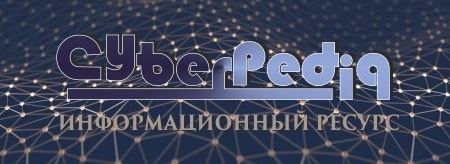
Кормораздатчик мобильный электрифицированный: схема и процесс работы устройства...
Механическое удерживание земляных масс: Механическое удерживание земляных масс на склоне обеспечивают контрфорсными сооружениями различных конструкций...
Топ:
Выпускная квалификационная работа: Основная часть ВКР, как правило, состоит из двух-трех глав, каждая из которых, в свою очередь...
Определение места расположения распределительного центра: Фирма реализует продукцию на рынках сбыта и имеет постоянных поставщиков в разных регионах. Увеличение объема продаж...
Эволюция кровеносной системы позвоночных животных: Биологическая эволюция – необратимый процесс исторического развития живой природы...
Интересное:
Наиболее распространенные виды рака: Раковая опухоль — это самостоятельное новообразование, которое может возникнуть и от повышенного давления...
Берегоукрепление оползневых склонов: На прибрежных склонах основной причиной развития оползневых процессов является подмыв водами рек естественных склонов...
Национальное богатство страны и его составляющие: для оценки элементов национального богатства используются...
Дисциплины:
![]() |
![]() |
5.00
из
|
Заказать работу |
|
|
Введение
Примечательным является тот факт, что сварка как явление была открыта в самом начале 19 века русским академиком – Петровым Василием Владимировичем. Именно он открыл такой эффект, что, при пропускании через два угольных стержня электричества, между ними возникает электрическая дуга высокой температуры.
Этот же ученый предположил возможность применения этой температуры для сплавления металлов. Это открытие послужило основой для дальнейшего развития технологий работы с металлами: сварка как таковая, газоплазменная резка, воздушно-плазменная резка и так далее.
Способность металлов свариваться (то есть образовывать неразъемные соединения) открыта человеком в начале бронзового века. До нас дошли изделия из меди, датированные VI-III тысячелетиями до нашей эры и представляющие различные амулеты, бляшки, долота, в которых применялась так называемая кузнечная сварка. Процесс соединения металла при этом был достаточно прост: его нагревали до состояния размягчения и ударом тяжелого предмета (камня, а в последствии молота) соединяли между собой. Качество такого соединения было невысоким, но быстро возрастало с совершенствованием орудий труда, и во времена скифской эпохи прочность сварных элементов мечей, боевых топоров, ножей, наконечников стрел была весьма высокой. Скифо-сарматское направление в развитии металлообработки продолжали алано-болгарские племена (VIII-X вв. нашей эры). Их кузнецы могли изготовлять высококачественные, сложные вещи: от сабель до замков. При этом применяли сварку железа и стали, а также пайку украшений из золота, бронзы и серебра. Особенно больших успехов в изготовлении различных изделий при помощи кузнечной сварки добились ремесленники Древней Руси в X-XIII веках. При помощи сварки они изготавливали серпы, плуги, гарпуны, мечи, ножницы, кольчуги, сверла, резцы, бритвы и другие виды изделий, используя уже высоко-углеродистые стали и биметаллы.
|
К первым способам сварки также можно отнести холодную и литейную сварку, в которых неразъемное соединение достигается, как и при кузнечной сварке, за счет взаимодействия атомов. Данные способы были несовершенны из-за отсутствия мощных и концентрированных источников тепла, поэтому свариваемые детали полностью нагревались в печах, а поскольку большие изделия нагревать было трудно, для таких соединений, применяли клепку.
Всего за сто лет технологии обработки металлов пополнились методами сварки, которые используют металлические и угольные электроды, роликовая и точечная контактная сварка. Сегодня сварочные процессы используются во всех сферах производства и народного хозяйства. Современные технологии позволяют соединять любые металлы и сплавы. Более того, в промышленности применяется и сварка других материалов: пластмасс, стекла и различных огнеупорных материалов.
Существует много видов сварки, основные из них это: электрошлаковая сварка, атомноводородная сварка, газовая сварка, термитная сварка, контактная сварка, кузнечная сварка, газопрессовая сварка, дуговая сварка в среде защитного газа.
2. Назначение узла.
Фермой называется система стержней соединенных между собой в узлах и образующих геометрически неизменяемую конструкцию. При узловой нагрузке жесткость узлов несущественно влияет на работу конструкции, и в большинстве случаев их можно рассматривать как шарнирные. В этом случае все стержни ферм испытывают только растягивающие или сжимающие осевые усилия.
