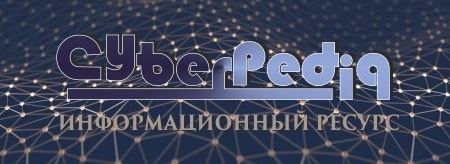
Механическое удерживание земляных масс: Механическое удерживание земляных масс на склоне обеспечивают контрфорсными сооружениями различных конструкций...
Таксономические единицы (категории) растений: Каждая система классификации состоит из определённых соподчиненных друг другу...
Топ:
Когда производится ограждение поезда, остановившегося на перегоне: Во всех случаях немедленно должно быть ограждено место препятствия для движения поездов на смежном пути двухпутного...
Отражение на счетах бухгалтерского учета процесса приобретения: Процесс заготовления представляет систему экономических событий, включающих приобретение организацией у поставщиков сырья...
Генеалогическое древо Султанов Османской империи: Османские правители, вначале, будучи еще бейлербеями Анатолии, женились на дочерях византийских императоров...
Интересное:
Как мы говорим и как мы слушаем: общение можно сравнить с огромным зонтиком, под которым скрыто все...
Мероприятия для защиты от морозного пучения грунтов: Инженерная защита от морозного (криогенного) пучения грунтов необходима для легких малоэтажных зданий и других сооружений...
Уполаживание и террасирование склонов: Если глубина оврага более 5 м необходимо устройство берм. Варианты использования оврагов для градостроительных целей...
Дисциплины:
![]() |
![]() |
5.00
из
|
Заказать работу |
|
|
Содержание
Введение
1. Промышленные способы получения фенола
2. Поиск новых путей синтеза фенола
3. Открытие цеолитных катализаторов для окисления бензола закисью азота
4. Природа каталитической активности цеолитов
5. Специфика действия N2O как окислителя
6. Стехиометрическая реакция бензола с a-кислородом
7. Биомиметические свойства a-кислорода
8. Активное состояние железа в цеолитной матрице
9. Новый фенольный процесс. Технологические аспекты
Заключение
Список литературы
Введение
История фенола насчитывает уже более 160 лет. Впервые он был выделен из каменноугольной смолы в 1834 г., откуда и получил свое название. карболовая (угольная) кислота. Быстрый рост потребления фенола поставил вопрос об искусственных способах его получения, создание которых является одной из самых ярких страниц в истории органической химии. Ниже кратко описаны промышленные процессы, которые в то или иное время использовались для получения фенола.
1. Промышленные способы получения фенола
1. Сульфонатный процесс был первым фенольным процессом, реализованным в промышленном масштабе фирмой «BASF» в 1899 г.[1]. Этот метод основан на сульфировании бензола серной кислотой с последующим щелочным плавлением сульфокислоты при 300–350 °С:
Для сульфирования бензола при получении бензолсульфокислоты применяют концентрированную серную кислоту; соотношение Н2SО4: бензол составляет 2:1. Периодический процесс сульфирования проводят при 120—150° С [95].
При щелочном плавлении сульфокислот замещение сульфогруппы на оксигруппу считают результатом сложного процесса, предполагающего промежуточное присоединение щелочи по кратной связи:
|
Кроме этого основного процесса возможно также прохождение и других, ведущих к образованию побочных продуктов, в частности протекает расщепление сульфонов с образованием фенолятов и частично дифенола:
Возможно взаимодействие сульфокислот и фенолятов с образованием дифениловых эфиров:
Наконец, возможно окисление компонентов сплава под действием кислорода воздуха с образованием диоксидифенилов, оксидифенилов и их гомологов [2].
Синтез фенолов слагается из ряда стадий, общая схема представлена на рис.1.
Рис.1. Схема получения фенолов щелочным плавлением сульфокислот.
Выход фенола в данном процессе зависит от температуры и времени щелочного плавления. Так на 1 тфенола в среднем расходуется несколько более 0,9 т бензола, 1,55 т серной кислоты (в пересчете на 100%-ную), и 1,54 г каустической соды [3].
Несмотря на применение агрессивных реагентов и образование большого количества отходов сульфита натрия, данный метод использовался в течение почти 80 лет. В США это производство было закрыто лишь в 1978 году [95].
2. В 1924 г. фирмой «Dow Chemical» (США) был разработан процесс получения фенола, включающий реакцию хлорирования бензола и последующий гидролиз монохлорбензола:
Независимо аналогичная технология была разработана немецкой фирмой «I.G. Farbenindustrie Co». Как отмечает Kirk Othmer [4], захват этой технологии составлял цель нескольких научных разведывательных групп стран-победительниц, прибывших в Германию сразу после окончания Второй мировой войны. Отметим, что в составе одной из таких групп был Г.К. Боресков. Впоследствии стадия получения монохлорбензола и стадия его гидролиза были усовершенствованы, и процесс получил название «процесс Рашига» [95].
