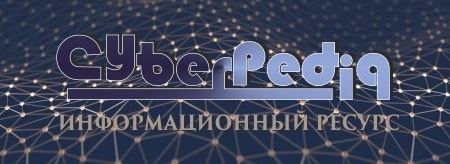
Историки об Елизавете Петровне: Елизавета попала между двумя встречными культурными течениями, воспитывалась среди новых европейских веяний и преданий...
Двойное оплодотворение у цветковых растений: Оплодотворение - это процесс слияния мужской и женской половых клеток с образованием зиготы...
Топ:
Марксистская теория происхождения государства: По мнению Маркса и Энгельса, в основе развития общества, происходящих в нем изменений лежит...
Отражение на счетах бухгалтерского учета процесса приобретения: Процесс заготовления представляет систему экономических событий, включающих приобретение организацией у поставщиков сырья...
Выпускная квалификационная работа: Основная часть ВКР, как правило, состоит из двух-трех глав, каждая из которых, в свою очередь...
Интересное:
Уполаживание и террасирование склонов: Если глубина оврага более 5 м необходимо устройство берм. Варианты использования оврагов для градостроительных целей...
Средства для ингаляционного наркоза: Наркоз наступает в результате вдыхания (ингаляции) средств, которое осуществляют или с помощью маски...
Аура как энергетическое поле: многослойную ауру человека можно представить себе подобным...
Дисциплины:
![]() |
![]() |
5.00
из
|
Заказать работу |
|
|
Введение
Дисперсные минеральные добавки рекомендуются вводить в бетон и бетонные смеси для достижения следующих основных целей:
- Обеспечение экономии цемента, повышение однородности, связанности, удобоукладываемости бетонной смеси и обеспечения специальных свойств. - Обеспечение специальных свойств бетона - сульфатостойкости, жаростойкости, водостойкости, сопротивляемости щёлочной коррозии, уменьшение тепловыделении; снижение стоимости бетона.
Эффективность действия минеральных добавок зависит от их водопотребности и активности, состава бетона, наличия пластификатора, условий выдерживания и режима ТВО. Эффективность возрастает со снижением класса бетона по прочности, а также при переходе от подвижных к жестким смесям и при использовании песков с повышенной пустотностью. Эффективность применения конкретных видов добавок следует устанавливать опытным путем в процентах подбора состава бетона.
Характеристика некоторых видов добавок
Доменные шлаки
Одним из важнейших компонентов шлаковых цементов является доменный шлак, получаемый при выплавке чугуна; так как в исходной железной руде содержатся глинистые примеси и в коксе — зола, для их удаления в доменную шихту вводят флюсы — карбонаты кальция и магния. В процессе плавки, вступая в химическое взаимодействие с примесями, они образуют шлак, представляющий собой силикатный и алюмосиликатный расплав. Плотность доменных шлаков в два с лишним раза меньше, чем чугуна, поэтому шлаки в горне домны располагаются над слоем расплавленного чугуна и их периодически удаляют через отдельную шлаковую летку. Небольшая часть шлака, захватываемая расплавленным чугуном, также периодически выпускается, но уже через чугунную летку. На 1 т выплавляемого чугуна приходится примерно 0,6—1 т шлака. Основные оксидные составляющие шлака те же, что и у портландцементного клинкера, по соотношения между ними другие. Шлаки в зависимости от агрегата, в котором происходит переплавка того или иного чугуна на сталь, называются шлаками бессемеровского или мартеновского чугуна; шлаки специальных чугунов разделяются на фер-рохромовые, ферромаргапцевые и др. Чугуны разделяются на литейные, передельные и специальные. Каждому виду чугуна соответствует шлак определенного состава; при высоком содержании серы в коксе повышают содержание извести в шлаке; для ускорения процесса плавки в состав шихты вводят марганцевую руду, доломит и др., что влияет на химический состав шлака. Обычно шлак выпускается из домны с температурой 1673—1773 К, при которой он становится жидкотекучим и минимально вязким. Возможность использования шлака для цемента зависит от характера его переработки по выходе из домны. При медленном охлаждении на воздухе в шлаковых отвалах он превращается в плотный камень, причем в зависимости от состава он может постепенно рассыпаться в порошок вследствие так называемого силикатного распада в результате перехода |3-C2S в Y-QS. Распад может вызываться и гидратацией CaS, FeS и MnS (известковый, железный и марганцевый). Нерассыпающиеся медленно охлажденные шлаки дробят и в кусках применяют в дорожном и других видах строительства; для проверки стойкости шлаков во времени используют специальные методы контроля.