Фермы экономичнее балок по расходу стали, но более трудоемки в изготовлении. Эффективность ферм по сравнению со сплошностенчатыми балками тем больше, чем больше пролет и меньше нагрузка.Фермы бывают плоскими (все стержни лежат в одной плоскости) и пространственными.Плоские фермы воспринимают нагрузку, приложенную только в их плоскости, и нуждаются в закреплении их связями. Пространственные фермы образуют жесткий пространственный брус, воспринимающий нагрузку в любом направлении.Основными элементами ферм являются пояса, образующие контур фермы, и решетка, состоящая из раскосов и стоек.Соединение элементов в узлах осуществляется путем непосредственного примыкания одних элементов к другим или с помощью узловых фасонок. Элементы ферм центрируются по осям центра тяжести для снижения узловых моментов и обеспечения работы стержней на осевые усилия.
|
1 - верхний пояс; 2 - нижний пояс; 3 - раскосы; 4 – стойки
Пояса ферм работают на продольные усилия и момент (аналогично поясам сплошных балок); решетка ферм воспринимает в основном поперечную силу, выполняя функции стенки балки. Стальные фермы широко применяются во многих областях строительства; в покрытиях и перекрытиях промышленных и гражданских зданий, мостах, опорах линий электропередачи, объектах связи, телевидения и радиовещания (башни, мачты), транспортных эстакадах, гидротехнических затворах, грузоподъемных кранах и т. д.
Фермы имеют разную конструкцию в зависимости от назначения, нагрузок и классифицируются по различным признакам:по статической схеме - балочные (разрезные, неразрезные, консольные);по очертанию поясов - с параллельными поясами, трапециевидные, треугольные, полигональные, сегментные.
Промежуточными между фермой и балкой являются комбинированные системы, состоящие из балки, подкрепленной снизу шпренгелем или раскосами либо аркой (сверху). Подкрепляющие элементы уменьшают изгибающий момент в балке и повышают жесткость системы. Комбинированные системы просты в изготовлении (имеют меньшее число элементов) и рациональны в тяжелых конструкциях, а также в конструкциях с подвижными нагрузками.Эффективность ферм комбинированных систем можно повысить, создав в них предварительное напряжение
Компоновка конструкций ферм.Выбор статической схемы и очертания фермы - первый этап проектирования конструкций, зависящий от назначения и архитектурно - конструктивного решения сооружения и производится на основании сравнения возможных вариантов.В покрытиях зданий, мостах, транспортных галереях и других сооружениях нашли применение балочные разрезные системы. Они просты в изготовлении и монтаже, не требуют устройства сложных узлов, но весьма металлоемки. При пролетах балок 40м разрезные фермы получаются негабаритными, и их собирают при монтаже.
|
Для двух и более перекрываемых пролетов применяют неразрезные фермы. Они экономичнее по расходу металла и обладают большей жесткостью, что позволяет уменьшить их высоту. Применение неразрезных ферм при слабых грунтах не рекомендуется, так как при осадке опор возникают дополнительные усилия. Кроме того, неразрезность усложняет монтаж.
Рамные фермы экономичнее по расходу стали, имеют меньшие габариты, но более сложны в монтаже. Их рационально применять для большепролетных зданий. Арочные системы, дают экономию стали, но приводят к увеличению объема помещения и поверхности ограждающих конструкций. Применение их диктуется архитектурными требованиями. Консольные фермы используют для навесов, башен, опор ЛЭП.
Очертания ферм должны соответствовать их статической схеме и виду нагрузок, определяющих эпюру изгибаемых моментов. Для ферм покрытий необходимо учитывать материал кровли и требуемый уклон для обеспечения водоотвода, тип узла сопряжения с колоннами (жесткий или шарнирный) и другие технологические требования.