Гидролиз хлорбензола в отсутствие катализатора протекает при 360—400° С и давлении более 300 ат. В этих условиях для гидролиза применяются сравнительно концентрированные растворы щелочи (150—200 г/л NaОН). В присутствии катализатора (медь) эта реакция протекает при 350° С и 200 ат за несколько минут. Процесс проводят в трубчатых реакторах, причем общую длину труб подбирают с таким расчетом, чтоб при прохождении через них реакционной смеси хлорбензол полностью гидролизовался.
|
В качестве побочного продукта при гидролизе хлорбензола образуется дифениловый эфир (дифенилоксид):
Равновесное количество дифенилового эфира составляет 10% от количества исходного хлорбензола. Если в исходную смесь хлорбензола и водного раствора щелочи специально ввести больше 10% дифенилового эфира, то избыток его гидролизуется в фенол:
Поэтому дифениловый эфир после отделения от воды добавляют к хлорбензолу, направляемому на гидролиз. Благодаря рециркуляции дифенилового эфира вновь вводимый хлорбензол почти полностью превращается в фенолят натрия и не расходуется на образование эфира.
Промышленный процесс производства фенола заключается в следующем. Насосами высокого давления хлорбензол с растворенным в нем дифениловым эфиром и водный раствор щелочи (мольное соотношение NаОН: С6Н5Сl от 2,25: 1 до 2,5: 1) подают в трубчатый реактор, где исходная смесь нагревается до 350° С. По выходе из реактора реакционную смесь охлаждают, при помощи дроссельного вентиля снижают давление до атмосферного и отгоняют из смеси дифениловый эфир вместе с парами воды. Фенол выделяют действием двуокиси углерода или соляной кислоты на раствор фенолята и очищают дистилляцией. Расходные коэффициенты на 1 т фенола: 1,13 т хлорбензола и 1,24 т каустической соды. Недостатками метода являются необходимость применения аппаратуры высокого давления, а также относительно высокий расход хлора и каустической соды, вследствие чего в мировой промышленной практике он вытесняется другими способами. Суммарный выход фенола по двум стадиям составляет 70.85%.
3. Парофазный каталитический гидролиз хлорбензола (метод Рашига). Синтез фенола по этому методу обычно проводят в две стадии. В первой стадии получают хлорбензол окислительным хлорированием бензола хлористым водородом в присутствии катализатора:
Хлорирование проводят в паровой фазе над катализатором, состоящим из хлоридов меди и железа на окиси алюминия. Катализатор приготовляют осаждением окиси алюминия из раствора, содержащего хлориды этих металлов. В реакторе поддерживается температура 235 — 245° С. Количественные отношения бензола, хлористого водорода и кислорода составляют примерно 10:2:3. Превращение бензола за один проход 10 — 15%. После удаления бензола, воды и хлористого водорода из хлоридов получают 95 — 98% хлорбензола и 2 — 5% дихлорбензола (количества п- и о-изомеров относятся как 7:3).
|
Каталитический гидролиз хлорбензола (вторую стадию процесса Рашига) проводят при атмосферном давлении и 400 — 420° С. В качестве катализаторов используют Са3(РО4)2 или смесь фосфатов кальция и меди.
Выделяющийся хлористый водород вновь может быть использован для окислительного хлорирования. Теоретически в этом процессе должны расходоваться только бензол и кислород воздуха; на практике приходится компенсировать потери хлористого водорода.
На 1 т фенола, получаемого по способу Рашига, расходуется примерно 0,998 т бензола и 0,172 т хлористого водорода. Недостатками метода Рашига являются высокие температуры, а также необходимость применения специального коррозионностойкого оборудования [3].
4. Циклогексановый процесс, разработанный фирмой «Scientific Design Co.», основан на окислении циклогексана в смесь циклогексанона и циклогексанола, которая далее дегидрируется с образованием фенола:
В 60-е годы фирма «Monsanto» в течение нескольких лет использовала этот метод на одном из своих заводов в Австралии, однако в дальнейшем перевела его на кумольный способ получения фенола.
5. В 1961 г. фирмой «Dow Chemical of Canada» был реализован процесс через разложение бензойной кислоты [4] - это единственный способ синтеза фенола, основанный на использовании небензольного сырья:
Обе реакции протекают в жидкой фазе. Первая реакция - окисление толуола - использовалась в Германии уже в период Второй мировой войны для получения бензойной кислоты. Реакция протекает в довольно мягких условиях с высоким выходом. Вторая стадия является более трудной вследствие дезактивации катализатора и низкой селективности по фенолу. Полагают, что проведение этой стадии в газовой фазе может сделать процесс более эффективным [5]. [95].
|
Метод привлек внимание прежде всего потому, что этим способом можно получать фенол из недефицитного толуола вместо бензола. Оказалось также, что метод пригоден для приготовления крезолов из толуиловых кислот и нафтолов из нафтойных кислот. Возможность использования в качестве сырья недефицитные гомологи бензола и нафталина, сравнительно малое количество побочных продуктов, высокая чистота производимых фенолов и использование кислорода воздуха в качестве окисляющего агента — все это вызвало значительный интерес к новому способу производства фенола.
Окислительное декарбоксилирование арилкарбоновых кислот проводится при 200—300°С в присутствии солей двухвалентной меди при подаче в реактор воздуха и водяного пара.
Процесс превращения ароматических карбоновых кислот в фенолы может быть представлен рядом следующих последовательных стадий.
