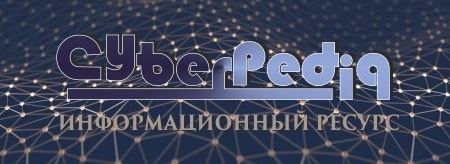
Наброски и зарисовки растений, плодов, цветов: Освоить конструктивное построение структуры дерева через зарисовки отдельных деревьев, группы деревьев...
История развития пистолетов-пулеметов: Предпосылкой для возникновения пистолетов-пулеметов послужила давняя тенденция тяготения винтовок...
Топ:
Когда производится ограждение поезда, остановившегося на перегоне: Во всех случаях немедленно должно быть ограждено место препятствия для движения поездов на смежном пути двухпутного...
Интересное:
Аура как энергетическое поле: многослойную ауру человека можно представить себе подобным...
Наиболее распространенные виды рака: Раковая опухоль — это самостоятельное новообразование, которое может возникнуть и от повышенного давления...
Распространение рака на другие отдаленные от желудка органы: Характерных симптомов рака желудка не существует. Выраженные симптомы появляются, когда опухоль...
Дисциплины:
![]() |
![]() |
5.00
из
|
Заказать работу |
Введение
Цех улавливания химических продуктов №2 (ЦУХП -2) был запущен в производство в 1975 году. Назначение цеха – очистка прямого коксового газа коксового цеха - 2 (КЦ - 2) от продуктов коксования, конденсация смолы и надсмольной воды и подача очищенного (обратного) коксового газа в отопительную систему коксовых печей КЦ-2. в составе ЦПХП-2 четыре отделения:
1) машинный зал с электрофильтрами для отсоса коксового газа КЦ-2 и транспортировки его через газовую аппаратуру цеха;
2) отделение конденсации для охлаждения коксового газа, выделения из него фусов, смолы, аммиачной воды, подача аммиачной воды на орошение газосборников КЦ-2, переработка избыточной аммиачной воды на аммиачной установке;
3) сульфатное отделение с бессатураторной схемой для очистки коксового газа от аммиака с получением товарного продукта сульфата аммония;
4) бензольное отделение для выделения из коксового газа бензольных углеводородов и конечного охлаждения коксового газа перед подачей его в КЦ-2.
Цели и задачи аммиачного отделения заключались в следующем это
· установка аммиачной колонны диаметром 1400 мм из нержавеющей стали производительностью до 50 надсмольной воды в час, замена колпачковых тарелок на пенно вихревые (провальные);
· замена внутренних устройств в 2-х существующих аммиачных колоннах из нержавеющей стали диаметром 1400 мм и доведение их производительности до 50 надсмольной воды в час каждой;
· отдувка в аммиачных колоннах аммиака из избыточной надсмольной воды и выводимой циркулирующей воды закрытого цикла конечного охлаждения водяным паром;
· разложение связанных солей аммиака избыточной и циркулирующей воды (в аммиачных колоннах 15%-ным раствором щёлочи);
· подача раствора щёлочи на всас насосов, подающих избыточную воду на аммиачные колонны (насосная конденсации);
· строительство нового склада реактивов (щёлочи, ортофосфорной кислоты) с разгрузочной площадкой и навесами над резервуарами и разгрузочной площадкой с целью исключения образования загрязнённых дождевых вод;
· установка одного резервуара ёмкостью 700 , 3-х резервуаров ёмкостью по 500
каждый для избыточной надсмольной воды (общая ёмкость 2200
) и отстойника 400
Общая часть
Состав аммиачного отделения
Аммиачное отделение включает в себя следующий состав:
Ø Аппаратная А.О.
Ø Насосная А.О.
Ø Хранилище щёлочи - 2 (старое).
Ø Насосная нового склада реактивов.
Ø Разгрузочная эстакада А.О.
Ø Новый склад реактивов.
Ø Хранилище смолы.
Ø Аммиачные колонны.
Контроль технологического режима в отделении
Назначение, виды контроля
На участке очищения избыточной аммиачной воды от аммиака осуществляется операционный контроль технологического режима цеховым персоналом. Входной контроль аммиака осуществляется на участке аммиачного отделения. Приемочный контроль щёлочи осуществляется так же на участке аммиачного отделения.
Таблица 3 – Виды контроля
Виды контроля | Назначение (что контролируется | Ответственность | Примечание |
Входной | Аммиак | Лаборант | См.таб.-3 |
Операционный | См.таб.-4 | - | - |
Приемочный | Щелочь | Аппаратчик А.О. | Конц. 48% |
Специальная часть
Расчёт шихты на коксование
Объём кокса килограмм в час:
Vкг= кг/ч.
