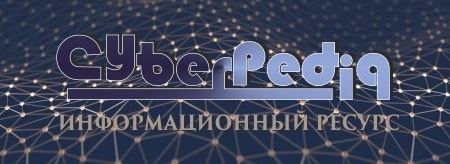
Особенности сооружения опор в сложных условиях: Сооружение ВЛ в районах с суровыми климатическими и тяжелыми геологическими условиями...
История развития хранилищ для нефти: Первые склады нефти появились в XVII веке. Они представляли собой землянные ямы-амбара глубиной 4…5 м...
Топ:
Техника безопасности при работе на пароконвектомате: К обслуживанию пароконвектомата допускаются лица, прошедшие технический минимум по эксплуатации оборудования...
Теоретическая значимость работы: Описание теоретической значимости (ценности) результатов исследования должно присутствовать во введении...
Комплексной системы оценки состояния охраны труда на производственном объекте (КСОТ-П): Цели и задачи Комплексной системы оценки состояния охраны труда и определению факторов рисков по охране труда...
Интересное:
Мероприятия для защиты от морозного пучения грунтов: Инженерная защита от морозного (криогенного) пучения грунтов необходима для легких малоэтажных зданий и других сооружений...
Распространение рака на другие отдаленные от желудка органы: Характерных симптомов рака желудка не существует. Выраженные симптомы появляются, когда опухоль...
Наиболее распространенные виды рака: Раковая опухоль — это самостоятельное новообразование, которое может возникнуть и от повышенного давления...
Дисциплины:
![]() |
![]() |
5.00
из
|
Заказать работу |
|
|
Наименование и характеристика дефекта | Основные причины образования дефекта | Основные мероприятия по исправлению дефекта |
Пониженная твёрдость серого чугуна после отжига для снятия внутренних напряжений | Распад цементита при нагреве выше 550—650 °С | Дефект исправим для деталей сравнительно простой конструкции путём нормализации с температуры 900-950 °С и последующим отпуском для снятия внутренних напряжений |
Высокая твёрдость после отжига отбелённого чугуна | Недостаточные температура или выдержка при отжиге | Повторный отжиг при температуре 850—870 °С с достаточной выдержкой |
Структурно свободный цементит в ковком чугуне | Низкая температура или недостаточная выдержка в 1-й стадии графитизации | Повторный отжиг по установленному графику |
Пластинчатый перлит в ферритном ковком чугуне, превышающий допускаемую по ТУ норму | Несоблюдение режима охлаждения или недостаточная выдержка при 2-й стадии графитизации | Повторный отжиг при температуре 730—710 °С |
Пластинчатый графит в ковком чугуне | Отжиг при температуре выше 1100 °С или наличие свободного графита в исходном чугуне | Дефект неисправим |
Дефекты закалки стали
Наименование и характеристика дефекта | Основные причины образования дефекта | Основные мероприятия по исправлению дефекта |
Закалочные трещины | Закалочные напряжения вследствие быстро протекающих с увеличением объёма структурных превращений | Предупреждение дефекта: 1. Для изделий из конструкционной углеродистой стали: а) изотермическая закалка в расплавленной селитре температурой 450— 500 °С; б) прерывистая закалка—охлаждение в воде до 300—200 °С, а затем в масле; в) закалка с самоотпуском— охлаждение в воде до 250—200 °С, затем выдержка на воздухе до саморазогрева поверхности до 600 °С с последующей замочкой в воде; г) непрерывная закалка до полного охлаждения в водном растворе 5—10%-ного NaCl или КОН температурой 50—60 °С; д) закалка в масло. 2. Для изделия из инструментальной углеродистой стали: а) прерывистая закалка — охлаждение в воде до 200 °С, затем перенос в масло или медленный отпуск; б) ступенчатая закалка в расплавленной селитре с температурой 180-200 °С и далее на возтолщиной или температурой 180 — 200 °С на воздухе (для инструментов диаметром до 8 мм). 3. Для инструментов из заменителей быстрорежущей стали (ЭИ-184, ЭИ-260 и т. д.) подстуживание до 1000—950 °С и ступенчатая закалка в расплавленной селитре температурой 450—550° С |
Недогрев. Недостаточная твёрдость изделий из углеродистой и легированной стали; повышенная твёрдость после закалки и пониженная после нормального отпуска изделий из быстрорежущей стали | Нагрев ниже нормальной температуры закалки стали | Исправление дефекта: нормализация или отжиг с последующей закалкой с нормальной температуры |
Перегрев. Крупноигольчатая структура и крупнокристаллический излом. Низкие пластические свойства | Нагрев выше нормальной температуры закалки | То же |
