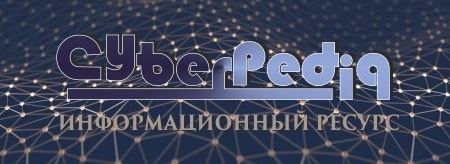
Поперечные профили набережных и береговой полосы: На городских территориях берегоукрепление проектируют с учетом технических и экономических требований, но особое значение придают эстетическим...
Автоматическое растормаживание колес: Тормозные устройства колес предназначены для уменьшения длины пробега и улучшения маневрирования ВС при...
Топ:
Техника безопасности при работе на пароконвектомате: К обслуживанию пароконвектомата допускаются лица, прошедшие технический минимум по эксплуатации оборудования...
Выпускная квалификационная работа: Основная часть ВКР, как правило, состоит из двух-трех глав, каждая из которых, в свою очередь...
Организация стока поверхностных вод: Наибольшее количество влаги на земном шаре испаряется с поверхности морей и океанов...
Интересное:
Инженерная защита территорий, зданий и сооружений от опасных геологических процессов: Изучение оползневых явлений, оценка устойчивости склонов и проектирование противооползневых сооружений — актуальнейшие задачи, стоящие перед отечественными...
Как мы говорим и как мы слушаем: общение можно сравнить с огромным зонтиком, под которым скрыто все...
Отражение на счетах бухгалтерского учета процесса приобретения: Процесс заготовления представляет систему экономических событий, включающих приобретение организацией у поставщиков сырья...
Дисциплины:
![]() |
![]() |
5.00
из
|
Заказать работу |
|
|
Технологическая схема цеха помола клинкера включает в себя следующие этапы: хранение исходных компонентов в силосах (клинкера, добавок, гипса), сушку влажных добавок для обеспечения требуемой влажности продуктов, дозирование компонентов, осуществляемое на питателях и дозаторах, для удовлетворения требуемого состава цемента, помол до требуемого гранулометрического состава, охлаждения цемента до 60 - 70º С, для исключения распада гипса, хранение цемента и отгрузка его в автомобильные или железнодорожные цистерны.
В цехе установлено 40 железобетонных силосов для хранения клинкера, добавок, гипса, цемента. Перемещение клинкера, добавок, гипса, цемента между силосами и сушильной камерой и мельницами осуществляется с помощью пневмокамерных насосов и конвейера ленточного типа. Отгрузка цемента в транспорт осуществляется пневматическим способом.
Расчёт материального баланса производства
Годовая производительность завода:
ПЦ 500: 1200000 × 0,2 = 240000 тонн в год;
СПЦ 500: 1200000 × 0,8 = 960000 тонн в год;
Клинкер для ПЦ 500: 240000 × 0,81 = 194400 тонн в год;
для СПЦ 500: 960000 ×0,80 = 768000 тонн в год;
всего клинкера 194400 + 768000 = 962400 тонн в год;
шлак (сухой) для ПЦ 500 240000 × 0,14 = 33600 т.г.
шлак (влажный) для ПЦ 500 33600 × 1,21 = 40656 т.г.
диатомит (сухой) для СПЦ 500 960000 × 0,15 = 144000 т.г.
диатомит (влажный) для СПЦ 500 144000 × 1,18 = 169920 т.г.
гипсовый камень для ПЦ 500 240000 × 0,05 = 12000 т.г.
для СПЦ 500 960000 × 0,05 = 48000 т.г.
всего гипсового камня 12000 + 48000 = 60000 т.г.
проверка 962400 + 33600 + 144400 + 60000 = 1200000 (правильно)
Суточная производительность цемента:
ПЦ 500 240000 / 365 =657,354 т. сутки
СПЦ 500 960000 / 365 = 2630,137 т. сутки
Клинкер 962400 / 365 = 2636, 712 т. сутки
Шлак сухой 33600 / 365 = 92,054 т. сутки
|
Шлак влажный 40656 / 365 = 111, 386 т. сутки
Диатомит сухой 144000 / 365 = 394,520 т. сутки
Диатомит влажный 169920 / 365 = 465,534 т. сутки
Гипс 60000 / 365 = 164,383 т. сутки
Расход материала в час
ПЦ 500 657,354 / 24 = 27,390 т. час
СПЦ 500 2630,137 / 24 = 109,589 т. час
Клинкер 2636,712 / 24 = 109,589 т. час
Шлак сухой 92,054 / 24 = 3,835 т. час
Шлак влажный 111,386 / 24 = 4,641 т. час
Диатомит сухой 394,520 / 24 = 16,438 т. час
Диатомит влажный 465,534 / 24 = 19,397 т. час
производительность | Тонн в год | Тонн в сутки | Тонн в час |
ПЦ 500 | 240000 | 657,354 | 27,390 |
СПЦ 500 | 960000 | 2630,137 | 109,589 |
клинкер | 962400 | 2636,712 | 109,863 |
Шлак сухой | 33600 | 92,054 | 3,835 |
Шлак влажный | 40656 | 111,386 | 4,641 |
Диатомит сухой | 144000 | 394,520 | 16,438 |
Диатомит влажный | 169920 | 465,534 | 19,397 |
Гипсовый камень | 60000 | 164,383 | 6,849 |
Расчёт объёма гипсового склада
Геометрический объём Vc м. куб силосного склада для каждого компонента
ПЦ 500 Vпц =(АСн) / (365 × Ρн ×Кз) = (240000 × 10) / (365 ×1,45 × 0,9) = 5039 м³.
