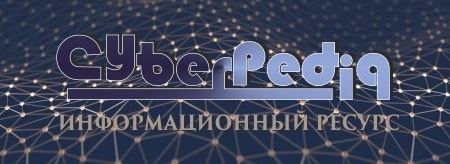
Поперечные профили набережных и береговой полосы: На городских территориях берегоукрепление проектируют с учетом технических и экономических требований, но особое значение придают эстетическим...
Кормораздатчик мобильный электрифицированный: схема и процесс работы устройства...
Топ:
Теоретическая значимость работы: Описание теоретической значимости (ценности) результатов исследования должно присутствовать во введении...
Проблема типологии научных революций: Глобальные научные революции и типы научной рациональности...
Комплексной системы оценки состояния охраны труда на производственном объекте (КСОТ-П): Цели и задачи Комплексной системы оценки состояния охраны труда и определению факторов рисков по охране труда...
Интересное:
Искусственное повышение поверхности территории: Варианты искусственного повышения поверхности территории необходимо выбирать на основе анализа следующих характеристик защищаемой территории...
Принципы управления денежными потоками: одним из методов контроля за состоянием денежной наличности является...
Распространение рака на другие отдаленные от желудка органы: Характерных симптомов рака желудка не существует. Выраженные симптомы появляются, когда опухоль...
Дисциплины:
![]() |
![]() |
5.00
из
|
Заказать работу |
|
|
2.1 Система технического обслуживания и ремонта тепловоза
Техническое обслуживание ТО-1 выполняется локомотивными бригадами при приемке и сдаче тепловоза, а также в пути следования его с поездом. Бригады выполняют работы по смазыванию, креплению ослабших соединений, проверке состояния экипажа, тормозного оборудования и тяговых электродвигателей. Локомотивные бригады несут ответственность за правильный режим работы тепловоза, своевременное предупреждение и устранение выявленных неисправностей и содержание его в исправном состоянии.
Техническое обслуживание ТО-2 проводят на специальных смотровых канавах и в пунктах технического обслуживания локомотивов (ПТОЛ), оборудованных средствами диагностики, специальными приспособлениями и инструментом и располагающих технологическим запасом деталей и материалов. Работы выполняют высококвалифицированные слесари под руководством мастера. На маневровых и вывозных тепловозах ТО-2 выполняют слесари совместно с локомотивными бригадами. В состав работ входят операции по контролю за состоянием ходовых частей, тормозного и другого оборудования, обеспечивающего безопасность движения и предупреждению повреждений тепловозов в эксплуатации.
Периодичность технического обслуживания ТО-2 устанавливает начальник железной дороги (исходя из условий эксплуатации) в пределах 24. 28 ч независимо от выполненного пробега. Продолжительность технического обслуживания ТО-2 для грузовых двухсекционных тепловозов не более 1,5 ч, для пассажирских - не более 2 ч.
Техническое обслуживание ТО-3 выполняется в депо приписки тепловоза для предупреждения появления неисправностей, поддержания тепловозов в работоспособном состоянии, обеспечения их бесперебойной работы и безопасности движения. При этом виде технического обслуживания, кроме осмотров, предусмотренных ТО-2, выполняют некоторые ремонтные операции (смена фильтров, снятие форсунок для проверки на стенде, замена щеток электрических машин, очистка выпускных окон и т.д.).
|
Техническое обслуживание ТО-4 предназначено для обточки бандажей колесных пар без выкатки из-под локомотива для поддержания оптимального размера проката. Продолжительность технического обслуживания ТО-4 устанавливается начальником дороги с учетом местных условий на 1,2 ч на обточку одной колесной пары. Разрешается совмещать обточку колесных пар с техническим обслуживанием ТО-3 и текущими ремонтами ТР-1, ТР-2, увеличивая нормы простоя на 1,2 ч на обточку одной колесной пары.