Очертания поясов ферм определяет их экономичность. Наиболее экономичной по расходу стали является ферма, очерченная по эпюре моментов. Для однопролетной балочной системы с равномерно распределенной нагрузкой будет сегментная ферма с параболическим поясом. Однако криволинейные пояса очень трудоемки в изготовлении, поэтому такие фермы применяют крайне редко. Более применяемыми являются полигональные фермы. В тяжелых большепролетных фермах дополнительные конструктивные затруднения из-за перелома поясов в узлах не так ощутимы, так как из условия транспортировки пояса в таких фермах приходится стыковать в каждом узле.Для легких ферм полигональное очертание нерационально, поскольку усложнение узлов не окупается экономией стали.Фермы трапецеидальные, хотя не совсем соответствуют эпюре моментов, имеют конструктивные преимущества, за счет упрощения узлов. Кроме того, применение таких ферм в покрытии позволяет устроить жесткий рамный узел, что повышает жесткость здания.Фермы с параллельными поясами по своему очертанию далеки от эпюры моментов и неэкономичны по расходу стали. Однако равные длины элементов решетки, одинаковая схема узлов, повторяемость элементов и деталей, возможность их унификации способствуют индустриализации их изготовления. Поэтому фермы с параллельными поясами стали основными для покрытия производственных зданий.Фермы треугольного очертания рациональны для консольных систем и для балочных при сосредоточенной нагрузке в середине пролета (подстропильные фермы). Недостатком этих фермявляется повышенный расход металла при распределенной нагрузке; острый опорный узел сложен и допускает только шарнирное сопряжение с колоннами, Средние раскосы очень длинные и их приходится подбирать по предельной гибкости, что ведет к перерасходу металла. Однако иногда их используют для стропильных конструкций, когда необходимо обеспечить большой уклон кровли (свыше 20%) или для создания одностороннего равномерного освещения (шедовые покрытия).
|
Пролет или длина ферм определяется эксплуатационными требованиями и обще компоновочным решением сооружения и рекомендуется конструктором. Там где пролет не диктуется технологическими требованиями (например, эстакады поддерживающие трубопроводы и т.п.), его назначают на основе экономических соображений, по наименьшей суммарной стоимости ферм и опор.Высота обычно бывает выше требуемой, поэтому треугольные фермы не экономичны. Высоту фермы можно уменьшить, придав нижнему поясу приподнятое очертание, но опорный узел не должен быть очень острым.Для высоты трапецеидальных ферм и ферм с параллельными поясами нет конструктивных ограничений, высоту фермы принимают из условия наименьшего веса фермы. Вес фермы складывается из веса поясов и решетки. Вес поясов уменьшается с увеличением высоты фермы, так как усилия в поясах обратно пропорциональны высоте.Вес решетки наоборот, с увеличением высоты фермы возрастает, так как увеличивается длина раскосов и стоек, поэтому оптимальная высота ферм составляет 1/4 - 1/5 пролета. Это приводит к тому, что при пролете 20м высота фермы больше предельно (3,85м) допустимой по условию транспортировки. Поэтому с учетом требований транспортировки, монтажа, унификации высоту ферм принимают в пределах 1/7 - 1/12 пролета (для легких ферм еще меньше).Наименьшая возможная высота фермы определяется допустимым прогибом. В обычных кровельных покрытиях жесткость ферм превосходит требуемую. В конструкциях работающих на подвижную нагрузку (фермы подкрановых эстакад, мостовых кранов и т. п.) требования жесткости настолько высоки (f// = 1/750 - 1/1000), что они диктуют высоту фермы.Размеры панели должны соответствовать расстояниям между элементами, передающими нагрузку на ферму, и отвечать оптимальному углу наклона раскосов, который в треугольной решетке составляет примерно 450, а в раскосной решетке - 350. Из конструктивных соображений - рационального очертания фасонки в узле и удобства прикрепления раскосов - желателен угол близкий к 450.В стропильных фермах размеры панелей принимаются в зависимости от системы кровельного покрытия.Желательно для исключения работы пояса на изгиб обеспечить передачу нагрузки от кровли на узлы фермы. Поэтому в покрытиях из крупноразмерных железобетонных или металлических плит расстояние между узлами принимается равным ширине плиты (1,5м или 3м), а в покрытиях по прогонам- шагу прогонов (от 1,5м до 4м). Иногда для уменьшения размеров панели пояса принимается шпренгельная решетка.Унификация и модулирование геометрических размеров ферм позволяет стандартизировать как сами фермы, так и примыкающие к ним элементы (прогоны, связи и т. д.). Это приводит к сокращению числа типоразмеров деталей и дает возможность при массовом изготовлении конструкций применять специализированное оборудование и перейти на поточное производство.В настоящее время унифицированы геометрические схемы стропильных ферм производственных зданий, мостов, радиомачт, радио башен, опор линий электропередачи.