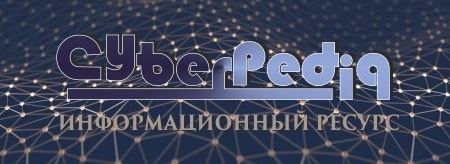
Адаптации растений и животных к жизни в горах: Большое значение для жизни организмов в горах имеют степень расчленения, крутизна и экспозиционные различия склонов...
Типы оградительных сооружений в морском порту: По расположению оградительных сооружений в плане различают волноломы, обе оконечности...
Топ:
Оснащения врачебно-сестринской бригады.
История развития методов оптимизации: теорема Куна-Таккера, метод Лагранжа, роль выпуклости в оптимизации...
Организация стока поверхностных вод: Наибольшее количество влаги на земном шаре испаряется с поверхности морей и океанов...
Интересное:
Искусственное повышение поверхности территории: Варианты искусственного повышения поверхности территории необходимо выбирать на основе анализа следующих характеристик защищаемой территории...
Национальное богатство страны и его составляющие: для оценки элементов национального богатства используются...
Как мы говорим и как мы слушаем: общение можно сравнить с огромным зонтиком, под которым скрыто все...
Дисциплины:
![]() |
![]() |
5.00
из
|
Заказать работу |
|
|
Определение нормы времени на сварку. В условиях промышленности техническое нормирование имеет особое значение,так как является основой для организации труда, его оплаты и планирования производства. Норма времени слагается из следующих элементов:
а) подготовительно-заключительного времени: оно даётся на партию изделий и включает время на получение задания, инструктаж, ознакомление с работой, подготовку и наладку оборудования и приспособлений, сдачу работы;
б) основного или машинного времени, которое дается на деталь или на 1 м шва или реза; основным называется время горения дуги или пламени, затрачиваемое только на процесс сварки или резки, включая и время на разогрев металла в начале резки;
в) вспомогательного времени, учитывающего затраты на смену электродов, промер и осмотр шва, очистку кромок и швов, установку, поворот во время сварки и уборку изделия, клеймение швов, переходы на другое место сварки и пр.;
г) дополнительного времени на обслуживание рабочего места (раскладку и уборку инструмента, смену баллонов, подключение шлангов, регулирование тока и давления газов, зажигание, регулирование и охлаждение горелки), на отдых и естественные надобности.
При установлении норм времени следует исходить из полного учета производственных возможностей цеха (предприятия), наиболее производительных режимов работы оборудования и применения наиболее эффективных для данных условий способов работы и форм организации труда. При этом должен использоваться опыт передовых рабочих-новаторов производства.
Основное время зависит от вида и толщины свариваемого металла, тока, мощности горелки, способа сварки, положения шва в пространстве и квалификации сварщика. При резке основное время зависит от толщины разрезаемого металла и способа резки.
|
Чтобы найти общее время, нужно сначала определить основное время, а затем прибавить к нему затраты времени по пунктам «а», «в», «г».
Основное время определяют по формуле
прощитать.
где t0 — основное время, ч; L — длина шва, см; F — площадь сечения шва, см2;
7,85 — плотность наплавленного металла, г/см3; I— ток, а;
Кп — коэффициент наплавки, г/а ч.
Количество наплавленного металла G в г подсчитывают по формуле G = 7,85F • L. Площади поперечного сечения швов F подсчитывают по чертежам сварных соединений и таблицам.
При многослойной сварке и выполнении разных слоев на различных режимах основное время сварки подсчитывают для каждого слоя отдельно, а затем суммируют.
Полученное время t0 нужно увеличить на 25% при сварке вертикального шва, на 30% для горизонтального и на 60% для потолочного шва.
Подготовительно-заключительное, вспомогательное и дополнительное время при ручной дуговой сварке составляет в процентах от основного времени: для сварки в условиях цеха — от 30 до 50%; для монтажной сварки на строительстве — от 40 до 60%.
