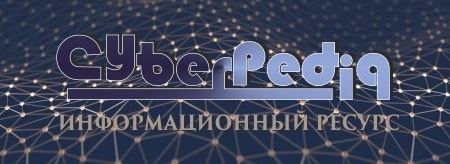
Эмиссия газов от очистных сооружений канализации: В последние годы внимание мирового сообщества сосредоточено на экологических проблемах...
Наброски и зарисовки растений, плодов, цветов: Освоить конструктивное построение структуры дерева через зарисовки отдельных деревьев, группы деревьев...
Топ:
Отражение на счетах бухгалтерского учета процесса приобретения: Процесс заготовления представляет систему экономических событий, включающих приобретение организацией у поставщиков сырья...
Определение места расположения распределительного центра: Фирма реализует продукцию на рынках сбыта и имеет постоянных поставщиков в разных регионах. Увеличение объема продаж...
Установка замедленного коксования: Чем выше температура и ниже давление, тем место разрыва углеродной цепи всё больше смещается к её концу и значительно возрастает...
Интересное:
Уполаживание и террасирование склонов: Если глубина оврага более 5 м необходимо устройство берм. Варианты использования оврагов для градостроительных целей...
Принципы управления денежными потоками: одним из методов контроля за состоянием денежной наличности является...
Подходы к решению темы фильма: Существует три основных типа исторического фильма, имеющих между собой много общего...
Дисциплины:
![]() |
![]() |
5.00
из
|
Заказать работу |
|
|
Задача пассивной защиты от коррозии состоит в устранении взаимодействия агрессивного раствора электролита и стальной поверхности. Чтобы достичь данного эффекта между грунтом или раствором электролита и поверхностью металла трубы, на трубопровод наносятся электрически изолирующие защитные покрытия. Комбинация пассивных средств с активным средством катодной защиты, представляет собой оптимальное решение с технико-экономической точки зрения (рис. 2.1).
Рис. 2.1. Меры защиты от коррозии
Покрытия металлических трубопроводов, защищающих их от коррозии, должны удовлетворять следующим основным требованиям:
- обладать высокими диэлектрическими свойствами;
- быть сплошными;
- иметь хорошую адгезию к металлу трубопровода;
- обладать низкой влагопроницаемостью и малой величиной влагопоглощения;
- химической способностью, обеспечивающей длительную работу покрытия в условиях наиболее агрессивных грунтов, то есть противостоять проникновению хлоридов, сульфатов и других ионов;
- обладать высокой механической прочностью;
- термостойкостью;
- материалы и конструкция покрытий должны иметь сравнительно простую технологию процесса нанесения, допускающую возможность механизации;
- экономичностью, то есть стоимость покрытия должна быть во много раз меньше стоимости сооружения.
Рис. 2.2. Системы покрытий, наносимых в заводских условиях:
1 – внутреннее покрытие на основе эпоксидной смолы;
2 – струйнообработанная поверхность трубы;
3 – трехслойная система из полиэтилена;
4 - трехслойная система из полиропилена;
5 – покрытие из порошковой эпоксидной смолы;
6 – полиуретан; 7 – сплавленный полиэтилен;
|
8 – механическая защита волоконноцеменным способом
Нанесение защитного покрытия на подземные объекты необходимо организовать таким образом, чтобы оно выполняло свою задачу без обновления в течение многих десятилетий. Тонкие защитные слои, как например, системы покрытий из краски с толщиной слоя менее 300 мкм в целом не подходят для пассивной защиты трубопроводов из-за активного процесса диффундирования кислорода и водяного пара. В настоящее время преимущественно применяются покрытия из полиэтилена, а также покрытия из пропилена, эпоксидного порошка и полиуретана (рис. 2.2). Для нанесения покрытия в трассовых условиях применяются защитные ленты и термоусаживающиеся материалы.
Защитное покрытие для труб можно подразделить в зависимости от назначения и, следовательно, способа изготовления на следующие группы:
- заводское покрытие;
- покрытие, наносимое в трассовых условиях;
- материалы для механического усиления обычного покрытия.
