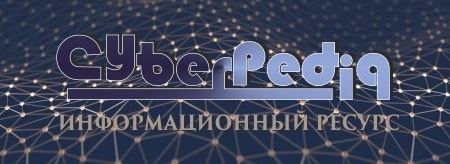
Индивидуальные и групповые автопоилки: для животных. Схемы и конструкции...
Особенности сооружения опор в сложных условиях: Сооружение ВЛ в районах с суровыми климатическими и тяжелыми геологическими условиями...
Топ:
Техника безопасности при работе на пароконвектомате: К обслуживанию пароконвектомата допускаются лица, прошедшие технический минимум по эксплуатации оборудования...
Генеалогическое древо Султанов Османской империи: Османские правители, вначале, будучи еще бейлербеями Анатолии, женились на дочерях византийских императоров...
Выпускная квалификационная работа: Основная часть ВКР, как правило, состоит из двух-трех глав, каждая из которых, в свою очередь...
Интересное:
Что нужно делать при лейкемии: Прежде всего, необходимо выяснить, не страдаете ли вы каким-либо душевным недугом...
Отражение на счетах бухгалтерского учета процесса приобретения: Процесс заготовления представляет систему экономических событий, включающих приобретение организацией у поставщиков сырья...
Наиболее распространенные виды рака: Раковая опухоль — это самостоятельное новообразование, которое может возникнуть и от повышенного давления...
Дисциплины:
![]() |
![]() |
5.00
из
|
Заказать работу |
|
|
Пневмотранспортные установки могут перемещать сыпучие материалы по сложной траектории; забирать их из различных средств доставки и труднодоступных мест; выдавать материал в различных точках. Пневмотранспорт надежно защищает груз от атмосферных воздействий и обеспечивает необходимые санитарно-гигиенические условия труда обслуживающего персонала. Окружающая среда защищена от распыления транспортируемого материала, и требования экологии соблюдаются.
Пневмотранспортные установки удобны для размещения оборудования и трубопроводов, которые могут быть проложены с учетом любых местных условий производства, в том числе и в труднодоступных местах. Это оборудование отличается простотой эксплуатации, легкостью управления, возможностью автоматизации процессов транспортирования и дистанционного управления.
Применение пневмотранспорта улучшает условия труда на предприятиях строительной индустрии, при производстве цемента, гипса и других вяжущих материалов. Широкое внедрение пневмотранспорта для пылящих материалов имеет большое социальное значение – резко уменьшается опасность массовых профзаболеваний.
К недостаткам пневмотранспорта относят сравнительно высокий удельный расход электроэнергии и износ трубопроводов и других частей установок, взаимодействующих с транспортируемым материалом.
В настоящее время промышленность выпускает серийно вагоны- цистерны с пневморазгрузкой, специализированный автотранспорт, оборудованный пневмосистемами, камерные и винтовые насосы различных модификаций, пневморазгрузчики и пневмоподъемники сыпучих материалов,
247
донные и боковые выгружатели, различное оборудование для пневмосистем, вакуум-насосы, воздуходувки и компрессоры.
|
Основными вяжущими материалами, применяемыми в строительстве, являются цемент, известь и гипс. Различные виды цемента, изготовляемые в России (портландцемент, гидрофобный, сульфатостойкий и пуццолановый цемент, глиноземный цемент, шлакопортландцемент, и др.), отличаются по физико-механическим свойствам, которые влияют на процесс пневмотранспортирования и, соответственно, должны учитываться. Пневматический транспорт применяется для перемещения порошкообразной извести, молотой известняковой муки, минеральных порошков для асфальтобетонных смесей, сухой золы, керамзита и других сыпучих материалов.
Широко применяется пневматическое транспортирование для перемещения сухих цементно-песчаных и известково-песчаных смесей в установках по набрызгу бетонных и растворных смесей при безопалубочном бетонировании; для укрепления горных выработок; при изготовлении тонкостенных резервуаров; при замоноличивании стыков сборных железобетонных конструкций.