Выход сухого кокса в кг/ч:
G=337968*0,94=317690 кг/ч.
Выход сухой шихты в кг/ч:
G= =410452кг/ч.
1 Влага шихты переведённая в килограммы в час по формуле
=Gв*
, (1)
где - влага шихты;
=
=26664 кг/ч.
Приходная часть
1. Сухая шихта. Загружаемую в камеру коксования сухую шихту подсчитывают по формуле
=
, (2)
где – количество рабочей шихты;
=
.
2. Влага шихты. Загружаемую в камеру коксования влагу вместе с шихтой подсчитываем по формуле:
G , (3)
где - количество рабочей шихты;
– влага шихты;
.
Расходная часть
Кокс валовый. Под коксом валовым понимается сумма крупного кокса, коксового орешка, коксовой мелочи,получаемых при сортировке рядового кокса, а так-же коксовый шлам, улавливаемый в отстойниках башен тушения.
Выход сухого кокса валового из сухой шихты подсчитываем по формуле:
G =
,
G *100+а, (4)
где –выход летучих веществ шихты на сухую массу, %. Для нашего примера – 26,6%;
– выход летучих веществ кокса валового на сухую зольную массу, %. Обычно принимается за 1,0%;
a – поправка (разница) на выход кокса, получаемого в производственных условиях и при определении выхода летучих веществ в лабораторных условиях, %.
Поправку а, часто называемую припеком, находят по следующей формуле, предложенной Г. П. Гейдом и А. Я. Обуховским:
а = *
, (5)
где – коэффициент пиролиза, зависящий при равномерном температурном режиме коксования от выхода летучих веществ
и определяемый с помощью графика (для донецких углей);
а =0,123*26,6=3,3%,
Тогда:
G *100+3,3=77,4%.
Выход сухого кокса валового на рабочую шихту пересчитываем по формуле:
G =G
*
, (6)
где G - выход сухого кокса валового из сухой шихты;
- влага шихты;
G =77,4*
73,7%.
Коксовый газ обратный (сухой). Выход коксового газа обратного (сухого)из сухой шихты подсчитываем по эмпирической формуле Я. О. Габинского:
G К
, (7)
где К-эмпирический коэффициент, уточнённый на кафедре ХТТ ДМетИ. Находиться в приделах 2,54-2,99 в зависимости от марочного состава шихты и режима коксования:
- выход летучих веществ шихты на сухую массу, %. Для нашего примера – 26,6%;
G 2
.
Пересчитываем выход сухого газа на рабочую шихту:
G = G
*
, (8)
где G - выход коксового газа обратного (сухого)из сухой шихты;
- влага шихты:
G =
*
.
Смола безводная. Выход смолы безводной из сухой шихты подсчитываем по эмпирической формуле С. Г. Аронова и Р. Л. Мишулович:
G =(-18,36+1,53
-0,026
, (9)
где -эмпирический коэффициент, уточнённый на кафедре ХТТ ДМетИ. Находиться в приделах 0,80-0,86 в зависимости от марочного состава шихты и режима коксования:
G =(-18,36+1,53*28,1-0,026
.
Пересчитываем выход безводной шихты на рабочую шихту по формуле:
G = G
*
, (10)
где G - выход смолы безводной из сухой шихты;
- влага шихты;
G =
*
.
Сырой бензол. Выход сырого бензола (бензольных углеводородов до 180ºС) из сухой шихты подсчитываем по эмпирической формуле С. Г. Аронова и Р. Л. Мишулович:
G =(-1,61+0,144
-0,0016
, (11)
где -эмпирический коэффициент, уточнённый на кафедре ХТТ ДМетИ. Находиться в приделах 0,84-0,97 в зависимости от марочного состава шихты и режима коксования;
G =(-1,61+0,144
-0,0016
.
Пересчитываем выход бензола на рабочую шихту по формуле:
G = G
*
, (12)
где G - выход сырого бензола (бензольных углеводородов до 180ºС) из сухой шихты;
- влага шихты;
G = 1,1*
.
Аммиак 100% - ный. Выход аммиака 100%-ного из рабочей шихты подсчитываем по формуле:
G , (13)
где в приделах 0,11-0,14;
G .