Номера технических обслуживании связаны между собой такой особенностью: состав плановых работ при ТО с большим номером обязательно включает в себя работы, имеющиеся в регламенте на техническое обслуживание с меньшим номером, т. е. при ТО-2 выполняются работы ТО-1 и сверх того специфические операции; при ТО-3 выполняются объем ТО-2 и плюс свои операции. Эта особенность характерна для всех видов технического обслуживания и ремонта тепловозов, кроме ТО-4 и ТО-5. Так, при текущем ремонте ТР-1 выполняют ТО-3 с соответствующими дополнительными работами по этому виду ремонта, при ТР-2 делаются ТР-1 и плюс операции, необходимые при ТР-2, и т.д., при ТО-5 производят подготовку к ремонту и др.
Текущие ремонты. Системой технического обслуживания и ремонта предусмотрено выполнение в локомотивных депо текущих ремонтов ТР-1, ТР-2 и ТР-3. Под ремонтом понимается совокупность работ, направленных на восстановление основных эксплуатационных характеристик, исправности и работоспособности локомотивов в соответствующих межремонтных периодах путем ревизии, ремонта и замены отдельных деталей, сборочных единиц и агрегатов, регулировки и испытаний, а также частичной модернизации. Текущие ремонты ТР-1, ТР-2 и ТР-3 локомотивов выполняют комплексные и специализированные бригады.
|
Текущий ремонт ТР-1 производится в основном в условиях депо и заключается в осмотре, ревизии и очистке, а при необходимости и в ремонте сборочных единиц (колесные пары, рессорное подвешивание, тормозное оборудование); осмотре тяговых электродвигателей, вспомогательных машин и электроаппаратуры; проверке зазоров подшипников коленчатого вала дизеля, моторно-осевых подшипников тяговых электродвигателей; осмотре поршневых колец и втулок цилиндров дизеля; ревизии и очистке турбокомпрессоров со снятием их с локомотива, проведении реостатных испытаний и т.д.
Текущий ремонт ТР-2 предназначен в основном для ремонта дизеля и вспомогательного оборудования. Основным фактором, определяющим постановку тепловоза на ТР-2, является износ цилиндропоршневой группы дизеля. При текущем ремонте ТР-2 дополнительно к ТР-1 производят ремонт шатунно-поршневой группы и втулок цилиндров, топливной аппаратуры, систем регулирования частоты вращения и мощности дизеля, редукторов, воздухо- нагнетателей, электропневматических приводов регулятора, контакторов, реверсора, вентилей; прожировку кожаных манжет аппаратов; лечебный заряд аккумуляторной батареи; ревизию якорных подшипников всех электрических машин (кроме тяговых электродвигателей); подбивку моторно-осевых подшипников; съемку и осмотр кожухов зубчатой передачи; промежуточную ревизию букс с проверкой разбегов колесных пар и ремонт вентиляторов ТЭД; ремонт тормозного компрессора, автотормозных приборов; полный осмотр автосцепки и фрикционных аппаратов. После выполнения ТР-2 проводятся полные реостатные испытания тепловоза.
Текущий ремонт ТР-3 предусматривает ремонт экипажной части и тяговых электрических машин; изнашивание их основных деталей определяет постановку тепловоза на этот вид ремонта. При текущем ремонте ТР-3 дополнительно к работам по ТР-2 ремонтируют антивибратор, предельный регулятор, водяной и масляный насосы, привод масляного насоса, воздуходувку и ее эластичный привод, вертикальную передачу, секции холодильника, редукторы, тяговые электродвигатели, двухмашинные агрегаты, электродвигатели калорифера, топливоподкачивающего и масло-
|
Примечание. Для тепловозов, имеющих три и более секций, норма продолжительности технического обслуживания ТО-3 и текущего ремонта ТР-1 увеличивается на каждую (более двух) секцию на 4 и 8 ч соответственно.
прокачивающего насосов, аккумуляторные батареи и электрические аппараты. При этом ремонте производятся выкатка из-под тепловоза тележек с полной их разборкой, освидетельствование колесных пар с обточкой бандажей, ремонт рам тележек, букс, рессорного подвешивания, опор рамы тепловоза, кузовного оборудования, песочниц, тормозной рычажной передачи, автоматической локомотивной сигнализации, автостопов, скоростемеров и противопожарной установки.
После выполнения текущего ремонта ТР-3 тепловоз проходит полные реостатные и обкаточные испытания пробной поездкой.
