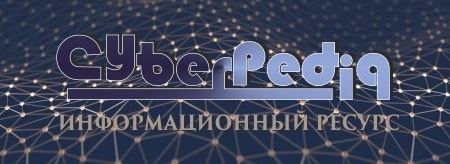
Архитектура электронного правительства: Единая архитектура – это методологический подход при создании системы управления государства, который строится...
Папиллярные узоры пальцев рук - маркер спортивных способностей: дерматоглифические признаки формируются на 3-5 месяце беременности, не изменяются в течение жизни...
Топ:
Марксистская теория происхождения государства: По мнению Маркса и Энгельса, в основе развития общества, происходящих в нем изменений лежит...
Характеристика АТП и сварочно-жестяницкого участка: Транспорт в настоящее время является одной из важнейших отраслей народного хозяйства...
Теоретическая значимость работы: Описание теоретической значимости (ценности) результатов исследования должно присутствовать во введении...
Интересное:
Влияние предпринимательской среды на эффективное функционирование предприятия: Предпринимательская среда – это совокупность внешних и внутренних факторов, оказывающих влияние на функционирование фирмы...
Инженерная защита территорий, зданий и сооружений от опасных геологических процессов: Изучение оползневых явлений, оценка устойчивости склонов и проектирование противооползневых сооружений — актуальнейшие задачи, стоящие перед отечественными...
Лечение прогрессирующих форм рака: Одним из наиболее важных достижений экспериментальной химиотерапии опухолей, начатой в 60-х и реализованной в 70-х годах, является...
Дисциплины:
![]() |
![]() |
5.00
из
|
Заказать работу |
|
|
a) Точение.
1. Для обработки поверхности воспользуемся проходным отогнутым резцом. Материал режущей части Р18. Так как резцом необходимо обработать ст. 3, с пределом прочности при растяжении sв.р. = 42кг/мм² [5, с34, т7]. То значение углов геометрии токарного резца будут следующие:
a = 12°; j1 = 5 - 10°
g = 25° j = 45°
Н ´ В = 25 ´ 16 [5, с103, т.34]
2. Исходя из общего припуска и характера выполняемого перехода (чистового) определяем глубину резания, мм:
t = (D – d)/ 2
D – диаметр обрабатываемой поверхности в мм;
d – диаметр обработанной поверхности в мм;
t = (40 - 38) / 2 = 1мм;
3. Выбираем табличное значение подачи S.
S = 0,4 мм/об;
4. Исходя из оптимального времени работы инструмента без переточки, выбираем стойкость инструмента Т = 60 мин [5, с96, т32] и определяем допустимую для этой стойкости скорость резания, м/мин:
V = (Сv * Кv) / (Тm * tхv * SYv),
где Сv, m, xv, Yv, постоянная и показатели степени, соответственно: 56; 0,20; 0,15; 0,20; [10, с430 т22]
Кv - поправочный коэффициент,
Кv = Кmv * Кnv * Кuv * Кjv * Кj'v * Кrv * Кqv * Кov
Кmv - качество обрабатываемого материала, 1,36
Кnv – состояние поверхности заготовки, 0,9
Кuv – материал режущей части, 1
Кjv – коэффициент главного угла в плане, 1
Кj'v – коэффициент вспомогательного угла в плане, 0,94
Кrv – коэффициент радиуса при вершине, 1
Кqv – коэффициент поперечного сечения державки, 0,97
Кov – вид обработки, 1
Кmv = 0,6(75 / sв.р.)1,25 = 0,6 * (75/ 42) 1,25 = 1,23
Кv = 1,23 * 0,9 * 1 * 1 * 0,94 * 1 * 0,97 * 1 = 1,016
V = (56 * 1,016) / (600,20 * 10,15 * 0,40,20) = 30,13 м/мин.
