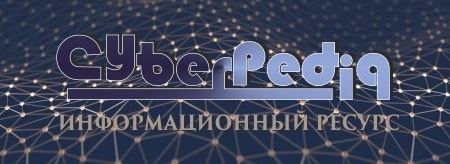
Состав сооружений: решетки и песколовки: Решетки – это первое устройство в схеме очистных сооружений. Они представляют...
История создания датчика движения: Первый прибор для обнаружения движения был изобретен немецким физиком Генрихом Герцем...
Топ:
Основы обеспечения единства измерений: Обеспечение единства измерений - деятельность метрологических служб, направленная на достижение...
Характеристика АТП и сварочно-жестяницкого участка: Транспорт в настоящее время является одной из важнейших отраслей народного...
Проблема типологии научных революций: Глобальные научные революции и типы научной рациональности...
Интересное:
Национальное богатство страны и его составляющие: для оценки элементов национального богатства используются...
Берегоукрепление оползневых склонов: На прибрежных склонах основной причиной развития оползневых процессов является подмыв водами рек естественных склонов...
Финансовый рынок и его значение в управлении денежными потоками на современном этапе: любому предприятию для расширения производства и увеличения прибыли нужны...
Дисциплины:
![]() |
![]() |
5.00
из
|
Заказать работу |
|
|
Оглавление
Аннотация……………………………………………………………………….4
Введение. 6
1. Общая часть. 8
1.1 Конструкционно-технологический анализ. 8
1.1.1 Служебное назначение детали. 8
1.1.2 Материал детали и его свойства. 9
1.2 Анализ конструкции детали на технологичность. 10
1.2.1 Качественная оценка технологичности. 12
1.2.2 Количественная оценка технологичности. 14
1.3 Конструкторский анализ чертежа детали. 16
1.4 Выбор типа производства. 17
1.5 Определение вида заготовки и способов их изготовления. 19
2. Технологическая часть. 23
2.1 Проектирование маршрутного технологического процесса. 23
2.1.1 Выбор маршрута обработки. 24
2.1.2 Обоснование выбора базовых поверхностей. 26
2.1.3 Выбор технологического оборудования. 28
2.1.4 Выбор режущего инструмента и технологической оснастки. 35
2.2 Проектирование операционной технологии. 38
2.2.1 Подробная разработка структуры технологических операций механической обработки. 40
2.2.2 Расчет промежуточных припусков на механическую обработку. 40
2.2.3 Расчет и выбор режимов резания. 45
2.2.4 Нормирование операций механической обработки. 61
3. Конструкторская часть. 64
3.1 Назначение приспособления. 64
3.2 Выбор способа базирования детали. 65
3.3 Расчет точности обработки. 65
3.4 Расчет режимов резания. 67
3.5 Расчет коэффициента надежности закрепления детали. 69
3.6 Расчет сил зажима. 70
4. Техника безопасности и охрана труда на рабочем месте. 72
4.1. Требования к производственным площадям. 72
4.1.1 Метеорологические условия. 72
4.1.2. Шум. 73
4.1.3. Освещение. 74
4.1.4. Вентиляция. 78
4.1.5. Вибрация. 78
4.2 Пожарная безопасность и электроопасность. 79
4.2.2. Техника безопасности при использовании электроустановок. 81
4.3.3 Требования безопасности в аварийных ситуациях. 82
|
Заключение. 83
Список использованной литературы. 84
МИНИСТЕРСТВО НАУКИ И ВЫСШЕГО ОБРАЗОВАНИЯ РОССИЙСКОЙ ФЕДЕРАЦИИ
Федеральное государственное бюджетное образовательное учреждение высшего образования
«Казанский национальный исследовательский технический университет им. А.Н.Туполева-КАИ»
(КНИТУ-КАИ)
Набережночелнинский филиал
Аннотация
Курсового проекта: Галлямова Ильназа Тагировича
На тему: «Разработка технологического процесса изготовления детали «Диск колеса КамАЗ 43118»
88 стр, 4 листа чертежей формата А1, 1 лист спецификации, операционные карты 4с,карта эскизов 3с. Использованные источники 50 шт.
Курсовой проект на тему: «Разработка технологического процесса изготовления детали «Диск колеса КамАЗ 43118» состоит из общей, технологической и конструкторской части.
