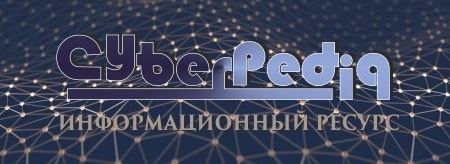
Состав сооружений: решетки и песколовки: Решетки – это первое устройство в схеме очистных сооружений. Они представляют...
Опора деревянной одностоечной и способы укрепление угловых опор: Опоры ВЛ - конструкции, предназначенные для поддерживания проводов на необходимой высоте над землей, водой...
Топ:
Проблема типологии научных революций: Глобальные научные революции и типы научной рациональности...
Оценка эффективности инструментов коммуникационной политики: Внешние коммуникации - обмен информацией между организацией и её внешней средой...
Интересное:
Лечение прогрессирующих форм рака: Одним из наиболее важных достижений экспериментальной химиотерапии опухолей, начатой в 60-х и реализованной в 70-х годах, является...
Национальное богатство страны и его составляющие: для оценки элементов национального богатства используются...
Что нужно делать при лейкемии: Прежде всего, необходимо выяснить, не страдаете ли вы каким-либо душевным недугом...
Дисциплины:
![]() |
![]() |
5.00
из
|
Заказать работу |
|
|
При использовании для изоляции труб композиций гранулированного полиэтилена применяют экструзионно-намоточный способ и способ непрерывной экструзии «чулком». Для труб диаметром более 600 мм пригоден первый способ, а для труб меньшего диаметра - способ непрерывной экструзии «чулком».
При экструзии используют гранулированный полиэтилен высокого и низкого давления и его сополимеры. При этом в конструкции покрытия обязательно предусматривается подклеивающий слой (адгезив). В качестве адгезива могут применяться сополимеры этилена с эфирами акриловой кислоты, сополимер этилена с винилацетатом (жесткие адгезивы), а также композиции на основе бутилкаучука (мягкий адгезив).
Для нанесения основного слоя покрытия может быть использован термо-светостабилизированный полиэтилен высокого давления (низкой плотности).
Электрические показатели композиций полиэтилена высокого давления:
Удельное объемное электрическое сопротивление, Ом×см | 1 × 1016 – 1 × 1017 |
Удельное поверхностное электрическое сопротивление, Ом | 1015 |
Тангенс угла диэлектрических потерь при частоте 1010 Гц | 0,0002 – 0,0005 |
Диэлектрическая проницаемость при частоте 1010 Гц | 2,25 – 2,31 |
Для особо стойкой противокоррозионной защиты наносится трехслойное покрытие. В качестве первого слоя наносится слой эпоксидной смолы. В качестве второго слоя, методом экструзии, наносится полиэтилен, который соединяется со слоем эпоксидной смолы при помощи специального клея. Этот материал может применяться при рабочих температурах до 800С и наружной температуре до – 400С.
Преимуществом многослойного покрытия является то, что оно не сдвигается на поверхности стали, что имеет существенное значение для эксплуатируемых трубопроводов или для трубопроводов, еще не засыпанных землей, и позволяет нанести на область кольцевых швов высококачественное покрытие, особенно при высоких колебаниях температуры.
|
Наряду с вышеперечисленными преимуществами отмечается так же высокая противоударная прочность, прочность на сжатие и отслаивание. Опыт строителей трубопроводов свидетельствует о том, что высокая сопротивляемость ПЭ - покрытий почти полностью исключает механические повреждения во время транспортировки, хранения и укладки, при условии соответствующего отношения к ним.
В табл. 2.1 приводятся предъявляемые требования и виды контроля, которым подлежит заводское покрытие.
Таблица 2.1
Контроль и требования к покрытиям стальных труб
Для подземных трубопроводов
От трубы к трубопроводу | Контроль и требование |
Изготовление | Контроль сырья, заключительный контроль покрытия на пористость, толщину слоя, адгезию, твердость, прочность, растяжение |
Транспорт | Противоударная прочность и прочность на сжатие, адгезия, износостойкость |
Хранение | Противоударная прочность и прочность на сжатие, адгезия, износостойкость, стойкость к ультрафиолетовому облучению |
Прокладка | Противоударная прочность и прочность на сжатие, адгезия, износ |
Эксплуатация | Противоударная стойкость, стойкость против старения, стойкость к окружающему грунту, противогрибковая и противобактериальная стойкость, большое переходное сопротивление, стойкость относительно проникновения воды в местах повреждения, а также в случае необходимости тепло- и морозоустойчивость |
Изоляция труб методом экструзии предусматривает следующую последовательность технологических операций. Трубы по рольгангу поступают в сушильную печь для удаления с их поверхности влаги, снега, инея, наледи и далее в камеру дробеметной очистки. Трубы очищают так же, как и перед нанесением на поверхность покрытия из порошкообразного полиэтилена.
|
Трубы большого диаметра нагревают в газопламенной печи до 2200С. При изоляции труб диаметром менее 600 мм для нагрева используют высокочастотные индукторы.