Образование медной соли ароматической карбоновой кислоты:
Термическое разложение полученной соли с переходом и с образованием сложного эфира салициловой или смещенной салициловой кислоты:
При нагревании солей двухвалентной меди без доступа пара и воздуха исчезает характерное для этих солей синее или зеленое окрашивание, образуются бесцветные соли одновалентной меди. При проведении процесса в более жестких условиях (высокая температуpa, длительное нагревание, недостаток свободной кислоты) образуется элементарная медь.
Это, как и образование одновалентной меди, связано с резким усилением электроноакцепторных свойств меди при повышении температуры.
Регенерация Сu1 и Сu0.При барботаже воздуха через расплав кислоты, содержащий одновалентную или элементарную медь, эта последняя окисляется до двухвалентного состояния:
Гидролиз н-декарбоксилирование сложных эфиров. Возможны два направления перехода кислых сложных эфиров в фенолы. В отсутствии водяного пара кислые сложные эфиры декарбоксилируются до эфиров, а последние затем гидролизуются с образованием фенола и исходной кислоты.
В присутствии водяного пара возможен гидролиз кислых эфиров с образованием исходных арилкарбоновых и оксиарилкарбоновых кислот, а последние декарбоксилируются до фенолов [2].
В настоящее время этот метод используется на практике, хотя его доля в мировом производстве фенола составляет лишь около 5%. Остальные 95% приходятся на кумольный процесс [6].
6. Кумольный процесс получения фенола включает три стадии: алкилирование бензола в кумол, окисление кумола в гидропероксид кумола и разложение гидропероксида на фенол и ацетон:
Впервые этот способ был разработан в Советском Союзе. Химический маршрут процесса был открыт в 1942 г. группой талантливых химиков, в которую входили П.Г. Сергеев, Р.Ю. Удрис и Б.Д. Кружалов. В это время они были репрессированы и работали в специальной весьма хорошо оборудованной лаборатории, которая одновременно служила и местом заключения.
|
В 1949 году в г. Дзержинске Горьковской области был введен в действие первый в мире кумольный завод. В 1951 г. в связи с успешным пуском завода большой группе советских ученых и инженеров была присвоена высшая награда страны. Сталинская премия. Драматическая история создания кумольного процесса в СССР описана в ряде статей, опубликованных в 80-е годы [10].
В 1947 г. Сергееву, Удрису и Кружалову были выданы авторские свидетельства СССР [8]. К сожалению, их открытие не получило мировой известности. На Западе кумольный метод был разработан в конце 40-х годов и отчасти известен как процесс Хока [9] - по имени немецкого ученого, позднее независимо открывшего кумольный путь синтеза фенола. В промышленном масштабе этот метод стал впервые использоваться в США в начале 50-х годов [4]. С этого времени на многие десятилетия кумольный процесс становится образцом химических технологий во всем мире.
В настоящее время производство фенола достигло около 6 млн. тонн в год и продолжает быстро расти. Как таковой, фенол практически не используется. Но благодаря тому, что его молекула включает два умеренно реакционноспособных фрагмента (ароматическое кольцо и ОН-группа), каждый из которых может быть вовлечен в дальнейшие превращения [10], фенол является основой для синтеза многих важных химических продуктов. [95].
При окислении углеводородов гидропероксиды образуются по радикально-цепному механизму. Ингибиторы (фенол, олефины, сернистые соединения) сильно тормозят процесс, приводя к появлению индукционного периода, поэтому исходные углеводороды должны быть тщательно очищены от нежелательных примесей. Так, изопропилбензол, полученный алкилированием в присутствии твердого фосфорнокислого катализатора, не пригоден для окисления. Снятию индукционного периода и ускорению реакции на ее начальных стадиях способствует добавление в исходное сырье гидропероксида. Соли металлов переменной валентности, являющиеся обычными катализаторами гомогенного окисления, разлагают гидропероксиды и поэтому не применяются, хотя в отдельных случаях их небольшие добавки ускоряют реакцию. Такой же эффект оказывает металлическая медь, если ее использовать в виде стружек. Иногда медь эффективна, даже если она присутствует в материале аппаратуры. В некоторых исследованиях сообщается о катализе реакции солями металлов постоянной валентности (натрий, калий, магний).
При получении гидропероксидов всегда образуются побочные продукты, главным образом спирты и в меньшем количестве — кетоны. Так, при окислении кумола получаются диметилфенилкарбинол и ацетофенон, причем характер кинетических кривых показывает, что спирт является последовательным продуктом превращения гидропероксида, а кетон образуется параллельно с ним из пероксидного радикала:
(24)
Кроме свободно-радикального пути расщепления, алкилароматические гидропероксиды способны к распаду под влиянием кислотных и щелочных катализаторов. В присутствии уже небольшого количества сильной кислоты (например, 0,1 % H2SO4) гидропероксиды распадаются с образованием фенолов и карбонильных соединений. Реакция протекает по сложному механизму ионного типа с промежуточным возникновением положительных ионов:
(25)
Образовавшийся ион перегруппировывается с миграцией фенильной группы от углерода к кислородному атому, дальнейшие превращения приводят к образованию фенола и ацетона:
(26)
При другом строении втор -алкильной группы образуются гомологи ацетона (метилэтилкетон и др.), а из гидропероксидов н -алкилбензолов — ацетальдегид и его гомологи.
