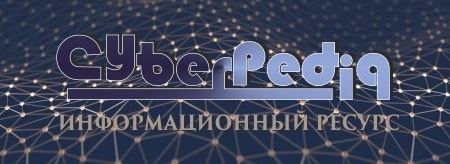
Особенности сооружения опор в сложных условиях: Сооружение ВЛ в районах с суровыми климатическими и тяжелыми геологическими условиями...
Поперечные профили набережных и береговой полосы: На городских территориях берегоукрепление проектируют с учетом технических и экономических требований, но особое значение придают эстетическим...
Топ:
История развития методов оптимизации: теорема Куна-Таккера, метод Лагранжа, роль выпуклости в оптимизации...
Марксистская теория происхождения государства: По мнению Маркса и Энгельса, в основе развития общества, происходящих в нем изменений лежит...
Интересное:
Принципы управления денежными потоками: одним из методов контроля за состоянием денежной наличности является...
Отражение на счетах бухгалтерского учета процесса приобретения: Процесс заготовления представляет систему экономических событий, включающих приобретение организацией у поставщиков сырья...
Что нужно делать при лейкемии: Прежде всего, необходимо выяснить, не страдаете ли вы каким-либо душевным недугом...
Дисциплины:
![]() |
![]() |
5.00
из
|
Заказать работу |
|
|
1. Трансформатор ТД-500.
2. Измерительные приборы: амперметр, вольтметр, секундомер, штангенциркуль.
3. Эталонные рамки для флюса.
4. Пластины, имитирующие изношенную деталь.
5. Пластинчатые стальные электроды.
6. Держатель электрода, флюс, угольный электрод (стальные опилки), металлический груз.
7. Плакат «Схема установки для наплавки пластинчатым электродом под флюсом».
8. Поперечный и продольный темплеты наплавленных слоев.
III Порядок выполнения работы
1. Ознакомиться с технологией наплавки пластинчатым электродом, пользуясь описанием, и плакатом.
2. Собрать опытную установку.
3. Последовательно произнести наплавку пластинчатыми электродами при трех значениях толщины подслоя флюса между пластиной и электродом, замеряя I св, U д и время каждой наплавки.
4. После охлаждения и очистки от шлака измерить ширину, высоту и глубину проплавления каждого слоя.
5. Параметры режима наплавки и результаты измерений занести в таблицу.
6. Изучить и нарисовать эскиз поперечного темплета наплавленного слоя.
7. Сделать выводы по работе.
IV Содержание отчета по работе
1. Схема установки для наплавки пластинчатым электродом.
2. Краткое описание технологии процесса наплавки.
3. Таблица опытных данных.
4. Эскиз поперечного темплета наплавленного слоя.
5. Выводы но работе.
ЛАБОРАТОРНАЯ РАБОТА № 3
ВЛИЯНИЕ НЕКОТОРЫХ ТЕХНОЛОГИЧЕСКИХ ПАРАМЕТРОВ ВИБРОДУГОВОЙ НАПЛАВКИ НА ПРОИЗВОДИТЕЛЬНОСТЬ ПРОЦЕССА И СВОЙСТВА НАПЛАВЛЕННОГО СЛОЯ
Цель работы: ознакомиться с процессом вибродуговой наплавки, изучить устройство установки для вибродуговой наплавки, а также установить влияние технологических параметров вибродуговой наплавки на производительность процесса и свойства наплавленного слоя.
|
I Краткие теоретические сведения
Вибродуговая наплавка является разновидностью дуговой наплавки плавящимся металлическим электродом. Этот метод отличается от автоматической дуговой наплавки тем, что конец электродной проволоки непрерывно вибрирует, в результате чего возникают периодически повторяющиеся электрические разряды, т.е. прерывисто горящая электрическая дуга.
|
Рис.6. Осциллограмма процесса вибродуговой
Наплавки
При правильно подобранных параметрах на осциллограмме вибродуговой наплавки видно, что процесс состоит из двух периодов (рис.6): короткого замыкания t к.з. и дугового разряда t д.р.. При коротком замыкании сила тока в цени возрастает, а напряжение падает до 1.5… 2.0 В. Вокруг обмоток источника тока и дросселя создается электрическое ноле. Электрод и деталь в месте контакта нагреваются. При отходе электрода от детали электромагнигное ноле начинает исчезать, пересекая обмотки. В них индуктируется электродвижущая сила самоиндукции, совпадающая по направлению с током источника питания.