При автоматической сварке под флюсом основной величиной является скорость сварки v м/ч, которая задается режимом сварки.
Основное время t0 (ч) при автоматической сварке одного слоя шва длиной L (м) равно:
При многослойных швах полученную величину t0 следует умножить на число слоев (проходов) при сварке.
Вспомогательное время при автоматической сварке (на регулирование режима, установку и снятие изделия и пр.) подсчитывают отдельно для каждой операции с помощью нормировочных таблиц, составленных по данным хронометража этих операций. Сумма вспомогательного и дополнительного времени при автоматической сварке под флюсом может составлять от 60 до 80% основного времени.
Основное время (мин) при газовой сварке подсчитывают по формуле
t0 = К • S мин/м,
где S — толщина свариваемого металла, мм;
|
К — коэффициент, зависящий от рода свариваемого металла.
Значения коэффициента К принимают следующими:
для низкоуглеродистой стали К = 4 -5;
для легированной стали, чугуна, латуни и бронзы К = 6;
для меди К = 3,5;
для алюминия и его сплавов К = 4.
Основное время кислородной резки (мин) подсчитывают по формуле
где L — длина резки, мм
v — скорость резки, мм/мин. Скорость резки берется по данным таблиц режимов резки и в зависимости от способа резки.
К основному времени резки прибавляют время на начальный подогрев металла, относя его к 1 пог. м длины реза пропорционально общей длине реза.
Время на подогрев металла при резке в начальной точке у края листа при использовании ацетилена, составляет для стали толщиной 10—20 мм — 5—10 сек; толщиной 20—100 мм — 7—25 сек; толщиной 100—200 мм — 25—40 сек. При работе на керосине это время нужно увеличить на 30%, а на газах — заменителях ацетилена—на 40—60%.
ОПРЕДЕЛЕНИЕ РАСХОДА ЭЛЕКТРОЭНЕРГИИ, ЭЛЕКТРОДОВ, ФЛЮСОВ И ГАЗОВ
Расход электроэнергии. В зависимости от типа агрегата, применяемого для питания сварочных постов, примерный расход энергии (квтч) на 1 кг наплавленного металла составляет:
Расход электродов и проволоки. Потребность в электродах определяется по общему весу наплавленного металла шва, к которому прибавляют 20—30% для электродов с тонким покрытием и 40—60% для электродов с толстым покрытием. Потребность в электродах в штуках подсчитывают делением общего веса электродов на вес одного электрода с учетом веса покрытия.
Для определения расхода электродной проволоки при сварке под флюсом или в защитном газе подсчитывают вес наплавленного металла, исходя из геометрических размеров шва; затем к полученной величине прибавляют 3%, учитывающие расход проволоки на наладку режима, вывод кратера шва, остаток концов в бухте, обрывы дуги и прочие потери.
Расход флюса. При сварке под флюсом расход его принимают равным 1,13G, где G — расход электродной проволоки, кг.
Для упрощенного подсчета количества наплавленного металла швов, выполненных встык газовой сваркой, можно пользоваться формулой
G = C.S2,
где G — вес наплавленного металла на 1 м шва, Г;
С — коэффициент;
5 — толщина свариваемого металла, мм.
Значения коэффициента С берут по данным табл. 49.
Для определения общего расхода проволоки при газовой сварке к полученному значению С прибавляют 10—15% на потери от угара и разбрызгивания.
|
Расход газов. При газовой сварке, сварке в защитных газах и плазменно-дуговой резке расход газов определяют по Мощности наконечника, размерам сопла и времени сварки и резки, добавляя к полученному общему расходу 5%, учитывающих дополнительные затраты газов на зажигание и регулирование пламени, на прихватки и пр.
Расход кислорода, ацетилена и газов-заменителей на резку определяют по таблицам режимов резки для металла данной толщины.