Среднесетевые нормы продолжительности ТО и ТР тепловозов приведены в табл. 2.1.
Капитальные ремонты. Системой технического обслуживания и ремонта тепловозов предусмотрено выполнение капитальных ремонтов КР-1 и КР-2.
Капитальный ремонт КР-1 предназначен для восстановления эксплуатационных характеристик и ресурса (срока службы) тепловоза путем замены и ремонта изношенных и поврежденных агрегатов, сборочных единиц и деталей, а также путем модернизации.
В процессе капитального ремонта КР-2 восстанавливают эксплуатационные характеристики и полный ресурс (срок службы) всех агрегатов, сборочных единиц и деталей, включая базовые, полностью заменяют провода и кабели, а также выполняют модернизацию тепловоза. ТО-3 - техническое обслуживание; ТР-1.ТР-3 - текущие ремонты; КР-1, КР-2 - капитальные ремонты тальных ремонтах возникает не более чем у нескольких десятков локомотивов. Даже если бы капитальные ремонты выполнялись в одном депо для целой дороги, то в среднем потребовалось бы отремонтировать не более сотни секции одной серии. При такой программе загрузка тяжелого ремонтного оборудования была бы слишком мала, чтобы окупиться даже за многие годы.
Разборка
|
С контроллера машиниста снимают кожух. С вертикальных реек снимают контакторные элементы. На верхней крышке снимают и рукоятки. Снимают верхнюю крышку и затем снимают вертикальные стойки. Снимают валы. С валов снимают зубчатый сектор. С нижней крышки снимают главный и тормозной валы, вынимают подшипники.
Ремонт контроллера
Контакторный элемент контроллера снимают со стойки, промывают бензином и осматривают. Проверяют состояние и толщину напаек контактов. При толщине серебряных напаек менее 0,8 мм контакты заменяют. Изоляторы с трещинами, сколами и ослаблением в запрессовке армированной втулки заменяют.
Заменяют и гибкие провода, имеющие оплавление залуженной жилы или с обрывом более 10% жил. Ослабшие наконечники гибких проводов приклепывают к неподвижным контактам и места присоединений припаивают припоем ПОС40. Ролики, имеющие износ по диаметру или износ внутреннего отверстия более, чем 0,2 мм заменяют.
Аксиальный зазор в шарнирных соединениях не должен быть более 0,3 мм, а суммарный зазор между роликом и рычагом не более 0,5 мм. Пружины элемента проверяют на соответствие техническим характеристикам.
Серебряный подвижный контакт очищают от копоти бензином. Определяют износ контакта и состояние бронзовой пружинной ленты, на которой он закреплен. При износе контакта до толщины 0,8 мм его заменяют. Заменяют также держатель контакта с трещинами и с потерей пружинных свойств и подвижный контакт с износом серебряной напайки до 0,2 мм.
Кулачковый вал разбирают.
С него снимают детали блокировочного механизма: диски, шестерни. Осматривают состояние деталей и подшипников. Подшипники промывают в бензине. Проверяют посадку шайб и деталей блокировочного механизма навалу. При наличии трещин в обоймах или сепараторах, повреждений поверхности шариков, подшипники заменяют. Диски, шестерни, шейки валов, стальные кулачки проверяют шаблонами и зубомерами. При необходимости восстанавливают наплавкой. Кулачковые шайбы, имеющие износ по диаметру более 4 мм, а также с нарушением профиля заменяют. Валы с биением более 0,5 мм протачивают на токарном станке.
Проверяют посадку шайб и деталей блокировочного механизма на валу.
Механизм блокировки разбирают. Разработанные отверстия в рычагах, дисках восстанавливают запрессовкой бронзовых втулок. При ослаблении оси в рычагах запорного механизма ее заменяют. Профиль блокировочных рычагов и шайб проверяют шаблонами. Износ запорных приливов, звездочек рычага или впадин шайб восстанавливают наплавкой или приваркой накладных пластин.