Битумные покрытия
Для защиты трубопроводов от коррозии применяются битумы. Битумы получают окислением остаточных продуктов прямой перегонки нефти или их смесей с асфальтами и экстрактами масляного производства. Строительные нефтяные битумы также получают окислением остаточных продуктов прямой перегонки нефти и их смесей с асфальтами и экстрактами масляного производства. Допускается получение строительных битумов и компаундированием окисленных и неокисленных указанных продуктов.
Упаковывают битум в четырехслойные бумажные мешки с внутренним покрытием, не прилипающим к битуму. Хранят битум под навесом с дощатым настилом. Запрещается применение битума загрязненного и засоренного посторонними предметами (земля, мусор и др.).
Наполнители
Для изменения эксплуатационных характеристик битума используют наполнители. Наполнителями называют материалы, вводимые в состав изоляционных мастик для придания им структурной и механической прочности. Это особенно важно при формировании покрытия методом облива на машинах. Малая вязкость мастики ограничивает возможность наращивания слоя необходимой толщины, а хрупкость при отрицательной температуре приводит к трещинообразованию. Наполнители, вводимые в битумные мастики, подразделяют на минеральные и полимерные. Мастика с минеральным наполнителем носит название битумно-минеральной, а с полимерным наполнителем - битумно-полимерной.
|
Добавка минерального наполнителя повышает прочность, теплостойкость, улучшает эластичные и пластические свойства. Введение 20% известняка в битум примерно в два раза повышает предельную вязкость. При эксплуатационных температурах увеличивается прочность и эластичность структуры мастик по сравнению с исходным битумом.
Гидрофильные поверхности частиц, минерального наполнителя образуют с асфальтогеновыми кислотами битума поверхностные химические соединения - кальциевые мыла, которые гидрофобизируют поверхности частиц наполнителя и улучшают их смачивание битумом.
Вокруг частиц наполнителя при этом образуются диффузионные структурированные оболочки битума с наибольшим значением вязкости в слое, прилегающем непосредственно к поверхности частиц, вследствие адсорбции на ней высокомолекулярных и адгезии коллоидообразующих составляющих битума. Некоторое увеличение всех реологических констант битума при объединении его с минеральным наполнителем связано с образованием вторичной коагуляционной структуры.
При большом процентном содержании (по массе) наполнителя увеличивается возможность образования прочных пространственных сеток из его частиц, разделенных тонкими прослойками - мостиками адсорбционно-упрочненной дисперсной среды битума, улучшаются и структурно-механические свойства битумно-полимерных материалов.
При введении полимеров в битуме формируется конденсационно-коагуляционная структура. Коагуляционная структура формируется вследствие ван-дер-ваальсового взаимодействия между частицами твердой фазы битума (эти связи обычно непрочные). Конденсационная сетка образуется в результате взаимодействия свободных полимерных радикалов системы (эти связи обычно прочные).
Битумно-полимерные материалы, имеющие конденсационно-коагуляционную структуру, по сравнению с битумно-минеральными материалами с коагуляционной структурой обладают большей прочностью и пластичностью при меньшей степени заполнения битума наполнителем.
|
В качестве минеральных наполнителей для битумных изоляционных мастик используют доломит, доломинизированный известняк, асфальтовый известняк, тальк, асбест.
Основными требованиями, предъявляемыми к минеральным наполнителям битумных мастик, являются тонко дисперсность, низкая влагонасыщенность, гидрофобность, устойчивость к воздействию различных агрессивных сред, способность к смачиванию битумом.
Доломит (ГОСТ 8267-75) - минерал из группы карбонатных осадочных пород, представляет собой двойную углекислую соль кальция и магния CaMg (CO 3)2. Состав наиболее распространенных доломитовых пород следующий: СаО 30,4%; MgO 21,7%; СО2 47,9% или СаСО3 54,35% и MgCO 3 45,65%.