Напряжение между электродом и деталью повышается до тех пор, пока не возникает дуговой разряд. В период дугового разряда накопленная энергия отделяется в виде дугового разряда и выделяется основное количество тепла (от 50 до 95% от общего количества). Металл электрода в виде мелких капель переносится в наплавочную ванну.
При неправильно подобранных параметрах процесса в результате дальнейшего отхода электрода может наступить период холостого хода, что нежелательно, так как в этот период тепло не выделяется и стабильность процесса ухудшается.
В зависимости от типа наплавочной головки электродная проволока совершает oт 20 до 110 колебаний в секунду. При длительности одного цикла 0.01 с длительность дугового разряда в зависимости от напряжения в сварочной цепи – 0.002… 0.0085 с.
|
С увеличением напряжения длительность дугового разряда увеличивается, и при напряжении выше 32 В дуга горит непрерывно (процесс переходит в непрерывный дуговой с вибрацией электрода).
Вибрация электрода дает возможность получить устойчивую дугу и наплавлять металл при низком напряжении источника тока в среде охлаждающей жидкости, при небольшой мощности в сварочной цепи, что снижает нагрев и деформацию деталей и позволяет выполнять наплавку тонких слоев от 0.5 до 3 мм на детали небольшого диаметра (D ³ 8 мм) и получать высокую твердость наплавленного слоя (до 62 HRC) без последующей термообработки.
Для защиты расплавленного металла при вибродуговой наплавке применяют жидкость, углекислый газ, флюс.
Жидкость (раствор щелочи или глицерина в воде) обеспечивает быстрое охлаждение детали, в результате чего деформация и размеры зоны термического влияния минимальны, а твердость и износостойкость наплавленного металла наиболее высокие.
Недостатком применения жидкости при вибродуговой наплавке является низкая усталостная прочность деталей, что связано с наличием пор, микротрещин и структурной неоднородностью наплавленного слоя.
Для ответственных деталей применяют флюс или углекислый газ с последующей обработкой для повышения усталостной прочности.
Принципиальная схема установки для вибродуговой наплавки представлена на рис. 7. Установка для вибродуговой наплавки состоит из наплавочной головки, вращателя, источника тока, оборудования для подвода жидкости, флюса или газа.
Рис.7. Принципиальная схема установки для Вибродуговой наплавки |
Наплавляемую деталь 9 закрепляют в центрах вращателя. На суппорте устанавливают изолированную от массы вибродуговую головку. К детали и токоподводящему мундштуку 12 подводят ток низкого напряжения (12… 20 В) от источника тока с жесткой вольт-амперной характеристикой.
Так как собственная индуктивность применяемых источников тока мала, то в цепь включают дополнительную индуктивность 7. При малой индуктивности запас энергии электромагнитного поля будет недостаточен, период дугового разряда уменьшается, появляется холостой ход, энергия магнитного поля выделяется быстро, что вызывает взрывообразное протекание дуговых разрядов и большие потери электродного металла.
|
При помощи роликов 8 электродную проволоку 6 подают через токоподводящий мундштук 12 к детали. Узел электромагнитного вибратора состоит из П-образного сердечника 1 с двумя параллельно соединенными катушками 2, которые питаются от источника переменного тока низкого напряжения (36 В). Сердечник электромагнита закреплен неподвижно.
Подвижной частью вибратора является якорь 3, жестко соединенный с рычагом 4, который может свободно поворачиваться относительно оси 5. К одному концу рычага прикреплен мундштук 6. Другое плечо рычага находится между двумя витыми пружинами, натяжением которых регулируется амплитуда вибрации рычага 4. При частоте тока 50 Гц создается вибрация конца электрода с частотой 100 колебаний в секунду.
