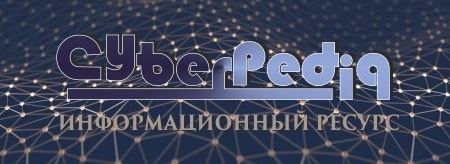
Особенности сооружения опор в сложных условиях: Сооружение ВЛ в районах с суровыми климатическими и тяжелыми геологическими условиями...
Своеобразие русской архитектуры: Основной материал – дерево – быстрота постройки, но недолговечность и необходимость деления...
Топ:
Когда производится ограждение поезда, остановившегося на перегоне: Во всех случаях немедленно должно быть ограждено место препятствия для движения поездов на смежном пути двухпутного...
Отражение на счетах бухгалтерского учета процесса приобретения: Процесс заготовления представляет систему экономических событий, включающих приобретение организацией у поставщиков сырья...
Проблема типологии научных революций: Глобальные научные революции и типы научной рациональности...
Интересное:
Национальное богатство страны и его составляющие: для оценки элементов национального богатства используются...
Принципы управления денежными потоками: одним из методов контроля за состоянием денежной наличности является...
Влияние предпринимательской среды на эффективное функционирование предприятия: Предпринимательская среда – это совокупность внешних и внутренних факторов, оказывающих влияние на функционирование фирмы...
Дисциплины:
![]() |
![]() |
5.00
из
|
Заказать работу |
|
|
окружающего воздуха 20 °С
Материал труб и соединительных деталей | Температура инструмента в начале сварки, °С | Продолжительность нагрева, с, при толщине стенок труб, мм | Продолжительность охлаждения сварного соединения, мин. при толщине стенок труб, мм | |||||||
2 | 3 | 4 | 6 | 8 | 12 | 2-3 | 4-5 | 10-12 | ||
ПВД | 300±15 | 3-6 | 4-8 | 5-10 | 6-12 | 8-15 | 15-20 | 1-1,5 | 1,5-3 | 3-5 |
ПНД | 260±10 | 4-5 | 8-12 | 10-20 | 15-30 | 20-40 | 30-50 | 1-2 | 2-5 | 5-10 |
ПП | 270±10 | 6-8 | 8-12 | 12-15 | 15-30 | 30-50 | 45-60 | 1-2 | 2-5 | 5-10 |
Порядок выполнения работы
Подготовить к сварке образцы трубы из ПЭНД (ПЭВД), для чего их торцы обработать с помощью ножовочного полотна или напильника.
Подобрав по толщине стенки трубы и марки материала оптимальные величины параметров режима (Тн, Ропл, Рос, tопл, tос), выполнить сварку.
После остывания сваренного стыка выпилить участок трубы дли иной 100 м со швом по середине и разрезать его вдоль оси трубы на образцы с толщиной, равной толщине стенки трубы (рис. 6)
Образцы на разрывной машине РП-100 испытать на растяжение и определить прочность сварного соединения стыка в % относительно прочности основного материала.
Рис. 6. Образцы для испытания
Данные занести в табл. 7
Таблица 7
№ образца | ![]() | № образца | s, кГс/см2 | № образца | s, кГс/см2 |
1 | 5 | 9 | |||
2 | 6 | 10 | |||
3 | 7 | 11 | |||
4 | 8 | 12 |
Относительную прочность определить по выражению
,
где - разрывная прочность
-го образца,
- разрывная прочность основного материла,
- количество образцов.
Выполнить сварку образцов в раструб при помощи муфт. Образцы после сварки распилить вдоль образующее и оценить качество сварки.
Контрольные вопросы
1. Назовите основные параметры режима процессов контактно-тепловой сварки термопластов оплавлением и проплавлением.
|
2. Опишите физическую сущность образования сварного соединения при контактно-тепловой сварке.
3. Укажите различие в физических свойствах термопластичных и термореактивных полимеров, приведите примеры.
4. Какие дефекты сварных соединений характерны для контактно-тепловой сварки.
5. Назовите основные преимущества и недостатки контактно-тепловой сварки.
Лабораторная работа 3.
Сварка пластмасс инфракрасным излучением
Цель работы
Изучить сущность процесса, методику нахождения оптимальных режимов и контроль качества сварных соединений при сварке полимерных материалов инфракрасным излучением.
