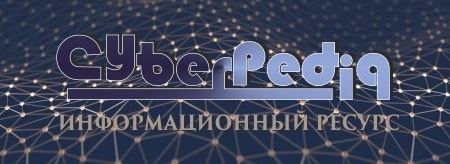
Эмиссия газов от очистных сооружений канализации: В последние годы внимание мирового сообщества сосредоточено на экологических проблемах...
Историки об Елизавете Петровне: Елизавета попала между двумя встречными культурными течениями, воспитывалась среди новых европейских веяний и преданий...
Топ:
Устройство и оснащение процедурного кабинета: Решающая роль в обеспечении правильного лечения пациентов отводится процедурной медсестре...
Основы обеспечения единства измерений: Обеспечение единства измерений - деятельность метрологических служб, направленная на достижение...
Марксистская теория происхождения государства: По мнению Маркса и Энгельса, в основе развития общества, происходящих в нем изменений лежит...
Интересное:
Национальное богатство страны и его составляющие: для оценки элементов национального богатства используются...
Принципы управления денежными потоками: одним из методов контроля за состоянием денежной наличности является...
Лечение прогрессирующих форм рака: Одним из наиболее важных достижений экспериментальной химиотерапии опухолей, начатой в 60-х и реализованной в 70-х годах, является...
Дисциплины:
![]() |
![]() |
5.00
из
|
Заказать работу |
|
|
Скорость скольжения в передаче. Передаточное число
Во время работы червячной передачи витки червяка скользят по зубьям червячного колеса рис. 2.5.11. Скорость скольжения направлена по касательной к винтовой линии делительного цилиндра червяка и определяется из параллелограмма скоростей
(2.5.11)
Как видно из формулы, всегда us> u1. Большое скольжение в червячной передаче повышает изнашиваемость зубьев червячного колеса, увеличивает склонность к заеданию.
Передаточное число червячной передачи определяют по условию, что за каждый оборот червяка колесо поворачивается на число зубьев, равное числу витков червяка:
(2.5.11)
где и — угловые скорости червяка и колеса;
z1 и z2 — число витков червяка и число зубьев колеса.
На практике в силовых передачах применяют червяки с числом витков z1 = 1; 2; 4. С увеличением z1 возрастают технологические трудности изготовления передачи и увеличивается число зубьев червячного колеса z2. Число витков червяка z1 зависит от передаточного числа и.
Рисунок 2.5.11 схема определения скорости скольжения в червячной передаче
Во избежание подреза основания ножки зуба в процессе нарезания зубьев принимают z2?26. Оптимальным является z2 = = 40...60. Диапазон передаточных чисел в этих передачах u = 10...80.
Вариаторы Основным критерием работоспособности фрикционных передач с указанными катками является усталостная прочность.
Расчет затянутых болтов. Пример затянутого болтового соединения – крепление крышки люка с прокладкой, где для обеспечения герметичности необходимо создать силу затяжки Q(рис.2.5). При этом стержень болта растягивается силой Qи скручивается моментом Мр в резьбе.
|
Рис. 2.5. Затянутое болтовое соединение
Напряжение растяжения , максимальное напряжение кручения τк = Мр/Wp, где
– момент сопротивления кручению сечения болта; Мр= 0,5Qd2tg(ψ+ φ'). Подставив в эти формулы средние значения угла подъема ψ резьбы, приведенного угла трения φ' для метрической крепежной резьбы, и применяя энергетическую теорию прочности, получим
Отсюда, согласно условию прочности σэкв ≤ [σр], запишем
где Qрасч= 1,3Q, а [σр] – допускаемое напряжение при растяжении.
Таким образом, болт, работающий на растяжение и кручение, можно условно рассчитывать только на растяжение по осевой силе, увеличенной в 1,3 раза. Тогда
Здесь уместно отметить, что надежность затянутого болтового соединения в значительной степени зависит от качества монтажа,т.е. от контроля затяжки при заводской сборке, эксплуатации и ремонте. Затяжку контролируют либо путем измерения деформации болтов или специальных упругих шайб, либо с помощью динамометрических ключей.
