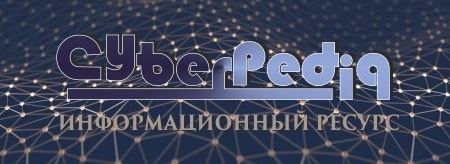
Поперечные профили набережных и береговой полосы: На городских территориях берегоукрепление проектируют с учетом технических и экономических требований, но особое значение придают эстетическим...
Архитектура электронного правительства: Единая архитектура – это методологический подход при создании системы управления государства, который строится...
Топ:
Отражение на счетах бухгалтерского учета процесса приобретения: Процесс заготовления представляет систему экономических событий, включающих приобретение организацией у поставщиков сырья...
Процедура выполнения команд. Рабочий цикл процессора: Функционирование процессора в основном состоит из повторяющихся рабочих циклов, каждый из которых соответствует...
Определение места расположения распределительного центра: Фирма реализует продукцию на рынках сбыта и имеет постоянных поставщиков в разных регионах. Увеличение объема продаж...
Интересное:
Подходы к решению темы фильма: Существует три основных типа исторического фильма, имеющих между собой много общего...
Инженерная защита территорий, зданий и сооружений от опасных геологических процессов: Изучение оползневых явлений, оценка устойчивости склонов и проектирование противооползневых сооружений — актуальнейшие задачи, стоящие перед отечественными...
Уполаживание и террасирование склонов: Если глубина оврага более 5 м необходимо устройство берм. Варианты использования оврагов для градостроительных целей...
Дисциплины:
![]() |
![]() |
5.00
из
|
Заказать работу |
|
|
ОБЩАЯ ХАРАКТЕРИСТИКА ВАЛОВ И ОСЕЙ
Назначение и классификация. Валы служат для поддержания вращающихся деталей и передачи вращающего момента от одной детали к другой (в осевом направлении) Их условно разделяют на: простые валы (валы) - работают в условиях кручения, изгиба и растяжения (сжатия), их применяют в передачах: зубчатых, ременных и др.; торсионные валы (торсионы) - работают лишь в условиях кручения и передают вращающий момент, соединяя обычно два вала на индивидуальных опорах; оси — поддерживающие валы, работающие лишь в условиях изгиба. В зависимости от распределения нагрузок вдоль оси вала и условий сборки прямые валы выполняют гладкимиилиступенчатыми, Гладкие валы более технологичны. Коленчатые валы используют в поршневых двигателях и компрессорах Для передачи вращающего момента между агрегатами со смещенными в пространстве осями применяют специальные гибкие валы. Такие валы обладают высокой жесткостью при кручении и малой жесткостью при изгибе. В зависимости от расположения, быстроходности и назначения различают валы входные, промежуточные, выходные, тихо- или быстроходные, распределительные.
Особенности конструирования.
Конструктивная форма вала (оси) зависит от нагрузки, способа фиксирования насаживаемой детали и условий сборки (разборки).
Для осевого фиксирования деталей (подшипников, зубчатых колес и др.) на валах выполняют упорные буртики или заплечики.
Материалы валов.
Для изготовления валов используют углеродистые стали марок 20, 30, 40, 45 и 50, легированные стали марок 20Х, 40Х, 40ХН, 18Х2Н4МА, 40ХН2МА и др., титановые сплавы ВТЗ-1, ВТ6 и ВТ9. Выбор материала, термической и химико-термической обработки определяется конструкцией вала и опор, условиями эксплуатации. Быстроходные валы, в подшипниках скольжения, требуют высокой твердости цапф (посадочных хвостовиков), поэтому их изготовляют из цементируемых сталей 12Х2Н4А, 18ХГТ или азотируемых сталей 38Х2МЮА. Валы-шестерни также изготовляют из цементируемых легированных сталей марок 12ХНЗА, 12Х2Н4А и др
|
58. Проектный расчет валов. Проверочный расчет валов на прочность, жесткость и колебания.
Расчёт валов на прочность и жёсткость
Вал принадлежит к числу наиболее ответственных деталей машин, нарушение его формы, или разрушение влечет за собой выход из строя всей конструкции. Для обеспечения работоспособности и надежности валы и оси должны удовлетворять основным критериям: прочности и жесткости (деформативности).
