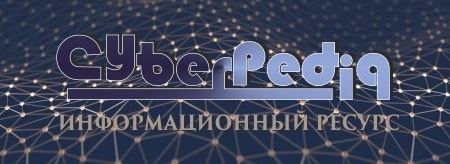
Биохимия спиртового брожения: Основу технологии получения пива составляет спиртовое брожение, - при котором сахар превращается...
Организация стока поверхностных вод: Наибольшее количество влаги на земном шаре испаряется с поверхности морей и океанов (88‰)...
Топ:
Методика измерений сопротивления растеканию тока анодного заземления: Анодный заземлитель (анод) – проводник, погруженный в электролитическую среду (грунт, раствор электролита) и подключенный к положительному...
Выпускная квалификационная работа: Основная часть ВКР, как правило, состоит из двух-трех глав, каждая из которых, в свою очередь...
Оценка эффективности инструментов коммуникационной политики: Внешние коммуникации - обмен информацией между организацией и её внешней средой...
Интересное:
Берегоукрепление оползневых склонов: На прибрежных склонах основной причиной развития оползневых процессов является подмыв водами рек естественных склонов...
Принципы управления денежными потоками: одним из методов контроля за состоянием денежной наличности является...
Как мы говорим и как мы слушаем: общение можно сравнить с огромным зонтиком, под которым скрыто все...
Дисциплины:
![]() |
![]() |
5.00
из
|
Заказать работу |
|
|
И обслуживания оборудования
Структура ремонтного цикла зависит от вида оборудования, его категории, класса точности, видов проводимых ремонтов и определяется по данным Типовой системы ТО и ремонта оборудования.
Структуры ремонтного цикла для металлорежущего оборудования нормального класса точности приведены в табл. 8.7.
Таблица 8.7
Структура ремонтного цикла
Оборудование | Структура ремонтного цикла | Число ремонтов в цикле | Число плановых осмотров в межремонтном периоде | |||
Вид | Класс точности | Категория (вес, т) | средних | теку-щих | ||
Метал-лоре-жущее | Н | До 10 | КР-ТР-ТР-СР-ТР-ТР-КР или КР-ТР-ТР-ТР-ТР-КР | 1 | 4 | 1 |
- | 4 | 1 | ||||
Св. 10 до 100 | КР-ТР-ТР-СР-ТР-ТР-КР или КР-ТР-ТР-ТР-ТР-ТР-КР | 1 | 4 | 2 | ||
- | 5 | 2 | ||||
Св. 100 | КР-ТР-ТР-СР-ТР-ТР-КР или КР-ТР-ТР-ТР-ТР-ТР-ТР-КР | 1 | 4 | 3 | ||
- | 6 | 3 |
Длительность ремонтного цикла для металлорежущего оборудования равна:
(8.18)
где – коэффициент обрабатываемого материала;
– коэффициент применяемого материала;
– коэффициент класса точности оборудования;
– коэффициент категории массы;
– коэффициент возраста;
– коэффициент долговечности (год выпуска).
Значения коэффициентов приведены в табл. 8.8–8.10.
Таблица 8.8
Значение коэффициентов
Коэффициент | Определяемый параметр | Значение коэффициента |
![]() | Обрабатываемый материал: Сталь конструкционная Прочие материалы | 1,0 0,75 |
![]() | Материал применяемого инструмента: Металл Абразив | 1,0 0,8 |
![]() | Класс точности: Н П В, А, С | 1 1,5 2,0 |
![]() | Категория массы: До 10 т Св.10 до 100 т Св.100 т | 1,0 1,35 1,7 |
Таблица 8.9
Значение коэффициента
Возраст, лет | Класс точности | Порядковый номер планируемого ремонтного цикла | Значение коэффициента | |
До 10
| Н, П В, А, С | Первый и второй Первый | 1,0 | |
Н П, В, А, С | Второй и третий Второй | 0,9 | ||
Свыше 10 | Н П, В, А, С | Четвертый Третий | 0,8 | |
Н П, В, А, С | Пятый и более Четвертый и более | 0,7 |
Таблица 8.10
Значение коэффициента
Год выпуска оборудования | Значение коэффициента |
До 1995 | 0,8 |
С 1996 по 2000 | 0,9 |
С 2001 | 1,0 |
Ремонтный цикл в годах определяется по выражению:
, (8.19)
где – действительный фонд времени работы оборудования
( ч и 3950 ч соответственно при односменной и двухсменной работе).