Расчет затянутого болтового соединения, нагруженного внешней осевой силой.Примером такого соединения может служить крепление zболтами крышки работающего под внутренним давлением резервуара (рис.2.6). Для такого соединения необходимо обеспечить отсутствие зазора между крышкой и резервуаром при приложении нагрузки Rz,иначе говоря, обеспечить нераскрытие стыка. Введем следующие обозначения: Q– силапервоначальной затяжкиболтового соединения; R– внешняя сила, приходящаяся на один болт; F– суммарная нагрузка на один болт (после приложения внешней силы R).
Тепловой расчет
Червячные передачи из-за высокого скольжения и низкого КПД работают с большим тепловыделением.
Нагрев масла выше допустимой температуры [t°]м приводит к снижению его вязкости, потере защитных свойств, разрушению масляной пленки и возможности заедания в передаче.
Тепловой расчет червячной передачи производят на основе теплового баланса, т.е. равенства тепловыделения Qвыд и теплоотдачи Qотд. Из условия
|
Qвыд = Qотд
определяют допустимую температуру tм масла в корпусе при непрерывной работе и естественном охлаждении
tм = t0 + 103(1 – η)Р1 / [KTA(1 + ψ)] ≤ [t]м,
где t0 – температура воздуха вне корпуса (обычно t0 = 20°C);
ψ - КПД передачи;
Р1 – мощность на червяке, кВт;
А – площадь поверхности редуктора, м2.Поверхность днища не учитывают, так как она не обтекается свободно воздухом;
ψ – коэффициент, учитывающий отвод тепла от днища редуктора в основание;
КТ – коэффициент теплоотдачи (тепловой поток в секунду с 1 м2 при перепаде температуры в 1°С) зависит от материала корпуса и скорости циркуляции воздуха. Для чугунного корпуса при естественном охлаждении КТ = 12…18 Вт/(м2·°С). В зависимости от марки масла [t]м = 90…110°С.
Если при расчете получится tм > [t]м, то необходимо:
1) на корпусе предусмотреть охлаждающие ребра. В расчете дополнительно к площади А учитывают 50% поверхности ребер;
2) применять искусственное охлаждение вентилятором, устанавливаемым на валу червяка. Коэффициент КТ = 20…40 Вт/(м2·°С) при n1 = 1000…3000 мин-1;
3) использовать охлаждение водой, проходящей через змеевик, установленный в масляной ванне;
4) применять специальную систему смазывания с охлаждающим радиатором.
Заклёпочные соединения.
^ Заклёпочным (клёпаным) называют неразъёмное неподвижное соединение, образованное с применением специальных закладных деталей заклёпок, выполненных из высокопластичного материала. Таким образом, заклёпочное соединение (Рис. 12.1) включает, по меньшей мере, 3 элемента (рис. 12.1, а): две соединяемых детали 1 и 2 и заклёпку 3, которая помещена в соосные отверстия, выполненные в соединяемых деталях. После сформирования соединения заклёпка, удерживающая во взаимном контакте соединяемые детали, имеет следующие 3 части (рис. 12.1, б): тело заклёпки или стержень 4 и две головки – закладную 5, изготавливаемую до формирования соединения, и замыкающую 6, создаваемую в момент образования заклёпочного соединения. Ряд заклёпок, соединяющих кромки двух или нескольких деталей, принято называть заклёпочным швом.
Рис. 12.1. Заклёпочное соединение:
а – в процессе сборки; б – в собранном виде
до появления современных видов сварки заклёпочные соединения были распространены особенно широко, однако и в настоящее время этот вид соединения достаточно активно используется в некоторых областях техники, например, в авиации, водном транспорте, приборостроении. Они применяются для соединения листовых, профильных (уголок, швеллер, двутавр и т.п.) и штампованных деталей, работающих в условиях переменных, вибрационных и ударных нагрузок. Особенно широко употребляются заклёпки для соединения разнородных или нагортованных (подвергнутых холодной деформации) материалов (сталь – алюминиевые сплавы; холоднокатаный лист; соединение металла с неметаллом).
|
Достоинства заклёпочных соединений:
простота конструкции и технологического исполнения;
возможность соединения разнородных и нагортованных материалов;
пригодность для неразрушающего контроля;
высокая стабильность;
высокая стойкость при действии ударных и вибрационных нагрузок.
