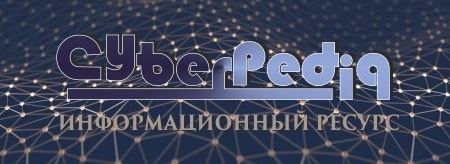
Типы сооружений для обработки осадков: Септиками называются сооружения, в которых одновременно происходят осветление сточной жидкости...
Семя – орган полового размножения и расселения растений: наружи у семян имеется плотный покров – кожура...
Топ:
Процедура выполнения команд. Рабочий цикл процессора: Функционирование процессора в основном состоит из повторяющихся рабочих циклов, каждый из которых соответствует...
Определение места расположения распределительного центра: Фирма реализует продукцию на рынках сбыта и имеет постоянных поставщиков в разных регионах. Увеличение объема продаж...
Интересное:
Берегоукрепление оползневых склонов: На прибрежных склонах основной причиной развития оползневых процессов является подмыв водами рек естественных склонов...
Мероприятия для защиты от морозного пучения грунтов: Инженерная защита от морозного (криогенного) пучения грунтов необходима для легких малоэтажных зданий и других сооружений...
Средства для ингаляционного наркоза: Наркоз наступает в результате вдыхания (ингаляции) средств, которое осуществляют или с помощью маски...
Дисциплины:
![]() |
![]() |
5.00
из
|
Заказать работу |
|
|
Современные станки для сквозной резьбы по металлу можно отнести к термическому и механическому методу резки.
1. Термическая резка металла
При работе между заготовкой и режущим инструментом нет непосредственного контакта.
1) Газовая (автогенная) резка металла
Это самый доступный, узнаваемый, «народный» способ резки металлов. Начало истории этой технологии следует искать во временах первых попыток использования для нагрева металла теплоты сгорания водорода, кислорода и особенно, ацетилена. Водород и кислород научились получать электролизом воды ещё в начале 19 века. Первый аппарат, способный выделять водород с последующим получением водородного пламени в горелке, предложил немецкий химик Д. Рихман в 1840 году. Этот аппарат мог сваривать и разрезать легкоплавкие металлы. Этот период считают началом газовой резке металла. Революцию произвело применение ацетилена, полученного в 1836 году из карбида кальция: теплота сгорания ацетилена в пять! раз превышала этот показатель для водорода. Но отсутствие экономичных технологий получения карбида кальция отложило триумф ацетилена на десятилетия. Лишь в 1892 году карбид научились получать электроплавкой, себестоимость его снизилась в сотни раз, начались новые исследования применения ацетилена для резки металла в промышленных масштабах. Смешивая в горелке кислород и ацетилен, научились достигать температуры плавления 4000 град. При этом окисления металла в зоне сварки и резки не происходило. Параллельно совершенствовалась конструкция горелки и способы хранения и транспортировки сжатого ацетилена в металлических баллонах.
Газокислородная резка металла ценятся за сравнительную простоту, дешевизну, возможность осуществлять необходимые работы в мобильных, полевых условиях. История знает немало примеров, когда эти достоинства оценивали взломщики банковских сейфов. Сейфовая броня бессильна перед мощью ацетилена, сгорающего вместе с железом в струе кислорода.
|
В 1906 году газовая резка впервые была применена в подводных условиях, газовая горелка зажигалась на поверхности, а под водой образующиеся продукты сгорания полностью изолировали зону реза от окружающей воды. В основу технологического процесса были заложены свойство металла нагреваться, плавиться и выгорать в чистом кислороде при высокой температуре (более 1000 °C).
Перед началом технологической операции необходимо разогреть место реза до такой температуры, при которой происходит воспламенение материала. Эта операция разогрева выполняется за счет пламени резака. В качестве разогревающего газа чаще всего эксплуатируют ацетилен. Время прогрева зависит от толщины, марки и состояния обрабатываемой металлической поверхности. Кислород на этом этапе не используется.
После прогрева к операции добавляется кислород. Струя пламени, равномерно перемещаясь вдоль линии реза, прорезает полуфабрикат на всю толщину. Кислород, используемый в процессе, не только режет, но и удаляет окислы, которые образуются на поверхности разрезаемого листового полуфабриката.