Строительный подъем. В фермах больших пролетов (более 36м), а также в фермах из алюминиевых сплавов или высокопрочных сталей возникают большие прогибы, которые ухудшают внешний вид конструкции и недопустимы по условиям эксплуатации.Провисание ферм предотвращается устройством стропильного подъема, т. е. изготовление ферм с обратным выгибом, который под действием нагрузки погашается, и ферма принимает проектное положение. Строительный подъем назначают равным прогибу от постоянной плюс половину временных нагрузок. При плоских кровлях и пролетах больше 36м строительный подъем следует принимать независимо от величины пролета равным прогибу от суммарной нормативной нагрузки плюс 1/200 пролета.Строительный подъем обеспечивается путем устройства перегиба в монтажных узлах. Системы решеток ферм и их характеристика. Решетка ферм работает на поперечную силу, выполняя функции стенки сплошной балки. От системы решетки зависит вес фермы, трудоемкость ее изготовления, внешний вид. Поскольку нагрузка на ферму передается в узлах, то решетка должна соответствовать схеме приложения нагрузки. Треугольная система решетки. В фермах трапецеидального очертания или с параллельными поясами рациональной является треугольная система решетки, дающая наименьшую суммарную длину решетки и наименьшее число узлов при кратчайшем пути усилия от места приложения нагрузки до опоры. В фермах, поддерживающих прогоны кровли или балки настила, к треугольной решетке часто добавляют дополнительные стойки, а иногда и подвески, позволяющие уменьшить расстояние между узлами фермы. Дополнительные стойки уменьшают также расчетную длину сжатого пояса. Работают дополнительные стойки только на местную нагрузку и не участвуют в передаче на опору поперечной силы.
|
Схемы строительного подъема при одном и нескольких укрупнительных стыках.Недостатком треугольной системы - наличие длинных сжатых раскосов (восходящих в фермах с параллельными поясами и нисходящих в треугольных фермах).Раскосная система решеток, применяется при малой высоте ферм, а также тогда, когда по стойкам передаются большие усилия (при большой узловой нагрузке).Раскосная решетка более трудоемка, чем треугольная, требует большого расхода металла, так как при равном числе панелей в ферме общая длина раскосной решетки больше, и в ней больше узлов. Путь усилия от узла до опоры в раскосной решетке длиннее; он идет через все стержни решетки и узлы.
Специальные системы решеток, применяют при большой высоте ферм (примерно 4 - 5м). Чтобы уменьшить размер панели, сохранив нормальный угол наклона раскосов, применяют шпренгельную решетку (см. рис.9.6,д). Устройство шпренгельной решетки более трудоемко и требует дополнительного расхода металла; однако такая решетка позволяет получить рациональное расстояние между элементами поперечной конструкции при рациональном угле наклона раскосов и уменьшить расчетную длину сжатых стержней.
Шпренгельная решетка применяется при крутых кровлях и сравнительно больших пролетах (l = 20 - 24м) для треугольной фермы.
В фермах, работающих на двустороннюю нагрузку устраивают крестовую решетку. К таким фермам относятся горизонтальные связевые фермы покрытий производственных зданий, мостов и других конструкций, вертикальные фермы башен, мачт и высоких зданий.
Ромбическая и полу раскосная решетки благодаря двум системам раскосов обладают большой жесткостью; эти системы применяются в мостах, башнях, мачтах, связях для уменьшения расчетной длины стержней и особенно рациональны при работе конструкций на большие поперечные силы.Обеспечение устойчивости ферм. Плоская ферма неустойчива из своей плоскости, поэтому ее необходимо присоединить к более жесткой конструкции или соединить связями с другой фермой, в результате чего образуется устойчивый пространственный брус.Поскольку этот пространственный брус в поперечном сечении замкнут, он обладает большой жесткостью при кручении и изгибе в поперечном направлении, поэтому потеря его общей устойчивости невозможна. Конструкции мостов, кранов, башен, мачт и т.п. представляют собой также пространственные брусья, состоящие из ферм.
В покрытиях зданий из-за большого числа поставленных рядом плоских стропильных ферм решение усложняется, поэтому фермы, связанные между собой только прогонами могут потерять устойчивость.Их устойчивость обеспечивается тем, что две соседние фермы скрепляются связями в плоскости верхнего и нижнего пояса и вертикальными поперечными связями. К этим жестким блокам другие фермы прикрепляются горизонтальными элементами, препятствующими горизонтальному перемещению поясов ферм и обеспечивающими их устойчивость (прогонами и распорками, расположенными в узлах ферм). Чтобы прогон мог закрепить узел фермы в горизонтальном направлении, он сам должен быть прикреплен к неподвижной точке - узлу горизонтальных связей.
