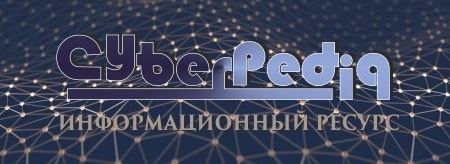
Архитектура электронного правительства: Единая архитектура – это методологический подход при создании системы управления государства, который строится...
Состав сооружений: решетки и песколовки: Решетки – это первое устройство в схеме очистных сооружений. Они представляют...
Топ:
Оснащения врачебно-сестринской бригады.
Оценка эффективности инструментов коммуникационной политики: Внешние коммуникации - обмен информацией между организацией и её внешней средой...
Процедура выполнения команд. Рабочий цикл процессора: Функционирование процессора в основном состоит из повторяющихся рабочих циклов, каждый из которых соответствует...
Интересное:
Инженерная защита территорий, зданий и сооружений от опасных геологических процессов: Изучение оползневых явлений, оценка устойчивости склонов и проектирование противооползневых сооружений — актуальнейшие задачи, стоящие перед отечественными...
Распространение рака на другие отдаленные от желудка органы: Характерных симптомов рака желудка не существует. Выраженные симптомы появляются, когда опухоль...
Наиболее распространенные виды рака: Раковая опухоль — это самостоятельное новообразование, которое может возникнуть и от повышенного давления...
Дисциплины:
![]() |
![]() |
5.00
из
|
Заказать работу |
|
|
Для выявления факторов, влияющих на качество червячной фрезы, необходимо определить основные параметры фрезы. В таблице 2.1. представлены параметры червячной фрезы, которые влияют на точность нарезаемого колеса, и взяты из чертежа. Таблица составлена для червячных фрез с посадочным отверстием Æ40 мм и модулем от 2 до 4 мм.
Таблица 2.1
Параметры червячной фрезы | Класс точности фрезы | |
А | АА | |
Допуски, мкм | ||
Отклонение диаметра посадочного отверстия | +11 | +11 |
Радиальное биение буртиков относительно оси отв. | 5 | 5 |
Торцовое биение буртиков относительно оси отв. | 3 | 3 |
Радиальное биение по наружному диаметру относительно оси отв. | 20 | 12 |
Нецилиндричность по наружному диаметру | 20 | 12 |
Отклонение от номинального положения образующей передней поверхности в сторону поднутрения | 20 | 12 |
Наибольшая разность соседних окружных шагов стружечных канавок | 20 | 12 |
Накопленная погрешность окружного шага стружечных канавок | 40 | 25 |
Погрешность направления стружечных канавок на длине 100 мм нормально к передней поверхности на делительном цилиндре | 70 | 50 |
Погрешность профиля зуба в сечении заданном чертежом | 8 | 5 |
Отклонение толщины зубьев от номинальной | ±16 | ±8 |
Наибольшая погрешность винтовой линии от зуба к зубу | 8 | 4 |
Наибольшая погрешность винтовой линии фрезы на 1/n оборота, где n – число заходов. | 12 | 6 |
Наибольшая погрешность винтовой линии фрезы на 3/n оборота, где n – число заходов. | 16 | 8 |
Погрешность деления от захода к заходу | 9 | - |
Отклонение точки начала фланка от номинального положения | ±50 | ±50 |
Несимметричность точек начала фланка | 50 | 50 |
Отклонения угла профиля фланка от номинального положения, градусы | ±1,5 | ±1,5 |
Отклонение ширины усика на вершине зуба, измеренное нормально к профилю, от номинального | ±18 | ±18 |
Погрешность высоты усика на вершине зуба фрезы | 200 | 200 |
|
Также определяющими параметрами червячной фрезы являются шероховатости базовых и рабочих поверхностей. Параметры шероховатостей представлены в таблице 2.2.
Таблица 2.2
Наименование поверхности фрезы | Шероховатость |
Передняя поверхность зубьев, Ra | 0,2 |
Поверхность отверстия, Ra | 0,2 |
Поверхность торцев, Ra | 0,2 |
Задняя поверхность на боковых сторонах и вершинах зубьев, Rа | 0,2 |
Цилиндрическая поверхность буртиков, Ra | 0,2 |
На основании особенностей работы червячной фрезы и данных из таблиц 2.1 и 2.2 можно сделать вывод, что некоторые параметры не участвуют в формообразовании рабочей части зуба нарезаемого колеса и как видно из таблицы 2.1 допуски на эти параметры не ужесточаются с повышением класса точности червячной фрезы:
Отклонение точки начала фланка от номинального положения;
Несимметричность точек начала фланка;
Отклонения угла профиля фланка от номинального положения, градусы
Отклонение ширины усика на вершине зуба, измеренное нормально к профилю, от номинального
Погрешность высоты усика на вершине зуба фрезы.
