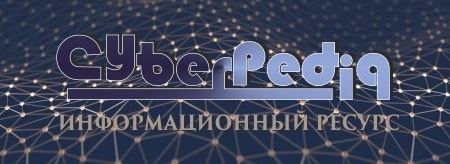
Состав сооружений: решетки и песколовки: Решетки – это первое устройство в схеме очистных сооружений. Они представляют...
История развития пистолетов-пулеметов: Предпосылкой для возникновения пистолетов-пулеметов послужила давняя тенденция тяготения винтовок...
Топ:
Установка замедленного коксования: Чем выше температура и ниже давление, тем место разрыва углеродной цепи всё больше смещается к её концу и значительно возрастает...
Особенности труда и отдыха в условиях низких температур: К работам при низких температурах на открытом воздухе и в не отапливаемых помещениях допускаются лица не моложе 18 лет, прошедшие...
Генеалогическое древо Султанов Османской империи: Османские правители, вначале, будучи еще бейлербеями Анатолии, женились на дочерях византийских императоров...
Интересное:
Лечение прогрессирующих форм рака: Одним из наиболее важных достижений экспериментальной химиотерапии опухолей, начатой в 60-х и реализованной в 70-х годах, является...
Искусственное повышение поверхности территории: Варианты искусственного повышения поверхности территории необходимо выбирать на основе анализа следующих характеристик защищаемой территории...
Инженерная защита территорий, зданий и сооружений от опасных геологических процессов: Изучение оползневых явлений, оценка устойчивости склонов и проектирование противооползневых сооружений — актуальнейшие задачи, стоящие перед отечественными...
Дисциплины:
![]() |
![]() |
5.00
из
|
Заказать работу |
|
|
Расчет и конструирование отдельных узлов и элементов станка подчиняются общей задаче, выраженной в техническом задании на вновь издаваемый станок. В нем определены характеристики и выходные параметры станка, которые должны быть обеспечены (см. табл. 1).
Несмотря на то что в станкостроении накоплен большой опыт по созданию разнообразных конструкций, положительно зарекомендовавших себя на практике, все время идет напряженная творческая работа как по разработке новых конструкций, так и по дальнейшему совершенствованию существующих. При этом основные решения принимают на стадии технического задания, технического предложения или эскизного проекта.
Новые решения позволяют либо создать конструкцию с более высокими технико-экономическими показателями (меньшие стоимость, массой, габаритные размеры, лучшая технологичность, удобство обслуживался), либо получить более высокие характеристики конструкции или дополнительные преимущества (большие надежность, точность, производительность, технологические возможности и др.) и обеспечить этим конкурентоспособность станка.
При разработке новых конструкций узлов может быть предложено несколько решений, каждое из которых имеет те или иные преимущества и недостатки. Генерирование вариантов (что особенно эффективно при применении методов автоматизированного проектирования с использованием ЭВМ) и выбор оптимального решения осуществляются на основе учета большого числа факторов, отражающих широкий диапазон требований к конструкции и специфику методов проектирования и расчета.
В табл. 1 приведены основные факторы, которые нужно учитывать при разработке новой конструкции любого узла, выполняющего заданные функции и формирующего характеристики и параметры всего станка.
|
В соответствии с этой таблицей рассмотрим те задачи, которые решают на каждом этапе проектирования данного узла или механизма станка исходя из заданных требований к станку в целом.
Табл. 1. Факторы, учитываемые при проектировании узла ставка
Фактор | Содержание | Этап |
1. Технические данные станка | Габаритные размеры, скорость и подача, мощность и др. | Выбирают характеристики, относящиеся к узлу |
2. Заданные характеристики и выходные параметры станка | Точность движения формообразующих узлов, производительность, надежность, КПД, технологические возможности | Оценивают долю участия узла в формировании характеристик станка |
3. Характеристики и выходные параметры узла | Габаритные размеры, точность, передаваемые нагрузки, скорость перемещения | Устанавливают значения основных характеристик узла, обеспечивающих требования к станку в целом |
4. Критерии работоспособности станка | Геометрическая точность, жесткость, вибростойкость, теплостойкость, износостойкость, прочность | Оценивают роль каждого критерия в обеспечении работоспособности узла |
5. Требования стандартов | Размеры, нормы точности, жесткости, уровень шума, стандартные и нормализованные детали и узлы | Проверяют требования стандартов, оценивают целесообразность принятия стандартных решений |
6. Технико-экономические показатели | Стоимость, технологичность, масса, удобство обслуживания | Эти данные используют как основные критерии при сравнении возможных вариантов конструкции |
7. Совершенство методов расчета | Эмпирические данные, аналитические расчеты, программы САПР | Оценивают возможность генерации различных решений и выбора оптимального варианта |
8. Характеристика существующих конструкций | Данные и характеристики лучших конструкций аналогичного назначения | Сравнение разрабатываемого варианта конструкции с существующими |
По установленным для всего станка техническим требованиям определяют те, которые относятся к разрабатываемому узлу и являются для него исходными характеристиками, которые должны быть обеспечены. В ряде случаев технические параметры станка выступают в качестве конструктивных и критериальных ограничений при выборе конструктивного варианта узла. Например, габаритные размеры и общая компоновка станка определяют наибольшие допустимые размеры узла, требуемая точность и соответствующие нагрузки, передаваемые механизмами, ограничивают их минимальные размеры из условия прочности и жесткости и др.