Сера в пересчёте на сероводород. Выход серы в пересчёте на сероводород из рабочей шихты подсчитываем по формуле:
G =
*
, (14)
где -коэффициент перехода серы шихты в сероводород, который находиться в приделах 0,17-0,29. Принимаем – молекулярный вес сероводорода; 32- атомный вес серы;
– содержание серы в рабочей шихте, %. Для нашего примера – 0,60;
G =
*
=0,15.
Влага шихты. Влагу шихты, испаряющейся в камере коксования, подсчитываем по формуле:
G , (15)
где – влага шихты;
– количество рабочей шихты;
.
Пирогенетическая вода. Выход пирогенетической воды изи рабочей шихты подсчитываем по формуле:
=
*
*
, (16)
где -коэффициент перехода кислорода шихты в пирогенетическую воду, который находиться в приделах 0,334-0,505. Для нашего примера принимаем равным 0,43; 18 – молекулярный вес воды; 16 – атомный вес кислорода;
– содержание кислорода в рабочей шихте, %. Для нашего примера – 4,96;
=0,43*4,96*
.
Невязка баланса. Находим по разности между приходной и расходной частями:
1000-(739,0+131,0+31,5+10,0+2,8+1,5+61,0+24)=1,2 кг; т.е. 0,12%.
Невязка баланса считается допустимой до 0,5%.
Для действующего завода невязка баланса является потерями производства. Чтобы эти потери были минимальными, необходимо выявить причины невязки баланса и устранять их.
Таблица 6 Сводный материальный баланс коксования угольной шихты
Приходная часть | Расходная часть | ||||||
Название статьи | Вес, кг | Процентный состав | Название статьи | Вес, кг | Процентный состав | ||
На рабочую шихту | На сухую шихту | На рабочую шихту | На сухую шихту | ||||
1. Сухая шихта | ![]() | ![]() | 100,0 | 1. Кокс валовый | 737,0 | 73,70 | 77,40 |
2. Влага шихты | ![]() | 6,1 | - | 2. Коксовый газ | 57262 | 13,10 | 13,13 |
3. Смола безводная | 13988 | 3,15 | 3,35 | ||||
4. Сырой бензол | 4371 | 1,00 | 1,10 | ||||
5. Аммиак 100%-ный | 1311 | 0,28 | 0,31 | ||||
6. Сера в пересчёте на Н2S | 874 | 0,15 | 0,20 | ||||
7. Влага шихты | 26664 | 6,1 | 6,31 | ||||
8. Пирогенетическая влага | 874 | 0,24 | 0,26 | ||||
9. Невязка баланса | 437 | 0,12 | 0,14 | ||||
Итого | 437116 | 100,0 | 100,0 | Итого | 100,0 | 100,0 |
Расчет аммиачной колонны
Дистилляционная колонна для переработки надсмольной воды аммиачной воды.
Назначение и конструкция колонны.
Дистилляционная колонна представляет собой непрерывно действующий аппарат, служащий для выделения аммиака из надсмольной воды с помощью водяного пара. При этом летучий аммиак выделяется в испарительной колонне, а связанный аммиак после его разложения выделяется так-же в колонне.
В настоящее время применяют различные конструкции аммиачных колонн, отличающихся взаимным расположением расстоянием между тарелками, типами тарелок и колпачков и другими конструктивными элементами.
Обычно испарительная колонна состоит из чугунных царг, к которым крепятся чугунные тарелки с переливными устройствами различных конструкций. Царги устанавливают одна на другую и соединяют болтами на уплотняющих прокладках.
Нормально колонны работают на отработанном паре от паровых турбин, а свежий пар подводиться как резерв.
Расчёт подачи надсмольной воды на колонну:
Количество воды, подаваемое на орошение газосборника:
410452*5=2055560
.
Количество испарившейся воды в газозборнике:
=
*0,025, (17)
где – количество воды, подаваемое на орошение газосборника;
=2055560*0,025=51306,5
.
Влага шихты переведённая в килограммы в час:
=Gв*
, (18)
где - влага шихты;
=
=26664 кг/ч.
Выводимая вода из ПГХ для пополнения цикла равняется 10 %
Количество воды идущей на аммиачную установку:
,
или для нашего примера возьмём количество воды идущей на аммиачную установку равной 50 м3 в час, что является производительностью установки по технологии.
Содержание летучего аммиака в аммиачной воде:
=
, (19)
где - количество воды идущей на аммиачную установку;
– количество рабочей шихты;
=
=187
/час.
Содержание связанного аммиака аммиачной воде:
=
, (20)
где - количество воды идущей на аммиачную установку;
– количество рабочей шихты;
=
=222
/час.
