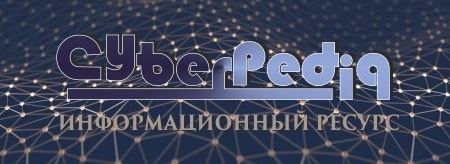
Особенности сооружения опор в сложных условиях: Сооружение ВЛ в районах с суровыми климатическими и тяжелыми геологическими условиями...
Индивидуальные и групповые автопоилки: для животных. Схемы и конструкции...
Топ:
Организация стока поверхностных вод: Наибольшее количество влаги на земном шаре испаряется с поверхности морей и океанов...
Характеристика АТП и сварочно-жестяницкого участка: Транспорт в настоящее время является одной из важнейших отраслей народного...
История развития методов оптимизации: теорема Куна-Таккера, метод Лагранжа, роль выпуклости в оптимизации...
Интересное:
Что нужно делать при лейкемии: Прежде всего, необходимо выяснить, не страдаете ли вы каким-либо душевным недугом...
Влияние предпринимательской среды на эффективное функционирование предприятия: Предпринимательская среда – это совокупность внешних и внутренних факторов, оказывающих влияние на функционирование фирмы...
Подходы к решению темы фильма: Существует три основных типа исторического фильма, имеющих между собой много общего...
Дисциплины:
![]() |
![]() |
5.00
из
|
Заказать работу |
|
|
Назначение, виды контроля
На участке очищения избыточной аммиачной воды от аммиака осуществляется операционный контроль технологического режима цеховым персоналом. Входной контроль аммиака осуществляется на участке аммиачного отделения. Приемочный контроль щёлочи осуществляется так же на участке аммиачного отделения.
Таблица 3 – Виды контроля
Виды контроля | Назначение (что контролируется | Ответственность | Примечание |
Входной | Аммиак | Лаборант | См.таб.-3 |
Операционный | См.таб.-4 | - | - |
Приемочный | Щелочь | Аппаратчик А.О. | Конц. 48% |
Схема лабораторного контроля отделения
Таблица 4 – Виды контроля
Что контролируется | Точка отбора | Показатели | Периодичность контроля | Ответственные |
Соединения аммиака | Отборный кран | Общий аммиак-0.300 не более | 10:00-16:00 22:00-4:00 | Аппаратчик аммиачного отделения |
Метрологическое обеспечение аммиачного отделения
Метрологическое обеспечение аммиачного отделения смотри приложение Г
Специальная часть
Расчёт шихты на коксование
Объём кокса килограмм в час:
Vкг= кг/ч.
Выход сухого кокса в кг/ч:
G=337968*0,94=317690 кг/ч.
Выход сухой шихты в кг/ч:
G= =410452кг/ч.
1 Влага шихты переведённая в килограммы в час по формуле
=Gв*
, (1)
где - влага шихты;
=
=26664 кг/ч.
Расчет материального баланса угольной шихты для
коксования
Расчёт материального баланса можно ввести для различного количества коксуемой шихты, но наиболее удобно рассчитывать на 1 т влажной (рабочей) шихты или в пересчёте на на сухую сухую шихту.
Материальный баланс коксования состоит из двух частей: приходной и расходной.
|
Приходная часть состоит из двух статей: сухая шихта и влага шихты.
Долгое время считалось, что приходная часть материального баланса коксования должна состоять из трёх статей: сухая шихта, влага шихты, а также количества воздуха и продукты горения, подсосанные из отопительной системы. В связи с внедрением положительного давления в камере коксования и соответствующего разрежения в отопительной системе возможность подсоса воздуха и продуктов горения исключена.
Расходная часть состоит из девяти статей: кокс валовый, коксовый газ и все улавливаемые из него химические продукты коксования, выход которых из шихты не ниже 0,1%. К ним относятся: каменноугольная смола, сырой бензол, аммиак, сероводород, влага шихты и вода пирогенетическая. Важной статьёй является “невязка баланса”, показывающая, на сколько точно сделан его расчёт.
Приходная часть
1. Сухая шихта. Загружаемую в камеру коксования сухую шихту подсчитывают по формуле
=
, (2)
где – количество рабочей шихты;
=
.
2. Влага шихты. Загружаемую в камеру коксования влагу вместе с шихтой подсчитываем по формуле:
G , (3)
где - количество рабочей шихты;
– влага шихты;
.