В общей части были описаны служебное назначение детали, его исполнительные поверхности и технические требования.
Разработан рабочий маршрутно-операционный технологический процесс изготовления диска. Проведен анализ служебного назначения и технический условий. Конструкция отработана на технологичность, обоснован выбор метода получения заготовки. Выполнены расчеты припусков и режимов резания. Введены изменения в существующий технологический процесс.
Также в данной работе в 4 главе особое внимание уделилось технике безопасности рабочего, влияния на вредные факторы(шум,вибрация,освещение)
Расписаны требования безопасности в аварийных ситуациях.
MINISTRY OF SCIENCE AND HIGHER EDUCATION OF THE RUSSIAN FEDERATION
Federal State Budgetary Educational Institution of Higher Education
"Kazan National Research Technical University named after A.N.Tupolev-KAI"
(KNITU-KAI) Naberezhnye
Chelny branch
Annotation
Course project: Ilnaz Tagirovich Gallyamov
On the topic: "Development of the technological process of manufacturing the part "Wheel disc KAMAZ 43118"
88 pages, 4 sheets of A1 drawings, 1 sheet of specification, 4c operational maps, 3c sketch map. Used sources 50 pcs.
Course project on the topic: "The development of the technological process of manufacturing the KAMAZ 43118 Wheel Disc part consists of a general, technological and design part.
|
In the general part, the service purpose of the part, its executive surfaces and technical requirements were described.
A working route-operational technological process of disk manufacturing has been developed. The analysis of the official purpose and technical conditions is carried out. The design is tested for manufacturability, the choice of the method of obtaining the workpiece is justified. Calculations of allowances and cutting modes are performed. Changes have been introduced to the existing technological process.
Введение
В условиях современного производства необходим рост производительностии надежности машин, снижение их массы на единицу мощности повышение точности изделий.Так же остро стоит и проблема улучшения качества агрегатов автомобилей, увеличения их надежности, работоспособности.
Для достижения поставленных задач необходимо внедрение высокоэффективныхтехнологических процессов, коллективной механизации и последовательное проведение автоматизации производства.
Особенно важно осуществление этих мероприятий в тех производственных процессах, в которых в настоящее время еще затрачивается ручной труд, недостаточная автоматизация и механизация. К числу таких производственных процессов относится и механическая обработка.
Значение постановки всех этих вопросов при подготовке квалифицированных кадров специалистов производства, полностью овладевших инженерными методами проектирования производственных процессов, очевидно. В связи с этим заключительной частью учебного процесса высших учебных заведений является дипломное проектирование.
Курсовое проектирование закрепляет, углубляет и обобщает знания, полученные студентами во время лекционных и практических занятии по практически всем дисциплинам, освоенным за время обучения. Дипломная работа является самостоятельной творческой работой студента и имеет цель научить его правильно применять теоретические знания, полученные ими в процессе учебы, использовать свой практический опыт работы для решения профессиональных технологических и экономических задач.
Увеличение степени автоматизации и, как следствие, расширение технологических задач, решаемых без непосредственного участия человека, означает повышение роли инженерно-технического обеспечения в создании и управлении современным машиностроительным производством. В соответствие с этим инженеру, работающему в области машиностроительного производства, требуются глубокие знания технологии, станочного оборудования, компьютерной и информационно-измерительной техники.
|
Обработка резанием является универсальным методом размерной обработки. Метод позволяет обрабатывать поверхности деталей различной формы и размеров с высокой точностью из наиболее используемых конструкционных материалов. Он обладает малой энергоемкостью и высокой производительностью.
Для выполнения работы необходимо решить следующие задачи:
- обосновать выбор вида заготовки;
- проанализировать схемы базирования;
- разработать маршрут обработки детали;
- рассчитать припуски на обработку;
- рассчитать режимы резания и нормы времени с составлением маршрутной и операционной карт;
- расчет и проектирование станочного приспособления;
- организационно-экономические расчеты.
Текстовые материалы состоят из пояснительной записки и карт технологического процесса. Записку необходимо писать одновременно с разработкой ТМ.КП и окончательно оформлять после выполнения всех работ. В записке излагаются основные принципиальные решения, принятые в проекте по отдельным вопросам, даются необходимые пояснения, приводятся инженерные расчеты, иллюстрируемые схемами, эскизами, графиками. Записка пишется в сжатой форме и должна иметь минимум извлечений из различных литературных источников в виде цитат и максимум ссылок на литературу, собственных выводов, предложений, пояснений, расчетов.