5. Рассчитываем частоту вращения шпинделя по допустимой скорости резания, об/мин:
n = (1000V) / (DП)
V – скорость резания, 30,13 м/мин;
D – диаметр обрабатываемой поверхности, 40мм;
n = (1000 * 30,13) / (40 * 3,14) = 239,88 об/мин;
6. Полученную расчетную частоту вращения корректируем по паспортным данным станка и рассчитываем действительную скорость резания Vд (об/мин):
|
Vд = (p * D * nд) /1000
nд – действительная частота вращения шпинделя (скорректированная по паспорту), 200 об/мин.
Vд = (3,14 * 40 * 200) / 1000 = 25,12 об/мин;
7. Определяем требуемую мощность станка (кВт):
N = (Pz * V) (60 * 102h)
Pz – тангенциальная составляющая силы резания, кгс
Pz = Ср * tхр * Syp * Vnp* Кp
t – глубина резания, 1мм;
Ср – постоянная для данных условий резания, 300;
xp, yp, np – показатели степени составляющих силы резания, соответственно: 1; 0, 75; -0,15; [10, т24]
Кp – поправочный коэффициент:
Кp = Кmp * Кjp* Кgp * Кlр * Кгp
Кmp – учитывает обрабатываемый материал;
Кmp = (sв.р. / 75) np0.35 = (42 / 75)-0.15 0.35 = 1,030
Кjp, Кgp, Кlр, Кгp – учитывают влияние геометрических параметров резца на составляющие силы резания, соответственно: 1; 1; 1; 1,04;
Кp = 1,030 * 1 * 1* 1 * 1,04 = 1,072
V – скорость резания, 30,13 м/мин;
h - к.п.д. передач станка, 0,75;
Pz = 300 * 11 * 0,40,75 * 30,13-0,15 * 1,07 = 96,87 кгс
N = (96,87 * 30,13) / (60 * 102 * 0,75) = 0,635 кВт
8. Определяем усилие подачи:
Pх = Ср * tхр * Syp * Vnp * Кp
Ср = 339; хp = 1; yp = 0,5; np = -0,4, [10, т24];
Кp = Кmp * Кjp* Кgp * Кlр * Кгp
Кmp = (sв.р. / 75) np0.35 = (42 / 75)-0.4 0.35 = 1,08
Кjp = 1;
Кgp = 1;
Кlр = 0,85;
Кгp = 1;
Кp = 1,08 * 1 * 1* 0,85 * 1= 0,92
Pх = 339 * 11 * 0,40,5 * 30,13-0,4 * 0,92 = 50,51 кгс
Определяем радиальную составляющую силы резания:
Pу = Ср * tхр * Syp * Vnp * Кp
Ср = 243; хp = 0,9; yp = 0,6; np = -0,13, [10, т24];
Кp = Кmp * Кjp* Кgp * Кlр * Кгp
Кmp = (sв.р. / 75) np0.35 = (42 / 75)-0.13 0.35 = 1,026
Кjp = 1;
Кgp = 1;
Кlр = 1,25;
Кгp = 1,14
Кp = 1,026 * 1 * 1 * 1,25 * 1,14 = 1,46
Pу = 243 * 10,9 * 0,40,6 * 30,13-0,13 * 1,46 = 71,28 кгс
Pz: Py: Px
96,87: 71,28: 50,51
9. Определяем основное время (мин):
То = (L * i) / (n * S)
L – длина прохода, 40мм [3, с44, т.47]
i – количество проходов, 1
n – частота вращения шпинделя, 1250 об/мин;
S – подача, 0,4 мм/об;
То = (40 * 1) / (1250 * 0,4) = 0,08 мин;
10. Вспомогательное время определяем по справочнику – мин; [9, с275]
Продольное точение и растачивание – 0,42
Твсп = 4,5 мин.
б) Сверление.