Доломитизированный известняк (ГОСТ 8267-75) представляет собой так же, как доломит, карбонатную осадочную горную породу группы известняков, в состав которой входит менее 40% доломита. Остальное содержание составляют кальциты (СаСО3).
Химический состав чистых известняков приближается к теоретическому - составу кальцита (СаО 56%, СО2 44%). В наиболее часто встречающихся доломитизированных известняках содержание MgO достигает 17%.
Асфальтовый известняк (ГОСТ 8267-75). Природный асфальт расположен в районах неглубокого залегания или выхода на поверхность земли нефтеносных пород. Обычно он заполняет трещины и каверны в известковых породах.
Асбест состоит из смеси волокон различной длины и их агрегатов. Он образует тонкие эластичные и прочные волокна, которые легко расщепляются. Асбест получают из минерала хризотил-асбеста. Химический состав минерала хризотил-асбеста приближенно соответствует теоретической формуле 3 MgO × 2 SiO 2 × 2Н2О. Его плотность 2,5 г/см3. Асбест обладает малыми теплопроводностью и электропроводностью. Хризотиловый асбест имеет слабую кислотоустойчивость, но он щелочеустойчив. В качестве наполнителя в битумно-минеральную мастику вводят асбест хризотиловый по
ГОСТ 12871-67*.
Для получения битумно-полимерных мастик используются полидиен, атактический полипропилен, порошкообразный нестабилизированный полиэтилен и резиновая крошка.
|
Атактический полипропилен (ТУ 6-05-131-2-78) - побочный продукт полимеризации пропилена в среде тяжелого растворителя. Атактический полипропилен представляет собой аморфный каучукоподобный продукт серого цвета с высокой текучестью и предназначается для производства изоляционных битумных мастик.
По физико-химическим характеристикам атактический полипропилен должен соответствовать следующим требованиям:
Содержание летучих, %, не более | 3 |
Зольность, %, не более | 3 |
Содержание изотактического полипропилена | не регламентируется |
Посторонние примеси, инородные включения (песок, механические загрязнения) | отсутствуют |
Температура плавления (ГОСТ 4255-75), 0С | до 128 |
Низкомолекулярный полиэтилен (воск) получается при полимеризации этилена и наряду с полиэтиленом высокой плотности является отходом производства. Он представляет собой воскообразную монолитную массу от белого до серо-желтого цвета. Содержание влаги в нем не более 3% от массы; зольность не более 2,0%; содержание летучих углеводородов не более 0,5%. Температура плавления 80 - 120, температура воспламенения около 300, температура самовоспламенения около 4000С.
Полидиен (ТУ 38-103-280-75) представляет собой продукт совместной полимеризации высших диэтиленовых углеводородов (минерилена, гексадиега и др.) с этинолевыми, углеводородами (гексилен, эмилен и др.). Полидиен - прозрачная жидкость от светло-желтого до вишнево-красного цвета. Полидиены выпускаются марок А и Б в зависимости от температуры вспышки. Полидиены должны соответствовать следующим техническим требованиям:
Марка А | Марка Б | |
Плотность при 200С, г/см3 | 0,910 – 0,960 | 0,910 – 0,960 |
Температура вспышки, 0С, не ниже | 145 | 137 |
Содержание влаги, %, не более | 0,1 | 0,20 |
Каучуки, используемые в качестве наполнителя, должны соответствовать указанным свойствам. Необходимо, чтобы вводимый каучук диспергировал до коллоидной дисперсии или молекулярного раствора. Поэтому большое значение имеет эффект контактирования составляющих компонентов и вида применяемого битума, а также форма каучука, применяемая для гуммирования битума. Вводимый каучук должен растворяться в расплавленном битуме и образовывать тончайшую сетку, которая армирует битум, придавая ему упруго-пластические свойства. При введении в битум полидиена, в состав которого входят маномеры, димеры и полимеры с разной степенью полимеризации, в системе увеличивается содержание дисперсной среды, поэтому мастика становится эластичной и менее чувствительной к повышению температуры.