Продолжительность межремонтного периода – равна продолжительности ремонтного цикла, деленной на число внутрицикловых ремонтов плюс 1, то есть:
, (8.20)
где – число внутрицикловых ремонтов.
График планово-предупредительного ремонта (ППР) каждой конкретной единицы оборудования (станка) сводится в виде табл. 8.11.
Производственная программа по ремонту и плановым осмотрам оборудования в ремонтных единицах представляется по форме согласно табл. 8.12.
Расчет производственной программы проводится по аналогии с приведенным ниже примером.
Пример: Имеем ремонтируемое оборудование – специальный станок для заточки твердосплавных пластин модели МЗ-3 класса точности «Н».
Согласно табл. 8.7 принимаем следующий ремонтный цикл: КР-ТР-ТР-ТР-ТР-КР.
Определяем длительность ремонтного цикла:
(8.21)
Величина ремонтного цикла в годах
г. (8.22)
Определяем длительность межремонтного периода:
мес. (8.23)
Определяем длительность межосмотрового периода:
мес. (8.24)
График планово-предупредительного ремонта станка МЗ-3 представлен в табл. 8.11.
Коэффициент цикличности капитального ремонта равен:
(8.25)
где – годовой период работы станка;
2,55 – ремонтный цикл в годах.
|
Коэффициент цикличности текущих ремонтов равен:
(8.26)
где 12 – число месяцев в году;
6 – длительность межремонтного периода в месяцах.
Коэффициент цикличности осмотров равен:
(8.27)
Годовая программа капитальных ремонтов:
ремонтных единиц.
Годовая программа текущих ремонтов:
ремонтные единицы,
где 2 – коэффициент цикличности текущих ремонтов;
0,12 – коэффициент перехода от текущего ремонта к капитальному.
Годовая программа осмотров:
ремонтных единицы,
где 2,35 – коэффициент цикличности осмотров;
0,018 – коэффициент перехода от капитального ремонта к осмотру.
Производственная годовая программа ремонта условного парка станков МЗ-3 в ремонтных единицах представлена в табл. 8.12.
Трудоемкость в чел.-ч (человеко-часах) ремонтных работ определяется по выражению:
, (8.28)
где – норма трудоемкости в чел.-ч на 1 Чм (или 1 Чэ), то есть одну ремонтную единицу;
– годовая программа в ремонтных единицах.
При ремонте электрической части годовая программа может быть выражена через
Трудоемкость ремонта и полного планового осмотра оборудования представлена в табл. 8.13.
Ремонт электронных устройств ЧПУ выполняется по потребности (по мере появления отказов).
По станкам с ЧПУ подсчитать годовые суммы планируемого оперативного времени работы(в ч.) отдельно по каждой из групп устройств ЧПУ – и определить суммарную трудоемкость устранения потока их отказов на год
по формуле:
, (8.29)
где – нормы трудоемкости устранения потока отказов на 1000 ч оперативного времени работы устройств соответствующей группы.
Учитывая, что устройства с ЧПУ современных станков построены по принципу ЭВМ, в табл. 8.14 приведены величины трудоемкости ремонта подобных электронных устройств ЧПУ.