Нагрузки на валы и расчётные схемы
Расчёт на прочность.
В предварительном (проектном) расчете диаметр входного вала d приближенно может быть найден по известному значению крутящего момента из условия прочности
Где Т – крутящий момент в расчётном сечении вала; [τk] - допускаемое напряжение на кручение. [τk] - =12...20 МПа для стальных валов; Р — передаваемая мощность, кВт; п — частота вращения вала, мин -1. Иногда при проектировании диаметр входного хвостовика вала (минимальный диаметр вала) принимают конструктивно (из практики проектирования) равным 0,8...1,0 d вала приводного двигателя. Наименьший диаметр промежуточного вала принимают обычно равным внутреннему диаметру подшипника. Оценку прочностной надежности вала в конструкции выполняют обычно в форме определения запасов прочности
. Статический запас прочности. Рассчитывают по наибольшей кратковременной нагрузке (с учетом динамических и ударных воздействий), которая не может вызвать усталостного разрушения (например, по нагрузке в момент пуска установки). Валы могут быть нагружены постоянными напряжениями, например от неуравновешенности вращающихся деталей. Валы работают в основном в условиях изгиба и кручения, а напряжения от осевых сил малы, поэтому эквивалентное напряжение в точке наружного волокна: где σн и τк — наибольшие напряжения от изгиба моментом Ми и кручения моментом Т. σн= M к / W н; τк=T/Wk Здесь W н и W K — осевой и полярный момент сопротивления сечения вала,
Так как Wk = 2 W Н, то с учетом этих соотношений можно записать
Запас прочности по пределу текучести
σТ – предел текучести материала вала. Обычно принимают допускаемый запас прочности [nT]:=1,2…1,8. Сечение (опасное сечение), в котором следует определить запас n T), находят после построения эпюр изгибающих и крутящих моментов. Если нагрузки действуют на вал в разных плоскостях, то сначала силы проецируют на координатные оси и строят эпюры моментов в координатных плоскостях. Затем геометрически суммируют изгибающие моменты, очерчивая эпюру прямыми линиями, что идет в запас прочности. Если угол между плоскостями 30°, то считают, что силы действуют в одной плоскости. Переменные напряжения в валах вызываются переменной или постоянной нагрузкой. Постоянные по величине и направлению силы передач вызывают во вращающихся валах переменные напряжения изгиба, изменяющиеся по симметричному циклу с амплитудой и средними напряжениями:
В расчетах валов условно принимают, что вращающий момент и касательные напряжения от кручения изменяются по пульсационному циклу, которому соответствуют амплитуда и среднее напряжение:
Условие прочностной надежности в этом случае имеет вид n≥[n].Допускаемые значения запаса прочности при переменных напряжениях назначают на основе предшествующего опыта расчетов и эксплуатации [n]≥2,0. Высокооборотные валы в ряде конструкций работают в условиях изгибных, крутильных и изгибно-крутильных колебаний, вызывающих появление переменных напряжений. Эти напряжения могут быть опасными для прочности вала на резонансных режимах работы. Для предотвращения резонансных колебаний валов проводят их расчет на колебания. Для повышения сопротивления усталости валов используют различные конструктивные и технологические методы. Основной конструктивный метод повышения надежности валов — снижение концентрации напряжений в опасных сечениях путем увеличения радиусов галтелей и др. Существенное значение имеет правильный выбор материала и режима термической обработки заготовки (вала). Для повышения сопротивления усталости валов производят упрочняющую обработку зон концентрации напряжений (выточек, галтелей, шпоночных канавок, резьбы и др.) путем обдувки дробью, лучом лазера и т. п.
|
|
68. Расчёт жёсткости вала. Упругие перемещения валов оказывают неблагоприятное влияние на работу связанных с ними соединений, подшипников, зубчатых колес и других деталей: увеличивают концентрацию контактных напряжений и износ деталей, снижают сопротивление усталости деталей и соединений, точность механизмов и т. п. Большие перемещения сечений вала от изгиба могут привести к выходу из строя конструкции вследствие заклинивания подшипников. Изгибная и крутильная жесткость валов существенно влияет на частотные характеристики системы при возникновении изгибных и крутильных колебаний. При проектировании валов следует проверять прогибы и углы φ поворота сечений, зависящих от требований, предъявляемых к валу, и особенностей его работы. Допустимые величины φ Максимальный прогиб вала не должен превышать (0,0002... 0,0003) L (L — расстояние между опорами), а допустимый прогиб под колесами составляет: 0,01m — для цилиндрических и 0,005 m — для конических, гипоидных и глобоидных передач (m — модуль зацепления).Допустимые относительные углы закручивания валов Ө зависят от требований и условий работы конструкции и лежат в пределах 0,20...1° на 1 м длины вала.
