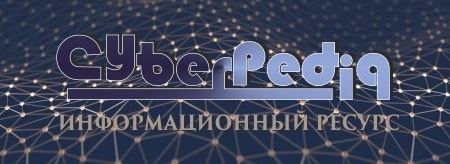
Общие условия выбора системы дренажа: Система дренажа выбирается в зависимости от характера защищаемого...
Таксономические единицы (категории) растений: Каждая система классификации состоит из определённых соподчиненных друг другу...
Топ:
Генеалогическое древо Султанов Османской империи: Османские правители, вначале, будучи еще бейлербеями Анатолии, женились на дочерях византийских императоров...
Основы обеспечения единства измерений: Обеспечение единства измерений - деятельность метрологических служб, направленная на достижение...
Устройство и оснащение процедурного кабинета: Решающая роль в обеспечении правильного лечения пациентов отводится процедурной медсестре...
Интересное:
Искусственное повышение поверхности территории: Варианты искусственного повышения поверхности территории необходимо выбирать на основе анализа следующих характеристик защищаемой территории...
Финансовый рынок и его значение в управлении денежными потоками на современном этапе: любому предприятию для расширения производства и увеличения прибыли нужны...
Уполаживание и террасирование склонов: Если глубина оврага более 5 м необходимо устройство берм. Варианты использования оврагов для градостроительных целей...
Дисциплины:
![]() |
![]() |
5.00
из
|
Заказать работу |
|
|
Кравченко, Д.Г.
Устройство двигателя РД–107: учебное пособие/Д.Г. Кравченко, Ю.В. Анискевич, А.М. Лабанова; Балт. гос. техн. ун-т. – Спб., 2018. – 50 с.
Изложены общие сведения о жидкостном ракетном двигателе РД–107, разработанном для первой ступени межконтинентальной баллистической ракеты Р-7. Приведены основные этапы технического развития двигателя, рассмотрены устройство и принцип действия основных агрегатов и систем, особенности запуска и останова. В пособии представлены некоторые теоретические аспекты работы системы уплотнения турбонасосного агрегата, охлаждения камеры сгорания, а также работы форсунок, позволяющие глубже понять особенности устройства и функционирования двигателя РД–107.
Пособие предназначено для бакалавров и специалистов, обучающихся по направлениям подготовки «Двигатели летательных аппаратов», «Энергетическое машиностроение», «Ракетные комплексы и космонавтика», «Проектирование, производство и эксплуатация ракет и ракетно-космических комплексов», «Баллистика и гидроаэродинамика».
УДК 621.454.2(075.8)
Рецензент канд. техн. наук, проф. каф. А3 БГТУ Л.И. Калягин
Утверждено
Редакционно-издаительским
советом университета
© Авторы, 2018
© БГТУ, 2018
Введение
Разработка многокамерных двигателей РД–107, РД–108 тягой в пустоте 1,0 МН и 0,92 МН соответственно была начата в опытно–конструкторском бюро под руководством главного конструктора В.П. Глушко в 1954 году. За сравнительно короткий срок были созданы двигатели, работающие при большом по тому времени давлении в камере и значительно превосходящие по своим характеристикам (тяга, удельный импульс, надежность и др.) все раннее созданные двигатели. Этому способствовала хорошо отработанная система смесеобразования и ряд принятых конструктивных решений. Создание двигателей РД–107, РД–108 явилось выдающимся событием в ракетостроении. С 1957 года советские космические и межконтинентальные ракеты были оснащены этими двигателями или их модификациями. С помощью РД–107 и РД–108 выводились на орбиту спутники Земли, Луны и Солнца, автоматические станции к Луне, Марсу и Венере, пилотируемые корабли–спутники «Восток», «Восход», «Союз».
|
На ракетах, для которых были созданы двигатели РД–107, РД–108 и их модификации, устанавливается по пять двигателей: по четыре двигателя РД–107 – на боковых блоках каждой ракеты, представляющих собой первую ступень, и по одному двигателю РД–108 – на центральном блоке, представляющим собой вторую ступень ракеты, запускающуюся одновременно с первой.
Двигатели РД–107 и РД–108 многокамерные. Они аналогичны по схеме и конструкции. Каждый двигатель состоит из четырех основных камер сгорания (КС), одного ТНА, газогенератора (ГГ), испарителя азота для наддува баков ракеты, комплекта агрегатов автоматики, узлов и деталей общей сборки. Кроме того, на двигателе РД–107 имеются два рулевых агрегата, а на двигателе РД–108 четыре рулевых агрегата, которые служат для управления полетом ракеты. Рулевые агрегаты включают в себя рулевые камеры и узлы, обеспечивающие их качание и подвод компонентов. Рулевые агрегаты питаются от основного ТНА.