В данном курсовом проектировании предлагается объединить операций выполняемые на разных станках в один станок с ЧПУ В связи с одной и той же схемой базирования детали и возможности используемого приспособления и оборудования, разработать приспособление.
Общая часть
Служебное назначение детали
Деталь «Диск» представляет собой совокупность цилиндрических и торцевых поверхностей. В центре детали имеется сквозное отверстие. Также деталь имеет десять болтовых отверстий и десять вентиляционных. Одно вентиляционное отверстие пробито под вентильный паз. Все поверхности детали доступны в обработке, что позволяет применить стандартный режущий и мерительный инструмент. Требования к точности размеров и шероховатости поверхностей обоснованы назначением детали. Деталь диск - изготавливается из стали конструкционная низколегированная для сварных конструкций 15ХСНД, поэтому конфигурация наружного контура и внутренних поверхностей не вызывает значительных трудностей при получении заготовки.
|
Деталь выполняется из материала Сталь 15ХСНД ГОСТ 6713.
Поверхности детали выполняется по 14 квалитету. После обработки деталь подвергают контролю.
Рисунок 1.1 - Диск Колеса 43118
Выбор типа производства
Определяем тип производства, в зависимости от габаритов, массы (веса) и размера годовой программы выпуска изделий, из этих данных необходимо установить тип производства:
Единичное - определяется выпуском деталей (продукции) в малом количестве.
Серийное - производство характеризуется ограниченным выпуском продукции, но большими сериями. Серийное производство подразделяется на крупносерийное и мелкосерийное.
Крупносерийное - относительно постоянный выпуск продукции большими сериями, либо изготовлением изделий, производство которых часто повторяется. По характеру ближе остальных к массовому.
Мелкосерийное - широкая номенклатура, большой размер серии, редкая периодичность выпуска. По характеру близко к единичному.
Массовое - характеризуется выпуском одной и той же продукции как правило длительное время (годами).
Таблица 1.4 - Определение типа производства по массе и годовой программе.
Масса детали, кг. | Тип производства | ||||
Единичное | Мелко- серийное | Средне-серийное | Крупно- серийное | Массовое | |
< 1,0 | < 10 | 10 - 2000 | 1500 – 100000 | 75000 - 200000 | 200000 |
1,0 - 2,5 | < 10 | 10 - 1000 | 1000 - 5000 | 50000 - 100000 | 100000 |
2,5 - 5,0 | < 10 | 10 - 500 | 500 - 35000 | 35000 - 75000 | 75000 |
5,0 – 10 | < 10 | 10 - 300 | 300 - 25000 | 25000 - 50000 | 50000 |
> 10 | < 10 | 10 - 200 | 200 - 10000 | 10000 - 25000 | 25000 |
Согласно массе детали 11,58 кг, и годовой программе 8600 шт. в год, тип производства - среднесерийное.
Согласно ГОСТ 3.1119-83 тип производства характеризуется коэффициентом закрепления операций Кзо: Кз.о ≤ 1 – массовое производство; 1 < Кз.о ≤ 10 – крупносерийное производство; 10 < Кз.о ≤ 20 – серийное производство; 20 < Кз.о ≤ 40 – мелкосерийное производство; Кз.о для единичного производства не регламентируется.
Значение коэффициента принимается для планового периода, равного одному месяцу и определяется по формуле:
где О – число операций, выполняемых на данном оборудовании в течении месяца; Р – количество единиц оборудования, число рабочих мест, за которыми закреплены эти операции.
По данным завода «Камаза»: О = 243; Р = 20;
По данной величине коэффициента закрепления определяем тип производства как среднесерийное.
|
Данный тип производства характеризуется тем, что запуск заготовок для обработки производится партиями, оптимальная величина которых определяется по формуле:
где D=8600 шт./год - количество деталей по заданной годовой программе вместе с запасными, t=10 дней - число дней, на которые необходимо иметь запас деталей для обеспечения непрерывности сборочного процесса, Ф=254 дня –число рабочих дней в году.
Такт выпуска:
Организационная форма производства – поточная.