Расходная часть
Кокс валовый. Под коксом валовым понимается сумма крупного кокса, коксового орешка, коксовой мелочи,получаемых при сортировке рядового кокса, а так-же коксовый шлам, улавливаемый в отстойниках башен тушения.
Выход сухого кокса валового из сухой шихты подсчитываем по формуле:
G =
,
G *100+а, (4)
где –выход летучих веществ шихты на сухую массу, %. Для нашего примера – 26,6%;
– выход летучих веществ кокса валового на сухую зольную массу, %. Обычно принимается за 1,0%;
a – поправка (разница) на выход кокса, получаемого в производственных условиях и при определении выхода летучих веществ в лабораторных условиях, %.
|
Поправку а, часто называемую припеком, находят по следующей формуле, предложенной Г. П. Гейдом и А. Я. Обуховским:
а = *
, (5)
где – коэффициент пиролиза, зависящий при равномерном температурном режиме коксования от выхода летучих веществ
и определяемый с помощью графика (для донецких углей);
а =0,123*26,6=3,3%,
Тогда:
G *100+3,3=77,4%.
Выход сухого кокса валового на рабочую шихту пересчитываем по формуле:
G =G
*
, (6)
где G - выход сухого кокса валового из сухой шихты;
- влага шихты;
G =77,4*
73,7%.
Коксовый газ обратный (сухой). Выход коксового газа обратного (сухого)из сухой шихты подсчитываем по эмпирической формуле Я. О. Габинского:
G К
, (7)
где К-эмпирический коэффициент, уточнённый на кафедре ХТТ ДМетИ. Находиться в приделах 2,54-2,99 в зависимости от марочного состава шихты и режима коксования:
- выход летучих веществ шихты на сухую массу, %. Для нашего примера – 26,6%;
G 2
.
Пересчитываем выход сухого газа на рабочую шихту:
G = G
*
, (8)
где G - выход коксового газа обратного (сухого)из сухой шихты;
- влага шихты:
G =
*
.
Смола безводная. Выход смолы безводной из сухой шихты подсчитываем по эмпирической формуле С. Г. Аронова и Р. Л. Мишулович:
G =(-18,36+1,53
-0,026
, (9)
где -эмпирический коэффициент, уточнённый на кафедре ХТТ ДМетИ. Находиться в приделах 0,80-0,86 в зависимости от марочного состава шихты и режима коксования:
G =(-18,36+1,53*28,1-0,026
.
Пересчитываем выход безводной шихты на рабочую шихту по формуле:
G = G
*
, (10)
где G - выход смолы безводной из сухой шихты;
- влага шихты;
G =
*
.
Сырой бензол. Выход сырого бензола (бензольных углеводородов до 180ºС) из сухой шихты подсчитываем по эмпирической формуле С. Г. Аронова и Р. Л. Мишулович:
G =(-1,61+0,144
-0,0016
, (11)
где -эмпирический коэффициент, уточнённый на кафедре ХТТ ДМетИ. Находиться в приделах 0,84-0,97 в зависимости от марочного состава шихты и режима коксования;
|
G =(-1,61+0,144
-0,0016
.
Пересчитываем выход бензола на рабочую шихту по формуле:
G = G
*
, (12)
где G - выход сырого бензола (бензольных углеводородов до 180ºС) из сухой шихты;
- влага шихты;
G = 1,1*
.
Аммиак 100% - ный. Выход аммиака 100%-ного из рабочей шихты подсчитываем по формуле:
G , (13)
где в приделах 0,11-0,14;
G .
Сера в пересчёте на сероводород. Выход серы в пересчёте на сероводород из рабочей шихты подсчитываем по формуле:
G =
*
, (14)
где -коэффициент перехода серы шихты в сероводород, который находиться в приделах 0,17-0,29. Принимаем – молекулярный вес сероводорода; 32- атомный вес серы;
– содержание серы в рабочей шихте, %. Для нашего примера – 0,60;
G =
*
=0,15.
Влага шихты. Влагу шихты, испаряющейся в камере коксования, подсчитываем по формуле:
G , (15)
где – влага шихты;
– количество рабочей шихты;
.
Пирогенетическая вода. Выход пирогенетической воды изи рабочей шихты подсчитываем по формуле:
=
*
*
, (16)
где -коэффициент перехода кислорода шихты в пирогенетическую воду, который находиться в приделах 0,334-0,505. Для нашего примера принимаем равным 0,43; 18 – молекулярный вес воды; 16 – атомный вес кислорода;
– содержание кислорода в рабочей шихте, %. Для нашего примера – 4,96;
=0,43*4,96*
.