Пневматический транспорт применяют в строительстве при выполнении различных производственных процессов и особенно часто при погрузке и разгрузке вяжущих материалов. Так, пневматический транспорт применяют при загрузке и выгрузке вяжущего из всех видов наземных транспортных средств закрытого типа. Перевозить вяжущие материалы в открытых автомобилях, железнодорожных полувагонах и вагонетках запрещено из-за больших потерь этого ценного строительного материала. Для этих целей созданы специализированные автомобильные и железнодорожные транспортные средства различной грузоподъемности, из которых вяжущие материалы выгружают по трубопроводу непосредственно в силос склада. Пневматический транспорт применяют при загрузке и выгрузке цемента из речных барж, в различных складских операциях и для подачи цемента со склада в расходные бункера бетоно-растворосмесительных заводов и установок.
|
В зависимости от характера и объема работ в строительстве применяют все основные виды и типоразмеры пневмотранспортных установок и оборудования с различными параметрами (производительностью от 0,1 до 100 т/ч; дальностью подачи от 1,5 до 1000 м; с расходом сжатого воздуха от 0,5 до 100 м3 /мин и т.д.).
В большинстве пневмотранспортных установок в качестве транспортирующего газа используют воздух. Однако, когда не допустимо соприкосновение воздуха с транспортируемым материалом, применяют инертный газ (например, при транспортировании взрывоопасных и легкоокисляющихся материалов). Установки для пневматического транспортирования материалов различают по давлению несущего потока, размеру частиц и концентрации перемещаемого материала в потоке, характеру движения потока, типам питательных устройств и др. Наиболее часто их классифицируют по концентрации перемещаемой смеси материала с воздухом
248
и значению давления в пневмосистеме. Концентрация смеси перемещаемого материала μ (или расходная массовая концентрация) – отношение массы материала к массе транспортирующего воздуха (материал, кг / воздух, кг).
Различают установки с низкой, средней и высокой концентрацией частиц транспортируемого материала. За верхнюю границу низкой концентрации принимают расходную массовую концентрацию μ до 4 кг/кг. Средняя концентрация соответствует значению μ от 4 до 20 кг/кг, μ > 20 кг/кг характеризует поток с высокой концентрацией. Границей между пневматическим транспортированием с разбавленной и плотной фазами является расходная массовая концентрация 50…60 кг/кг. Массовая концентрация 500…600 кг/кг считается наиболее высокой.
В последнее время в различных отраслях промышленности стали применять новые, более экономичные установки пневмотранспорта, в которых материал перемещается сплошным потоком, т.е. в условиях плотной фазы (аэрожелоба, поршневой транспорт). Еще более экономичен интенсивно развивающийся контейнерный пневмотранспорт, в котором материал перемещается по трубопроводам в специальных емкостях-контейнерах.
По способу воздействия воздуха все пневмотранспортные установки можно разделить на несколько основных групп (рис. 5.12).
К первой группе относятся пневмотранспортные установки, в которых сыпучий материал перемещается в потоке воздуха, т.е. на материал действуют силы давления. По способу создания в транспортном трубопроводе разности давления эти установки могут быть всасывающего, нагнетательного и всасывающе-нагнетательного действия. Для перемещения сыпучего материала в воздушном потоке скорость потока должна превышать скорость витания перемещаемого материала, которая может быть определена эмпирической зависимостью
|
v вит
» 4,8 ,
где d – средняя величина поперечного размера частиц перемещаемого материала; γ –
плотность частиц.
Пневмотранспортные установки второй группы работают по принципу аэрации порошкообразных материалов. Здесь воздух косвенно воздействует на перемещаемый материал. Установки этой группы по характеру выполняемых работ подразделяются на аэротранспортные и аэрационные.
Установка всасывающего действия (рис. 5.12, а) состоит из заборного устройства или сопла 1, системы материалопроводов 2, осадителя материала с фильтрами 3, воздухопровода 4 и побудителя тяги – воздуходувки или вакуум- насоса 5, который просасывает через всю установку воздух. Этот воздух, поступая в сопло, захватывает материал, перемещая его по системе материалопроводов.
Материал выделяется в осадителе, а транспортирующий воздух очищается, проходя через фильтры, и выбрасывается в атмосферу. Всасывающие установки имеют разгрузочные устройства и фильтры сложной конструкции, находящиеся под значительным разрежением. Из них необходимо непрерывно выводить наружу осажденный материал.