Пятнистая закалка. Налячие на поверхности деталей участков с пониженной твёрдостью (мягких мест) | 1. Неправильное погружение в закалочную среду. 2. Скопление пара в отдельных местах на поверхности изделий при закалке. 3. Малая скорость охлаждения в закалочной среде в интервале температур 650—500 °С. 4. Неоднородность исходной структуры в связи с первичной кристаллизацией. 5. Малая чувствительность стали к закалке 6. Местное обезуглероживание | Предупреждение дефекта: нормализация с последующей закалкой в 5— 10%-ном водном растворе NaCl или непосредственная закалка в том же растворе. Исправление дефекта: нормализация и закалка в 5—10 %-ном водном растворе NaCl |
Нафталиновый излом в быстрорежущей стали. Крупнозернистая структура. Крупнокристаллический излом с блёстками | Окончание ковки или прокатки при температуре выше 1100 °С или вторичная закалка без предварительного отжига | Предупреждение дефекта: окончание ковки или прокатки при температуре ниже 1100 °С; отжиг перед вторичной закалкой. Исправление дефекта: перековка на новый профиль |
Деформация (изменение размеров) | а) Термические напряжения, выэьмюшие пластическую деформацию; б) структурные превращения в интернале темпераратур 650—500 °С и ниже 300 °С, вызывающие пластическую деформацию | Предупреждение дефекта: а) понижение температуры закалки и уменьшение скорости охлаждения; б) применение природно мелкозернистой или специальной легированной стали; в) изотермическая или ступенчатая закалка |
Коробление (искривление длинных и тонких изделий) | а) Внутренние напряжения в изделии перед нагревом под закалку; б) неравномерный нагрев и охлаждение частей изделия; в) структурные превращения при температурах ниже 300 °C | Предупреждение дефекта: высокий отпуск (600—650 °С) перед закалкой и равномерный нагрев и охлаждение при закалке. Исправление дефекта: правка |
Окисление. Значительный слой окалины на поверхности закалённого изделия | Окислительная атмосфера в печи при нагреве под закалку | Предупреждение дефекта; а) нагрев в печах с восстановительной, нейтральной или защитной атмосферой: б) ускоренный нагрев изделий; в) нагрев в ящиках с сухим углем, отработанным карбюризатором или чугунной стружкой; г) нагрев в соляных или свинцовых ваннах |
Обезуглероживание (выгорание углерода в поверхностных слоях изделия) | То же | То же |
Эрозия (уменьшение размеров изделий или искажение профиля их вследствие уноса металла с поверхности) | Химическое действие хлористых солей и окисление металла при нагреве в соляных ваннах | Меры предупреждения: раскисление соляных ванн углём или ферросилицием |
Разъедание (точечное или ручьеобразное поражение поверхностм изделия) | При нагреве в соляных ваннах: а) повышенное содержание сернокислых солей; б) обогащение ванны кислородом из воздуха и окислами железа; в) химическое действие хлористых солей. При нагреве в свинцовых ваннах — образование окислов свинца. При нагреве в пламенных печах — неравномерное образование окалины. | Предупреждение дефекта: а) тщательный контроль состава солей для нагрева; б) раскисление соляных ванн углем, ферросилицием; в) засыпка на зеркало поверхности свинцовой ванны древесного угля или легкоплавких солей. |
Дефекты отпуска стали
|
|
|
Наименование и характеристика дефекта | Основные причины образования дефекта | Основные мероприятия по исправлению дефекта |
Недоотпуск. Повышенная твёрдость и пониженные пластические свойства изделий из углеродистой и легированной стали. Пониженная твёрдость инструмента из быстрорежущих сталей | Пониженная температура или недостаточная выдержка | Исправление дефекта: вторичный отпуск при нормальной температуре с достаточной выдержкой |
Переотпуск. Пониженная твёрдость и низкие пределы прочности и упругости | Отпуск при температуре выше нормальной | Исправление дефекта: отжиг, а затем закалка с последующим отпуском при нормальной температуре |
Хрупкий отпуск. Низкая ударная вязкость после отпуска: а) при температуре 250—350 °С — стали углеродистой, кремнистой, никелевой, кремненикелевой; б) при температуре 325—425 °С — стали марганцовистой и кремне-марганцовистой; в) при температуре 275—325 и 475-575 °С — стали хромистой и хромоникелевой | Обособление и коагуляция карбидов критической степени дисперсности и превращение остаточного аустенита | Исправление дефекта; отжиг, а затем закалка с последующим отпуском при температуре ниже или выше интервала температур хрупкого |