Недостатки заклёпочных соединений:
высокий расход металла на образование соединения;
высокая трудоёмкость, а значит, и стоимость соединения;
ослабление прочности соединяемых деталей отверстиями под заклёпки;
нарушение плотности швов в процессе эксплуатациии.
Большое разнообразие областей применения заклёпочных соединений порождает и большое число их разновидностей.
Классификация заклёпочных соединений:
по функциональному назначению – прочные, предназначенные только для передачи нагрузки; плотные, обеспечивающие герметичное разделение сред, и прочно-плотные, способные выполнять обе названные функции;
по конструктивным признакам шва – нахлёсточное соединение (рис. 12.2, а); стыковое соединение, которое в свою очередь может быть выполнено с одной (рис. 12.2, б) либо с двумя (рис. 12.2, в) накладками;
Рис. 12.2. Основные типы заклёпочных швов: а – нахлёсточный;
б – стыковой с одной накладкой;
в – стыковой с двумя накладками.
по числу поверхностей среза, приходящихся на одну заклёпку под действием рабочей нагрузки – односрезные; двухсрезные; и т.д.; многосрезные;
по количеству заклёпочных рядов в шве – однорядные; двухрядные; и т.д.; многорядные.
критериями работоспособности заклепочных соединений будут прочность заклепки, смятие стержня заклепки
|
Расчёт передач винт-гайка
Основной причиной выхода из строя винтов и гаек передач является износ резьбы.
Интенсивность изнашивания связана с давлением p между витками резьбы винта и гайки,
которое, исходя из условий триботехнической надёжности (триботехника-наука об износе
и взаимодействии контактирующих тел), не должно превышать допускаемого [p]. Исходя
из этого определяется средний диаметр резьбы:
Жесткость валов, вращающихся в не-самоустанавливающихся подшипниках скольжения, должна быть достаточной, чтобы обеспечить необходимую равномерность распределения давления по длине подшипников. Расчет валов и подшипников в совместной работе при рассмотрении задачи как контактной и как гидродинамической приводится в специальной литературе. Применяют также упрощенные расчеты, в которых допустимый угол упругой линии вала в опоре (в радианах) выбирают равным минимальному диаметральному зазору в подшипнике, деленному на длину подшипника. Эти расчеты не могут считаться достаточно обоснованными, так как контактные деформации и упругие углы поворота корпусов соизмеримы с зазорами в подшипниках. [1]
Жесткость валов, вращающихся в шарикоподшипниках, должна обеспечиваться такой, чтобы шарики не защемлялись в результате перекоса колец. Это условие обычно выдерживается и не требует специальной проверки. Жесткость валов, вращающихся в роликоподшипниках, должна обеспечивать достаточно равномерное распределение давления по длине роликов. Ввиду отсутствия экспериментальных данных по влиянию перекосов на долговечность подшипников этот расчет носит условный характер. Для этих подшипников соответствующая проверка отпадает. [2]
Жесткость вала в ряде случаев может ограничиваться в связи с нарушением нормальной работы сопряженных деталей при неремещеипях, превышающих предельно допустимые. Поворот вала на опоре связан с перекосом колец подшипника качения и перераспределением нагрузки или защемлением тела качения, поворот осп вала в месте посадки шестерни - с перекосом зубьев в зацеплении и изменением напряженности зубьев. Жесткость вала определяет также частотные характеристики системы при возникновении крутильных или изгибных колебаний. [3]
Жесткость вала существенно зависит от его конструкции. При консольном расположении деталей прогибы и углы поворота получаются обычно больше и, соответственно, значения нагрузок, при которых достигаются предельно допустимые перемещения, понижаются. [4]
Жесткость вала существенно зависит от его конструкции. При консольном расположении деталей прогибы и углы поворота получаются обычно больше и, соответственно, значения нагрузок, при которых достигаются предельно допустимые перемещения, понижаются. [4]
|
Жесткость валов должна быть такой, чтобы Деформация их (с учетом деформации подшипников) была меньше соответствующих радиальных зазоров между шестернями и корпусом насоса, так как прогиб валов может вызвать задиры корпуса, а также нарушить условия нормального зацепления. [5]