Технологическая часть
Выбор маршрута обработки
Операции Штамповки диска Пресс механический К04.147.240 Р=1000тонн;
1. Вырубка Квадратной Заготовки и центрального технологического отверстия.
2. Вырубка углов заготовки.
3. Вырубка. Маркирование. Заготовка (рисунок 2)
4. Вытяжка. Формовка диска.
5. Пробивка болтовых и центрального отверстия
6. Чеканка. Вентильных отверстий.
7. Пробивка вентильного паза. Контроль.
Рисунок 1.4 - Заготовка диска Выруленная после 3й операции штамповки.
АМ 13369
Станок АМ 13369 агрегатный полу автоматический (рис. 2.2)
Технологическая оснастка:
· 55-7030-6037 палец;
· 55-7030-6533 опора;
· 55-7271-6006 упор;
· 55-7050-6671 втулка кондукторская;
55-6314-6003 головка резцовая;
· 63-6240-6000 оправка переходная;
· 2039-8127 вставка резцовая;
· 63-2322-5014 зенкер;
· 55-2322-6004 зенкер;
·
Рисунок 2.2 - Расточка центрального и болтовых отверстий диска 43118на Станке АМ 13369 |
· пластина твердосплавная опорная ВК 15 2007-1072 РТМ 37.104.06.067-85;
Работа в полуавтоматическом режиме. Включение с пульта управления станка.
I позиция
Установить диск Рукавицы Ми,Мп ГОСТ 12.4.103-83
Точить отверстие и снять фаску, выдерживая размеры ø222*.
Зенкеровать десять отверстий предварительно и снять десять фасок, выдерживая размер ø32*
II позиция
4.Перевернуть и Переустановить диск лицевой стороной вверх.
Расточить отверстие, выдерживая размер ø222*.
Зенкеровать десять отверстий с образованием сферических фасок R22*, выдерживая размеры ø32*
Убирать стружку по мере накопления.
Щетка ЩТ ГОСТ 10597-87; 02.18.00.000 Совок; 04.280.00000 удалитель стружки; 03.163.00000 тара для стружки.
Положить диск на контрольную плиту
Калибром 55-8384-7052 калибр Ø32+0,8проверить 10 отверстий.
Комплексным калибром 55-8364-6024 проверить позиционный допуск крепежных отверстий.
Контролировать исполнителем 10% согласно эскизам и переходам.
7. Снять диск и уложить на рольганг для передачи на следущий станок.
Рукавицы Ми,Мп ГОСТ 12.4.103-83
2. 1Б284 вертикальный токарный 6-тишпиндельный полу автоматический. (рисунок 7)
Технологическая оснастка:
· 63-7021-6016 приспособление;
· 55-6675-6003-01 державка;
· 55-6675-6011 державка левая;
· 63-6675-6006 державка;
· 06-6675-4222 державка;
· 2115-8031 резец;
· 2100-8037 резец;
·
Рисунок 2.4 - Расточка Внешнего диаметра и торцевой кромки диска 43118 на станке1Б284 |
· TNMG 220412 GR
пластина твердосплавная NC3030;
· 2007-0074 пластина твердосплавная ВК 15 РТМ 37.104.06.067-85;
· SNMG 120 412-GR пластина твердосплавная NC3030; 2007-1072 пластина твердосплавная ВК 15 РТМ 37.104.06.067-85.
Работа в полуавтоматическом режиме. Включение с пульта управления станка.
зять заготовку с рольана. Установить заготовку на станок в приспособление.
Позиция 1 (рис. 2.5) Произвести поворот рабочего стола.
Рисунок 2.5 - Схематическое расположение шпинделей станка 1Бб284
II поз.
Подрезать торец, выдерживая размер 55±0,5 и снять фаску 8 х 45°*.
IVпоз.
Точить наружный диаметр предварительно, выдерживая размер ø481±0,5.
VI поз.
Точить наружный диаметр окончательно, выдерживая размер ø479+1,2-0,5.
Снять диск со станка. Положить на контрольную плиту.
С помощью штангенциркуля ШЦ-III-500-0,05 ГОСТ 166-89 измерить наружный диаметр.