Схема установки двигателей на ракете приведена ниже (Рис. 1).
Рис. 1. Двигатели РД–107 и РД–108, установленные на ракете: 1 — основные камеры сгорания двигателей РД–107; 2 — основные КС двигателя РД–108; 3 — рулевые агрегаты двигателей РД–107; 4 — рулевые агрегаты двигателя РД–108
Таблица 1.
Основные агрегаты и узлы двигателя
Камера двигателя (основная)
Камера двигателя (КД) – основной силовой элемент двигателя, создающий тягу, в котором химическая энергия топлива преобразуется в кинетическую энергию истекающей струи. Как известно, тяга ЖРД – реактивная сила, создаваемая КД, т.е. это равнодействующая гидрогазодинамических сил, действующих на внутренние поверхности камеры при истечении из нее вещества и сил давления окружающей среды, действующей на её внешние поверхности, за исключением сил внешнего аэродинамического сопротивления.
|
КД представляет собой паяно-сварную неразъемную конструкцию и состоит из цилиндрической камеры сгорания с плоской форсуночной головкой, докритической и закритической части сопла.
Форсуночная головка обеспечивает требуемое распределение компонентов топлива по сечению. На форсуночной головке (рис. 4) установлены 277 двухкомпонентных тангенциальных центробежных форсунок открытого типа с внутренним смешением и 60 однокомпонентных центробежных форсунок горючего «Г» в периферийном ряду.
Двухкомпонентные центробежные форсунки (рис. 3) подают компоненты топлива в соотношении, обеспечивающем высокий удельный импульс двигателя, при этом температура газа в ядре потока КС составляет порядка 3500 К. Во избежание перегрева стенок КС недопустимо, чтобы они омывались газами такой температуры. Поэтому по периферии форсуночной головки установлен внешний ряд однокомпонентных форсунок горючего, который создает пристеночный слой с избытком восстановительных элементов, температура которого значительно ниже, чем в ядре потока.
Рис. 3. Двухкомпонентные центробежные форсунки
Рис.4. Форсуночная головка: 1 — днище среднее; 2 — фланец с патрубком подвода окислителя; 3 — перегородки соединительные; 4 — секции наружного сферического днища; 5 — форсунка двухкомпонентная; 6 — форсунка однокомпонентная; 7 — днище внутреннее; 8 — силовое кольцо головки; 9 — втулки; 10 — штифт
В центробежной форсунке жидкость подается через тангенциальный входной канал поэтому момент количества движения струи жидкости на входе в форсунку относительно оси сопла не равен нулю, и жидкость течет по форсунке вращаясь. На выходе из сопла струя преобразуется в коническую пленку, которая дальше распадается на капли.
В КС установлены двухкомпонентные тангенциальные центробежные форсунки с внутренним смешением компонентов (рис. 3). Форсунки этого типа состоят из двух центробежных форсунок окислителя и горючего, связанных конструктивно в один смесительный элемент. Окислитель «О» поступает в форсунку через четыре тангенциальных отверстия, горючее через три (рис. 3). Особенностью является то, что сопло внутренней форсунки (окислителя) углублено относительно сопла внешней форсунки (горючего) настолько, что обеспечивается устойчивое взаимодействие компонентов на внутренней поверхности сопла внешней форсунки.
|
Все двухкомпонентные форсунки одинаковы по конструкции и расположены равномерно по девяти концентрическим окружностям (плюс одна форсунка в центре головки). Двухкомпонентные форсунки по точности изготовления (по расходу через них) разбиты на девять классов – для каждой из полостей «Г» и «О» устанавливаются по три градации расхода (размеров). Форсунки различных классов достаточно равномерно распределяются по площади головки. Такая компоновка головки позволила получить стабильные характеристики системы смесеобразования и явилась достаточно эффективным методом подавления высокочастотных пульсаций давления в КС.
Все форсунки припаяны к плоским внутреннему 7 (рис. 4) и среднему 1 днищам, между которыми находится полость горючего.
Полость окислителя образована средним днищем 1 и наружным сферическим днищем 4. Для увеличения прочности между средним 1 и наружным 4 днищами установлены две кольцевые перегородки 3 с отверстиями для прохода окислителя.
В КД применяется два варианта конструктивного исполнения охлаждающих трактов. Наименее теплонапряженные места КД, а именно цилиндрическая КС (1, рис.5), начальный участок докритической части сопла и второй участок расширяющейся части сопла (3, рис.5) состоят из двух оболочек – гладкой внутренней (огневой) и наружной, соединенных между собой через гофрированную проставку посредством пайки.
