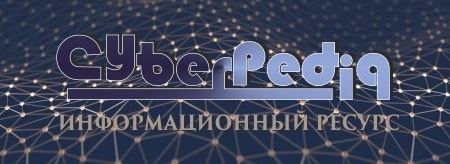
Таксономические единицы (категории) растений: Каждая система классификации состоит из определённых соподчиненных друг другу...
История создания датчика движения: Первый прибор для обнаружения движения был изобретен немецким физиком Генрихом Герцем...
Топ:
Определение места расположения распределительного центра: Фирма реализует продукцию на рынках сбыта и имеет постоянных поставщиков в разных регионах. Увеличение объема продаж...
Проблема типологии научных революций: Глобальные научные революции и типы научной рациональности...
Интересное:
Принципы управления денежными потоками: одним из методов контроля за состоянием денежной наличности является...
Подходы к решению темы фильма: Существует три основных типа исторического фильма, имеющих между собой много общего...
Влияние предпринимательской среды на эффективное функционирование предприятия: Предпринимательская среда – это совокупность внешних и внутренних факторов, оказывающих влияние на функционирование фирмы...
Дисциплины:
![]() |
![]() |
5.00
из
|
Заказать работу |
|
|
3.2.1. Методы образования поверхностей деталей при обработке
На металлорежущих станках
Тела деталей машин ограничены геометрическими поверхностями, образованными при обработке. Это в основном плоскости, круговые и некруговые цилиндры и конусы, линейчатые и сферические поверхности. Все они имеют определенные протяженность и относительное положение. Реальные поверхности детали, полученные в результате обработки на станках, отличаются от идеальных геометрических поверхностей.
Поверхности обрабатываемых деталей можно рассматривать как непрерывное множество последовательных положений (следов) движущейся производящей линии, называемой образующей, по другой производящей линии, называемой направляющей. Например, для получения плоскости необходимо образующую прямую 1 перемещать по направляющей прямой 2 (рис.8, а). Цилиндрическая поверхность может быть получена при перемещении образующей прямой 1 по направляющей – окружности 3 (рис.8, б) или при движении образующей окружности 3 вдоль направляющей прямой 1 (рис.8, в). Рабочую поверхность зуба цилиндрического колеса можно получить, если образующую – эвольвенту 4 передвигать вдоль направляющей 1 (рис.8, г) или, наоборот, образующую прямую 1 передвигать по направляющей – эвольвенте 4 (рис.8, д).
Рис.8. Схемы образования поверхностей деталей
Большинство поверхностей деталей машин может быть образовано при использовании в качестве производящих линий прямой, окружности, эвольвенты, винтовой и ряда других линий. В реальных условиях обработки производящие линии воспроизводятся комбинацией согласованных между собой вращательных и прямолинейных перемещений инструмента и заготовки. Существуют четыре метода образования производящих линий: копирования, огибания, следа и касания.
|
Метод копирования основан на том, что режущая кромка инструмента по форме совпадает с производящей линией. Например, при получении цилиндрической поверхности (рис.9, a) образующая линия 1 воспроизводится копированием прямолинейной кромки инструмента, а направляющая линия 2 – вращением заготовки.
Рис.9. Методы воспроизводства образующих линий
На рис.9, б показан пример обработки зубьев цилиндрического колеса. Контур режущей кромки фрезы совпадает с профилем впадин и воспроизводит образующую линию. Направляющая линия получается при прямолинейном движении заготовки вдоль своей оси. Здесь необходимы два формообразующих движения: вращение фрезы и прямолинейное перемещение заготовки. Кроме того, для обработки последующих впадин заготовка должна периодически поворачиваться на угол, соответствующий шагу зацепления. Такое движение называют делительным.
Метод огибания (обката) основан на том, что образующая линия возникает в форме огибающей ряда положений режущей кромки инструмента в результате его движений относительно заготовки. Режущая кромка отличается по форме от образующей линии и при различных положениях инструмента является касательной к ней. На рис.9, в показана схема обработки зубьев цилиндрического колеса по методу огибания. Режущая кромка инструмента имеет форму зуба зубчатой рейки. Если заготовке сообщить вращение и согласованное с ним прямолинейное перемещение рейки вдоль ее оси, то режущий контур инструмента в своем движении относительно заготовки будет иметь множество положений. Ихогибающей явится образующая зуба колеса. Направляющая линия по предыдущему образуется в результате прямолинейного перемещения инструмента или заготовки вдоль оси колеса. Для рассматриваемого случая требуются три формообразующих движения: вращение заготовки, перемещение инструмента вдоль своей оси, перемещение инструмента или заготовки вдоль оси зубчатого колеса.
|
Метод следа состоит в том, что образующая линия получается как след движения точки – вершины режущего инструмента. Например, при точении образующая 1 (рис.9, г) возникает как след точки А – вершины резца, а при сверлении (рис.9, д) – как след сверла. Инструмент и заготовка перемещаются относительно друг друга таким образом, что вершина А режущего инструмента все время касается образующей линии 1. В первом случае (рис.9, г) направляющая линия получается в результате вращения заготовки, во втором случае (рис.9, д) – при вращении сверла или заготовки. В обоих случаях требуются два формообразующих движения.