|
1. Значения технических характеристик (производительность, надежность, КПД, уровень шума, диапазон регулирования и др.) и выходные параметры по показателю точности, установленные для всего станка, являются исходными для формирования аналогичных требований к данному узлу. Это связано с оценкой той роли, которую играет данный узел в формировании показателя, относящегося к станку в целом. Для выходных параметров точности рассчитывают составляющие погрешности обработки и оценивают ту долю, которая приходится на данный узел.
2. Вышеуказанные расчеты позволяют установить численные характеристики узла с учетом конструктивных особенностей, габаритных размеров в расположения узла, передаваемых нагрузок, скоростей и других факторов. Если установленные характеристики узла будут обеспечены, то это должно давать гарантию обеспечения и требований к станку в целом. как правило, с некоторым запасом на неучтенные факторы и на возможность приближенных оценок по доли участия. данного узла в формировании характеристик станка.
. Далее рассчитывают отдельные элементы конструкции и узла в целом для выбора таких размеров, конструктивных форм и материалов, которые позволяют с наилучшими технико-экономическими показателями обеспечить заданные технические характеристики. Для этого в первую очередь оценивают влияние начальной геометрической точности, жесткости, виброустойчивости, стойкости к тепловым деформациям, на выходные параметры узла.
. При формировании конструкции узла должны быть учтены все требования стандартов и нормативно-технической документации (НТД), относящиеся к станку данного типа и класса точности. Однако это необходимые, но не всегда достаточные требования. На этом этапе также анализируют целесообразность установления дополнительных требований или ужесточения существующих нормативов для достижения поставленных целей с учетом требований заказчика (потребителя).
|
. Обеспечить требуемые параметры можно, применяя, как правило, различные конструктивные решения. Критерием для выбора оптимального варианта являются технико-экономические показатели и в первую очередь затраты на разработку и производство новой модели станка.
. Генерирование различных решений при проектировании данного узла с учетом конструктивных и критериальных ограничений наиболее эффективно осуществляется при автоматизированных расчетах, которые дают новые возможности производить большое число расчетов с широкой вариацией значений входных параметров. Важное значение при этом имеет совершенство расчетных методов и наличие банка данных, содержащего справочные данные, данные по аналогам, требования нормативно-технической документации, типовые решения и другие необходимые сведения.
. При окончательном выборе варианта и на всех стадиях разработки новой конструкции узла, начиная с формирования концепции его построения, сравнивают его с лучшими образцами существующих аналогичных конструкций. Создавать новый вариант узла имеет смысл лишь в том случае, если выявлены его существенные преимущества и высокая конкурентоспособность.
Стремление создать конкурентоспособную конструкцию, обладающую более совершенными характеристиками, заставляет разработчиков искать новые конструктивные решения, непрерывно повышать качество создаваемых изделий. [4]
Эргономика
Термин эргономика был принят в Великобритании в 1949 году, когда группа английских ученых положила начало организации Эргономического исследовательского общества. В СССР в 20-е годы предлагалось название эргология, в США раньше имелось собственное наименование - исследование человеческих факторов, а в ФРГ - антропотехника, но в настоящее время наибольшее распространение получил английский термин.
|
«Эргономика - научно-прикладная дисциплина, занимающаяся изучением и созданием эффективных систем, управляемых человеком. Эргономика изучает движение человека в процессе производственной деятельности, затраты его энергии, производительность и интенсивность при конкретных видах работ». [16]
Эргономические свойства человека - антропометрические, физиологические, психофизиологические и психологические - обусловливают эффективность его деятельности в системе «человек - машина - среда». Указанные свойства рассматриваются как комплекс (ГОСТ 16035-70).
Эргономические требования к металлорежущему станку - требования, определяемые эргономическими свойствами человека и устанавливаемые с целью оптимизации его деятельности (ГОСТ 16035-70).
Эргономический показатель качества металлорежущего станка - показатель качества (ГОСТ 15467-70), используемый для определения соответствия станка эргономическим требованиям; он включает весь комплекс эргономических показателей.
