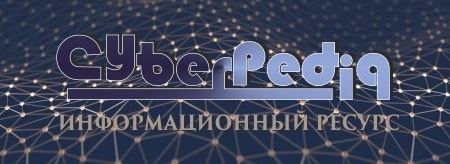
Особенности сооружения опор в сложных условиях: Сооружение ВЛ в районах с суровыми климатическими и тяжелыми геологическими условиями...
Архитектура электронного правительства: Единая архитектура – это методологический подход при создании системы управления государства, который строится...
Топ:
История развития методов оптимизации: теорема Куна-Таккера, метод Лагранжа, роль выпуклости в оптимизации...
Установка замедленного коксования: Чем выше температура и ниже давление, тем место разрыва углеродной цепи всё больше смещается к её концу и значительно возрастает...
Отражение на счетах бухгалтерского учета процесса приобретения: Процесс заготовления представляет систему экономических событий, включающих приобретение организацией у поставщиков сырья...
Интересное:
Инженерная защита территорий, зданий и сооружений от опасных геологических процессов: Изучение оползневых явлений, оценка устойчивости склонов и проектирование противооползневых сооружений — актуальнейшие задачи, стоящие перед отечественными...
Уполаживание и террасирование склонов: Если глубина оврага более 5 м необходимо устройство берм. Варианты использования оврагов для градостроительных целей...
Национальное богатство страны и его составляющие: для оценки элементов национального богатства используются...
Дисциплины:
![]() |
![]() |
5.00
из
|
Заказать работу |
|
|
Технически обоснованные нормы времени устанавливают на основе тщательного анализа и выявления всех производственных возможностей каждого цеха, участка, рабочего места и исследования составных частей данной операции.
При установлении технически обоснованных норм соблюдается следующая очередность работ:
– анализируют нормируемую операцию по ее структурным элементам;
– проектируют рациональный состав и содержание операции по элементам;
– проектируют наиболее рациональный технологический режим работы оборудования для данной операции;
проектируют регламент трудового процесса рабочего-исполнителя;
– рассчитывают норму времени на операцию по длительности отдельных элементов с учетом их рационального сочетания, возможности перекрытия, совмещения и т.д.;
– разрабатывают организационно-технические мероприятия, обеспечивающие внедрение спроектированной операции со всеми относящимися к ней режимами и приемами труда.
Основными методами установления технически обоснованных норм времени, базирующимися на анализе процесса, являются: аналитически-исследовательский, аналитически-расчетный, расчетно-сравнительный метод.
Аналитически-исследовательский метод основан на исследовании операции в производственных условиях и изучении затрат рабочего времени на ее выполнение при помощи хронометража и фотографии рабочего дня. Особое значение этот метод приобретает при изучении и обобщении передовых приемов труда, при разработке нормативов для установления технически обоснованных норм расчетным путем. При этом методе выполняют следующее: изучают процесс в конкретных условиях производства; анализируют и проектируют рациональную структуру операции; разрабатывают и внедряют мероприятия по совершенствованию организации труда на рабочем месте; рассчитывают и внедряют технически обоснованную норму времени.
|
Этот метод применяется при разработке и корректировании нормативов, а также для нормирования операций крупносерийного и массового производства, не охваченных системой нормативов.
При аналитически-расчетном методе длительность нормируемой операции находят расчетным путем, используя нормативы для определения затрат времени на отдельные ее элементы. При этом используют действующие дифференцированные нормативы для различных видов обработки по типам производства, укрупненные нормативы, номограммы, таблицы. Этот метод характерен для нормирования операций массового и крупносерийного и серийного производства.
При расчетно-сравнительном методе нормы устанавливают на основе сопоставления и расчета типовых операций, технологических процессов, а также организации труда и рабочих мест. Такие нормы времени, хотя и предусматривают поэлементный расчет, будут более укрупненными и менее точными, чем при расчете по описанным выше методам. Этот метод применяют в условиях мелкосерийного и единичного производства. Нормы времени в этом случае не являются технически обоснованными.