|
Зола-унос
Зола-уноса (далее — зола) представляет собой тонкодисперсный материал, состоящий, как правило, из частичек размером от долей микрона до 0,14 мм. Зола образуются в результате сжигания твердого топлива на ТЭС, и улавливается электрофильтрами, после чего в сухом состоянии отбирается с помощью золоотборника на производственные нужды, либо вместе с водой и шлаком отправляется на золоотвал.
|
Строение и состав золы зависит от целого комплекса одновременно действующих факторов: вида и морфологических особенностей сжигаемого топлива, тонкости помола в процессе его подготовки, зольности топлива, химического состава минеральной части топлива, температуры в зоне горения, времени пребывания частиц в этой зоне и др. При значительном содержании карбонатов в минеральной части исходного топлива под воздействием высоких температур в процессе горения образуются силикаты, алюминаты и ферриты кальция – минералы, способные к гидратации. Такие золы при затворении водой способны к схватыванию и самостоятельному твердению. В них, как правило, содержатся окись кальция и окись магния в свободном состоянии.
В соответствии с ГОСТ 25818-91 все золы по виду сжигаемого угля подразделяют на:
- антрацитовые, образующиеся при сжигании антрацита, полуантрацита и тощего каменного угля (А);
- каменноугольные, образующиеся при сжигании каменного, кроме тощего, угля (КУ);
- буроугольные, образующиеся при сжигании бурого угля (Б).
В зависимости от химического состава золы подразделяют на типы:
кислые (К) — антрацитовые, каменноугольные и буроугольные, содержащие оксид кальция до 10 %;
основные (О) — буроугольные, содержащие оксид кальция более 10 % по массе.
Золы в зависимости от качественных показателей подразделяют на 4 вида:
I — для железобетонных конструкций и изделий из тяжелого и легкого бетонов;
II — для бетонных конструкций и изделий из тяжелого и легкого бетонов, строительных растворов;
III — для изделий и конструкций из ячеистого бетона;
IV — для бетонных и железобетонных изделий и конструкций, работающих в особо тяжелых условиях (гидротехнические сооружения, дороги, аэродромы и др.).
Таблица 2. Увеличение водопотребности бетонной смеси, приведение различных минеральных добавок
добавки | Расход добавки, кг/м3 | Увеличение водопотребности бетонной смеси при расходе цемента, кг/м3 | ||
<200 | 200-300 | >300 | ||
доменные и электротермофосфорные шлаки | <100 100-200 200-300 | 0 0-5 5-10 | 0-5 5-10 10-20 | 5-10 10-20 20-35 |
топливные золы и гранулированные топливные шлаки | <100 100-200 200-300 | 0 0-10 5-20 | 0-5 5-20 15-40 | 5-15 10-30 – |
|
Состав бетона
Номер состава | Расходы компонентов, кг | Ц/В | Плотности, кг/м3 | ||||
Ц | В | Д | Щ | П | |||
0 | 305 | 195 | – | 1215 | 675 | 1,56 | 2390 |
1 | 238,82 | 205 | 200 | 1215 | 528,54 | 1,16 | 2387,36 |
2 | 240 | 220 | 225 | 1215 | 531 | 1,09 | 2431 |
3 | 226,73 | 225 | 250 | 1215 | 501,78 | 1,01 | 2418,51 |
Применяем расход добавки N1 по таблице 1
Д1= 200 кг/м3 Расход воды определяем по таблице 2
В1= В0+ ∆В
В0 – расход воды бетонной смеси без добавки
1. ∆В – увеличение бетонной смеси за счёт введения добавки В1=195+10=205 л/м3 Рассчитывает расход цемента
Ц0, П0 – расход цемента и песка в составе без добавки
Ц1, Д1 – расход цемента и добавки в составе с добавкой
Расход крупного заполнителя в составе с добавкой принимают такие же как и бездобавочных бетонов Щ1=Щ0 Щ1=1215 кг/м3 Расход мелкого заполнителя определяют по формуле
Определение цементно-водное отношение
(Ц/В)1 = Ц1/В1=238,82/205=1,16
Рассчитанные в пунктах 2-6 начальный состав бетона с добавкой проверяют на опытном замесе для уточнения и корректировки удобоукладываемости бетонной смеси.
