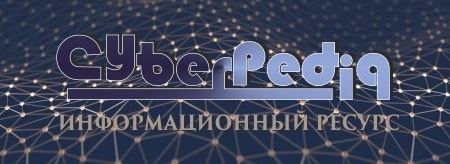
Эмиссия газов от очистных сооружений канализации: В последние годы внимание мирового сообщества сосредоточено на экологических проблемах...
Состав сооружений: решетки и песколовки: Решетки – это первое устройство в схеме очистных сооружений. Они представляют...
Топ:
Установка замедленного коксования: Чем выше температура и ниже давление, тем место разрыва углеродной цепи всё больше смещается к её концу и значительно возрастает...
Проблема типологии научных революций: Глобальные научные революции и типы научной рациональности...
Методика измерений сопротивления растеканию тока анодного заземления: Анодный заземлитель (анод) – проводник, погруженный в электролитическую среду (грунт, раствор электролита) и подключенный к положительному...
Интересное:
Искусственное повышение поверхности территории: Варианты искусственного повышения поверхности территории необходимо выбирать на основе анализа следующих характеристик защищаемой территории...
Отражение на счетах бухгалтерского учета процесса приобретения: Процесс заготовления представляет систему экономических событий, включающих приобретение организацией у поставщиков сырья...
Национальное богатство страны и его составляющие: для оценки элементов национального богатства используются...
Дисциплины:
![]() |
![]() |
5.00
из
|
Заказать работу |
|
|
Содержание пояснительной записки
I. Технологическая часть
1. Обоснование выбора заготовки. Расчет объема и массы заготовки и детали. Расчет потерь металла при обработке
2. Определение величин припусков на обработку
3. Выбор оборудования оснастки
4. Разработка технологического процесса
Нормативная часть
1. Определение режимов резания и норм времени
2. Расчет резцов на прочность и жесткость
3. Определение основного времени
4. Определение вспомогательного времени
5. Определение времени на обслуживание рабочего места. Отдых и естественные надобности
6. Определение норм штучного времени
7. Определение подготовительно-заключительного времени
Определение штучно-калькуляционного времени
Экономическая часть
1. Экономическая оценка технологического процесса
Содержание графической части
1. Технологическая карта механической обработки заготовки на формате А1.
2. Чертеж режущего инструмента на формате А4.
Технологическая часть
Обоснование выбора заготовки. Расчет объема и массы заготовки и детали. Расчет потерь металла при обработке
В зависимости от типа производства, конфигурации, размеров и материала детали определяем тип заготовки: прокат в виде прутков круглого сечения.
Материал детали – ст3 ГОСТ 535-79 сталь углеродистая обыкновенного качества 3 категории с гарантией механических свойств.
Прокат горячекатаный диаметром 40мм. [1, с131]
Правильность выбора заготовки оцениваем по величине коэффициента использования материала:
Км = Qд/Q,
Qд - чистая масса детали, кг;
Q – норма расхода материала на одну деталь, кг;
Q = Qз +Zобщ,
Qз – черновая масса заготовки, определяемая из теоретической массы одного погонного метра проката;
|
Zобщ – общие потери при обработке в % к длине прутка:
Zобщ = Zз + Zотр + Zнк,
Zз – потери на зажим;
Zотр – потери на отрезание;
Zнк – потери на некратность;
а) потери на зажим:
Zз = (Z'з / lпр) * 100%
Z'з – 60мм., исходя из экономической и технологической целесообразности процесса изготовления детали.
lпр = 3500мм – это длина прутка.
Zз = (60/3500)*100%= 1, 7%
б) потери на отрезание:
Zотр = (b/lдет)*100%
b – глубина отрезного резца, b = 0,1d, где d - диаметр прутка;
b = 0, 1* 40 = 4 мм
lдет – длина детали, мм с припуском lдет =38+1, 2=39,2мм табл.31с.30 [3]
Zотр = (4/39, 2) * 100% = 10, 2%
в) потери на некратность:
Zнк = (lост пр / lпр) * 100%
Считаем, какое количество деталей можно изготовить из прутка длинной 3,5м:
X = (lпр – Z'з) / (lдет + b)
X = (3500 – 60) / (39,2 + 4) = 79
Находим остаток длины прутка:
3440- 79 * (39,2 + 4) = 87,2мм
Zнк = (27, 2 / 3500) * 100 = 2, 49%
Итак, общие потери при обработке составляют:
Zобщ = 1, 7 + 10, 2 + 0, 7 = 14, 39%
Таким образом, норма расхода материала Q на одну деталь с учетом всех потерь будет:
Q = Qз + Zобщ
Масса 1 м стали – 9,86 кг, по табл.33,с130 [1]
9,86 кг – 1000 мм
Х кг - 39,2 мм
Х – (9,86 * 39,2) / 1000 = 0,386 кг
где Qзаг = 0,386 * 0,0392= 0,015 кг,
Zобщ = (0,015 / 100) * 14, 39 = 0,002
Q = 0,386 + 0,002 = 0,388 кг.