Хронометраж. Хронометраж технологической операции – способ изучения затрат времени на выполнение циклически повторяющихся ручных и машинно-ручных элементов операции. Он применяется для проектирования рациональной структуры операции, установления их нормативной продолжительности и разработки на этой основе нормативов, используемых при расчете технически обоснованных норм времени. Хронометраж применяется также для проверки норм, установленных расчетным путем, преимущественно в массовом и крупносерийном производстве. Кроме того, хронометражем пользуются при изучении передовых методов работы с целью их распространения.
|
Для проведения хронометража операцию расчленяют на нормируемые элементы: движение, приемы или их комплексы; определяют продолжительность их выполнения, проектируют рациональную структуру операции и рассчитывают нормальную продолжительность каждого элемента операции.
Хронометраж может быть сплошным и выборочным. При сплошном непрерывно измеряют все приемы операции в их технологической последовательности; при выборочном хронометраже за время выполнения операции измеряют лишь отдельные приемы независимо от их последовательности, но так, чтобы, в конечном счете, была определена продолжительность всех приемов операции.
Хронометраж состоит из следующих этапов:
а) подготовка к наблюдению;
б) наблюдение;
в) обработка хронометражных наблюдений;
г) анализ результатов, выводы, установление норм и проектирование нормативов оперативного времени.
Обычно хронометрируют работу передовых рабочих. Их предупреждают о цели наблюдения и инструктируют о порядке выполнения работы.
Подготовка к наблюдению заканчивается занесением в наблюдательный лист элементов изучаемой операции в их технологической последовательности и установлением фиксажных точек. Под фиксажной точкой подразумевается момент, в котором совпадают окончание последнего движения предыдущего приема (комплекса) с началом первого движения последующего приема операции. Установление фиксажных точек необходимо для правильного измерения продолжительности приемов.
В процессе наблюдения измеряют и фиксируют продолжительность каждого нормируемого элемента операции (движение, прием или комплекса приемов). Для измерения продолжительности применяют секундомеры, хронометрии специальные регистраторы времени (стрелочные и цифровые приборы), устройства нанесения информации на специальные бланки или перфоленту и киноаппаратуру. Длительность элементов операции определяют по текущему времени или по отдельным отсчетам. При записи по текущему времени в наблюдательный лист заносят данные, фиксирующие момент окончания первого и начала последующих элементов операции без остановки хронометра или секундомера. Продолжительность элементов операции, необходимую для получения хронометражных рядов, выявляют позднее, в процессе обработки данных хронометражного наблюдения.
|
При выборочном хронометрировании за время выполнения операции фиксируют продолжительность только отдельных нормируемых элементов. При этом секундомер или хронометр пускают в ход с началом данного элемента операции и выключают одновременно с ее окончанием.
Хронометражные наблюдения следует начинать при установившемся рациональном темпе работы, когда соблюдены все предусмотренные условия и освоены приемы труда.
Количество всех замеров хронометражного ряда должно быть достаточным для получения достоверного норматива.
Данные хронометража используют в виде первичного материала для разработки нормативов времени на вспомогательные и основные элементы операции и для расчета нормы на исследуемую операцию.
Организация оплаты труда
Заработная плата представляет собой часть общественного продукта, идущая на личное потребление рабочих и служащих и распределяемая в соответствии с количеством и качеством их труда.
Заработная плата регулируется следующим образом:
– планирование фондов заработной платы;
– установления дифференцированных норм оплаты труда для работников различных квалификаций и разных видов труда;
– определения конкретных форм и порядка оплаты труда разных групп работников в зависимости от организационно-технических и других условий работы.
В основе организации заработной платы лежит тарифная система, системы заработной платы рабочих, инженерно-технических работников и служащих; премиальные системы для различных категорий работников предприятия.
Тарифная система представляет собой совокупность нормативов, определяющих дифференциацию труда в зависимости от сложности труда и условий, форм заработной платы, отрасли производства и района страны. Основными элементами тарифной системы оплаты труда рабочих являются тарифные сетки, часовые ставки, тарифно-квалификационные справочники и районные коэффициенты к заработной плате. Тарифная система лежит в основе организации оплаты труда рабочих на предприятии. Рабочему присваивается определенный разряд в зависимости от уровня профессиональных знаний и трудовых навыков. Для установления разряда рабочим в цехах создаются специальные квалификационные комиссии.
|
Тарифная сетка – это шкала, с помощью которой дифференцируются все работы на группы (разряды) в зависимости от сложности труда, затрачиваемого на их выполнение. Для каждого разряда устанавливается коэффициент, определяющий соотношение в оплате труда данного разряда и первого (коэффициент квалификации).