59. Подшипники (опоры валов и осей).
Опоры валов и осей передают нагрузки от вращающихся частей на корпус или плату. Точность действия и надежность работы механизмов во многом зависят от особенностей конструкций опор, значения и стабильности в них сопротивления качению.
Опоры скольжения применяют при необходимости получить небольшие радиальные размеры. Максимальные износ и момент сил трения таких подшипников происходят во время разгона. Использование пористых вкладышей, пропитанных смаз- кой, позволяет существенно уменьшить сопротивление вращению при очень простой конструкции опорного узла. Если нужно получить малый момент сил трения, и вал вращается с небольшой скоростью, то в приборах применяются опоры на центрах и кернах.
|
Наибольшее распространение получили цилиндрические подшипники скольжения. Для снижения момента трения и из- носа соприкасающихся элементов применяют антифрикционные материалы. Крепление втулки в корпусе осуществляют по- садкой с натягом или стопорным винтом. При использовании в конструкции таких опор следует иметь в виду, что даже при незначительном прогибе вала, а также из-за монтажных погрешностей возможны перекосы геометрических осей подшипни- ка и вала, вследствие чего нагрузка по длине подшипника распределяется неравномерно.
По виду трения различают подшипники скольжения с сухим, граничным и жидкостным трением.
I. Радиальные подшипники
1. Шариковые подшипники
Радиально-упорные подшипники
Радиальные шариковые подшипники
Самоустанавливающиеся подшипники
Подшипники с трех- и четырехточечным контактом
Подшипники для подшипниковых узлов
Магнетные подшипники
2. Роликовые подшипники
Цилиндрические роликоподшипники
Игольчатые роликоподшипники
Подшипники с длинными роликами
Конические роликоподшипники
Сферические роликоподшипники
II. Упорные подшипники
1. Шариковые подшипники
Упорные подшипники
Упорно-радиальные подшипники
2. Роликовые подшипники
Цилиндрические упорные подшипники
Игольчатые упорные подшипники
Конические упорные подшипники
Сферические упорные пдшипники
III.Специальные подшипники
Автомобильные подшипники для сцеплений, водяных насосов, ступичные
Железнодорожные буксовые подшипники
Подшипники канатных блоков кранов
Опорно-поворотные устройства
Подшипники для цепных конвейеров
Определение радиальных реакций. Вал на подшипниках, установленных по одному в опоре, условно рассматривают как балку на шарнирно-подвижных опорах или как балку с одной шарнирно-подвижной и одной шарнирно-неподвижной опорой. Радиальную реакцию Fr подшипника считают приложенной к оси вала в точке пересечения с ней нормалей, проведенных через середины контактных площадок. Для радиальных подшипников эта точка расположена на середине ширины подшипника. Для радиально-упорных подшипников расстояние а между этой точкой и торцом подшипника может быть определено графически (рис. 25) или аналитически:
подшипники шариковые радиально-упорные однорядные
a=0,5[B+0,5(d+D))tgα];
подшипники роликовые конические однорядные
a=0,5(T+(d+D)е/з].
Ширину В кольца, монтажную высоту Т, коэффициент е осевого нагружения, угол
Рис.25.Расположение точки приложения
радиальной реакции в радиально-упорных
подшипниках
α контакта, а также диаметры d и D принимают по каталогу.
Реакции опор определяют из уравнения равновесия: сумма моментов внешних сил относительно рассматриваемой опоры и момента реакции в другой опоре равна нулю.
|
В ряде случаев направление вращения может быть переменным или неопределенным, причем изменение направления вращения может привести к изменению не только направления, но и значений реакций опор. При установке на концы валов соединительных муфт направление силы на вал от муфты неизвестно. В таких случаях при расчете реакций рассматривают наиболее опасный вариант. Возможная ошибка при этом приводит к повышению надежности.