Дробленая резина (резиновая крошка) (ТУ 38-104-38-70) - продукт переработки изношенных автомобильных покрышек. Резиновая крошка должна отвечать следующим техническим требованиям:
|
Содержание текстиля, %, не более | 5 |
Просев через сито, %, не менее: с отверстиями диаметром 1,5 мм с отверстиями диаметром 1,0 мм | 100 96 |
Содержание влаги, %, не более | 1,5 |
Содержание черных металлов после магнитной сепарации, %, не более | 01 |
Содержание видимых посторонних включений | отсутствие |
Пластификаторы
Основное назначение пластификаторов - повышение пластичности изоляционной мастики при отрицательных температурах.
В качестве пластификаторов битумных мастик применяют зеленое и осевое масла.
Масло зеленое (ОСТ 38-01140-77) - продукт пиролиза нефтепродуктов.
Масла осевые (ГОСТ 610-72) - неочищенные смазочные масла, изготовляются из продуктов прямой перегонки нефти.
Растворители
Для приготовления битумных и полимерных грунтовок в качестве растворителей применяют бензины: неэтилированный авиационный Б-70 (ГОСТ 1012-72*); автомобильный А-72 (ГОСТ 2084-77).
Армирующие обмотки
В качестве материала для армирующих обмоток применяют стеклохолст, соответствующий основным показателям, установленным нормативно-технической документацией.
Стеклохолст должен иметь неворсистую, ровную без складок поверхность и ровно обрезанные края. На поверхности холста не допускаются жгуты. Холст не должен расслаиваться.
Наружные обертки
В качестве, материалов для наружной обертки применяют материалы, обеспечивающие гидрофобность и защиту от механических воздействий на битумное покрытие.
Грунтовки
Битумные грунтовки изготовляются из битума, растворенного в бензине в соотношении 1:3 по объему или 1:2 по массе. Составы битумных грунтовок зависят от сезона нанесения.
Для приготовления битумной грунтовки нужное количество соответствующего битума расплавляют, обезвоживают и охлаждают до 700С; затем в бак наливают необходимое количество соответствующего бензина, в который при непрерывном перемешивании деревянной лопастью вливают небольшими порциями битум. В случае если в зимний период трубы изолируют битумными мастиками в помещении с температурой не ниже – 100С на поточных линиях, оборудованных устройством сушки грунтовки, допускается применять битумную грунтовку для летнего времени.
Для приготовления каменноугольной грунтовки каменноугольную основу грунтовки расплавляют, обезвоживают и охлаждают до температуры не выше 850С. Затем в бак наливают необходимое количество толуола, в который при непрерывном перемешивании деревянной лопастью вливают небольшими порциями каменноугольную основу в соотношении 1:3 по объему.
Грунтовка считается готовой, если в ней после смешивания нет комьев основы.
Мастики битумные
Битумную мастику можно изготовлять в заводских условиях и непосредственно на трассе строящегося или ремонтируемого трубопровода в битумноплавильных установках с механическим смесителем или в передвижных котлах и на стационарных установках в условиях изоляционных баз строительно-монтажных управлений.
Битумно-резиновые мастики (ГОСТ 15836-79) готовятся в заводских условиях из обезвоженного битума и просушенной резиновой крошки путем продувки через смесь этих продуктов перегретого пара в течение 60 - 90 мин при температуре смеси 200 – 2400С (в механических смесителях). Для розлива мастики температуру понижают до 160 – 1800С. Битумно-резиновая мастика заводского производства поступает на трассу в бумажных мешках по 45 - 50 кг.
При отсутствии мастик заводского изготовления разрешается изготавливать мастики на месте производства работ. Перед загрузкой битума в котел его тщательно очищают. Для приготовления мастики битум освобождают от тары, разбивают на куски и загружают в котел до ¾ его объема.