Оборудование и материалы
1. Сварочное устройство ПИЛАД-220 и приспособления
2. Разрывная машина РП-100
3. Инструменты для подготовки образцов (ножницы, штангенциркуль, линейка)
4. Полимерный листовой материал (ПВХ, линолеум), полимерные пленки.
5. Растворители для обезжиривания образцов (бензин, ацетон, спирт)
Содержание и форма отчета
1. Название и цель работы
2. Описать ход выполнения работы
3. Привести данные, полученные в ходе выполнения работы, схему выполнения работ (экспериментов)
4. Сделать выводы по работе
Общие положения
Физическая сущность сварки ИК излучением заключается в переходе лучистой энергии инфракрасного источника в тепловую внутри свариваемого материала.
ИК лучи подразделяются на деци-микронные (100-10 мкм) и микронные (10-0,76 мкм). Наиболее оптимальная область ИК излучения находится в пределах частот, совпадающих или близких к частотам собственных колебаний звеньев макромолекул. У большинства полимеров максимум поглощающей способности относится к длинам волн выше 2,5-3 мкм. Такое излучение соответствует температуре излучателя около 700 ºС. Однако, интенсивность излучения при этой температуре не высока, в связи с чем, пользуются излучателями с температурой выше 1000 ºС (до 2100-2200 ºС), генерирующими поток широкого спектра частот, а при оценке нагрева учитывают характер поглощения не только самого полимера, но и всевозможных добавок (красителей, пластификаторов, стабилизаторов).
|
В качестве ИК излучателей в настоящее время практическое применение находят силитовые стержни, нагреватели из высокохромистых сталей и кварцевые лампы. Стержневая кварцевая лампа представляет собой газонаполненную трубку из кварцевого стекла с вольфрамовой спиралью. Напряжение питания – 220 В, мощность – до 1 кВт.
Способом сварки ИК излучением сваривают встык трубные заготовки, а также встык и внахлестку листы и пленки из различных полимерных материалов.
Схема устройства для сварки ИК излучением листовых и пленочных материалов представлена на рис.7.
Рис. 7. Оптическая схема устройства «Пилад-220»
Основными параметрами процесса сварки ИК излучением являются мощность излучения (температура нагревателя), время нагрева, или скорость перемещения нагревателя, усилие (давление) сварки. Выбор параметров сварки некоторых термопластичных материалов при одностороннем нагреве с помощью устройства «Пилад-220» (лампы КИ 220-1000, 2 шт.) приведены в табл. 8.
Таблица 8
Материал | Толщина, мм | Напряжение питания ламп, В | Давление после прогрева, МПа | Скорость сварки, м/мин | Зазор, мм |
Линолеум из ПВХ | 1,2 2 | 130-155 180-200 | 0,2 0,6 | 0,5-0,65 0,65-1 | 0,8 1 |
ПЭНД | 1,5 | 200-220 | 0,4 | 0.35-0,5 | 1 |
Пластикат ПВХ | 3 | 190-210 | 0,8 | 0,4-0,65 | 1,8 |
С целью выравнивания температуры по толщине свариваемых встык листов толщиной более 1 мм при одностороннем облучении, используют следующий прием. Листы собирают с зазором в пределах 50-80 % их толщины на подложке из черной микропористой резины; облучают одновременно двумя лампами, установленными параллельно друг другу с рефлекторами, повернутыми под углом 20 ºС к плоскости, перпендикулярной к плоскости соединяемых листов.
При такой схеме нагрева излучение проникает в зазор и, отражаясь от подложки, прогревает корень шва так, что разность температуры на поверхности и в корне шва не превышает 10-15 ºС.
При сварке ИК излучением нагрев соединяемых кромок происходит без внешнего давления. После рас плавления, для получения плотного сварного соединения, кромки прокатывают роликом или специальным формирующим выступом (лапки).
|
Для предотвращения прилипания свариваемого материала к инструменту на зону шва укладывают прозрачную целлофановую (полиацетатную) пленку, либо покрывают рабочие поверхности инструмента слоем фторопласта.