Также не ужесточаются с увеличением класса точности фрезы следующие параметры:
Радиальное биение буртиков относительно оси отв.
Торцовое биение буртиков относительно оси отв.
Данные параметры служат лишь для проверки правильности установки фрезы на оправке в зубофрезерном станке.
Параметр – погрешность деления от заходу к заходу, необходимо исключить из этого исследования, т.к. у высокоточных фрез заход всегда один.
Выше перечисленные параметры можно не считать определяющими, т.к. ГОСТ не считает возможным их ужесточение при производстве более точных червячных фрез.
Оставшиеся параметры можно считать определяющими качество червячных фрез. Теперь необходимо определиться какой параметр, на какой технологической операции формируется. Данные сведем в таблицу 2.3.
|
Таблица 2.3
№ | Параметры червячной фрезы | Определяющая технологическая операция |
1 | Отклонение диаметра посадочного отверстия | Внутришлифовальная |
2 | Радиальное биение по наружному диаметру относительно оси отв. | Шлифование профиля |
3 | Нецилиндричность по наружному диаметру | Шлифование профиля |
4 | Отклонение от номинального положения образующей передней поверхности в сторону поднутрения | Заточная |
5 | Наибольшая разность соседних окружных шагов стружечных канавок | Заточная |
6 | Накопленная погрешность окружного шага стружечных канавок | Заточная |
7 | Погрешность направления стружечных канавок на длине 100 мм нормально к передней поверхности на делительном цилиндре | Заточная |
8 | Погрешность профиля зуба в сечении заданном чертежом | Шлифование профиля |
9 | Отклонение толщины зубьев от номинальной | Шлифование профиля |
10 | Наибольшая погрешность винтовой линии от зуба к зубу | Шлифование профиля |
11 | Наибольшая погрешность винтовой линии фрезы на 1/n оборота, где n – число заходов. | Шлифование профиля |
12 | Наибольшая погрешность винтовой линии фрезы на 3/n оборота, где n – число заходов. | Шлифование профиля |
13 | Шероховатость посадочного отверстия | Внутришлифовальная |
14 | Шероховатость по задней поверхности и вершине зубьев | Шлифование профиля |
15 | Шероховатость по передней поверхности | Заточная |
Полученные данные можно разделить на параметры, отвечающие за точность фрезы и параметры, отвечающие за стойкость. Несложно догадаться, что все погрешности профиля инструмента будут переносится на профиль, обрабатываемого им изделия. Поэтому на точность однозначно влияют параметры №8, 9 и 14. Так как червячная фреза – это инструмент, работающий методом обката, то все отклонения винтовой линии или шага зубьев приводят в итоге к искажению профиля детали. То есть параметры точности №10, 11, 12. Червячная фреза затылованная имеет достаточно большой задний угол (обычно 8–11 градусов), поэтому искажение передней поверхности в итоге приводит к искажению и профиля – это будут также параметры точности №4, 5, 6, 7. Параметры №2 и 3 влияют на величину равномерной загрузки зубьев фрезы, поэтому это будут и параметры точности и стойкости. Параметр №1 и 13 отвечают за плотность посадки фрезы на оправку, посадочное отверстие является основной базой, поэтому эти параметры относятся к точности. Параметр №15 отвечает за процесс резания, чем лучше шероховатость передней поверхности, тем меньше трение между деталью и заготовкой и тем меньше силы резания и температура в зоне, а значит и износ фрезы, поэтому это параметры стойкости.
|
Параметры отвечающие за точность червячной фрезы: №1, 2, 3, 4, 5, 6, 7, 8, 9, 10, 11, 12, 13, 14.
Параметры отвечающие за стойкость червячной фрезы: №2, 3, 15.