Побочные продукты окисления, содержащиеся как примеси к гидропероксиду (особенно алкилфенилкарбинолы), тоже чувствительны к кислотному катализу. Например, при расщеплении гидропероксида кумола диметилфенилкарбинол отщепляет воду, образуя α-метилстирол, и алкилирует фенол с образованием кумилфенола. Кроме того, α-метилстирол частично димеризуется:
(27)
Получается также небольшое количество смол сложного строения. При повышении концентрации кислоты и температуры становятся возможными кислотно-каталитические превращения ацетофенона и ацетона, например, по типу реакций альдольной конденсации с последующим отщеплением воды.
(28)
В кинетическом отношении кислотное разложение гидропероксидов характеризуется очень высокой скоростью, причем практически полное превращение в присутствии 0,05–1 масс. % H2SO4 (в расчете на гидропероксид) при 50–60 °С достигается за 2–3 мин. Реакция тормозится водой и ускоряется образующимся фенолом, имея первые порядки по кислотному катализатору и гидропероксиду. Вместо серной кислоты в качестве катализаторов можно использовать катионообменные смолы.
Ввиду высокой скорости процесса при его промышленной реализации очень важен эффективный отвод большого количества выделяющегося тепла: 2080 кДж на 1 кг гидропероксида. Для этой цели применяют, прежде всего, разбавители, которыми являются продукты реакции или ацетон.
Один из методов проведения реакции состоит в применении проточно-циркуляционной установки, когда выделяющееся тепло снимают в трубчатом реакторе за счет охлаждения его водой. Реакционную смесь по выходе из реактора частично отводят на дальнейшую переработку, но основное количество направляют на рециркуляцию: добавляют кислоту-катализатор и в насосе смешивают с исходным гидропероксидом. При такой системе время контакта лимитируется теплоотводом и является завышенным. Кроме того, рециркуляция смеси ведет к повышенному выходу побочных веществ. Так, на 1 т фенола получается 100–150 кг отходов, в том числе 15–20 кг α-метилстирола, 40–50 кг димера и смол, 5–10 кг ацетофенона, 30 кг кумилфенола и т. д. Хотя оксида мезитила образуется немного, он существенно затрудняет очистку фенола.
Другой способ кислотного разложения гидропероксидов состоит в проведении реакции в растворе ацетона и отводе тепла за счет его испарения. Ацетон конденсируют в обратном холодильнике и возвращают в реактор, который можно секционировать поперечными перегородками. Это (наряду с уменьшением концентрации фенола в растворе и времени контакта) снижает выход побочных веществ.
Современный процесс получения фенола и ацетона включает 10 основных стадий: получение изопропилбензола (ИПБ); окисление его до гидропероксида кумола (ГПК); концентрирование продуктов окисления, содержащих 20–40 % гидропероксида, путем отгонки под вакуумом (1–3 стадии) непрореагировавшего кумола; разложение ГПК в среде фенола, ацетона и кумола в присутствии серной кислоты до фенола, ацетона, α-метилстирола и побочных продуктов (так называемой «фенольной смолы»); нейтрализация серной кислоты и выведение из системы Na2SO4 и NaHSO4; разделение полученных продуктов до индивидуальных веществ; гидрирование α-метилстирола до кумола; очистка фенола-сырца от микропримесей с использованием кислотных катионитов; очистка ацетона от микропримесей с использованием щелочей; частичный термический крекинг побочных продуктов производства (рис. 2). Окисление проводится в тарельчатой реакционной колонне, снабженной холодильниками; при их помощи поддерживают температуру жидкости от 120 °С на верхней тарелке до 105 °С в кубе. Воздух, предварительно очищенный от загрязнений и механических примесей и подогретый, подают в нижнюю часть колонны под давлением 0,4 МПа. Свежий и оборотный изопропилбензол, к которому добавлен ГПК, инициирующий начальную стадию окисления, подают в подогреватель, а оттуда на верхнюю тарелку реактора.
Воздух движется противотоком к жидкости, барботируя через нее на тарелках колонны. При этом он увлекает с собой пары изопропилбензола и летучих побочных продуктов (муравьиная кислота, формальдегид), которые конденсируются в холодильнике. Оставшийся воздух выводят в атмосферу, а конденсат отмывают от муравьиной кислоты водной щелочью в промывателе-сепараторе. Углеводородный слой сливают в сборник, а водный слой рециркулируют на промывку, сбрасывая в конечном счете в канализацию.
Рис. 2. Технологическая схема кумольного метода получения фенола и ацетона: 1 — реакционная колонна; 2 — холодильник; 3 — промыватель-сепаратор; 4 — теплообменник; 5 — сборник; 6, 8–11 — ректификационные колонны; 7 — узел кислотного разложения ГПК
Оксидат из нижней части колонны отдает свое тепло изопропилбензолу в теплообменнике, дросселируется до остаточного давления 4 кПа и поступает на вакуум-ректификацию для концентрирования гидропероксида. Отгонку изопропилбензола ведут в насадочной ректификационной колонне непрерывного действия, снабженной конденсатором-дефлегматором. Применение вакуума обусловлено термической нестабильностью гидропероксида. Часть конденсированного изопропилбензола возвращают из конденсатора-дефлегматора на орошение колонны, а остальное количество выводят в сепаратор, промывают щелочью и снова направляют на окисление.