Часовая тарифная ставка определяет размер оплаты труда рабочего соответствующего разряда за один час. Тарифная ставка первого разряда является основной, она задает уровень ставок в других разрядах.
Отношение часовой тарифной ставки соответствующего разряда к часовой ставке первого разряда называется тарифным коэффициентом. Разрыв в тарифных коэффициентах первого и шестого разрядов (диапазон тарифной сетки) в машиностроении составлял 1,71.
Часовые тарифные ставки дифференцированы по специальностям, а также по условиям выполнения работы (нормальные, тяжелые и вредные, особо тяжелые и особо вредные условия труда) и по системе оплаты труда (сдельная или повременная).
Месячная тарифная ставка рассчитывается путем умножения часовой ставки соответствующего разряда на число рабочих часов в месяц; дневная ставка на число рабочих часов в смену.
Система сдельной оплаты труда. Мерой количества труда выступает либо отработанное рабочим время, либо количество выработанной им продукции. Соответственно формы заработной платы могут быть повременными и сдельными. Сдельная форма оплаты может быть индивидуальной и коллективной (бригадной) и включать системы: прямую сдельную, сдельно-премиальную, прогрессивно-сдельную, косвенную сдельную и аккордную. Повременная форма применяется в виде простой повременной и повременно-премиальной систем.
Основной системой на машиностроительных предприятиях является прямая сдельная оплата. Заработная плата рабочего находится в прямой зависимости от количества выработанной им продукции (количества работы).
Применение сдельной оплаты труда экономически целесообразно при наличии количественных показателей выработки или работы в натуральных измерителях; при наличии возможностей для рабочего перевыполнить задание без изменения (и нарушения) технологического процесса; при рациональном обслуживании рабочих мест и полноценном использовании рабочего времени.
Сдельная расценка представляет собой оплату труда за единицу продукции, выплачиваемую рабочему независимо от фактически затраченного им на выполнение данной работы времени. Расценки пересматриваются одновременно с нормами времени выработки.
В зависимости от принятой на данном участке системы учета результатов работы (по отдельным рабочим, бригадам) применяют две разновидности прямой сдельной оплаты труда: индивидуальную и бригадную.
|
При прямой индивидуальной сдельной оплате рабочий получает оплату за все работы (количество продукции), выполненные им в течение отчетного периода по соответствующим расценкам без ограничений. Сдельная заработная плата рабочего за расчетный период может быть определена по формуле:
(3.11)
где m – число видов работ (деталеопераций), выполненных рабочим за расчётный период;
–фактическая выборка по каждому виду работ;
–расценка каждого вида работ.
При бригадной сдельной оплате труда устанавливают коллективные сдельные расценки на все виды работ.
(3.12)
где n – число членов бригады, чел;
li – тарифные ставки членов бригады, коп.;
tшк – норма времени, устанавливаемая на единицу выполняемой работы, ч.
Заработная плата всей бригады:
(3.13)
где – фактическая выработка продукции бригадой за расчётный период.
Тарифная заработная плата бригады за расчётный период:
, (3.14)
где Fi – время, отработанное каждым членом бригады за расчётный период.
Заработная плата La распределяется между членами бригады в соответствии с присвоенными им разрядами и отработанным временем.
Прогрессивно-сдельная система оплаты труда отличается от прямой сдельной. При ее применении устанавливаются дифференцированные расценки за работы, выполненные в пределах установленной нормы, или повышенные (например, полуторные и двойные расценки) за работы, выполненные сверх установленной месячной нормы выработки:
, (3.15)
где – повышенная расценка за продукцию, выполненную сверх нормы;
Nф i – фактическая выработка продукции одного рабочего за расчётный период;
Nвыр i – нормативная выработка продукции одного рабочего за расчётный период.
Эта система устанавливается в виде исключения в качестве временной оплаты труда на «узких» участках основного производства.
Косвенная сдельная система оплаты труда применяется для стимулирования производительности труда вспомогательных и обслуживающих рабочих. Для этого применяют косвенные расценки, устанавливаемые за единицу продукции, произведенной за расчетный период рабочими цеха или участка, которых обслуживают вспомогательные рабочие. По такой системе оплачиваются наладчики станков, транспортные рабочие, рабочие по дежурному обслуживанию в основных цехах и др.