где ρн - средняя насыпная масса материала, т/м³
А - производительность завода по данному цементу, либо расход клинкера, гипса, добавки, т/год
Кз - коэффициент заполнения силоса, обычно принимается 0,9.
СПЦ 500 Vспц =(АСн)/(365 × ρн × Кз) = (960000×10) / (365×1,45×0,9) = 20154 = м³
Клинкера Vкл = (962400×4) / (365×1,5×0,9) = 7812 м³
Шлака Vш = (40656×15) / (365×0,5×0,9) = 3713 м³
Диатомита Vд = (169920×15) / (365×0,9×0,9) = 8621 м³
Гипса Vг = (60000×15) / (365×1,35×0,9) = 2029 м³
Из утверждённых ГОСТом РФ размеров силосов, выбираем для хранения цемента силосы:
Для ПЦ 500 12×19,8 м V = 1700 м³
шт. VΣ = 5100 м³
Для СПЦ 500 12×19,8 V = 1700 м³
шт. VΣ = 22100 м³
Общее количество 16 силосов.
Такое количество выбрано из соображения более быстрой погрузки железнодорожных составов.
Силосы для клинкера:
Vк = (962400×4) / (365×1,6×0,9) = 7324 м³
Выберем размер силоса 12×19,8 V = 1700 м³
Количество силосов для клинкера n = (7324) / (1700) = 4,3
Примем количество силосов для клинкера 5шт.
Силосы для гипса:
Vг = (60000×15) / (365×1,35×0,9) = 2029 м³
|
n = (2029) / (1700) = 1,19
примем количество силосов для гипса 2 шт.
Силосы для диатомита:
Vд сух = (144000×15) / (365×1,1×0,9) = 7300 м³
n = (7300) / (1700) = 5 шт.
Силосы для шлака:
Vш сух = (33600×15) / (365×0,5×0,9) = 3068 м³
n = (3068) / (1700) = 1,8. примем количество силосов 2 шт.
Итого количество силосов:
Для цемента N6 4 шт.15 12 шт.
Размером 12×19,8 м общим количеством 16 штук.
Для клинкера 12×19,8 м 5 штук
Для гипса 12×19,8 м 2 штуки
Для диатомита 12×19,8 м 5 штук
Для шлака 12×19,8 м 2 штуки
Общее количество силосов 30 штук.
Расчёт сушильного отделения
Необходимость сушки активных минеральных добавок, измельчаемых совместно с клинкером, определяется высокой влажностью добавок. Доменные гранулированные шлаки также имеют высокую влажность, так как их получают грануляцией огнненожидкого шлама в специальных водных бассейнах. Содержащаяся в добавках влага начнёт реагировать с клинкерной частью цемента и качество его в результате преждевременной гидратации резко ухудшится. Кроме того тонко измельчённый материал налипает на мелющие тела, броневые плиты, замазывает междукамерные и разгрузочные перегородки мельницы, затрудняя или полностью прекращая в ней измельчение.
Так как в цементах 6 и 15 разные добавки, то расчёт сушильного отделения будем производить отдельно для доменного шлака, имеющего влажность 21 %, и отдельно для диатомита влажностью 18 %.
Производительность сушильного барабана для шлака
Выход высушенного шлака
Qбш = (1000×Q)/3600 = (1000×3,835)/3600 = 1,065 кг/сек.
где Q - количество материала, нуждающегося в сушке (по высушенной массе), т/час;
Выход влаги Qwш
Qwш = Qобщ (Wн/(100 - Wн)-Wk/(100 - Wk)) = 1,065×
×(21/(100 - 21) - 1/(100 - 1)) = 0,272 кг/сек.