Таблица 8.11
График планово-предупредительного ремонта оборудования (станка МЗ-3)
Год | Месяц и вид ремонтных работ | |||||||||||
1 | 2 | 3 | 4 | 5 | 6 | 7 | 8 | 9 | 10 | 11 | 12 | |
2007 | КР | ТР | ||||||||||
2008 | ТР | ТР | ||||||||||
2009 | ТР | КР |
Таблица 8.12
Производственная программа по ремонту оборудования
|
Наименование оборудования | Исходные данные | Ремонтный цикл | Коэффициенты цикличности | Годовая программа в ремонтных единицах | |||||||
Количество единиц оборудования, шт. | Ремонтосложность единицы оборудования, р. е. | Количество ремонтных единиц | Длительность цикла, год | Структура ремонтного цикла *) | Капитальный ремонт | Текущий ремонт | Осмотры | Капитальный ремонт | Текущий ремонт | Осмотры | |
Станок для заточки твердосплавных пластин МЗ-3 | 50 | 6 | 300 | 2,55 | К1 Т4 О5 | 0,39 | 2 | 2,35 | 117,0 | 72,0 | 12,7 |
*) – капитальный ремонт – 1 раз;
– текущий ремонт – 4 раза;
– осмотр – 5 раз.
Таблица 8.13
Трудоемкость ремонта и осмотра оборудования
Вид работ | Капитальный ремонт | Средний ремонт | Текущий ремонт | Плановый осмотр | |
Перед внутрицикловым ремонтом | Перед капитальным ремонтом | ||||
Норма трудоемкости, чел.-ч на 1 Чм и на 1 Чэ | |||||
Механическая часть | |||||
Станочные | 14,0 | 3,0 | 2,0 | 0,1 | 0,1 |
Слесарные и прочие | 36,0 | 6,0 | 4,0 | 0,75 | 1,0 |
Всего | 50,0 | 9,0 | 6,0 | 0,85 | 1,1 |
Электрическая часть | |||||
Станочные | 2,5 | - | 0,3 | - | - |
Слесарные и прочие | 10,0 | - | 1,2 | 0,2 | 0,25 |
Всего | 12,5 | - | 1,5 | 0,2 | 0,25 |
В форме табл. 8.15. в качестве примера приведены результаты расчета годовой трудоемкости ремонтных работ механической части условного парка промышленного оборудования.
По такой же форме приводятся результаты расчетов годовой трудоемкости ремонтных работ электрической части оборудования. Следует отметить, что может быть представлена таблица, учитывающая одновременно результаты расчетов трудоемкости ремонтов и механической и электрической частей.
Таблица 8.14
Трудоемкость ремонта и технического обслуживания отдельных групп электронных устройств ЧПУ
№ группы | Конструктивная группа устройств ЧПУ | Тип устройства ЧПУ | Норма трудоемкости ремонта на 1000 ч оперативного времени работы устройств, чел.-ч | Норма трудоемкости ТО на 1000 ч оперативного времени работы устройств, чел.-ч | |
планового | непланового | ||||
1 | Контурная и комбинированная с перфолентой и линейно-круговым интерполятором, а также построенная на базе микроЭВМ и микропроцессоров | Фанук 2000С, 2П62-ЗИ, П321-М, К-5П, Н221М, 1Р22, Н322М, Н-531, СП22-1М, 2С42, 2У92, У221, 2Р32, У522, УМС, ЭМ907, К1-03, 2М-43, НЦ-31, БОШ МИКРО-5, Люмо-61, Луч-430,2М30 | 98 | 62,6 | 2,2 |
2 | Универсальная, построенная по принципу ЭВМ | Н-551, О551, Н55-2Л, Синумерик 0551 7т, Алкатель, Н55-2М | 133 | 90,4 | 2,9 |
|
Таблица 8.15
Годовая трудоемкость ремонтных работ механической части
оборудования (на примере условной годовой программы работ
в ремонтных единицах)
Вид работ | Годовая программа, рем. ед. | Норма и суммарная трудоемкость, чел.- ч | |||
слесарные и прочие работы | станочные работы | ||||
Норма на 1чм | Трудоемкость | Норма на 1чм | Трудоемкость | ||
Капитальный ремонт | 402 | 36,0 | 14472 | 14,0 | 5628 |
Текущий ремонт | 1608 | 4,0 | 6432 | 2,0 | 3216 |
Осмотр | 2010 | 1,0 | 2010 | 0,1 | 201 |
Итого | 22914 | 9045 |
Структуру цикла технического обслуживания (ТО) изображают в виде суммы входящих в него операций. Виды ТО, производимые неремонтным персоналом (станочниками, уборщиками), в структуру цикла не включают. Например, структуру цикла ТО, включающего ежесменный осмотр четыре пополнения смазочного материала
две профилактические регулировки
один частичный осмотр
и ежесменное смазывание
записывают так:
Продолжительность цикла ТО и продолжительность межремонтного периода
равны между собой, так как все операции планового ТО выполняются между двумя последовательными плановыми ремонтами.