Отпускная хрупкость (чувствительность к скорости охлаждения при отпуске). Низкая ударная вязкость после отпуска при температуре 400—600 °С (обычно около 525 °С) с медленным охлаждением стали хромистой, хромоникелевой, марганцовистой и хромомарганцовистой (содержащих свыше 1% хрома или марганца) | Выпадение высокодисперсных карбидов, оксидов, фосфидов и нитридов по границам зёрен при медленном охлаждении с интервала температур отпускной хрупкости или при длительной выдержке при этих температурах | Предупреждение дефекта: а) охлаждение в воде или в масле после отпуска с последующим снятием внутренних напряжений при 300—350 °С; б) отпуск при температуре ниже 400 °С; в) применение стали, содержащей 0,3—0,5% Мо или Ti, Nb. Исправление дефекта: вторичный отпуск при температуре 400—600 °С с охлаждением в воде или масле с последующим снятием внутренних напряжений при 300—350 °С |
|
Дефекты цементации
Наименование и характеристика дефекта | Основные причины образования дефекта | Основные мероприятия по исправлению дефекта |
Точечные углубления на поверхности цементованных изделий | Наличие сернокислых солей (более 3-6%) в карбюризаторе | Предупреждение дефекта: не допускать в карбюризаторе наличия сернокислых солей более 3—6% |
Лишаеобразное разъедание поверхности цементованных изделий | Загрязнение карбюризатора серным колчеданом | Предупреждение дефекта: мероприятия малоэффективны (рекомендуется обжиг карбюризатора при температуре 900 °С в течение 10—30 час. или просев карбюризатора) |
Различная глубина цементированного слоя | Ссыпание солей в нижние зоны ящика вследствие непрочной связи их с частицами угля в карбюризаторе; неравномерный прогрев ящиков в печи | Предупреждение дефекта: применение крупнозернистого карбюризатора с частицами угля размером 5—7 мм и введение крепителя — патоки; равномерный нагрев ящиков |
Стекловидные наплывы, препятствующие цементации и приводящие к образованию мягких мест после закалки | Загрязнение карбюризатора песком | Предупреждение дефекта: просеивать карбюризатор с последующей добавкой углекислых солей до требуемой концентрации |
Слишком глубокая цементация | Повышенные температура и время выдержки при цементации. Применение сильного карбюризатора | Предупреждение дефекта: соблюдение установленной технологии цементации |
Повышенная концентрация углерода в цементированном слое (цементитная сетка) | То же | То же |
Пониженная концентрация углерода в цементованном слое | Низкая температура цементации. Применение слабого карбюризатора | Предупреждение дефекта: применение более сильного карбюризатора. Исправление дефекта: повторная цементация при нормальной температуре |
Недостаточная глубина цементированного слоя | То же | То же |
Поверхностное обезуглероживание цементированного слоя | Медленное охлаждение вместе с печью ящиков после цементации (особенно с крупнозернистым карбюризатором) | Предупреждение дефекта охлаждение ящиков после цементации на воздухе. Исправление дефекта: повторная кратковременная цементация при нормальной температуре |
Пятнистая цементация (мягкие пятна на поверхности закалённых цементированных изделий) | Загрязнение поверхности цементирууемых изделий; усадка карбюризатора в ящике и обнажение изделий; плохая укупорка ящика; абнормальность стали | Предупреждение дефекта: применение нормальной природной крупнозернистой стали и точное |
Отслаивание закалённого цементированного слоя (резкий переход от цементированного слоя к нецементированному) | Применение сильного карбюризатора | Предупреждение дефекта - цементация в слабом карбюризаторе. Исправление дефекта: нагрев в ящиках с углем до температуры 920—940 °С и выдержка при этой температуре 2—4 часа |
Остаточный аустенит. Пониженная твёрдость цементироованного слоя, в закалённой высоколегированной стали | Повышенное содержание углерода в цементованном слое; большая скорость охлаждения при закалке | Исправление дефекта: а) высокий отпуск при температуре 650—670 °С перед закалкой; б) закалка с нормальной температуры (760 °С) в масло с подстуживанием изделий до температуры 650—60О °С; в) закалка с температуры 860 °С в масло с высоким отпуском при температуре 6Б0—670 °С, затем закалка с температуры 760 °С и oтпуск при 200 °С; г) обработка холодом при температуре ниже 0 °С |
