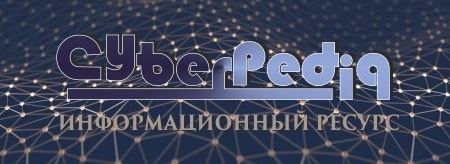
Таксономические единицы (категории) растений: Каждая система классификации состоит из определённых соподчиненных друг другу...
Автоматическое растормаживание колес: Тормозные устройства колес предназначены для уменьшения длины пробега и улучшения маневрирования ВС при...
Топ:
Техника безопасности при работе на пароконвектомате: К обслуживанию пароконвектомата допускаются лица, прошедшие технический минимум по эксплуатации оборудования...
Особенности труда и отдыха в условиях низких температур: К работам при низких температурах на открытом воздухе и в не отапливаемых помещениях допускаются лица не моложе 18 лет, прошедшие...
Когда производится ограждение поезда, остановившегося на перегоне: Во всех случаях немедленно должно быть ограждено место препятствия для движения поездов на смежном пути двухпутного...
Интересное:
Лечение прогрессирующих форм рака: Одним из наиболее важных достижений экспериментальной химиотерапии опухолей, начатой в 60-х и реализованной в 70-х годах, является...
Средства для ингаляционного наркоза: Наркоз наступает в результате вдыхания (ингаляции) средств, которое осуществляют или с помощью маски...
Подходы к решению темы фильма: Существует три основных типа исторического фильма, имеющих между собой много общего...
Дисциплины:
![]() |
![]() |
5.00
из
|
Заказать работу |
|
|
Прокатка (ротационное обжатие вращающимися валками)
Прокатка(горячий процесс) – способ обработки давлением, заключающийся в пластической деформации заготовки во вращающихся валках прокатных станов. В большинстве случаев горячая.
S – направление движения заготовки
n – направление вращения валков
Свободная ковка (сжатие между плоскостями инструмента)
Свободная ковка(горячий процесс) – способ обработки давлением, заключающийся в свободном пластическом течении металла заготовки при сжатии её между бойками молота или пресса. Свободной ковкой обрабатываются заготовки любого размера и массы. Выполняется только в горячую.
P – направление приложения силы
n – направление движения верхнего бойка
Горячая объемная штамповка (затекание металла в полость инструмента)
Горячая объемная штамповка – способ обработки давлением, при котором металл заготовки затекает в полость штампа, называемую ручьем, принимая его форму. Течение металла ограничивается поверхностями полостей штампа. Горячей объемной штамповкой обрабатываются детали массой до нескольких сотен килограммов.
Холодная листовая штамповка
Холодная листовая штамповка(холодный процесс) – способ обработки давлением, заключающийся в пластической деформации листовой заготовки при вдавливании её пуансоном в полость матрицы. Прижимное кольцо препятствует возникновению складок на фланце заготовки.
P – направление действия силы
Прессование (выдавливание металла)
Прессование (горячий процесс)– способ обработки давлением, заключающийся в выдавливании металла заготовки пресс-шайбой, движущейся под действием пуансона, из замкнутого объема пресс-цилиндра через отверстие матрицы.
P – направление действия силы
|
Волочение
Волочение – способ обработки давлением, заключающийся в протягивании заготовки через отверстие специальной матрицы, называемой волокой (очаг деформации). Для получения отверстия применяется оправка, устанавливаемая в отверстии матрицы.
В процессе деформации пара движущихся дислокаций порождает сотни и сотни новых, в результате этого плотность дислокаций повышается, что и приводит к упрочнению (повышению предела прочности) - рис.4.
Упрочнение металла под действием пластической деформации называется наклепом, или нагартовкой.
Пластическая деформация вносит существенные изменения в строение металла. Кристаллическая структура пластически деформированного металла характеризуется не только искажением кристаллической решетки, но и определенной ориентировкой зерен - текстурой.
Беспорядочно ориентированные кристаллы под действием деформации поворачиваются осями наибольшей прочности вдоль направления деформации (рис.5).
С увеличением деформации степень текстурованности возрастает и при больших степенях деформации достигает 100%, т.е. все зерна оказываются одинаково ориентированными.
Не следует думать, что в результате деформации зерно измельчается. В действительности оно только деформируется, сплющивается и из равноосного превращается в неравноосное (в виде лепешки, блина), сохраняя ту же площадь поперечного сечения.
