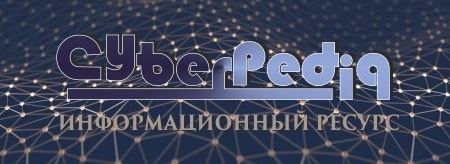
Индивидуальные очистные сооружения: К классу индивидуальных очистных сооружений относят сооружения, пропускная способность которых...
Особенности сооружения опор в сложных условиях: Сооружение ВЛ в районах с суровыми климатическими и тяжелыми геологическими условиями...
Топ:
Эволюция кровеносной системы позвоночных животных: Биологическая эволюция – необратимый процесс исторического развития живой природы...
Организация стока поверхностных вод: Наибольшее количество влаги на земном шаре испаряется с поверхности морей и океанов...
Определение места расположения распределительного центра: Фирма реализует продукцию на рынках сбыта и имеет постоянных поставщиков в разных регионах. Увеличение объема продаж...
Интересное:
Распространение рака на другие отдаленные от желудка органы: Характерных симптомов рака желудка не существует. Выраженные симптомы появляются, когда опухоль...
Подходы к решению темы фильма: Существует три основных типа исторического фильма, имеющих между собой много общего...
Что нужно делать при лейкемии: Прежде всего, необходимо выяснить, не страдаете ли вы каким-либо душевным недугом...
Дисциплины:
![]() |
![]() |
5.00
из
|
Заказать работу |
|
|
Аннотация
Ленточные конвейеры играют важную роль в процессе транспортировки сухих сыпучих материалов. Управление скоростью является перспективным способ снижения энергопотребления ленточных конвейеров. Однако, мимолетными операции это может привести к таким рискам, как утечка материала с ленточного конвейера. Неожиданные риски ограничивают применимость контроля скорости. Современные исследования по управлению скоростью в основном сосредоточены на разработке энергетических моделей ремней безопасности конвейеры или построение алгоритмов управления вариаторами, в то время как редкие исследователи принимают во внимание рассмотрены риски при переходных режимах работы и динамические характеристики ленточных конвейеров при регулировании скорости движения. То в статье предложен метод Estimation-Calculation-Optimization (оценки-расчета-оптимизации) (ЭКО) для определения минимальной скорости движения время регулировки для обеспечения здоровых переходных операций. Метод ЭКО состоит из трех этапов и учитывает как риски при переходных операциях, так и динамику конвейера.На этапе оценки,оценщик построен так, чтобы приблизить допустимое максимальное ускорение, рассматривая ленту как жесткое тело.Учитывая вязкоупругие свойства ленты, на этапе расчета производится расчет динамики конвейера методом конечных элементов. Что касается рисков при переходных операциях, то оптимизация шаг улучшает динамические характеристики конвейера и оптимизирует время регулировки скорости. В случае длительного изучена система ленточного конвейера и применен метод ЭКО. Секущий метод также используется для улучшения эффективность оптимизации. Согласно экспериментальным результатам, метод ЭКО успешно применяется определить минимальное время регулировки скорости для обеспечения работоспособности переходных процессов, включая оба ускоряющие и замедляющие операции. С предложенным временем регулировки, непредвиденные риски избегаются и ленточный транспортер показывает соответствующее динамическое поведение. Соответственно, ЭКО-метод обеспечивает здоровые переходные операции и улучшает применимость регулирования скорости с учетом о потенциальных рисках и динамике конвейера.