Сдельная форма оплаты труда в сочетании с премированием образует сдельно-премиальную систему или аккордную.
Системы повременной оплаты труда. При повременной оплате труда мерой количества труда рабочего является только отработанное им время. Они применяются при аппаратурных процессах, при работе на конвейерных линиях, при выполнении работ, требующих большой тщательности (некоторые контрольные операции, экспериментальные работы).
Различают две системы повременной оплаты труда: простую повременную и повременно-премиальную. При простой повременной оплате труда заработная плата рабочего LП зависит от его квалификации (часовой тарифной ставки l ) и отработанного времени Тф т.е.:
. (3.16)
Материально она не побуждает рабочего к увеличению выработки, к повышению качества продукции, экономии материальных ресурсов. Чаще ее сочетают с дополнительными условиями и показателями премирования и применяют в виде повременно-премиальной системы.
Заработная плата при повременно-премиальной системе складывается из тарифной и премии, как правило, начисляемой в зависимости от тарифной заработной платы или от размера достигнутой экономии.
3.3.6 Общие рекомендации по использованию нормативов
Определение штучно-калькуляционного времени осуществляют с использованием сборника нормативных материалов для расчёта технически обоснованных норм времени на работы, выполняемые на металлообрабатывающем оборудовании в серийном производстве [11,12,13].
По указанным нормативам определяются все составляющие вспомогательного времени, время на обслуживание рабочего места (техническое и организационное, время перерывом на отдых и личные надобности) и подготовительно-заключительное время.
Основное время на выполнение всех не совмещённых рабочих переходов – То при выполнении всей операции определяется по формуле:
, (3.17)
где Toi – время выполнения i-го рабочего перехода;
m – количество несовмещенных рабочих переходов.
Основное время – То определяется при расчёте режимов резания, который выполнен на предшествующей лабораторной работе.
В нормативах предусмотрены два метода определения вспомогательного времени на операцию с различной степенью укрупнения норм в зависимости от вида применяемого оборудования и содержания выполняемой работы на технологической операции.
Первый метод. Для операций, выполняемых на универсальном оборудовании, предназначенном для выполнения нескольких рабочих переходов без замены инструмента (токарно-револьверные станки, вертикально-сверлильные станки с револьверной головкой), а также на станках за несколько рабочих переходов, требующих замену инструмента (токарно-винторезные, фрезерные), вспомогательное время определяется как сумма затрат на:
– установку и снятие детали;
– переустановку заготовки, (если это предусмотрено в операционной карте);
– времени на рабочий переход, определяемого для каждого рабочего перехода отдельно с учётом количества рабочих ходов;
– времени на изменение режимов обработки, смену инструмента и перемещения частей станка, на совмещение осей при растачивании, на выводы сверла при сверлении глубоких отверстий (для удаления стружки);
– времени на вспомогательные переходы, не вошедшее в укрупнённые комплексы (замену кондукторных втулок и др.);
– времени на контрольные измерения всех параметров, которые обеспечиваются на каждом рабочем переходе, (с учётом процента контролируемых деталей от обработанной партии деталей).
Второй метод. Для однопереходных операций, когда обработка производится без изменения технологических режимов обработки и смены инструмента, вспомогательное время дано на укрупнённый комплекс приёмов на операцию.
При выполнении лабораторной работы необходимо установить какие приёмы вошлив комплексы. Если для конкретной операции необходимы дополнительные действия рабочего, не учтённые в комплексах, то вспомогательное время на их выполнение устанавливается по нормативным таблицам и добавляется к комплексному вспомогательному времени.
Необходимо помнить о том, что в норму штучного времени включают только те составляющие вспомогательного времени, которые не перекрываются основным временем.
Пример. Обработка производится на горизонтально-фрезерном станке с использованием многоместного приспособления со сменной кассетой для установки заготовок. Время установки заготовок в сменную кассету перекрывается основным временем, в течении которого фрезеруется пакет деталей, ранее установленных и закреплённых в сменной кассете.
При определении вспомогательного времени на установку и закрепление одной заготовки необходимо время на установку и закрепление кассеты с деталями в приспособлении поделить на количество одновременно обрабатываемых деталей.