Жесткость валов, вращающихся в подшипниках, должна быть такой, чтобы обеспечивались легкость и плавность вращения, а также достаточно равномерное распределение напряжений в контакте, влияющее в конечном итоге на ресурс подшипников. [6]
Жесткость валов, вращающихся в подшипниках скольжения, должна обеспечивать необходимую равномерность распределения давления по длине вкладышей. [7]
Жесткость вала в случае его касания по четырем точкам будет значительно больше, чем двухопорного. [8]
Жесткость валов, вращающихся в подшипниках скольжения, должна обеспечивать необходимую равномерность распределения давления по длине вкладышей. [9]
Жесткость вала К должна быть такой, чтобы е0т было больше начального эксцентриситета е0 в 1 6 ч - 2 0 раза. [10]
Жесткость валов оценивается величиной прогиба и наклона сечения вала под шестерней
При проверке прочности сварных швов учитывается возможный непровар в начале шва и образование кратера в конце. Поэтому расчетная длина шва принимается меньшей, чем действительная или проектная на 10 мм.
Необходимо отметить, что наиболее простым и надежным видом соединения является соединение встык, образуемое путем заполнения зазора между торцами соединяемых элементов наплавленным металлом. Соединение встык осуществляется, в зависимости от толщины соединяемых элементов, по одному из типов, показанных на Рис.2. Проверка прочности производится на растяжение или сжатие по формуле:
Здесь условная рабочая площадь сечения шва, где расчетная длина шва
, а высота шва h принимается равной толщине свариваемых элементов t.
Поскольку допускаемое напряжение для сварного шва ниже, чем для основного металла, стремятся к увеличению длины стыкового шва. С этой целью применяют соединение встык с косым швом
Предельные и допустимые напряжения
Предельным напряжением считают напряжение, при котором в материале возникает опасное состояние (разрушение или опасная деформация).
Для пластичных материалов предельным напряжением считают предел текучести, т. к. возникающие пластические деформации не исчезают после снятия нагрузки:
.Для хрупких материалов, где пластические деформации отсутствуют, а разрушение возникает по хрупкому типу (шейки не образуется), за предельное напряжение принимают предел прочности:
.Для пластично-хрупких материалов предельным напряжением считают напряжение, соответствующее максимальной деформации 0,2% (σо,2): курсы по наращиванию ногтей и маникюру.
.Допускаемое напряжение — максимальное напряжение, при котором материал должен нормально работать.
Допускаемые напряжения получают по предельным с учетом запаса прочности:
где [σ] — допускаемое напряжение; s — коэффициент запаса прочности; [s] — допускаемый коэффициент запаса прочности.
Примечание. В квадратных скобках принято обозначать допускаемое значение величины.
Допускаемый коэффициент запаса прочности зависит от качества материала, условий работы детали, назначения детали, точности обработки и расчета и т. д.
Он может колебаться от 1,25 для простых деталей до 12,5 для сложных деталей, работающих при переменных нагрузках в условиях ударов и вибраций.
Ускорение характеризует не только изменение величины скорости, но и изменение ее направления. Очевидно, что быстрота изменения направления вектора скорости, при прочих равных условиях, зависит от степени искривленности траектории. Для количественной оценки этой искривленности вводится понятие кривизны.
Клиновые ремни предназначены для передачи вращательного движения от ведущего шкива к ведомому. Применяются ремни приводные клиновые в приводах автомобилей, тракторов, сельскохозяйственных машин, станков и специализированных установках. Ремни клиновые работают в диапазоне температур от -30 до +60. Ремни приводные клиновые в разрезе имеют форму трапеции. Рабочими поверхностями ремня являются боковые поверхности они максимально прилегают к поверхности шкива образуя большую площадь сцепления и предотвращая проскальзывания при больших нагрузках. Ремни приводные клиновые стандартизированы и отвечают требованиям ГОСТа 1284-89. В зависимости от материалов применяемых для изготовления ремни приводные клиновые разделяются на пять классов.