|
ABSTRACT
Belt conveyors play an important role in the dry bulk material handling process. Speed control is a promising method of reducing the power consumption of belt conveyors. However, inappropriate transient operations might cause risks like material spillage away from the belt conveyor. The unexpected risks limit the applicability of speed control. Current studies on speed control mainly focus on designing energy models of belt conveyors or building control algorithms of variable speed drives, while rare researchers take into account the risks in transient operations and the dynamic performance of belt conveyors under speed control. The paper proposes an Estimation-Calculation-Optimization (ECO) method to determine the minimum speed adjustment time to ensure healthy transient operations. The ECO method is composed of three steps and takes both risks in transient operations and the conveyor dynamics into account. In the Estimation step, an estimator is built to approximate the permitted maximum acceleration by treating the belt as a rigid body. Taking the belt’s visco-elastic property into account, the Calculation step computes the conveyor dynamics by using a finite-element-method. With respect to the risks in transient operations, the Optimization step improves the conveyor’s dynamic behaviors and optimizes the speed adjustment time. A case of a long belt conveyor system is studied and the ECO method is applied. The secant method is also used to improve the optimization efficiency. According to the experimental results, the ECO method is successfully used to determine the minimum speed adjustment time to ensure healthy transient operations, including both the accelerating and the decelerating operations. With the suggested adjustment time, unexpected risks are avoided and the belt conveyor shows an appropriate dynamic behavior. Accordingly, the ECO method ensures healthy transient operations and improves the applicability of speed control with the consideration of the potential risks and the conveyor dynamics.
Введение
Ленточная конвейерная система-это типичная непрерывная транспортная система, транспортирующая сухие сыпучие твердые материалы без каких-либо перерывов.На протяжении более чем столетия ленточные конвейеры были важным фактором часть погрузочно-разгрузочных работ как для внутризаводских, так и для сухопутных перевозок [1,2]. После Второй Мировой Войны появились резиновые технологии период бурного развития и эти изменения способствовали совершенствование конвейерных систем. В предыдущие десятилетия ленточные конвейеры стали длиннее и быстрее, с большей производительностью и меньше воздействие на окружающую среду [3]. Кроме того, ленточные конвейерные системы зарекомендовали себя как один из самых экономичных способов обработки грузов сыпучие твердые материалы.
|
Из-за присущих им преимуществ, таких как большая емкость и низкая требования к труду, ленточные конвейеры играют значительную роль в сыпучих веществах погрузочно-разгрузочные работы и транспортировка, особенно в некоторых районах, где транспорт инфраструктура развита слабо или вообще отсутствует[4]. Согласно [5], ежегодно здесь работает более 2,5 миллионов ленточных конвейеров в мире. Учитывая широкое применение ленточных конвейеров, их операции требуют огромного количества электроэнергии. Hiltermann [6] дает пример, показывающий, что ленточные конвейеры отвечают за 50% до 70% от общего потребления электроэнергии в сухогрузном терминале. Тем не менее, большая часть электроэнергии сегодня все еще производится за счет сжигания ископаемого топлива такие виды топлива, как уголь и нефть. Как Гото и др. [7] далее предполагают, что угольные электростанции в настоящее время обеспечивают 41% мирового производства электроэнергии, в то время как на долю угля приходится более 45% мировых выбросов углекислого газа в атмосферу. топливо [8]. Поэтому, принимая во внимание соответствующие экономические и социальные проблемы, есть сильный запрос на улучшение энергетики эффективность ленточных конвейеров и снижение углеродного следа.
Доказано, что регулирование скорости является перспективным подходом к повышению энергоэффективности ленточных конвейеров. Способ корректировки скорость транспортера для того чтобы соответствовать фактической материальной подаче как уменьшить расход энергии - это так называемое регулирование скорости [6]. Обычно,ленточные конвейеры работают с постоянной нормальной скоростью. Они всегда так делают являются частью цепи обработки сыпучих материалов, и фактическая скорость подачи определяется процессом обработки верхнего потока. Затем из-за изменения потока сыпучих материалов, сбрасываемых на ленту, однако в большинстве случаев они заполняются лишь частично. В таких случаях,если фактический материальный поток или пик предстоящего материала подачу можно предсказать, скорость транспортера можно отрегулировать для того чтобы соответствовать их вариация. Затем, согласно полученной расчетной модели по сравнению со стандартом DIN 22101 [9] ожидается снижение энергопотребления ленточного конвейера. К тому же перспективная энергетика экономия, дополнительные преимущества могут быть достигнуты за счет контроля скорости, например, меньше техническое обслуживание [10].