Измерить высоту диска штангенглубиномер ШГ-160-0,05 ГОСТ 162-90
Эскиз Диска 43118
Рисунок 2.6. Эскиз Диска 43118 в Разрезе
Рисунок 2.7. Эскиз Диска 43118 вид сверху(лицевая сторона)
Конструкторская часть
Назначение приспособления
Содержание технологического перехода: Черновое точение верхней плоской поверхности, выдерживая размеры, указанные на рисунке 3.1.
Рисунок 3.1 – Операционный эскиз на операцию 015.
Металлорежущий станок: выбирается в зависимости от схемы установки заготовки. В свою очередь схема установки определяется величиной погрешности базирования εБ, которая не должна превышать половины допуска на размер т.е. величину 0,2 мм.
Оборудование: Станок АМ 13369 агрегатный полу автоматический со сменой инструмента (АСИ), с автоматической уборкой стружки и числовым программным управлением (ЧПУ).
Размеры рабочей части стола: 800х1600, частота вращения шпинделя 0…8000 об/мин, число подач стола 16; 8,3-416,6 мм/мин, мощность электродвигателя привода главного движения – 18,5 кВт.
Технологическая база: Нижний торец детали.
Режущий инструмент: Цилиндричес Операция 005 – «Токарная»
.
Расчет точности обработки
Приспособление устанавливается на стол станка и выверяется по техническим требованиям:
- отклонение от параллельности оси контрольного валика, установленного в призму, относительно поверхности стола станка не более 0,005 мм;
- отклонение от перпендикулярности оси контрольного валика, установленного в призму, относительно поверхности направляющей шпонки 0,01 мм.
где К = 1,2 - коэффициент зависящий от случайных погрешностей;
бс= 0 - погрешность станка в ненагруженном состоянии вызываемая погрешностями изготовления и сборки, мм;
бпр = 0,005 - погрешность расположения на станке посадочных поверхностей, мм;
боп= 0,01 - погрешность расположения опорных поверхностей относительно посадочных поверхностей приспособления, мм;
ббаз - погрешность базирования заготовки в приспособлении, мм;
бз = 0 - погрешность вызываемая закреплением заготовки, мм;
би = 0 - погрешность изготовления инструмента, мм;
бри = 0 - погрешность расположения инструмента на станке, мм;
бд= 0 - погрешность вызываемая деформацией при обработке, под действием сил резания, мм;
биз = 0 - погрешность вызываемая износом инструмента, мм.
где d1= 0,4 - допуск на размер, мм.
Необходимо выполнить условие:
где а = 0,4 – допуск на паза, мм
0,4 мм 0,24 мм. Условие выполняется.
Расчет режимов резания
Исходя из данных предыдущей главы, выберем расчет наибольшей по силе резания. Учитывая рекомендации примем следующие параметры обработки:
Глубина резания: При черновой обработке назначают по возможности максимальную глубину резания, равную всему припуску на обработку.
tчерн. = 2,5 мм
Подача: Рекомендуемое значение подачи на один зуб фрезы при черновой обработке Sz=0,14…0,24 мм/об.
Sчерн = 0,2 мм/об
Стойкость инструмента: T = 180 мин
Скорость резания:
где Сv – коэффициент в формуле скорости резания; – период стойкости инструмента, мин; t – глубина резания, мм; s– подача, мм/об; B – ширина фрезерования, мм; z – число зубьев; q, m, x, y, u, p – показатели степени в формуле скорости резания;
Kmv = 1,0 – коэффициент, учитывающий влияние материала заготовки;
KПV = 0,9 – коэффициент, учитывающий состояние поверхности заготовки;
KИv = 2,7 – коэффициент, учитывающий материал режущей части инструмента – ВК6.
Таблица №3.1 – Значения коэффициентов скорости резания для операции 015.
В | Сv | q | х | y | u | p | m |
80 | 133,5 | 0,45 | 0,3 | 0,4 | 0,1 | 0,1 | 0,33 |
Частота вращения:
где υ –скорость, м/мин; D –диаметр фрезы, мм.
По паспорту станка уточняем число оборотов nф и находим фактическую скорость:
nф.черн = 1150 об/мин
Сила резания:
где СР – коэффициент в формуле силы резания; x, y, n, q, w – показатели степени в формуле силы резания.
Таблица №3.2 – Значения коэффициентов силы резания для операции 015.
СР | u | Q | w | x | y |
101 | 1,0 | 0,87 | 0 | 0,88 | 0,75 |
Мощность резания:
Основное технологическое время:
где L – расчетная длина обрабатываемой поверхности, мм; – минутная подача, мм/мин; I – число проходов.