Наиболее теплонапряженный участок КД – район критического сечения сопла (2, рис.5). Для его охлаждения используется каналы, образованные фрезерованием огневой стенки КД. По вершинам ребер стенка припаивается к наружной оболочке камеры.
Рис. 5. Схема охлаждения КД
|
Для уменьшения габаритов двигателя подвод горючего осуществляется на некотором удалении от среза сопла. При этом на входе в охлаждающий тракт горючее делится на два потока (рис 5). Один поток по каналам между рубашкой и гофрированной проставкой направляется в сторону форсуночной головки, второй по таким же каналам доходит до среза сопла и возвращается обратно по каналам, образованным гофрированной проставкой и огневой стенкой. В месте стыка гофрированных проставок оба потока соединяются и продолжают движение в сторону форсуночной головки.
Таблица 3.
Основные параметры КС
Параметр | Значение |
Расход горючего, кг/с | 20,8 |
Расход окислителя, кг/с | 52,2 |
Диаметры, мм: | |
цилиндрической части КС | 430 |
критического сечения | 165,8 |
выходного сечения сопла | 720 |
Объем КС докритического сечения, м3 | 0,085 |
Относительная расходонапряженность (расход отнесенный к давлению в КС и к площади форсуночной головки), кг/с∙м2∙Па | 86∙10–6 |
Время пребывания продуктов в КС, с | 5,59∙10–3 |
Турбонасосный агрегат
ТНА РД–107 (Рис. 6) состоит из турбины 5, НОК 4, НГ 3, перекиси водорода 2 и жидкого азота 1. В РД–107 с ТНА совмещен также испаритель жидкого азота 6.
НОК и НГ подают компоненты топлива в камеру сгорания, насос перекиси водорода служит для подачи перекиси водорода в газогенератор, а насос жидкого азота – для подачи азота в испаритель, а затем на наддув баков.
ТНА выполнен по схеме с консольным расположением турбины. Такая компоновка обеспечивает удобство подвода генераторного газа к турбине, снижает требования к уплотнениям по газу междунасосом и турбиной, кроме того, при таком расположении турбины выходной коллектор является несиловым элементом, в отличие от межопорных схем ТНА, и следовательно он имеет существенно меньший вес.
Рис. 6. Схема ТНА РД–107: 1 – насос азота; 2 – насос перекиси водорода; 3 – НГ; 4 – НОК; 5 – турбина; 6 – испаритель
Турбина – автономная, осевая, двухступенчатая, высокоперепадная, активного типа с консольным расположением ротора, работает на продуктах разложения перекиси водорода.
Газовая турбина – разновидность лопаточной машины, в которой энергия газа преобразуется в механическую энергию вращения. Газ, выходя из автономной турбины, выбрасыватся в окружающую среду.
Для повышения удельной мощности турбины в ней срабатывается большой сверхзвуковой перепад давления. Дальнейшее увеличение перепада по сравнению с выбранной величиной нецелесообразно, так как приводит к увеличению веса турбины при незначительном приросте удельной мощности. При выбранном сверхзвуковом перепаде давлений высокий коэффициент полезного действия турбины можно получить только применив двухступенчатую турбину.
|
Турбина в общем случае состоит из соплового аппарата 2 (Рис. 7), рабочего колеса с лопатками 3, корпуса с коллектором подвода парогаза 1 и выходным патрубком 5.
Рис. 7. Турбина ТНА двигателя: 1 – коллектор подвода парогаза; 2 – сопловой аппарат турбины; 3 – лопатки турбины первой, второй ступени, 4 – направляющий аппарат турбины; 5 – выходной патрубок парогаза
Сопловой аппарат 2 (рис. 8) служит для преобразования потенциальной энергии газа в кинетическую и придания потоку газа нужного направления для входа на лопатки рабочего колеса 3, где производится полезная работа. Сопловой аппарат выполнятся в виде круговой лопаточной решетки. Рабочее колесо представляет собой диск с лопатками, имеющими специальный профиль.
При движении по сопловому аппарату кинетическая энергия газа увеличивается, вследствие чего газ на лопатки диска первой ступени истекает со сверхзвуковой скоростью. При движении в межлопаточных каналах часть кинетической энергии газа превращается в механическую работу вращения рабочего колеса турбины. На выходе из первой ступени турбины газ попадает на лопатки направляющего аппарата 4, которой придает потоку газа нужное направление на входе во вторую ступень турбины. Отработанный газ через выходной патрубок 5 истекает в атмосферу. Вращающееся рабочее колесо турбины приводит в действие насосы компонентов топлива.