Содержание общего аммиака в воде:
=
, (21)
где - содержание летучего аммиака;
- содержание связанного аммиака;
=222+178=400
/час.
Количество сероводорода в аммиачной воде:
=
, (22)
где - количество воды идущей на аммиачную установку;
– количество рабочей шихты;
=
=500 г/
.
Количество гидроксида натрия 100-процентного рассчитывается по уравнению по уравнению реакции:
() S
+ 2Na OH => 2N
+ N
S
,
X= =522 г/
,
=
=522 г/
100%-тный NaOH,
15кг – в 100 кг р-ра
522 – х кг р-ра,
=
=3480 кг/
час.
Количество АВП- аммиачно водяных паров находим по формуле:
=
*0,99, (23)
где - содержание общго аммиака;
=400*0,99=396.
Количество воды в аммиачном стоке:
O=
, (24)
где - количество аммиака в водяных парах;
O=
=2079
/час.
Количество аммиака в сточной воде:
GNH3= -
, (25)
где - содержание общего количества аммиака;
- количество аммиака в водяных парах;
GNH3=400-396=4 кг/ч.
Содержание аммиака в сточных водах будет ровно:
=
, (26)
где - количество аммиака в сточной воде;
- количество рабочей шихты;
- количество воды в аммиачном стоке;
=1,93 г/л, или 0,19%.
Общий материальный баланс аммиачной колонны (без учета флегмы) будет следующей, кг/ч.
Приход | Расход | ||
Аммиак | 400 | Аммиачно-водяные пары | |
Сероводород | 500 | Аммиак | 396 |
Вода | 49100 | Сероводород | 500 |
Итого | 50000 | Вода | 2079 |
Щёлочи | 3480 | Итого | 2975 |
Всего | 53480 | Всего W | (50 505) |
Тепловой расчёт колонны
Приход тепла. 1. Тепло вносимое аммиачной водой в испарительную колонну:
Q1= 50000*70=3500000 ккал/ч или 14665000 кДж, (27)
где 70 – температура поступающей воды, °С.
Тепло, вносимое раствором щёлочи:
Q2=3480* 1,47*70=358092 кДж, (28)
где 70-темпиратура поступающей щёлочи;
1,47 – теплоёмкость щёлочи в кДЖ.
Итого:
Qприх=3500000+358092=3858092 ккал/ч или 16165405,5 кДж.
Расход тепла
Тепло уносимое парами из колонны:
Q3=2079(595+0,44*106)+(396*0,508+0,24*500)=1368014 ккал/ч или кДж, (29)
где 0,44; 0,508; 0,24 – теплоёмкости паров воды, аммиака, сероводорода соответственно, ккал/(кг*град);
106 – температура выходящих паров из колонны, °С;
Q4=50505*106=5353530 ккал/ч или 22431290,7 кДж.
Итого:
Q5=5353530+1368014=6721544 ккал/ч или 28163269,4 кДж.
Тепло химической реакции:
qрасл(NH4)2S=500*182,3=91150 ккал/ч или 381918,5 кДж, (30)
где 500 – количество сероводорода;
182,3 – тепло разложения в ккал/кг (NH4)2S.
qвыд(NH3)=396*491=194436 ккал/ч или 814686,84 кДж, (31)
где 396 – количество аммиака в аммиачно водяных парах;
491 – тепло выделения в ккал/кг NH3.
qразл(H2S)=500*139,3=69650 ккал/ч или 291833,5 кДж, (32)
где 500 - количество сероводорода;
139,3 - тепло выделения в ккал/кг H2S.
Qрасх=91150+194436+69650+6721544=7076780 ккал/ч или 29651708,2 кДж.
Таким образом, необходимо сообщить тепло греющим паром:
Q=7076780-3858092=3218688 ккал/ч или 13486302,7 кДж.
Принимая потери тепла в окружающую среду равным 1% или 37000 ккал/ч или 155030 кДж, получим общий расход тепла:
3218688+37000=3255688 ккал/ч или 13641332,7 кДж.
Расход греющего пара давлением 3 ат будет равен:
=5931 кг/час, или 5,93 т/час, или 2164,45 т/год.
Вывод
В специальной части я рассчитал количество пара идущей на колонну, количество щёлочи, количество аммиачной воды.
В итоге количество щёлочи идущей на колонну равно 3480 кг/ч, количество аммиачной воды 50 м3, количество пара идущего на колонну равно 5931 кг/час, или 5,93 т/час.