В установках всасывающего действия используется низкий (до 90 кПа), средний (до 70 кПа) и высокий (до 40 кПа) технический вакуум.
В пневматических установках нагнетательного действия (рис. 5.12, б)
трубопроводы и аппаратура находятся под избыточным давлением.
Материал подается в пневмотранспортную систему специальным устройством: пневматическим винтовым насосом, камерным насосом, струйным насосом и т.п.
Главной отличительной особенностью нагнетательных установок является высокая величина избыточного давления, что позволяет применять их для транспортирования материалов на значительные расстояния при максимальных концентрациях аэросмеси. Рабочее давление сжатого воздуха на входе в установку составляет 30 кПа, а в отдельных случаях – 500…600 кПа.
|
Установки всасывающе-нагнетательного действия (рис. 5.12, в) сочетают
основные преимущества рассмотренных установок. В них использованы заборные устройства установок всасывающего действия, работающих без пылевыделения.
В основном, наиболее протяженном, транспортном трубопроводе материал переносится под давлением при более высоких концентрациях. В небольших установках обе ветви (всасывающая и нагнетающая) могут работать от одного вентилятора. Осадитель 3 всасывающей установки имеет в верхней
части матерчатый фильтр, который не допускает попадания пыли в воздуходувную машину.
Аэрационная установка (рис. 5.12, г) применяется для равномерной выгрузки материалов из силосов и бункеров. Расположенные в конической части силоса аэролотки 18, через перфорированную поверхность которых подается сжатый воздух, аэрируют материал, не позволяют ему зависать и образовывать своды при выпуске из емкости.
В аэротранспортной установке (рис. 5.12, д) происходит псевдоожижение сыпучего материала сжатым воздухом, проходящим через перфорированную перегородку, расположенную внутри аэрожелоба 16. Мелкий некомкующийся материал в псевдоожиженном слое устойчиво перемещается вдоль желоба, устанавливаемого под небольшим углом к горизонтальной плоскости, за счет гравитационных сил и пониженного коэффициента трения, за счет воздушной подушки. Они относятся к установкам нагнетательного действия с низким давлением, транспортирующим материал в условиях плотной фазы.
Рис. 5.13. Пневматический транспортный желоб
Конструктивная схема аэрожелоба приведена на рис. 5.13. Он состоит из двух частей 1 и 3, изготовленных из листовой стали и соединенных болтами. Между частями желоба помещают пористую перегородку 2, которая может быть керамической или матерчатой – тканой, цельной или составной. Материал поступает из бункера 8 и движется в желобе по поверхности перегородки. Вентилятором 5 с двигателем 10 через всасывающий фильтр 9 и гибкий шланг 7 подают воздух в нижнюю часть желоба, который равномерно распределяется по всей поверхности перегородки и, проходя сквозь нее, аэрирует слой материала, приводя его в состояние текучести. Далее воздух проходит сквозь слой материала и пропускается через матерчатые фильтры 4, расположенные в окнах по всей длине крышки желоба. Подача воздуха регулируется дросселем
6. Пневматический желоб в ряде случаев выгоднее винтового конвейера, так как в нем отсутствуют движущиеся изнашивающиеся части и он менее энергоемок. Давление сжатого воздуха составляет 0,005 МПа, скорость
|
перемещения частиц материала – не более 4…7 м/с, а концентрация до
600…800 кг/кг.
В последнее время на ряде промышленных предприятий успешно применяют контейнерный пневмотранспорт (рис. 5.11, е). Материал при таком пневмотранспортировании перемещается по трубопроводам в специальных емкостях под действием давления воздуха. Высоконапорное импульсное пневмотранспортирование (рис. 5.14) осуществляется в установках пульсирующего действия. В них материал перемещается импульсами в виде пробок с промежутками, заполненными сжатым воздухом. Материал подается с высокой концентрацией, и его можно транспортировать, даже если он имеет плохую текучесть, склонен к налипанию на стенки трубопровода. Также можно перемещать без разрушения частиц гранулированные и зернистые материалы. Импульсное транспортирование со скоростями от 2 до 6 м/с отличается высокой экономичностью, так как при минимальном расходе воздуха достигается высокая производительность. Малые скорости материаловоздушных потоков дают возможность снижать общие энергетические затраты, сокращать абразивный износ элементов установки, транспортировать чувствительные к истиранию продукты, ликвидировать расслоение подаваемой смеси и применять фильтрующие установки с малой поверхностью фильтров.