Основными факторами, влияющими на выбор величины силы тока, являются качество и толщина свариваемого металла и вид соединения. При сварке больших толщин наплавку шва производят в несколько слоев, причём во избежание пережога основного металла первый слой наплавляется электродами меньшего диаметра при меньшей силе тока, чем при наплавлении последующих слоев.
В тех случаях, когда конструкцию при изготовлении расчленяют на отдельные узлы, нормирование работ производят на каждый отдельно собираемый и свариваемый узел, а затем определяют норму времени на общую сборку и сварку конструкции из отдельных узлов. Нормы времени на сборку и на сварку, выражают в человеко-час. или в на одну операцию,, на узел и изделие и устанавливают по элементным нормативам.
В качестве примера приведены таблицы для определения нормы времени на каждую сборочную операцию при сборке балок двутаврового сечения. Нормы времени установлены с учетом изготовления одного узла без применения механизированных приспособлений, применяемых в серийном производстве. В случае применения механизированных приспособлении (кондуктор или стенд) к времени на сборку нужно применить коэффициент, уменьшающий норму времени.
В табличных нормативах на сварку норму времени задают на один погонный метр углового или стыкового данного сечения, а для определения нормы времени- на каждую сварочную операцию предварительно по чертежам подсчитывают количество метров шва данного сечения.
Для определения нормы времени на один погонный метр шва заданного сечения пользуются следующей зависимостью. Коэффициент наплавки берут согласно паспортным данным для принятых электродов. Вес наплавленного металла Р определяют по формуле. В практике нормирования сварочных работ пользуются специальными таблицами. Для примера приведена одна из таблиц с нормами времени на угловые швы. В зависимости от производственных условий к нормам времени могут быть применены различные коэффициенты.
|
7. Контроль качества сварочных работ.
Операционный контроль сварочных работ выполняется производственными мастерами службы сварки и контрольными мастерами службы технического контроля (СТК).
Перед началом сварки проверяется:
наличие у сварщика допуска к выполнению данной работы;
качество сборки или наличие соответствующей маркировки на собранных элементах, подтверждающих надлежащее качество сборки;
состояние кромок и прилегающих поверхностей;
наличие документов, подтверждающих положительные результаты контроля сварочных материалов;
состояние сварочного оборудования или наличие документа, подтверждающего надлежащее состояние оборудования;
температура предварительного подогрева свариваемых деталей (если таковой предусмотрен НТД или ПТД).
В процессе сварки проверяется:
режим сварки;
последовательность наложения швов;
размеры накладываемых слоев шва и окончательные размеры шва;
выполнение специальных требований, предписанных ПТД;
наличие клейма сварщика на сварном соединении после окончания сварки.
Проверка сварных соединений с помощью керосина.
Проверку качества сварных швов и соединений на строительных металлических конструкциях проводят в соответствии с требованиями СНиП III-18-75.
При организации технического контроля сварочных работ следует предусматривать предварительный, пооперационный и окончательный этапы.
Предварительный контроль включает проверку качества сварочных материалов, условия их хранения и подготовки к работе; проверку состояния сварочного и вспомогательного оборудования; контроль квалификации сварщиков; контроль качества сборки и подготовки стыков под сварку.
Пооперационный контроль заключается в систематической проверке правильности выполнения заданного технологического процесса сварки и общих технологических операций.
Окончательный контроль заключается в оценке качества выполненных работ. При окончательном контроле качества сварные соединения могут быть подвергнуты внешнему осмотру и измерениям, различным видам физических методов контроля, механическим испытаниям, металлографическому исследованию и прочим видам испытаний, обеспечивающим достоверную оценку качества конструкций, если такие испытания предусмотрены технологическим процессом или производственной инструкцией по сварке изделия.
|
Внешний осмотр и измерения.
Внешним осмотром контролируют все типы сварных соединений при всех способах сварки всех свариваемых металлов и сплавов.