Спецификация оборудования
Таблица 8- спецификация оборудования
Наименование оборудования, материалов при проектировании | Строительные работы | Монтажные работы | Стоимость оборудования | Общая стоимость, млн. руб |
Аммиачная колонна | 5,616 | 5,025 | 21,032 | 31,673 |
В том числе | - | - | - | - |
Строительные работы | 2,363 | - | - | 2,363 |
Отопление и вентиляция | 0,335 | 0,017 | 0,06 | 0,412 |
электроосвещение | - | 0,41 | - | 0,41 |
Технологическое оборудование | 2,511 | 1,704 | 18,368 | 22,573 |
электрооборудование | - | 0,392 | 1,385 | 1,777 |
КИП и АСУ | 0,407 | 2,502 | 1,229 | 4,138 |
Экономика производства
Обоснование мероприятия
Внедрение АУ направлено на повышение качества очистки и производительности аммиачной установки, что позволит повысить расход очищенной аммиачной воды в процессе орошения и увеличить производительность по охлаждению коксового газа.
Аммиачная установка с высокой производительностью позволит повысить объём очищаемой воды.
Аммиачная установка дает возможность значительно повысить технико-экономические показатели разложения аммиака и химических предприятий, а также улучшить условия труда в химических цехах.
В проекте предлагается аммиачная установка, состоящая из трёх колонн 50м3 в час, что позволит очистить наибольший объём воды.
4.2 Выбор методики оценки эффективности
При оценке эффективности внедрения аммиачной установки для цеха переработки отходов химического производства КАДП ПАО «Северсталь»целесообразно использовать традиционный метод абсолютной эффективности без учета фактора времени.
Этот метод предполагает:
· расчет капитальных затрат на проведение инновационного мероприятия,
· расчет годовой экономии,
· расчет годового экономического эффекта,
· расчет срока окупаемости капитальных затрат,
· расчет экономической эффективности капиталовложений.
4.3 Оценка эффективности
К капитальным вложениям относятся затраты:
- на приобретение, доставку, монтаж, демонтаж, техническую подготовку, наладку и освоение производства;
- на пополнение оборотных фондов, связанных с использованием мероприятия;
- на необходимые производственные площади и другие элементы основных фондов, непосредственно связанных с использованием мероприятия.
Затраты на приобретение и монтаж оборудования можно найти по формуле:
Кпмо=Цо×(1+ктр+км+кф), (1)
где Кпмо – затраты на приобретение и монтаж оборудования, руб;
Цо – цена приобретаемого оборудования, руб;
ктр – коэффициент транспортно–заготовительных расходов;
км – коэффициент, учитывающий затраты на монтаж и освоение;
кф – коэффициент, учитывающий затраты на сооружение фундамента.
Коэффициент транспортно–заготовительных расходов принимается от 0,05 до 0,08. Коэффициент монтажа и освоения принимается от 0,06 до 0,15. Коэффициент на сооружение фундамента от 0,03 до 0,15.
В данной курсовой работе коэффициент транспортно–заготовительных расходов - 0,08, коэффициент монтажа и освоения -0,1. коэффициент на сооружение фундамента - 0,15. В результате капитальные затраты составят:
Кпмо= 20372504,7×(1+0,05+0,06+0,15) = 25669355,90 руб.
Стоимость пара получаемого на установке сухого тушения определяется по формуле:
Впар = (Упар×Вгк× Ц) / 1000, (2)
где Впар - стоимость пара, тыс. руб/ год;
Упар - производительность по пару кг/ т.
Вгк - производительность по надсмольной воде в год т/ год.
Ц - цена пара руб./ кг.
Впар= (57,7×438000×0,535) / 1000 = 13520,84тыс. руб/ год
Расчет годовой экономии по сырью, материалам, топливу, энергии и стороны производится по формуле:
Эг= DВк + Впар, (3)
где Эг- годовая экономия, тыс.руб/ год;
Эг=165454,5 + 13520,84 =178975,34тыс. руб./ год.
Экономическая эффективность рассчитывается по формуле:
Е= , (4)
где Эф- годовая экономия, тыс.руб/ год;
Кпмо - капитальные затраты;
Е= =0,007тыс.руб,
Срок окупаемости рассчитывается по формуле:
Ток= ; (5)
где Эг- годовая экономия, тыс.руб/ год;
Кпмо - капитальные затраты;
Ток= =143.4;
Вывод
В данном расчёте была определена экономическая эффективность внедрения аммиачного отделения. Для этого были рассчитаны капитальные затраты, стоимость пара, годовая экономия, срок окупаемости и экономическая эффективность отделения. В предлагаемом проекте срок окупаемости затрат на внедрение аммиачного отделения составляет 143.4 года. Экономическая эффективность составляет 0,007тыс.руб, что указывает на экономическую не целесообразность внедрения проекта. Этот показатель не превышает нормативный 0,2.