По расходу стали наиболее эффективным является трубчатое сечение. Труба обладает хорошей обтекаемостью, поэтому ветровое давление меньше, что важно для высоких сооружений (башен, мачт, кранов). На трубах мало задерживается иней и влага, поэтому они стойки к коррозии; их легко очищать и окрашивать. Это повышает долговечность трубчатых конструкций.
Для предотвращения коррозии внутренних плоскостей трубчатые элементы следует герметизировать. Однако определенные конструктивные трудности сопряжения трубчатых элементов и высокая стоимость труб ограничивают их применение.
Прямоугольные гнуто замкнутые сечения обладают почти теми же преимуществами, что и трубчатые, позволяют упростить узлы сопряжения элементов и нашли широкое применение. Однако, фермы из гнуто замкнутых профилей с бесфасоночными узлами требуют высокой точности изготовления.Технологические трудности не позволяют изготавливать гнутые профили толщиной более 10-12 мм. Это ограничивает возможность их использования. Кроме того, большие пластические деформации в углах гиба снижают хрупкую прочность стали.Часто сечения элементов ферм принимаются из разного вида профилей: пояса из двутавров, решетка из гнутозамкнутых профилей или пояса из тавров, решетка из парных или одиночных уголков. Такое решение оказывается более рациональным.В пространственных фермах (башнях, мачтах, стрелах кранов и т.п.), где пояс является общим для двух ферм, его сечение должно обеспечивать удобное сопряжение элементов в разных плоскостях. Этому требованию лучше всего отвечает трубчатое сечение.В четырехгранных фермах при небольших усилиях, простейшим типом сечения пояса является одиночный уголок или крестовое сечение из двух уголков. При больших усилиях применяются также двутавры.Сжатые элементы ферм следует проектировать равноустойчивыми в двух взаимно перпендикулярных направлениях.В каждом конкретном случае выбор типа сечения элементов ферм определяется условиями работы конструкции (степень агрессивности среды, характер и место приложения нагрузок и т.д.), возможностью изготовления, наличием сортимента и экономическими соображениями.Стержни тяжелых ферм отличаются от легких более мощными и развитыми сечениями, составленными из нескольких элементов. Сечения таких стержней обычно проектируют двухстенчатыми, а узловые сопряжения выполняются с помощью фасонок, расположенных в двух плоскостях. Стержни тяжелых ферм (раскосы, стойки и пояса) имеют разные сечения, но для удобства сопряжения в узлах ширина, элементов “в” должна быть одинаковой.Для поясов ферм желательно применять сечения имеющие две оси симметрии, что облегчает стык в узле двух сечений соседних панелей разной площади и не создает дополнительного момента вследствие несовпадения центров тяжести этих сечений.Тяжелые фермы, работающие на динамические нагрузки (железнодорожные мосты, краны и т.п.), иногда еще проектируют клепанными, но в основном, как правило, проектируют из сварных стрежней с монтажными узлами на высокопрочных болтах. Применяются следующие типы сечений стержней тяжелых стальных ферм:
Н-образное - два вертикальных листа, связаны горизонтальным листом, а также клепанные из четырех не равнополочных уголков, связанных горизонтальным листом. Развитие таких сечений в смежных панелях производят креплением дополнительных вертикальных листов. Такие сечения малотрудоемкие. Если конструкция не защищена от попадания атмосферных осадков, то в горизонтальных элементах необходимо оставлять отверстия для стока воды диаметром 50 мм. Н-образные сечения применяют для поясов и раскосов.Швеллерное сечение состоит из двух швеллеров, поставленных полками внутрь; используются как прокатные, так и составные швеллеры. Такое сечение целесообразно для сжатых элементов, особенно при большой их длине. Недостатком швеллерного сечения является наличие двух ветвей, которые приходится соединять планками или решетками (аналогично центрально сжатым колоннам). Коробчатое сечение состоит из двух вертикальных элементов, соединенных горизонтальным листом сверху.Применяется в основном для верхних поясов тяжелых мостовых ферм. Жесткость сечения повышается, если снизу вертикальные листы соединить решеткой или перфорированным листом.Одностенчатое двутавровое сечение состоит из сварного или широкополочного прокатного двутавра, поставленного вертикально.Трубчатые стержни применяются в тяжелых сварных фермах, имеют те же преимущества, что и в легких фермах.Замкнутое коробчатое сечение обладает повышенной изгибной и крутильной жесткостью, поэтому применяют его для длинных сжатых элементов тяжелых ферм. Сечение может быть выполнено как из гнутых элементов, так и сварных, составленных из четырех листов.В фермах из прокатных и гнутых профилей для удобства комплектования металла принимают не более 5-6 калибров профилей.Из условия обеспечения качества сварки и повышения коррозионной стойкости толщину профилей (труб, гнутых сечений) не следует принимать менее 3 мм, а для уголков - менее 4 мм. Для предотвращения повреждения стержней при транспортировке и монтаже не следует применять профили менее 50 мм.Профильный прокат поставляется длиной до 12 м, поэтому при изготовлении ферм пролетом 24 м (включительно) элементы пояса принимают постоянного сечения.Для снижения расхода стали, целесообразно, особенно при больших усилиях и нагрузках, элементы ферм (пояса, опорные раскосы) проектировать из стали повышенной прочности, а остальные элементы - из обычной стали.