Сущность наклепа металла
Металлы и их сплавы имеют кристаллическую структуру и состоят из большого количества зерен. Эти зерна имеют неправильную форму и различные размеры. В каждом зерне атомы упорядочены, но смежные зерна по-разному ориентированы относительно друг друга. В процессе холодной деформации структура зерен меняется за счет их фрагментации зерен, движения атомов и искажения атомной решетки. Подробнее об этом см. Физическая сущность наклепа.
Когда материал подвергается механическому нагружению, в его кристаллической структуре образуются микроскопические дефекты, которые известны как дислокации. Если нагрузки продолжают увеличиваться, эти дислокации начинают продвигаться и взаимодействовать между собой. Таким образом они образуют новую внутреннюю структуру, которая сопротивляется дальнейшей пластической деформации. Эта структура повышает предел текучести материала, то есть его способность сопротивляться прилагаемым усилиям. При этом пластические свойства материала снижаются. Одним из наиболее известных путей намеренного создания наклепа является холодная формовка деталей и изделий.
|
Полезный наклеп
Наклеп может быть желательным и нежелательным, полезным и вредным. Если наклеп металла является полезным, то при его изготовлении стремятся применять операции холодного пластического деформирования: холодную прокатку, волочение, обработку дробью, галтовку, накатку и тому подобное. Это особенно важно для металлов и сплавов, которые не способны упрочнятся термически. К этим материалам относятся низкоуглеродистые стали, некоторые алюминиевые сплавы, а также чистая медь. Когда эти материалы подвергаются сжатию, волочению, гибке или ковке, то напряжения, которые при этом возникают, приводят к возникновению в кристаллической структуре дислокаций, которые упрочняют металл. В этом случае применяют оба термина: и наклеп, и нагартовка.
Вредный наклеп
Нежелательный, вредный наклеп возникает, например, когда пластичные и мягкие металлы и сплавы подвергаются механической обработке резанием. Чрезмерно глубокие резы за один проход приводят с большой скоростью могут приводить к возникновению интенсивного наклепа с нежелательным увеличением прочности металла и его охрупчиванию. Это препятствует дальнейшей механической обработке детали, а может привести и к повреждению режущих инструментов. Другим примером вредного наклепа может служить повторяющееся нагружение детали с превышением предела текучести материала. При таком нагружении материал в критических сечениях может быстро наклепываться, терять свою пластичность и разрушаться. В подобных случаях явление деформационного упрочнения называют наклепом, но никогда не называют нагартовкой.
Рекристаллизация
|
Рекристаллизация – это процесс зарождения и роста новых недеформированных зерен при нагреве наклепанного металла до определенной температуры.
Нагрев металла до температур рекристаллизации сопровождается резким изменением микроструктуры и свойств. Нагрев приводит к резкому снижению прочности при одновременном возрастании пластичности. Также снижается электросопротивление и повышается теплопроводность.
1 стадия – первичная рекристаллизация (обработки) заключается в образовании центров кристаллизации и росте новых равновесных зерен с неискаженной кристаллической решеткой. Новые зерна возникают у границ старых зерен и блоков, где решетка была наиболее искажена. Количество новых зерен постепенно увеличивается и в структуре не остается старых деформированных зерен.
Движущей силой первичной рекристаллизации является энергия, аккумулированная в наклепанном металле. Система стремится перейти в устойчивое состояние с неискаженной кристаллической решеткой.
2 стадия – собирательная рекристаллизация заключается в росте образовавшихся новых зерен.
Движущей силой является поверхностная энергия зерен. При мелких зернах поверхность раздела большая, поэтому имеется большой запас поверхностной энергии. При укрупнении зерен общая протяженность границ уменьшается, и система переходит в более равновесное состояние.
Температура начала рекристаллизации связана с температурой плавления:
Tрек = a Tпл
для металлов а = 0,4;
для твердых растворов а = 0,5.. 0,8;
для металлов высокой чистоты а = 0,1.. 0,2.
На свойства металла большое влияние оказывает размер зерен, получившихся при рекристаллизации. В результате образования крупных зерен при нагреве до температуры t1 начинает понижаться прочность и, особенно значительно, пластичность металла.
Основными факторами, определяющими величину зерен металла при рекристаллизации, являются температура, продолжительность выдержки при нагреве и степень предварительной деформации.