где l – чертежная длина обрабатываемой поверхности, мм; l1 – величин врезания, мм; l2 – величина перебега, мм.
Величины остальных составляющих силы резания найдём через окружную силу.
Горизонтальная сила (подачи) Ph=0,4хPz = 709 Н.
Вертикальная сила Pv=0,9хPz = 1596 Н.
Радиальная сила Py=0,4хPz = 709 Н.
Осевая сила Px=0,55хPz = 975 Н.
Расчет сил зажима
На практике расчет сил зажима обрабатываемой заготовки производится в двух основных случаях:
1. При использовании имеющихся универсальных и переналаживаемых приспособлений с зажимными устройствами, развивающими определенную силу зажима.
2. При конструировании новых приспособлениях.
В данном приспособлении используется поворотный винтовой зажим с резьбой М12. Будем рассчитывать зажимную силу винта исходя из следующей формулы:
Сила зажима определяется по формуле:
где W – сила зажима;
Mкр = =
– крутящий момент
- средний диаметр резьбы
=
’ – угол подъема резьбы
=
’ – угол трения резьбовой пары
Кф= 0,7 – коэффициент фиксации
Значение коэффициента надежности закрепления k выбираем дифференцированно в зависимости от конкретных условий выполнения технологической операции и способа закрепления нашей заготовки. Его величина уже определена в предыдущей главе. Если в результате расчета величина К оказывается меньше 2,5, то при расчете надежности закрепления ее следует принять равной 2,5. Этот запас надежности оговорен ГОСТ 12.2.029 — 77. Таким образом: К = 3,24.
Данный зажим вполне удовлетворяет всем требованиям и обеспечивает необходимую зажимную силу, которая превосходит силы резания.
Требования к производственным площадям
Метеорологические условия.
Метеорологические условия определяются следующими факторами:
- температура воздуха (t,˚C);
- относительная влажность (%);
- скорость движения воздуха (V, м/с).
Кроме этих параметров, являющихся основными, на метеорологические условия в цехе также влияет атмосферное давление (Р).
Человек находится в постоянном тепловом взаимодействии с окружающей средой. Для того чтобы физиологические процессы в его организме протекали нормально, выделяемая организмом теплота должна отводиться в окружающую среду.
Соответствие между количеством теплоты и охлаждающей способности среды характеризуют ее как комфортную. В условиях комфорта у человека не возникает беспокоящих его температурных ощущений – холода или перегрева.
На рабочем месте станочника оптимальная температура воздуха должна составлять:
- для холодного периода года +16…+18ºС;
- для теплого периода года +20…+23ºС.
Влажность воздуха оказывает большое влияние на терморегуляцию организма. Повышенная влажность (φ>85%) затрудняет терморегуляцию организма из-за снижения испарения пота, а слишком низкая влажность (φ<20%) вызывает пересыхание слизистых оболочек дыхательных путей. Оптимальные величины относительной влажности составляют 40-60%.
Движение воздуха влияет на тепловое самочувствие человека. В жарком климате движение воздуха способствует увеличение теплоотдачи человека и способствует улучшению его самочувствия, но оказывает неблагоприятное воздействие при низких температурах воздуха в холодное время года.
Минимальная скорость движения воздуха, ощущаемая человеком превышает 0,2-0,5 м/с, а летом 0,2-1 м/с. в горячих цехах разрешается увеличение скорости обдува рабочих до 3,5 м/с.
Шум
На многих производствах чрезмерный шум, в несколько раз превышающий санитарные нормы, создает неблагоприятную производственную обстановку, отрицательно влияет на состояние здоровья работников, что ведет к снижению производительности труда.
Нормируемыми параметрами шума являются уровни в децибелах.
L=90 дБ
Основными физическими величинами, характеризующими шум являются:
1. интенсивность;
2. звуковое давление;
3. частота;
В соответствии с ГОСТом 121003-83 защита от шума, создаваемого на рабочих местах осуществляется следующим образом:
- уменьшение шума в самом источнике;
- применение средств коллективной защиты;
- размещение источника шума на возможно более удаленном расстоянии;
- использование средств звукопоглощения при выполнении акустической обработки шумных помещений;
- применение средств индивидуальной защиты (ГОСТ 12.4-051-87);
- рациональная планировка помещений
В качестве звукопоглащающих конструкций можно предложить маты из стекловаты или перфорированные плиты, укрепленные на стене.