Время на установку заготовок в сменную кассету не учитывается, т.к. оно перекрывается основным временем.
Вспомогательное времени установку и снятие детали. Нормативное время на установку заготовки и снятие детали предусматривает следующие работы:
– установить и закрепить заготовку;
– включить станок (главное движение, движение подачи);
– выключить станок;
– очистить приспособление от стружки.
Если по технике безопасности допускается перемещение заготовки для последовательной обработки поверхностей детали без выключения вращения шпинделя, (последовательное сверление нескольких отверстий одного диаметра), то вспомогательное время необходимо уменьшать с указаниями, приведёнными в нормативах.
Вспомогательное время, связанное с переходом или обрабатываемой поверхностью. В нормативах эта составляющая вспомогательного времени дана по типам станков на укрупнённый комплекс приёмов, составленный по технологическим признакам и видам работ. В комплекс включены:
– подвод инструмента к заготовке;
– включение и выключение подачи;
– измерение детали при взятки пробных стружек (обработка по методу пробных проходов);
– отвод инструмента в исходное положение.
Во вспомогательное время связанное с переходом кроме затрат на комплекс приёмов включают дополнительные составляющие на приёмы, которые не вошли в комплекс (смена инструмента, смена кондукторных втулок, время на перемещение частей станка, если длина обработки превышает указанную в нормативах и др.).
Вспомогательное время на контрольные измерения обработанной детали. Устанавливается по нормативам на контрольные измерения после окончания обработки поверхности с учётом периодичности измерения, которая определяется при проектировании технологической операции.
При выполнении лабораторной работы следует принять, что 10÷15% деталей от всех обработанных на операции подлежит контролю оператором (станочником).
Время на контроль каждого из параметров, которые обеспечиваются на данной операции, устанавливается в зависимости от формы, размеров, точности и шероховатости обрабатываемой поверхности, а также вида средства измерения, а затем суммируется. В норму штучного времени (в общее вспомогательное время) включается, 10÷15% вспомогательного времени на контроль всех параметров (диаметра, длины, межосевого расстояния, шероховатости и т.п.).
Время на обслуживание рабочего места. Принимается в процентах от оперативного, процент выбирается по нормативам в зависимости от вида обработки и оборудования.
В укрупненных нормативах даётся процент для определения времени на обслуживания рабочего места, которое включает две составляющие:
– время технического обслуживания рабочего места, (смена затупившегося инструмента, правка шлифовального круга регулировки и подналадка станка в процессе работы, сметание и уборка стружки в процессе работы);
– время организационного обслуживания рабочего места (осмотри опробование в начале смены, уборка рабочего места в конце смены; получение инструктажа, раскладка инструмента в начале и уборка его в конце смены).
Время на отдых и личные надобности принимают в процентах от оперативного времени, которые устанавливаются по нормативам в зависимости от интенсивности и условий труда.
Подготовительно-заключительное время на обработку деталей партии запуска объёмом – n принимается для выполнения следующей работы:
– получение на рабочем месте наряда, технической документации, инструктажа;
– ознакомление с технической документацией;
– подготовка рабочего места, наладка оборудования, установка приспособлений и инструмента;
– пробная обработка деталей (пробной партии);
– демонтаж наладки после обработки партии запуска и сдача её в инструментальную кладовую.
При выборе подготовительно-заключительного времени необходимо учитывать условия организации труда, производится ли доставка приспособлений, инструмента на рабочее место вспомогательным рабочим или самим наладчиком. В последнем случае необходимо включить дополнительную составляющую в нормируемое подготовительно-заключительное время.
В норму полного штучного времени (штучно-калькуляционного) включается часть подготовительно-заключительного времени, приходящаяся на одну деталь партии запуска. Объём партии запуска можно определить по формуле:
, шт. (3.18)
где Nгод – годовой объём выпуска деталей данного наименования в штуках, можно принять Nгод = 2000 шт, если объём не был задан;
а – количество дней, на которые необходимо обеспечить запас деталей на сборки, можно принять дней;
Fр.в – действительный годовой фонд рабочего времени, рабочих дней.