Орган управления - устройство, с помощью которого вводятся команды человеком в технические звенья системы.
Различают следующие действия человека с органами управления:
а) переключение;
б) установка;
в) управление;
г) передача энергии.
Мышечное усилие - усилие, развиваемое нервномышечным аппаратом человека, которое протекает по биохимическим законам. Различают статическое и динамическое мышечное усилие. Мышечное усилие подразделяется на: небольшое - слабоощутимое, неутомительное; среднее - может быть выдержано без перерыва не менее часа; большое - может быть выдержано без перерыва не более получаса.
Индикационное устройство - техническое устройство, преобразующее, сигнал таким образом, что он становится допустимым для органов чувств человека; входит как составная часть в более общее понятие средств отображения информации (СОИ).
Рабочая зона - совокупность точек рабочего пространства, в котором ведется обслуживание органов управления человеком из фиксированного положения.
Рабочее пространство - совокупность всех точек в пространстве, на которые может распространяться воздействие человека во время работы. Эти точки либо доступны из одного места, либо требуют перемещения работника.
Рабочее место - зона, где работник (или группа работников) выполняет определенную часть технологического процесса. [7]
2.2.1 Общие требования к рабочему месту
1. Основные элементы управления должны быть расположены в пределах радиуса действий рук (зон действия рук) или ног (пространство для размещения ножных органов управления).
2. Наиболее значимые органы управления и индикаторы должны размещаться в пределах пространства, которое определяет оптимальные размеры зон действия рук в соответствующем поле зрения.
|
. Размеры рабочего места выбираются в зависимости от размеров и особенностей структуры поля зрения, зон ручного действия и зон действия ног, которые, в свою очередь, определяются прямо или косвенно антропометрическими размерами.
. Поле зрения.
. Все размеры поля зрения в плане и боковой проекции приведены на рис. 4., где учтены необходимые для проектирования данные о свойствах поля зрения.
Зоны ручного действия
При расчете зон ручного действия за исходное положение станочника относительно станка принимается положение, которое обеспечивает свободное наблюдение за процессом резания. Рабочая поза «стоя» является основной. Поза в этом случае должна быть свободная; корпус станочника по оси плечевых точек расположен параллельно передней кромке стола (станины) станка.
В пространственной структуре моторного поля для ручных органов управления различают три зоны: оптимальная, нормальная и предельная зоны досягаемости и захвата.
Зона оптимального захвата складывается из соответствующих зон левой и правой руки. Границы этих зон описываются радиусами, имеющими центр вращения в локтевых суставах и равными по длине расстояниям от головок локтевых костей до третьих пястно-фаланговых суставов. Этот радиус принимается равным 340 мм. Радиус зоны оптимальной досягаемости равен 440 мм.
Рис. 4. Основные визуальные данные
Зона нормального захвата складывается из соответствующих зон левой и правой руки. Границы этих зон описываются радиусом, имеющим центр вращения в плечевых суставах и равным по длине расстоянию от головок плечевых костей до третьих пястно-фаланговых суставов при полностью выпрямленных в локтевых суставах руках, что составляет 600 мм. Радиус зоны досягаемости равен 720 мм.
Зона предельной досягаемости (захвата) очерчивается точками на конце указательного пальца (пястно-фаланговых суставов) при выпрямленных руках и максимально возможном повороте или наклоне туловища, что увеличивает зоны нормального захвата и досягаемости на 400 мм. [7]
Зоны действия ног
При управлении металлорежущими станками желательно исключить использование ножных органов управления, поскольку они применяются при основной рабочей позе «сидя». Конструкция станины не должна мешать свободному перемещению станочника вдоль фронтальной части станка.
Общие требования к системам управления
Размеры и компоновка стационарных пультов управления должны обеспечивать удобную позу рабочего, для чего:
углы наклона поверхностей пульта к вертикали должны быть:
Верхняя плоскости (выше стандартной линии наблюдения) - 10° (наклон на оператора);
Рис. 6.
|
|
Архитектура электронного правительства: Единая архитектура – это методологический подход при создании системы управления государства, который строится...
Состав сооружений: решетки и песколовки: Решетки – это первое устройство в схеме очистных сооружений. Они представляют...
Поперечные профили набережных и береговой полосы: На городских территориях берегоукрепление проектируют с учетом технических и экономических требований, но особое значение придают эстетическим...
Организация стока поверхностных вод: Наибольшее количество влаги на земном шаре испаряется с поверхности морей и океанов (88‰)...
© cyberpedia.su 2017-2024 - Не является автором материалов. Исключительное право сохранено за автором текста.
Если вы не хотите, чтобы данный материал был у нас на сайте, перейдите по ссылке: Нарушение авторских прав. Мы поможем в написании вашей работы!