Угол клина сечения ремня обычно составляет 38-40° (или 22-34°, если с помощью ремня регулируется скорость передачи). Основные геометрические характеристики клиновых ремней:
b - ширина ремня по большему основанию сечения;
h - высота ремня;
bp - расчетная ширина сечения - это ширина на уровне;
а - угол клина ремня.
Конструктивно ремни приводные клиновые состоят из несущего (тягового) слоя, растяжного, слоя сжатия и обертки. В зависимости от материала тягового слоя различают кордошнуровые и кордотканевые клиновые ремни. Кордошнуровые конструкции клиновые ремни имеют в тяговом слое спиральные витки кордошнура, а в кордотканевых конструкциях ремни имеют тяговый слой состоящий из слоев кордной ткани. В среднем, срок службы кордошнурового клинового ремня в1,5-2 раза больше срока службы кордотканевых приводных ремней, причем разница тем больше, чем короче ремни, и наоборот, эта разница уменьшается для приводных клиновых ремней больших длин.
Клиновые ремни в кордотканевой конструкции имеют нижние слои кордной ткани расположены в зоне сжатия. Кордошнуровые ремни обладают большей продольной гибкостью. Они могут работать на шкивах меньших диаметров, при больших скоростях. В кордотканевых ремнях на нижних слоях ткани, находящейся в зоне сжатия, в процессе работы наблюдается появление усталостных трещин, постепенно распространяющихся на весь тяговый слой. Для изгиба жестких кордотканевых ремней требуется затрата большей энергии и соответственно имеет место большее теплообразование, способствующее разрушению ремня. Кордошнуровые клиновые ремни обладают большей продольной гибкостью. Они могут работать на шкивах меньших диаметров, но при больших скоростях.
Плоскоременные передачи применяются как простейшие, с минимальными напряжениями изгиба. Плоские ремни имеют прямоугольное сечение, применяются в машинах, которые должны быть устойчивы к вибрациям (например, высокоточные станки). Плоскоременные передачи в настоящее время применяют сравнительно редко (они вытесняются клиноременными). Теоретически тяговая способность клинового ремня при том же усилии натяжения в 3 раза больше, чем у плоского. Однако относительная прочность клинового ремня по сравнению с плоским несколько меньше (в нем меньше слоев армирующей ткани), поэтому практически тяговая способность клинового ремня приблизительно в два раза выше, чем у плоского. Это свидетельство в пользу клиновых ремней послужило основанием для их широкого распространения, в особенности в последнее время. Клиновые ремни могут передавать вращение на несколько валов одновременно, допускают umax = 8 – 10 без натяжного ролика.
Компенсирующие муфты, допускающие небольшие осевые, радиальные и угловые смещения одного вала по отношению к другому, но не смягчающие толчков, относятся к группе жестких муфт. Компенсирующие упругие муфты смягчают толчки за счет деформации упругих элементов, передающих вращающий момент. Взаимное смещение соединяемых валов (см. рис. 15.2) может быть следствием погрешностей монтажа агрегата. Поэтому компенсирующие муфты рекомендуют применять, в частности, для соединения валов при отсутствии общего фундамента для всей установки или при монтаже ее на раме, не обладающей высокой жесткостью. Смещение валов может быть также следствием их упругих и температурных деформаций. [1]
Компенсирующие муфты позволяют соединяемым валам надежно работать при небольших неточностях монтажа, компенсировать деформации валов под нагрузкой и температурные деформации. Для компенсации некоторого несовпадения и перекоса осей валов (примерно до 30) применяется к у л а ч к о в о-д исков а я муфта (рис. 40.4), допускающая также и небольшое осевое смещение. Муфта состоит из двух одинаковых полумуфт / и 3 с промежуточным диском 2, входящим своими торцовыми взаимно перпендикулярными выступами в торцовые диаметральные пазы полумуфт. [2]