С повышением температуры происходит укрупнение зерен, с увеличением времени выдержки зерна также укрупняются. Наиболее крупные зерна образуются после незначительной предварительной деформации 3…10 %. Такую деформацию называют критической. И такая деформация нежелательна перед проведением рекристаллизационного отжига.
|
Горячая деформации металлов
В отличие от холодной деформации горячая деформация металлов и сплавов происходит при температуре, величина которой достаточна для того, чтобы рекристаллизация деформированной структуры металла происходила одновременно с пластическим деформированием. Обычно горячую деформационную обработку (обработку давлением) производят при температуре выше температуры рекристаллизации металла (обычно от 70 до 90 % абсолютной температуры плавления). После такой горячей обработки получают металл с благоприятной мелкозернистой рекристаллизованной структурой.
Прокатный стан
Прокатный стан – это машина для осуществления прокатки, то есть для обработки металла (и других материалов) давлением между вращающимися валками. Основными частями стана являются:
1. Рабочая клеть – комплект валков со станиной.
2. Шестеренная клеть – устройство для распределения крутящего момента двигателя и передачи его на валки при помощи шпинделей.
3. Редуктор – устройство для повышения крутящего момент а за счет снижения угловой скорости.
4. Электродвигатель
Прокатные станы различаются по количеству рабочих клетей, длине бочки, назначению, количеству и расположению валков.
По количеству валков в клети различают прокатные станы дуо (два валка), трио (три валка), кватро (четыре валка) и многовалковые.
В трио-станах заготовка проходит сначала между верхним и средним валками, а потом между средним и нижним валками в обратную сторону. В кватро-станах и многовалковых станах два валка являются рабочими, а остальные – опорными. Опорные валки предотвращают изгиб рабочих валков.
Сортамент прокатки
При помощи прокатки производятся следующие виды заготовок:
· Сортовой прокат (сокращенно сорт)
· Листовой прокат (сокращенно лист)
· Трубный прокат (сокращенно трубы)
· Специальный прокат
Сортовой прокат
Существуют следующие виды сортового проката:
1. Простой – в сечении имеет форму простых геометрических фигур: круг, квадрат, прямоугольник и т.д.
2. Фасонный общего назначения
3. Фасонный специального назначения – изготавливается только под заказ и только большими партиями, так как проектирование и изготовление валков, переналадка прокатных станов стоят чрезвычайно дорого
Листовой прокат
Производятся одно- и многослойные листы; листы с покрытием и без покрытия.
В зависимости от толщины листовой прокат называется по-разному:
Толщина менее 0,2 мм – фольга
менее 4 мм – тонкий лист
менее 60 мм – толстый лист
более 60 мм – броня
|
Трубный прокат
Производятся монолитные (бесшовные) и сварные (шовные) трубы.
Для производства монолитных труб болванку прошивают в гильзу, затем раскатывают её в трубу за счет утонения стенок гильзы. Недостаток монолитных труб – ограниченная длина.
Для производства сварных труб лист сворачивают в трубу (по ширине или по винту) и сваривают кромки. Сварные трубы могут иметь большую длину, чем монолитные.
Технология прокатки листа
1. Слиток (массой до нескольких десятков тонн) нагревается до необходимой температуры
2. Слиток обжимается на слябинге и режется на слябы. Сляб – это заготовка, предназначенная для изготовления листового проката. В сечении сляб имеет форму прямоугольника высотой от 150 до 350 мм и шириной от 1000 до 2300 мм. Масса – до 45 тонн. Для прокатки слябов используются специальные прокатные станы – слябинги. Характеризуются диаметром бочки валков; например, слябинг 1150.
3. Сляб укатывается в толстый лист
4. Прокатку повторяют до получения листа необходимой толщины и ширины
5. Лист очищают от окалины (водой под давлением, щетками или другими способами)
6. Неровные края обрезаются
7. Лист режут на листы или сворачивают в рулон
Горячая прокатка применяется только до получения листа толщиной 1,5 мм – при меньшей толщине лист остывает быстрее, чем идет процесс прокатки, поэтому прокатка ведется в холодную.
При холодной прокатке лист можно крацевать (обрабатывать щетками), полировать, наносить покрытия и т.д.
Бесслитковая прокатка
Бесслитковая прокатка – это технология получения заготовок (обычно листа, ленты, прутков), заключающаяся в заливке жидкого металла в зазор между вращающимися валками. Жидкий металл заливается в металлоприемник, из которого поступает в зазор между валками, которые охлаждаются водой. При попадании в зазор, жидкий металл кристаллизуется, образуя заготовку.
