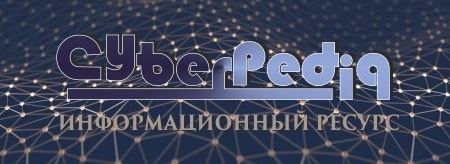
Автоматическое растормаживание колес: Тормозные устройства колес предназначены для уменьшения длины пробега и улучшения маневрирования ВС при...
История развития хранилищ для нефти: Первые склады нефти появились в XVII веке. Они представляли собой землянные ямы-амбара глубиной 4…5 м...
Топ:
Комплексной системы оценки состояния охраны труда на производственном объекте (КСОТ-П): Цели и задачи Комплексной системы оценки состояния охраны труда и определению факторов рисков по охране труда...
Эволюция кровеносной системы позвоночных животных: Биологическая эволюция – необратимый процесс исторического развития живой природы...
Характеристика АТП и сварочно-жестяницкого участка: Транспорт в настоящее время является одной из важнейших отраслей народного хозяйства...
Интересное:
Аура как энергетическое поле: многослойную ауру человека можно представить себе подобным...
Мероприятия для защиты от морозного пучения грунтов: Инженерная защита от морозного (криогенного) пучения грунтов необходима для легких малоэтажных зданий и других сооружений...
Влияние предпринимательской среды на эффективное функционирование предприятия: Предпринимательская среда – это совокупность внешних и внутренних факторов, оказывающих влияние на функционирование фирмы...
Дисциплины:
![]() |
![]() |
5.00
из
|
Заказать работу |
|
|
Теоретическая часть
Превращения ферритно-перлитной структуры при охлаждении рулонов
После охлаждения на отводящем рольганге полоса сматывается в рулон до 36 тонн, где охлаждается со скоростью ~10 град/ч в течение 2-3 суток. Если температура смотки рулона ниже критической точки , то при охлаждении горячекатаной стали в рулоне происходят процессы собирательной рекристаллизации феррита, сфероидизации цементитных пластин перлита, диффузионного выделения избыточных фаз.
Исследования показали, что собирательная рекристаллизация феррита развивается незначительно. Рост зерна феррита не превышает 0,25 балла.
Сферодизация цементитных пластин перлита происходит путем деления пластин на части с последующей коалесценцией больших «осколков» цементита (центров сфероидизации) за счет более мелких. Из опытных данных следует, что в зависимости от состава стали и скорости охлаждения рулонов превращение пластинчатого цементита в глобулярный может достигать более 50%. При остывании рулона до температуры ниже 550°С процессы сфероидизации цементита и роста зерна феррита практически полностью прекращаются.
Итак, если ферритно-перлитная структура образовалась до смотки, дальнейший рост зерна феррита при температуре смотки 680°С и ниже будет несущественным, так что размер и однородность зерна определяются только условиями горячей прокатки и охлаждения при g®a-превращении. Однако и скорость охлаждения в интервале g®a-превращения, и температура смотки в рулон сильно влияют на превращение пластинчатого перлита в сферический выше 500°С.
Степень сфероидизации перлита при охлаждении рулонов оказывает значительное влияние на пределы текучести и прочности. Они могут уменьшиться на 10-30 и 40-50 МПа соответственно.
|
Пример расчета
Пример расчета структурообразования в центральном участке по длине полосы сечением 3´1250 мм2 из стали Ст3сп приведен на рис. 2-4 [6]. Температура конца прокатки составляла 850°С, температура смотки в рулон 640°С, скорость выхода полосы из последней клети стана 11 м/с. Душирование полосы водой на отводящем рольганге начинали на расстоянии 39 м от последней клети.
Рис.2. Температурно-деформационный режим прокатки (а), изменение размера зерна (б) и кинетика рекристаллизации аустенита в чистовой группе клетей (в); Т – температура раската; h – толщина раската; e – относительное обжатие
Деформация полосы в клетях чистовой группы сопровождается снижением температуры металла, сокращением длительности междеформационных пауз, а также уменьшением величины относительного обжатия в отдельной клети (рис. 2, а). В этих условиях после деформации в первых четырех клетях (клети 6-9) первичная рекристаллизация аустенита успевает завершиться за время до входа полосы в следующую клеть, после деформации в клети 10 рекристаллизация проходит частично, а после деформации в клети 11 не получает развития (рис. 2, в). В результате накопленная суммарная деформация при выходе из клети 12 составляет 44%. Последующая рекристаллизация обуславливает сохранение к моменту начала распада переохлажденного аустенита остаточного наклепа, равного 14%. После измельчения зерна аустенита до ~25 мкм в первых двух циклах деформация – рекристаллизация его размер остается практически неизменным (рис. 2, б).