|
Исследования в области контроля скорости можно датировать еще до конца прошлого века. прошлый век. За последние несколько лет было получено несколько важных результатов были достигнуты определенные результаты. На основе стандарта DIN 22101, Hiltermann и др. [11] предложен метод расчета экономии энергии достигается за счет регулирования скорости. Чжан и Ся [12] предложили альтернативную расчетную модель, которая объединила энергетические расчеты DIN 22101 и ISO 5048 [13] и предложил модель-прогностический контроль способ оптимизации эффективности работы ленточных конвейеров. Около рассматривая динамику ленточных конвейеров, авторы настоящей статьи предложен нечеткий метод управления для регулирования скорости движения конвейера в дискретным образом [14]. Еще один нечеткий логический контроллер был построен компанией Ristic et al. [15] с целью применения регулирования скорости к ленте конвейеры.
Однако предыдущие исследования не охватывали некоторые вопросы, такие как потенциальные риски в переходных операциях. Переходными операциями являются операции регулировки скорости конвейера в соответствии с фактической материальный поток. В переходных режимах большая скорость подъема конвейера может привести к очень высокому напряжению на ленте [14]. То неожиданная высокая напряженность является основной причиной разрыва ремня на зона сращивания. Помимо риска чрезмерного натяжения ремня, существуют некоторые другие риски при переходных операциях, включая риск проскальзывания ремня вокруг приводного шкива, риск высыпания материала из ремень, риск перегрева двигателя, а также риск проталкивания мотор в регенеративную работу. Тем не менее, мало исследований обсуждали динамические характеристики конвейера в переходных режимах работы контроля скорости. Хотя некоторые исследователи и инженеры имеют изучая динамику конвейеров на протяжении десятилетий [16-19], они в основном ориентированы о реализации мягких пусков или мягких остановок. По сравнению с нормальный запуск или остановка, переходные операции для контроля скорости следует уделить больше внимания, так как ленточные конвейеры часто имеют высокий коэффициент заполнения в этих операциях. Кроме того, динамика конвейера в переходном режиме работы имеет сложность, особенно в случае где часто используется ленточный транспортер большой протяженности и большой емкости ускоренный или замедленный, чтобы соответствовать переменному потоку материала.
|
Эта статья является еще одним шагом нашей предыдущей работы [20,21]. То целью данной статьи является поиск способа сохранения контроля скорости движения здоровый с учетом динамики конвейера, особенно в переходные операции. Для реализации здорового управления скоростью предлагается метод расчетно-оптимизационного оценивания (сокращенно ЭКО)определите требуемое минимальное время регулировки скорости. ОЭС метод состоит из трех этапов и принимает оба риска в переходном периоде деятельность и динамические характеристики ленточного транспортера в счет. На этапе оценки строится оценщик для вычисления минимальное время разгона. Так как оценщик не учитывает вязкоупругое свойство ленты, шаг расчета необходимо выполнить для анализа динамики конвейера при изменении скорости конвейера корректируется с учетом расчетного времени разгона. Если на этапе расчета наблюдаются такие риски как проскальзывание ремня вокруг ведущего шкива, дальнейшее моделирование следует проводить на этапе оптимизации, чтобы улучшить переходный режим работы и найти theminimum ускорение время. Помимо нашей предыдущей работы [20,21], в этой статье обсуждаются оба ускоряющие и замедляющие операции. Кроме того, он также учитывает различные диапазоны регулировки скорости. Кроме того, итерация метод используется для сокращения времени моделирования при оптимизации шаг по повышению эффективности оптимизации.