63. Конструкции узлов. Уплотнительные устройства. Посадки подшипников на вал и в корпус. Монтаж и демонтаж подшипников. Смазка подшипников качения.
Выборконструкции уплотнительных устройств определяется видом и параметрами уплотняемой среды (давлением, температурой), скоростью и направлением перемещения уплотняемых деталей.
Правильный выбор уплотнительных устройств для подшипниковых узлов повышает долговечность и надежность работы машин. Уплотнения обеспечивают герметичность, предотвращают утечку смазочного материала и проникновение сквозь него пыли, газов, влаги и других посторонних веществ, тем самым предохраняя подшипниковый узел от быстрого износа.
Уплотнительные устройства по принципу действия и конструкции бывают различных типов.
В подшипниковых узлах сельскохозяйственных машин применяют уплотнения контактного типа, в которых уплотнение осуществляется контактом (при трении) между неподвижным уплотнением и валом или между подвижным элементом и корпусом. В устройствах этого типа уплотняющие элементы изготавливают из эластичного или твердого материала (резины, войлока, фетра, кожи и т. п.). По величине максимальной окружной скорости, определяемой на уплотняемой поверхности, по максимальной температуре в подшипниковом узле при наиболее неблагоприятных условиях его работы подшипниковые узлы делят на пять групп. В них используют контактные уплотняющие устройства с эластичными трущимися элементами, качественность и износостойкость которых увеличивается с увеличением 'Групп.
ПОЛЯ ДОПУСКОВ И ПОСАДКИ
Установлены следующие обозначения полей допусков на посадочные диаметры колец подшипника по классам точности (ГОСТ 3325-85):
- для среднего диаметра отверстия подшипников - Ldm, L0, L6,..., L2, LT, где L - обозначение основного отклонения среднего диаметра отверстия подшипника. Ldm - общее обозначение поля допуска средний диаметр dm отверстия подшипника (рис. 33); L0, L6,..., L2, LT - обозначение полей допусков для среднего диаметра отверстия по классам точности 0, 6,..., 2, подшипников (ГОСТ 520-89);
Рис. 33. Схема расположения полей допусков на средние наружный диаметр и диаметр отверстия подшипника
- для среднего наружного диаметра подшипников - lDm, l0, l6,..., l2., lT, где l -обозначение основного отклонения для среднего наружного диаметра подшипника; lDm - общее обозначение поля допуска для среднего наружного диаметра Dm подшипника (рис. 33); l0, l6,..., l2, lT - обозначение полей допусков для среднего наружного диаметра по классам точности 0, 6,..., 2, T подшипников (ГОСТ 520-89).
Установлены поля допусков для диаметров посадочных поверхностей валов и корпусов (табл. 81), а для соединения подшипников с валами (осями) и корпусами - посадки (табл. 82), определяемые сочетаниями полей допусков на сопрягаемые детали в зависимости от классов точности подшипников. Выбор посадок подшипников качения на вал и в отверстие корпуса осуществляют в соответствии с требованиями к точности и необходимой плотности соединения колец с посадочными поверхностями.
Условные обозначения посадок подшипников указывают на сборочных чертежах и в нормативно-технической документации.
Пример обозначения посадки подшипника качения класса точности 0 на вал с номинальным диаметром 50мм, с полем допуска k6 по ГОСТ 25347-82:
Ø50L0lk6 или Ø50L0-k6;
то же в отверстие корпуса с номинальным диаметром 90мм, с полем допуска Н7:
Ø90Н7ll0 или Ø90H7-l0.
Допускается на сборочных. чертежах подшипниковых узлов указывать только размер, поле допуска или предельные отклонения сопряженной с подшипником детали: Ø50k6; Ø90H7.
Паяные соединения
Пайка — технологическая операция, применяемая для получения неразъёмного соединения деталей из различных материалов путём введения между этими деталями расплавленного материала (припоя), имеющего более низкую температуру плавления, чем материал (материалы) соединяемых деталей.