Рис. 3. Кинетика распада переохлажденного аустенита при охлаждении полосы на отводящем рольганге и в рулоне (скорость охлаждения полосы на воздухе 8,3°С/с, в рулоне 1,6°С/ч): а – температура полосы; б – объемная доля аустенита; в – объемная доля феррита; г – объемная доля перлита
Рис. 4. Кинетика сфероидизации пластинчатого перлита при охлаждении в рулоне:
|
а – температура; б – степень сфероидизации (е) перлита
Распад переохлажденного аустенита начинается при 770°С через 0,8 с от момента начала душирования полосы водой на отводящем рольганге стана (см. рис. 3). После завершения образования феррита при 680°С начинается перлитное превращение, которое заканчивается во время смотки полосы в рулон. В процессе охлаждения рулона массой 30 т от температуры смотки получает развитие сфероидизация цементитных пластин перлита (см. рис. 4).
Выбор скоростей прокатки
В современных непрерывных листовых станах горячей прокатки скорость прокатки в последней клети чистовой группы достигает 19 м/сек. Регулирование чисел оборотов двигателей рабочих клетей чистовой группы может производиться в широких пределах, что дает возможность выбирать скорость прокатки в соответствии с технологическими требованиями.
Скорости прокатки в чистовой группе клетей должны обеспечить максимальную производительность стана и максимальную температуру конца прокатки. Заправочные скорости в каждой клети выбирают по графику, который строится для каждой группы сталей.
При изменении химического состава прокатываемой стали, скорость прокатки устанавливают в зависимости от сопротивления деформации: чем больше сопротивление деформации металла, тем ниже скорость прокатки.
Выбор режима обжатия
Режим обжатий в чистовой группе определяет величины обжатия, скорости прокатки, давление и мощность прокатки во всех клетях группы.
Оптимальный режим обжатий в чистовой группе должен удовлетворять следующим требованиям:
1) производительность чистовой группы должна быть максимальной при прокатке полосы данного сорторазмера;
2) прокатываемый металл по размерам полосы, профилю поперечного сечения, металлографической структуре, прочностным свойствам и качеству поверхности должен удовлетворять требованиям ГОСТов и ТУ;
3) при прокатке полосы давление металла на валки не должно превышать допустимой величины с точки зрения прочности деталей рабочих клетей, а расходуемая мощность должна соответствовать возможностям становых двигателей по перегрузке и нагреву;
4) распределение обжатий и скорости прокатки по клетям должно быть таким, чтобы обеспечить простую настройку и перестройку чистовой группы в минимально короткое время.
|
Практическая часть
Расчетные данные
Таблица 3
Номер клети | 6 | 7 | 8 | 9 | 10 | 11 | 12 |
hi, мм | 25,5 | 15,3 | 10,7 | 7,7 | 5,8 | 4,64 | 4 |
D hi, мм | 24,5 | 10,2 | 4,6 | 3 | 1,9 | 1,16 | 0,64 |
e i | 0,49 | 0,4 | 0,3 | 0,334 0,28 | 0,376 0,25 | 0,348 0,2 | 0,395 0,137 |
Vi, м/с | 1,41 | 2,35 | 3,36 | 4,67 | 6,21 | 7,76 | 9 |
t i, с | 4,25 | 2,55 | 1,78 | 1,29 | 0,97 | 0,77 | 0,67 |
Тi, К | 1342,1 | 1313,7 | 1283,2 | 1243,6 | 1197,3 | 1150,5 | 1113 |
tн.р | 0,0014 | 0,0056 | 0,0354 | 0,039 | 0,012 | 0,159 | 0,004 |
tк.р | 0,49 | 0,973 | 2,409 | 2,63 | 1,55 | 5,706 | 2,035 |
Состояние | п | п | н | н | н | н | н |
Примечание: п – рекристаллизация проходит полностью;
н – рекристаллизация не завершена.
Теоретическая часть
Температурный режим горячей прокатки и его влияние на качество стали
Стали, предназначенные для изготовления листов, подвергаются горячей прокатке в области температур, где их микроструктура полностью состоит из аустенита. Во время охлаждения изделий после прокатки структура становится феррито-перлитной. При данных составах стали и скорости охлаждения существует корреляция между размером зерен аустенита и характерными размерами элементов структуры в феррито-перлитной смеси после фазового перехода. Если ограничиться лишь одной ее структурной составляющей – ферритом, то размер зерен феррита линейно зависит от величины исходных зерен аустенита. Таким образом, необходимо контролировать размер зерен аустенита. Конечной целью является уменьшение размера зерен феррита, что приведет к увеличению прочности и снижению критической температуры хрупкости. В настоящее время основным способом улучшения свойств сталей после горячей прокатки является нормализация. В то же время для достижения необходимых свойств сталей, которые поставляются потребителю непосредственно после прокатки без дополнительной термообработки, применяются сложные способы. Свойства таких сталей значительно лучше, чем свойства, которые можно получить в настоящее время с помощью нормализации. Такие способы обработки обычно называются контролируемой прокаткой.
