаметр намотки в процессе наработки початка меняется. Чем диаметр меньше, тем натяжение пряжи больше, значит увеличивается опасность ее обрыва, поэтому следует менять скорость вращения веретена при изменении диаметра намотки. Простейшим вариантом является так называемое базисное управление скоростью (рис. 7)
|
Рисунок 6 – Форма прядильного початка
Самым простым вариантом базисного управления является просто переключение скорости веретена (штриховая линия на рис. 7) использованием двухдвигательного привода. При этом регулирования скорости попросту не требуется.
Значительно более сложной задачей является обеспечение послойного регулирования скорости веретена, которое может потребоваться при получении пряжи высоких номеров. Здесь приходится учитывать, что при укладке каждого слоя пряжи на веретено диаметр намотки меняется, а значит меняется и натяжение пряжи. Схемы послойного регулирования весьма сложны и здесь рассматриваться не будут.
Рисунок 7 – Базисное управление скоростью ω вдоль початка L.
При безверетенном прядении (рис. 8) лента подается в прядильную камеру, вращающуюся с очень большой скоростью (до 45000 об/мин.). Волокна ленты центробежной силой раскладываются по стенке камеры, непрерывной оттяжкой извлекается из камеры скрученный материал (пряжа) и наматывается в паковку. Таким способом получают пряжу невысоких номеров.
Рисунок 8 – Схема безверетенного прядения
|
|
Типы сооружений для обработки осадков: Септиками называются сооружения, в которых одновременно происходят осветление сточной жидкости...
Биохимия спиртового брожения: Основу технологии получения пива составляет спиртовое брожение, - при котором сахар превращается...
Общие условия выбора системы дренажа: Система дренажа выбирается в зависимости от характера защищаемого...
Эмиссия газов от очистных сооружений канализации: В последние годы внимание мирового сообщества сосредоточено на экологических проблемах...
© cyberpedia.su 2017-2024 - Не является автором материалов. Исключительное право сохранено за автором текста.
Если вы не хотите, чтобы данный материал был у нас на сайте, перейдите по ссылке: Нарушение авторских прав. Мы поможем в написании вашей работы!