Кубовая жидкость из колонны содержит 70–75 % гидропероксида (ГП), а также побочные продукты окисления и остатки изопропилбензола. Путем дополнительной вакуум-ректификации при остаточном давлении 665 Па повышают концентрацию гидропероксида до 88–92 %. Следующую стадию (кислотное разложение гидропероксида) осуществляют одним из двух описанных выше методов [3].
Недостатки кумольного метода. Несмотря на прекрасно отлаженную технологию и длительный опыт эксплуатации, кумольный метод имеет ряд недостатков. Прежде всего это наличие взрывоопасного промежуточного соединения (гидропероксид кумола), а также многостадийность метода, что требует повышенных капитальных затрат и делает труднодостижимым высокий выход фенола в расчете на исходный бензол. Так, при выходе полезного продукта 95% на каждой из трех стадий итоговый выход составит лишь 86%. Приблизительно такой выход фенола и дает кумольный метод в настоящее время.
Но самый важный и принципиально неустранимый недостаток кумольного метода связан с тем, что в качестве побочного продукта образуется ацетон. Это обстоятельство, которое первоначально рассматривалось как сильная сторона метода, становится все более серьезной проблемой, поскольку ацетон не находит эквивалентного рынка сбыта. В 90-х годах эта проблема стала особенно ощутимой после создания новых способов синтеза метилметакрилата путем окисления углеводородов С4, что резко сократило потребность в ацетоне. Об остроте ситуации говорит тот факт, что в Японии разработана технология, предусматривающая рецикл ацетона. С этой целью к традиционной кумольной схеме добавляются еще две стадии - гидрирование ацетона в изопропиловый спирт и дегидратация последнего в пропилен [11]:
(29)
(30)
Образующийся пропилен снова возвращают на стадию алкилирования бензола. В 1992 году фирма «Mitsui» пустила крупное производство фенола (200 тыс. т/год), основанное на этой пятистадийной кумольной технологии.
Предлагаются также другие сходные модификации кумольного метода, которые позволили бы смягчить проблему ацетона. Однако все они приводят к значительному усложнению технологии и не могут рассматриваться как перспективное решение проблемы. Поэтому исследования, ориентированные на поиск новых путей синтеза фенола, которые основывались бы на прямом окислении бензола, в последнее десятилетие приобрели особенно интенсивный характер. Работы ведутся главным образом в следующих направлениях: окисление молекулярным кислородом, окисление моноатомными донорами кислорода и сопряженное окисление.
Отметим, что аналогичные подходы применяются и для поиска эффективных способов селективного окисления низших парафинов, включая метан.
Открытие цеолитных катализаторов для окисления бензола закисью азота
Термодинамически N2O - неустойчивая эндотермическая молекула, свободная энергия образования которой равна 103,6 кДж/моль. Однако кинетически закись азота весьма стабильна, ее некаталитическое разложение становится заметным лишь при температуре выше 600 0С.
В 1983 году Ивамото с сотруд. впервые использовал закись азота для окисления бензола в фенол [39]:
(39)
Эта реакция позволила выйти на принципиально новый уровень селективности по фенолу. При температуре 550 0С и добавлении в реакционную смесь 30% H2O селективность по фенолу на нанесенных ванадиевых катализаторах достигала 71% при конверсии бензола 10%. Этот результат вызвал со стороны ученых оживленные отклики, в которых особо подчеркивалась экологическая безопасность нового процесса и давались весьма оптимистические оценки относительно его практической перспективы [40,41]. Однако пилотные испытания, проведенные в реакторе с кипящим слоем катализатора, не подтвердили эти ожидания. Селективность ванадиевых катализаторов оказалась недостаточно высокой для практического применения процесса.
Тем не менее, работа Ивамото и сотруд. [39] стимулировала поиск новых более эффективных катализаторов. Испытания огромного числа каталитических систем выявили чрезвычайно высокую требовательность реакции окисления бензола в фенол закисью азота. Катализаторы оказывались либо неактивными, либо неселективными [42].
В 1988 г. три группы исследователей - Сузуки с соавт. [43] (Токийский технологический институт), Губельманн и Тирель [44] (фирма «Rhone Poulenc») и Харитонов с соавт. (Институт катализа СО РАН) независимо показали, что лучшими катализаторами этой реакции являются цеолиты ZSM-5. На цеолитах реакция протекает при значительно более низкой температуре и, что особенно важно, с селективностью по фенолу, близкой к 100%. Несмотря на сравнительно небольшой выход фенола, полученный в этих работах, было ясно, что найдена перспективная основа для создания новых катализаторов. Дальнейшие исследования [45-55] позволили значительно улучшить каталитические свойства цеолитов и расширить круг катализируемых ими реакций, включая окисление закисью азота различных производных бензола. В настоящее время на этой основе фирмой «Solutia» (бывшая фирма «Monsanto», США) и Институтом катализа СО РАН ведется создание нового фенольного процесса, который успешно прошел пилотные испытания и принят фирмой к промышленному освоению [56].