Важный критерий для получения качественного реза – выдерживание одинакового расстояния между резаком и разрезаемой поверхностью на протяжении всей операции. Этого сложно добиться, если резка металла выполняется ручным газокислородным резаком. При автоматизированном процессе (скоростная, газокислородная с повышенным качеством, резка кислородом высокого давления) скорость резания увеличивается, а качество реза возрастает (Рисунок 9).
Рисунок 9 – Резка ручным газокислородным резаком
Уникальность метода:
- возможность разрезать заготовки большой толщины;
|
- возможность резать титановые листы.
- дешевое оборудование
- Отдельные недостатки газокислородной резки:
- резке не поддаются цветные металлы типа алюминия, меди, а также высокоуглеродистые или хромоникелевые стали;
- большая ширина реза, невысокое качество, образование окислов, наплывов,
- невозможно работать с криволинейными поверхностями;
- изменение физических свойств в области реза [10].
2) Плазменная резка металла
Это одна из самых молодых технологий. Эта технология подразумевает использование в качестве оборудования плазмотрон, в котором роль режущего инструмента выполняет струя плазмы.
Раскаленный ионизированный газ (плазма) с высокой скоростью проходит через сопло плазматрона. Плазма нагревает, расплавляет металл, а затем сдувает расплав, тем самым образуя линию раздела заготовки.
В промышленном варианте появилась в середине 50-х годов 20-го столетия, как альтернатива механической резке при разделке заготовок из легированной стали и цветных металлов. Хотя физическое явление плазмы известно давно, возможность управлять процессами в плазме появилась только с развитием электротехнической элементной базы высокой мощности, ведь управлять приходится токами от 300 и более ампер. Сначала в качестве плазмообразующего газа использовался аргон, обеспечивающий более низкое напряжение зажигание дуги и износостойкость вольфрамовых электродов. Технология совершенствовалась, и вскоре были предложены плазмотроны, использующие более доступные технические газы: азот, кислород, сжатый воздух, а в качестве электродов более износостойкие вставки из циркония и, особенно, гафния. Рабочая газовая среда выбирается в зависимости от материала и толщины заготовки. Современные установки плазменной резки с ЧПУ имеют быстросменные плазмотроны (электроды плюс сопло) и бесступенчатые двигатели перемещения рабочих органов. Потребности самолётостроения и ракетостроения, атомной промышленности развили отдельный сегмент – микроплазменную резку малыми токами до 40 ампер. С помощью микроплазменной резки сваривают и раскраивают листовые материалы из драгоценных и тугоплавких металлов толщиной до 0.025 мм (Рисунок 10).
Рисунок 10 – Плазменная резка станком с ЧПУ
Уникальность метода:
- безопасность процесса;
- высокая скорость;
|
незначительный ограниченный нагрев разрезаемой поверхности.
Недостатки данной технологии:
- высокая цена оборудования;
- необходимость в обучении персонала;
- шум при работе плазменных установок;
- ограниченность значений толщин обрабатываемого металла [10].
3) Лазерная резка металла
Н начало лазерных технологий можно отнести к 1917 году и связать с именем Альберта Эйнштейна, впервые описавшего физику принудительного испускания и предположившего возможность создания генераторов-усилителей когерентного света. Позже лазерные пушки стали благодарным объектом фантазий писателей-фантастов, а вскоре реально работающие лазерные генераторы, способные лазерным пучком нагревать и изменять физическое состояние различных веществ, параллельно появились в разных странах.
Эта технология подразумевает резку и раскрой металла посредством сфокусированного лазерного луча, получаемого при помощи специального оборудования.
Луч лазера сосредотачивается в определенной точке разрезаемой детали. Под воздействием тепловой энергии лазерного луча поверхность прогревается, закипает и испаряется. Луч плавно передвигается вдоль границы реза, разделяя металлическую заготовку на части.
Лазерная резка применяется для разделения металлов с низкой теплопроводностью. Ее используют при резке, раскрое тонких листов (от 0,2 мм), цветных металлов (алюминия, меди), нержавеющей стали, трубных изделий (Рисунок 11).
Рисунок 11 – Лазерная резка станком с ЧПУ
Уникальность метода: обрабатываются практически все металлы, металлические сплавы, неметаллы.