Структура этого документа выглядит следующим образом. В разделе 2 дается определение концепции переходного процесса и анализируются потенциальные риски при его реализации,переходные операции. В разделе 3 подробно описан метод ЭКО, компоненты которого подробно описаны шаг за шагом. Длинная система ленточного транспортера изучено в разделе 4, где метод ЭКО используется для достижения минимальное время регулировки скорости переходных операций. Последний раздел завершает результаты и выводы настоящего исследования.
|
Перегрев двигателя
По мере того как мотор работает, он преобразовывает электрическую энергию в механическую энергия. При таком преобразовании часть энергии теряется за счет двигателя утрата. Температура двигателя повышается из-за тепла, выделяемого от потери двигателя во время работы. Если температура обмоток равна при превышении номинальной температуры двигатель перегревается. Перегрев возникает из-за ряда факторов, одним из которых может быть нездоровый переходная работа с быстрым ускорением. Как правило, двигатели могут обеспечьте больший крутящий момент вала, чем номинальный в течение короткого периода времени,время без перегрева. Однако, если перегрузка продолжается в течение долгое время или нагрузка значительно превышает допустимую нагрузку, она увеличивается опасность перегрева. Особенно в тех случаях, когда мотор есть работающий на низкой частоте и охлаждающий вентилятор установлен на вал ротора, уменьшенная эффективность охлаждения увеличивает риск мотора перегрев.
Перегрев является серьезной проблемой для двигателя и может привести к количество проблем с производительностью. Как предполагает Виденбрюг [28],срок службы изоляции обмоток сокращается вдвое на каждые 10 °C выше номинального температура. Например, в случае двигателя со сроком службы 20 лет и с номинальной температурой 40 ◦C, срок службы двигателя сокращается примерно до 1 года, если он работает при температуре 80 °C. Более того, как Мирза [29] таким образом, более 55% отказов изоляции вызваны перегревом. Хотя современные изоляционные материалы более долговечны,перегрев по-прежнему значительно сокращает срок службы двигателя.Таким образом, переходные операции должны избегать перегрузки системы.
ЭКО метод
При проектировании ленточных конвейеров применяются существующие стандарты, такие как DIN 22101 [9], CEMA [27] и ISO5048 [13], Как правило, используются для расчета необходимые движущие силы на приводных шкивах и приблизить минимальное время запуска. Важно отметить, что при расчете этих стандартов конвейерная лента рассматривается как жесткое тело да и упруговязкие свойства ремня не учитываются. В если речь идет о системах ленточного конвейера малой протяженности и малой производительности, то это может привести к приемлемому динамическому поведению ремня. Однако, в случай систем ленточных конвейеров большой протяженности и большой производительности,незнание динамики ремня может вызвать такие эксплуатационные проблемы, как преждевременное разрушение ремня и повреждение приводных систем.Поэтому необходим способ обеспечения здоровых переходных процессов для защиты ленточного конвейера от потенциальных рисков, особенно в условиях эксплуатации в случаи, когда скорость конвейера часто регулируется. Основывающийся на основе нашей предыдущей работы [20,21] в данной работе предлагается метод расчетно-оптимизационной оценки (ЭКО) для определения минимума время регулировки скорости, принимая на себя как потенциальные риски, так и учитывается динамика конвейера.
Метод ЭКО основан на моделировании и состоит из трех этапов этапы: оценка, расчет и оптимизация. при оценке шаг, оценщик строится для оценки минимального времени корректировки.Принимая во внимание потенциальные риски, перечисленные в разделе 2, оценщик рассматривает ремень как жесткий элемент и вычисляет допустимые значения максимальное ускорение в переходных режимах работы. Затем, учитывая профили ускорения, требуемая минимальная скорость время регулировки может быть грубо оценено. В разделе 3.1 описываются оценка в деталях. Цель этапа расчета состоит в том, чтобы наблюдать динамические характеристики ленты в переходных режимах работы. Этот шаг учитывает влияние гистерезиса ремня и проводит компьютерное моделирование. Моделирование проводится на основе конечного элемента метод, который подробно описан в разделе 3.2. В случае дальнего следования и ленточный транспортер большой емкости, динамика транспортера в переходном процессе сложна относительно вязкоупругости ленты.Поэтому переходная операция наблюдается на этапе расчета это может привести, например, к риску чрезмерного натяжения ремня. В таких случаях,оптимизация необходима для улучшения динамических характеристик и для достижения требуемого минимального времени регулировки скорости.В разделе 3.3 представлен шаг оптимизации.