При сварке полимерных пленок их укладывают внахлестку на эластичной подложке из микропористой резины. Сварочное давление между соединяемыми пленками создается за счет упругого деформирования подложки. Сварку осуществляют непрерывным способом, перемещая излучатель по поверхности изделия, или перемещая изделие относительно неподвижного источника. Ориентировочные режимы сварки инфракрасным излучением пленок с помощью кварцевой лампы КИ220-1000 приведены в табл. 9.
Таблица 9
Материал пленки | Толщина, мкм | Температура в зоне сварки, ºС | Давление, МПа | Скорость сварки, м/мин |
ПЭВД | 200- 1500 | 210-240 | 0,15-0,2 | 0,3-0,5 |
ПЭНД | 200-1500 | 240-260 | 0,2-0,25 | 0,3-0,4 |
ПВХ | 200-1500 | 240-260 | 0,15-0,2 | - |
Порядок выполнения работы
Изучить конструкцию устройства для сварки ИК излучением, а также правила его эксплуатации по техническому описанию и паспорту.
Произвести измерение температуры в плоскости сварки и построить зависимости температуры от напряжения питания и времени действия излучения.
Для определения оптимальных режимов сварки пленочного материала выполнить сварку образцов при различных температурах нагрева, изменяя напряжение на лампе. Скорость сварки (продолжительность выдержки материала при температуре сварки) поддерживать постоянной согласно табл. 9.
Для сварки подготовить образцы из полиэтиленовой пленки с размерами 300×160 мм.
Перед сваркой поверхности пленки, подлежащие соединению, необходимо очистить от пыли и обезжирить с помощью тканевого тампона, смоченного в бензине или ацетоне.
Сварку произвести с помощью устройства «Пилад-220», с блоком питания, снабженным регулятором напряжения.
Величину сварочного давления в процессе экспериментов поддерживать постоянной и равной 0,05 МПа (0,5 кГс/см2).
Выполнить последовательно сварные швы на образцах при напряжениях, соответствующих температурам нагревателя 150, 180, 210, 240 ºС.
Определение прочности сваренных пленочных образцов на расслаивание и на сдвиг произвести на полосках прямоугольной формы, вырезанных из сваренных образцов. Для каждого вида испытаний вырезать по 4-5 образцов шириной 10 мм.
|
Испытания производить на разрывной машине WPМ со скоростью перемещения подвижного зажима равной 100 мм/мин.
Прочность на расслаивание и сдвиг вычислить из соотношений:
и
,
где P – разрушающее усилие, Н; b – ширина образца, см.
Результаты испытаний внести в табл. 10.
Таблица 10
Режим сварки | Прочность, МПа | ||
Температура, ºС | Продолжительность | При расслаивании | При сдвиге |
Контрольные вопросы
1. Назовите основные параметры режима процесса сварки ИК излучением полимерных пленок и листовых полимерных материалов.
2. Опишите физическую сущность образования сварного соединения при сварке ИК излучением.
3. Укажите различие в технологических схемах сварки ИК излучением листовых материалов и пленок.
4. Какие дефекты сварных соединений сварки полимерных материалов инфракрасным излучением.
5. Назовите основные преимущества сварки ИК излучением.
Лабораторная работа 4.
Сварка полимерных материалов газовым
теплоносителем
Цель работы
Изучить сущность процесса, ознакомиться с методикой определения основных технологических параметров и контроля качества сварных соединений при сварке полимерных материалов с помощью газового теплоносителя.
Оборудование и материалы
1. Электрическая горелка ГЭП-2 с воздухонагнетателем
2. Лабораторный автотрансформатор
3. Ручной аппарат ТРИАК S
4. Приспособление для крепления заготовок.
5. Термометр для замера температуры газа.
6. Образцы винипласта или полиэтилена с размерами 70×100 мм, толщиной 3-6 мм.
7. Присадочный пруток.
8. Ножовка по металлу
Содержание отчета
1. Название и цель работы
2. Описание хода выполнения работы
3. Эскизы образцов, подготовленных к испытаниям
4. Таблица полученных опытным путем данных
5. Выводы по работе
Общие положения
Сущность процесса сварки с применением газового теплоносителя заключается в том, что свариваемые поверхности и присадочный пруток нагреваются в зоне сварки до температуры вязкотекучего состояния полимера газовой струей, выходящей из сопла сварочной горелки. Одновременно, присадочный пруток подают в разделку кромок, образуя, после охлаждения, сварной шов. Присадочный пруток подается в зону сварки с заданным усилием и одновременным перемещением в направлении сварки.