Ряд недостатков технологии резки лазером:
- ограничение по толщине разделяемых изделий;
- большие энергетические затраты в ходе процесса;
- работу может выполнить только специально обученный персонал.
Современные технологии лазерной резки металлов реализованы в простейших ручных установках и оборудовании лазерной резки с ЧПУ. Так как различные заготовки имеют разную толщину и марку стали, необходимые технологические параметры реза подбираются мощностью и толщиной лазерного пучка. Лазерная резка наиболее оптимальна с точки зрения раскроя металла (листовая заготовка). Позиционирование перемещений и мощность излучения регулируются настолько точно, что позволяют за один рез получить две смежные поверхности разных деталей, не требующие финишных, слесарных операций. Максимальная толщина обрабатываемой стальной заготовки – до 30 мм. Уникальность лазерной резки ещё и в том, что заготовка не обязательно должна быть токопроводящей. Поэтому этой технологии подвластна обработка и любых неметаллических материалов, особенно это важно для резки чрезвычайно хрупких материалов. Лазерное оборудование резки металлов одно из самых дорогостоящих, поэтому оправдывает себя только при полной загрузке [2].
|
4) Ультразвуковая резка металла
Принцип ультразвуковой резки полностью отличается от традиционных технологий резки материалов. В первом случае используется энергия ультразвука, не требующая заточки режущих граней инструмента и приложения больших усилий.
В отличие от механической резки, при ультразвуковой резке нет ни стружки, ни шума, нет сожженных краев, как при лазерной или другой термической обработке, нет выделяющегося дыма или газов. По сравнению с водоструйной резкой, нет проникновения влаги в материал. Однако, с точки зрения стоимости резки, ультразвуковой метод является альтернативой лазерной и гидроабразивной резке.
Режущий наконечник совершает ультразвуковые вибрации, при которых очень малы силы трения, а разрезаемый материал не прилипает, что является особенно важным для вязких и эластичных материалов.
Ультразвуковые волны не слышны для человека. Ультразвуковой режущий нож вибрирует с амплитудой 10 - 70 мкм в продольном направлении. Вибрация является микроскопической, поэтому она не может быть видна. Движение повторяется 20000 - 40000 раз в секунду (частота 20 - 40 кГц).
Ультразвуковые устройства с более низкой частотой имеют больший вес и более высокую выходную мощность. Высокие значения амплитуды могут быть достигнуты также при более низких частотах. Машины с частотой 20 кГц более подходят для резки толстых и прочных материалов.
Недостатком таких устройств является то, что частота ультразвука близка к слышимому диапазону и, возможно, потребуются меры для снижения шума при работе.
Устройства для ультразвуковой резки состоят из ультразвукового преобразователя, наконечника-концентратора, ножа и блока питания. Ультразвуковой преобразователь служит для превращения электрической энергии в механическую (ультразвуковую).
Устройства с 35 кГц больше подходят для более тонких материалов, таких, как фольга, искусственная кожа и текстиль, а также для обработки деталей сложной формы. При этом машины бесшумны в работе (Рисунок 12).
|
Рисунок 12 – Ультразвуковая резка станком с ЧПУ
Среди преимуществ ультразвуковой технологии резки, выделяют следующие:
- Производительность процесса обработки возрастает в несколько раз.
- Износ применяемого инструмента для ультразвукового метода обработки сокращается в 8-10 раз по сравнению с обычными способами механической обработки.
- При сверлении увеличиваются параметры обработки по глубине и диаметру.
- Повышается точность механического воздействия.
Однако, широкому применению данного метода пока препятствует и ряд недостатков. В основном они связаны с технологической сложностью организации процесса.
- Ультразвуковая обработка деталей требует обеспечения дополнительных операций, среди которых доставка абразивного материала к рабочей зоне и подключение оборудования для водяного охлаждения. Эти факторы могут повышать и стоимость работ.
- При обслуживании промышленных процессов возрастают и энергетические затраты.
- Дополнительные ресурсы требуются не только на обеспечение функции основных агрегатов, но также и на функционирование систем предохранения и токосъемников, передающих электрические сигналы [24].