Оценка
Принимая во внимание потенциальные риски в переходных операциях,оценщик строится на этом шаге для оценки минимальной корректировки время. Для того, чтобы четко описать оценщик, случай, как показано в рис. 3 - это пример. Ленточный транспортер приводится в движение головным шкивом. В чтобы обеспечить предварительное натяжение, один шкив гравитационного захвата устройства устанавливается на обратной стороне после головного шкива. В следующем,как допустимое максимальное ускорение, так и замедление являются вычисленный.
Максимальное ускорение
Что касается риска разрыва ленты в месте соединения, вызванного чрезмерным натяжением, то натяжение ленты на пути транспортировки должно поддерживаться на безопасном уровне. В случаях, показанных на рис. 3, максимальный пояс натяжение обычно происходит непосредственно перед приводным шкивом. Напряжение Т1 прежде чем приводной шкив в установившемся состоянии можно будет аппроксимировать с помощью
=
+ Fd (4)
где Fd-движущая сила, а T2-натяжение ремня после привода шкив. Как показано на рис. 3.Если горизонтальное расстояние между приводной шкив и гравитационное приемное устройство с массой mT невелики,натяжение ремня T2 после приводного шкива можно аппроксимировать следующим образом
=
g (5)
Рис. 3. Ленточный транспортер с одиночным срезанным гравитационным захватом. “a": конвейерная лента; " b”:зевака; “с”: приводной шкив; “d”: до шкива; “е”: принять меры массы; “Lconv: длина конвейера; " Ls: горизонтальное расстояние между приводным шкивом и приемным шкивом.
где g-ускорение силы тяжести. По данным эквалайзера. (1), допустимое натяжение ремня перед приводным шкивом может быть оценено с помощью
=
(6)
Затем комбинация эквалайзеров. (4) - (6) дает максимально допустимые значения движущих сил
=
-
(7)
в отношении риска чрезмерного натяжения ремня.
Проскальзывание ремня является еще одним серьезным риском в операциях ускорения. Как согласно Эйлеру [24] и Энтельвейну [25], проскальзывание ремня происходит всякий раз, когда движущая сила, действующая на приводной шкив, превышает максимально допустимое трение. Тогда по экв. (3), максимум требуемые движущие силы ограничены
=
=
(
-1) (8)
чтобы предотвратить риск проскальзывания ремня.
Номинальный крутящий момент двигателя-это максимальный непрерывный крутящий момент, доступный при расчетной скорости, которая позволяет двигателю выполнять работу без перегрев. В практических ускоряющих операциях максимальный рабочий крутящий момент должен быть немного больше номинального крутящего момента на несколько секунд. Коэффициент максимального рабочего момента а номинальный крутящий момент определяется как коэффициент обслуживания (
). Например, в стандартный коэффициент обслуживания для открытого капельного двигателя составляет 1,15 дюйма [30].Затем в режиме разгона максимально допустимый двигатель рабочий крутящий момент
.,
=
(9)
и максимальная движущая сила на приводной шкив
(10)
в котором является передаточным отношением коробки передач, а
-приводными шкивами радий.
Затем принимая эти три риска при ускорении операций в учет, разрешенная максимальная движущая сила в переходном процессе операции являются
(11)
Согласно Второму закону Ньютона, ускорение- это конечный результат любых и всех сил, действующих на ленточные конвейеры. Затем в ускорении операции, допустимое ускорение которых составляет
(12)
где -общее сопротивление движению, а
-общий комок масса ленты, роликов и насыпного материала на ленте. По данным немецкого Института стандартизации [9], эмоциональная сопротивления вдоль транспортирующего маршрута могут быть оценены по формуле
(13)
а общая масса составляет
(14)
в котором
-коэффициент вторичных сопротивлений
-искусственный коэффициент сопротивления трению
-длина транспортирования транспортера
-масса роликов в единице длины
-линейная плотность пояса
-линейная плотность сыпучего материала
-угол наклона ленточного конвейера
-разность высот между погрузкой и разгрузкой зоны ленточного конвейера
Наконец, максимально допустимое ускорение можно оценить по формуле замена эквалайзеров. (13) и (14) в эквалайзер. (12).
