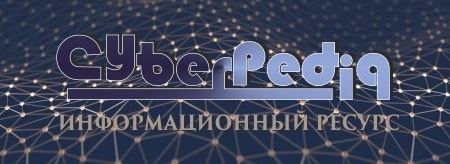
Папиллярные узоры пальцев рук - маркер спортивных способностей: дерматоглифические признаки формируются на 3-5 месяце беременности, не изменяются в течение жизни...
Археология об основании Рима: Новые раскопки проясняют и такой острый дискуссионный вопрос, как дата самого возникновения Рима...
Топ:
Оснащения врачебно-сестринской бригады.
Определение места расположения распределительного центра: Фирма реализует продукцию на рынках сбыта и имеет постоянных поставщиков в разных регионах. Увеличение объема продаж...
Процедура выполнения команд. Рабочий цикл процессора: Функционирование процессора в основном состоит из повторяющихся рабочих циклов, каждый из которых соответствует...
Интересное:
Аура как энергетическое поле: многослойную ауру человека можно представить себе подобным...
Как мы говорим и как мы слушаем: общение можно сравнить с огромным зонтиком, под которым скрыто все...
Отражение на счетах бухгалтерского учета процесса приобретения: Процесс заготовления представляет систему экономических событий, включающих приобретение организацией у поставщиков сырья...
Дисциплины:
![]() |
![]() |
5.00
из
|
Заказать работу |
|
|
· Токарная обработка – вид обработки резанием, при котором главным движением является вращательное движение заготовки, а движением подачи является поступательное движение резца на заготовку.
· Фрезерная обработка – вид обработки резанием, при котором главным движением является вращательное движение фрезы, а движением подачи является поступательное движение заготовки на фрезу.
· Строгание – вид обработки резанием, при котором главным движением является прямое поступательное движение резца (обратное является холостым), а движением подачи является движение заготовки перпендикулярно резцу, совершаемое в конце холостого хода.
· Сверление – вид обработки резанием, при котором главным движением является вращательное движение сверла, а движением подачи является поступательное движение сверла на заготовку.
· Протягивание – вид обработки резанием, при котором главным движением является поступательное движение протяжки, а движение подачи отсутствует (хотя подача есть).
Приведенные выше виды обработки резанием осуществляются лезвийным инструментом.
· Шлифование – вид обработки резанием, при котором главным движением является вращательное движение шлифовального круга, а движениями подачи являются: поступательное движение круга на заготовку, поступательное и вращательное движения заготовки.
Шлифование производится абразивным инструментом, то есть инструментом, который режет не лезвиями, а частицами абразивных материалов, закрепленными в материале инструмента.
1. Черновая – при черновой обработке срезается бо̀льшая часть припуска, форма заготовки приближается к форме будущей детали. После черновой обработки требуется доведение заготовки до необходимой точности.
|
2. Чистовая – при чистовой обработке удаляется остаток припуска, заготовка превращается в деталь заданной формы и размеров. Во многих случаях достигается и заданная шероховатость поверхности. Чистовой обработке всегда предшествует черновая.
3. Отделочная – при отделочной обработке шероховатость поверхности доводится до требуемых значений. Размеры детали при этом не должны выходить за допуски.
Инструментальные материалы
5. Режущий инструмент в процессе резания металлов подвергается большому давлению срезаемого слоя и нагреву, что вызывает его износ. Поэтому основным требованием к материалам режущих инструментов является износоустойчивость при высокой температуре нагрева в течение продолжительного времени. Это требование обеспечивается большой твердостью материала в нагретом состоянии и его красностойкостью.
6. В настоящее время в машиностроении для изготовления режущих инструментов применяют инструментальные углеродистые, легированные и быстрорежущие стали. Кроме перечисленных сталей, применяют также пластины твердых металлокерамических и минералокерамических материалов.
7. Инструментальные углеродистые стали в настоящее время имеют ограниченное применение вследствие низкой красностойкости. Инструменты из этой стали хотя и имеют твердость после термообработки HRC 60 — 63, но при нагреве до 200 — 250°С твердость резко падает и инструмент тупится.