2. Механическая резка металла
1) Фрезерная резка металла
Фреза – это инструмент в виде зубчатого колеса со множеством лезвий, который при помощи фрезерного станка вращается с большой скоростью, что позволяет снимать слои металла в нужных местах. Долгие годы фрезерные станки работали только в ручном режиме, поэтому процент брака при фрезеровке был довольно высок.
Фрезеровка ЧПУ начала применяться не так давно, ее прообразом можно считать используемую на обычных механических станках систему рычагов, которые соединяли шпиндель станка с шаблонной деталью.
И только несколько лет спустя, управление фрезерным станком было поручено компьютеру, а для взаимодействия фрезеровщика-оператора со станком стали писать специальные программы
С развитием программирования и технологии появилось новое поколение фрезерных станков – с числовым программным управлением, применение которых намного облегчило работу фрезеровщиков и упростило ее.
В рамках нашей работы, мы рассматриваем данную технологию с позиции сквозной резки металла. Обработка листового материала этим способом позволяет получить предметы большей точности, снизить количество брака, увеличить производительность, а также выпускать серийные детали со сложной геометрией поверхности в большом количестве (Рисунок 13).
Рисунок 13 – Станок для фрезерной резки с ЧПУ
Недостатки данной технологии:
- Данная технология, безусловно, имеет много преимуществ. Однако, есть и свои негативные моменты. Они должны учитываться при выборе подобных методов. Технологи должны внимательно рассмотреть подобные отрицательные стороны.
- Многочисленные мелкие отходы должны удаляться с рабочей поверхности агрегата.
- При обработке крупногабаритных материалов должна быть продумана их загрузка и выгрузка с рабочего стола.
- Необходимо чётко отрегулировать величину зазоров между соседними заготовками перед началом кроя.
- При смене профилей и изменения размера заготовок необходимо проводить калибровку подкладочного листа.
- Если работа ведётся с двухсторонним облицовочным материалом, то должны применяться интегральные фрезы, а так же снижена скорость поступления материала.
- При использовании данной технологии может наблюдаться недостаточное качество обработки по кромкам. Может увеличиться количество сколов и повреждений материала.
- Не каждый фрезер с ЧПУ позволяет обрабатывать заготовку с обратной стороны без применения переустановки. Некоторое оборудование не имеет горизонтального сверления. Может не иметься опции пакетной обработки.
Уникальность метода:
- Экономится много времени. Изготовить мебельный набор, на который уходит 6 листов материала можно за один час.
- Экономятся производственные площади. Агрегаты, способные работать по технологии Нестинга, не займут много места.
- Исключается человеческий фактор. Процесс производства практически полностью автоматизирован.
- Высокие показатели производительности. Для криволинейных деталей не требуется предварительный крой на прямоугольные части. Экономия материала при этом доходит до 20%.
- Скорость обработки. Она достигается использованием компьютерных программ [15].
2) Гидроабразивная резка металла
Пожалуй, самая молодая технология. Гидроабразивная резка – это технология обработки материала, где режущим элементом является струя воды с абразивом, которая подается под высоким давлением. Способ используют для раскроя деталей из: нержавеющих, низколегированных и углеродистых сталей; цветных металлов; титана; резины; пластика и других материалов. Использование методики позволяет выполнять заготовки с точным соблюдением указанных размеров. Оборудование дает возможность с высокой скоростью осуществлять раскрой заготовок. В процессе обработки между элементами остается минимальное расстояние. Благодаря этому сокращается расход сырья. Гениально-простая мысль – разрезать материалы силой напора (до 50 бар) воды принадлежит российским учёным. Способ был запатентован в 1947 году. На тот момент технология позволяла разрезать только мягкие материалы. Лишь в 1980 году в воду стали добавлять гранитный абразив, сила реза увеличилась многократно, стало возможным разрезать струёй воды металл, стекло и бетон. Этот деликатный, высокоэкологичный и безопасный способ резки особенно востребован в инновационных космической и атомной промышленности, где часто применяются конструкционные материалы высокой твёрдости. Толщина разрезаемой заготовки – до 30 см.