Горячая объемная штамповка
Горячая объемная штамповка – способ обработки давлением, при котором металл заготовки затекает в полость штампа, называемую ручьем, принимая его форму. Течение металла ограничивается поверхностями полостей штампа. Давления при горячей объемной штамповке значительно выше, чем при свободной ковке, поэтому, таким способом обрабатываются детали массой до нескольких сотен килограммов. Для штамповки применяются молоты, прессы, горизонтально-ковочные машины.
Открытые штампы
В открытых штампах между подвижной и неподвижной частями штампа имеется переменный зазор с облойной канавкой. В этот зазор вытекает избыточная часть металла – облой, который затем обрезается на специальных обрезных штампах. Такие штампы широко применяются при штамповке на молотах. Открытые штампы не предъявляют высоких требований к точности заготовки, так как избыточный металл в любом случае будет выдавлен в облой.
Закрытые штампы
В закрытых штампах зазор между половинками штампа постоянен и невелик, образование облоя в зазоре не предусмотрено. Поэтому требуется соблюдать высокую точность заготовок по объему: если объем заготовки будет меньше объема полости штампа, то углы полости не заполнятся металлом; если же объем заготовки будет больше необходимого, то поковка будет выше, чем требуется; кроме того, если штамповка происходит на прессе или горизонтально-ковочной машине, возможна поломка механизма. Достоинствами штамповки в закрытых штампах являются снижение расхода металла (так как нет облоя), более благоприятная структура поковки (так как волокна обтекают контур поковки, а не перерезаются в месте выхода в облой). Штамповка в закрытых штампах обеспечивает большие сжимающие напряжения, поэтому позволяет обрабатывать малопластичные сплавы.
Обрезные штампы
Для обрезки облоя применяются обрезные штампы. Поковка устанавливается на матрицу, опираясь на неё облоем. Пуансон надавливает на поковку и режущие кромки матрицы срезают облой. Поковка проваливается в отверстие матрицы, которое для предотвращения застревания в нем поковки имеет конусность.
Пробивные штампы
Пробивные штампы применяются для пробивания пленок, возникающих при штамповке отверстий в поковках. Поковка устанавливается в матрицу, с помощью пуансона пробивается пленка. Отход проваливается в отверстие матрицы. Часто используются штампы совмещенного действия, которые одновременно удаляют облой и пробивают пленку.
Листовая штамповка
Отрезка
Отрезка – операция листовой штамповки, заключающаяся в отделении части заготовки на ножницах или в штампах. Для резки используются ножницы с поступательным движением ножа – гильотинные ножницы и ножницы с вращающимися дисковыми ножами – дисковые ножницы. У гильотинных ножниц кромки ножей наклонены друг к другу под углом 1…5° для уменьшения необходимых для резки усилий. Длина отрезаемой части листа ограничена длиной ножей. Дисковые ножницы не имеют ограничений по длине отрезаемой полосы.
Вырубка и пробивка
Вырубка и пробивка– операции листовой штамповки, заключающиеся в отделении части заготовки по замкнутому контуру. Отличаются тем, что вырубкой оформляется внешний контур изделия, а пробивкой – внутренний (т. е. отверстия). Для выполнения этих операций заготовку вдавливают в отверстие матрицы пуансоном. Режущие кромки матрицы врезаются в металл и отделяют часть заготовки, которая проваливается в отверстие матрицы.
В случае вырубки то, что было вырезано – изделие, а в случае пробивки – отход.
Гибка
Гибка – это операция листовой штамповки, заключающаяся в изменении кривизны заготовки практически без изменения её линейных размеров. Для гибки заготовка укладывается на матрицу, которая имеет углубление, соответствующее контуру изгиба. На заготовку надавливают пуансоном, имеющим выступ. В результате заготовка изгибается. После снятия нагрузки угол между полками уменьшается в результате пружинения. Для уменьшения пружинения применяют гибку с подчеканкой – для этого при гибке полки заготовки сжимаются между соответствующими плоскостями пуансона и матрицы. Чтобы избежать трещин на внешней поверхности изгиба, углубление в матрице выполняется с закругленным углом.