Расчитываем объем и массу заготовки и готовой детали.
Vз =(pd²*lдет)/4
Vз = [3,14 * (40мм)² * 39,2мм]/4 = 49235,2 мм3
Масса заготовки:
mз = Vз* p
где p = 7,8 – 7,85 г/см3
mзаг = [(49235,2 / 1000) * 7,8] /1000= 0,384кг.
Находим объем детали:
Vдет = (V1 + V2 + V3) - V4 - V5 - V6 – V7 – V8
V1 = (pd²*l)/4 = (3,14 * 30² * 20) / 4 = 14130 мм3
V2 = (pd²*l)/4 = (3,14 * 36² * 13) / 4 = 13225,68 мм3
V3= (pd²*l)/4 = (3,14 * 38² * 5) / 4 = 5667,7 мм3
V4 = (pd²*l)/4 = (3,14 * 16² * 38) / 4 = 7636,48 мм3
V5 = (pd²*l)/4 = (3,14 * 26² * 15) / 4 = 7959,9 мм3
V6 = (pd²*l)/4 = (3, 14 * 21² * 12) / 4 = 4154, 22 мм3
V7 = [(r² + r1² + rr1) * ph] / 3 = [(13² + 10, 5² + 13 * 10, 5) * (3, 14 * 2)] / 3 =870, 30 мм3
V8 = (pd²*l)/4 = (3, 14 *²)/ 4 = (3, 14 * 26² * 2) / 4 =1061, 32 мм3
Отсюда объем детали:
Vдет = (14130 + 13225,68 + 5667,7) – 7636,48 – 7959,9 – 4151,22 – 870,30 – 1061,32 = 11344,16 мм3
Масса детали:
m = p * Vдет
m = [(11344,16 / 1000) *7,8] / 1000 = 0,088 кг
Определяем коэффициент использования материала:
Kм = Qдет/Q
Kм = 0,088 / 0,388 = 0,22
|
Вывод: материал детали выбран правильно, так как коэффициент использования материала Kм = 0,22, что в пределах норм.
Определение величин припусков на обработку
Таблица1
№ операции | № перехода | Наименование операций и переходов | Припуск, мм | Размер d,мм | Допуск, мкм |
1 | Установить заготовку | - | d = 40; l = 60; | - | |
2 | Точить торец | 0,6 | d = 38 l = 40 | 160 | |
3 | Сверлить отверстие | - | d = 16 l = 38 | 130 | |
4 | Расточить отверстие | 0,5 | d = 21 l = 30 | 110 | |
5 | Выточить канавку | 1 | d = 26 l = 15 | 110 | |
6 | Расточить отверстие | 0,5 | d = 26 l = 2 1,75х45° | 110 | |
7 | Нарезать резьбу | 2 | M24X1.5-7H | +25 | |
8 | Точить наружную поверхность | 1,5 | d = 38 l = 43 | 160 | |
9 | Точить наружную поверхность | 1,5 | d = 36 l = 33 | 160 | |
10 | Точить наружную поверхность | 1,5 | d = 30 l = 20 | 160 | |
11 | Снять фаску | 1 | 30° | 110 | |
12 | Снять фаску | 1 | 3X45° | 110 | |
13 | Отрезать заготовку | 0,7 | l = 38 | 160 | |
14 | Снять и установить заготовку | - | - | ||
15 | Точить торец | 0,6 | d = 30 l = 30 | 160 |
Схема расположения полей припусков и допусков.