Такую продукцию сегодня используют на различных строительных объектах - как жилых, так и промышленных, а также для возведениях мостов, рекламных щитов, изготовления подъемных кранов и прочее. Специалисты разделяют все фермы из металла на плоские и пространственные. В первом варианте все стержни расположены в одной плоскости, во втором - образуют брус, каждая грань которого является плоской фермой.
Технология строительства из легких металлических конструкций применима не только в быстровозводимом промышленном и складском строительстве, но и особое место эта технология занимает в сельскохозяйственном строительстве. Не секрет, что бюджет фермера ограничен, и выбор строительной технологии для строительства коровника, свинарника или птичника представляется очень ответственной задачей.
Кроме этого, свинарник, птичник или коровник может обеспечить ферму светом и теплом. Современное быстровозводимое строительство коровников и свинарников предусматривает монтаж оборудования для переработки навоза с получением природного биогаза и высококачественного удобрения (перегноя) из навоза, производимого фермой. Для этого, наш завод начал производство автоматизированных биогазовых установок средней мощности.
Вес её состовляющих частей от 100 до 200 кг.
Выбор режимов сварки.
Техника выполнения сварных швов
Под техникой выполнения сварных швов понимают выбор режимов сварки и приемы манипулирования электродом.
Зажигание дуги является одной из основных операций сварочного процесса. Зажигание производится каждый раз до начала процесса сварки, повторное возбуждение дуги - в процессе сварки при ее обрыве.
Возбуждение сварочной дуги производится путем касания торцом электрода поверхности свариваемого изделия с быстрым последующим отводом торца электрода от поверхности изделия. При этом если зазор не слишком велик, происходит мгновенное появление тока и установление столба дуги. Прикосновение электрода к изделию должно быть кратковременным, так как иначе он приварится к изделию ("прилипнет").
Отрывать "прилипший" электрод следует резким поворачиванием его вправо и влево. Возбуждение дуги может производиться либо серией возвратно-поступательных движений с легким прикосновением к поверхности свариваемого металла и последующим отводом от поверхности изделия на 2-4 мм, либо путем царапающих движений торцом электрода по поверхности изделия, которые напоминают чирканье спички. Используйте наиболее удобный для вас способ.
После возбуждения дуги электрод должен выдерживаться некоторое время Точке начала наплавки, пока не сформируется сварной шов и не произойдет расплавление основного металла. Одновременно с расплавлением электрода необходимо равномерно подавать его в сварочную ванну, поддерживая тем самым оптимальную длину дуги. Показателями оптимальной длины дуги является резкий потрескивающий звук, ровный перенос капель металла через дуговой промежуток, малое разбрызгивание.
Длина дуги значительно влияет на качество сварки. Короткая дуга горит устойчиво и спокойно. Она. обеспечивает получение высококачественного шва, так как расплавленный металл электрода быстро проходит дуговой промежуток и меньше подвергается окислению и азотированию. Но слишком короткая дуга может вызывать "прилипание" электрода, дуга прерывается, нарушается процесс сварки. Длинная дуга горит неустойчиво с характерным шипением. Глубина проплавления недостаточная, расплавленный металл электрода разбрызгивается и больше окисляется и азотируется. Шов получается бесформенным, а металл шва содержит большое количество оксидов.