Вытяжка без утонения
Вытяжка без утонения – операция листовой штамповки, заключающаяся в получении полого изделия из плоской заготовки за счет уменьшения её периметра. Толщина стенок изделия такая же, как и у заготовки. Для этого заготовку укладывают на матрицу, надавливают на центральную часть заготовки пуансоном. Центральная часть заготовки вдавливается в матрицу и тянет за собой периферийную часть (фланец) заготовки, которая, втягиваясь в матрицу, образует стенки изделия. При вытягивании глубоких изделий на фланце могут появиться складки. Для предотвращения их появления фланец прижимают к матрице прижимом.
Вытяжка с утонением
Вытяжка с утонением – операция листовой штамповки, заключающаяся в увеличении длины полой заготовки за счет уменьшения толщины её стенок. Для этого заготовку вдавливают в матрицу пуансоном. При этом зазор между матрицей и пуансоном меньше толщины стенки заготовки. Стенки при сжатии между матрицей и пуансоном утоняются и удлиняются. Вытяжка с утонением применяется для получения изделий, у которых толщина стенки уменьшается или увеличивается по направлению к донышку, изделий большой длины, которые трудно получить вытяжкой без утонения из-за образования складок.
Отбортовка
Отбортовка – операция листовой штамповки, заключающаяся в создании бортов (горловин) путем вдавливания центральной части заготовки с предварительно пробитым отверстием в матрицу. При отбортовке диаметр исходного отверстия увеличивается, но не более чем в 1,2 … 1,8 раза. В противном случае возможно разрушение борта. Полученные в результате горловины применяются для установки в них деталей цилиндрического сечения.
Обжим
Обжим – операция листовой штамповки, заключающаяся в уменьшении диаметра краевой части полой заготовки. Для этого заготовку заталкивают в сужающуюся полость матрицы. Этим способом получают патронные и снарядные бутылочные гильзы.
Формовка
Формовка – операция листовой штамповки, заключающаяся в изменении формы заготовки за счет растяжения её отдельных участков. Этим способом получают разнообразные выступы, ребра жесткости и т.п.
Для формовки вместо металлической матрицы часто применяют резиновую подушку. Кроме того с помощью разъемной матрицы и резинового вкладыша или жидкости можно увеличить размеры средней части полой заготовки. Для этого заготовку помещают в матрицу, вставляют внутрь вкладыш (или заливают жидкость) и надавливают пуансоном. Вкладыш (или жидкость) растягивают заготовку. Затем матрицу раскрывают, достают изделие и извлекают вкладыш (выливают жидкость).
Свободная ковка
Свободная ковка – способ обработки давлением, заключающийся в свободном пластическом течении металла заготовки при сжатии её между бойками молота или пресса. Свободной ковкой обрабатываются заготовки любого размера и массы.
Бойки для свободной ковки могут иметь разную форму рабочих поверхностей. Для закрепления бойков в бабе молота или ползуне пресса применяется крепление типа «ласточкин хвост».
Основные операции свободной ковки
К основным операциям свободной ковки относятся
· Осадка
· Высадка
· Протяжка
· Прошивка
· Рубка
· Раскатка
Осадка
Осадка – это операция свободной ковки, заключающаяся в уменьшении высоты заготовки за счет увеличения её поперечного сечения. Если длина заготовки более чем в 2,5 раза больше её диаметра, заготовка при осадке может погнуться.
Высадка
Высадка – это операция свободной ковки, представляющая собой разновидность осадки. Отличается тем, что при высадке металл осаживают только на части длины заготовки. Для этого ту часть заготовки, которую не требуется осаживать, не нагревают и устанавливают в отверстие обоймы. Для облегчения извлечения заготовки отверстие обоймы имеет небольшую конусность.
Протяжка
Протяжка – это операция свободной ковки, заключающаяся в увеличение длины и ширины заготовки за счет уменьшения её высоты. Протяжку производят, нанося последовательные удары (или совершая нажатия) по участкам заготовки, примыкающим один к другому, и перемещая заготовку вдоль оси протяжки, одновременно поворачивая её на 90°. Протяжка может выполняться на оправке для удлинения полой заготовки за счет утонения стенок. Для облегчения удаления оправки из заготовки оправку выполняют с небольшой конусностью. Подвидом протяжки является разгонка – операция увеличения ширины заготовки за счет уменьшения высоты.
Раскатка на оправке
Раскатка на оправке – операция свободной ковки, заключающаяся в увеличении внутреннего и внешнего диаметров кольцевой заготовки за счет уменьшения толщины стенок. Для этого заготовка устанавливается на специальное приспособление – оправку – и деформируется на ней. После каждого нажатия заготовку поворачивают на оправке.