Межоперационный период обслуживания – это период оперативного времени работы оборудования между двумя последовательно выполняемыми операциями планового ТО. Период между двумя последовательными плановыми осмотрами называется межосмотровым периодом
. Структуры циклов ТО, кроме плановых осмотров, устанавливают по данным карт планового технического обслуживания.
Определение трудоемкости технического обслуживания оборудования производится по следующей методике.
Трудоемкость ТО механической части каждого из видов оборудования – составляет:
(8.30)
где – ремонтосложность оборудования;
– оперативное время работы оборудования на планируемый год;
– сумма норм трудоемкости планового технического обслуживания 1 Чм механической части оборудования одного вида слесарями, смазчиками и станочниками на 1000 ч оперативного времени работы оборудования, чел.-ч;
– то же непланового технического обслуживания;
– нормы трудоемкости полного осмотра и осмотра перед капитальным ремонтом механической части оборудования, чел.-ч/1 Чм;
– сумма
оборудования, проходящего полный ос-мотр;
– сумма
оборудования, проходящего осмотр перед капитальным ремонтом;
– сумма
оборудования, подвергаемого консервации;
– нормы трудоемкости на консервацию, чел.-ч/1 Чм.
|
Трудоемкость осмотров может быть учтена при определении трудоемкости ремонтов, как это показано в табл. 8.15.
Трудоемкость технического обслуживания слесарями, смазчиками и станочниками приведена в табл. 8.16–8.18.
Таблица 8.16
Трудоемкость технического обслуживания слесарями
Вид обслуживания | Норма трудоемкости на 1 Чм за 1000 ч оперативного времени работы оборудования, чел.-ч | ||||
металлорежущие станки | Кузне-чное | прессовое | литейное | деревообрабатывающее | |
Плановое техническое обслуживание | 2,37 | 4,54 | 2,58 | 6,08 | 2,00 |
Неплановое техническое обслуживание | 0,83 | 1,25 | 1,25 | 1,46 | 0,73 |
Норма планового и непланового обслуживания | 3,20 | 5,79 | 3,83 | 7,54 | 2,73 |
Таблица 8.17
Трудоемкость технического обслуживания смазчиками
Вид обслуживания | Норма трудоемкости на 1 Чм за 1000 ч отработанного оборудования, чел.-ч | |||||
металлорежущие станки | кузне-чное | прессовое | литейное | деревообрабатывающее | ||
без ЧПУ | с ЧПУ | |||||
Плановое техническое обслуживание | 1,21 | 0,92 | 1,40 | 1,40 | 1,25 | 1,10 |
Неплановое техническое обслуживание | 0,21 | 0,21 | 0,31 | 0,31 | 0,31 | 0,21 |
Норма планового и непланового обслуживания | 1,42 | 1,13 | 1,71 | 1,71 | 1,56 | 1,31 |
Таблица 8.18
Трудоемкость технического обслуживания станочниками
Вид обслуживания | Норма трудоемкости на 1 Чм за 1000 ч, отработанных оборудованием, чел.-ч. | Норма обслуживания рем. ед. | ||
плановое ТО | неплановое ТО | плановое ТО | неплановое ТО | |
Металлорежущее и деревообрабатывающее | 0,52 | 0,21 | 1920 | 4800 |
Металлорежущее с ЧПУ | 0,40 | 0,16 | 2526 | 600 |
Кузнечное | 0,77 | 0,33 | 1297 | 3000 |
Прессовое | 0,52 | 0,21 | 0,391920 | 4080 |
Литейное | 0,94 | 0,39 | 1067 | 2526 |
К нормам трудоемкости на плановое ТО оборудования должны применяться следующие поправочные коэффициенты: при обслуживании оборудования в разных цехах норму времени умножать на 1,10; при ТО оборудования, проработавшего от двух до четырех ремонтных циклов, норму времени умножать на 1,05, а в случаях свыше четырех ремонтных циклов – на 1,10.