Повышенная твёрдость цементованного слоя после высокого отпуска | Недостаточные температура и выдержка при отпуске или нагрев выше Ас1 | Повторный отпуск при нормальной температуре и выдержке |
Дефекты азотации
|
Наименование и характеристика дефекта | Основные причины образования дефекта | Основные мероприятия по исправлению дефекта |
Коробление | Внутренние напряжения вследствие: а) быстрого охлаждения после отпуска предварительно закалённых изделий; б) механической обработки изделий | Предупреждение дефекта: а) охлаждение после отпуска со скоростью не более 2-3 °С в минуту; б) стабилизующий отпуск при температуре 520—540 °С в течение 3—5 час. после механической обработки. Исправление дефекта: правка |
Растрескивание (шелушение азотированного слоя изделий) | Внутренние напряжения вследствие резкого перехода от азотированного слоя к сердцевине | Предупреждение дефекта: медленное охлаждение после азотирования или азотирование с отпуском. Исправление дефекта: отпуск при 570—580 °С в течение 4—5 час. в печи с постоянной атмосферой аммиака |
Надутия на поверхности | Шлаковые включения, расположенные у поверхности азотированного изделия | Предупреждение дефекта: тщательный контроль стали на шлаковые включения |
Хрупкость (выкрашивание поверхности азотированного слоя) | Чрезмерное насыщение нитридами тонкого слоя поверхности вследствие крупнозернистости структуры и обезуглероживания поверхности при предварительной термообработке | Предупреждение дефекта: ступенчатый процесс азотирования. Исправление дефекта: отпуск в атмосфере аммиака при температуре 570—580 °С в течение 4—5 час. или при 630—650 °С в течение 2 час. |
Неравномерная (пятнистая) твёрдость (мягкие места на поверхности азотированного изделия) | Наличие отдельных участков, покрытых оловом, на азотируемой поверхности изделия | Предупреждение дефекта: фосфатирование перед азотированием и тщательная подготовка поверхности изделия |
Дефекты цианированного слоя
Наименование и характеристика дефекта | Основные причины образования дефекта | Основные мероприятия по исправлению дефекта |
Разъедание (поражения в виде точек или рельефа на поверхности изделия при жидком высокотемпературном цианировании) (830-850 °С) | Наличие сернокислых солей свыше 0,7—0,8% в нейтральных солях, применяемых для составления цианистой ванны; химическое действие нейтральных хлористых солей | Предупреждение дефекта: тщательный контроль нейтральных солей на содержание в них сернокислых |
Хрупкость (выкрашивание поверхностного слоя инструмента из быстрорежущей стали после низкотемпературного жидкого цианирования) | Чрезмерное насыщение нитридами тонкого слоя поверхности вследствие длительной выдержки или повышенной температуры при цианировании | Исправление дефекта: нагрев в селитровой ванне до температуры 550—560* С с выдержкой 30 мин. |
Остаточный аустенит (пониженная твёрдость цианированного слоя легированной стали после закалки | Высокая концентрация углерода и азота в цианированном слое; большая скорость охлаждения | Предупреждение дефекта: закалка в масло с подстуживанием до 650—600 °С. Исправление дефекта: обработка холодом при температурах ниже 0 °С |
|
|
Историки об Елизавете Петровне: Елизавета попала между двумя встречными культурными течениями, воспитывалась среди новых европейских веяний и преданий...
История развития хранилищ для нефти: Первые склады нефти появились в XVII веке. Они представляли собой землянные ямы-амбара глубиной 4…5 м...
Папиллярные узоры пальцев рук - маркер спортивных способностей: дерматоглифические признаки формируются на 3-5 месяце беременности, не изменяются в течение жизни...
История развития пистолетов-пулеметов: Предпосылкой для возникновения пистолетов-пулеметов послужила давняя тенденция тяготения винтовок...
© cyberpedia.su 2017-2024 - Не является автором материалов. Исключительное право сохранено за автором текста.
Если вы не хотите, чтобы данный материал был у нас на сайте, перейдите по ссылке: Нарушение авторских прав. Мы поможем в написании вашей работы!