Рис. 5.14. Схемы импульсного пневмотранспортирования:
а – импульсная подача с образованием пробок в начале транспортного трубопровода;
б – импульсная подача с прокладкой перфорированного транспортного трубопровода;
в – импульсная подача с прокладкой параллельного воздухопровода с форсунками
Разгрузчики цемента. В последние годы созданы разнообразные машины для выгрузки цемента из крытых железнодорожных вагонов, судов и барж. Наиболее широко применяются вакуумные разгрузчики (рис. 5.15) производительностью 15…90 т/ч.
В состав разгрузчика входят: самоходное заборное устройство 1, гибкий цементопровод 2, осадительная камера 3, водокольцевой вакуум-насос 5, шкаф
с электроаппаратурой 4.
Заборное устройство серийных разгрузчиков цемента (рис 5.16) представляет собой самоходную тележку безрамной конструкции на двух ребристых металлических колесах 9 с приводом от индивидуальных электродвигателей 7 через специальные червячные редукторы 8. В центральной части тележки смонтирован редуктор 4 с электродвигателем 5 привода
253
подгребающих дисков 1, расположенных под углом 3° к плоскости пола вагона. В дисках выполнены пазы (перфорации) заданной формы со скошенными внутренними стенками. С помощью перфорации разгружаемый сыпучий материал подается вращающимися дисками к заборной кромке всасывающего сопла. Режим работы дискового питателя обеспечивает дозированную подачу материала к соплу, причем в процессе перемещения разгружаемый материал частично насыщается воздухом, что способствует интенсификации его поступления во всасывающее сопло. Для обрушения цементной массы на диски к передней стенке редуктора прикреплен штыревой рушитель 3. В ряде конструкций применяются приводные рушители. Над подгребающими дисками расположено всасывающее сопло 2, конфигурация которого обеспечивает введение материала во всасывающую линию при сравнительно небольших потерях давления на разгонном участке трубопровода. К верхней части сопла крепится поворотный патрубок 10, на который насаживается гибкий резинотканевый рукав 6. К нижней части сопла крепится зачистное устройство, улучшающее зачистку пола вагона от разгружаемого материала. Оператор с переносного пульта включением соответствующих кнопок может перемещать заборное устройство вперед, назад и разворачивать его на месте. Основные параметры, определяющие производительность заборного устройства, – диаметр перфорированных дисков и соответствующее сечение всасывающего сопла.
Рис. 5.15. Общий вид пневматического разгрузчика цемента всасывающего типа
Цементопровод разгрузчика состоит из трех секций резинотканевых рукавов общей длиной 12 м, что достаточно для забора материала из всех частей железнодорожного вагона. Увеличение длины всасывающей линии нежелательно, так как вследствие увеличения потерь давления ухудшается работа разгрузчика.
![]() |
Рис. 5.16. Заборное устройство пневматического разгрузчика всасывающего типа
Осадительная камера (рис. 5.17) состоит из камеры фильтров 4, механизма выгрузки 1 и механизма продувки фильтров 5. Камера фильтров представляет собой металлический бункер цилиндрической формы с коническим днищем, установленный на корпусе шнека 8 механизма выгрузки. В камере фильтров, разделенной на два отсека перегородкой, размещены рукавные фильтры 3. Фильтровальная рукавная ткань надета на проволочный каркас, предотвращающий сплющивание фильтра во время работы, и закреплена на нем хомутами. Собранные фильтры устанавливают и закрепляют в верхней части камеры. На конической части камеры фильтров расположены два люка для монтажа и ревизии фильтров. Под фильтрами смонтирован металлический отбойник 2, предохраняющий ткань фильтров от пробоя посторонними предметами, загрязняющими цемент, и отбрасываемыми лопастями шнека.