Насос окислителя шнекоцентробежный с двухсторонним подводом компонента. В высокорасходных насосах двигателей больших тяг широко применяется двухсторонний вход, то есть центробежное колесо 5 (рис. 8) выполняется симметричным, состоящим как бы из двух колес с односторонним входом, что позволяет сократить массогабаритные характеристика насоса, а также снизить осевые нагрузки на вал. Выходная рабочая полость выполнена в виде спирального отвода (улитки) и комбинации с диффузором. НГ шнекоцентробежный с односторонним подводом компонента.
Каждый насос состоит из корпуса, рабочего колеса 5 (крыльчатки), шнека 3, вала, подшипников, узлов уплотнения и крышки с подводящим патрубком (рис. 9).
Подводимая по оси работающего центробежного насоса жидкость под воздействием центробежных сил отбрасывается к периферии в результате чего возрастает давление. В улитках корпуса насоса давление жидкости продолжает расти вследствие уменьшения скорости ее движения. В результате на выходе из насоса жидкость находится под высоким давлением.
Турбина 6 и НОК 5 имеют общий вал (рис. 8), НГ имеет свой вал. Валы расположены соосно и соединены рессорой 4.
Рис. 8. Обьемная модель ТНА: 1 – рабочее колесо насоса перекиси водорода; 2 – рабочее колесо насоса азота; 3 – ведущая шестерня мультипликатора; 4 – рессора; 5 – рабочее колесо НГ; 6 – рабочее колесо НОК; 7 – диск турбины; 8 – испаритель
Крутящий момент на валы вспомогательных насосов перекиси водорода 1 (рис. 8) и жидкого азота 2 передается через мультипликатор, ведущая шестерня 3 которого расположена консольно на валу насоса горючего. Применение мультипликатора 3 позволило использовать для вспомогательных насосов более высокие частоты вращения, что повысило экономичность, уменьшило вес и габариты как насосов перекиси водорода и жидкого азота, так и всего ТНА. Вспомогательные насосы центробежные, имеют односторонний подвод, преднасосов нет.
В ТНА применяются комбинированные уплотнения, состоящие из уплотнительных колец 6 (рис. 9), манжет 1, чугунных разрезных колец (сегментных колец) 2, импеллера (отражателя) и лабиринтных колец 4.
Рис. 9 — фторопластовая манжета; 2 — чугунные разрезные кольца; 3 — шнек; 4 — лабиринт; 5 — рабочее колесо НОК; 6 — алюминиевое кольцо
Уплотнительными кольцами снабжены все фланцевые соединения корпусных деталей ТНА 6 (рис. 9). Герметичность соединений обеспечивается высокой точностью изготовления посадочных мест, высокой чистотой сопрягаемых поверхностей и выбором материала уплотнительного кольца, например, алюминия для насоса окислителя.
Лабиринтные уплотнения (рис. 10) предназначены для уменьшения протечки компонентов из полости высокого давления (на выходе из рабочего колеса) в полость низкого давления (на входе в насос), то есть с их помощью производится первичное уплотнение рабочих колес насосов. Зазор между лабирантами и уплотнительными буртами крыльчатки δ выбран минимально возможным с точки зрения безопасности работы.
Рис. 10. Схема лабиринтного уплотнения
Лабиринтные уплотнения представляют собой ряд последовательно расположенных кольцевых полостей (камер). На входе в лабиринт поток жидкости сужается, а в камере лабиринта происходит внезапное расширение, которое приводит к турбулизации и перемешиванию всей массы. В конце камеры из объема струи выделяется поток постоянной массы, который вытекает во вторую щель и т.д. Присоединенные массы окружающей среды, оставаясь в камере, циркулируют и вновь примешиваются к входящей струе. Малый радиальный зазор δ уплотнения в сочетании с трением жидкости между поверхностями длиной L, образующими зазор, препятствует ее утечкам.
Манжетные уплотнения (рис. 11) служат для герметизации различных областей по валу. Уплотняющим элементом является фторопластовая (в НОК) и резиновая (в НГ) манжета,армированная для повышения жесткости металлическим кольцом 2. Работоспособность и срок службы манжеты с ростом перепада давлений уплотняемой среды и скорости на контактной поверхности резко уменьшаются. Предварительный натяг манжеты на уплотняемую поверхность обеспечивается ее губкой 4, которая направлена в сторону повышенного давления, и нажимным устройством в виде браслетной пружины 5. Внутренний диаметр манжеты всегда меньше диаметра вала на 5...8 %.