Толщину новой пластины определяют при предварительном осмотре контроллера перед разборкой. Упорные накладки блокировочных звездочек при ослаблении наклепывают. Пружины блокировок проверяют на их соответствие характеристикам.
|
Рукоятки контроллера КВ-0801 разбирают. Изношенную накладку защелки рычага заменяют. Разработанные отверстия в корпусе заваривают с последующей рассверловкой до чертежных размеров. Изношенный упорный зуб и выступ рычага наваривают. Окончательную высоту выступа пригоняют по месту после установки рукоятки на контроллер. Пружины с отогнутыми концевыми витками, имеющие остаточную деформацию заменяют. Рукоятки промывают бензином и полируют.
Сборка
Собирают контроллер в порядке, обратном разборке. В нижнюю крышку впрессовывают подшипники и устанавливают в них главный и тормозной валы. На промежуточной раме монтируют валы рукояток с укрепленными на них зубчатыми секторами. Нижнюю и верхнюю крышку скрепляют на уголки, образуя каркас. После этого проверяют легкость вращения валов, осей, убеждаются в совпадении осевых линий зубчатых секторов и шестерен, деталей блокировочного механизма. На верхней крышке укрепляют секторы положений и рукоятки. На вертикальных рейках устанавливают контакторные элементы, при этом следят, чтобы паз изолятора плотно прилегал к квадрату рейки.
Регулировка
После смазки всех трущихся частей проверяют четкость работы контроллера и правильность включения и выключения контакторных элементов на каждой фиксированной позиции главной и тормозной рукояток контроллера. Положение контакторных элементов должно соответствовать диаграмме их замыкания (развертке кулачковых шайб). При замкнутом контакторном элементе зазор между роликом контакторного элемента и линией профиля кулачковой шайбы должен быть не менее 1 мм.
При разомкнутых контакторах точка касания ролика с рабочей поверхностью кулачковой шайбы должна находиться до начала линии профиля на расстоянии не менее 0,5 мм. Раствор контактов, равный 4-7 мм, регулируют постановкой прокладок из электрокартона между пазом изолятора и рейкой. Боковое смещение ролика контакторного элемента с кулачковой шайбы устраняют перемещением подвижного рычага контактора. Кулачковые валы в любом положении не должны иметь свободного хода по окружности кулачковых шайб более 25 мм.
В пределах свободного хода контакты контакторных элементов не должны перемещаться, а на фиксированных позициях должны быть или полностью включены, или полностью выключены.
После проверки работы контроллера производят подгонку уплотнения кожуха и окраску корпуса и кожуха серой эмалью ГФ-92-ХС.
Инструмент и приспособления
При ремонте контроллеров применяют мерительный, слесарный и механизированный инструмент.
К мерительному инструменту относятся: линейки, складные и ленточные метры, штангенциркули, шаблоны, микрометры, угольники, лекала.
Слесарные инструменты составляют: кувалды, молотки, зубила, крейцмессели, тиски, напильники, пассатижи, набор гаечных ключей, отвертки, циркули, ножовки и т.д.
К механизированному инструменту и приспособлениям относятся: пневматические гайковерты, сверлильные машины, пневмо отвертки, краскораспылители, гидравлические съемники для спрессовки шестерен с валов барабанов, приспособление для выпрессовки подшипников и др.
2.7 ТИ обслуживания
Контролер машиниста тепловоза КВ-0801.
Контроллер машиниста осматривают на тепловозе. При включенном рубильнике аккумуляторной батареи открывают смотровую дверцу и протирают детали контроллера без ворсовыми салфетками, слегка смоченными бензином, а затем сухими.
Затем проверяют состояние проводов, подходящих к контроллеру, плотность затяжки их наконечников, покачивая каждый наконечник за "трубку", наличие бирок на проводах, состояние штурвала 11, пружин 15 и 21 и контактных элементов 2 (Приложение А рис. 1), а также четкость фиксации позиций. При люфте, превышающем 1°, у штурвала подбирают и устанавливают между ним и валом прокладку из латуни размером 9*20 мм и толщиной 0,1-0,6 мм в зависимости от величины люфта. После установки прокладки плотно затягивают гайку штурвала.