Фильтры очищаются во время кратковременного поочередного сообщения отсеков осадительной камеры с атмосферой. Механизм очистки (продувки) состоит из сварного корпуса, в котором расположены закрепленные на штоках тарелки клапанов. Закрываются наружные клапаны пружинами. Во время работы разгрузчика весь отсасываемый воздух проходит через фильтры в вакуум-насос. Для очистки фильтров шток клапана перемещается тросовой
системой вручную, при этом атмосферный воздух проходит с большой скоростью через фильтровальную ткань в обратном направлении.
Механизм выгрузки состоит из корпуса шнека 8, электродвигателя 6 с установленным и закрепленным на его валу напорным шнеком 12, узла уплотнения 7, обратного клапана 15, выгрузочного патрубка 14 и рамы 17. Напорный шнек плотно насажен на конусный конец винтовой втулки 10, напрессованной на вал электродвигателя, и закреплен с помощью шпильки 11. Уплотнение вала шнека обеспечивается вращающейся в гильзе 9 винтовой втулкой 10 в сочетании с сальниковой набивкой, выполненной из асбестографитового шнура диаметром 8 мм, поджатого в гнезде грундбуксой.
Рис. 5.17. Осадительная камера пневморазгрузчика цемента всасывающего типа
Основная масса цемента отбрасывается винтовой частью уплотнения, остальная часть задерживается сальниковой набивкой. Между винтовой втулкой и гильзой предусмотрен зазор 0,5…0,6 мм на сторону. При увеличении этого зазора надежность работы уплотнения снижается.
Для предотвращения проникновения атмосферного воздуха в полость шнека в патрубке механизма выгрузки устанавливается обратный клапан 15, создающий цементную пробку в гильзе. Для этого в конструкции шнека часто предусматривается уменьшение шага витков в направлении движения материала, но это увеличивало потребляемую мощность и износ шнека и гильзы 13. Выполнение шнека с большим шагом на конце, как показано на рис.
5.17, обеспечивает создание надежной цементной пробки в конце гильзы даже в разгрузчиках цемента всасывающе-нагнетательного и нагнетательного действия, а также в пневмоподъемниках, когда вместо выгрузочного патрубка 14 имеется смесительная камера, в которой цемент перемешивается с воздухом, подаваемым под давлением. Ось клапана смонтирована на шарикоподшипниках в выносных опорах. Для обеспечения необходимой износостойкости витки шнека наплавляются по торцовой и рабочей поверхности износостойкой порошковой лентой.
Для создания разрежения в системе пневматического разгрузчика цемента применяют водокольцевой вакуум-насос соответствующей производительности по воздуху. В комплект электрооборудования входят шкаф с электроаппаратурой; две клеммные коробки, одна из которых устанавливается в помещении склада цемента, а вторая – на заборном устройстве; переносной пульт управления и комплект электрокабелей. В системе дистанционного управления заборным устройством применено безопасное напряжение 40 В. В пластмассовом корпусе пульта управления смонтированы кнопки управления заборным устройством и тумблер включения дискового питателя. В электрошкафу расположена вся пусковая аппаратура и приборы контроля. Открывающаяся передняя дверца и съемная задняя стенка обеспечивают удобство монтажа и обслуживания электроаппаратуры. Заборное устройство через распределительную коробку соединено с электрошкафом и пультом управления кабелями.
С переносного пульта управления включаются и выключаются электродвигатели привода перфорированных дисков и колес.
Все агрегаты разгрузчика и клеммные коробки для заземления присоединены к общему заземляющему контуру склада цемента.
Агрегаты пневморазгрузчика устанавливают на месте эксплуатации в соответствии с типовой схемой прирельсового склада цемента силосного типа (рис. 5.18) в целях повышения эксплуатационной производительности пневморазгрузчика осадительную камеру целесообразно располагать возможно ближе к рельсовому пути над приемным бункером вместимостью не ниже 1,5…2 т.
Под приемным бункером монтируют пневматический подъемник цемента соответствующего типоразмера, обеспечивающий подачу разгружаемого материала в силосные емкости склада.
Вакуум-насос с водоотделительным бачком и шкаф с электроаппаратурой монтируют в отдельном, смежном со складом помещении машинного отделения. Для нормальной эксплуатации разгрузчика в зимнее время это помещение должно быть утеплено. Эксплуатационная производительность разгрузчиков зависит от времени, затрачиваемого обслуживающим персоналом на выполнение вспомогательных операций, включая открывание дверей крытого железнодорожного вагона, установку въездного трапа, разборку и удаление щита дверного проема и зачистку вагона после выгрузки основной массы.