В качестве оборудования для сварки используют отечественные электрические горелки типа ГСП-2 или импортные устройства типа TRIAC-S (рис 8).
|
Рис.8 Сварочное устройство TRIAC-S
1 – сопло, вставляемое 2- винт, 3 труба нагревательного элемента для вставляемого сопла, 4 охлаждаемая защитная труба, 5- температурная шкала, 6 резиновая опора, 7 –шнур присоединения сети, 8 – выключатель сети, 9 – вентилятор, 10 – потенциометр настройки температуры.
Образование соединения между прутком и кромками происходит за счет диффузионных процессов в поверхностных слоях разогретого до температуры сварки полимерного материала и образования химических и межмолекулярных связей между макромолекулами соединяемых поверхностей.
Параметрами сварки являются: температура сварки полимера, толщина свариваемых деталей, диаметр присадочного прутка, угол раскрытия (разделки) кромок свариваемых поверхностей, усилие подачи присадочного прутка, температура и расход нагретого газа, скорость подачи присадочного прутка, скорость сварки, диаметр сопла сварочной горелки, расстояние между наконечником сварочной горелки и нагреваемыми поверхностями в зоне сварки (рис. 9).
Рис. 9. Схема процесса сварки полимеров с применением
газового теплоносителя
Температура сварки для различных полимеров определяется их свойствами и устанавливается температурой струи газа на выходе из наконечника (сопла) сварочной горелки.
Обычно эта температура на 50-100 ºС превышает температуру, до которой необходимо нагреть свариваемые поверхности. Превышением температуры компенсируют потери тепла газовой струей между соплом и поверхностью материала. Расстояние между наконечником и поверхностью сварного шва поддерживают равным 5-8 мм. Изменение этого расстояния вызывает колебания температуры нагрева основного материала и присадочного прутка.
Ориентировочные значения температур сварки приведены в табл. 11.
Таблица 11
Материал | Температура, ºС | |
на свариваемых поверхностях | газа на выходе из сопла | |
Поливинилхлорид жесткий | 180-210 | 200-260 |
Поливинилхлорид пластифицированный | 160-230 | 180-280 |
ПЭНД | 200-250 | 300 |
ПЭВД | 180-230 | 300 |
Полипропилен | 210-250 | 300 |
Полиметилметакрилат | 210-250 | 300 |
Полиизобутилен | 200 | 300 |
Поливинилиденхлорид | 185-200 | 280-315 |
Практически, температура газа подбирается перед сваркой путем нагрева полимера. При недогреве отсутствует сцепление и пруток легко отслаивается от свариваемых поверхностей, а при перегреве полимер либо изменяет цвет, либо начинает выделять газообразные продукты разложения. Регулировку температуры нагретой газовой струи осуществляют путем изменения напряжения питания нагревательного элемента, или путем изменения расхода газа с помощью вентильного устройства горелки или сменой рабочего наконечника.
В качестве газа-теплоносителя чаще всего используют воздух, как наиболее дешевый газ. При сварке полимеров, склонных к активной термоокислительной деструкции (полиамиды, пропилен, полиметилметакрилат), рекомендуется применять инертные газы – аргон, гелий. Применяют также азот и углекислый газ.
При ручной сварке присадочный пруток применяют преимущественно круглого сечения с диаметром 2-4 мм, или в виде двух спаренных прутков диаметром 3-4 мм. Диаметр прутка выбирается в зависимости от толщины и угла разделки кромок свариваемых деталей. Для заполнения корня шва применяют пруток диаметром 2 мм, а для заполнения разделки кромок - диаметром 4 мм. Применять прутки диаметром более 4 мм при ручной сварке не рекомендуется.
При отсутствии промышленных присадочных прутков присадку изготавливают из свариваемого полимера в виде полосок с сечением 3×3, 3×4, 2×4 мм.
Подачу и укладку присадочного прутка при ручной сварке осуществляют вручную, придерживая его на расстоянии 60-80 мм от зоны сварки.