Практическая часть
Исходные данные для выполнения практического занятия
Для выполнения работы у студента должно быть исходная информация следующего содержания:
- наименование технологической операции;
- модель станка;
- вид заготовки;
- масса заготовки;
- материал заготовки;
- размеры, точность размеров, шероховатость обрабатываемой поверхности;
- тип станочного приспособления для установки заготовки, вид зажимного механизма этого приспособления;
- количество и содержание рабочих переходов в структуре операции;
- вид обрабатывающего инструмента на каждом рабочем переходе;
- вид контрольно-измерительных средств, применяемых на операции и объем контроля в процентах от обработанной партии деталей;
- основное время выполнения рабочих переходов, входящих в структуру операции;
- возможное совмещение рабочих или рабочих и вспомогательных переходов;
- тип производства, годовой объем выпуска.
Перечисленная информация содержится в операционной технологической карте и карте эскизов, которые оформляются на предыдущих лабораторных работах или выдаются преподавателем на специальном бланке задания. Все исходные данные должны быть представлены в виде таблицы (таблица 3.1).
3.4.2 Порядок выполнения задания
1) Заполнить таблицу 3.1 исходными данными.
2) Установить по нормативам и занести в расчетный лист полученную информацию (таблица 3.2) [11,12,13,14].
3) Рассчитать составляющие штучно-калькуляционного времени и полную технически обоснованную норму времени выполнения технологической операции. Все расчеты представить в отчёте, результаты занести в таблицу 3.2.
4) Установить квалификацию рабочего-оператора и разряд выполняемых работ [15].
5) Дать рекомендации по сокращению штучного времени на выполнение технической операции.
Таблица 3.1 – Исходные данные для расчёта нормы времени
№ п/п | Наименование | Исходная информация | |||||||
1 | Наименование детали |
| |||||||
2 | Вид исходной заготовки | (отливка, пруток, предварительно обработанная с припуском и др.) | |||||||
3 | Обрабатываемый материал | (марка, ГОСТ, σв, НВ) | |||||||
4 | Масса заготовки |
| |||||||
5 | Наименование операции | (номер, наименование) | |||||||
6 | Тип и модель станка |
| |||||||
7 | Обрабатывающий инструмент | Рабочий переход* | 1 |
| |||||
2 |
| ||||||||
8 | Приспособление для закрепления заготовки
(Тип, наименование) | Количество одновременно закрепляемых заготовок |
| ||||||
Наличие сменной кассеты | Вид зажимного устройства | ||||||||
|
| ||||||||
9 | Контрольно- измерительные средства | Контролируемый параметр | Контрольно-измерительное средство | Процент контроля. | |||||
123 | _____________________ | ______________________________ | _________________________________ | ||||||
10** | Оснастка для закрепления инструмента | Комбинированные державки |
| ||||||
Многошпиндельная головка | Кол-во шпинделей | ||||||||
Револьверная сверлильная головка | Кол-во шпинделей | ||||||||
| |||||||||
*Для операций, состоящих из нескольких рабочих переходов, выполняемых различным инструментом.
** Для операций, на которых используется многошпиндельные, револьверные головки или комбинированные державки
Таблица 3.2 – Расчётный лист
Операционный эскиз | Объём партии запуска, шт.: | |||||||||||||
(с указанием схемы базирования и закрепления, положения обрабатывающего инструмента в начале и конце рабочего хода) | Подготовительно-заключительное время, мин: | |||||||||||||
Время на обслуживание рабочих меств % от оперативного,мин.: | ||||||||||||||
Основное время на операцию, мин.: | ||||||||||||||
Оперативное время, мин.: | ||||||||||||||
Квалификация рабочего.: | ||||||||||||||
Разряд работ.: | ||||||||||||||
Полное штучное время на операцию.: | ||||||||||||||
Содержаниевспомогательных рабочих переходов, дополнительных действий рабочего в порядке их выполнения | Составляющие вспомогательного (не перекрываемого) времени, мин | |||||||||||||
Установка и снятие детали | Связанное с переходом | Дополнительные перемещения частей стола | Смена | Смена | Изменение | Контрольные измерения | Наодну | Примечание | ||||||
Подачи | Число оборотов | |||||||||||||
Пример заполнения | ||||||||||||||
1 | Установить, закрепить (снять) заготовку | Х |
| Х | ||||||||||
2 | Сверлить отверстие Ø12,7Н12 на проход, выдержав размеры 10±0,2, 20±0,2 | Х |
| Х |
| |||||||||
3 | Сменить инструмент |
| Х | Х | ||||||||||