Таким образом для опытного замеса используется следующий состав(N1)
Ц1=238,82 кг/м3; В1=205 л/м3 ; Д1= 200 кг/м3 ; Щ1= 1215 кг/м3; П1=528,54
Дополнительные составы бетона с добавкой определяют назначая расходы добавки равные границам диапазонов приведённых в таблице 1, рассчитывая и корректируя составы бетона соотвецтвенно с пунктами 2-7.
1. Применяем ещё один расхода добавки 150 кг аналогичным путём рассчитываем начальные составы бетона(N3) и осуществляем их корректировку. Д1= 250 кг/м3. Расход воды определяем по таблице 2
В1= В0+ ∆В
В0 – расход воды бетонной смеси без добавки
2. ∆В – увеличение бетонной смеси за счёт введения добавки
В1=195+30=225 л/м3
Рассчитывает расход цемента
Ц0, П0 – расход цемента и песка в составе без добавки
Ц1, Д1 – расход цемента и добавки в составе с добавкой
Расход крупного заполнителя в составе с добавкой принимают такие же как и бездобавочных бетонов Щ1=Щ0 Щ1=1215 кг/м3
Расход мелкого заполнителя определяют по формуле
Определение цементно-водное отношение
|
(Ц/В)1 = Ц1/В1=226,73/225=1,01
Рассчитанные в пунктах 2-6 начальный состав бетона с добавкой проверяют на опытном замесе для уточнения и корректировки удобоукладываемости бетонной смеси.
Таким образом для опытного замеса используется следующий состав(N1)
Ц1=226,73 кг/м3; В1=225 л/м3 ; Д1= 250 кг/м3 ; Щ1= 1215 кг/м3; П1=501,78 кг/м3
Готовим опытный замес из готовой смеси состава № 2 объём 10 литров и проверяем жесткость бетонной смеси составляет 5 сек. соответствует заданному значению.
Определяем плотность смеси опытным путём, её величина составляет 2350 кг/м3 , а расчетное равно 2431 принимаем расчётную. Корректируем расходы компонентов с учётом фактической плотности бетонной смеси и фактических материалов на замес.
Определяем плотность смеси опытным путём, её величина составляет 2350кг/м3 , а расчетное равно 2387,36 принимаем расчётную. Корректируем расходы компонентов с учётом фактической плотности бетонной смеси и фактических материалов на замес.
Определяем плотность смеси опытным путём, её величина составляет 2350 кг/м3 , а расчетное равно 2418,51 принимаем расчётную. Корректируем расходы компонентов с учётом фактической плотности бетонной смеси и фактических материалов на замес.
№ сост. | Расход компонентов | Жёсткость смеси | Ц/В | Плотность, кг/м3 | ||||
Ц | В | П | Щ | Д | ||||
0 | 305 | 195 | 675 | 1215 | – | 5 | 1,56 | 2390 |
1 | 235 | 202 | 520 | 1196 | 197 | 5 | 1,16 | 2350 |
2 | 232 | 213 | 513 | 1174 | 218 | 5 | 1,09 | 2350 |
3 | 220 | 219 | 488 | 1181 | 243 | 5 | 1,00 | 2351 |
Дополнительные составы рассчитывают принимая для них значение Ц/В отличаются на ±0,4 исходного расчётного значения соответствующих начальных составов.
При определение водопотребности в этих составах пользуются уточненнымии данными при приготовлении смесей составов 1–3.
Из бетона № 2 формуем опытные образцы. После этого подвергаем пропариванию по заданному режиму испытания образцов через четыре часа и 28 суток нормального твердения после пропаривания сводим в таблицы и строим зависимости. По критерию минимального расхода цемента применяем состав с оптимальным расходом добавки, цемента, воды и цементно-водного отношения.