где Wн - начальная влажность материала,%к - конечная влажность материала, % (0,5 - 1,0 %).
Производительность сушильного барабана для диатомита.
Выход высушенного диатомита:
Qбд = 1000×Q / 3600 = 1000×16,438 / 3600 = 4,566 кг / сек.
Выход влаги Qwд = Qбд×(Wн/(100 - Wн) - Wk/(100 - Wk)) = 4,566×(18/(100-18) - 1/(100 - 1)) = 0,956 кг/сек.
Определение рабочего объёма сушильного барабана для шлака и выбор его по таблицам.
V = 3600×Qwш/А = 3600×0,272/55 = 17, 8 м³
Где А - удельный паросъём, кг/(м³ч), для шлака 55 - 60 кг/(м³ч), для остальных материалов А = 45 - 55 кг/(м³ч).
Время прохождения материала через сушильный барабан:
|
τ = (120×β×ρ×(Wн - Wk))/(А(200×(Wн - Wk))) =
= (120×500×0,2×(21 - 1)/(55×(200×(21 -1))) =
= 24,2 минуты.
где ρ - средняя насыпная плотность материала, кг/м³,
β - коэффициент заполнения барабана в долях единицы, β = 0,2.
Необходимая мощность привода для вращения барабана N (кВт):
N = 0,0013×Dб³×Lб×n×ρ×δ = 0,0013×2,2³×14×3,6×500×0,02 =
= 7 кВт
где - D, L диаметр и длина барабана, мчастота вращения выбранного барабана
ρ средняя насыпная плотность 500 кг/м³
δ коэффициент учитывающий вид теплообменных устройств в барабане, δ = 0,04 - 0,07 для лопастного теплообменника или при навеске цепей, и δ = 0,01 - 0,02 для ячейково - сепараторного теплообменника.
Из выпускаемых сушильных барабанов наиболее оптимальным является СМЦ - 440.
Размеры барабана:
D = 2,2 м, L = 14 м, V = 53 м³
Наклон барабана 1-4%
Производительность по сухому материалу 14 т/ч
Влажность материала:
На входе 22 %
На выходе 3 %
Частота вращения барабана 3,6 об/мин
Мощность привода двигателя 36 кВт
Масса 35 тонн.
Определение рабочего объёма сушильного барабана для сушки диатомита и выбор его по таблицам.
Рабочий объём сушильного барабана для диатомита
Vд = 3600 Qwд / А = 3600×0,95 / 45 = 76,48 м³
где А - удельный паросъём кг/(м³×ч) = 45 - 55 кг/(м³×ч)
Время прохождения через сушильный барабан τ
τ = 120×β×ρ×(Wн - Wк) / (А×(200 - (Wн - Wк))) =
= 120×0,2×1100×(18 - 1)/ (45×(200 - (18 - 1))) = 54,50 мин.
где - β коэффициент заполнения барабана = 0,1 - 0,25;
ρ средняя насыпная плотность материала = 900 - 1100 кг / м³
Мощность привода для вращения барабана N (кВт)
N = 0,0013×Dб³×Lб×n×ρ×δ = 0,0013×2,8³×14×4,68×1100×0,02 = 41,13 кВт
где Dб, Lб диаметр и длина барабана,число оборотов выбранного барабана об/мин,
δ коэффициент, учитывающий вид теплообменных устройств = 0,01 - 0,02 Из выпускаемых сушильных барабанов подходит СМЦ - 429, имеющий характеристики:
Диаметр барабана 2,8 м
Длина барабана 14 м
Наклон барабана 5 %
Производительность по 20 - 25 т/ч сухому материалу
Влажность материала
на входе 20 - 22 %
на выходе 1 - 8 %
Частота вращения барабана 4,68 об \мин
Мощность привода двигателя 55 кВт
Масса 62,4 т
|
|
Поперечные профили набережных и береговой полосы: На городских территориях берегоукрепление проектируют с учетом технических и экономических требований, но особое значение придают эстетическим...
Двойное оплодотворение у цветковых растений: Оплодотворение - это процесс слияния мужской и женской половых клеток с образованием зиготы...
Состав сооружений: решетки и песколовки: Решетки – это первое устройство в схеме очистных сооружений. Они представляют...
История развития пистолетов-пулеметов: Предпосылкой для возникновения пистолетов-пулеметов послужила давняя тенденция тяготения винтовок...
© cyberpedia.su 2017-2024 - Не является автором материалов. Исключительное право сохранено за автором текста.
Если вы не хотите, чтобы данный материал был у нас на сайте, перейдите по ссылке: Нарушение авторских прав. Мы поможем в написании вашей работы!