Вывод: улучшая параметры, отвечающие за точность червячной фрезы можно ожидать снижение брака при обработке зубчатых колес, а улучшая параметры, отвечающие за стойкость – увеличение срока службы червячной фрезы. Также были выявлены операции технологического процесса, где формируются эти параметры.
Анализ проблемных операций
Внутришлифовальная операция.
Как показал анализ замеров по параметрам: допуск на размер отверстия и шероховатость в отверстии, основные нарекания вызывает не сам размер отверстия, а требования к конусности. Перепад диаметров должен быть не более половины допуска на размер.
По существующему техпроцессу отверстие сначала шлифуется с припуском 0,005 мкм, а затем вручную доводится при помощи притира. Так как червячные фрезы, изготавливаемые в ИП ОАО «АВТОВАЗ» длиной от 150 до 220 мм, то во время ручной обработки притиром возникает неравномерность давления на разные его стороны, вследствие чего и возникает конусность.
Операция шлифование профиля.
Анализ замеров червячных фрез показал, что наиболее часто происходит брак по двум параметрам: радиальное биение по наружному диаметру относительно оси отверстия и допуск на наружный диаметр. На этой операции червячная фреза устанавливается на конусную оправку, а оправка в центрах находится в станке, поэтому погрешность по биению наружного диаметра складывается в основном из двух факторов:
– радиальное биение шпинделя изделия станка
– радиальное биение наружного диаметра оправки относительно центров.
Остальные погрешности станка влияют косвенно и не значительно. Также присутствует некоторое влияние сил резания и самого веса фрезы, но в данном случае, окончательно профиль фрезы формируется после выхаживания, то есть работы без подачи, а значит, силы резания крайне малы; вес фрезы мы изменить не в силах, потому эти погрешности не приводим в качестве основных факторов.
|
При этом фактическая величина биения шпинделя станка находится в пределах 2–3 мкм. Биение же оправки доходит до 8 мкм.
Допуск на наружный диаметр 0,2 мм, на операции токарной обработки оставляется припуск 0,5 мм на диаметр, но в связи с биением, возникающим после внутришлифовальной операции (до 0,5 мм), этого припуска не всегда хватает и приходится занижать весь профиль зубьев, а с ним и наружный диаметр фрезы. Необходимо проанализировать, почему появляется такое биение наружного диаметра после внутришлифовальной операции. На этой операции базирование происходит по торцам фрезы, а это, во-первых, нарушает принцип единства баз и, во-вторых, опорная длина торца, в некоторых случаях, в 4 раза меньше длины фрезы. Необходимо совместить конструкторскую и технологическую базу и увеличить опорную длину.
Заточная операция.
Здесь наибольший интерес представляет параметры фрезы №5, 6, 15. Остальные параметры в большей степени зависят от правильности настройки станка по первой детали. По параметру №15 больше всего нареканий от потребителя. Выявим факторы, оказывающие влияние наибольшее влияние на параметры №5 и 6. Червячная фреза устанавливается с зазором на цилиндрическую оправку, оправка одним концом базируется по коническому хвостовику в шпинделе станке, а другой конец поджимается вращающимся центром. Деление осуществляется при помощи делительного диска. Отсюда можно сделать вывод, что смещение стружечной канавки от номинального положения происходит преимущественно из-за двух явлений – биение зубьев червячной фрезы и погрешность деления, отсюда можно сделать вывод, что смещение передней поверхности происходит ввиду факторов:
– радиальное биение шпинделя станка;
– радиальное биение оправки;
– зазор между оправкой и фрезой;
– погрешность делительного диска.
Для выявления факторов, не обеспечивающих шероховатость, в соответствии с требованиями чертежа, воспользуемся статистическим методом анализа.
|
|
Общие условия выбора системы дренажа: Система дренажа выбирается в зависимости от характера защищаемого...
Историки об Елизавете Петровне: Елизавета попала между двумя встречными культурными течениями, воспитывалась среди новых европейских веяний и преданий...
Таксономические единицы (категории) растений: Каждая система классификации состоит из определённых соподчиненных друг другу...
Кормораздатчик мобильный электрифицированный: схема и процесс работы устройства...
© cyberpedia.su 2017-2024 - Не является автором материалов. Исключительное право сохранено за автором текста.
Если вы не хотите, чтобы данный материал был у нас на сайте, перейдите по ссылке: Нарушение авторских прав. Мы поможем в написании вашей работы!