Невязка баланса. Находим по разности между приходной и расходной частями:
1000-(739,0+131,0+31,5+10,0+2,8+1,5+61,0+24)=1,2 кг; т.е. 0,12%.
Невязка баланса считается допустимой до 0,5%.
Для действующего завода невязка баланса является потерями производства. Чтобы эти потери были минимальными, необходимо выявить причины невязки баланса и устранять их.
Таблица 6 Сводный материальный баланс коксования угольной шихты
Приходная часть | Расходная часть | |||||||
Название статьи | Вес, кг | Процентный состав | Название статьи
| Вес, кг | Процентный состав | |||
На рабочую шихту | На сухую шихту | На рабочую шихту | На сухую шихту | |||||
1. Сухая шихта | ![]() | ![]() | 100,0 | 1. Кокс валовый | 737,0 | 73,70 | 77,40 | |
2. Влага шихты | ![]() | 6,1 | - | 2. Коксовый газ | 57262 | 13,10 | 13,13 | |
3. Смола безводная | 13988 | 3,15 | 3,35 | |||||
4. Сырой бензол | 4371 | 1,00 | 1,10 | |||||
5. Аммиак 100%-ный | 1311 | 0,28 | 0,31 | |||||
6. Сера в пересчёте на Н2S | 874 | 0,15 | 0,20 | |||||
7. Влага шихты | 26664 | 6,1 | 6,31 | |||||
8. Пирогенетическая влага | 874 | 0,24 | 0,26 | |||||
9. Невязка баланса | 437 | 0,12 | 0,14 | |||||
Итого | 437116 | 100,0 | 100,0 | Итого | 100,0 | 100,0 |
Расчет аммиачной колонны
Дистилляционная колонна для переработки надсмольной воды аммиачной воды.
Назначение и конструкция колонны.
Дистилляционная колонна представляет собой непрерывно действующий аппарат, служащий для выделения аммиака из надсмольной воды с помощью водяного пара. При этом летучий аммиак выделяется в испарительной колонне, а связанный аммиак после его разложения выделяется так-же в колонне.
В настоящее время применяют различные конструкции аммиачных колонн, отличающихся взаимным расположением расстоянием между тарелками, типами тарелок и колпачков и другими конструктивными элементами.
Обычно испарительная колонна состоит из чугунных царг, к которым крепятся чугунные тарелки с переливными устройствами различных конструкций. Царги устанавливают одна на другую и соединяют болтами на уплотняющих прокладках.
Нормально колонны работают на отработанном паре от паровых турбин, а свежий пар подводиться как резерв.
Расчёт подачи надсмольной воды на колонну:
Количество воды, подаваемое на орошение газосборника:
410452*5=2055560
.
Количество испарившейся воды в газозборнике:
=
*0,025, (17)
где – количество воды, подаваемое на орошение газосборника;
=2055560*0,025=51306,5
.
Влага шихты переведённая в килограммы в час:
=Gв*
, (18)
где - влага шихты;
=
=26664 кг/ч.
Выводимая вода из ПГХ для пополнения цикла равняется 10 %
Количество воды идущей на аммиачную установку:
,
или для нашего примера возьмём количество воды идущей на аммиачную установку равной 50 м3 в час, что является производительностью установки по технологии.
Содержание летучего аммиака в аммиачной воде:
=
, (19)
где - количество воды идущей на аммиачную установку;
– количество рабочей шихты;
=
=187
/час.
Содержание связанного аммиака аммиачной воде:
|
=
, (20)
где - количество воды идущей на аммиачную установку;
– количество рабочей шихты;
=
=222
/час.
Содержание общего аммиака в воде:
=
, (21)
где - содержание летучего аммиака;
- содержание связанного аммиака;
=222+178=400
/час.
Количество сероводорода в аммиачной воде:
=
, (22)
где - количество воды идущей на аммиачную установку;
– количество рабочей шихты;
=
=500 г/
.
Количество гидроксида натрия 100-процентного рассчитывается по уравнению по уравнению реакции:
() S
+ 2Na OH => 2N
+ N
S
,
X= =522 г/
,
=
=522 г/
100%-тный NaOH,
15кг – в 100 кг р-ра
522 – х кг р-ра,
=
=3480 кг/
час.
Количество АВП- аммиачно водяных паров находим по формуле:
=
*0,99, (23)
где - содержание общго аммиака;
=400*0,99=396.