Максимальный диаметр вала dN = 40 мм;
Допуск на шлифование d1 = 0,013 мм;
Припуск на шлифование z1 = 0,1 мм;
d* = dN – z1 – d1
d* = 40 -0,1 – 0,013
d* = 39,88 мм
Определение основного времени
Основное время Т0 суммируется как основное время определенное для каждого отдельного перехода во всех операциях.
Т0 токарное – 4,25 мин.
Т0 сверлильное – 0,26 мин.
Общие основное время – 4,51 мин. [9, с275]
Определение времени на обслуживание рабочего времени, отдых на естественные надобности
Топер. = То + Твсп.
Топр. = 8,72 -* 4% = 0,348 мин.[9, с263]
Определение норм штучного времени
Норму штучного времени на операцию подсчитываем по формуле:
Тшт = То + Твсп + Тобсл. + Тп
То – 4,51 мин.
Твсп. – 8,72 мин.
Тобсл – 0,348 мин.
Тп – 0,348 мин.
Тшт = 4,51 + 8,72 + 0,348 + 0,348 = 13,92 мин.
Определение подготовительно-заключительного времени.
Всего: 28 мин.
Экономическая часть
Литература
1. Анурьев В.И. «Справочник конструктора- машиностроителя», Москва, 2001г.
2. Златоустов В.Д. «Технологические расчеты в курсовом проектировании по резанию металлов», Череповец, 1988г.
3. Комков А.А. «Справочные материалы к курсовому проекту по резанию материалов», Череповецкий государственный университет, 1998г.
4. Дальской А.М., Суслова А.Г. «Справочник технолога – машиностроителя», том 2, Москва 2001г.
|
5. Бергер И.И. «Справочник молодого токаря», Минск 1972г.
6. Орлова П.Н., Скороходова Е.А. «Краткий справочник металлиста», Москва, 1987г.
7. Нефедов Н.А. «Дипломное проектирование в машиностроительных техникумах», Москва, 1976г.
8. Косилова А.Г., Мещеряков Р.К., Калинин Р.К. «Точность обработки, заготовки и припуски в машиностроении», Москва, 1976г.
9. «Общемашиностроительные укрупненные нормативы времени на работы, выполняемые на металлорежущих станках», Москва, 1989г.
10. Под ред. А.Н. Малова Справочник технолога машиностроителя.
Содержание пояснительной записки
I. Технологическая часть
1. Обоснование выбора заготовки. Расчет объема и массы заготовки и детали. Расчет потерь металла при обработке
2. Определение величин припусков на обработку
3. Выбор оборудования оснастки
4. Разработка технологического процесса
Нормативная часть
1. Определение режимов резания и норм времени
2. Расчет резцов на прочность и жесткость
3. Определение основного времени
4. Определение вспомогательного времени
5. Определение времени на обслуживание рабочего места. Отдых и естественные надобности
6. Определение норм штучного времени
7. Определение подготовительно-заключительного времени
Определение штучно-калькуляционного времени
Экономическая часть
1. Экономическая оценка технологического процесса
Содержание графической части
1. Технологическая карта механической обработки заготовки на формате А1.
2. Чертеж режущего инструмента на формате А4.
Технологическая часть
Обоснование выбора заготовки. Расчет объема и массы заготовки и детали. Расчет потерь металла при обработке
В зависимости от типа производства, конфигурации, размеров и материала детали определяем тип заготовки: прокат в виде прутков круглого сечения.
Материал детали – ст3 ГОСТ 535-79 сталь углеродистая обыкновенного качества 3 категории с гарантией механических свойств.
Прокат горячекатаный диаметром 40мм. [1, с131]
Правильность выбора заготовки оцениваем по величине коэффициента использования материала:
Км = Qд/Q,
Qд - чистая масса детали, кг;
|
Q – норма расхода материала на одну деталь, кг;
Q = Qз +Zобщ,
Qз – черновая масса заготовки, определяемая из теоретической массы одного погонного метра проката;
Zобщ – общие потери при обработке в % к длине прутка:
Zобщ = Zз + Zотр + Zнк,
Zз – потери на зажим;
Zотр – потери на отрезание;
Zнк – потери на некратность;
а) потери на зажим:
Zз = (Z'з / lпр) * 100%
Z'з – 60мм., исходя из экономической и технологической целесообразности процесса изготовления детали.
lпр = 3500мм – это длина прутка.