Прошивка
Прошивка – операция свободной ковки, заключающаяся в проделывании в заготовке полости за счет вытеснения металла при помощи специального инструмента – прошивня. Прошивень имеет форму цилиндра или усеченного конуса, укрепленного на ручке. Может быть сплошным (для небольших отверстий) или пустотелым (для отверстий диаметром 400…900 мм). При прошивке прошивень не проходит до конца, так как трение между нижним бойком и металлом нижних слоев заготовки препятствует движению металла. Поэтому при необходимости прошить заготовку насквозь, сначала проделывают глухое отверстие с одной стороны, а затем переворачивают заготовку и прошивают её в том же месте.
Рубка
Рубка – операция свободной ковки, заключающаяся в отделении части заготовки при помощи топора. Топор имеет клиновидную форму и укреплен на ручке. При рубке топор устанавливают под верхний боек. Чтобы не повредить топор, бойки и станок, заготовку не прорубают до конца сразу, а оставляют нетронутым слой металла толщиной 10-20 мм. После этого заготовку переворачивают, на место, где топор выйдет из заготовки, подкладывают брусок и доламывают.
Гибка
Гибка – операция свободной ковки, заключающаяся в изгибании заготовки по заданному контуру. Для гибки применяют фигурные бойки: нижний имеет углубление, соответствующее контуру изгиба, верхний – выступ. При штучном изготовлении небольших изделий гибку производят ударами кувалдой по концу зажатой между бойками заготовки. В месте изгиба площадь сечения заготовки уменьшается – происходит утяжка. Для компенсации утяжки заготовку в месте изгиба делают толще. Также при гибке возможно появление складок на внутренней поверхности изгиба и трещин на внешней. Для предотвращения этих дефектов углы выполняют закругленными.
Чертеж поковки
Чертеж поковки выполняется на основе чертежа готовой детали с учетом напусков, припусков и допусков. Напуск – объем металла, добавляемый к поковке для упрощения её формы, а, следовательно, и технологии её изготовления. Припуск – слой металла на поверхности поковки, который удаляется при обработке резанием для получения необходимых размеров и качества поверхности. Допуск – допустимое отклонение от номинального размера поковки (то есть разница между минимальным и максимальным допустимыми размерами).
Холодная объемная штамповка
Холодная объемная штамповка – это процесс получения поковок в результате холодной пластической деформации заготовок в штампах.
Основные разновидности
· Выдавливание
· Высадка
· Штамповка в открытом штампе
Выдавливание
Выдавливание – операция холодной объемной штамповки, заключающаяся в выдавливании металла заготовки из замкнутой полости через отверстия. При прямом выдавливании металл выходит через отверстие в донной части матрицы в направлении движения пуансона. При обратном выдавливании металл выходит в зазор между стенками матрицы и пуансоном против направления движения пуансона.
Высадка
Высадка – операция холодной штамповки, заключающаяся в увеличении поперечного сечения части заготовки за счет уменьшения её высоты. Заготовку помещают в матрицу, установленную на плите, и надавливают на выступающую часть заготовки пуансоном.
Жидкая штамповка
Жидкая штамповка – это технология получения заготовок, заключающаяся в затвердевании жидкого металла в полости инструмента под высоким давлением. Металл заливают в полость формы-матрицы, соответствующей форме поковки, сжимают пуансоном. После кристаллизации поковка извлекается выталкивателем.
Прессование
Прессование – способ обработки давлением, заключающийся в выдавливании металла заготовки пресс-шайбой, движущейся под действием пуансона, из замкнутого объема пресс-цилиндра через отверстие матрицы.
P – направление действия силы
Волочение
Волочение – способ обработки давлением, заключающийся в протягивании заготовки через отверстие специальной матрицы, называемой волокой. Для получения отверстия применяется оправка, устанавливаемая в отверстии матрицы.
Литейное производство
Литейное производство – это производство, продукция которого – отливки, получаемые в литейных формах при кристаллизации жидких сплавов.