В России ведущей фирмой, разрабатывающей и выпускающей пневмотранспортное оборудование, является ОАО «Строительные машины» (Санкт-Петербург). Всасывающие пневматические установки широко применяют за рубежом для выгрузки пылевидных, мелкозернистых и гранулированных сыпучих грузов, перевозимых навалом железнодорожным, водным и автомобильным транспортом. За рубежом длительное время осуществляется производство и совершенствуются конструкции пневмовинтовых насосов. Ведущими фирмами являются Fuller (США) и Claudius Peters Technologies (ФРГ). Бельгийская фирма Vigan выпускает пневмоустановки всасывающе-нагнетательного действия. Швейцарская фирма Bűller выпускает пневмотранспортные установки трех типоразмеров.
Рис. 5.18. Схема установки пневморазгрузчика цемента всасывающего действия на силосном складе цемента: 1 – пневматический винтовой насос; 2 – пневматический подъемник; 3 – пневморазгрузчик цемента всасывающего действия; 4 – цементопровод; 5 – бункер-осадитель; 6 – аэрожелоб; 7
– силосные емкости; 8 – донный выгружатель; 9 – аэрожелоб
Шведская фирма Atlas Copco выпускает пневматические всасывающие установки для перемещения зернистых и гранулированных сыпучих материалов, например зерна, песка, стальных опилок, дроби, медного шлака,
формовочной земли. Небольшие габаритные размеры установки позволяют использовать ее на различных площадках, вместе с компрессором размещать на автомобильном прицепе, устанавливать на палубе разгружаемого судна.
Основные узлы установки (рис. 5.19) – эжектор 5, первичный 3 и вторичный 4 сепараторы и блок управления 6. Воздушный эжектор создает вакуум в двух сепараторах и всасывающем трубопроводе 2. Разгружаемый материал проходит через заборное сопло 1 и направляется в первичный сепаратор 3, где отделяются крупнозернистые частицы; более мелкие эффективно сепарируются во вторичном циклонном сепараторе 4, а транспортирующий воздух выбрасывается в атмосферу через эжектор. Для опорожнения сепараторов во время работы под ними расположены шлюзовые камеры 8. Между сепаратором и соответствующей шлюзовой камерой, а также между шлюзовой камерой и атмосферой установлены специально сконструированные клапаны, приводимые в действие сжатым воздухом. Перед опорожнением сепаратора в шлюзовой камере с помощью специального вентиля 7 создается такое же разрежение, как и в сепараторе. После открытия верхнего клапана 9 включается пневматический шаровой вибратор, обеспечивающий полное опорожнение сепаратора от материала. После закрытия верхнего клапана в шлюзовой камере вновь создается атмосферное давление, при котором открывается нижний клапан 10, и материал выгружается. Специальный блок 6 автоматически управляет работой установки, причем цикл работы устанавливается в зависимости от перемещаемого материала. Установкой можно управлять и вручную, используя блок управления.
Рис. 5.19. Принципиальная схема пневморазгрузчика шведской фирмы Atlas Copco
Группу отверстий заборного сопла 1 установки закрывает или открывает оператор при помощи штурвала, смонтированного в верхней части сопла. Таким образом регулируется поступление дополнительного воздуха в транспортный материалопровод. Для обеспечения надежной эксплуатации установки на сопле установлен вакуумметр, по показаниям которого оператор поддерживает в системе необходимое разрежение.
Установка смонтирована на трубчатой раме, и ее можно расположить на рабочей площадке в непосредственной близости от места разгрузки. В зависимости от требуемой производительности установку оборудуют одним или двумя эжекторами.
Шведская фирма Interconsult разработала систему для разгрузки цемента из судов (рис. 5.20). На береговом причале устанавливают камерные насосы с воздуходувками, которые всасывают и нагнетают материал. Трюмы обычных судов оборудуют аэроднищами. Сжатый воздух к ним подают с берега от воздуходувки 14. С помощью вакуум-насоса 10 создается разрежение в резервуаре 5, благодаря чему в него засасывается аэрированный цемент из трюма. Наполненный цементом резервуар, вместимость которого равна вместимости трюма, переключают на нагнетательный режим работы. Резервуары разгружают поочередно по трубопроводам, проложенным от
камерного насоса непосредственно в силос. Аэроднища выполняют из синтетического пористого материала, натянутого на стальную решетку.