Контролируемая прокатка представляет собой высокотемпературную обработку низколегированной и низкоуглеродистой стали и предполагает определенное сочетание основных параметров горячей деформации: температуры нагрева и конца прокатки; суммарной степени деформации и распределения деформации по температуре; скорости охлаждения и т. д. В температурном интервале прокатки с контролируемым режимом деформаций в металле можно отметить три стадии изменения структуры. На первой стадии (t>950°C) в процессе деформации происходит рекристаллизация; на второй стадии (t<950°C) металл упрочняется вследствие измельчения структуры и повышения плотности дислокаций. На третьей стадии (t<900°C) рекристаллизация не успевает полностью завершиться, что приводит к деформации нерекристаллизованных зерен аустенита и в итоге к еще большему измельчению структуры. При наличии в стали микролегирующих добавок ванадия, титана и особенно ниобия происходит дисперсионное твердение вследствие выделения избыточных фаз. Размер зерен феррита горячекатаной стали зависит от химического состава стали и совокупности технологических факторов: условий нагрева слябов под прокатку; температурного режима прокатки (особенно при последних проходах); степени и кратности обжатия; скорости охлаждения между проходами; температуры смотки полосы.
|
Особенности кинетики рекристаллизации в процессе изотермических выдержек после горячей деформации создают широкие возможности для управления величиной зерна и соответственно свойствами деформированного металла, т. е. можно разработать режимы последовательной деформации стали на непрерывных станах с регулируемым числом проходов и длительностью меж деформационных пауз. Последние выбирают так, чтобы конец паузы (начало деформации при очередном проходе) соответствовал завершению первичной рекристаллизации после предшествовавшего прохода. Такой режим деформации обеспечивает последовательное от прохода к проходу измельчение величины зерна и соответствующее улучшение механических свойств.
Известно, что при критических степенях обжатия наблюдается резкий рост размера зерен. Если при прокатке стали для глубокой штамповки температура конца прокатки ниже точки , то критические обжатия вызывают увеличение размеров зерен металла, что приводит к ухудшению штампуемости. Наличие мелкозернистой структуры повышает предел текучести и снижает удлинение металла; в противоположность этому при крупном зерне на поверхности штамповок образуется чешуйчатая структура так называемая апельсиновая корка. Для получения равномерного и равноосного зерна и мелкодисперсного цементита относительное обжатие в последних клетях чистовой группы должно быть не менее 10%, температура конца прокатки выше критической точки
, а температура смотки полосы в рулоны ниже 680°С.
|
Особенно жесткие требования предъявляются к температурным режимам конца прокатки и смотки полосы из раскисленных алюминием нестареющих сталей для глубокой вытяжки. В этих сталях оптимальная конечная структура достигается при температурах конца прокатки 840¸880°С, т. е. выше , быстром охлаждении металла и смотке его в рулон при 540¸620°С.
Для стареющих сталей оптимальная температура конца прокатки 840¸900°С, температура смотки полосы в рулон 600¸650°С.
Для регулирования температуры полосы, при смотке в рулоны на центральном рольганге непрерывных и полунепрерывных станов, между станом и моталками установлены душирующие устройства, которые подают воду через распылительные сопла на верхнюю и нижнюю поверхности выходящей из стана полосы. Душирующий рольганг располагается за последней клетью приблизительно на расстоянии 15-20 м. Требуемая температура полосы перед смоткой обеспечивается соответствующим количеством подаваемой воды.
|
|
Организация стока поверхностных вод: Наибольшее количество влаги на земном шаре испаряется с поверхности морей и океанов (88‰)...
Типы оградительных сооружений в морском порту: По расположению оградительных сооружений в плане различают волноломы, обе оконечности...
Историки об Елизавете Петровне: Елизавета попала между двумя встречными культурными течениями, воспитывалась среди новых европейских веяний и преданий...
Таксономические единицы (категории) растений: Каждая система классификации состоит из определённых соподчиненных друг другу...
© cyberpedia.su 2017-2024 - Не является автором материалов. Исключительное право сохранено за автором текста.
Если вы не хотите, чтобы данный материал был у нас на сайте, перейдите по ссылке: Нарушение авторских прав. Мы поможем в написании вашей работы!