8. Из инструментальной углеродистой стали марок У10А, У12А изготовляют режущие инструменты, работающие с малыми скоростями резания (V ≤ 10 м/мин), например напильники, ножовочные полотна, метчики, плашки и т. д.
9. Инструментальные легированные стали отличаются от углеродистых инструментальных сталей тем, что в них введены легирующие металлы: хром, вольфрам, молибден, ванадий, никель и др. Эти стали содержат 0,85 ÷1,5%С. Они после закалки имеют твердость HRC 62 — 64, обладают высокой вязкостью и высокими механическими качествами σпч = 160 — 170 кГ/мм2. Однако их красностойкость не превышает 350 — 400°С, поэтому эти стали применяют при изготовлении режущих инструментов для обработки металлов (отбеленный чугун, нагартованную сталь и т. п.) при малых и умеренных скоростях резания (примерно в 1,2 ÷ 1,5 раза больших, чем при работе инструментами, изготовленными из инструментальной углеродистой стали). Легированная хромокремнистая сталь 9ХС и особенно хромовольфрамовые марок ХВГ и 9ХВГ мало деформируются при закалке, что очень важно приизготовлении таких сложных режущих инструментов, как протяжки, длинные развертки, метчики, сверла, фрезы и т. п.
|
10. Быстрорежущие стали — это хромовольфрамовые стали с содержанием вольфрама от 8,5 до 19% и от 3,8 до 4,4% хрома. Режущий инструмент из быстрорежущих сталей имеет после термообработки твердость HRC 62 — 65, повышенную сопротивляемость износу и сохраняет режущие свойства при нагреве до 600 — 650°С. Это позволяет работать инструментом, изготовленным из быстрорежущей стали со скоростями, в 2 — 4 раза большими, чем инструментами, изготовленными из инструментальной углеродистой стали.
11. В настоящее время широко применяют быстрорежущие стали марок Р9 и Р18 с содержанием вольфрама в среднем соответственно 9 и 18%. Кроме этих основных марок, при обработке жаропрочных и других сплавов применяют кобальтовые и ванадиевые инструментальные быстрорежущие стали марок Р9Ф5, Р14Ф4, Р18Ф2, Р8К5, Р9К10, Р10К5Ф5, Р18К5Ф2.
12. В приведенных марках буква Р обозначает вольфрам, буква Ф — ванадий, буква К — кобальт, а следующие за буквой цифры обозначают содержание данного металла в процентах. Например, марка стали Р10К5Ф5 содержит десять процентов вольфрама, пять процентов кобальта и пять процентов ванадия.
13. Твердые сплавы представляют раствор карбидов вольфрама и карбидов титана в металлическом кобальте. Их изготовляют в виде пластин необходимой формы путем спекания при температуре около 1900°С. Получающиеся пластины обладают очень высокой твердостью HRC 88 — 92, большой износостойкостью и красностойкостью (900 — 1000°С). Пластины твердых сплавов припаивают или механически крепят специальными прижимами к корпусу (державке) из конструкционной или инструментальной углеродистой стали (У7А, У8А).
|
14. Режущие инструменты с пластинами из твердых сплавов применяют для обработки самых твердых металлов, включая закаленную сталь и неметаллические материалы (стекло, фарфор, пластмассы) при скоростях резания в 3 — 4 раза больше, чем скорость обработки инструментом из быстрорежущей стали.В настоящее время заводы твердых сплавов выпускают две основные группы этих сплавов: вольфрамовая группа, основные марки которой ВК2, ВКЗ, ВК4, ВК6, ВК6М, ВК8, ВК8В, и титановольфрамовая с основными марками Т5К10, Т5К12В, Т14К8, Т15К6, Т30К4 и Т60К6, и тантало-титановольфрамовая ТТ7К12. Твердые сплавы группы ВК предназначены для обработки чугуна и других твердых, хрупких металлов и неметаллических материалов; сплавы группы ТК предназначаются для обработки сталей.