Рис. 5.20. Схема пневмоустановки для разгрузки барж шведской фирмы Interconsult:
1 – баржа-цементовоз; 2 – указатель уровня материала; 3 – фильтр грубой очистки; 4 – диффузор; 5 – резервуар;
6 – фильтр тонкой очистки; 7 – предохранительные клапаны; 8 – глушитель; 9 – обратные клапаны: 10 –
вакуум-насос; 11 – глушитель; 12 – аэроплитка; 13 – автоматический регулирующий клапан; 14 – воздуходувка;
15 – всасывающий лоток
В последние десятилетия широко применяются специализированные железнодорожные вагоны (рис.5.21), автотранспортные средства (рис. 3.7, г, 3.10, в, 5.22) и специализированные суда (рис. 5.23) для транспортировки цемента. Все эти транспортные средства имеют пневмосистемы. Некоторые из них снабжены устройствами для самозагрузки материала (рис. 5.24).
В связи с существенным увеличением зданий из монолитного железобетона, наряду с доставкой готовой бетонной смеси миксерами, все более актуальным становится применение передвижных складов цемента (рис.5.25).
а
б
Рис. 5.21. Вагоны-цистерны:
а – модели 15-1405-02: 1 – котел; 2 – лестница наружная; 3 – лестница внутренняя; 4 – крепление котла на раме; 5 – подножка составителя; 6 – платформа; 7 – воздушная коммуникация; 8 – устройство разгрузочное; 9 – люк лазовый; б – модели 15-854: 1 – рама; 2 – котел; 3 – люк лазозый; 4 – предохранительный клапан; 5 – лестница наружная с площадками; 6 – автотормоз. 7 – система разгрузки; 8 – тормоз стояночный; 9 – тележка; 10 – ударно-тяговые приборы
Рис. 5.22. Автоматериаловоз ТЦ-25:
1 – седельный тягач; 2 – цистерна; 3 – загрузочный люк; 4 – компрессор; 5 – электрооборудование; 6 – опорное устройство; 7 – разгрузочные рукава; 8 – пневмооборудование; 9 – боковая защита; 10 – аэрирующие устройство
Рис. 5.23. Судно-цементовоз: 1 – система погрузочных трубопроводов; 2 – система разгрузочных трубопроводов; 3 – аэроустройство; 4 – корпусная труба
Рис. 5.24. Устройство самозагружающегося автоматериаловоза:
1 – сопло; 2 – загрузочный шланг; 3, 13, 14 – пробковые краны; 4, 12 – обратные клапаны; 5 –
распределительная труба; 6 – воздуховод; 7 – сигнализатор уровня; 8 – фильтр первой ступени; 9 – цистерна; 10
- шланг; 11 – мановакууметр; 15 – аэролотки; 16 – влагомаслоотделитель; 17 – вакууметр; 18 – крышка;
19 – фильтр второй; 20 – инерционный фильтр; 21 – ротационный компрессор;
22 – разгрузочный клапан
![]() |
Рис.5.25. Передвижной склад цемента СБ-74А-1 (с электроприводом):
1 – цистерна; 2 – компрессорный агрегат; 3 – подкатная тележка
|
|
Двойное оплодотворение у цветковых растений: Оплодотворение - это процесс слияния мужской и женской половых клеток с образованием зиготы...
Таксономические единицы (категории) растений: Каждая система классификации состоит из определённых соподчиненных друг другу...
Типы сооружений для обработки осадков: Септиками называются сооружения, в которых одновременно происходят осветление сточной жидкости...
Автоматическое растормаживание колес: Тормозные устройства колес предназначены для уменьшения длины пробега и улучшения маневрирования ВС при...
© cyberpedia.su 2017-2024 - Не является автором материалов. Исключительное право сохранено за автором текста.
Если вы не хотите, чтобы данный материал был у нас на сайте, перейдите по ссылке: Нарушение авторских прав. Мы поможем в написании вашей работы!