Спаиваемые элементы деталей, а также припой и флюс вводятся в соприкосновение и подвергаются нагреву с тем-пературой выше температуры плавления припоя, но ниже температуры плавления спаиваемых деталей. В результате, припой переходит в жидкое состояние и смачивает поверхности деталей. После этого нагрев прекращается, и припой переходит в твёрдую фазу, образуя соединение.
Прочность соединения во многом зависит от зазора между соединяемыми деталями (от 0,03 до 2 мм), чистоты по-верхности и равномерности нагрева элементов. Для удаления оксидной плёнки и защиты от влияния атмосферы при-меняют флюсы.
Паяные соединения подобны сварным; отличие пайки от сварки – отсутствие расплавления или высокотемпера-турного нагрева соединяемых деталей, так как припои имеют более низкую температуру плавления, чем материалы соединяемых деталей.
Клеевые соединения
Клеевыми соединениями называют неразъемные соединения с помощью клея, образующего между деталями со-единения тонкую прослойку. Клеевые соединения получили широкое распространение благодаря созданию конструкционных высокопрочных клеев на основе синтетических полимеров. Иногда склеивание – единственный способ соединения деталей из различных материалов.
Процесс склеивания
• превращение клеящего вещества в состояние, пригодное для нанесения на поверхности склеиваемых мате-риалов (расплавление, растворение, смешивание и т.д.);
• подготовка поверхностей склеивания (придание шероховатости, обезжиривание и т.д.);
• нанесение клеящего вещества и сборка соединения;
• превращение клеящего вещества в клеевой слой, соединяющий материалы при соответствующей температу-ре, давлении и времени выдержки.
Достоинства и недостатки клеевых соединений
Достоинства клеевых соединений:
• снижение требований к точности сопрягаемых деталей, быстро и экономично осуществляется сборка деталей;
• клеевой слой является хорошим тепло-, звуко- и электроизолятором; • нет ослабления соединяемых деталей;
• клеевые соединения способны скреплять детали, изготовленные из абсолютно разных по физико-химическим свойствам материалов;
• клеящие материалы заполняют микрозазоры, что позволяет получить герметичные соединения;
• пленка клея улучшает распределение нагрузки и препятствует возникновению контактной коррозии.
Недостатки клеевых соединений:
• малая прочность при отрывающих нагрузках с неравномерным ее распределением;
• нестабильность физико-химических свойств во времени;
• ухудшение механических характеристик при понижении и повышении температур, при воздействии биосре-ды, химических реагентов и других факторах;
• необходимость тщательной подготовки поверхностей под склеивание.
Классификация клеев по типу склеивания
• высыхающие клеи (силикатный клей, казеин, столярный клей, клей ПВА, крахмальный клейстер, наирит, 88-Н …);
• невысыхающие адгезивы (например, на основе канифоли), клеи-расплавы; • связки на основе полимеризующихся композиций — неорганические, например алюмофосфатные связки (АФС) и органические, полимеризующиеся композиции (циакрин, эпоксидная смола).
Клей БФ относится одновременно и к категории высыхающих, и полимеризующихся композиций.
Классификация клеев по составу
• неорганические (растворы, расплавы, а также припои, в частности — полимерные композиции типа «клей-припой»);
• органические (растворы, расплавы, полимеризующиеся).
Основой органического клея служат главным образом синтетическое олигомеры и полимеры (например, феноло-формальдегидные, эпоксидные, полиэфирные смолы, полиамиды, полиимиды, полиуретаны, кремнийорганические полимеры, каучуки и др.) образующие клеевую пленку в результате затвердевания при охлаждении (термопластичные клеи), отверждения (термореактивные клеи) или вулканизации (резиновые клеи); этим процессам иногда предшествует улетучивание растворителя.
К неорганическим клеям относят алюмофосфатные, керамические (основа — оксиды магния, алюминия, кремния, щелочных металлов), силикатные (основа — калиевое или натриевое жидкое стекло), металлические (основа — жид-кий металл, например ртуть).
По физическому состоянию клеи могут быть жидкими (растворы, эмульсии, суспензии) или твёрдыми (пленки, прутки, гранулы, порошки); последние используются в виде расплава или наносят на нагретые поверхности.
69. С натягом и профильные соединения.
Профильные соединения.