Максимальное замедление
При мягком торможении движущая сила, действующая на приводные шкивы постепенно уменьшаются и скорость конвейера уменьшается гладко. В отличие от операции ускорения, операция торможения в основном учитывает риск вдавливания двигателя в двигатель восстановительные операции. В случае ленточных транспортеров которые не могут обеспечьте отрицательные движущие силы, максимальное торможение может быть оцененным по:
(15)
Расчет
На этапе оценки строится оценщик для аппроксимации полученного результата.допустимое ускорение и требуемое время регулировки. Оценщик рассматривает пояс как жесткий элемент, и он предполагает, что все массы ускоряются или замедляются одновременно с та же скорость. Однако пренебрежение эластичностью ремня в условиях высокой емкости и / или междугородние конвейеры могут привести к эксплуатационным проблемам.Кроме того, оценщик не учитывает риск материального ущерба.утечка вызвана низкой скоростью или низким натяжением ремня. Таким образом, динамический анализ играет важную роль для определения того, является ли потенциальные риски возникают при проведении переходных операций.
В нашей предыдущей работе [3] дан подробный исторический обзор моделирования динамики ленточного конвейера. Конечно-элементные модели ленточного конвейера были разработаны системы для расчета динамики конвейера поведение, особенно во время пристального взгляда и остановки. Хотя эти модели определяют только продольный отклик ремня по формуле главным образом используя ферменные элементы, они успешно предсказывают упругий отклик ремня при запуске и остановке.Лодевейкс и Крузе [32] приводят важный пример, в котором оба были проведены полевые измерения и моделирование на основе конечно-элементной модели. Экспериментальные результаты показывают, что отклонение между измеренными результатами и расчетными результатами может быть ограничено в пределах 5%, что соответствует точности полевые измерения. Поэтому конечно-элементная модель, принимая учитывая вязкость-эластичность ленты, способен анализировать динамика конвейера в переходных режимах работы.
Модель конечных элементов, используемая в работе [32], является производной от нашей предыдущей работы [33], которая была широко принята и использована другими авторами.исследователи и инженеры. При Конечно-элементном подходе распределенная масса ленты, холостых роликов и сыпучего материала составляет делится на конечное число элементов. на рисунке. 5, эти элементы являются представлены узлами и пронумерованы последовательно. Как показано на рисунке,конвейер равномерно разделен на N-1 сегментов с N узлами. То сумма массы ленты, массы холостого хода, массы сыпучего материала (на несущей стороне ленты) рассматривается как единичная комковатая масса на каждом узле.На несущей стороне комковатая масса узла равна сумме эквивалентная масса ремня, эквивалентная масса холостого хода и эквивалентный объем материальная масса. На обратной стороне комковатая масса узла равна сумма массы ремня и массы холостого хода. Важной нотацией является что масса комка (i + 1) - го узла включает в себя массу хвоста шкив. Кроме того, из-за вязкости-эластичности ленты, прилегающие узлы соединены пружинно-демпфирующим соединителем, кратко представленным с помощью пружинного элемента на рис. 5.
Как предполагает Лодевейкс [33], разумно предположить, что лента укладывается в горизонтальном направлении и движется в одном направлении. Рис. 6 иллюстрирует одномерную модель одного приводного ремня
Рис. 5. Метод конечных элементов кусковой пружины-демпфера.