При чрезмерном усилии на пруток по бокам уложенного прутка наблюдаются большие наплывы выдавленного полимера, при недостаточном усилии наплывы отсутствуют совсем. При правильно выбранном усилии по бокам уложенного прутка наблюдают тонкие ниточные наплывы без признаков разложения полимера. Экспериментально установлено, что оптимальное значение удельного давления подачи прутка должно быть для полиэтилена – 0,2-0,25 МПа, для поливинилхлорида – 0,2-0,35 МПа, для полипропилена – 0,35 МПа, для полиметилметакрилата – 0,4 МПа. В зависимости от диаметра прутка величина усилия подачи для жесткого поливинилхлорида (винипласта) может быть выбрана по табл. 12.
Таблица 12
Диаметр прутка, мм | 2 | 3 | 4 | 5 |
Усилие подачи прутка, Н | 1 | 1,4-1,6 | 2,2-2,5 | 2,8-3 |
Перед началом сварки конец присадочного прутка необходимо срезать под острым углом. Затем место начала шва нагревают до температуры сварки. После чего, в зону нагрева вносят срезанный конец присадочного прутка. Он быстро нагревается и под действием усилия подачи сваривается с основным материалом в разделке кромок свариваемых поверхностей.
При сварке жестких полимеров (ПВХ, ПЭНД и др.), присадочный пруток подается перпендикулярно к свариваемым поверхностям. При увеличении угла в сварном шве возникают усадочные напряжения, при уменьшении же угла пруток нагревается до температуры сварки быстрее основного материала и теряет устойчивость, что затрудняет его правильную укладку в разделку кромок. При сварке мягких полимеров присадочный пруток подается под углом 110-140º.
При нагреве свариваемых поверхностей и присадочного прутка, соплу сварочной горелки придают колебательные движения, направляя газовую струю поочередно на основной материал и на присадочный пруток. Для обеспечения равномерного нагрева зоны сварки газовая струя большую часть общего времени должна быть направлена на основной материал (2/3). Угол наклона горелки по отношению к свариваемым поверхностям должен составлять 45º.
При сварке пластмасс нагретым газом применяют стыковые швы всех видов, угловые, тавровые, торцевые и швы внахлестку. Швы без разделки кромок применяют при сварке деталей толщиной менее 2 мм, но при этом между деталями оставляют зазор 1-1,5 мм.
Порядок выполнения работы
Сварку выполнять горелкой ГЭП-2 с нагнетателем воздуха в виде центробежного вентилятора. Температуру газа регулировать подбором наконечника и изменением напряжения питания электрической спирали сварочной горелки.
Внимание! Напряжение на спираль сварочной горелки подавать только при включенной подаче газа.
Замер температуры газа производить с помощью термометра, или термопары при фиксированном положении сварочной горелки. Изменяя напряжение питания спирали горелки, построить кривую зависимости напряжение–температура.
Для сварки встык нарезать пластины с размерами 745×100 мм толщиной 3‑5 мм. На одной из длинных сторон с помощью напильника срезать кромку под углом 30º. После зачистки мест сварки наждачной бумагой и обезжиривания бензином, пластинки зажать в приспособление, согласно рис. 10.
Рис. 10. Схема расположения образца перед сваркой встык
Выполнить сварку, укладывая присадочный пруток согласно правилам (см. Общие положения).
Определить изменение ударной вязкости сварных образцов. Испытание провести на маятниковом копре.
Метод заключается в разрушении образца, установленного горизонтально на двух опорах, ударом маятника поперек образца. Удар маятника должен приходиться по середине образца по всей его ширине. Перед испытанием измерить угол отклонения маятника на холостом ходу. Для чего стрелку шкалы установить в начальном положении и дать маятнику свободно падать из его верхнего положения.
Для испытаний сваренные образцы разрезать поперек шва на полоски шириной 6 ± 0,2 мм. Полученные образцы разделить на две равные части, одну из которых подвергнуть испытанию на удельную вязкость. Маятник поднять в верхнее исходное положение и закрепить его защелкой. Затем установить стрелку шкалы в нижнее положение и освободить маятник, давая ему свободно падать. После разрушения образца маятник остановить и отсчитать по шкале работу, затраченную на разрушение образца.
Затраченную работу А рассчитать по формуле:
,
где - вес маятника, кГс; L - длина маятника, см;
- угол зарядки маятника, град;
- угол взлета маятника после разрушения образца, град;
- угол взлета маятника при холостом ходу, град.