В начале изготовления битумной мастики загруженный битум нагревают при температуре 140 – 1500С до полного расплавления. Для предотвращения интенсивного вспенивания в битум добавляют низкомолекулярный силоксановый каучук из расчета 2 г на 1 т массы или пеногаситель в тех же количествах. После полного обезвоживания при температуре 170 – 1800С в битум при непрерывном его перемешивании добавляют наполнитель. Для получения однородной мастики необходимо интенсивное ее перемешивание в процессе изготовления. С этой целью котлы, в которых изготовляется мастика, снабжают механическим перемешивающим устройством.
При использовании в качестве наполнителя атактического полипропилена последний следует добавлять в расплавленный и обезвоженный битум порциями по 10 - 15 кг.
В случае применения в качестве наполнителя полидиена в котел сначала заливают полидиен и загружают 10 - 20% от предусмотренного рецептурой количества битума в кусках. После полного расплавления битума в котел по мере расплавления вводится порциями остальное количество битума.
При использовании в качестве минерального наполнителя доломита, асфальтового или доломитизированного известняка или талька мастики изготовляют в битумоварочных котлах с огнеупорной футеровкой, исключающей прямой контакт пламени с днищем котла. Минеральный наполнитель загружают в разогретый и обезвоженный битум с помощью бункеров-дозаторов с щелевым регулирующим затвором и наклонным лотком. Бункер устанавливается над загрузочным отверстием котла. К наружной плоскости днища лотка укреплен стандартный плоский вибратор. При включении вибратора наполнитель, загруженный в бункер, должен высыпаться в котел полосой. Количество поступающего из бункера в котел наполнителя регулируется щелевым затвором и не должно превышать 25 кг/мин.
Мастика изготовляется при включенном механизме перемешивания. После введения необходимого количества наполнителя в битум перемешивание мастики продолжается в течение 10 - 15 мин до получения однородной массы. Перемешивающее устройство должно работать непрерывно до полной выработки мастики, чтобы минеральный наполнитель не оседал на дно котла. В случае применения в качестве наполнителя асбеста и низкомолекулярного полиэтилена сначала в расплавленный и обезвоженный битум вводится в нужном количестве асбест (порциями, не превышающими 15 кг). После получения однородной обезвоженной массы ее температуру снижают до 1500С и в. котел вводят низкомолекулярный полиэтилен кусками до 10 -
15 кг. Готовые битумные мастики должны быть хорошо перемешаны, однородны, чтобы избежать коксования битумных мастик, не следует держать их при температуре 180 – 1900С более 1 ч и при температуре 160 – 1700С более
3 ч. Признаком начинающегося коксования битума является появление на поверхности расплавленной массы пузырей и зелено-желтого дыма. Температура готовой битумно-асбополимерной мастики в изоляционной ванне перед нанесением на трубы должна быть в зависимости от температуры наружного воздуха в пределах 150 – 1700С.
Нанесение битумных покрытий
Важнейшим условием, определяющим качество защитного покрытия и продолжительность срока его службы, является соблюдение технологического и температурного режимов в процессе изготовления мастики и нанесения ее на трубы. Толщина наносимого битумного изоляционного слоя, сплошность и прилипаемость его, степень пропитки армирующей обмотки в основном зависят от вязкости битумной мастики, которую регулируют изменением температуры в ванне в зависимости от температуры окружающего воздуха.
Битумную мастику наносят по периметру и длине трубопровода ровным слоем заданной толщины, без пузырей и посторонних включений.
Слои армирующей обмотки из стеклохолста и наружная обмотка должны накладываться на горячую мастику по спирали с нахлестом и определенным натяжением, исключающим пустоты, морщины и складки и обеспечивающим непрерывность слоя и необходимую толщину защитного покрытия.
При нанесении защитных покрытий концы труб оставляют неизолированными длиной 150 - 200 мм для труб диаметром 57 - 219 мм и 250 -
300 мм для труб диаметром 277 - 1420 мм.