конвейерная система. В этой модели, движущая сила , размещенных на 1- й узел и предварительное натяжение размещаются как на 1-м, так и на
узлах.Смещение всех узлов можно выразить как относительное смещение
-го узла. Затем, согласно Второму закону Ньютона,движение ленточного конвейерa можно описать следующим образом
Mx¨ + Cx˙ + Kx = F (21)
где
M- Матрица массы, размер N × N
C -матрица коэффициентов демпфирования, размер N × N
K -матрица коэффициентов пружины, размер N × N
x -вектор узлового смещения, размер N × 1
x˙ -вектор узловой скорости, размер N × 1
x¨ -вектор узлового ускорения, размер N × 1
F -вектор силы, размер N × 1
Оптимизация
Что касается эластичности-вязкости ленты, то динамические характеристики ленточного конвейера сложны. В связи с тем, что оценщик рассматривает ленту как жесткий объект, переходная работа конвейера на этапе расчета может привести, например, к тому, что,риск проскальзывания ремня безопасности. Если это так, то необходимо провести дальнейшие исследования для повышения динамических характеристик конвейера в переходных режимах работы. В таблице 1 приведены некоторые решения, в том числе замена нового пояс с более высокой номинальностью напряжения, оптимизируя массу приемного устройства, применяя более мягкий профиль торможения и увеличивая время регулировки скорости. По отношению к тому, что изменение конструкция или компоненты существующего конвейера непрактичны в какой-то степени общий метод улучшения состоит в том, чтобы расширить время регулировки скорости. Затем выполняется третий этап-оптимизация выходите, чтобы найти минимальное время регулировки скорости.
Оптимизация осуществляется с использованием конечно-элементной модели на основе имитационные расчеты. Процедуру оптимизации можно рассматривать как процесс поиск корней. Например, рискуя проскальзыванием ремня. Максимальное доступное сопротивление трению между ремнем и приводом шкив . Предполагается, что во время переходных операций,движущая сила может превышать максимально допустимое трение
. Оно далее предполагается, что
представляет собой максимальную движущую силу при различном времени ускорения t. например,
(30) представляет собой максимальная движущая сила во время конкретной переходной операции в течение времени разгона 30 сек. Затем по отношению к риску проскальзывание ремня, минимальное время разгона может быть приближено к нахождение корня функции
(22)
Хотя компьютер в наше время очень мощный и может быстро завершить расчеты, предложены итерационные методы таким образом, чтобы
Рис.6. Одномерная модель ленточной конвейерной системы.
Таблица 1
Потенциальные риски при переходных операциях и их решения.
Потенциальный риск | Предлагаемое решение |
Чрезмерное натяжение ремня при сращивании область | Замените новый ремень на более высокий номинальность напряжения Увеличьте время регулировки скорости или применить более мягкий профиль ускорения Уменьшите массу поглощения устройства |
Проскальзывание ремня вокруг привода шкив | Увеличьте массу приемного устройства Увеличить угол обхвата или заменить новый шкив с более высоким коэффициентом трения коэффициент сопротивления Увеличьте время регулировки скорости и уменьшите движущую силу |
Перегрев двигателя | Увеличьте время регулировки скорости и уменьшите движущую силу Уменьшите частоту скорости процесс регулирования Замените новый мотор на более высокий номинальный крутящий момент Установка устройства охлаждения |
Утечка материала в сторону от ремня | Уменьшите механический рывок на удлиняя время регулировки скорости или применение более мягкого профиля замедления |
Толкает мотор в машину восстановительные работы | Нанесите более мягкий профиль ускорения или увеличьте время регулировки скорости |
находите решения быстрее. Эти методы главным образом включают метод деления пополам, метод ложного положения, метод Ньютона-Рафсона способ и метод секущих. Потому что исследование итерации методы выходят за рамки данной статьи, итерационные методы будут здесь мы больше не будем обсуждать этот вопрос. Более подробно о методах итерации можно найти в [34-36].