Электромагнитный узел вибрации прост по конструкции, однако обладает некоторыми недостатками:
· в процессе работы нарушается жесткость витых пружин, меняется амплитуда вибрации и стабильность процесса наплавки;
· на стабильность процесса сильно влияет изменение напряжения питающей сети;
· в зазор между якорем и сердечником могут попадать брызги расплавленного металла;
· сильный шум от магнитного вибратора.
Наплавочные головки с механическим вибратором почти лишены этих недостатков, поэтому они получили наибольшее распространение.
Рассмотрим работу кинематической схемы привода головки с механическим вибратором системы МИИТа (рис. 8).
Рис.8. Кинематическая схема головки с механическим вибратором |
Механический привод находится внутри корпуса головки, он обеспечивает вибрацию токоподводящего мундштука, расположенного на рычаге 4 и подачу электродной проволоки 8 с помощью тянущих роликов 6 и 7. Привод осуществляется от одного электродвигателя постоянного тока 1 с максимальным числом оборотов до 2000 об / мин.
Обмотки возбуждения двигателя питаются постоянным током напряжением 26 В.
На выходном валу электродвигателя 1 находится кулачок 2, который прижимается к упорному ролику 3 пружиной 5. Число оборотов кулачка равно числу оборотов двигателя 1, т. е. 2000 об / мин. В этом случае число колебаний токоподводящего мундштука составляет 4000 в минуту.
|
С тянущими роликами 6 и 7 электродвигатель, связан с помощью двух червячных пар: z r1 и z k2; z r3 и z k4 с передаточным отношением каждом пары i = 20 / 1 и зубчатых колес z 5 и z 6 с i = 13 / 32.
Таким образом, число оборотов тянущего ролика:
(1)
При D p = 30 мм и пpи отсутствии скольжения скорость подачи проволоки V эл = 1.16 м / мин. Изменение скорости подачи проволоки и числа колебаний ее производится изменением числа оборотов электродвигателя 1.
Рассмотрим схему внешних соединений установки для вибродуговой наплавки (рис.9).
Рис.9. Схема внешних соединений установки для вибродуговой наплавки: I – вращатель, II – наплавочная головка, III – блок питания цепей управления, IV – источник питания, V – пульт управления
|
Вращатель 2 детали состоит из блока электродвигатель-редуктор 1. В качестве вращателя можно использовать токарный станок, после модернизации которого число оборотов шпинделя 3 должно быть от 1 до 10 об / мин, а перемещение суппорта 5 от 1.5 до 8 мм за один оборот шпинделя.
Деталь 4 зажимается в патроне шпинделя 3, а кронштейн 9 наплавочной головки II устанавливается па суппорте через изолирующую вставку 10. При помощи шарнира 8 корпус головки 7 может занимать любое положение. На кронштейне 11 крепится барабан с электродной проволокой.
По технике безопасности требуется, чтобы применялись низковольтные электродвигатели, поэтому в электрооборудование установки входит блок питания III, в котором имеется трансформатор, понижающий напряжение с 380 до 36 В, для питания электродвигателя вращателя и выпрямитель для получения постоянного тока напряжением 26 В для питания электродвигателя 6 головки.
В качестве источника питания дуги IV могут бытьиспользованы выпрямители ВДГ-302, ВДУ-305, имеющие жесткую вольт-амперную характеристику и регулируемое индуктивное сопротивление. Прямое назначение выпрямителя - сварка или наплавка в среде углекислого или инертного газа, но низкое напряжение (>15 В) позволяет использовать их и для вибродуговой наплавки.
Определенная последовательность включения электрооборудования установки осуществляется при помощи пульта управления V. На нем располагаются приборы (амперметр и вольтметр), потенциометр 12 для изменения числа оборотов электродвигателя 6 головки, магнитный пускатель 13 для включения и выключения процесса наплавки. К пульту управления подключается блок питания и источник тока для наплавки.