15. Во всех приведенных марках твердых сплавов цифры после буквы К обозначают содержание кобальта в процентах, а цифры после буквы Т — содержание карбида титана в процентах; остальное до 100% — карбиды вольфрама. Например, твердый сплав ВК6 содержит 6% кобальта и 94% карбидов вольфрама; сплав Т60К6 — 60% карбида титана, 6% кобальта и 34% карбида вольфрама.Среди перечисленных марок твердых сплавов марки ВК4, ВК6М и ВК8В включены в ГОСТ в 1958 г. Они предназначаются для обработки резанием металлов и неметаллических материалов и по ряду свойств — твердости, эксплуатационной прочности и износоустойчивости — превосходят некоторые старые марки твердых сплавов (ВКЗ, ВК6, ВК8).
16. Минералокерамический материал для изготовления пластин к режущим инструментам состоит из окиси алюминия (Аl2Оз) и получается методом прессования с последующей термообработкой. Минералокерамические пластины крепят механически к металлическим державкам или же припаивают их, предварительно подвергая металлизации. В промышленности применяют минералокерамические пластины марок Т-48 и ЦМ-332. Эти материалы, обладая очень большой твердостью (HRC 91 — 93) и красностойкостью 1200ºС, позволяют обрабатывать металлы резанием со скоростью до 2000 м/мин, т. е. превышающую скорость резания твердыми сплавами в 1,5 — 2 раза. Но существенным недостатком минерало-керамического материала является высокая хрупкость, препятствующая его широкому внедрению в промышленность.
|
17. Наиболее эффективно минералокерамические материалы используют для режущего инструмента при получистовой и чистовой обработке сталей, чугуна и цветных металлов в условиях безударной нагрузки.
18.
Абразивные материалы
Большое место в современном производстве деталей машин занимают процессы шлифования, при которых используются различные абразивные инструменты. Режущими элементами этих инструментов служат твердые и теплоустойчивые зерна абразивного материала с острыми кромками.
Абразивные материалы подразделяются на естественные и искусственные. К естественным абразивным материалам относятся такие минералы, как кварц, наждак, корунд и др. Естественные абразивные материалы отличаются большой неоднородностью, наличием посторонних примесей. Поэтому по качеству абразивных свойств они не удовлетворяют растущие потребности промышленности.
В настоящее время обработка искусственными абразивными материалами занимает ведущее место в машиностроении.
Наиболее распространенными искусственными абразивными материалами являются электрокорунды, карбиды кремния и бора.
Электрокорунд получают электрической плавкой материалов, богатых окисью алюминия, например из боксита или глинозема в смеси с восстановителем (антрацитом или коксом). Электрокорунд выпускается следующих разновидностей нормальный — Э, белый — ЭБ, монокорунд— М, хромистый — ЭХ, титанистый — ЭТ. Электрокорунд нормальный в зависимости от содержания окиси алюминия подразделяется на несколько марок
Электрокорунд Э1 32 ЭЗ Э4
Содержание Аl2О3, % 91 92 93 94
С увеличением содержания Аl2О3 повышается качество и возрастает абразивная способность электрокорунда. В настоящее время производство электрокорунда марок Э1, Э2, ЭЗ почти прекращено. Зерна электрокорунда наряду с высокой твердостью и механической прочностью имеют значительную вязкость, необходимую при выполнении работ с переменными нагрузками при больших давлениях.
Электрокорунд нормальный применяют для обработки различных материалов повышенной прочности, в частности, конструкционных и углеродистых сталей в незакаленном и закаленном состоянии.
Электрокорунд белый Э8 и Э9 содержит окись алюминия в количестве не менее 97%, имеет белый или светло-розовый цвет.
В настоящее время в основном выпускается электрокорунд белый марки Э9 с содержанием Аl2О3 99% и выше.
По особой технологии промышленность выпускает электрокорунд белый марки Э9А повышенного качества, который применяется для изготовления инструментов класса А.