омпенсирующие муфты применяются при возможном некотором относительном смещении валов (рис. 15.1): продольном Д, поперечном г, угловом а ыя комбинированном. Рационально выбранная конструкция компенсирующей муфты в значительной мере устраняет вредное влияние несоосности осей валов, ч-ю особенно важно, если соединяются агрегаты, устанавливаемые на отдельных фундаментах или недостаточно жестких рамах. [3]
Компенсирующие муфты получили широкое распростра. [4]
Компенсирующая муфта позволяет соединить валы, оси которых установлены с погрешностью, например несо-осны или пересекаются. [5]
Компенсирующие муфты делятся на жесткие и упругие. В жестких муфтах компенсация несоосности валов достигается за счет подвижности жестких деталей муфты, а в упругих-за счет деформации упругих деталей муфты. [6]
Компенсирующие муфты возмещают влияние несоосности валов за счет подвижности деталей муфты. [7]
Компенсирующие муфты предназначены для соединения валов с небольшими взаимными смещениями осей, связанными с неточностями изготовления, монтажа и упругими деформациями. [8]
Компенсирующие муфты предназначены для соединения валов с небольшими взаимными смещениями осей, связанными с неточностями изготовления, монтажа п упругими деформациями. [9]
Компенсирующие муфты предназначены для соединения валов с небольшими взаимными смещениями осей, связанными с неточностями изготовления, монтажа и упругими деформациями. [10]
Компенсирующие муфты допускают смещение валов, происходящее из-за неточности монтажа или температурных деформаций. [11]
Основными критериями работоспособности валов являются прочность и жесткость. Валы и вращающиеся оси при работе испытывают циклически изменяющиеся напряжения. Прочность оценивают коэффициентом запаса прочности при расчете валов и осей на сопротивление усталости, а жесткость — прогибом, углами поворота или закручивания сечений в местах установки деталей. Практикой установлено, что разрушение валов и осей быстроходных машин в большинстве случаев носит усталостный характер, поэтому основным является расчет на сопротивление усталости.
Основными расчетными силовыми факторами являются крутящие Мк и изгибающие М моменты. Влияние растягивающих и сжимающих сил на прочность мало и их в большинстве случаев не учитывают.
Цепная передача относится к передачам зацеплением с гибкой связью. Цепные передачи применяют в станках, транспортных, сельскохозяйственных и других машинах для передачи движения между параллельными валами, расположенными на значительном расстоянии, когда зубчатые передачи непригодны, а ременные ненадежны. Наибольшее применение получили цепные передачи мощностью до 120 кВт при окружных скоростях до 15м/с. Она состоит из ведущей и ведомой звездочек и огибаемой их приводной цепи. К.П.Д. передачи зависит от потерь на трение в шарнирах цепи, на зубьях звездочек и на перемешивание масла при смазывании погружением -.
Рисунок 2.7.1 Цепная передача роликовой цепью а), зубчатой цепью б)
8.2 Достоинства цепных передач
1. Передача движения зацеплением, а не трением позволяет передавать большие мощности, чем с помощью ремня;
2. Практически не требуется натяжение цепи, следовательно, уменьшается нагрузка на валы и опоры;
3. Отсутствие скольжения и буксования обеспечивает постоянство среднего передаточного отношения;
4. Цепи могут устойчиво работать при меньших межосевых расстояниях и обеспечить большее передаточное отношение, чем ремённая передача;
5. Цепные передачи хорошо работают в условиях частых пусков и торможений;
6. Цепные передачи имеют высокий КПД.
8.3 Недостатки цепных передач
1. Износ цепи при недостаточной смазке и плохой защите от грязи;
2. Сложный уход за передачей;
3. Повышенная вибрация и шум;
4. По сравнению с зубчатыми передачами повышенная неравномерность движения;
5. Удлинение цепи в результате износа шарниров и сход цепи со звёздочек.
Валы и оси
Зубчатые колеса, шкивы, звездочки и другие вращающиеся детали машин устанавливают на валах или осях.
Деталь, на которую насаживают неподвижно или подвижно вращающееся устройство называется осью или валом.