Для оценки звукопоглащающей способности ограждения введено понятие звукопоглащаемости численно равное отношению звуковой энергии, прошедшей через ограждение, и падающей на него.
Предельно допустимый уровень шума на рабочих местах в производственных помещениях обозначается ПС-80.
Освещение
Освещение рабочего стола – важный фактор создания нормальных условий труда.
Хорошее освещение оказывает положительное психологическое воздействие на рабочего, способствует повышению производительности труда.
В зависимости от источника световой энергии, освещение делят на:
- естественное;
- искусственное;
- совмещенное
Естественное освещение какой-либо точки в помещении характеризуется коэффициентом естественной освещенности. Наименьшая расчетная освещенность при естественной освещенности определяется при наружной освещенности 5000 Лк. Для искусственного освещения применяют люминесцентные лампы с высокой световой отдачей и продолжительным сроком службы.
Применяются лампы ЛБ (белый свет) и ЛТБ (теплобелый свет) мощностью 20, 40 и 80 ВТ. Лампы должны быть размещены параллельно светопроемам и равномерно по потолку. В проектируемом цехе производятся малой и средней точности в зависимости от габаритов детали.
Освещенность: комбинированная 1000 Лк, общее 300 Лк для люминесцентных ламп. Общая освещенность на расстоянии от 0,8 м. от пола 200 Лк для вспомогательных помещений.
Искусственное освещение может быть двух видов: рабочее и аварийное.
Аварийное освещение подразделяется на освещение для продолжения работы и освещение для эвакуации людей.
Наименьшая освещенность при аварийном режиме должна составлять 5% освещенности, нормируемой для рабочего освещения, но не менее 2 Лк внутри зданий и не менее 1 Лк на площадках предприятий.
а) Расчет искусственного освещения.
При правильно рассчитанном и выполненном освещении производственных помещений глаза работающего персонала в течение продолжительного времени сохраняют способность хорошо различать предметы и орудия труда, не утомляясь.
На рабочих местах освещенность нормируется согласно СНиП 23-05-95 "Нормы проектирования. Естественное и искусственное освещение".
В связи с тем, что естественного освещения недостаточно и с учетом, например, круглосуточного графика работы, необходимо применять общее искусственное освещение.
Для этого освещения используются, например, лампы ртутные газоразрядные ДРЛ 1000(6)-2 (дуговая ртутная лампа 1000Вт).
СНиП 23-05-95 устанавливает норму освещенности в цехе 300 Лк для общего освещения и работах средней точности. Данная норма в цехе выдерживается для четвертого разряда подразряда зрительных работ.
Произведем расчет количества ламп, обеспечивающих требуемую освещенность помещения:
где E - минимальная освещенность по норме: E = 300 Лк;
k - коэффициент запаса лампы, необходимый для компенсации потерь освещения из-за ее запыленности (в России, коэффициент запаса равен 1,4 - для газоразрядных ламп. В Европе применяется единственный коэффициент для всех типов ламп и он равен 1,25): k = 1,4;
Sп - площадь помещения: Sп = 1440 м2
Z - коэффициент минимальной освещенности, определяемый отношением Еср/Еmin значения которого для ламп накаливания и газоразрядных ламп высокого давления (ДРЛ, МГЛ, НЛВД) – 1,15:
F - световой поток одной лампы: F=57000лм – для ламп ДРЛ 1000(6)-2
η - коэффициент использования светового потока (коэффициент использования светового потока лампы (%), зависящий от типа лампы, типа светильника, коэффициента отражения потолка и стен, высоты подвеса светильников и индекса помещения i:
Индекс помещения i определяется по формуле:
где А и В – длина и ширина помещения, м;
Нр – высота подвеса светильника над рабочей поверхностью, м: Нр= 11,5 м.
При использовании светильников РСП07, коэффициенте отражения потолка 50% (чистый бетонный потолок) и стен 30% (бетонные стены с окнами) коэффициент использования светового потока η для ламп ДРЛ и индекса помещения i=1,5 будет равен: η = 0,46.
Количество ламп, обеспечивающих требуемую освещенность помещения:
Принимаем N=27 шт.