Если во время сварки по какой-либо причине сварочная дуга погаснет, то применяется специальная техника повторного зажигания дуги, обеспечивающая начало сварки с хорошим сплавлением и внешним видом. При повторном зажигании дуга должна возбуждаться на передней кромке кратера, затем через весь кратер переводиться на противоположную кромку, на только что наплавленный металл, и после этого снова вперед, в направлении проводившейся сварки. Если электрод при повторном зажигании дуги не буде достаточно далеко отведен назад, между участками начала и конца сварки останется углубление. Если же при повторном зажигании электрод отвести слишком далеко назад, то на поверхности сварного валика образуется высокий наплыв. Положение и перемещение электрода при сварке. В процессе сварки электроду сообщаются следующие движения: поступательное по оси электрода в сторону сварочной ванны, при этом для сохранения постоянства длины дуги скорость движения должна соответствовать скорости плавления электрода;
перемещение вдоль линии свариваемого шва, которое называют скоростью сварки; скорость этого движения устанавливается в зависимости от тока, диаметра электрода, скорости его плавления, вида шва и других факторов;
перемещение электрода поперек шва для получения шва шире, чем ниточный валик, так называемого уширенного валика.
При слишком большой скорости сварки наплавленные валики получаются узкими, с малой выпуклостью, с крупными чешуйками. При слишком медленной скорости перемещения электрода сварной валик имеет слишком большую выпуклость, шов неровный по форме, с наплывами по краям.
Внешний осмотр и измерения.
Внешним осмотром контролируют все типы сварных соединений при всех способах сварки всех свариваемых металлов и сплавов.
Внешним осмотром выявляют следующие дефекты: излом и неперпендикулярность осей соединяемых элементов;
отступления по размерам и форме швов от требований стандартов, чертежей, технических условий и инструкций по сварке конструкций;
смещение кромок соединяемых элементов; поверхностные трещины всех видов и направлений; наплывы, подрезы, прожоги, незаверенные кратеры, непровары, пористость и др.
Осмотр сварных швов производится по всей их протяженности с двух сторон невооруженным глазом или с применением лупы десятикратного увеличения.
Контроль размеров сварного шва и определение величины выявленных дефектов производят измерительным инструментом или специальными шаблонами для проверки геометрических размеров.
Геометрическая форма и размер сварных соединений должны удовлетворять требованиям следующих стандартов:
при ручной электродуговой сварке ГОСТ 5264—80; при автоматической и полуавтоматической сварке в защитных газах ГОСТ 14771—76.
Перед контролем сварной шов и прилегающая к нему поверхность основного металла на ширину не менее 20 мм по обе стороны шва должны быть очищены от шлака и других загрязнений, затрудняющих осмотр. Определение границы выявленных трещин производится путем шлифовки дефектного участка наждачной бумагой и травлением 20 %-ным раствором азотной кислоты.
По внешнему виду сварные швы должны удовлетворять следующим требованиям:
иметь гладкую или мелкочешуйчатую поверхность (без наплывов, сужений, прожогов и перерывов) и плавный переход к основному металлу;
направленный металл должен быть плотным по всей длине шва, не иметь трещин, скоплений и цепочек поверхностных пор (отдельно расположенные поры допускаются);
подрезы основного металла допускаются глубиной не более 0,5—1 мм при толщине стали соответственно 5— 10 мм;
все кратеры должны быть заварены.
Ультразвуковой контроль
Ультразвуковые колебания прямолинейно распространяются в металле и отражаются от границы раздела сред, имеющих различные акустические свойства. Для возбуждения ультразвуковых колебаний используется пьезоэлектрический эффект, при котором электрические колебания, приложенные к пьезоэлементу, превращаются в механические колебания. Отраженные ультразвуковые волны, попадая на пьезопластину, вызывают электрические импульсы, которые усиливаются и поступают на экран дефектоскопа (рис. 39, а).
Ультразвуковые колебания вводятся в контролируемое изделие при помощи плоских искателей через слой жидкости, необходимой для акустического контакта искателя с поверхностью металла.
В практике наибольшее распространение нашел эхо-импульсный метод дефектоскопии сварных швов, при котором в шов посылают кратковременные импульсы ультразвуковых колебаний, а в паузах между ними отраженные от дефектов колебания поступают на пьезоэлемент.
Ультразвуковой контроль производится в соответствии с требованиями ГОСТ 14782—86.
Выбор параметров контроля и методика его проведения регламентируются специальными инструкциями по УЗК, которые разрабатываются для отдельных видов сварных соединений, толщин проверяемого металла или для конкретных изделий.
Скорость ручного ультразвукового контроля обычно не превышает 5—7 м/ч.
Для проверки качества сварных швов при производстве сварных строительных конструкций применяют дефектоскопы с рабочими частотами 0,6; 1,8; 2,5; 5 и 10 МГц. Минимальная площадь выявляемых дефектов — 1—2 мм2.
Организация рабочего места.