Примерное исследование: ленточный конвейер большой грузоподъемности и большой дальности действия
Для того чтобы показать, как ЭКО-метод используется для определения минимальное время регулировки скорости, этот раздел изучает горизонтальное положение ленточный транспортер большой дальности и большой емкости. Ленточный транспортер-это разработан компанией Lodewijks [33]. Проектная мощность составляет 2500 тонн в час для транспортировка угля с плотностью 850 кг/м3, а расстояние транспортировки составляет 1000 м. тканевая лента, с модулем Юнга 370 МПа и выбирается номинальное натяжение 500 кН/м. Линейная плотность ленты составляет 14,28 кг/м. несущая часть ремня поддерживается тремя кольцевыми станциями со средней массой на единицу длины 14,87 кг /м. Возвратная часть поддерживается однороликовыми станциями со средней массой на единицу длины 7,72 кг/м. конвейер приводится в движение одним роликом.Двигатель мощностью 250 кВт, Номинальный крутящий момент которого составляет 1592 Нм. Дополнительные параметры характеристики ленточной конвейерной системы проиллюстрированы в таблице 2. В качестве примеров из приведенного примера следует, что одна операция ускорения составляет от 2 м/с до 4 м/с и одна операция замедления от 4 м/с до 2 м/с изучаются в подразделы 4.1 и 4.2, соответственно.
Шаг 1: Оценка
На основе данных, приведенных в таблице 2, экв. (7) предполагает, что разрешенные движущие силы
=
-
(23)
что касается риска чрезмерного натяжения ремня. Принимая на себя риск пояса проскальзывание вокруг приводного шкива учитывается, эквалайзер. (8) дает следующие результаты: разрешенные движущие силы
=
(24)
Кроме того, что касается риска перегрева двигателя, то максимальные движущие силы аппроксимируются уравнением (10):
(25)
Затем, принимая во внимание эти три риска, разрешенные максимальные движущие силы составляют
(26)
Результат в эквалайзере. (26) предполагает, что при ускорении работы эта специфическая система ленточного транспортера, самый высокий риск смещение ленты вокруг приводного шкива. Кроме того, он также предполагает, что из- за явление проскальзывания ремня, как и риск чрезмерного натяжения ремня и риск перегрева двигателя предотвращается. Затем взяв на себя движущие сопротивления вдоль транспортирующего маршрута учитываются, экв. (12) предлагает максимальное значение ускорения
(27)
Соответственно, для этого требуется как минимум
(28)
для завершения операции разгона от 2 м/с до 4 м/с с помощью синусоидальный профиль ускорения.
Шаг 2: Расчет
На этом этапе проводится моделирование для исследования конвейера динамическое поведение в режиме разгона от 2 м/с до 4 м/с в течение 41 сек. моделирование основано на следующих предположениях:
* Конвейерная лента полностью загружается во время моделирования. То весь пояс визуально разделен на 21 часть. Как На Рис. 5 показывает, узлы пронумерованы от выгруженной области несущей стороны. Длина узлов 1 и 21 составляет 50 м, а остальные длина узлов составляет 100 м.
• Всякий раз, когда движущая сила пытается превысить имеющуюся сопротивление трению, ремень скользит вокруг приводного шкива,а силы, приложенные к приводному шкиву, равны максимуму доступные трения между ремнем и приводным шкивом.
Кроме того, даны некоторые другие предположения, что максимум допустимое отношение провисания ремня составляет 3%, и это допустимое отклонение скорости это 15%. Поэтому натяжение ремня вдоль несущей стороны должно быть не менее чем
(29)
где - расстояние между зеваками несущей стороны, а каблук - макс<
|
|
Опора деревянной одностоечной и способы укрепление угловых опор: Опоры ВЛ - конструкции, предназначенные для поддерживания проводов на необходимой высоте над землей, водой...
Поперечные профили набережных и береговой полосы: На городских территориях берегоукрепление проектируют с учетом технических и экономических требований, но особое значение придают эстетическим...
Типы оградительных сооружений в морском порту: По расположению оградительных сооружений в плане различают волноломы, обе оконечности...
Эмиссия газов от очистных сооружений канализации: В последние годы внимание мирового сообщества сосредоточено на экологических проблемах...
© cyberpedia.su 2017-2024 - Не является автором материалов. Исключительное право сохранено за автором текста.
Если вы не хотите, чтобы данный материал был у нас на сайте, перейдите по ссылке: Нарушение авторских прав. Мы поможем в написании вашей работы!