Рис. 11. – Манжетное уплотнение: 1 –корпус; 2 –кольцо арматуры; 3 – мостик; 4 – губка; 5 – браслетная пружина.
Манжетные уплотнения обеспечивают полную герметизацию по валу при залитом компонентом насосе. При работе насоса возможен некоторый износ манжет по внутреннему диаметру; в этом случае просочившийся по валу компонент отводится через дренажные каналы. Для уменьшения утечки в дренажи устанавливаются по две манжеты.
Для снижения нагрузки на манжету и, следовательно, ее износа, а также для уменьшения утечки в дренажи в НГ используют гидродинамическое уплотнение – импеллер, представляющий собой центробежное колесо полузакрытого типа с радиальными лопатками.
Основным элементом данного уплотнения служит диск (импеллер), заключенный в полость (рис. 12). Импеллер с одной стороны гладкий, а на другой имеет радиальные лопатки толщиной δ, выполненные высотой h. Импеллер на валу устанавливается гладкой поверхностью в сторону полости высокого давления. Жидкость движется по валу ротора в сторону низкого давления и заполняет полость с импеллером. При вращении импеллера жидкость под действием лопаток тоже будет вращаться. При этом на каждую частицу жидкости, заполнившей каналы импеллера, действует сила давления, направленная к центру, и центробежная сила – противоположного направления. В случае их равенства перетекание жидкости в радиальном направлении к центру прекратится.
Рис. 12. – Импеллер
На лопаточной стороне импеллера при нормальной работе уплотнений одновременно образуются газовая полость размером (Dг – dвт) и жидкостная полость размером (Dим – Dг). Таким образом, роль герметизатора обеспечивает вращающееся жидкостное кольцо толщиной (Dим – Dг), которое удерживает перепад давлений на уплотнении и препятствует проникновению газа из соседней полости (дренажной) или из полости турбины в насос.
Отбрасывая компонент к периферии навстречу его движению, импеллер, с одной стороны, повышает давление в области, куда просачивается компонент, то есть повышает гидравлическое сопротивление по линии утечки, а с другой стороны, снижает давление перед манжетой, уменьшая ее износ.
Для герметизации полостей газовой турбины с высокой температурой, а также насоса окислителя, подающего криогенную жидкость, применяют уплотнения с разрезанными на три сегмента кольцами. Зазор между сегментами составляет 0,3...0,6 мм (рис. 13). Сегменты 3 располагаются в гнезде корпуса с осевым зазором 0,02...0,06 мм и прижимаются к поверхности вала браслетной пружиной 2, располагаемой в канавке по их наружной цилиндрической поверхности. От проворачивания они удерживаются штифтом 4, который входит в гнездо опорного кольца 1 или корпуса и в отверстие одного из сегментов. Кольцевые сегменты притираются к валу и прижимаются давлением из уплотняемой полости своими боковыми поверхностями к стенкам пазов так, что создают герметизацию одновременно по цилиндрической и торцевой поверхностям. Для повышения герметичности узел такого уплотнения может иметь два или три последовательно установленных кольца из сегментов. При этом их фиксируют относительно корпуса так, чтобы торцевые зазоры между сегментами соседних колец смещались относительно друг друга. По мере износа сегментов торцевой зазор между ними уменьшается при неизменном контакте по поверхности вала. Кольцевые сегменты изготавливаются из графита или графитизированного чугуна с обязательной приработкой по уплотняемой поверхности.
Рис. 13. Уплотнение с кольцевыми сегментами: 1 – опорное кольцо; 2 – браслетная пружина; 3 – сегменты кольцевые;
4 – штифт
Смазка и охлаждение шариковых подшипников, применяемых в ТНА РД–107, осуществляется различно: в насосе окислителя – небольшим расходом жидкого кислорода из полости высокого давления через специальные сверления, в насосе горючего – с помощью специальной консистентной смазки, стойкой к горючему, в насосе перекиси водорода тоже консистентной смазкой, а в насосе жидкого азота – жидким азотом.
В полость мультипликатора заливается специальная жидкая смазка.
Таблица 5.