Основными задачами организации труда являются: увеличение производительности труда на основе применения передовой техники, технологии и обмена производственным опытом, улучшение условий труда и его облегчение путем механизации и автоматизации работ, улучшение санитарно-гигиенических условий труда, состояния техники безопасности, повышение квалификации и культурно-технического уровня рабочих, укрепление трудовой дисциплины и широкое развитие социалистического соревнования.
Повышение производительности труда в значительной мере зависит от правильной организации рабочего места. Мероприятия по правильной и рациональной организации рабочего места должны обязательно предусматриваться в планах научной организации труда (НОТ).
Рабочее место должно быть оборудовано шкафом для хранения инструмента, электродов и чертежей, сборочно-сварочными приспособлениями, сварочными столами. Все инструменты следует располагать в определенном порядке, чтобы они всегда находились под рукой.
Рабочее место для сварки тяжелых изделий необходимо оборудовать подъемными и поворотными приспособлениями.
В зависимости от размеров изделий и характера сварочных работ рабочее место может быть расположено в отдельной кабине или в цехе у сварочного стенда, или на монтажной площадке. Размеры кабины в плане 2X2 или 2x2,5 м. На рис. 215 показана типовая кабина для ручной дуговой сварки. Если кабина расположена на поточной линии или конвейере, то в боковых стенках ее делаются проемы для прохождения конвейера с деталями, закрываемые дверцами или брезентовыми шторами.При сварке в монтажных условиях рабочее место должно быть защищено от ветра, дождя, снега и иметь ограждения. При частой смене места работы необходимы приспособления для быстрого перемещения источника сварочного тока, провода, запаса электродов и сварочного инструмента (тележки, ящики для инструмента и электродов, ящики для сбора огарков и пр.). У мест сварки
должны быть сделаны лестницы, снабженные ограждениями. Для работы в зимних условиях на открытом воздухе сварщики должны быть снабжены теплой спецодеждой. Вблизи места работ необходимо оборудовать теплое помещение для периодического обогрева рабочих. При сварке на высоте узлов различных конструкций могут также применяться легкие подвесные люльки для сварщика, снабженные надежными ограждениями и легко перемещаемые с места на место.
Для монтажа ответственных конструкций (кожухов доменных печей, резервуаров, высотных и мостовых конструкций) создаются специализированные сварочные участки. Монтажной сварке таких объектов предшествует разработка проекта организации сварочно-монтажных работ.
При установлении норм времени следует исходить из полного учета производственных возможностей цеха (предприятия), наиболее производительных режимов работы оборудования и применения наиболее эффективных для данных условий способов работы и форм организации труда. При этом должен использоваться опыт передовых рабочих-новаторов производства.
Литература
«Электродуговая сварка: Практика и теория.» О.М. Черный
Электрогазосварщик. А.А. Николаев
Технология электрической сварки металлов и сплавов плавлением. Б.Е. Патон
Справочник электросварщика ручной сварки. О.И. Титов
Справочник сварщика строителя. В.Х. Бондарь, Г.Д. Шкуратовский
Справочник молодого сварщика. Э.С. Каракозов, Р.И. Мустафаев
Справочник газосварщика и газорезчика. Н.И. Никифоров, С.П. Нешумова
Сварочные работы. В.И. Маслов
Основы сварочного дела. В.Г. Геворкян
Содержание.
1.Введение…………………………………………………………………………………………1
2. Назначение узла................................................................................2
3. Выбор оборудования, приспособлений и инструментов..............3
4. Выбор режимов сварки....................................................................4
5. Технология монтажа сварки............................................................5
6. Нормирование сварочных работ.....................................................6
7. Контроль качества сварочных работ...............................................7
8. Организац<
|
|
Поперечные профили набережных и береговой полосы: На городских территориях берегоукрепление проектируют с учетом технических и экономических требований, но особое значение придают эстетическим...
Адаптации растений и животных к жизни в горах: Большое значение для жизни организмов в горах имеют степень расчленения, крутизна и экспозиционные различия склонов...
Семя – орган полового размножения и расселения растений: наружи у семян имеется плотный покров – кожура...
Историки об Елизавете Петровне: Елизавета попала между двумя встречными культурными течениями, воспитывалась среди новых европейских веяний и преданий...
© cyberpedia.su 2017-2024 - Не является автором материалов. Исключительное право сохранено за автором текста.
Если вы не хотите, чтобы данный материал был у нас на сайте, перейдите по ссылке: Нарушение авторских прав. Мы поможем в написании вашей работы!