При нанесении полиэтиленового покрытия экструзионно-намоточным способом на трубу, совершающую равномерное вращательно-поступательное движение, из экструдера через щелевую головку поступает лента клеевого слоя (адгезива) толщиной 0,15 - 0,2 мм и шириной 200 - 250 мм. На этой же позиции поверх клеевого слоя из другого экструдера также через щелевую головку наносится в несколько слоев основное покрытие из свето- и термостабилизированного полиэтилена. Существуют конструкции устройств нанесения полиэтиленовой изоляции методом экструдирования, в которых напыляется слой эпоксидной смолы как клеевая основа.
Температура изоляционных материалов на выходе из щелевых головок экструдеров составляет 200 – 2200С. Рабочая температура выбрана таким образом, чтобы могли склеиться под давлением соответственно углу подъема намотки наносимые друг на друга внахлест слои в бесшовное, однородное покрытие, которое прочно держится на трубе. Толщина полиэтиленового покрытия регулируется кратностью нахлеста спирально наматываемой ленты из головки экструдера, что в свою очередь обусловливает частоту вращения и осевое перемещение труб (рис. 2.3).
Толщина ленты основного слоя 0,3 - 0,5 мм и ширина 600 - 650 мм.
Для получения покрытия толщиной 2,5 - 3,0 мм выполняют четырех-пятикратный нахлест ленты основного слоя. В процессе формирования изоляционного покрытия трубы вращаются с частотой 7 об/мин и перемещаются в продольном направлении со скоростью 0,5 - 1,2 м/мин. Вращение труб осуществляется за счет косорасположенных роликов рольганга.
Рис. 2.3. Принцип способа экструзионной намотки
Для уплотнения полиэтиленового покрытия используется прижимной ролик с фторопластовым покрытием, который, обжимая изоляцию, способствует соединению отдельных слоев полиэтилена и превращает его в монолитное покрытие.
Покрытие методом непрерывной экструзии «чулком» наносится с помощью наклонной кольцевой головки, питание которой обеспечивается двумя или тремя экструдерами в зависимости от диаметра труб и производительности изоляционной установки.
Температурный режим работы экструдеров и головки аналогичен экструзионно-намоточному способу. Для обеспечения оптимальных условий формирования адгезионной связи между клеевым слоем (адгезивом) и поверхностью трубы применяется вакуумирование головки.
|
После нанесения полиэтиленового покрытия его охлаждают до температуры 60 – 700С, обливая трубы холодной водой. Далее охлажденные трубы поступают на пост контроля для проверки сплошности, толщины и адгезии покрытия.
Трубы с полиэтиленовым покрытием можно гнуть холодным способом.
Эпоксидные покрытия
Из термореактивных материалов (эпоксидных, фенольных, полиэфирных, полиакрилатных и др.) широкое применение для изоляции труб нашли эпоксидные.
Основные требования к защитным покрытиям на основе эпоксидных порошковых красок:
Толщина, мм | 0,25 – 0,50 |
Диэлектрическая сплошность при напряжении, кВ | 2,0 |
Прочность при ударе, Дж, не менее | 7,5 |
Переходное электросопротивление, Ом×м2, не менее: после нанесения защитных покрытий на законченных строительством и засыпанных участках сооружений | 1,0 × 107 5,0 × 104 |
Максимальная температура эксплуатации (температура транспортируемого продукта), 0С | 80 |
Эпоксидные порошковые краски представляют собой смесь эпоксидной смолы, отвердителя, ускорителя, пигмента, наполнителя, тиксотропных и поверхностно-активных добавок. Для получения порошков используют эпоксидные смолы с температурой плавления 95 – 1100С. В качестве отвердителя применяют дициандиамид, гидразин, метилтетрагидрофталевый ангидрид. Наполнителем может служить сульфат бария. В качестве пигментов применяют окислы титана, хрома, железа.
К преимуществам эпоксидных покрытий относятся высокая адгезионная прочность, стойкость к воздействию повышенных температур, низкая кислородопроницаемость. Их можно наносить без предварительного грунтования поверхности металла.
Порошковые эпоксидные краски наносят на трубы методом пневматического напыления как с применением электростатического поля так и без него.
Покрытия наносят на тщательно очищенную от всех загрязнений поверхность труб, нагретую до 220 – 2300С. Порошок напыляют на вращающуюся трубу через специальные распылители, при этом труба перемещается, вдоль распылителей со скоростью 0,8 - 1,2 м/мин. Далее труба с напылен-ным покрытием поступает в камеру полимеризации, где происходит отверждение изоляционного покрытия. Время отверждения при температуре 2000С составляет 20 - 30 мин. После камеры полимеризации изолированные трубы обдуваются воздухом и, охлажденные до комнатной температуры, поступают на пост контроля, где проверяют сплошность, толщину и ударную прочность изоляции.
|
Эмаль-этинолевое покрытие
Применяемая для изготовления защитных покрытий труб и емкостей эмаль этиноль представляет однородную массу, состоящую из пленкообразующего материала — лака этиноль и наполнителя - хризотилового асбеста.