Основные параметры ТНА
Параметр | Значение |
Мощность ТНА, МВт | 3,827 |
Число оборотов турбины и основных насосов О и Г, об/мин | 8300 |
Число оборотов вспомогательных насосов, об/мин | 18100 |
Расходы, кг/с: | |
окислителя | 226 |
горючего | 91,4 |
перекиси водорода | 8,8 |
жидкого азота | 1,75 |
Минимальные давления на входе, МПа: | |
НОК | 0,44 |
НГ | 0,27 |
насос перекиси водорода | 0,28 |
насос азота | 0,35 |
Давление на выходе, МПа: | |
НОК | 7,84 |
НГ | 9,26 |
насос перекиси водорода | 8,03 |
насос азота | 3,82 |
КПД насоса «О» | 0,67 |
КПД насоса «Г» | 0,65 |
Эффективный КПД турбины | 0,57 |
Температура парогаза на входе в турбину, К | 833 |
Давление на входе в турбину, МПа | 5,34 |
Давление на выходе из турбины, МПа | 0,14 |
Сухая масса ТНА, кг | 237 |
Относительная масса ТНА (масса ТНА, заполненного компонентами, отнесенная к единице тяги двигателя у Земли), кг/МН | 330 |
Газогенератор
Газогенератор (рис.14) предназначен для выработки рабочего тела для турбины. В нем происходит каталитическое разложение 82 %-ной перекиси водорода, в результате чего образуется парогаз – смесь водяного пара и газообразного кислорода.
Рис.14.Газогенератор двигателя РД–107: 1 — труба; 2 — ребро; 3 — стакан; 4 — уплотнительная прокладка; 5 — крышка; 6 — стеклянный жгут; 7 — фланцы; 8 — болт; 9 — катализатор; 10 — корпус с теплозащитным кожухом; 11 — шнек
В качестве катализатора 9 используется твердый катализатор марки «Ж–30–С–О», представляющий собой смесь зерен неправильной формы размером от 6 до 10 мм. Зерна представляют собой спеченное из карбонильного порошкового железа, натриевой селитры и соды пористое окисленное железо. 50% общего количества зерен покрывается активным слоем, состоящим из водного раствора перманганата калия и соды. Эти зерна и являются соответственно катализатором.
Наличие двух пакетов катализатора позволяет увеличить поверхность контакта перекиси водорода с катализатором при небольшом диаметре ГГ и уменьшить перепад давления на катализаторе. Перекись водорода через жиклер подается в полость между пакетами. Неразложившаяся в пакетах перекись доразлагается в устанавливаемых для этой цели сетках и шнеках 11. ГГ заключен в корпусе 10 с теплоизолирующим кожухе.
Таблица 7.
Основные характеристики ГГ
Характеристика | Значение |
Давление парогаза на выходе из ГГ, МПа | 5,35 |
Расход перекиси водорода, кг/с | 8,8 |
Удельная нагрузка, кг перекиси/кг катализ. | 3,8 |
Время работы с обеспечением выходных параметров, с | > 140 |
Масса ГГ с катализатором, кг | 19,5 |
Редукторы
Редуктор точной настройки
Редуктор точной настройки 21 предназначен для управления работой регулятора расхода перекиси водорода 23 (рис. 2).
Принципиальная схема редуктора представлена ниже (рис. 15).
Рис.15. Редуктор точной настройки: 1 – электропривод; 2, 7, 10, 11, 12 – пружина; 3 – жиклёр с фильтром; 4, 13 – клапан; 5, 14 – седло; 6 – теплообменник; 8, 15 – регулирующий винт; 9 – фильтр
ВВД через фильтр 9 поступает в полость высокого давления редуктора. Редуцирование воздуха происходит между седлом 5 и клапаном 4, который отжат от седла разностью усилий пружин 7 и 10, а также разностью сил давлений ВВД и воздуха в полости «Б» редуктора организованно постоянное стравливание воздуха из этой полости через жиклер с фильтром 3. Величина стравливания определяется зазором между клапаном 13 и седлом 14. Зазор устанавливается, исходя из равновесия сил сжатия пружин 12 и 2 и сил давления воздуха в полостях «А» (или «В») и «Б».
Предварительная настройка редуктора осуществляется поджатием пружины 7 с помощью регулировочного винта 8.
Перенастройка редуктора в полете осуществляется изменением поджатия пружины 2 регулировочным винтом 15 с электроприводом 1, входящим в систему РКС.
В редукторе применены следующие материалы: седла выполнены из бронзы БрАжмц , клапаны и шнеки из стали Ст.2Х13, манжеты из резины 9035, корпус и другие детали из алюминиевого сплава АВ.
Редуктор грубой настройки
Редуктор грубой настройки 15 (рис.2) предназначен для поддержания рабочего давления, необходимого для работы агрегатов автоматики, в течение всего времени работы двигателя.
Принципиальная схема редуктора представлена ниже (рис.16).