1. Материал режущей части инструмента – Р18, [5, с.145], тип – сверло спиральное Æ 16. геометрия сверла:
a = 12°; = 4-6°;
a = 1,5 мм; l = 3мм; l1 = 1,5 мм;
2. Исходя, из диаметра просверливаемого отверстия и характера выполняемого перехода назначаем количество проходов – 1 и определяем глубину резания:
|
t = 0,5D
D – диаметр просверливаемого отверстия, 16мм;
t = 0,5 * 16 = 8
3. Выбираем максимальную допустимую подачу:
S = 0,1 мм/об [5, с.224, т.63]
Принятую подачу проверяем по осевой силе, допускаемой прочностью станка. Для этого определяем осевую силу:
Р0 = Ср * Dqp * Syp * Kр
Ср, qp, ур – постоянная и показатели степени, соответственно: 37,5; 1; 0,7; [10, т32];
Кp = Кmp – поправочный коэффициент, 0,92
Р0 = 37,5 * 161 * 0,10,7 * 0,92 = 178,92 кгс
Р0 < Р0 max.
178,92 < 300
4. Назначаем период стойкости сверла: Т = 25 мин, [5, с.97, т.32]
5. Определяем скорость резания:
V = [(Cv * Dqp) / (Tm * txv * SYv)] * Кv
Cv, qp, m, xv, Yv – постоянная и показатели степени, соответственно: 7; 0,4; 0,2; 0; 0,7; [10, т32];
Кv = Кmv * Кuv * Кlv – общий поправочный коэффициент.
Кmv – коэффициент на качество обрабатываемого материала,
Кmv = Cm * (75 / sв)nv = 0,6 * (75 / 75) 0,9 = 0,6
Кuv – коэффициент на инструментальный материал, 0,3;
Кlv - коэффициент, учитывающий глубину просверливаемого отверстия, 1;
Кv = 0,6 * 0,3 * 1 = 0,18
V = [(7 * 160,4 ) / (250,2 * 80 * 0,10,7)] * 0,18 = 19,79 м/мин
6. Рассчитываем частоту вращения шпинделя, соответствующую найденной скорости резания об/мин:
n = (1000 * V) / (p * D)
n = (1000 * 19,79) / 3,14 * 16 = 393,90 об/мин.
nд = 400 об/мин.
7. Определяем действительную скорость резания м/мин:
V = (p * D * nд) / 1000
V = (3,14 * 16 * 400) / 1000 = 20,096 м/мин.
8. Рассчитываем крутящий момент от сил сопротивления резанию при сверлении, кгс/м:
M = Cm * Dqm * SYm * Kр
Cm, qm, Ym – постоянная и показатели степени, соответственно: 0,0345; 2; 0,8; [10, т32];
Кp = Кmp – поправочный коэффициент, 0,92
M = 0,0345 * 162 * 0,10,8 * 0,92 = 1,28
9. Определяем мощность, затрачиваемую на резание:
Nрез = (M * nд) / 975
Nрез = (M * nд) / 975 = 0,52 кВт.
10. Проверяем достаточность мощности привода станка.
Nшп = Nэ * h
Nэ – мощность электродвигателя станка, 10 кВт
h - к.п.д. станка, 0,75
Nшп = 10 * 0,75 = 7,5 кВт.
11. Определяем основное и машинное время:
Tо = L / (nд * S)
L – общая длина прохода сверла, 40 мм
Tо = 40 / (400 * 0,4) = 0,25 мин
12. Определяем вспомогательное время, связанное с переходом:
Твсп = 1,8 мин.
|
|
Таксономические единицы (категории) растений: Каждая система классификации состоит из определённых соподчиненных друг другу...
Архитектура электронного правительства: Единая архитектура – это методологический подход при создании системы управления государства, который строится...
Историки об Елизавете Петровне: Елизавета попала между двумя встречными культурными течениями, воспитывалась среди новых европейских веяний и преданий...
История создания датчика движения: Первый прибор для обнаружения движения был изобретен немецким физиком Генрихом Герцем...
© cyberpedia.su 2017-2024 - Не является автором материалов. Исключительное право сохранено за автором текста.
Если вы не хотите, чтобы данный материал был у нас на сайте, перейдите по ссылке: Нарушение авторских прав. Мы поможем в написании вашей работы!