Профильные соединения применяют для передачи вращающего момента от вала к ступице. В профильных соеди-нениях контакт вала и ступицы осуществляется по некруглой поверхности.
Профильные соединения имеют в поперечном к оси соединения сечении плавный некруглый профиль поверхности контакта вала и ступицы. Чаще применяют равноосные соединения треугольного профиля. Применяемый профиль обладает свойством равноосности – постоянством диаметрального размера. Профильные соединения в осевом направлении могут быть цилиндрическими или коническими (фасонно-профильные соединения: а — по цилиндрическим поверхностям, б — по коническим поверхностям.).
Конструкция и материалы.
Конструкции и материалы.
Корпус редуктора (вместе с крышкой) имеет сложную форму и подвержен действию пространственных нагрузок. Расчет деталей корпуса на прочность и жесткость возможен лишь методами теории упругости.Конструкции деталей корпусов сложны и разнообразны. На практике их конструируют по прототипам. Невысокая нагруженность корпуса редуктора позволяет изготавливать его тонкостенным, а жесткость обеспечивать с помощью ребер и соответствующих утолщений. Для облегчения изготовления корпуса выполняют с разъемом по плоскости, проходящей через оси валов. Экономически целесообразный способ изготовления - литье, а материал - серый чугун. Корпуса могут отливаться из сталей, алюминиевых и магниевых сплавов. Стыковые поверхности корпуса и отверстия под подшипники обрабатывают на станках.
Для защиты от коррозии и в декоративных целях детали корпусов покрывают красками и др. покрытиями.
73. Требования, предъявляемые к корпусным деталям. Классификация. Конструкции.
От конструкции корпусных деталей во многом зависит точность, жесткость и виброустойчивость всей машины. Поэтому к ним предъявляются соответствующие требования достаточно большой жесткости и виброустойчивости, сохранения точности, технологичности конструкции, минимального веса, удобства расположения компонуемых сборочных единиц и механизмов и эстетики.
Отконструкции корпусных деталей во многом зависит точность, жесткость и виброустойчивость всего станка.
Отконструкции корпусных деталей и узлов во многом зависит точность, жесткость и виброустойчивость всего станка. К корпусным деталям станка, предъявляются следующие требования: высокая жесткость и виброустойчивость, длительное сохранение точности, технологичность конструкции, минимально возможный вес, удобное взаимное расположение отдельных узлов, наличие резервуаров для смазки и охлаждения и нИ ш для электроаппаратуры. [ 8 ]
Есликонструкция корпусной детали такова, что базовая плоскость имеет недостаточную протяженность, или на ней отсутствуют базовые отверстия, следует создать дополнительные технологические площадки с отверстиями на них для обеспечения обработки детали от этих баз. В качестве черновой технологической базы при подготовке основной базы рекомендуется использовать поверхности, которые должны быть наиболее точными по ТУ. [ 9 ]
Технологичностьконструкции корпусных деталей имеет особенное значение, так как от этого в значительной степени зависит трудоемкость их изготовления. Чтобы снизить трудоемкость изготовления корпусных деталей и повысить их качество, необходимо при проектировании обеспечить следующие технологические требования.
Классификация корпусных деталей:
1.
-По степени конструктивной сложности
1.
простые, не имеющие внутренних перегородок, рёбер и приливов;
2.
сложные.
2.
-По сообщённости внутреннего пространства с внешней средой
1.
закрытые, внутренняя полость которых, как во время работы, так и в неработающем состоянии, полностью изолирована от внешней среды;
2.
полузакрытые, внутренняя полость которых может сообщаться с внешней средой в отдельные моменты (часть времени) работы машины (механизма) или в неработающем состоянии;
3.
открытые, внутренняя полость которых постоянно сообщена с внешней средой.
3.
По пригодности для хранения эксплуатационного запаса смазочных материалов -
3.1) сухие корпуса, не предназначенные для хранения эксплуатационного запаса смазочных материалов;
3.2) маслонаполненные, ёмкость которых достаточна для хранения эксплуатационного запаса смазочных материалов.
4) По основному материалу, из которого изготовлены детали корпуса -
4.1) металлические (чугун, сталь литая, сталь сварная, лёгкие сплавы - алюминиево-кремниевые, алюминиево-магниевые);
4.2) неметаллические (пластики, дерево, фанера).