Техническое обслуживание бездействующего оборудования – это его консервация. Норма трудоемкости на консервацию (расконсервацию) – 0,2 чел.-ч/1 Чм.
Трудоемкость ТО электрической части оборудования – определяется по формуле:
(8.31)
где и
– нормы трудоемкости планового и непланового ТО 1 Чэ электрической части оборудования одного вида электриками на 1000 ч оперативного времени работы, чел.-ч;
и
– нормы трудоемкости полного осмотра и осмотра перед капитальным ремонтом электрической части оборудования, чел. - ч/1 Чэ.
– сумма
оборудования, проходящего полный осмотр;
– сумма
оборудования, проходящего осмотр перед капитальным ремонтом.
Нормы трудоемкости технического обслуживания электриками представлены в табл. 8.19.
Таблица 8.19
Трудоемкость ТО электриками
Вид технического обслуживания | Норма трудоемкости на 1 Чэ за 1000 ч, отработанных оборудованием, чел.-ч | |||
металлорежущее и деревообрабатывающее | кузнечное | прессовое | литейное | |
Суммарная норма планового обслуживания | 1,02 | 1,29 | 1,17 | 1,27 |
Неплановое техническое обслуживание | 0,31 | 0,42 | 0,42 | 0,42 |
Норма планового и непланового ТО | 1,33 | 1,71 | 1,59 | 1,69 |
Трудоемкость технического обслуживания устройств ЧПУ – определяется по следующей формуле:
, (8.32)
где – норма трудоемкости планового и непланового (суммарного) технического обслуживания устройств ЧПУ
-й группы на 1000 ч оперативного времени работы, приведенная в табл. 8.14.
– оперативное время работы
-й группы устройств ЧПУ.
Трудоемкости ремонта и технического обслуживания других видов оборудования (например, самой ремонтной базы) принимаются равными 7% от трудоемкости ремонта и обслуживания основного оборудования.
Трудоемкость работ по монтажу оборудования, изготовлению технологической оснастки, а также выполнению прочих работ принимаются каждая равной 5%от трудоемкости ремонта и технического обслуживания основного оборудования.
|
|
Автоматическое растормаживание колес: Тормозные устройства колес предназначены для уменьшения длины пробега и улучшения маневрирования ВС при...
Своеобразие русской архитектуры: Основной материал – дерево – быстрота постройки, но недолговечность и необходимость деления...
Индивидуальные и групповые автопоилки: для животных. Схемы и конструкции...
Общие условия выбора системы дренажа: Система дренажа выбирается в зависимости от характера защищаемого...
© cyberpedia.su 2017-2024 - Не является автором материалов. Исключительное право сохранено за автором текста.
Если вы не хотите, чтобы данный материал был у нас на сайте, перейдите по ссылке: Нарушение авторских прав. Мы поможем в написании вашей работы!