Заключение
В работе были приведены основные синтетические методы производства фенола, их преимущества и недостатки. Наряду с ранее использовавшимися способами были изложены современные альтернативные тенденции в области улучшения технологических, экономических и экологических показателей этого процесса. Были рассмотрены научные изыскания по данной тематике. Особое место в данной работе уделяется получению фенола методом окисления бензола закисью азота, как наиболее перспективному и современному методу, упрощающему не только технологический процесс, но и решающему экологическую проблему утилизации закиси азота.
Список литературы
1. Кружалов Б.Д., Голованенко Б.И. Совместное получение фенола и ацетона. М.: Наука, 1963, 200 с.
2. Харлампович, Г.Д. и Чркин Ю. В. Фенолы. М.: «Химия», 1974, 376 с.
3. Юкельсон И.И. Технология основного органического синтеза М.: «Химия», 1968, 848 с.
4. Kirk-Othmer. Encyclopedia of Chemical Technology. 3rd Edition, v.17, p. 373, see article «Phenol».
5. Brownstain A.M. CHEMTECH, September, 1994, p. 58.
6. Miki J., Asanuma M., Tashibana Y., Shikoda T. Bull. Chem. Soc. Japn., 1995, v. 68, p. 2429.
7. ChemExpo, Phenol (1999, March 29) http://www.chemexpo.com/news/PROFILE990329.cfm
8. Полищук В. Химия и жизнь, 1988, № 8, с. 68.
9. Авт. свид. СССР № 7238 и № 7240 от 7.01.1947.
10. Толстиков Г.А. Панорама нефтехимии, 1997, № 4, с. 76.
11. Харлампович Г.Д., Чуркин Ю.В. Фенолы. М.: Химия, 1974, 376 с.
12. SRI report No. 22C, 2-2 (Appl. Catal. A, 1994, v. 114, № 1, p. N2).
13. Марек Л.Ф., Ган Д.А. Каталитическое окисление органических соединений. М.: ОНТИ, 1936, с. 446.
14. Голодец Г.И. Гетерогенно-каталитическое окисление органических веществ. Киев: Наукова думка, 1978, с. 209.
15. Sheldon R.A. Top. Curr. Chem., 1993, v. 164, p. 21.
16. Sasaki K., Kitano T., Nakai T. e. a. New Developments in Selective Oxidation II, Elsevier, 1994, p. 451.
17. Zakharov V.Yu., Zakharova O.M., Romanovsky B. V., Mardaleishvili R.E. React. Kinet. and Catal. Lett., 1977, v. 6, p. 133.
18. Sheldon R.A., Arends I.W.C.E., Lempers H.E.B. Catal. Today, 1998, v. 41, p. 387.
19. Караханов Э.А., Волков С.М., Дедов А.Г. Катализ. М.: изд. МГУ, 1987, с. 147.
20. Notary B. Adv. Catal., 1996, v. 41, p. 253.
21. Belussi G., Rigutto M.S. Stud. Surf. Sci. Catal., 1994, v. 85, p. 177.
22. De Vos D.E., Buskens P.L., Vanoppen D.L. e.a. Compr. Supramol. Chem., 1996, v. 7, p. 647.
23. Arends I.W.C.E., Sheldon R.A., Wallau M., Schuchardt U. Angew. Chem., 1997, Bd. 36, S. 1144.
24. Заявка 62-67038, Япония. Заявл. 20.09.85, № 60-206234, опубл. 26.03.87. МКИ С 07 С 37/60, С 07 С 39/04.
25. Sittig M. Organic Chemical Process Encyclopedia. 2nd ed., 1969, p. 517.
26. Mori M., Nakai T., Jahiro H., Nata M., Sasaki K. Bull. Chem. Soc. Jap., 1995, v. 68, № 6, p. 1747.
27. Shengchun CaO e. a. Chin. J. Petrochem. Tech., 1995, v. 10, p. 708 [Chem. Abstracts, 1995, v. 123].
28. Moro-oka Y., Akita M. Catal. Today, 1998, v. 41, p. 327.
29. Kuznetsova N.I., Detusheva L.G., Kuznetsova L.I. e.a. J. Mol. Catal. A: Chemical, 1996, v. 114, p. 131.
30. Шилов Н.А. О сопряженных реакциях окисления. М., 1905, 304 с.; Нагиев Т.М. Химическое сопряжение. М.: Наука, 1989, 216 с.
31. Clerici M. G., Ingallina P. Catal. Today, 1998, v. 41, p. 351.
32. Kitano T., Wani T., Ohnishi T. e.a. Catal. Lett., 1991, v. 11, p. 11.
33. Jintoku T., Nishimura K., Takaki K., Fujiwara Y. Chem. Lett., 1991, v. 193.
34. Иоффе И. И., Левин Я. С., Кронич И. Г. Ж. физ. химии, 1959, т. 33, № 4, с. 863.
35. Sasaki K., Ito S., Sahek Y., Kinoshita T., Yamasaki T., Harada J. Chem. Lett., 1983, v. 37.
36. Kitajima N., Ito M., Fukui H., Moro-oka Y. J. Chem. Soc. Chem. Communs., 1991, p. 102.
37. Vayenas C.G., Bebelis S.I. Stud. Surf. Sci. Catal., 1997, v. 110, p. 77.
38. Galvita V.V., Belyaev V.D., Demin A.K., Sobyanin V.A. Appl. Catal. A: General, 1997, v. 165, p. 301.
39. Otsuka K., Yamanaka I. Catal. Today, 1998, v. 41, p. 311.
40. Iwamoto M., Matsukami K., Kagawa S. J. Phys. Chem., 1983, v. 87, p. 903.
41. Chem. Econ. Eng. Rev., 1982, v. 14, p. 47.
42. Process Econ. Intern., 1983, v. 4, p. 48.
43. Харитонов А.С., Соболев В.И., Панов Г.И. Успехи химии, 1992, т. 61, № 11, с. 2062.