Рис.16. Редуктор грубой настройки: 1 – седло; 2 – фильтр; 3 – клапан; 4, 6 – пружина; 5 – манжетное уплотнение; 7 – регулирующий винт
ВВД через фильтр 2 поступает в полость «А». Редуцирование осуществляется в зазоре между клапаном 3 и седлом 1. Величина зазора определяется из условия равенства нулю алгебраической сумме всех сил, действующих на клапан. Суммарная сила воздействия формируется при воздействии силы сжатия пружин 4 и 6 с одно стороны и силы давления воздуха со стороны полости «А» и «Б»).
Настройка редуктора на заданное давление на выходе осуществляется изменением поджатия пружины с помощью регулировочного винта 7.
В редукторе применены следующие материалы: седло выполнено из алюминиевого сплава Д16, регулировочный винт из стали Ст.2Х13, манжета из резины 9035 корпус из алюминиевого сплава АК8.
Регуляторы
Дроссель горючего
Дроссель горючего 6 (рис.2) предназначен для изменения гидравлического сопротивления магистрали горючего при первоначальной настройке двигателя на требуемое соотношение компонентов и в процессе работы ДУ в соответствии с сигналами системы СОБ. Агрегат состоит из собственного дросселя и электропривода.
Принципиальная схема дросселя горючего представлена ниже (рис.17).
Дросселирующая часть выполнена в виде двух колец с окнами, расположенных вплотную друг за другом. Часть горючего протекает по внутренней полости колец «А», имеющей постоянное сечение, а часть через окна «Б», меняющие площадь проходного сечения в зависимости от расположения подвижного кольца 1 относительно неподвижного 2. Поворот подвижного кольца 1 во время работы дросселя осуществляется с помощью червячной передачи в паре: валик 4 – подвижное кольцо. Валик 4 при этом перемещается поступательно, выступая в роли рейки в зависимости от поворота зубчатого сектора электропривода 5, также образующего с валиком червячную пару. Настройка дросселя обеспечивающая первоначальное соотношение компонентов, осуществляется при повороте валика 4 за хвостовик 6. При этом сектор 5 остается неподвижным, а валик 4 вращаясь, движется поступательно. Поворот подвижного кольца 1 происходит из–за разных величин шагов двух червяков валика.
Рис. 17. Дроссель горючего: 1 – подвижное кольцо; 2 – ролик; 3 – неподвижное кольцо; 4 – валик; 5 – зубчатый сектор электропривода; 6 – хвостовик; А – внутренняя полость колец; Б – окна
В дросселе применены следующие материалы: кольца выполнены из стали марки Х18Н10Т, корпус из алюминиевого сплава, валик из стали марки 12Х2НВФ.
Регулятор перекиси водорода
Регулятор 23 (рис.2) служит для поддержания заданного давления перекиси водорода (расхода) на входе в ГГ в течение всего времени работы двигателя, а также для ее слива из магистрали при испытании двигателя на стенде .
Рис. 18. Регулятор перекиси водорода: 1 – гильза; 2 – золотник; 3 – мембрана; 4 – корпус; 5 – клапан
Принципиальная схема регулятора представлена на рис.18.
Элементом сравнения в регуляторе является мембрана 4. В полость «А» подается управляющий воздух от редуктора точной настройки. Дросселирование перекиси водорода осуществляется в проходных щелях гильзы 2. Площадь щелей меняется при перемещении золотника 1, которое происходит до тех пор, пока силы, действующие на мембрану, – давление управляющего воздуха и давление жидкости на днище золотника – не будут уравновешены. При этом на выходе (полость «Б») устанавливается необходимое давление подачи перекиси водорода в ГГ. Для слива компонента из магистрали открывается вручную клапан 5.
В регуляторе применены следующие материалы: золотник, гильза, корпус выполнены из алюминиевого сплава Амг7, мембрана резиновая армированная.
Клапаны жидких компонентов
Главный клапан кислорода
Главный клапан кислорода 34 (рис.2) служит для подачи окислителя в основные и рулевые КС двигателя РД–107.
Принципиальная схема клапана представлена на рис.19.
Рис.19. Клапан окислителя: 1,6 – сильфон; 2 – штанга; 3 – пружина; 4,7 – клапан; 5 – разрывной болт; 8 – контакты; 9 – включатель; А – управляющая полость клапана давления воздуха
При подачe сжатого воздуха в управляющую полость «А» клапана давления воздуха, действующее на подвижное основание большого сильфона 1 через штангу 2 передается на клапан 4. Клапан, сжимая пружину 3, плотно прижимается тарелями к седлам корпуса. Наконечник включателя 9 размыкает контакты 8. Клапан закрыт.