Внешним осмотром выявляют следующие дефекты: излом и неперпендикулярность осей соединяемых элементов;
отступления по размерам и форме швов от требований стандартов, чертежей, технических условий и инструкций по сварке конструкций;
смещение кромок соединяемых элементов; поверхностные трещины всех видов и направлений; наплывы, подрезы, прожоги, незаверенные кратеры, непровары, пористость и др.
Осмотр сварных швов производится по всей их протяженности с двух сторон невооруженным глазом или с применением лупы десятикратного увеличения.
Контроль размеров сварного шва и определение величины выявленных дефектов производят измерительным инструментом или специальными шаблонами для проверки геометрических размеров.
Геометрическая форма и размер сварных соединений должны удовлетворять требованиям следующих стандартов:
при ручной электродуговой сварке ГОСТ 5264—80; при автоматической и полуавтоматической сварке в защитных газах ГОСТ 14771—76.
Перед контролем сварной шов и прилегающая к нему поверхность основного металла на ширину не менее 20 мм по обе стороны шва должны быть очищены от шлака и других загрязнений, затрудняющих осмотр. Определение границы выявленных трещин производится путем шлифовки дефектного участка наждачной бумагой и травлением 20 %-ным раствором азотной кислоты.
По внешнему виду сварные швы должны удовлетворять следующим требованиям:
иметь гладкую или мелкочешуйчатую поверхность (без наплывов, сужений, прожогов и перерывов) и плавный переход к основному металлу;
направленный металл должен быть плотным по всей длине шва, не иметь трещин, скоплений и цепочек поверхностных пор (отдельно расположенные поры допускаются);
подрезы основного металла допускаются глубиной не более 0,5—1 мм при толщине стали соответственно 5— 10 мм;
все кратеры должны быть заварены.
Ультразвуковой контроль
Ультразвуковые колебания прямолинейно распространяются в металле и отражаются от границы раздела сред, имеющих различные акустические свойства. Для возбуждения ультразвуковых колебаний используется пьезоэлектрический эффект, при котором электрические колебания, приложенные к пьезоэлементу, превращаются в механические колебания. Отраженные ультразвуковые волны, попадая на пьезопластину, вызывают электрические импульсы, которые усиливаются и поступают на экран дефектоскопа (рис. 39, а).
Ультразвуковые колебания вводятся в контролируемое изделие при помощи плоских искателей через слой жидкости, необходимой для акустического контакта искателя с поверхностью металла.
В практике наибольшее распространение нашел эхо-импульсный метод дефектоскопии сварных швов, при котором в шов посылают кратковременные импульсы ультразвуковых колебаний, а в паузах между ними отраженные от дефектов колебания поступают на пьезоэлемент.
Ультразвуковой контроль производится в соответствии с требованиями ГОСТ 14782—86.
Выбор параметров контроля и методика его проведения регламентируются специальными инструкциями по УЗК, которые разрабатываются для отдельных видов сварных соединений, толщин проверяемого металла или для конкретных изделий.
Скорость ручного ультразвукового контроля обычно не превышает 5—7 м/ч.
Для проверки качества сварных швов при производстве сварных строительных конструкций применяют дефектоскопы с рабочими частотами 0,6; 1,8; 2,5; 5 и 10 МГц. Минимальная площадь выявляемых дефектов — 1—2 мм2.
|
|
Архитектура электронного правительства: Единая архитектура – это методологический подход при создании системы управления государства, который строится...
Папиллярные узоры пальцев рук - маркер спортивных способностей: дерматоглифические признаки формируются на 3-5 месяце беременности, не изменяются в течение жизни...
Двойное оплодотворение у цветковых растений: Оплодотворение - это процесс слияния мужской и женской половых клеток с образованием зиготы...
Своеобразие русской архитектуры: Основной материал – дерево – быстрота постройки, но недолговечность и необходимость деления...
© cyberpedia.su 2017-2024 - Не является автором материалов. Исключительное право сохранено за автором текста.
Если вы не хотите, чтобы данный материал был у нас на сайте, перейдите по ссылке: Нарушение авторских прав. Мы поможем в написании вашей работы!