В деталях корпуса 3 контроллера не должно быть трещин. Все ролики или шарикоподшипники должны свободно вращаться, пружины не иметь трещин и изломов. При обнаружении нечеткой фиксации позиций проверяют состояние рабочих поверхностей храповика главного барабана, износ ролика или шарикоподшипника и их оси, установленных на рычаге 20, и упругость пружины 20. Неисправные детали заменяют. Если это невозможно сделать на тепловозе, заменяют контроллер и ремонтируют его в электроаппаратном отделении изломов. При осмотре контактных элементов 2 в первую очередь проверяют контакты.
При копоти и небольших подгарах контакты зачищают стальной хромированной пластинкой. Допускается зачищать контакты и стеклянной шлифовальной бумагой.
Контактный элемент контроллера КВ-0801.
Рычаг контактный элемент контроллера должен перемещаться свободно и без заеданий. Изолятор с трещинами или отколами заменяют.
При необходимости добавляют в подшипники вала главного барабана смазку ЦИАТИМ-221. В заключение проверяют диаграмму замыканий контактов контактных элементов главного и реверсивного барабанов.
Требования к организации рабочего места
Эксплуатируемое оборудование должно быть в полной исправности. Ограждение или защитные устройства должны быть установлены на место и соответствующим образом закреплены.
Работать на неисправном оборудовании и при отсутствии или неисправном ограждении запрещается.
Вновь установленное или вышедшее из капитального ремонта оборудование может быть пущено в работу только после его комиссионной приемки с участием начальника цеха и инженера по охране труда.
Верстаки, столы и стеллажи должны быть прочными, устойчивыми и безопасными для работы и надежно закреплены на полу.
Ящики верстаков должны иметь стопоры.
Поверхность верстаков должна быть обита гладким материалом, столы и стеллажи не должны иметь выбоин, заусенцев, трещин и др. дефектов.
Полки стеллажей должны иметь наклон внутрь во избежание падения хранящихся предметов.
При обивке верстака нельзя допускать выступающих кромок и острых уголков. Ширина верстака должна иметь не более 0.75м. Расстояние между тисами на верстаках должно соответствовать размеру обрабатываемых деталей и быть не менее 1м между осями тисов.
Для защиты рабочих от отлетающих осколков на верстаке должны быть установлены сетки высотой не менее 1м с ячейками не более 3-х мм.
Детали и материалы, поступившие на обработку, должны размешаться на специальных и четко обозначенных местах.
Передачи (ременные, канатные, цепные, шарнирные и др.) должны иметь прочные предохранительные ограждения. Вращающиеся элементы оборудования и механизмов, находящиеся на высоте ниже 2,5м от пола, должны быть ограждены.
Для каждого работающего должно быть обеспечено удобное рабочее место, не стесняющее его действий во время исполняемой работы. Рабочее место должно быть обеспечено достаточной площадью для размещения вспомогательного оборудования, а так же необходимым инвентарем для хранения инструмента, оснастки заготовок и обрабатываемых изделий (стеллажи, столы, ящики, тумбочки и т.п.).
На рабочем месте под ногами рабочего должен быть исправный деревянный решетчатый настил, у которого расстояние между планками должно соответствовать 25-30мм.
Рабочее место должно быть достаточно освещенным и содержатся в чистоте.
Уборка рабочего места должна производиться в течение рабочего дня и после каждой смены по мере накопления на рабочих местах готовой продукции и отходов
|
|
Своеобразие русской архитектуры: Основной материал – дерево – быстрота постройки, но недолговечность и необходимость деления...
Историки об Елизавете Петровне: Елизавета попала между двумя встречными культурными течениями, воспитывалась среди новых европейских веяний и преданий...
Архитектура электронного правительства: Единая архитектура – это методологический подход при создании системы управления государства, который строится...
Биохимия спиртового брожения: Основу технологии получения пива составляет спиртовое брожение, - при котором сахар превращается...
© cyberpedia.su 2017-2024 - Не является автором материалов. Исключительное право сохранено за автором текста.
Если вы не хотите, чтобы данный материал был у нас на сайте, перейдите по ссылке: Нарушение авторских прав. Мы поможем в написании вашей работы!