При сбросе сжатого воздуха из полости «А» под действием давления компонента (давление наддува бака «О» и гидростатический напор), а также пружины 3 клапан 4 отводится от седел до упора головки разрывного болта в корпус. Наконечник включателя 9 замыкает контакты 8. Клапан окислителя открыт на предварительную ступень. В КС подается ограниченный расход окислителя.
При достижении работы окислителя на входе в клапан ~ 2,6 МПа обрывается разрывной болт 5 и клапан под действием давления окислителя и усилия пружины 3 резко открывается (до упора в корпус). Контакты включателя 8 размыкаются. Такое положение клапана соответствует его открытию на главную ступень. В клапане окислителя предусмотрена продувка его полостей газообразным азотом перед запуском.
Основные детали клапана выполнены из следующих материалов: корпус из алюминиевого сплава АЛ4, сильфон из стали Х18Н10Т, пружина 3 из стали 50ХФА.
Главный клапан горючего
Главный клапан горючего 40 (рис.2) предназначен для управления подачей керосина в основные и рулевые КС двигателя РД–107.
Принципиальная схема клапана изображена на рис.20.
С целью увеличения эффективной площади, на которую воздействует сжатый воздух, полость управляющего давления представляет собой две сообщающиеся полости «А» и «Б». Их герметизация осуществляется с помощью манжет. При подаче сжатого воздуха в управляющие полости тарель клапана 1 плотно прижимается к седлу. Клапан закрыт.
При стравливании воздуха из управляющих полостей тарель под действием давления горючего отходит от седла до упора буртика 6 в опору 2. Клапан открыт на предварительную ступень.
Рис.20 . Клапан горючего: 1 – седло; 2 – тарель; 3 – опора; 4 – клапан; 5,6 – пружина; 7 – буртик
При достижении определенного давления горючего на входе в клапан тарель начинает отжиматься, преодолевая усилие пружин 5 и 6. С ростом давления тарель отжимается до упора в торец направляющей 1. Клапан открывается полностью.
Основные детали выполнены из следующих материалов: корпус – из алюминиевого сплава АЛ4, направляющая из алюминиевого сплава АВ, сильфон – из стали Х18Н10Т, пружина стали 50ХФА.
Перекрывной клапан
Перекрывной клапан 31 (рис.2) служит для управления подачей перекиси водорода в ГГ. Он выполняет также функции обратного клапана.
Принципиальная схема перекрывного клапана представлена на рис.22.
Рис. 22. Перекрывной клапан: 1 – клапан; 2 – поршень; 3,5 – пружина; 4 – шток
Клапан находится в закрытом состоянии под действием пружин 3. При подаче управляющего воздуха в полость клапана «А» под действием последнего на поршень 2 пружины 3 сжимаются. Шток 4 отходит от клапана 1. Давлением перекиси водорода клапан 1 отжимается от седла. При этом сжимается пружина 5. Клапан открыт.
Если по каким–либо причинам давление на выходе из клапана сравняется с входным или превысит его, клапан закроется под действием пружины 5. В этом случае перекрывной клапан работает, как обратный.
При стравливании воздуха из управляющей полости клапан закрывается.
Основные детали изготовлены из следующих материалов: корпус выполнен из алюминиевого сплава АВ, клапан и седло из алюминиевого сплава АМГ7.
Клапан жидкого азота
Клапан 26 (рис.2) предназначен для подачи жидкого азота в испаритель. Его принципиальная схема изображена на рис.23.
Рис.23 . Клапан азота: 1 – тарель; 2, 7– седло; 3 – клапан; 4 – сильфон; 5 – пружина; 6 – основание; А – управляющая полость клапана
Клапан работает следующим образом. При отсутствии управляющего воздуха в полости «А» тарель 1 клапана под действием пружины 5 и давления жидкого азота плотно прижата к седлу 2. Клапан закрыт.
При подаче в управляющую полость «А» сжатого воздуха основание 6 сильфона 4 перемещается до упора 7, отжимая клапан 1 от седла 2. Пр
|
|
Общие условия выбора системы дренажа: Система дренажа выбирается в зависимости от характера защищаемого...
Эмиссия газов от очистных сооружений канализации: В последние годы внимание мирового сообщества сосредоточено на экологических проблемах...
Индивидуальные очистные сооружения: К классу индивидуальных очистных сооружений относят сооружения, пропускная способность которых...
Состав сооружений: решетки и песколовки: Решетки – это первое устройство в схеме очистных сооружений. Они представляют...
© cyberpedia.su 2017-2024 - Не является автором материалов. Исключительное право сохранено за автором текста.
Если вы не хотите, чтобы данный материал был у нас на сайте, перейдите по ссылке: Нарушение авторских прав. Мы поможем в написании вашей работы!