Удар производить по образцу один раз. Ударную вязкость образца без надреза рассчитать по формуле:
,
где - работа, затраченная на разрушение образца, кгм,
- толщина и ширина образца по его середине, м.
Испытания произвести для образцов, сваренных с различной температурой нагретого газа, а также образцов исходного материала.
Вторую половину образцов, полученных разрезанием сваренной заготовки, подвергнуть испытаниям на растяжение для определения предела прочности по ГОСТ 11262-80.
Результаты всех испытаний занести в табл. 13.
Таблица 13
Температура сварки | Ударная вязкость сварных образцов | Ударная вязкость образцов материала | Предел прочности сварных образцов | Предел прочности исходного материала |
Определить коэффициенты относительной прочности и ударной вязкости
,
,
где – предел прочности при растяжении сварных соединений и основного материала соответственно,
– ударная вязкость сварного соединений и основного материал соответственно.
На основании анализа полученных данных определить оптимальную величину температуры сварки, остальных параметров режима.
Выполнить по заданию преподавателя сварку конкретного изделия или образцов материалов с применением выбранного оптимального режима.
Контрольные вопросы
1. Объяснить сущность процесса сварки с применением газового теплоносителя.
2. Как выбирается температура газа-теплоносителя.
3. По каким признакам можно определить при внешнем осмотре качество сварного шва.
4. Как подобрать присадочный пруток для сварки.
5. Перечислить газы, которые применяются в качестве теплоносителя, охарактеризовать их.
6. Преимущества и недостатки метода, область его применения.
Лабораторная работа 5.
Ультразвуковая сварка полимерных материалов
Цель работы
Изучить сущность процесса, ознакомиться с методикой определения оптимальных параметров режима при ультразвуковой сварки полимерных материалов.
Оборудование и материалы
1. Установка для прессовой ультразвуковой сварки пластмасс МТУ-1,5 с источником питания УЗГ1-1.
2. Лабораторная установка для ультразвуковой сварки пленочных материалов.
3. Электросекундомер.
4. Скоба для замера сварочного усилия
5. Образцы полимерных материалов (полистирол, полиэтилен, винипласт, полиметилметакрилат).
6. Ножовка, наждачная бумага.
7. Шлифовальный круг.
8. Микроскоп МБС-9.
9. Реактивы для обработки шлифов
Содержание и форма отчета
1. Название и цель работы
2. Описание хода выполнения работы.
3. Схемы ультразвуковой сварки пластмасс.
4. Выводы по работе.
Общие положения
Ультразвуковая сварка полимерных материалов основана на разогреве пластмассовых деталей механическими колебаниями ультразвуковой частоты (свыше 16 кГц). Из-за наличия в полимерных материалах двух типов связей - сильных химических и относительно слабых межмолекулярных, материал воспринимает колебания не упруго, а вязко, что и обуславливает значительное рассеивание в нем механической энергии и превращение ее в тепловую.
Несовершенство структуры полимера в приповерхностных слоях приводит к тому, что максимум тепловыделения приходится на границу раздела соединяемых деталей. Образующийся при этом слой размягченного температурой материала обладает повышенным коэффициентом поглощения УЗ энергии, в результате чего, полимер плавится преимущественно на соединяемых поверхностях, при сохранении в целом по детали относительно низкой температуры. Таким образом, появляется возможность сваривать детали без плавления всего объема полимера.
Наряду с функцией источника тепловой энергии, выделяющейся непосредственно внутри свариваемых деталей, ультразвуковые колебания обладают также способностью к разрушению и удалению из зоны соединения поверхностных жировых и окисных пленок, а также способностью к интенсивному перемешиванию расплава полимера. Эти особенности воздействия ультразвука на полимер делают процесс сварки высокопроизводительным и обеспечивающим высокое качество сварных соединений многих полимерных материалов.
Хорошей и удовлетворительной свариваемостью любыми способами обладают полимеры, способные переходить при нагреве в вязко-текучее состояние и сохранять в нем свои физические свойства в достаточно широком интервале температур.