Требования охраны окружающей среды
1
2
3
4
5
6
7
8
Воздушный бассейн.
Источниками выделения загрязняющих веществ в атмосферу в процессе очистки избыточной аммиачной воды от аммиака в цехе переработки химических продуктов -2 коксоаглодоменного производства являются воздушники емкостного оборудования.
Нормативы выбросов от источников аммиачного отделения цеха переработки химических продуктов-2 КАДП (производство кокса) отражены в «Проекте нормативов ПДВ вредных веществ в атмосферу для «ОАО Северсталь»».
В период действия неблагоприятных метеорологических условий запрещается проводить плановые ремонты и пропарочные работы, связанные с дополнительным выбросом загрязняющих веществ в атмосферу.
Водный бассейн.
В технологическом процессе очистки избыточной аммиачной воды от аммиака образуется до 90 м3/ч воды, которая поступает для дальнейшей очистки на биохимическую установку КАДП (производство кокса).
Требования к качеству воды, разрешенной для сброса в фенольную канализацию, приведены в таблице 9 настоящей ТИ.
Таблица 9- Требования к качеству воды, разрешенной для сброса в фенольную канализацию
Наименование стока | Объём стока, не более, м3/ч | Качественные показатели | ||||||
рН | Массовая концентрация, не более, мг/дм³ | ХПК, мгО2/дм³ | ||||||
Фосфор | фенолы | аммиак общего | роданиды | общие масла | ||||
Аммиачный сток ЦПХП - 2 | 90 | 7-9 | 5 | 1 100 | 300 | 450 | 70 | 4 000 |
Отходы.
В процессе очистки избыточных надсмольных вод от аммиака и при техническом обслуживании, эксплуатации и ремонтах оборудования аммиачного отделения цеха переработки химических продуктов - 2 КАДП (производство кокса) образуются следующие виды отходов:
Лампы ртутные, ртутно-кварцевые, люминесцентные, утратившие потребительские свойства. Класс опасности – I. Образуется при эксплуатации электроосветительных приборов. Собираются в металлическую емкость, установленную в специальном закрытом помещении. Передаются для обезвреживания в специализированную организацию по договору. Первичный учет образования и передачи ведется в Журнале образования и передачи отходов ответственными лицами, назначенными совместным распоряжением директора по производству чугуна и начальника сервисного производства по чугуну.
Шлак сварочный. Класс опасности – IV. Образуется при производстве сварочных работ. Собирается и накапливается в смеси с другими производственными отходами в металлических контейнерах, установленных на территории ЦПХП-2. По мере накопления вывозится автотранспортом на полигон промышленных отходов управления транспорта. Первичный учет ведется в Журнале учета образования и передачи отходов, ответственным лицом, назначенным распоряжением директора по производству чугуна.
Электробезопасность
Электротехнические установки отделения очистки избыточной аммиачной воды от аммиака должны эксплуатироваться в соответствии с ПТЭ.
Электродвигатели открытого типа устанавливают только в помещениях без повышенной опасности. В сырых, пыльных, опасных по взрыву или пожару помещениях.
К устройству электрических сетей тоже повышенные требования. Их надлежит выполнять из изолированных проводов, защитные оболочки которых по механической прочности и п
Организация стока поверхностных вод: Наибольшее количество влаги на земном шаре испаряется с поверхности морей и океанов (88‰)...
Адаптации растений и животных к жизни в горах: Большое значение для жизни организмов в горах имеют степень расчленения, крутизна и экспозиционные различия склонов...
Наброски и зарисовки растений, плодов, цветов: Освоить конструктивное построение структуры дерева через зарисовки отдельных деревьев, группы деревьев...
История развития хранилищ для нефти: Первые склады нефти появились в XVII веке. Они представляли собой землянные ямы-амбара глубиной 4…5 м...
© cyberpedia.su 2017-2024 - Не является автором материалов. Исключительное право сохранено за автором текста.
Если вы не хотите, чтобы данный материал был у нас на сайте, перейдите по ссылке: Нарушение авторских прав. Мы поможем в написании вашей работы!