Количество воды в аммиачном стоке:
O=
, (24)
где - количество аммиака в водяных парах;
O=
=2079
/час.
Количество аммиака в сточной воде:
GNH3= -
, (25)
где - содержание общего количества аммиака;
- количество аммиака в водяных парах;
GNH3=400-396=4 кг/ч.
Содержание аммиака в сточных водах будет ровно:
=
, (26)
где - количество аммиака в сточной воде;
- количество рабочей шихты;
- количество воды в аммиачном стоке;
=1,93 г/л, или 0,19%.
Общий материальный баланс аммиачной колонны (без учета флегмы) будет следующей, кг/ч.
Приход | Расход | ||
Аммиак | 400 | Аммиачно-водяные пары | |
Сероводород | 500 | Аммиак | 396 |
Вода | 49100 | Сероводород | 500 |
Итого | 50000 | Вода | 2079 |
Щёлочи | 3480 | Итого | 2975 |
Всего | 53480 | Всего W | (50 505) |
Тепловой расчёт колонны
Приход тепла. 1. Тепло вносимое аммиачной водой в испарительную колонну:
Q1= 50000*70=3500000 ккал/ч или 14665000 кДж, (27)
где 70 – температура поступающей воды, °С.
Тепло, вносимое раствором щёлочи:
Q2=3480* 1,47*70=358092 кДж, (28)
где 70-темпиратура поступающей щёлочи;
1,47 – теплоёмкость щёлочи в кДЖ.
Итого:
Qприх=3500000+358092=3858092 ккал/ч или 16165405,5 кДж.
Расход тепла
Тепло уносимое парами из колонны:
Q3=2079(595+0,44*106)+(396*0,508+0,24*500)=1368014 ккал/ч или кДж, (29)
где 0,44; 0,508; 0,24 – теплоёмкости паров воды, аммиака, сероводорода соответственно, ккал/(кг*град);
106 – температура выходящих паров из колонны, °С;
Q4=50505*106=5353530 ккал/ч или 22431290,7 кДж.
Итого:
Q5=5353530+1368014=6721544 ккал/ч или 28163269,4 кДж.
Тепло химической реакции:
qрасл(NH4)2S=500*182,3=91150 ккал/ч или 381918,5 кДж, (30)
где 500 – количество сероводорода;
182,3 – тепло разложения в ккал/кг (NH4)2S.
qвыд(NH3)=396*491=194436 ккал/ч или 814686,84 кДж, (31)
где 396 – количество аммиака в аммиачно водяных парах;
491 – тепло выделения в ккал/кг NH3.
qразл(H2S)=500*139,3=69650 ккал/ч или 291833,5 кДж, (32)
где 500 - количество сероводорода;
139,3 - тепло выделения в ккал/кг H2S.
Qрасх=91150+194436+69650+6721544=7076780 ккал/ч или 29651708,2 кДж.
Таким образом, необходимо сообщить тепло греющим паром:
Q=7076780-3858092=3218688 ккал/ч или 13486302,7 кДж.
Принимая потери тепла в окружающую среду равным 1% или 37000 ккал/ч или 155030 кДж, получим общий расход тепла:
3218688+37000=3255688 ккал/ч или 13641332,7 кДж.
Расход греющего пара давлением 3 ат будет равен:
=5931 кг/час, или 5,93 т/час, или 2164,45 т/год.
Вывод
В специальной части я рассчитал количество пара идущей на колонну, количество щёлочи, количество аммиачной воды.
В итоге количество щёлочи идущей на колонну равно 3480 кг/ч, количество аммиачной воды 50 м3, количество пара идущего на колонну равно 5931 кг/час, или 5,93 т/час.
|
|
История развития пистолетов-пулеметов: Предпосылкой для возникновения пистолетов-пулеметов послужила давняя тенденция тяготения винтовок...
Автоматическое растормаживание колес: Тормозные устройства колес предназначены для уменьшения длины пробега и улучшения маневрирования ВС при...
Кормораздатчик мобильный электрифицированный: схема и процесс работы устройства...
Типы сооружений для обработки осадков: Септиками называются сооружения, в которых одновременно происходят осветление сточной жидкости...
© cyberpedia.su 2017-2024 - Не является автором материалов. Исключительное право сохранено за автором текста.
Если вы не хотите, чтобы данный материал был у нас на сайте, перейдите по ссылке: Нарушение авторских прав. Мы поможем в написании вашей работы!