Иногда гидроабразивное оборудование называют «гидрорезка», «водоструйная резка», «водорезка», «ГАР» или «waterjet». В промышленности такие станки используются с 1982 года, а их прототипы, появились еще в 1970 году.
В чем же суть процесса гидроабразивной резки? Если обычную воду сжать под давлением около 4000 атмосфер, а затем пропустить через отверстие диаметром меньше 1 мм, то она потечет со скоростью, превышающей скорость звука в 3-4 раза. Будучи направленной на обрабатываемое изделие, такая струя воды становится режущим инструментом. С добавлением частиц абразива ее режущая способность возрастает в сотни раз, и она способна разрезать почти любой материал (Рисунок 14).
Рисунок 14 – Гидроабразивная резка станком с ЧПУ
Уникальность данного метода заключается в следующем:
- с помощью такой резки можно раскроить практически любые виды материалов;
- данный метод является альтернативой не только механической, но и лазерной, плазменной, а также ультразвуковой резке, и в некоторых случаях является единственно возможной;
- более высокое качество реза из-за минимального термического влияния на заготовку (без плавления, оплавления или пригорания кромок);
- возможность резки термочувствительных материалов (ряда пожаро- и взрывоопасных, ламинированных, композитных и др.);
- экологическая чистота процесса, полное отсутствие вредных газовых выделений;
- взрыво- и пожаробезопасность процесса.
Недостатки данной технологии:
- существенно меньшая скорость разрезания стали малой толщины по сравнению с плазменной и лазерной резкой;
- высокая стоимость оборудования и высокие эксплуатационные затраты (характерно и для лазерной резки), обусловленные расходом абразива, электроэнергии, воды, заменами смесительных трубок, водяных сопел и уплотнителей, выдерживающих высокое давление, а также издержками по утилизации отходов;
- повышенный шум из-за истечения струи со сверхзвуковой скоростью (характерно и для плазменной резки) [10].
Выводы по первому разделу
В первом разделе мы изучили вопросы исторического возникновения и этапов развития сквозной резьбы по металлу. Отметили, что резьба является одним из древнейших и наиболее распространенных видов декоративного искусства, уникальным и простым способом художественной обработки дерева, камня, кости и других материалов путем вырезания. Из всего многообразия видов резьбы нас интересовала художественная сквозная резьба по металлу.
Процесс резьбы и сверления развивался не одну тысячу лет. Большой вклад в развитие резьбы и сверлильного дела внесли египетские и римские мастера. Сверлить камень научились уже в Древнем Египте. С развитием торговых связей и обменом опытом, сверлильные инструменты появились и в других странах, например, в Древней Руси.
Большое внимание в первом разделе мы уделили анализу и описанию современных тенденций развития технологии прорезного металла. Мы пришли к выводу, что все современные станки для сквозной резьбы по металлу можно отнести к термическому и механическому методу резки. К термической резке металла относят такие виды, как газовая (автогенная) резка металла, плазменная резка металла, лазерная резка металла, ультразвуковая резка металла.
Механическая резка металла включает в себя фрезерную резку металла, гидроабразивную резку металла.
Таким образом, все описанные нами современные тенденции развития технологии прорезного металла в настоящее время являются востребованными и актуальными.
Во втором разделе изучен поисково-технологический процесс изготовления сквозной резьбы по металлу; рассмотрены аналогичные технологии работы с металлом и описано оборудование, используемое для резки металла. Данный материал является базовым для решения задачи изучения основы сквозной резьбы по металлу и в дальнейшем описанию технологии исполнения на станках с числовым программным управлением.
|
|
Индивидуальные и групповые автопоилки: для животных. Схемы и конструкции...
Кормораздатчик мобильный электрифицированный: схема и процесс работы устройства...
Архитектура электронного правительства: Единая архитектура – это методологический подход при создании системы управления государства, который строится...
Опора деревянной одностоечной и способы укрепление угловых опор: Опоры ВЛ - конструкции, предназначенные для поддерживания проводов на необходимой высоте над землей, водой...
© cyberpedia.su 2017-2024 - Не является автором материалов. Исключительное право сохранено за автором текста.
Если вы не хотите, чтобы данный материал был у нас на сайте, перейдите по ссылке: Нарушение авторских прав. Мы поможем в написании вашей работы!