Вал – вращающаяся деталь машины, предназначенная для поддержания установленных на нём деталей или для передачи вращающегося момента. При работе вал испытывает изгиб и кручение, в отдельных случаях растяжение и сжатие.
Ось – деталь машины, предназначенная только для поддержания установленных на ней деталей. Ось не передаёт вращающегося момента и следовательно не испытывает кручения. Оси могут быть подвижными и неподвижными.
По геометрической форме валы делятся на прямые, коленчатые и гибкие. Оси, как правило, изготовляют прямыми.
Прямые валы и оси могут быть гладкими или ступенчатыми. Образование ступеней связано с различной напря-женностью отдельных сечений, а также условиями изготовления и сборки. По типу сечения валы и оси бывают сплошные и полые. Полое сечение применяется для уменьшения массы и для размещения внутри другой детали.
Цапфы валов
Цапфы – участки вала или оси, лежащие в опорах. Они подразделяются на шипы, шейки и пяты.
Шипом называется цапфа, расположенная на конце вала или оси и передающая преимущественно радиальную нагрузку.
Шейкой называется цапфа, расположенная в средней части вала или оси. Опорами для шипов и шеек служат подшипники. Шипы и шейки по форме могут быть цилиндрическими, кониче-скими и сферическими. В большинстве случаев применяются цилиндрические цапфы. Пятой называют цапфу, передающую осевую нагрузку. Опорами для пят служат подпятники. Пяты по форме мо-гут быть сплошными (а), кольцевыми (б), гребенчатыми (в).
Посадочные поверхности валов
Посадочные поверхности валов и осей под ступицы насаживаемых деталей выполняют цилиндрическими и кони-ческими.
При посадках с натягом диаметр этих поверхностей принимают больше диаметра соседних участков для удобства напрессовки. Диаметры посадочных поверхностей выбирают из ряда нормальных линейных размеров, а диметры под подшипники качения – в соответствии с ГОСТами на подшипники.
Эффективным средством для снижения концентрации напряжений в переходных участках являются выполнение разгрузки канавок (а), увеличение радиусов галтелей, высверливание отверстий в ступенях большого диаметра (б). Деформационное упрочнение (наклеп) галтелей обкаткой роликами повышает несущую способность валов и осей.
Материалы валов и осей
Материалы валов и осей должны быть прочными, хорошо обрабатываться и иметь высокий модуль упругости. Валы и оси изготавливают преимущественно из углеродистых и легированных сталей. Для валов и осей без термообработки применяют стали Ст5, Ст6, а для валов с термообработкой – 45, 40Х. Цапфа на валах, работающих в подшипниках скольжения, цементируется для повышения износостойкости. Валы и оси обрабатываются на токарных станках с последующим шлифованием цапф и посадочных поверхностей.
Критерии работоспособности валов и осей
Валы и вращающиеся оси при работе испытывают циклически изменяющиеся напряжения. Основными критерия-ми работоспособности являются сопротивление усталости и жесткость. Сопротивление усталости валов и осей оценивается коэффициентом запаса прочности, а жесткость – прогибом в местах посадок деталей и углами наклона или закручивания сечений.
Основными силовыми факторами являются крутящие и изгибающие моменты. Влияние растягивающих и сжи-мающих сил невелико и в большинстве случаев не учитывается.
|
|
История развития пистолетов-пулеметов: Предпосылкой для возникновения пистолетов-пулеметов послужила давняя тенденция тяготения винтовок...
Поперечные профили набережных и береговой полосы: На городских территориях берегоукрепление проектируют с учетом технических и экономических требований, но особое значение придают эстетическим...
История создания датчика движения: Первый прибор для обнаружения движения был изобретен немецким физиком Генрихом Герцем...
Типы сооружений для обработки осадков: Септиками называются сооружения, в которых одновременно происходят осветление сточной жидкости...
© cyberpedia.su 2017-2024 - Не является автором материалов. Исключительное право сохранено за автором текста.
Если вы не хотите, чтобы данный материал был у нас на сайте, перейдите по ссылке: Нарушение авторских прав. Мы поможем в написании вашей работы!