Электрокорунд белый может быть использован для тех же материалов, что и электрокорунд нормальный. Однако из-за высокой стоимости его применяют для ответственных работ при шлифовании углеродистых и быстрорежущих сталей в закаленном состоянии и легированных сталей в незакаленном и закаленном состоянии.
|
Монокорунд марок М8 и М7 содержит 98% и 97% Аl2О3. Главная особенность монокорунда состоит в том, что он получается непосредственно в виде зерна, имеющего высокую механическую прочность, острые кромки и вершины с более выраженным свойством самозатачивания по сравнению с электрокорундом. Это обеспечивает ему повышенные режущие свойства. Однако с повышением размеров зерен монокорунда его структура ухудшается и прочность снижается.
Монокорунд предпочтителен для шлифования труднообрабатываемых жаропрочных, кислотоупорных, легированных сталей и сплавов.
Электрокорунд хромистый (технический рубин) содержит не менее 97% Аl2О3 и 0,4—1,2% Cr2О3. Зерна электрокорунда хромистого имеют розовую или темно-вишневую окраску. Они обладают большим постоянством физико-механических свойств и содержат больший процент монокристаллов по сравнению с электрокорундом белым. Рекомендуется применять электрокорунд хромистый для шлифования изделий из углеродистых и конструкционных сталей круглого сечения при интенсивных режимах. Применять этот материал для обработки вязких сталей нецелесообразно.
Электрокорунд титанистый (технический сапфир) с присадкой окиси титана близок к электрокорунду нормальному, но отличается от него большим постоянством свойств и увеличенной вязкостью. Это позволяет применять его в условиях тяжелых и неравномерных нагрузок и для прецизионных работ.
Карбид кремния получается в результате взаимодействия кремнезема и углерода в электрических печах, а затем дробления на зерна. Он состоит из карбида кремния SiC и незначительного количества примесей. Наиболее распространены две разновидности карбида кремния зеленый (КЗ), имеющий цвет от светло-зеленого до темно-зеленого, и черный (КЧ) — обычно черного или, темно-синего цвета. Карбид кремния выпускается следующих марок К39, К38, К37, К36, КЧ8, КЧ7. Цифры в. маркировке означают содержание SiС в. процентах. Например, К39 означает карбид кремния зеленый с содержанием 99% SiС; КЧ8 — означает карбид кремния черный с содержанием 98% SiС. Карбид кремния зеленый отличается от карбида кремния черного меньшим, количеством примесей. Карбид кремния обладает большой твердостью, превосходящей твердость электрокорунда, высокой механической прочностью и режущей способностью.
Карбид кремния является незаменимым материалом для шлифования чугуна, цветных металлов, стекла, пластмасс и других хрупких материалов. Зеленый карбид кремния обладает большей твердостью, но меньшей прочностью по сравнению с черным карбидом кремния. Это и определяет некоторое превосходство зеленого карбида кремния над черным при обработке твердых сплавов.
Карбид бора В4С обладает высокой твердостью, высокой износоустойчивостью и абразивной способностью. Вместе с тем карбид бора очень хрупок, что и определяет его применение в промышленности в виде порошков и паст для доводки твердосплавных режущих инструментов, фильер из твердых сплавов, шлифования камней из искусственного рубина, агата и т. п.
Абразивные материалы характеризуются такими основными свойствами, как форма абразивных зерен, зернистость, твердость, механическая прочность, абразивная способность зерен.
По форме абразивные зерна могут быть изометричные, пластинчатые и мечевидные. Изометричные зерна имеют округлую симметричную форму, а зерна пластинчатые и мечевидные имеют ярко выраженную несимметричную форму. Основной формой абразивных зерен является изометричная. Однако при увеличении количества изометричных зерен шлифовальный инструмент требует больших усилий при резании; он получается с более плотной упаковкой зерен, т.е. с меньшей пористостью, что ухудшает режущую способность. Поэтому изометричную форму абразивных зерен нельзя считать оптимальной во всех случаях. Изометричные зерна предпочтительны для инструментов, работающих при обдирочных режимах с тяжелой переменной нагрузкой в условиях больших давлений на инструмент.
Зерна пластинчатые и мечевидные, обладающие большей способностью скалывания, самозатачивания, более целесообразны при чистовых операциях и обработке труднообрабатываемых материалов.