Состав 1
1. Расход минеральной добавки состава N1 применяем с пунктом 1 первой части. Д1= 200 кг/м3
2. Ц/В в начальном составе
Ц/В=1,25
Расход воды в начальном составе применяем по рисунку 1 В1= В0+ ∆В
В0 – расход воды бетонной смеси без добавки
∆В – увеличение бетонной смеси за счёт введения добавки
В1=195+10=205 л/м3
3. Расход цемента
Ц = Ц/В×В1 = 1,25×205=256,25 кг/м3
4. Абсолютный объём заполнителя рассчитывают
м3
1. Расход писка определяем при доли писка r принятой по таблице 3
|
П=Vзап*r*ρп=695,27*0,555*2,05=791,04 кг/м3
2. Расход щебня
Щ=Vзап*(1-r)*ρщ=695,27*(1-0,555)*2,62=810,6 кг/м3
Состав 3
1. Расход минеральной добавки состава N3 применяем с пунктом 1 первой части. Д1=250 кг/м3
2. Ц/В в начальном составе
Ц/В=1,25
Расход воды в начальном составе применяем по рисунку 1
В1= В0+ ∆В
В0 – расход воды бетонной смеси без добавки
∆В – увеличение бетонной смеси за счёт введения добавки
В1=195+30=225 л/м3
3. Расход цемента
Ц = Ц/В×В1 = 1,25×225=281,25 кг/м3
Абсолютный объём заполнителя рассчитывают
Расход песка определяем при доли писка r принятой по таблице 3
3. П=Vзап*r*ρп=667,2*0,555*2,05=759,1 кг/м3
Расход щебня
4. Щ=Vзап*(1-r)*ρщ=667,2*(1-0,555)*2,62=777,9 кг/м3
Номер состава | Расходы компонентов, кг | Ц/В | Плотности, кг/м3 | ||||
Ц | В | Д | Щ | П | |||
1 | 256,25 | 205 | 200 | 810,6 | 791,04 | 1,25 | 2263 |
2 | 275 | 220 | 225 | 786,05 | 767,07 | 1,25 | 2273 |
3 | 281,25 | 225 | 250 | 777,9 | 759,1 | 1,25 | 2293 |
Введение
Дисперсные минеральные добавки рекомендуются вводить в бетон и бетонные смеси для достижения следующих основных целей:
- Обеспечение экономии цемента, повышение однородности, связанности, удобоукладываемости бетонной смеси и обеспечения специальных свойств. - Обеспечение специальных свойств бетона - сульфатостойкости, жаростойкости, водостойкости, сопротивляемости щёлочной коррозии, уменьшение тепловыделении; снижение стоимости бетона.
Эффективность действия минеральных добавок зависит от их водопотребности и активности, состава бетона, наличия пластификатора, условий выдерживания и режима ТВО. Эффективность возрастает со снижением класса бетона по прочности, а также при переходе от подвижных к жестким смесям и при использовании песков с повышенной пустотностью. Эффективность применения конкретных видов добавок следует устанавливать опытным путем в процентах подбора состава бетона.