Изоляционные работы в зимнее время в трассовых условиях разрешается проводить при температуре воздуха не ниже – 250С.
Нанесение защитных покрытий па основе битумных мастик непосредственно на месте укладки трубопроводов (изоляция сварных соединений, исправление мест повреждений) во время дождя и снега запрещается.
Поверхность изолируемого трубопровода перед нанесением грунтовки не должна иметь заусенцев, задиров, брызг металла, шлака. Очистку трубопроводов от грязи, неплотной окалины, ржавчины и пыли производят очистными машинками.
Очищенная поверхность должна быть серого цвета с характерными металлическими проблесками, шероховатой и обеспыленной. Поверхность трубопровода при нанесении грунтовки должна быть сухой; наличие влаги в виде пленки, пузырьков, наледи или инея не допускается. Грунтовку наносят на сухую поверхность тонким слоем сразу после очистки трубопровода. Слой грунтовки должен быть ровным, без пропусков, сгустков, подтеков и пузырей. Особенно тщательно следует огрунтовывать околошовную зону прямых и спиральных швов.
Марку битумно-резиновой мастики выбирают в зависимости от температуры транспортируемого продукта и минимальной температуры воздуха.
В случае использования битумных мастик при отрицательной температуре, но не ниже – 300С изоляционно-укладочные работы выполняют с подогревом трубопровода до температуры не ниже 150С, но не выше температуры его эксплуатации. Чтобы предохранить покрытие от растрескивания при чрезвычайном охлаждении (ниже температур для соответствующих марок битумно-резиновых мастик), трубопровод немедленно опускают в траншею и засыпают.
Полимерные покрытия
Для защиты подземных трубопроводов применяют полимерные покрытия из полиэтиленовых изоляционных липких лент, поливинилхлоридных изоляционных липких лент, экструдированного или напиленного полиэтилена, эпоксидной порошковой краски, эмали этиноль. В зависимости от условий нанесения полимерные покрытия делят па заводские, базовые или трассовые.
Защитные покрытия из полиэтилена отличается также высокой стойкостью относительно внешнего влияния после укладки, например, относительно агрессивности грунтов, пресной и соленой воды, морских растительных организмов, побегов растений в грунте, микроорганизмов, а также относительно большого спектра минеральных масел и химического воздействия. Покрытие из полиэтилена обладает высоким электрическим сопротивлением, которое остается постоянным в течение длительного времени. Данное свойство важно для электрохимической защиты.
Защитные покрытия заводского нанесения на основе порошковых полимеров следует применять на трубопроводах любого диаметра при температуре транспортируемого продукта не выше: + 700С для полиэтиленовых покрытий, + 800С - для эпоксидных. Защитные покрытия на основе полимерных лент допускается применять на трубопроводах диаметром не более 1420 мм при температуре транспортируемого продукта не выше: + 600С для полиэтиленовых лент, + 400С для поливинилхлоридных.
Грунтовки
Под покрытие из полимерных липких лент применяют клеевые или битумно-клеевые грунтовки.
Температурный интервал применения покрытий из полимерных лент на применяемой грунтовке должен соответствовать показателям ТУ на данный тип ленты, но не ниже – 600С и не выше 70 – 800С.
|
|
Историки об Елизавете Петровне: Елизавета попала между двумя встречными культурными течениями, воспитывалась среди новых европейских веяний и преданий...
Индивидуальные и групповые автопоилки: для животных. Схемы и конструкции...
Таксономические единицы (категории) растений: Каждая система классификации состоит из определённых соподчиненных друг другу...
Двойное оплодотворение у цветковых растений: Оплодотворение - это процесс слияния мужской и женской половых клеток с образованием зиготы...
© cyberpedia.su 2017-2024 - Не является автором материалов. Исключительное право сохранено за автором текста.
Если вы не хотите, чтобы данный материал был у нас на сайте, перейдите по ссылке: Нарушение авторских прав. Мы поможем в написании вашей работы!