Серый чугун (СЧ15, СЧ20) является одним из самых дешёвых и распространённых материалов для изготовления корпусных деталей. Вместе с тем чугунные корпусные детали имеют наибольшую массу по сравнению с аналогичными деталями, выполненными из других материалов. Поэтому из чугуна изготавливают корпуса стационарных машин и механизмов, устанавливаемых на фундаменте.
74. Упругие элементы. Назначение. Конструкци и.
Упругими элементами называют детали машин, работа которых основана на способности изменять свою форму под воздействием внешней нагрузки и восстанавливать ее в первоначальном виде после снятия этой нагрузки.
В технических устройствах используется большое число различных упругих элементов, но наиболее распространены следующие три типа элементов, выполненных как правило из металла:
Пружины (рис. 16.1, а…м) – упругие элементы, предназначенные для создания (восприятия) сосредоточенной силовой нагрузки.
Торсионы (рис. 16.1, н) - упругие элементы, выполненные обычно в форме вала и предназначенные для создания (восприятия) сосредоточенной моментной нагрузки.
Мембраны - упругие элементы, предназначенные для создания (восприятия) распределенной по их поверхности силовой нагрузки (давления).
Пружины и упругие элементы используют в конструкциях в качестве виброизолирующих, амортизирующих, аккумулирующих, натяжных, динамометрических и других устройств.
Классификация пружин: По виду воспринимаемой нагрузки различают:пружины растяжения, сжатия, кручения и изгиба.
По геометрической форме их называют: винтовыми, спиральными, прямыми и др.
В зависимости от назначения пружины бывают: силовыми (аккумуляторы энергии или движители), измерительными (упругие чувствительные элементы), амортизирующими и т. д.
В машиностроении наиболее распространены
винтовые цилиндрические пружины растяжения, сжатия и кручения.
Реже применяют специальные пружины:
тарельчатые и кольцевые – сжатия,
спиральные и стержневые- кручения; листовые (рессоры). пружины а - растяжения; б - сжатия; в - кручения; г - фасонные
а - тарельчатая; б- кольцевая; в - спиральная; г - стержневая; д - рессора
ОБЩАЯ ХАРАКТЕРИСТИКА ВАЛОВ И ОСЕЙ
Назначение и классификация. Валы служат для поддержания вращающихся деталей и передачи вращающего момента от одной детали к другой (в осевом направлении) Их условно разделяют на: простые валы (валы) - работают в условиях кручения, изгиба и растяжения (сжатия), их применяют в передачах: зубчатых, ременных и др.; торсионные валы (торсионы) - работают лишь в условиях кручения и передают вращающий момент, соединяя обычно два вала на индивидуальных опорах; оси — поддерживающие валы, работающие лишь в условиях изгиба. В зависимости от распределения нагрузок вдоль оси вала и условий сборки прямые валы выполняют гладкимиилиступенчатыми, Гладкие валы более технологичны. Коленчатые валы используют в поршневых двигателях и компрессорах Для передачи вращающего момента между агрегатами со смещенными в пространстве осями применяют специальные гибкие валы. Такие валы обладают высокой жесткостью при кручении и малой жесткостью при изгибе. В зависимости от расположения, быстроходности и назначения различают валы входные, промежуточные, выходные, тихо- или быстроходные, распределительные.
|
|
Поперечные профили набережных и береговой полосы: На городских территориях берегоукрепление проектируют с учетом технических и экономических требований, но особое значение придают эстетическим...
Особенности сооружения опор в сложных условиях: Сооружение ВЛ в районах с суровыми климатическими и тяжелыми геологическими условиями...
Типы оградительных сооружений в морском порту: По расположению оградительных сооружений в плане различают волноломы, обе оконечности...
Индивидуальные очистные сооружения: К классу индивидуальных очистных сооружений относят сооружения, пропускная способность которых...
© cyberpedia.su 2017-2024 - Не является автором материалов. Исключительное право сохранено за автором текста.
Если вы не хотите, чтобы данный материал был у нас на сайте, перейдите по ссылке: Нарушение авторских прав. Мы поможем в написании вашей работы!