Требования к литейным сплавам
Требования к каждому литейному сплаву специфичны, однако существует и ряд общих требований:
состав сплава должен обеспечивать получение заданных свойств отливки (физических, химических, физико-химических, механических и др.);
сплав должен обладать хорошими литейными свойствами: высокой жидкотекучестью, несклонностью к насыщению газами и к образованию неметаллических включений, малой и стабильной усадкой при затвердевании и охлаждении, несклонностью к ликвации и образованию внутренних напряжений и трещин в отливках;
состав, свойства и структура сплава как в исходном состоянии, так и в готовой литой детали должны быть постоянными и не изменяться в процессе ее эксплуатации;
сплав должен быть по возможности простым по составу, легко приготовляться, не содержать токсичных компонентов, не выделять при плавке и заливке сильно загрязняющих окружающую среду продуктов;
потери сплава при его приготовлении и в процессе литья должны быть минимальными;
сплав должен быть технологичным не только в изготовлении отливок, но и на всех последующих операциях получения готовых деталей (при обработке резанием, сварке, пайке, термической, гальванической и других видах окончательной обработки);
сплав должен быть экономичным: содержать по возможности меньшее количество дорогостоящих компонентов (быть экономно легированным), иметь минимальные потери при переработке его отходов (литников, брака, сплесков).
Выполнить все перечисленные требования в большинстве случаев практически невозможно, поэтому для решения определенных технических задач используют сплавы, свойства которых отвечают какому-нибудь одному (основному) требованию, а остальные требования приобретают подчиненное ему значение. Так, для изготовления рабочих лопаток газотурбинного авиационного двигателя применяют сплавы на никелевой основе, обладающие хорошей прочностью при высоких температурах (800—1200°С), т. е. жаропрочные. Однако эти сплавы не отвечают многим другим требованиям: они плохо обрабатываются резанием, образуют оксидные плены, что вызывает необходимость ведения плавки и заливки форм в вакууме, имеют сложный состав (содержат до 10 легирующих компонентов), весьма дороги.
Литейные свойства сплавов
Литейными называют ряд свойств металлов и сплавов, определяющих их технологичность в литейных процессах, т. е. пригодность для получения из них отливок необходимой конфигурации, с высокими эксплуатационными свойствами, заданной размерной точностью и требуемым качеством поверхности. Литейные свойства проявляются как в расплавах, так и на всех стадиях их затвердевания и охлаждения. Важнейшими литейными свойствами сплавов являются жидкотекучесть, усадка, склонность к образованию неметаллических включений, к поглощению газов, ликвации, склонность к образованию внутренних напряжений и трещин.
Жидкотекучесть — способность металлов и сплавов в расплавленном состоянии заполнять литейную форму, четко воспроизводя контуры ее и поверхность.
Усадка — свойство металлов и сплавов уменьшать объем при охлаждении в расплавленном состоянии, в процессе затвердевания и в затвердевшем состоянии при охлаждении до температуры окружающей среды. Различают объемную и линейную усадки, выражаемые обычно в процентах.
Ликвация — неоднородность химического состава литейного сплава в различных частях отливки, возникающая при ее затвердевании, из-за различной растворимости отдельных компонентов сплава в его жидкой и твердой фазах.
Формовочные материалы
Формовочные материалы – это материалы, из которых изготавливаются элементы литейной формы
Стержень формируют и нагревают – олифа связывает песчинки и стержень твердеет. При заливке металла олифа сгорает. После извлечения отливки из формы песок легко вытряхивается из полостей
Модельно-опочная оснастка
Элементы сборки формы
Для правильного ориентирования опок друг относительно друга и предотвращения смещения одной опоки относительно другой служат центрирующие проушины, в которые устанавливают центрирующие стержни. Чтобы опоки не раскрылись под давлением жидкого металла, их либо придавливают сверху грузом, либо скрепляют скобами, которые надеваются на специальные кронштейны.
|
|
Биохимия спиртового брожения: Основу технологии получения пива составляет спиртовое брожение, - при котором сахар превращается...
Адаптации растений и животных к жизни в горах: Большое значение для жизни организмов в горах имеют степень расчленения, крутизна и экспозиционные различия склонов...
Семя – орган полового размножения и расселения растений: наружи у семян имеется плотный покров – кожура...
Эмиссия газов от очистных сооружений канализации: В последние годы внимание мирового сообщества сосредоточено на экологических проблемах...
© cyberpedia.su 2017-2024 - Не является автором материалов. Исключительное право сохранено за автором текста.
Если вы не хотите, чтобы данный материал был у нас на сайте, перейдите по ссылке: Нарушение авторских прав. Мы поможем в написании вашей работы!