Метод касания основан на том, что образующая линия 1 является касательной к ряду геометрических вспомогательных линий 3, образованных реальной точкой движущейся режущей кромки инструмента (рис.9, е).
Итак, образование различных поверхностей сводится к установлению таких формообразующих движений заготовки и инструмента, которые воспроизводят образующие и направляющие линии.
Классификация движений
Звенья, несущие заготовку и инструмент, называют рабочими или вспомогательными. В процессе обработки они совершают согласованные движения, называемые также рабочими или исполнительными. По назначению исполнительные движения разделяют на формообразующие, установочные и делительные. Установочные движения необходимы для того, чтобы привести инструмент и заготовку в положение, обеспечивающее снятие припуска и получение заданного размера. Установочное движение, при котором происходит резание, называют движением врезания (например, рис.9, а), а движение, при котором резания не происходит, называют наладочным движением. Примером наладочного движения может служить перемещение стола координатно-сверлильного станка с заготовкой после обработки одного отверстия в новое положение (на новую координату) для сверления последующих отверстий в этой заготовке.
Делительное движение осуществляется для поворота установленной на станке заготовки на заданный угол. Предназначенные для этого механизмы представляют собой либо отдельную делительную головку, либо часть конструкции станка или приспособления. Деление может быть прерывным и непрерывным. В первом случае (рис.9, б) оно совершается периодически. Заготовка поворачивается вокруг своей оси после окончания обработки очередной впадины. Во втором случае делительное движение продолжается в течение времени, которое необходимо для перемещения инструмента по заготовке (рис.9, в). Данный метод применяют при обработке зубчатых колес, шлицевых валов и т.п. деталей. Метод обеспечивает высокую точность, а непрерывность процесса – высокую производительность.
|
Рабочие движения инструмента и заготовки в процессе резания принято делить на главное движение и движение подачи. Главным называют движение, которое обеспечивает отделение стружки от заготовки с определенной скоростью резания. Движением подачи называют такое движение, которое позволяет подвести под кромку инструмента новые участки заготовки и тем обеспечить снятие стружки со всей обрабатываемой поверхности. Указанные рабочие движения могут быть вращательными и прямолинейными; их могут совершать как заготовка, так и инструмент.
Рабочие движения являются формообразующими движениями. Если для формообразования требуется одно движение, то оно будет главным (например, вращение заготовки, рис.9, а). При необходимости двух формообразующих движений одно будет главным, а другое – движением подачи (рис.9, б, г, д, е). Если формообразующих движений больше двух, то одно из них будет главным, а остальные – движениями подачи.
Кроме рабочих движений для обработки деталей на станках необходимы вспомогательные движения, которые в процессе резания не участвуют. К их числу относятся движения, связанные с установкой и закреплением заготовки, подводом и отводом инструмента, включением и выключением приводов, а также движения, осуществляющие автоматическую установку и снятие инструмента, его правку, транспортирование заготовок, активный контроль размеров, реверсирование и др.
Основные понятия о приводе
Совокупность устройств, приводящих в действие рабочие органы металлорежущих станков, называют приводом. Он состоит из двигателя и механизмов, передающих движение рабочим органам. Для приводов металлорежущих станков применяют обычно односкоростные асинхронные электродвигатели переменного тока с короткозамкнутым ротором, с синхронной частотой вращения 3000, 1500, 1000 и 750мин-1. Обладая жесткой характеристикой, эти двигатели обеспечивают постоянство мощности во всем диапазоне скоростей и незначительное изменение частоты вращения вала под нагрузкой. Используют также многоскоростные двигатели переменного тока и, в частности, двухскоростные – 1500/3000, 750/1500 мин-1, трехскоростные – 1000/1500/3000 мин-1 и др.
|
При электрическом регулировании частоты вращения находят применение двигатели постоянного тока с тиристорным управлением, которые позволяют регулировать частоту вращения валов в диапазоне порядка 10:1. Включение переборов с электромагнитными муфтами дает возможность еще более расширить этот диапазон. В станках с числовым программным управлением применяют шаговые двигатели, быстродействие которых достигает 8 кГц и выше.
|
|
Индивидуальные очистные сооружения: К классу индивидуальных очистных сооружений относят сооружения, пропускная способность которых...
Поперечные профили набережных и береговой полосы: На городских территориях берегоукрепление проектируют с учетом технических и экономических требований, но особое значение придают эстетическим...
Особенности сооружения опор в сложных условиях: Сооружение ВЛ в районах с суровыми климатическими и тяжелыми геологическими условиями...
Двойное оплодотворение у цветковых растений: Оплодотворение - это процесс слияния мужской и женской половых клеток с образованием зиготы...
© cyberpedia.su 2017-2024 - Не является автором материалов. Исключительное право сохранено за автором текста.
Если вы не хотите, чтобы данный материал был у нас на сайте, перейдите по ссылке: Нарушение авторских прав. Мы поможем в написании вашей работы!