Необходимым условием для получения качественных соединений при ультразвуковой сварке, полимеры, кроме указанных выше свойств, должны обладать упругими свойствами, которые обычно характеризуются модулем упругости полимера E или коэффициентом . Указанные свойства полимера определяют глубину проникновения УЗ колебаний в деталь без существенных потерь энергии.
В зависимости от этих свойств полимеры условно подразделяют на три группы: жесткие (E > 2×103 МПа), мягкие (E < 2×103 МПа) и промежуточной группы (E = 2×103 МПа).
К первой группе относят, в частности, полистирол (ПС), полиметилметакрилат (ПММА), которые могут быть сварены без расплавления всего объема полимера под волноводом на значительном удалении места ввода УЗК от соединяемых поверхностей. Такую сварку называют сваркой в дальнем поле или передаточной.
Мягкие полимеры (полиэтилен, пластифицированный ПВХ) могут быть сварены при толщине детали, через которую передаются ультразвуковые колебания, не более 5 мм.
Для полимеров промежуточной группы (винипласт, поликарбонаты, полиамиды) передаточная сварка (на большом удалении волноводов), хотя и возможна, однако затруднена перегревом верхней детали, ее чрезмерной деформацией.
Основными параметрами режима ультразвуковой сварки являются: амплитуда колебаний (смещений) рабочего торца волновода A, частота f, продолжительность ультразвукового импульса или скорость сварки v в случае непрерывной сварки и величина сварочного (статического) давления
, или усилие прижима волновода к материалу.
Все основные параметры режима взаимосвязаны. Время, необходимое для сварки, зависит от амплитуды колебаний и сварочного давления. При более высоких амплитудах прочные сварные соединения могут быть достигнуты при меньшем времени сварки и наоборот.
Зависимость прочности сварных соединений от амплитуды колебаний выражается кривой с максимумом, соответствующим ее оптимальному значению. При амплитудах меньших оптимальных, вводимой механической энергии недостаточно для образования сварных соединений. Увеличение ее значения выше оптимального приводит к разогреву материала под волноводом, что может сопровождаться выдавливанием расплава и деструкцией (термическим разложением) полимера. Оптимальное значение амплитуды колебаний рабочего торца волновода на стандартной частоте 22 кГц обычно принимают равным 30-40 мкм.
Величина сварочного давления определяется в первую очередь механическими свойствами свариваемого полимера и должна с одной стороны обеспечить надежный акустический контакт на границе волновод – свариваемая деталь, с другой стороны, не вызывая чрезмерной деформации материала в зоне сварки, обеспечить совместное течение расплава полимера на соединяемых поверхностях. Для большинства полимеров величины сварочного давления лежат в пределах от 0,1 до 0,5 МПа.
Максимальная прочность сварных соединений достигается при времени включения ультразвуковых колебаний в пределах 0,1-2 сек.
Ультразвуковая сварка изделий из полимерных материалов подразделяется на две технологические схемы: прессовую и шовную (рис. 11).
а) б)
Рис.11. Схемы ультразвуковой сварки пластмасса) прессовая; б) шовная
При УЗС по прессовой схеме неподвижные детали зажимают между ультразвуковым инструментом - волноводом и его опорой. После этого включают УЗК, полимер разогревается до температуры сварки, а после отключения УЗК - остывает под давлением, образуя сварное соединение.
Наиболее распространенным видом шовной ультразвуковой сварки является сварка по схеме «напротяг», при которой свариваемый полимерный материал (пленка, синтетическая ткань) протягиваются в зазоре между ультразвуковым инструментом-волноводом и опорой. Опора, при этом выполняется в виде свободно вращающегося на оси, или снабженного приводом опорного ролика. Время ультразвукового воздействия на материал определяется шириной ультразвукового инструмента и скоростью вращения опорного ролика, линейное значение которой совпадает со скоростью сварки.
Порядок выполнения работы
Изучить влияние параметров режима ультразвуковой сварки на прочность сварного соединения. Включить, согласно инструкции по эксплуатации, машину МТУ-1,5 и генератор УЗГ1-1, установить ориентировочные режимы сварки: регулировкой мощности генератора установить последовательно мощности, соответствующие амплитудам инструмента – 10,20 и 30 мкм.
Регулировкой воздушного редуктора установить по манометру оптимальное в зависимости от свариваемого материала сварочное давление в пределах от 2,0 до 2,5 кг/см2.