Выбираем светильники РСП07 ГОСТ 17677–82 с дуговыми ртутными лампами ДРЛ 1000(6)-2, данные светильники обеспечат необходимую освещенность в производственном помещении цеха.
б) Расчет естественного освещения
Длительное отсутствие естественного света угнетающе действует на психику человека, способствует развитию чувства тревоги, снижает интенсивность обмена веществ в организме способствует развитию близорукости и утомляемости.
Рассчитаем необходимую площадь световых проемов при боковом естественном освещении и при условии, что оператором осуществляется четвертый разряд зрительных работ:
, (5.4)
где Sп - площадь пола: Sп = 24 · 60 = 1440 м2;
kз - коэффициент запаса, учитывающий потерю освещенности из-за запыленности окон: kз = 1,3;
е - коэффициент естественного освещения для четвертого разряда зрительных работ и бокового освещения: е = 1,5%;
h0 - световая характеристика здания: h0 = 10;
кзд = 1;
r0 - общий коэффициент светопропускания: r0 = 0,6;
rк - коэффициент увеличения освещенности за счет отражения света от пола: rк = 1,2.
Таким образом, площадь световых проемов:
Площадь стен:
, (5.5)
Sст = 2·(60+24)·12,6= 2116,8 м2;
Процентное отношение площади окон и площади стен:
Итак, рационально устроенное освещение создает достаточную равномерную освещенность производственного помещения, сохраняет зрение рабочего персонала, уменьшает травматизм, позволяет повышать производительность труда, влияет на уменьшение процента брака и улучшение качества.
Вентиляция
Вредные вещества, находящиеся в производственных помещениях в воздухе через дыхательные пути, пищевой тракт могут попасть в организм человека и при определенных условиях вызвать острые хронические отравления (заболевания).
При помощи вентиляции в помещениях создаются нормальные санитарно-гигиенические условия воздушной среды. Воздухообмен в помещениях осуществляется приточно-вытяжной вентиляцией.
Вентиляция может быть общеобменная, когда смесь воздуха с выделяющимися вредностями доводится до допустимых пределов по всему объему помещения, или местной, когда вредности удаляются от мест их выделения через специальные укрытия (местные отсосы).
В помещениях с влаговыделениями устройство общеобменной механической вытяжки предусматривается в случаях, когда невозможно предусмотреть естественную вытяжку. При возможных поступлениях больших количеств токсичных и взрывоопасных веществ предусматривается аварийная вытяжная вентиляция.
Вентиляция должна обеспечивать в помещении метеорологические условия в полном соответствии с требованиями санитарных норм (сн 245-71) и ГОСТ 12.1.005 – 76.
Вибрация
В промышленности в связи новыми технологиями изготовления деталей, ростом мощности оборудования и его быстроходности широкое применение получили машины и оборудования, создающие вибрации, неблагоприятно воздействующие на человека. В соответствии с ГОСТ 24346-80 вибрация может быть вызвана множеством причин: неуравновешенными силовыми воздействиями, неоднородностью материала вращающегося тела, несовпадением осей вращения с осью массы тела.
Основными параметрами вибраций, происходящих по синусоидальному закону, является амплитуда виброперемещений. Различают общую и локальные вибрации. Общая вибрация вызывает сотрясение всего организма, местная вовлекает в колебательное движение отдельные части тела. В ряде случаев рабочий может подвергаться и общей и локальной вибрации одновременно.
Существует несколько способов борьбы с вибрацией:
- отстройка от режимов р
|
|
Механическое удерживание земляных масс: Механическое удерживание земляных масс на склоне обеспечивают контрфорсными сооружениями различных конструкций...
Типы сооружений для обработки осадков: Септиками называются сооружения, в которых одновременно происходят осветление сточной жидкости...
Археология об основании Рима: Новые раскопки проясняют и такой острый дискуссионный вопрос, как дата самого возникновения Рима...
Состав сооружений: решетки и песколовки: Решетки – это первое устройство в схеме очистных сооружений. Они представляют...
© cyberpedia.su 2017-2024 - Не является автором материалов. Исключительное право сохранено за автором текста.
Если вы не хотите, чтобы данный материал был у нас на сайте, перейдите по ссылке: Нарушение авторских прав. Мы поможем в написании вашей работы!