Zз = (60/3500)*100%= 1, 7%
б) потери на отрезание:
Zотр = (b/lдет)*100%
b – глубина отрезного резца, b = 0,1d, где d - диаметр прутка;
b = 0, 1* 40 = 4 мм
lдет – длина детали, мм с припуском lдет =38+1, 2=39,2мм табл.31с.30 [3]
Zотр = (4/39, 2) * 100% = 10, 2%
в) потери на некратность:
Zнк = (lост пр / lпр) * 100%
Считаем, какое количество деталей можно изготовить из прутка длинной 3,5м:
X = (lпр – Z'з) / (lдет + b)
X = (3500 – 60) / (39,2 + 4) = 79
Находим остаток длины прутка:
3440- 79 * (39,2 + 4) = 87,2мм
Zнк = (27, 2 / 3500) * 100 = 2, 49%
Итак, общие потери при обработке составляют:
Zобщ = 1, 7 + 10, 2 + 0, 7 = 14, 39%
Таким образом, норма расхода материала Q на одну деталь с учетом всех потерь будет:
Q = Qз + Zобщ
Масса 1 м стали – 9,86 кг, по табл.33,с130 [1]
9,86 кг – 1000 мм
Х кг - 39,2 мм
Х – (9,86 * 39,2) / 1000 = 0,386 кг
где Qзаг = 0,386 * 0,0392= 0,015 кг,
Zобщ = (0,015 / 100) * 14, 39 = 0,002
Q = 0,386 + 0,002 = 0,388 кг.
Расчитываем объем и массу заготовки и готовой детали.
Vз =(pd²*lдет)/4
Vз = [3,14 * (40мм)² * 39,2мм]/4 = 49235,2 мм3
Масса заготовки:
mз = Vз* p
где p = 7,8 – 7,85 г/см3
mзаг = [(49235,2 / 1000) * 7,8] /1000= 0,384кг.
Находим объем детали:
Vдет = (V1 + V2 + V3) - V4 - V5 - V6 – V7 – V8
V1 = (pd²*l)/4 = (3,14 * 30² * 20) / 4 = 14130 мм3
V2 = (pd²*l)/4 = (3,14 * 36² * 13) / 4 = 13225,68 мм3
V3= (pd²*l)/4 = (3,14 * 38² * 5) / 4 = 5667,7 мм3
V4 = (pd²*l)/4 = (3,14 * 16² * 38) / 4 = 7636,48 мм3
V5 = (pd²*l)/4 = (3,14 * 26² * 15) / 4 = 7959,9 мм3
V6 = (pd²*l)/4 = (3, 14 * 21² * 12) / 4 = 4154, 22 мм3
V7 = [(r² + r1² + rr1) * ph] / 3 = [(13² + 10, 5² + 13 * 10, 5) * (3, 14 * 2)] / 3 =870, 30 мм3
V8 = (pd²*l)/4 = (3, 14 *²)/ 4 = (3, 14 * 26² * 2) / 4 =1061, 32 мм3
Отсюда объем детали:
Vдет = (14130 + 13225,68 + 5667,7) – 7636,48 – 7959,9 – 4151,22 – 870,30 – 1061,32 = 11344,16 мм3
Масса детали:
m = p * Vдет
m = [(11344,16 / 1000) *7,8] / 1000 = 0,088 кг
Определяем коэффициент использования материала:
Kм = Qдет/Q
Kм = 0,088 / 0,388 = 0,22
Вывод: материал детали выбран правильно, так как коэффициент использования материала Kм = 0,22, что в пределах норм.
|
|
Семя – орган полового размножения и расселения растений: наружи у семян имеется плотный покров – кожура...
Биохимия спиртового брожения: Основу технологии получения пива составляет спиртовое брожение, - при котором сахар превращается...
Архитектура электронного правительства: Единая архитектура – это методологический подход при создании системы управления государства, который строится...
История создания датчика движения: Первый прибор для обнаружения движения был изобретен немецким физиком Генрихом Герцем...
© cyberpedia.su 2017-2024 - Не является автором материалов. Исключительное право сохранено за автором текста.
Если вы не хотите, чтобы данный материал был у нас на сайте, перейдите по ссылке: Нарушение авторских прав. Мы поможем в написании вашей работы!