С помощью регулятора циклов сварки машины (РЦС) для каждого значения амплитуды колебаний инструмента установить три значения времени пропускания ультразвуковых колебаний в пределах от 0,2 до 2 сек.
Форму подготовки образцов, в зависимости от свариваемого материала, выбрать по указанию преподавателя.
Сваренные образцы испытать на растяжение на машине РП-100. Результаты испытаний внести в табл. 14 и оценить влияние различных параметров на прочность соединений.
Таблица 14
Свариваемый материал | Режим сварки | Разрушающая нагрузка | Примечания (дефекты шва) | |||
Амплитуда, мкм | Давление, МПа | Продолжит.УЗК, с | при растяжении | при сдвиге | ||
Изучить внутреннее строение сварного шва с помощью оптического микроскопа. Для чего из сваренного образца вырезать пластину шириной 10 мм и длиной 30 мм так, чтобы сварной шов располагается по середине пластины, и зажать ее в струбцине. Образец с прокладками должен выступать под струбцинами на 5 мм.
Выполнить зачистку исследуемой поверхности наждачной бумагой, смачивая ее водой, затем поверхности отполировать фетровым или бархатным кругом с помощью полировочной пасты до исчезновения рисок на поверхности образца.
Произвести травление поверхности при 60 ºС в течение 1-2 мин, в растворе из циклогексана (30 мл), муравьиной кислоты (50 мл) и эталона (20 мл). Шлифы рассмотреть в микроскопе МБС-9. Выявить наличие границы раздела и дефектов в сварном шве.
Ознакомиться с технологическими особенностями подбора режимов при шовной ультразвуковой сварке пленочных материалов «напротяг». На образцах пленочного материала (полиэтилен, поливинилхлорид, полиэтилентерефталат), пользуясь инструкцией по работе на сварочной лабораторной установке, подобрать ориентировочный режим сварки по внешнему виду и испытанием шва на отрыв вручную.
На подобранных режимах выполнить сварку изделий из пленочного материала по заданию преподавателя. Изделия подвергнуть гидравлическому испытанию на герметичность сварных швов.
Контрольные вопросы
1. Объяснить механизм ультразвуковой сварки пластмасс.
2. Назвать основные параметры процесса и их влияние на прочности сварных соединений
3. Рассказать о разновидностях схем ультразвуковой сварки полимерных материалов.
4. Классифицировать полимерные материалы по возможностям их сварки ультразвуком.
Лабораторная работа 6.
Расчет магнитострикционных акустических головок
Цель работы
Изучить конструктивное устройство акустических головок технологических установок и освоить методику расчета преобразователя стержневого типа.
Материалы и оборудование
1. Ультразвуковые головки типов ПМС1-1, ПМС15-18, ПСМ-6
2. Ультразвуковой генератор УЗГ1-1
3. Ванна для настройки преобразователей
4. Цифровой частотомер Ч3-33
Содержание и форма отчета
1. Название и цель работы
2. Описание хода выполнения работы.
3. Схемы ультразвуковой головки
4. Привести расчет элементов магнитострикционного преобразователя.
5. Выводы по работе.
Общие положения
Ультразвуковая головка технологической установки включает в себя: электромеханический магнитострикционный преобразователь, трансформатор колебаний с диафрагмой крепления, волновод, или сменный рабочий инструмент, корпус – бачок, охлаждаемый проточной водой, электрическую обмотку. (Рис.12)
Рис.12. Ультразвуковая головка
Магнитострикционный преобразователь представляет собой пакет, набранный из пластин толщиной 0,15-0,2 мм. В качеств
|
|
Индивидуальные и групповые автопоилки: для животных. Схемы и конструкции...
История создания датчика движения: Первый прибор для обнаружения движения был изобретен немецким физиком Генрихом Герцем...
Кормораздатчик мобильный электрифицированный: схема и процесс работы устройства...
Организация стока поверхностных вод: Наибольшее количество влаги на земном шаре испаряется с поверхности морей и океанов (88‰)...
© cyberpedia.su 2017-2024 - Не является автором материалов. Исключительное право сохранено за автором текста.
Если вы не хотите, чтобы данный материал был у нас на сайте, перейдите по ссылке: Нарушение авторских прав. Мы поможем в написании вашей работы!