4 | Сменить кондукторную втулку |
| Х | Х | ||||||||||
5 | Сменить подачу |
| Х | Х | ||||||||||
6 | Зенкеровать отверстие Ø13Н11, выдержав размеры10±0,2 и 20±0,2 | Х |
| Х | ||||||||||
7 | Контролировать размеры |
| Одного параметра | Всех параметров | Времянаконтроль одной | |||||||||
Ø13Н11, |
| Х |
| |||||||||||
10±0,2 |
| Х | ||||||||||||
20±0,2 |
| Х | ||||||||||||
Полное вспомогательное время на операцию | Х | |||||||||||||
3.4.3 Порядок оформления отчета
Отчет должен включать:
- описание исходных данных (таблица 3.1, операционная карта);
- эскиз обработки заготовки (операционный эскиз);
- описание методики определения нормы времени с приведением аналитических зависимостей, используемых при расчетах;
- таблицу 3.2 с содержанием элементов технологической операции и времени выполнения каждого элемента (или комплекса элементов);
- расчет нормы времени – Тшт, полной нормы времени – Тш.к;
- определение квалификации рабочего;
- рекомендации по снижению затрат времени на операцию;
3.4.4 Контрольные вопросы
1) Какова цель технического нормирования?
2) Назовите задачи, решаемые при техническом нормировании.
3) Назовите методы технического нормирования, в каких случаях они применяемы?
4) Назовите структурные составляющие штучного времени.
5) Назовите структурные составляющие штучно-калькуляционного времени. В каких случаях оно нормируется?
6) Как устанавливаются значения составляющих штучного времени?
7) На какие действия нормируется подготовительно-заключительное время?
8) Дайте понятие определения «партия запуска».
9) Как определить заработную плату рабочего-станочника за выполненную операцию?
10) Какие формы оплаты труда используют на предприятии?
Какие нормативные материалы используются при нормировании?
11) Назовите пути сокращения затрат времени на операцию.
4 Практическое занятие №4. Определение припусков и промежуточных технологических размеров
Цель занятия
Целью работы является:
- закрепление и углубление знаний в области определения промежуточных технологических размеров и размеров исходной заготовки;
- приобретение практических навыков работы со справочными и нормативно- техническими документами.
Содержание занятия
Определение параметров качества заготовки. Определение составляющих припуска для каждого рабочего перехода по таблицам среднеэкономической точности. Расчет минимальных, номинальных, максимальных припусков, номинальных значений промежуточных технологических размеров.
Теоретическая часть
4.3.1 Цель определения припусков на механическую обработку деталей на металлорежущих станках
Для выбранного метода получения заготовки по справочным таблицам можно установить размерную точность заготовки, отклонения формы (коробление, смещение, кривизну и др.), шероховатость ее поверхностей.
Выполнив сравнительный анализ качества поверхностей и точности размеров заготовки и детали (по рабочему чертежу), можно установить те поверхности заготовки, которые подлежат дополнительной обработке.
Дополнительная обработка поверхности может осуществляться на одной или нескольких технологических операциях за один или несколько рабочих переходов, т.е. каждая поверхность детали проходит несколько ступеней обработки.
Первой ступенью обработки является заготовительная операция, ей присваивают индекс 1. При проектировании технологического процесса важно установить количество ступеней обработки – m, а также величину уточнения – K ут i , которая обеспечивается на каждой ступени обработки и определяется по формуле:
|
|
Типы оградительных сооружений в морском порту: По расположению оградительных сооружений в плане различают волноломы, обе оконечности...
Автоматическое растормаживание колес: Тормозные устройства колес предназначены для уменьшения длины пробега и улучшения маневрирования ВС при...
Историки об Елизавете Петровне: Елизавета попала между двумя встречными культурными течениями, воспитывалась среди новых европейских веяний и преданий...
Механическое удерживание земляных масс: Механическое удерживание земляных масс на склоне обеспечивают контрфорсными сооружениями различных конструкций...
© cyberpedia.su 2017-2024 - Не является автором материалов. Исключительное право сохранено за автором текста.
Если вы не хотите, чтобы данный материал был у нас на сайте, перейдите по ссылке: Нарушение авторских прав. Мы поможем в написании вашей работы!