Характеристика некоторых видов добавок
Доменные шлаки
Одним из важнейших компонентов шлаковых цементов является доменный шлак, получаемый при выплавке чугуна; так как в исходной железной руде содержатся глинистые примеси и в коксе — зола, для их удаления в доменную шихту вводят флюсы — карбонаты кальция и магния. В процессе плавки, вступая в химическое взаимодействие с примесями, они образуют шлак, представляющий собой силикатный и алюмосиликатный расплав. Плотность доменных шлаков в два с лишним раза меньше, чем чугуна, поэтому шлаки в горне домны располагаются над слоем расплавленного чугуна и их периодически удаляют через отдельную шлаковую летку. Небольшая часть шлака, захватываемая расплавленным чугуном, также периодически выпускается, но уже через чугунную летку. На 1 т выплавляемого чугуна приходится примерно 0,6—1 т шлака. Основные оксидные составляющие шлака те же, что и у портландцементного клинкера, по соотношения между ними другие. Шлаки в зависимости от агрегата, в котором происходит переплавка того или иного чугуна на сталь, называются шлаками бессемеровского или мартеновского чугуна; шлаки специальных чугунов разделяются на фер-рохромовые, ферромаргапцевые и др. Чугуны разделяются на литейные, передельные и специальные. Каждому виду чугуна соответствует шлак определенного состава; при высоком содержании серы в коксе повышают содержание извести в шлаке; для ускорения процесса плавки в состав шихты вводят марганцевую руду, доломит и др., что влияет на химический состав шлака. Обычно шлак выпускается из домны с температурой 1673—1773 К, при которой он становится жидкотекучим и минимально вязким. Возможность использования шлака для цемента зависит от характера его переработки по выходе из домны. При медленном охлаждении на воздухе в шлаковых отвалах он превращается в плотный камень, причем в зависимости от состава он может постепенно рассыпаться в порошок вследствие так называемого силикатного распада в результате перехода |3-C2S в Y-QS. Распад может вызываться и гидратацией CaS, FeS и MnS (известковый, железный и марганцевый). Нерассыпающиеся медленно охлажденные шлаки дробят и в кусках применяют в дорожном и других видах строительства; для проверки стойкости шлаков во времени используют специальные методы контроля.
Зола-унос
Зола-уноса (далее — зола) представляет собой тонкодисперсный материал, состоящий, как правило, из частичек размером от долей микрона до 0,14 мм. Зола образуются в результате сжигания твердого топлива на ТЭС, и улавливается электрофильтрами, после чего в сухом состоянии отбирается с помощью золоотборника на производственные нужды, либо вместе с водой и шлаком отправляется на золоотвал.
Строение и состав золы зависит от целого комплекса одновременно действующих факторов: вида и морфологических особенностей сжигаемого топлива, тонкости помола в процессе его подготовки, зольности топлива, химического состава минеральной части топлива, температуры в зоне горения, времени пребывания частиц в этой зоне и др. При значительном содержании карбонатов в минеральной части исходного топлива под воздействием высоких температур в процессе горения образуются силикаты, алюминаты и ферриты кальция – минералы, способные к гидратации. Такие золы при затворении водой способны к схватыванию и самостоятельному твердению. В них, как правило, содержатся окись кальция и окись магния в свободном состоянии.
В соответствии с ГОСТ 25818-91 все золы по виду сжигаемого угля подразделяют на:
- антрацитовые, образующиеся при сжигании антрацита, полуантрацита и тощего каменного угля (А);
- каменноугольные, образующиеся при сжигании каменного, кроме тощего, угля (КУ);
- буроугольные, образующиеся при сжигании бурого угля (Б).
В зависимости от химического состава золы подразделяют на типы:
кислые (К) — антрацитовые, каменноугольные и буроугольные, содержащие оксид кальция до 10 %;
основные (О) — буроугольные, содержащие оксид кальция более 10 % по массе.
Золы в зависимости от качественных показателей подразделяют на 4 вида:
I — для железобетонных конструкций и изделий из тяжелого и легкого бетонов;
II — для бетонных конструкций и изделий из тяжелого и легкого бетонов, строительных растворов;
III — для изделий и конструкций из ячеистого бетона;
IV — для бетонных и железобетонных изделий и конструкций, работающих в особо тяжелых условиях (гидротехнические сооружения, дороги, аэродромы и др.).
|
|
Индивидуальные очистные сооружения: К классу индивидуальных очистных сооружений относят сооружения, пропускная способность которых...
Кормораздатчик мобильный электрифицированный: схема и процесс работы устройства...
Особенности сооружения опор в сложных условиях: Сооружение ВЛ в районах с суровыми климатическими и тяжелыми геологическими условиями...
История развития хранилищ для нефти: Первые склады нефти появились в XVII веке. Они представляли собой землянные ямы-амбара глубиной 4…5 м...
© cyberpedia.su 2017-2024 - Не является автором материалов. Исключительное право сохранено за автором текста.
Если вы не хотите, чтобы данный материал был у нас на сайте, перейдите по ссылке: Нарушение авторских прав. Мы поможем в написании вашей работы!