Наиболее высокие показатели получают при наплавке на обратной полярности, поэтому катод («минус») подсоединен к детали 4, через корпус вращателя, а анод («плюс») к электродной проволоке через корпус головки.
|
Режим вибродуговой наплавки выбирают в зависимости от толщины наплавленного слоя. Между основными параметрами вибродуговой наплавки существует определенная взаимосвязь (табл.4).
С увеличением напряжения возрастает длительность разрядов в каждом цикле вибрации и возрастает нагрев детали, а твердость слоя снижается.
Таблица 4
Износ, мм | Диаметр проволоки, мм d эл | Напряжение на дуге, В U д |
0.3 – 1.0 | 1.2 – 1.6 | 12 – 15 |
1.0 – 1.5 | 1.6 – 2.0 | 15 –20 |
1.5 – 2.5 | 2.0 – 2.5 | >20 |
Величину тока наплавки выбирают исходя из зависимости:
I н = j × F эл (2)
где j = 50… 75 А / мм 2, F эл - площадь поперечного сечения электродной проволоки, мм 2.
Скорость подачи электродной проволоки выбирают н зависимости от мощности дуги по формуле:
, м / мин (3)
где d эл - диаметр электрода, мм. Обычно V эл меняют в пределах 1… 2 м / мин, а скорость наплавки V нп = 0,3… 2,0 м / мин.
При выборе скорости наплавки детали следует учитывать, что отношение:
(4)
Чем больше диаметр проволоки, тем больше должно быть это отношение. Если это отношение очень мало, то под электродом проходит много холодного металла и проплавление ухудшается, а потери на разбрызгивание - возрастают. При слишком большом отношении повышается тепловое воздействие дуги на деталь, в результате чего также возрастают потери (y) и ухудшается сцепление с наплавляемым слоем.
При увеличении V нп высота наплавленного слоя h уменьшается, однако, учитывая, что соотношение (4) можно менять в небольших пределах, h регулируют главным образом за счет диаметра проволоки. Для расчета толщины наплавленного слоя пользуются формулой
, мм (5)
где S - шаг наплавки, мм / об; а - коэффициент, учитывающий условия формирования шва (а = 0,6… 0,7); К – коэффициент, учитывающий переход металла в наплавленный валик, равный 0.85.
Шаг наплавки S выбирается в зависимости or диаметра проволоки:
S = (1.6… 2.2) d эл (6)
При увеличении S возрастает твердость наплавленного слоя, улучшается сцепление с основным металлом, однако ухудшается шероховатость слоя, так как увеличиваются впадины между валиками.
При малых значениях S сплавление хуже, твердость наплавки ниже, больше потери на угap и разбрызгивание (y), возрастает толщина наплавленного слоя.
Амплитуду конца электродной проволоки выбирают в зависимости от диаметра проволоки:
А = (0.7… 1.3) d эл (7)
Расход и место подвода охлаждающей жидкости оказывают большое влияние на скорость охлаждения наплавленного металла и защиту его от действия воздуха. Этот фактор оказывает значительное влияние на структуру и твердость наплавленного металла.
|
|
Состав сооружений: решетки и песколовки: Решетки – это первое устройство в схеме очистных сооружений. Они представляют...
Биохимия спиртового брожения: Основу технологии получения пива составляет спиртовое брожение, - при котором сахар превращается...
Индивидуальные очистные сооружения: К классу индивидуальных очистных сооружений относят сооружения, пропускная способность которых...
Папиллярные узоры пальцев рук - маркер спортивных способностей: дерматоглифические признаки формируются на 3-5 месяце беременности, не изменяются в течение жизни...
© cyberpedia.su 2017-2024 - Не является автором материалов. Исключительное право сохранено за автором текста.
Если вы не хотите, чтобы данный материал был у нас на сайте, перейдите по ссылке: Нарушение авторских прав. Мы поможем в написании вашей работы!