44. Suzuki E., Makashiro K., Ono Y. Chem. Soc. Jap. Chem. Communs., 1988, p. 953.
45. Gubelmann M.H., Tirel P.J. Pat. 2 630 735 (Fr.).
46. Харитонов А. С., Александрова Т. Н., Вострикова Л. А., Соболев В. И., Ионе К. Г., Панов Г. И. А.с. СССР № 1805127 (Заявка № 4445646 от 22.06.88).
47. Burch R., Howitt C. Appl. Catal. A: General, 1992, v. 86, № 2, p. 139.
48. Zholobenko V. Mendeleev Communs., 1993, v. 1, p. 28.
49. Yoo J.S., Sohail A.R., Grimmer S.S., Chin C.-F. Catal. Lett., 1994, v. 29, p. 299.
50. Bogdan V.I., Kustov L.M., Batizat D.B. e.a. Stud. Surf. Sci. Catal., 1995, v. 94.
51. H д fele N., Reitzmann A., Roppelt D., Emig G. Appl. Catal. A: General, 1997, v. 150, p. 153.
52. Kowalak S., Nowinska K., Swiecicka M. e.a. Proc.: 12th Int. Zeolite Conf., 1998, Baltimore, MRS, v. 4, p. 2847.
53. Nowinska K., Kowalak S., Sopa M., Swiecicka M. Proc.: 3rd Polish-German Zeolite Coll., 1998, Torin: Nicholas Copernicus University Press, p. 215.
54. Motz J.L., Heinichen H., H ц lderich W.F. J. Mol. Catal. A: Chemical, 1998, v. 136, p. 175.
55. Vereshchagin S.N., Kirik N.P., Shishkina N.N., Anshits A.G. Catal. Lett., 1998, v. 56, p. 145.
56. Ushiroguchi T., Sugimoto T. Jap. Patent 10-25260, Jan. 27, 1998.
57. Kuhnle A., Duda M. Eur. Pat. Appl. (1999), EP 953558 A1 19991103.
58. Thayer A.M. Chem. Eng. News, 1998, April 6, p. 21.
59. Sobolev V.I., Dubkov K.A., Paukshtis E.A. e.a. Appl. Catal. A, 1996, v. 141, p. 185.
60. Pirutko L.V., Ivanov D.P., Dubkov K.A. e.a. Proc.: 12th Int. Zeolite Conf., 1998, Baltimore, p. 1245.
61. Panov G.I., Sheveleva G.A., Kharitonov A.S. e.a. Appl. Catal. A, 1992, v. 82, p. 31.
62. Шевелева Г.А., Харитонов А.С., Панов Г.И. и др. Нефтехимия, 1993, № 6, с. 530.
63. Sobolev V.I., Panov G.I., Kharitonov A.S. e. a. J. Catal., 1993, v. 139, p. 435.
64. Filatov M. J., Pelmenschikov A. G., Zhidomirov G. M. J. Mol. Catal., 1993, v. 80, p. 243.
65. Yakovlev A.L., Zhidomirov G.M. Ibid., 1999, v. 91, p. 91.
66. Knops-Gerits P.P., Labinger J.A., Davis M.E. Proc.: Europacat-4 ISO Workshop, 1999, Rimini, p. 129.
67. Panov G.I., Sobolev V.I., Kharitonov A.S. J. Mol. Catal., 1990, v. 61, p. 85.
68. Дубков К.А., Соболев В.И., Панов Г.И. Кинетика и катализ, 1997, т. 38, № 6, с. 1; Харитонов А.С., Александрова Т.Н., Панов Г.И. и др. Кинетика и катализ, 1994, т. 35, № 2,
с. 296.
69. Panov G. I., Uriarte A. K., Rodkin M. A., Sobolev V. I. Catal. Today, 1998, v. 41, p. 365.
70. Zhidomirov G. M., Yakovlev A. L., Kachurovskaya N. A., Yudanov I. V. Ibid., 1999, v. 51, p. 397.
71. Боресков Г.К. Гетерогенный катализ. М.: Наука, 1986, 303 с.
72. Боресков Г.К., Музыкантов В.С., Панов Г.И., Поповский В.В. Кинетика и катализ, 1969, т. 10, № 5, с. 1043.
73. Che M., Tench A.J. Adv. Catal., 1983, v. 32, p. 1.
74. Шилов А.Е., Шульпин Г.Б. Активация и каталитические реакции углеводородов. М.: Наука, 1995, 327 с.