Для изоляции трубопроводов, прокладываемых на участках, где отсутствуют блуждающие токи, в состав эмали этиноль может быть введен литейный графит.
Плотность эмали этиноль при 200С составляет 1,65 - 1,75 г/см3.
Толщина эмали этинолевого покрытия, соответствующего весьма усиленному типу, должна быть не менее 0,6 мм. Покрытие наносится в условиях трубоизоляционных баз (мастерских).
Лак этиноль (ТУ 6-01-985-75) представляет собой однородную прозрачную жидкость коричневого цвета, являющуюся раствором полимеризованных производных ацетилена в ксилоле или ксилольной фракции. В состав лака входят стабилизаторы, древесно-смоляной антиокислитель или антиполимеризатор.
Приготовление эмали этиноль сводится к перемешиванию компонентов в специальной мешалке - диспергаторе, рассчитанном на единовременное приготовление 250 - 300 кг эмали этиноль. Диспергатор должен быть оборудован водяным охлаждением и заземлением. Частота вращения вала диспергатора должна быть 1400 - 1600 об/мин. При изготовлении эмали этиноль в диспергатор заливают лак этиноль и при непрерывном перемешивании порциями вводят асбест. В случае приготовления эмали этиноль с литейным графитом последний вводится в лак этиноль порциями одновременно с асбестом. После введения всего нормируемого количества компонентов массу продолжают перемешивать 45 мин.
Подготовка поверхности должна обеспечить полную очистку стали от продуктов коррозии, грязи, неплотно сцепленной со сталью окалины и т.д. Одновременно с очисткой поверхности металла ему следует придать оптимальную шероховатость, обеспечивающую наилучшую адгезию защитного покрытия к стали, путем дробеструйной обработки поверхности стальной или чугунной колотой дробью с размером частиц 0,6 - 0,8 мм. Для дробеструйной очистки труб могут быть использованы двухкамерные аппараты напорного действия или инжекционные дробеструйные установки.
|
Эмаль этиноль наносится на трубы трехвалковым механизмом в режиме обратной ротации, при котором совпадают направления вращения изолируемой трубы наносящего и подающего валков. Трехвалковый механизм состоит из подающего, калибрующего и наносящего валков, смонтированных в емкости для эмали этиноль и приводимых в действие одним электродвигателем.
Механизм установлен на каретке, передвигающейся под действием пневмоцилиндра в направлении, перпендикулярном к оси трубы.
Каретка со всем наносящим устройством монтируется на тележке, передвигающейся по рельсам параллельно оси вращаемой изолируемой трубы.
Трубы и емкости с нанесенными эмаль-этинолевыми защитными покрытиями могут оставаться на складе не менее 120 ч, в течение которых происходит сушка покрытий.
Стеклоэмалевые покрытия
Стеклоэмалевые покрытия обладают высоким сопротивлением на истирание, устойчивы к воздействию различных агрессивных сред, к почвенной коррозии и высоким температурам. Их рекомендуется применять на горячих участках нефте- и газопроводов. Стеклоэмалевые покрытия толщиной 0,5 - 0,6 мм допускается эксплуатировать при температурах транспортируемого по трубопроводу продукта до + 3000С. Термическая стойкость эмалей 220 - 2900С.
Стеклоэмалевое покрытие состоит из одного слоя грунтовой и трех слоев покровной эмали.
Технология индукционного эмалирования труб заключается в следующем. Чтобы удалить с поверхности органические загрязнения, трубы обжигают в печи при температуре 400 – 6500С, затем очищают от ржавчины, окалины на дробеструйных установках.
На очищенную поверхность трубы наносят эмалевый шликер методом распыления или окунанием в шликерную ванну.
Сушка и обжиг нанесенного шликера осуществляются индукционным способом на роторном стане. Толщина одного слоя эмали не превышает
150 мкм. Сушат покрытие при температуре 95 – 1100С.
Температура обжига эмали зависит от ее состава. После нанесения и обжига каждого слоя эмали контролируют качество покрытия.
Номенклатура материалов,
|
|
Общие условия выбора системы дренажа: Система дренажа выбирается в зависимости от характера защищаемого...
Поперечные профили набережных и береговой полосы: На городских территориях берегоукрепление проектируют с учетом технических и экономических требований, но особое значение придают эстетическим...
Таксономические единицы (категории) растений: Каждая система классификации состоит из определённых соподчиненных друг другу...
История развития пистолетов-пулеметов: Предпосылкой для возникновения пистолетов-пулеметов послужила давняя тенденция тяготения винтовок...
© cyberpedia.su 2017-2024 - Не является автором материалов. Исключительное право сохранено за автором текста.
Если вы не хотите, чтобы данный материал был у нас на сайте, перейдите по ссылке: Нарушение авторских прав. Мы поможем в написании вашей работы!