Абразивные зерна имеют определенную округленность своих режущих элементов. Установлено, что при уменьшении размеров абразивных зерен соответственно уменьшаются как радиусы округлений, так и углы при вершине их режущих элементов. Уменьшение размеров зерен влияет на процесс снятия тонких стружек и способствует получению более чистой обработанной поверхности. Зерна из электрокорунда имеют радиусы округлений от 4 до 180 мкм. Зерна из карбида кремния имеют, как правило, меньшие радиусы округлений.
Абразивные материалы по величине зерна подразделяются на шлифзерно (200, 160, 125, 100, 80, 63, 50, 40, 32,25, 20, 16), шлифпорошки (12, 10, 8, 5, 4, 3) и микрошлифпорошки (М40, М28, М20, М14, М10, М7, М5).
Зернистость шлифзерна и шлифпорошков определяется размерами сторон ячеек контрольных сит. Например, номер зернистости 16 обозначает, что зерна этой зернистости проходят через сито с ячейками размером стороны 200 мкм и не проходят через сито с ячейками размером сторон 160 мкм.
Размеры зерен микрошлифпорошков определяются по линейным размерам зерен в микрометрах. Так, для микрошлифпорошка М40 пределы размеров зерен основной фракции равны 40—28 мкм.
Твердость абразивных материалов характеризуется сопротивлением зерен поверхностному измельчению, местному воздействию приложенных сил. Она должна быть выше твердости обрабатываемого материала. Твердость абразивных материалов определяется методом царапания острия одного тела по поверхности другого и методом вдавливания алмазной пирамиды под малой нагрузкой в абразивное зерно. При методе царапания более твердым будет тело, способное сделать царапину у менее твердого тела. Этот метод не достаточно точный, чтобы определить твердость абразивного материала. Поэтому несомненный интерес представляет испытание микротвердости абразивов на приборе ПМТ-3. На этом приборе определяют отношение силы вдавливания пирамиды к площади отпечатка. Как показывают испытания, с повышением температуры микротвердость абразивных материалов снижается.
Механическая прочность характеризуется дробимостью зерен под влиянием внешних усилий.
Абразивные зерна должны быть достаточно прочными, чтобы выдержать без разрушения давления резания, когда кромки еще достаточно остры, и допускать откалывание от них кусочков лишь тогда, когда кромки в должной мере затупятся.
Оценку прочности производят раздавливанием навески абразивных зерен в стальной форме под прессом с помощью определенной статической нагрузки. Показателем прочности служит процентное весовое количество зерен, не просеивающихся через сито, с которого была взята навеска. О прочности единичных зерен судят по величине нагрузки, разрушающей зерно, взятой как среднее из 100 испытаний.
При обдирочных режимах с большим съемом металла требуются прочные абразивы, а при чистовом шлифовании и обработке труднообрабатываемых материалов предпочтительны абразивы с большей хрупкостью и способностью к самозатачиванию. Абразивная способность характеризуется количеством материала, сошлифованного испытываемыми зернами за определенный промежуток времени. Определенное количество испытываемых зерен насыпается между двумя вращающимися с небольшой скоростью дисками.
В порядке снижения абразивной способности и твердости абразивные материалы располагаются в следующей последовательности карбид бора, карбид кремния, монокорунд, электрокорунд.
Токарная обработка
|
|
Таксономические единицы (категории) растений: Каждая система классификации состоит из определённых соподчиненных друг другу...
Типы сооружений для обработки осадков: Септиками называются сооружения, в которых одновременно происходят осветление сточной жидкости...
Индивидуальные и групповые автопоилки: для животных. Схемы и конструкции...
Археология об основании Рима: Новые раскопки проясняют и такой острый дискуссионный вопрос, как дата самого возникновения Рима...
© cyberpedia.su 2017-2024 - Не является автором материалов. Исключительное право сохранено за автором текста.
Если вы не хотите, чтобы данный материал был у нас на сайте, перейдите по ссылке: Нарушение авторских прав. Мы поможем в написании вашей работы!