75. Panov G. I., Sobolev V. I., Dubkov K. A., Kharitonov A. S. Stud. Surf. Sci. Catal., 1996, v. 101, p. 493.
76. Dubkov K.A., Sobolev V.I., Talsi E.P. e.a. J. Mol. Catal., 1997, v. 123, p. 155.
77. Ионе К.Г. Полифункциональный катализ на цеолитах. Новосибирск: Наука, 1982. 230 с.; Ratnasami P., Cumar R. Catal. Today, 1991, v. 9, p. 328.
78. Pirutko L.V., Parenago O.O., Lunina E.V. e.a. React. Kinet. and Catal. Lett., 1994, v. 52, № 2, p. 275.
79. Panov G.I., Kharitonov A.S., Fenelonov V.B. e.a. Zeolites, 1995, v. 15, № 3, p. 253.
80. Pirutko L.V., Dubkov K.A., Solovyeva L.P., Panov G.I. React. Kinet. and Catal. Lett., 1996, v. 58, № 1, p. 105.110.
81. Пирютко Л. В., Харитонов А. С., Панов Г. И., Бухтияров В. И. Кинетика и катализ, 1997, т. 38, № 1, с. 102.
82. Panov G.I., Sobolev V.I., Dubkov K.A. e.a. React. Kinet. and Catal. Lett., 1997, v. 61, No. 2, p. 251.
83. Ованесян Н.С., Соболев В.И., Дубков К.А. и др. Изв. Акад. наук, Сер. хим., 1996, т. 6, с. 1583.
84. Ованесян Н.С., Штейнман А.А., Соболев В.И. и др. Кинетика и катализ, 1998, т. 39, № 6, с. 863.
85. Filatov M., Elizarova G., Gerasimov O. e.a. J. Mol. Catal., 1994, v. 91, p. 71.
86. Feng X., Hall W.K. J. Catal., 1997, v. 166, p. 368.
87. Voskoboinikov T.V., Chen H.-Y., Sachtler W.M.H. Appl. Catal. B: Environmental, 1998, v. 19, p. 279.
88. Lazar K., Lejeune G., Ahedi R.K., Shevade S.S., Kotasthane A.N. J. Phys. Chem. B, 1998, v.102, p. 4865.
89. Lobree L.J., Hwang I.-C., Reimer J.A., Bell A.T. J. Catal., 1999, v. 186, p. 242.
90. Joyner R., Stockenhuber M. J. Phys. Chem. B, 1999, v. 103, p. 5963.
91. Bordiga S., Buzzoni R., Geobaldo F. e.a. J. Catal., 1996, v. 158, p. 486.
92. Delmon B. Appl. Catal. B: Environmental, 1992, v. 1, p. 139.
93. Uriarte A.K., Rodkin M.A., Gross M.J. e.a. Stud. Surf. Sci. Catal., 1997, v. 110, p. 857.
94. Патент РФ № 2102135, 1998.
95.Г. И. Панов, А. С. Харитонов Прогресс в области окислительного катализа: окисление бензола в фенол закисью азотаУДК 547.532:542.943
Содержание
Введение
1. Промышленные способы получения фенола
2. Поиск новых путей синтеза фенола
3. Открытие цеолитных катализаторов для окисления бензола закисью азота
4. Природа каталитической активности цеолитов
5. Специфика действия N2O как окислителя
6. Стехиометрическая реакция бензола с a-кислородом
7. Биомиметические свойства a-кислорода
8. Активное состояние железа в цеолитной матрице
9. Новый фенольный процесс. Технологические аспекты
Заключение
Список литературы
Введение
История фенола насчитывает уже более 160 лет. Впервые он был выделен из каменноугольной смолы в 1834 г., откуда и получил свое название. карболовая (угольная) кислота. Быстрый рост потребления фенола поставил вопрос об искусственных способах его получения, создание которых является одной из самых ярких страниц в истории органической химии. Ниже кратко описаны промышленные процессы, которые в то или иное время использовались для получения фенола.
1. Промышленные способы получения фенола
1. Сульфонатный процесс был первым фенольным процессом, реализованным в промышленном масштабе фирмой «BASF» в 1899 г.[1]. Этот метод основан на сульфировании бензола серной кислотой с последующим щелочным плавлением сульфокислоты при 300–350 °С:
Для сульфирования бензола при получении бензолсульфокислоты применяют концентрированную серную кислоту; соотношение Н2SО4: бензол составляет 2:1. Периодический процесс сульфирования проводят при 120—150° С [95].
При щелочном плавлении сульфокислот замещение сульфогруппы на оксигруппу считают результатом сложного процесса, предполагающего промежуточное присоединение щелочи п
|
|
Папиллярные узоры пальцев рук - маркер спортивных способностей: дерматоглифические признаки формируются на 3-5 месяце беременности, не изменяются в течение жизни...
Историки об Елизавете Петровне: Елизавета попала между двумя встречными культурными течениями, воспитывалась среди новых европейских веяний и преданий...
Особенности сооружения опор в сложных условиях: Сооружение ВЛ в районах с суровыми климатическими и тяжелыми геологическими условиями...
Своеобразие русской архитектуры: Основной материал – дерево – быстрота постройки, но недолговечность и необходимость деления...
© cyberpedia.su 2017-2024 - Не является автором материалов. Исключительное право сохранено за автором текста.
Если вы не хотите, чтобы данный материал был у нас на сайте, перейдите по ссылке: Нарушение авторских прав. Мы поможем в написании вашей работы!